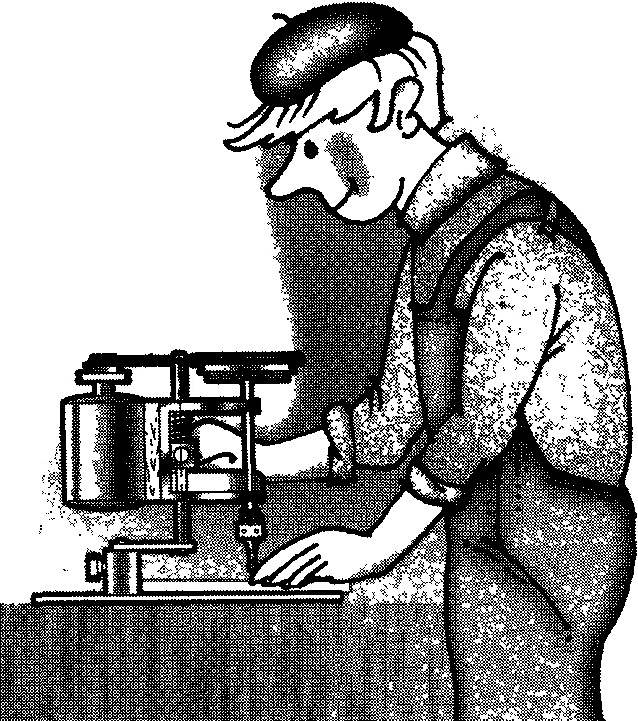
My machine consists of a steel plate sizes 300x200x5 mm, which is welded to the glass screw fixing swivel arm with a vertical column — this allows you to bring the drill to any point of the processed printed circuit Board regardless of its size.
On the counter is put on a bracket with electric motor, pulley and spindle. This node can slide along a vertical pole and return to its original position by a spring, resting on a bronze bushing with screw fixing M6.
The bracket is made of aluminum alloy and is a C-shaped bracket, the upper and lower shelves where you drilled holes with a diameter of 10.1 mm for the upper strut rod and machined the seats for the two bearings. The last is vertically mounted spindle shaft length 150 mm (specify the place) — a steel rod from a rod with a diameter of 6 mm To the bottom shelf of the bracket is adjacent to the stiffener with a hole diameter of 6.2 mm at the handle of the machine control.
In the vertical wall of the bracket done by the three M6 holes for mounting the wooden spacer; it, in turn, is screwed the electric motor drive.
Motor type KD-30 power 50 W (220 V, 2800 rpm) with a paper capacitor 4 µf x 400 is controlled by a micro switch located on a wooden spacer, in the vicinity of the handle.
Circular turns of the strut bracket restricts the flatted cylindrical bronze bushings, turned to its vertical wall. Bracket slides on it when drilling.
On the lower end of the shaft is pressed onto the adapter with Morse taper No. 1A, which is put on jaw-Chuck for drills with a diameter more than 6 mm, and the upper trerosewill driven pulley, made of aluminum alloy. In the upper part to facilitate the selected spherical recess.
A drive pulley coupled with the driven rubber drive belt from the tape recorder, also made of aluminum alloy and has a toroidal groove to facilitate.
When working on your drill press, I am bringing the rotating drill bit to the point where there should be a hole and press the button on the handle. After making a hole, let her go. The spring expands and returns the bracket to its original position, the Drill is removed from the PCB. Thus, a significant part of the load with the hands removed. To drill a hundred holes in these conditions is not difficult.
