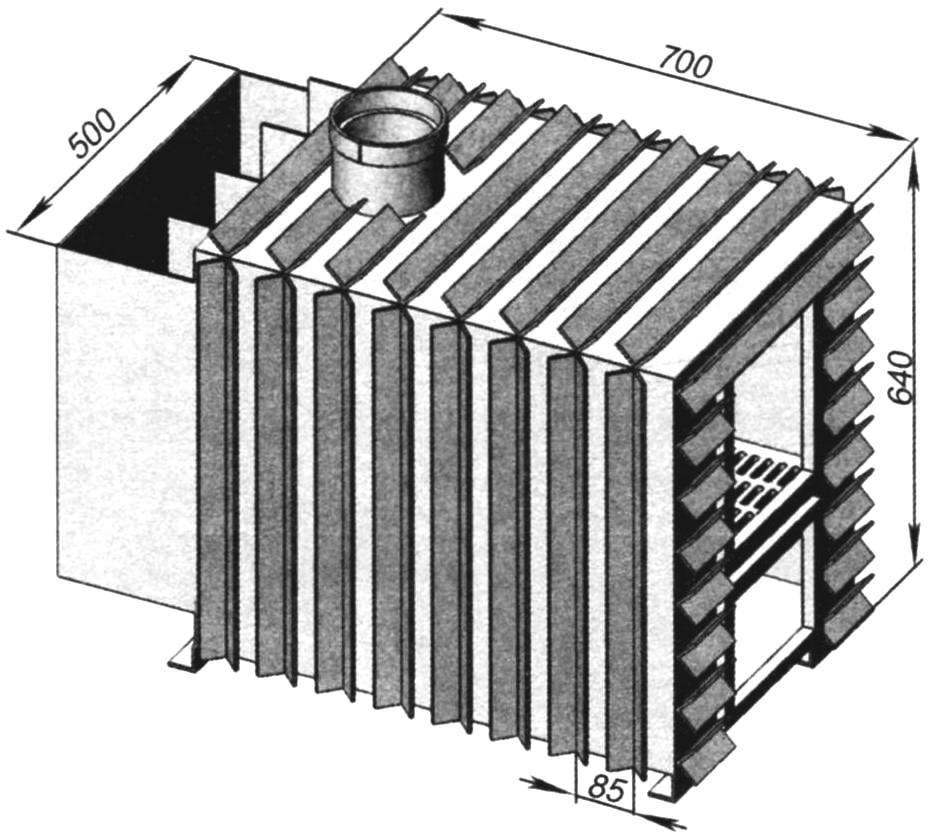
I’ve seen a lot of different types of furnaces and boilers for baths and garages. But I never came across such that (simple and effective) that I made ten years ago. So I want to offer it to the readers of “M-K”, and in several versions.
And the history of the manufacture of the furnace is as follows. In a newly built garage, with the onset of cold weather it took heating. Were available: a small tank of sheet steel 4 mm thick, cuts a variety of metal area and quite a lot of leaves from the “wazowski” and “moskvichova” springs left after the bulkhead, and the replacement cars. “Vazovskie” the springs a little wider – they are a cross section of 50×5 mm, and the “moskvichova” – 40×5 mm.
Since the tank was narrow, and the furnace was planned with a sufficiently large volume of the furnace for the combustion of various scraps of lumber, branches, etc., had him cut in half lengthwise. Besides, the tank was made from a relatively thin sheet of steel – it was necessary somehow to protect him from a fast burn-out, for example, improve heat transfer, the steel is heated to “red” from the 550 °C, the metal begins to soften and hard to oxidize and, in the end, burns quickly.
Based on the foregoing and guided by the goal to increase and speed up the heat, I decided to do an efficient heating stove.
