The advantages of this car are structural simplicity, reliability on the road and high cross-country ability. It was built by Stanislav Khopshanosov from Yerevan.
Residents of the capital of Armenia love cars and know a lot about them. We were convinced of this by trips through the streets of Yerevan with ErAZ design engineer Stanislav Khopshanosov on his homemade all-terrain vehicle. Wherever we stopped, curious passers-by immediately gathered around. The inevitable questions in such cases followed: what? How? from what? Stanislav answered patiently. In the three years since he first drove his new car, he had become accustomed to such “press conferences.”
I especially often had to talk with amateurs in 1983 during the traditional run of home-made cars. The all-terrain vehicle, which ultimately received the first prize, invariably became the center of attention in parking lots throughout the entire run.
Cosmonaut Vladimir Dzhanibekov, who traveled with the convoy most of the way and sat behind the wheel of almost all home-made vehicles, said about it: “Comfort, breadth of visibility, beauty!”
But S. Khopshanosov gained even greater popularity from the television program “You Can Do It,” dedicated to homemade transport. At the request of TV viewers and readers of the Modeler-Constructor magazine, we talk about the design of his all-terrain vehicle.
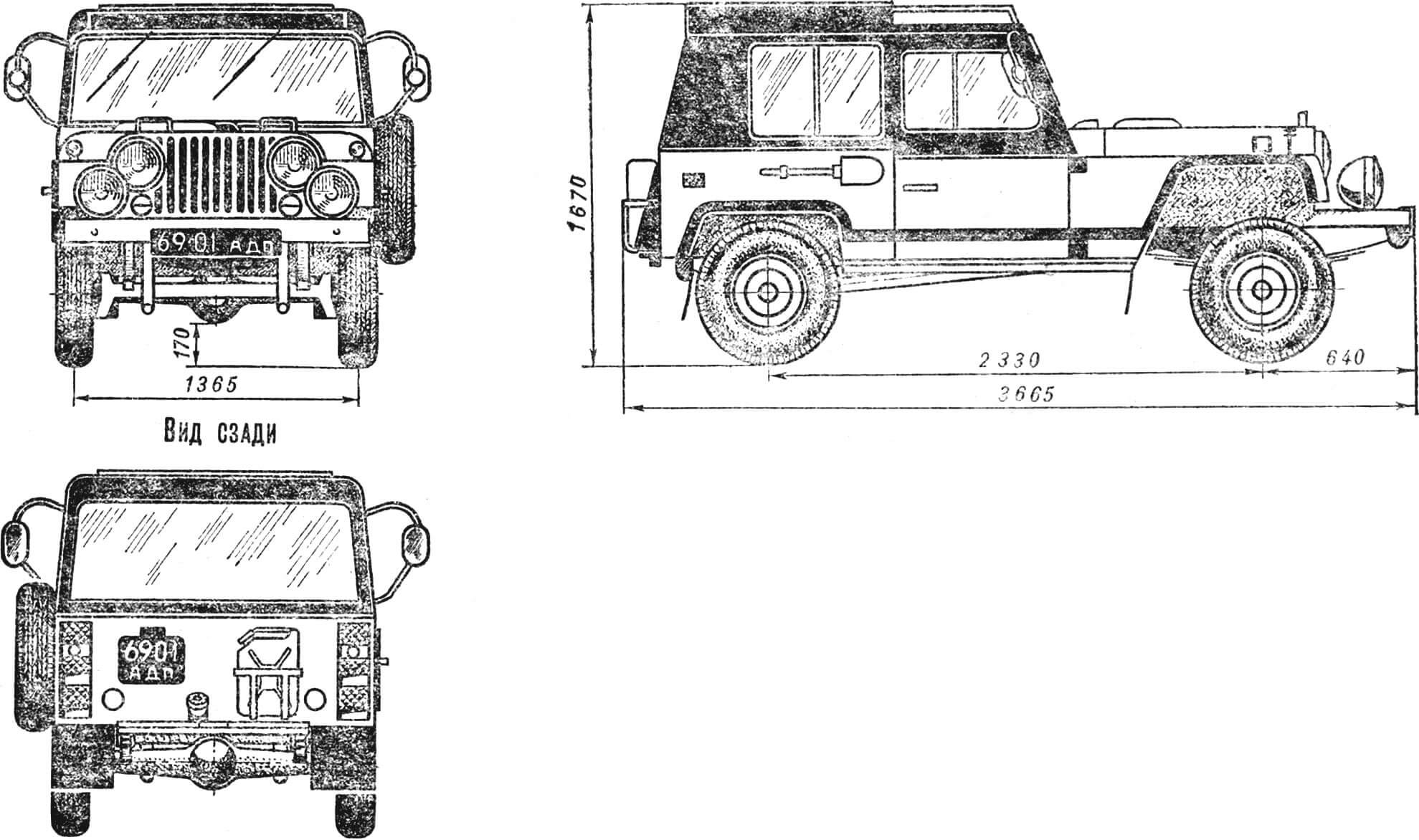
When conceiving a car for travel, Stanislav decided to include in it design simplicity, reliability in operation, unpretentiousness and ease of maintenance. When choosing a layout, I settled on the “jeep” design, but its version differed from the classic one in that it had only one drive axle – the rear one, for simplicity.