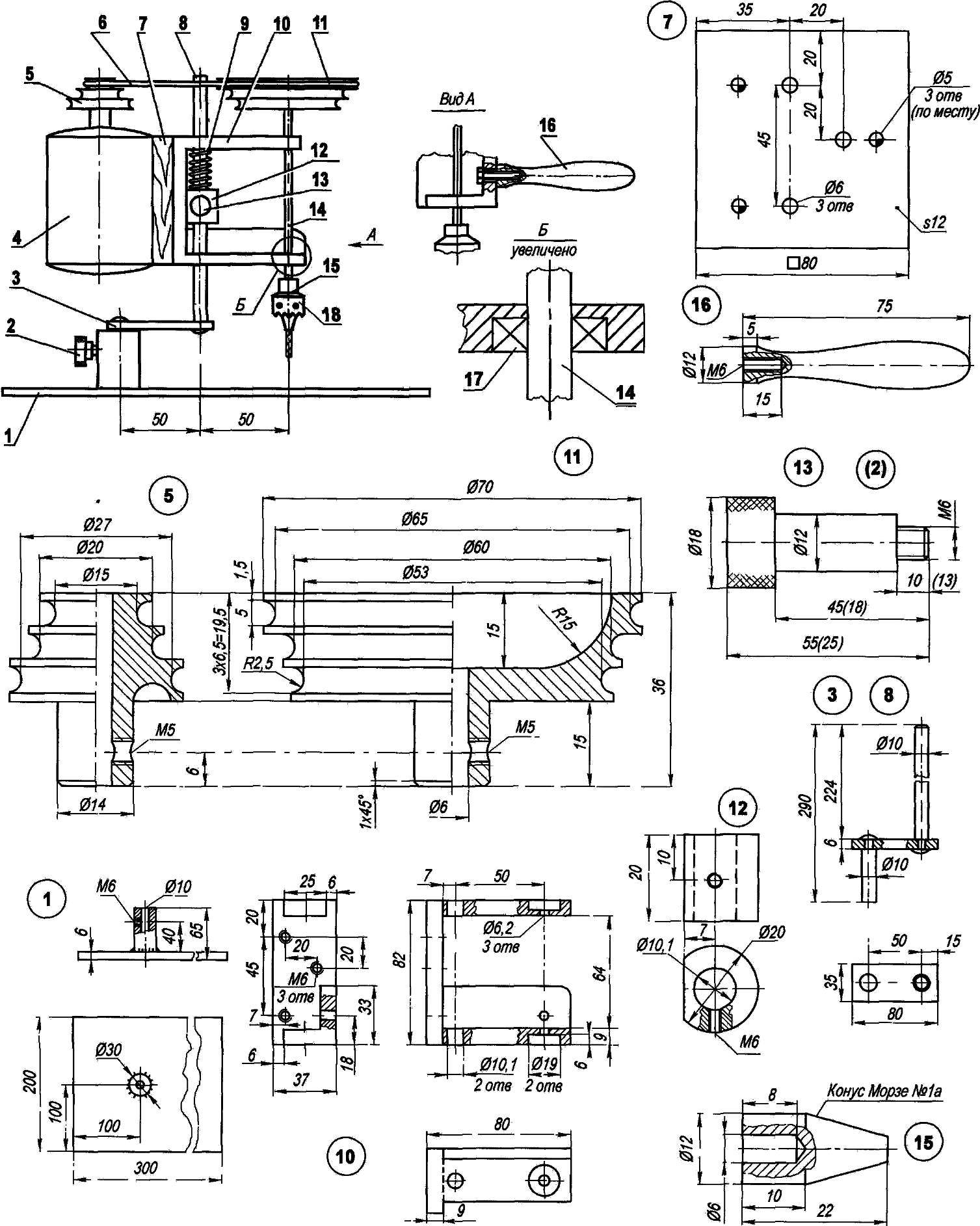
Miniature lapping machine:
1 — table, 2 — screw fixing rack, 3 — arm rack; 4 — electric motor; 5 — a drive pulley; 6 — a rubber drive belt, 7 — wood proseucha, 8—, 9 —spring; 10 — bracket, 11 — driven pulley, 12 — bearing sleeve 13 — screw fixing the sleeve 14, the spindle shaft, 15 — adaptors with Morse taper, 16 — arm, 17 — 26 ball bearing (2 PCs), 18 — cartridge.
C. RYBAS