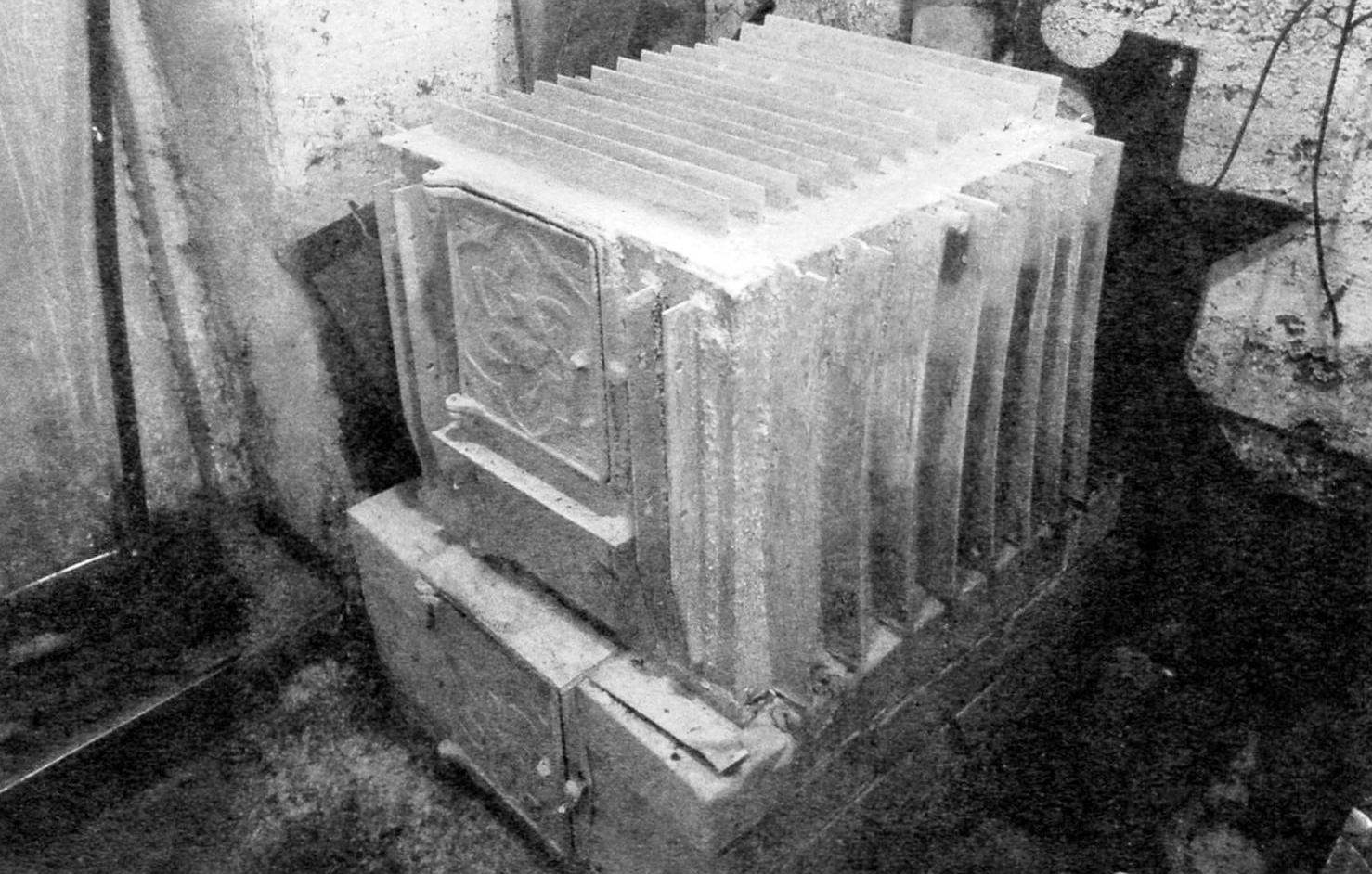
Garage furnace shell steel tank with 4 mm sides, cut in half lengthwise. Openings in the roof and rear wall of the sealed cohesive segments of area No. 5, laid “on the shelf”. The rest of the wall “Gabrini” springs from the car UAZ
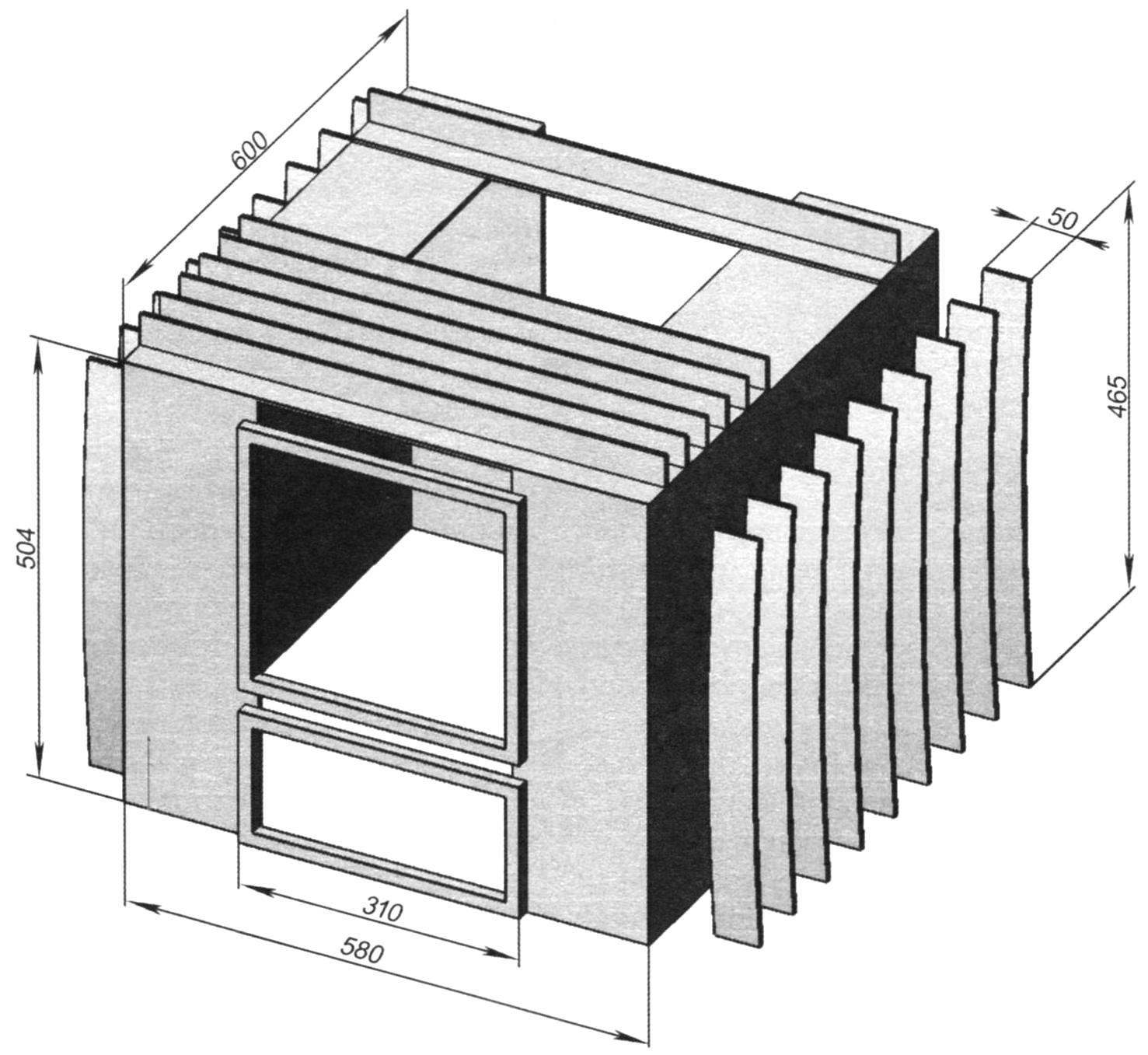
The exact same furnace for the garage in the “semi” (for clarity)
Of course, using an intermediate heat transfer fluid can evenly heat the room in terms of area and volume, but this raises a few problems. First, it is quite expensive and time consuming to pull the pipes for the coolant at the perimeter of the room. Secondly, the coolant has a limited capacity, which increases the time of heating the room. And thirdly, you need to use a non-freezing heat carrier, and in large volumes it is quite expensive. My friend, for example, having a garage heating system, eventually, was abandoned.
It was therefore decided to use as coolant, the air in the room – it is quite a good carrier of heat energy through convection. However some peculiarities, specifically: cold air intake better done from the floor, that is, the heating surface should be as low as possible. So in the bath-the sauna afterwards, I re-installed the furnace so that half are below floor level, for a more uniform heating. Even the furnace must be shielded from flammable wooden walls.