Externally, the “jeep” looks smaller than, say, a LuAZ, although it is not inferior in size to the interior and trunk. This is achieved, firstly, by the dense “packing” of the engine compartment and, secondly, by the external placement of part of the luggage (on the roof), a spare wheel (on the left side) and a canister (at the rear). Total weight – 900 kg.
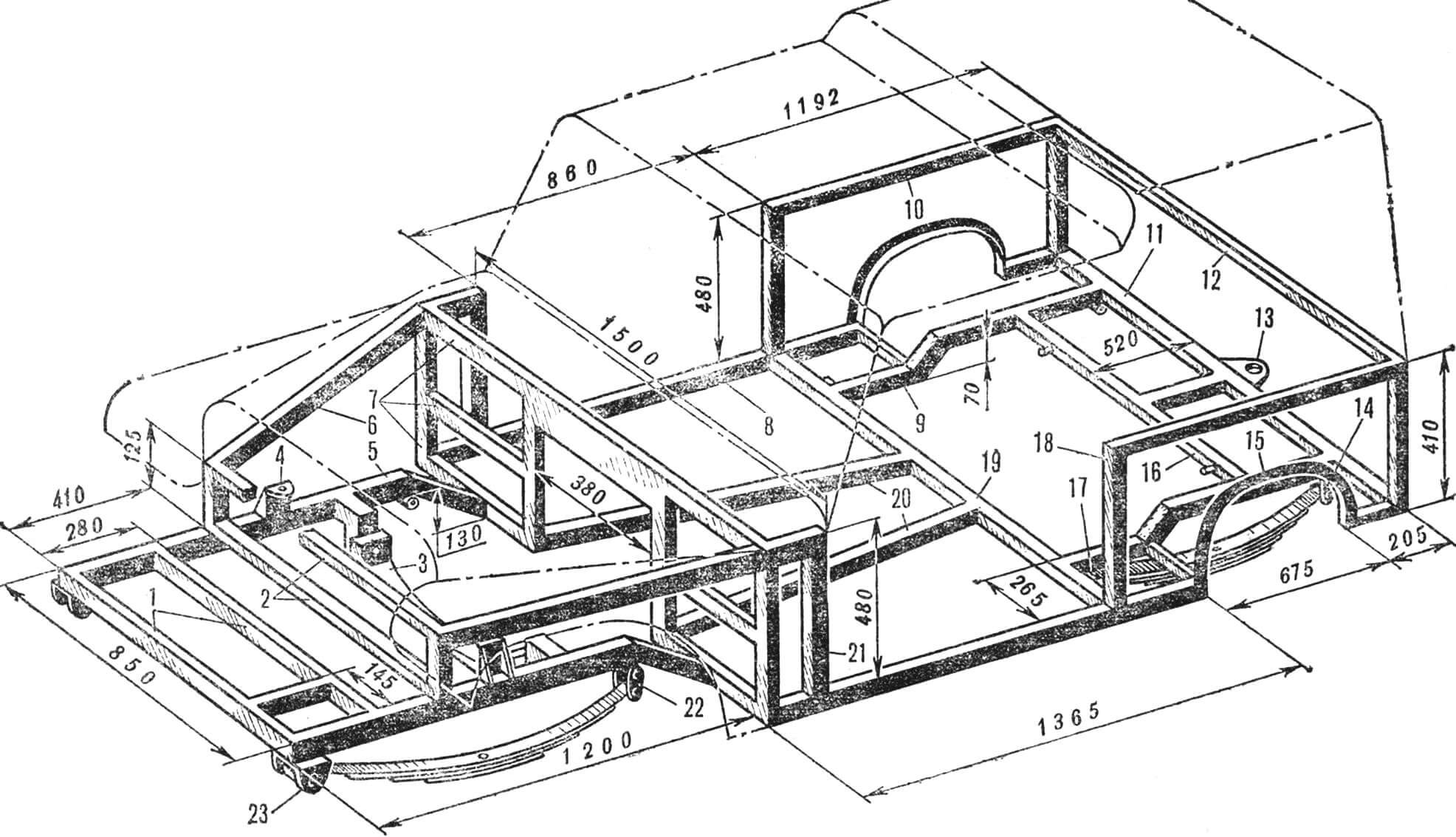
1 — front beams (50X25 mm), 2 — elements of the front wall of the engine compartment (50X25 mm), 3 — engine mounting cradle, 4 — shock absorber bracket, 5 — front spar (50X50 mm), 6 — hood beam (40X40 mm ), 7 — elements of the rear wall of the engine compartment (50X25 mm), 8 — threshold (50X25 mm), 9 — rear spar (40X40 mm), 10 — side (25X20 mm), 11 — rear cross member (40X40 mm), 12 — window sill crossbar (25X20 mm), 13 — trailer bracket, 14 — rear spring shackle, 15 — rear wheel arch (angle 25X25 mm), 16 — intermediate cross member (40X40 mm) with shock absorber mounting pins to the body, 17 — rear spring bracket, 18, 21 — door pillars (40X40 mm), 19 — front cross member (40X40 mm), 20 — struts (50X25 mm), 22 — front spring shackle, 23 — front spring bracket.