Theory: heat transfer depends on the temperature difference between two environments (the heated metal and the surrounding air) and the square soprikasalis surfaces. And as the temperature of the sheet metal of the furnace, radiating heat energy, we can raise only up to 500 °C, then we may be able to increase the area of heat radiation.
The first method is to make a large oven. But it is irrational. The second is to increase the area of heat transfer surfaces of the furnace. And here is a handy automotive leaf springs, only in a completely unexpected version of the application. They were welded with a continuous weld to the side walls of the oven (better heat transfer). The leaf springs were installed at such a distance from each other to the electrode during welding can be hold at an angle of 45 degrees to form a “proper” weld. If with one free hand to weld the spring does not interfere, then the other side is another, already welded – with a height of 50 mm (or 40 mm – “Moskvichka”). Therefore, the minimum “effort” the distance between the leaves in this case also approximately 50 mm and even a little more.
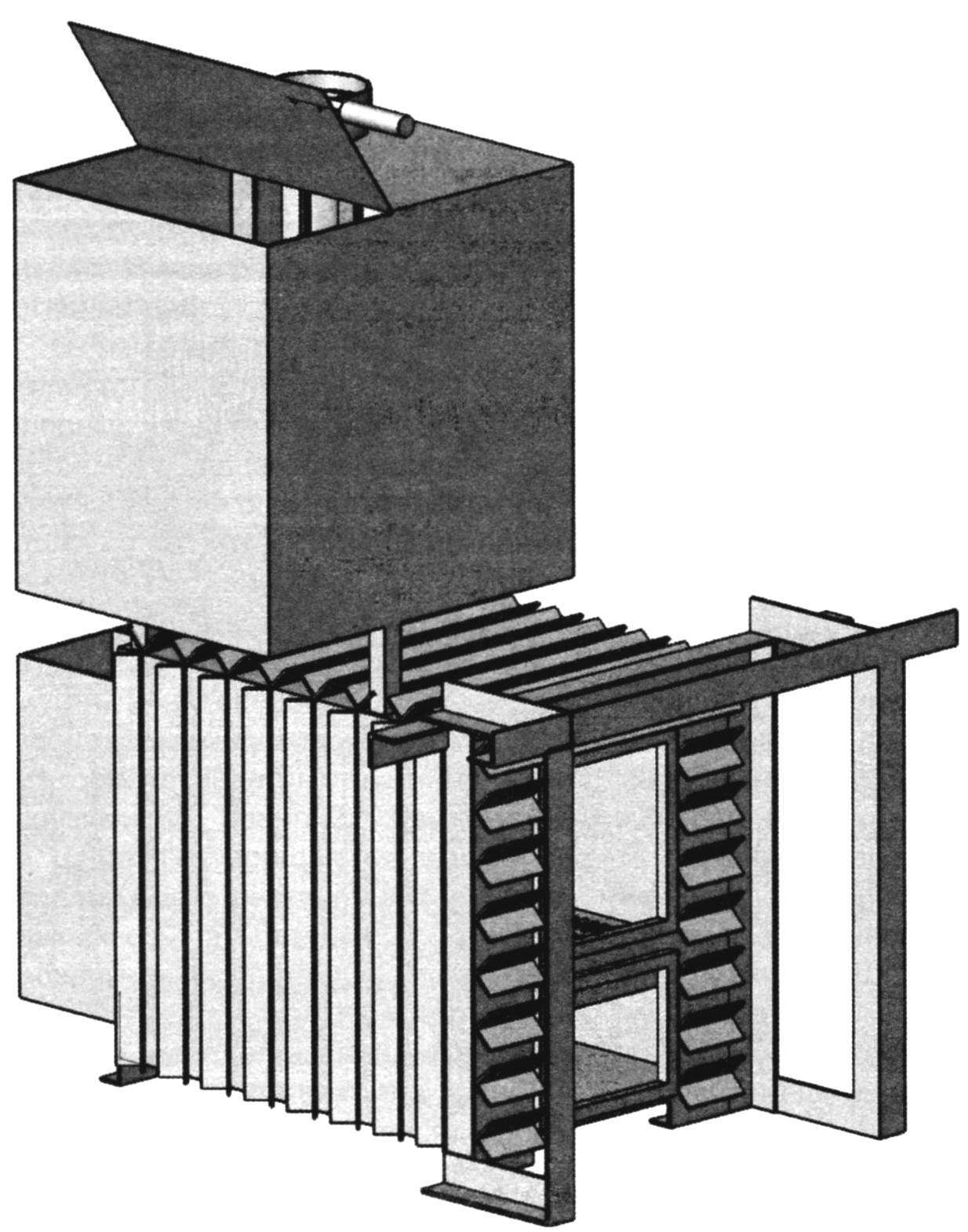
Furnace for a bath Assembly (without doors)
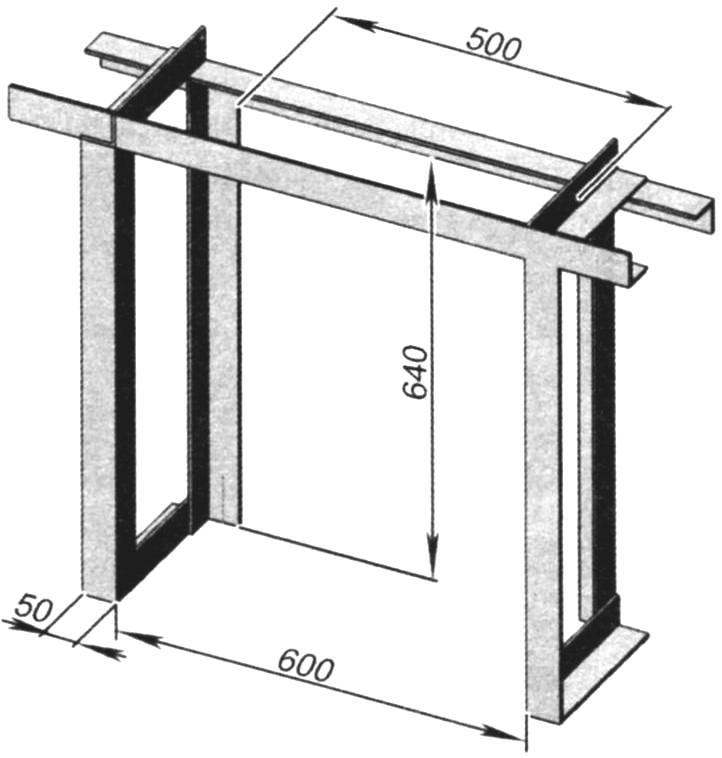
Frame to strengthen the wall between the dressing room and steam room
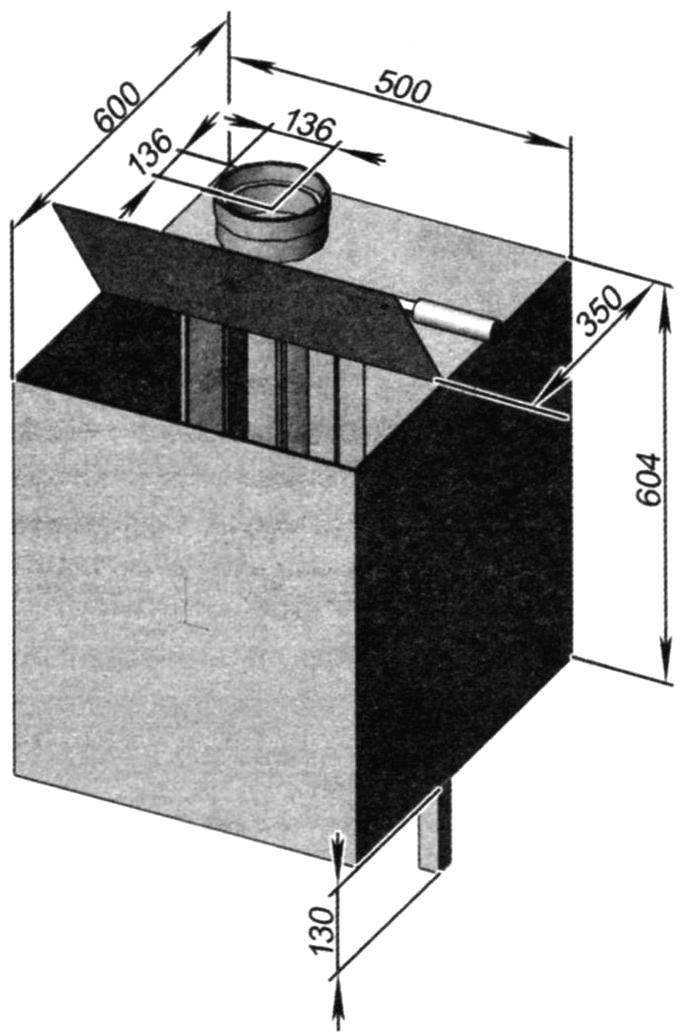
Tank for heating water; set on the stove. The pipe is in the tank “rebreed” to increase and accelerate heat transfer
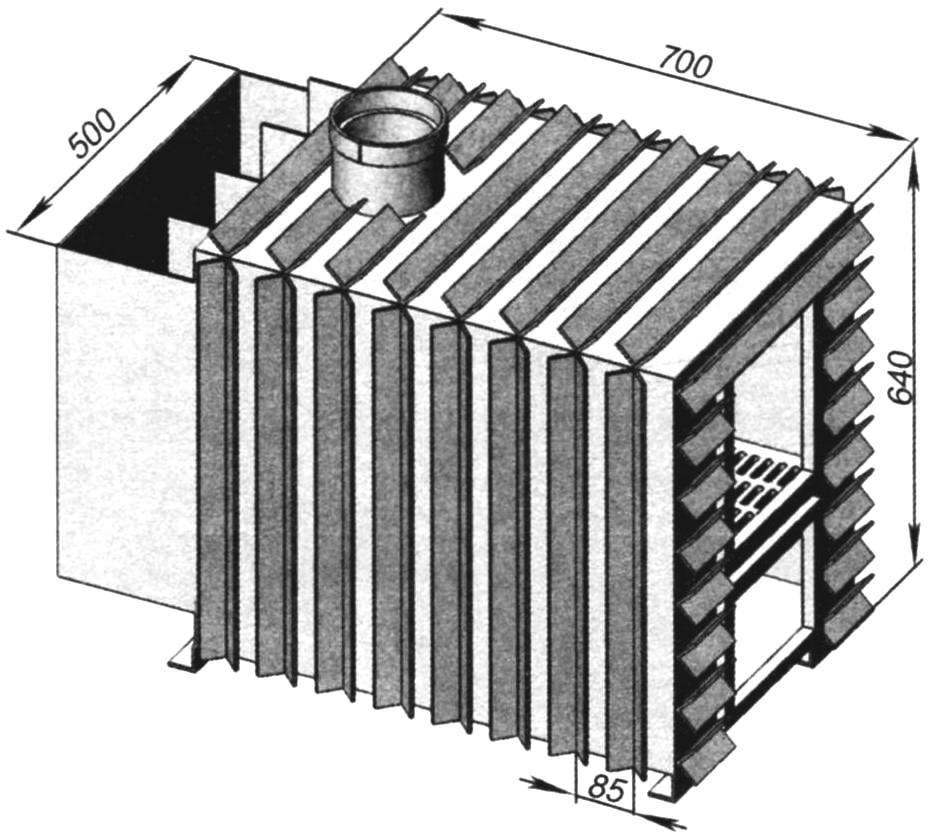
Stove with the “fin” segment of the area No. 4, is welded on edge to the wall surface (the shelf is inclined at an angle of 45° to the surface of the leaf base)
The side wall of the furnace has dimensions 600×500 mm, then its area is equal to 0.3 m2. The area of the nine ribs (excluding the ends) “wazowski springs”: (0,05 + 0,05)x0,465х9 (PCs) = 0,42 (m2). The result is a total area equal to 0.72 m2. And yet – welded bow spring serves as a stiffener and in the case of strong heating of the metallic walls does not allow it to scorch.
After I cut the tank and put the iron frame of the doors in the front, top and rear of the “tank” was formed opening, it had to be something close. Then came another similar idea: to make the wall solid and welded sections of area size 40x40x5 mm (surface area of heat transfer was the same – as in the “fins” springs).
The result is that the same amount of heat energy from combustible fuel in a furnace can increase heat transfer (the amount of heat energy per unit time) – and then the heating rate of the room will also increase.
On the Intro to the article – the very first version of the furnace in the garage. Oven is set on a large brick ash box, so that it as rare as possible and it was easier to rake out the ashes. The ash pit is located above the ash pan, although it violates the General concept of air, it is desirable to raise from the floor. This may open the ash pan door and ash-pit is closed. In the meantime, the need for rebuilding furnaces does not arise. But in this not quite “right”, it has a pretty decent heating features: after a long break, the garage area of about 80 m2 can be melted down for 2 hours – 3 at room temperature even in sorokogradusnuyu frosts.
In the future, after the construction of baths, there is a need to produce and for her stove, only with a tank to heat water. Operation of the furnace in the garage showed the correctness planted the idea, and so decided to use it here. They only needed to “adjust” basic dimensions. So different types of fuels in a furnace are very uneven. Example: wood can be a length from 40 cm to 60 cm, coal is also filled with different (but preferably away from the walls of the furnace). And then, having estimated the area can hold four buckets of coal (about practice) for the furnace, determined by the width and depth of the furnace (dimensions should be take with a small margin). The height of the furnace may be different (within reason), depending on the available material. In practice, all the coal was loaded, there can be a couple of times during the operation, and that in severe frosts. As a result of staying on the following dimensions: furnace itself 500x600x700 mm (serenajwilliams) plus podvarennoe from the back (rear) of the furnace wall pocket stones dimensions mm. 500x200x500 Looking ahead, I note that the furnace can be slightly shortened, and a pocket of stones is also reduced. I almost never use (90 – 100 °C in the steam room – risky to health).
Now on the furnace design.
By this time, I still had a stock of springs, sheet 4 mm thick and rolling area size 50x50x5 mm. That this material was used in the case. Fox-the welded base, consisting of walls (side and back pair), floor and roof. From the same sheet welded tank for water heating. The rear wall “gebril” springs, and welded pockets for stones. The front wall was performed with two openings (one above the other): fire doors and blew. The internal sides of the side walls welded to the longitudinal lodgements from corner No. 4, for the subsequent laying them on the grate. After this “gebril” springs and the rest of the wall, and emerging from the furnace outlet to the chimney pot covers – steel strips of the same section. For ease of welding necessary to make the distance between the ribs a little more than their height, thus “anterograde” properties and rigidity of the walls of the furnace, of course, reduced. When using firewood, it’s not scary – I never failed to heat the oven with “fins” springs from “the Muscovite” at least until brown glow. But of course in chemistry it is known that with increasing temperature the rate of chemical processes (oxidation, and as a result burnt walls) increases.
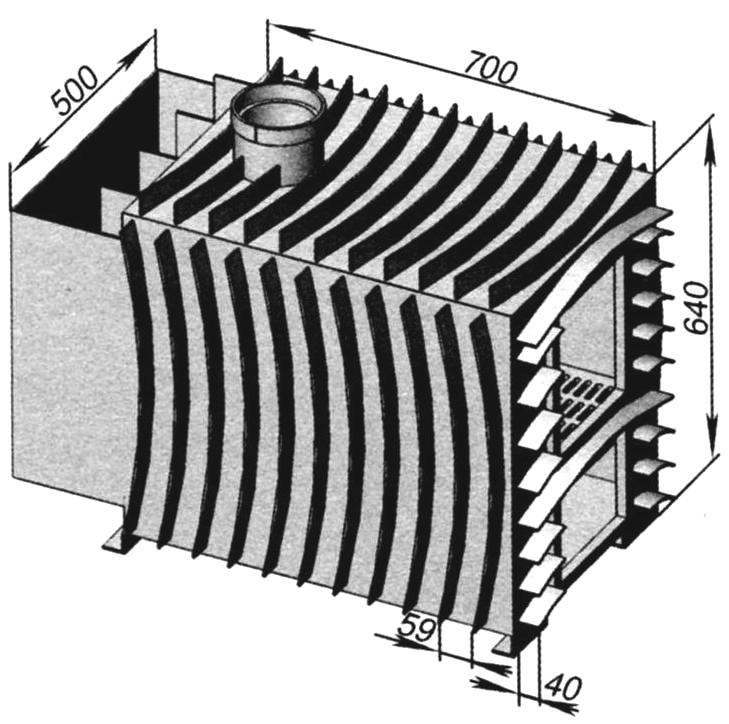
Furnace-based steel sheet with the “fins” of the springs from the car “Moskvich-412”
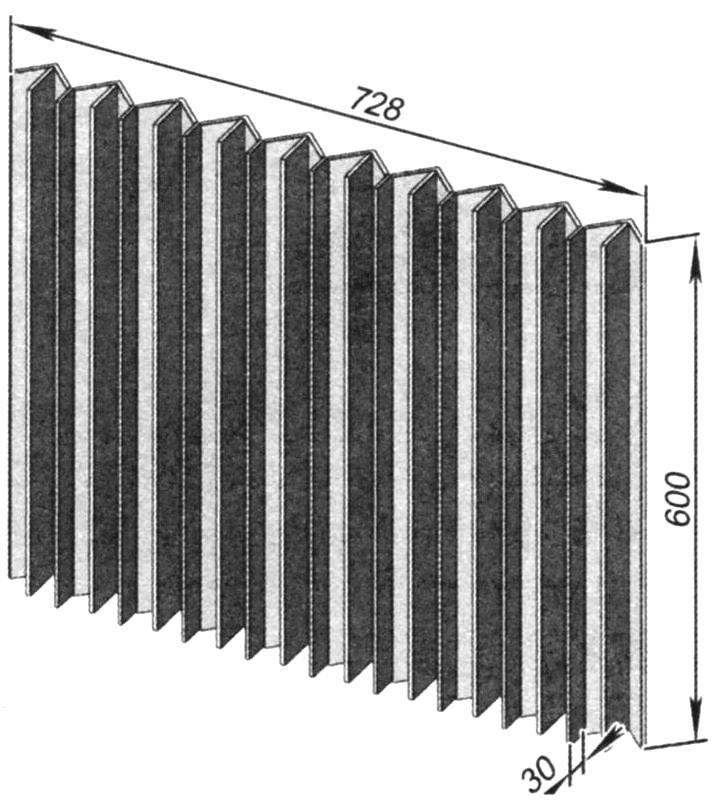
Quite an interesting use of the area 40 mm or 50 mm “accordion”, increasing both internal and external surfaces of the walls. To increase the area of heat transfer walls in the inner corners of “bunching”, you can weld it strips with a width of 40mm. For even greater efficiency – welded to the outer corners of the strip with a width of 30 mm. will Definitely try something like this to cook!
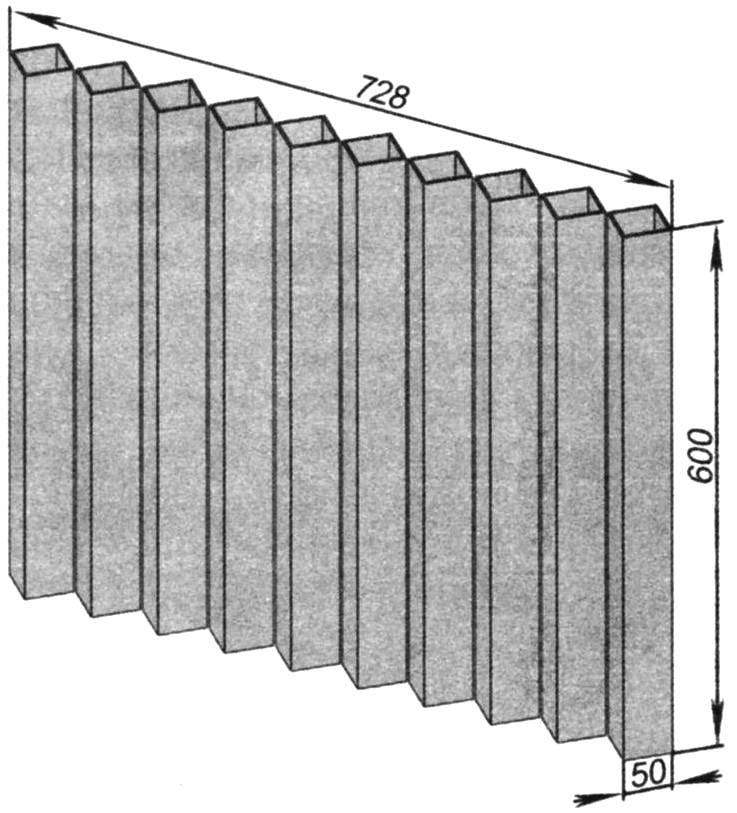
The use of shaped tubes secanim up to 40×40 mm for the walls of the furnace or boiler
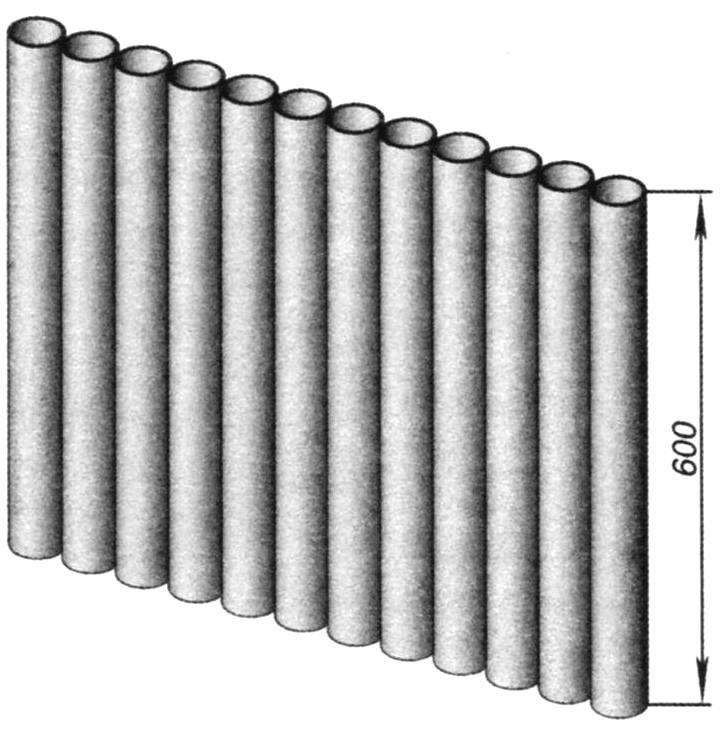
The use of round pipes up to 40 mm in diameter, the walls of the furnace or boiler
The grate, and the door frames of the furnace and blower, bought ready. These items are cast iron. The prison, however, the installation had to be sharpened to match the perimeter of the “grinder.”
The furnace in the bath was planned to be positioned so that the front wall with the doors, heat the dressing room, the left wall is the sink; and the right, top, and rear of the steam room.
Here’s a furnace was using leaf springs from cars UAZ and “the Muscovite-412”. Instead of springs you can, of course, to use the metal strip cross-section 40×5 50×5 mm or mm. Strip, in contrast to springs which have bending, suitable even for “finning” of the cylindrical surfaces.
Not everyone who wanted to make a similar oven, is available spring. So I decided to give drawing furnace with “fins” not scarce steel area.
The figure shows just such a stove, with a welded base (walls, roof) sheet 5-mm steel, which is then “strengthened” or rather, “gabral” area size 50x50x5 mm, welded on edge to the base (shelf corners thus located at an angle of 45 degrees to the base – sheet walls or roof).
Ash pan furnace (the gap between the floor and the grate) is about 1/3 of the volume of the furnace. However, this size is preferred when burning in a furnace of coal, wood the ash pan is enough to do in 1/4 of the volume (from the combustion of coal ash is bigger than that from wood). When filling the ash pan to a certain extent the thrust is reduced so you can’t do too little ash and often it is cleaned.
Furnace for a bath made with a raised floor bottom (with legs), underneath pass “ventilation” of the room bath. Fresh dry air passing under the bottom using a kind of “window” formed between the legs of the furnace, is heated and passes into the steam room, “airing” it.
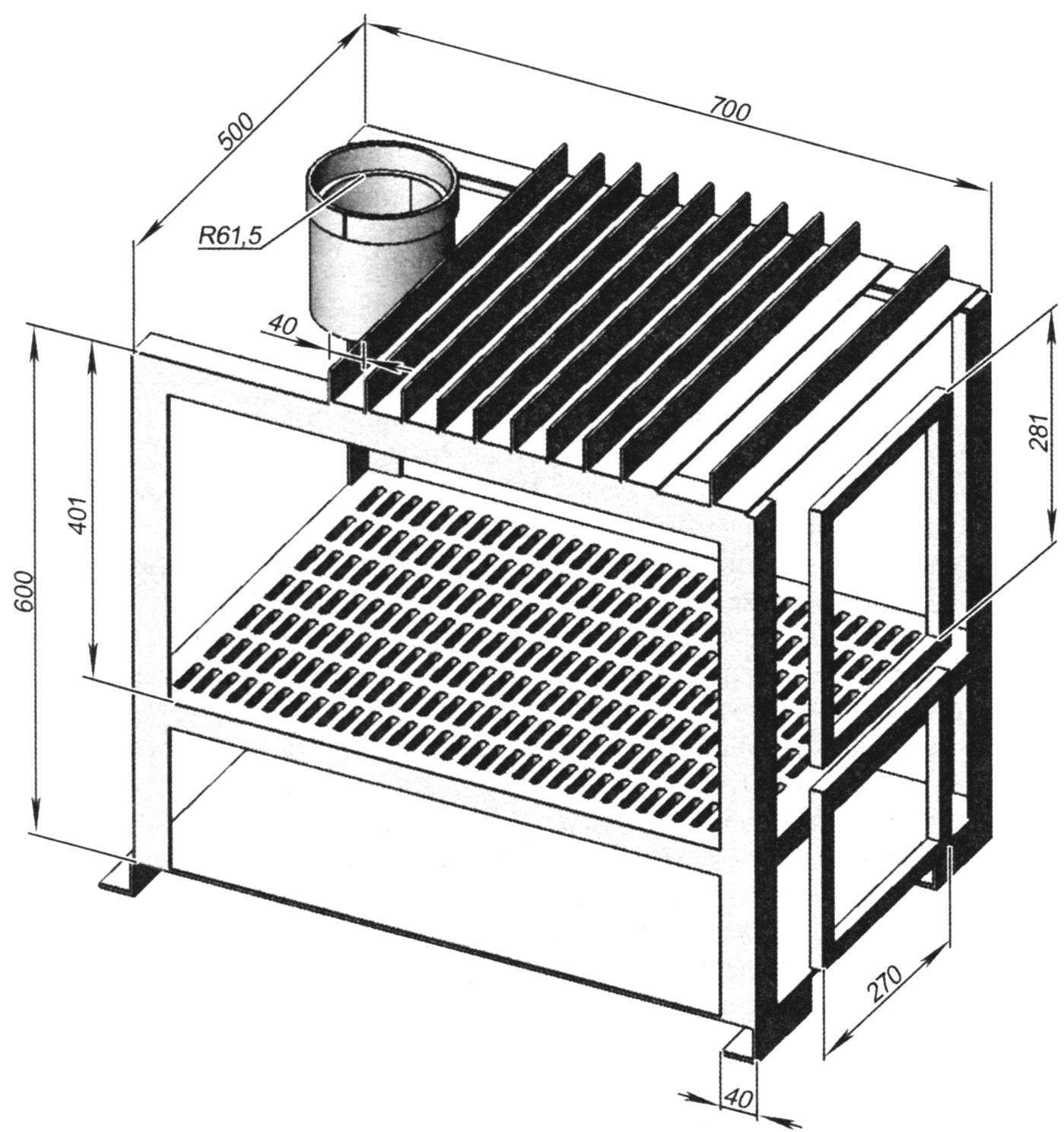
The production version of the frame of the furnace area and welding to it “reinforcing” elements
Notice. Installing a furnace or boiler in the garage, legs and even the bottom is better not to do (in order to avoid falling under the boiler anything flammable), and mount the heater directly on a concrete base.
A chimney for a furnace is a steel pipe with an internal diameter of not less than 120 mm (but not more than 150 m). Otherwise, if you make it smaller, it will be delayed soot, but if a larger diameter is formed too powerful a pull and most of the heat will stay in the black. Interestingly, the longer the chimney, the more it is necessary to heat and more soot is formed on the cold pipe. According to various sources, at the end of the pipe, the chimney, the smoke temperature should not be less than 95 degrees. Before garage furnace had a chimney with a diameter of 107 mm, and it had a lot of problems: it kept “saakshvilis” soot and it had to be clean. Tried the same chimney to insulate – did not help. The result had to replace and put a larger diameter pipe. Sometimes in the fireplace is the gathering of a small amount of soot on the down pipe, and thereby it is possible to overlap the chimney, which is very dangerous due to the ingress of carbon monoxide in the bath! So you need to make the pipe straight, without elbows and ledges – this will prevent overlap of the chimney, leaving soot will fall directly into the furnace and burn up. Still for the same reasons the pipe must be same diameter all over.
Using the accumulated experience, I believe that the issue of the chimney pipe to the furnace to do the same should not be, because it will serve as a screen, scattering of thermal radiation inside the furnace and continuously heated red-hot, in the end, just “burn”. And the issue will contribute to the “exit” of smoke through the door when you ignite fuel. If the chimney is done correctly, the smoke coming from the chimney, the combustion process should be almost colorless or have a slight grayish-blue tint. This is a sign that the fuel burns completely.
The tank has a volume of about 170 liters Of operating experience – less volume of water leads to its rapid boiling, which increases the humidity in the room and very awkward to type hot, and sometimes even boiling water from a half empty tank.
The heating element in the water tank serves as the output part of the chimney with a wall thickness of 10 mm. the pipe is welded ten steel strips cross-section of 50×5 mm – they accelerate the heating of the water, and on the other hand, are more evenly distributed heat, which in itself should increase the life of the pipe. Let me explain: in contact with water additives non-alloy stainless hot metal very quickly oxidized, and because even a thick-walled tube is long. Therefore proveribal steel strips from the bottom to the top of the tank. After almost ten years of constant use, this pipe is in good condition, however there are signs of corrosion. In this tank the water is heated in winter to a temperature of 80 – 90 °C in about two hours. However, due to the presence of stainless metal to make him a tank is preferable, as it is not oxidized.
Buck shifted so that the heating pipe was in the far corner. Probably heating the water in the tank because it gets a bit slower, but easier to approach (up to the furnace still distance) and scoop up the water.
The tank has a lid, it is attached by two small loops and does not allow water to evaporate. Cover made of stainless sheet steel 1.5 mm thick. Previous cover was made of galvanized steel of 0.5 mm sheet, but it’s “eaten” by the corrosion. The properties cover special! Open -it converts a dry sauna in a Russian steam bath with high humidity. Cover handle located on the side, as if opened from the tank to the hot steam comes out. The handle is stretched a piece of rubber hose for insulation.
Tank is installed on the stove at three points of support: one – tube passing through the tank, two other podvarennoe on the sides of the tank and hit the edge of the pot. And since the oven has edges of rigidity, a heavy tank does not affect the ductility of the walls of the furnace at high temperature.
Furnace itself is mounted in a specially made opening the wall between the bath room and dressing room. In the opening pre-installed fortifying the portal, having dimensions of the width of the wall and the “front” of the furnace. Pay attention to the fact that the area size: 50x50x5 mm, which is welded to the portal, from the furnace is located so that it can be inserted oven.
As a family cook asked a similar boiler and them in the bath. Then I decided to “estimate” how else can “enhance” the boiler-these options were many.
Of course, boil of the individual elements of finned surface – works great, but it’s worth it. First (now from experience), high speed of warming up of a room, which in itself is nice when using. Second, the oven or in the bath or in the garage for a long time use is not burned, the walls are not “led” temperature, moreover, are very rarely part of the walls is heated to the brown “glow”, and it’s easy to eliminate – reduce the air supply to the furnace.
For fun, drowned in the bath in the cold – about 43 °C, and nothing is hot! Recently put advanced, for fun, an experiment: when cold on the street all week (minus 22 – 24 °C) in just two hours heating with coal, the air in the bath, as well as the water in the tank is heated to a temperature of 90 °C. For reference, the external dimensions of the bath – 4x5x2,4 m; wall thickness 0.3 m; (made from slag), ceiling insulation – boiler ash layer of about 0.25 m And in summer the bath is heated very quickly: in less than an hour.
A SUMMARY TABLE OF THE CALCULATED PARAMETERS
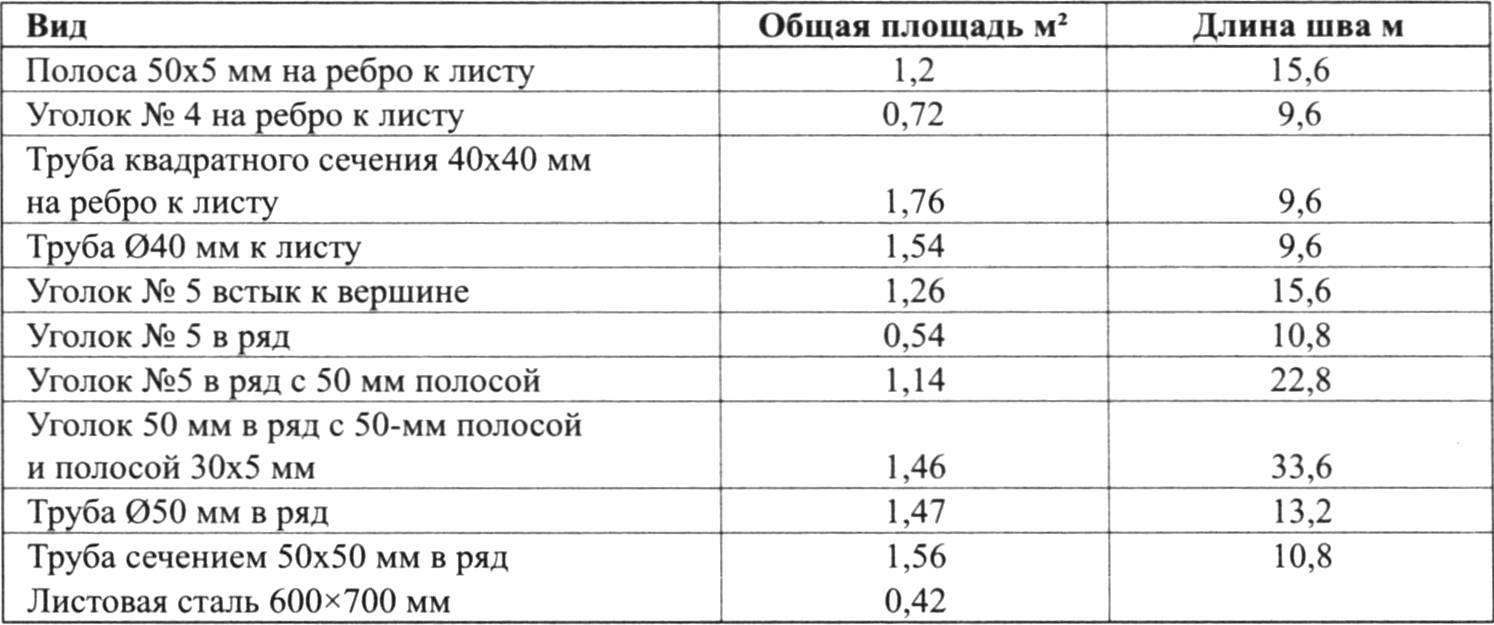
I believe that the use of old automobile springs on the walls of the boiler are preferable because of better “anterograde” properties, compared with the area on “the edge”, construction rebar or steel strip to the steel sheet. An additional positive point is the fact that the various springs, or area today, it’s easy to find or inexpensive to purchase, which in itself will reduce the cost of manufacture of the boiler, and if you use the method of welding area in a row (or circle), then save the sheet when welding steel furnace or boiler. It is also necessary to say that the boiler with the “fifties” area on the edge of the sheet turned out to be less successful, it was necessary to use the area on the edge of a sheet of steel is only 40 mm so that the distance between the tops of the “amplifier” was not more than 50 mm. Can be “reduced” and the size of the furnace to 600x600x500 mm, and a “pocket” under the stones to reduce the size 400x500x200 mm and pull down. Yet, of the revealed shortcomings: the iron door of the boiler temperature sometimes burst, apparently, and they must be made of sheet steel with “amplifier”, using the same technology. And the next time the need arises, after all, cook stove or boiler “angled design”.
Recently, steaming in the bath, pointed out another useful feature of furnace: the furnace in the dry mode (which he used most often) wood, which is sheathed inside the bath, does not swell from moisture, does not warp, rot, and even better preserved.
Finally, I also want to wish all the readers of the journal easy couple to be healthy and have success in the technical work – in a warm garage.
D. ELEPHANT, R. p. Rodino, Altai Krai