The simplifications, however, did not affect the driving performance of the car. Built in 1931, it has covered approximately 150,000 km. Every year, trips were made on it from Yerevan to Moscow and back. Last time with a homemade trailer-dacha weighing 500 kgf. Participation in the rally made this journey much longer. However, the design passed the test of the roads of Karelia and the Kola Peninsula with honor. The Jeep confidently walked both on the highway (at speeds of up to 120 km/h) and along a broken track.
It used to be that S. Khopshanosov helped stranded fellow motorists by pushing their cars with the front bumper of his all-terrain vehicle.
In his native Armenia, he climbed on it to a height of up to 3000 m above sea level, overcoming off-road conditions, rocky screes, and slopes of up to 30°.
The hardships of the journey are easily tolerated in the comfortable and cozy interior of the car. In hot weather, you can slide any of the four side windows to bring in fresh air. Or, if that’s not enough, open the sunroof.
There are many other simple and original design solutions in the car. Here, for example, is how the body works. It consists of a space frame and outer skin. The frame, designed to withstand significant torsional and bending loads, is welded from square and rectangular steel pipes. The less loaded hood, doors and rear window are made of channels, tees and angles connected with rivets.
The floor in the cabin and the hood trim are made of corrugated duralumin sheets 2 mm thick. The body trim is made of smooth sheets 1.5 mm thick. They are attached to the frame with M5 screws with countersunk heads. The joints of the sheets are hidden by rubber and metal overlays.
The inside of the cabin is lined with a thin layer of foam rubber and soft plastic. Triplex glazing, as well as the doors, are equipped with rubber seals from cars from the Volzhsky Automobile Plant. The floor is covered with rubber and synthetic mats. All this reduces the noise level in the cabin and prevents the penetration of dust.
The instrument panel and glove box are homemade. The front seats with reclining backrests are “Zhiguli” ones. The rear passenger seat, designed for three people, is homemade and has a fixed backrest. Behind it, at the bottom, is a fuel tank with a capacity of 45 liters (from a UAZ) with a neck leading outwards above the rear bumper. Above the tank there is an internal trunk. Access to it through the rear window.
The principle of “simplicity plus reliability” has also extended to the power plant: the engine and gearbox are taken together with the units that serve them from the Zhiguli VAZ-2101. Only the paper oil filter was replaced by a cheaper inertia filter from the ZAZ-968.
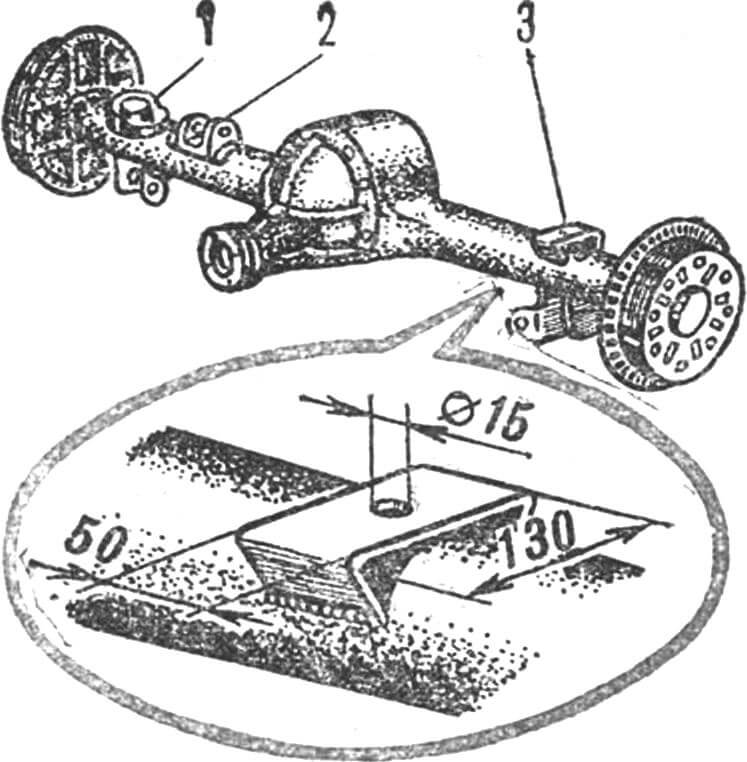
1 — lower support cup of the suspension spring (removed. Instead, a spring cushion is welded), 2 — mounting bracket for the upper reaction rod (removed), 3 — left spring cushion (welded).
The rear axle, taking into account the possibility of towing a trailer, was taken from the VAZ-2102 and slightly modified: the lower support cups of the suspension springs and the mounting brackets for the upper reaction rods were removed. Instead, two U-shaped suspension pads are welded to the bridge beam.
The springs are used from the front suspension of the UAZ-469 car. Each package consists of five sheets, coated with graphite lubricant before assembly. They are suspended from the body frame in the area of the rear side members.
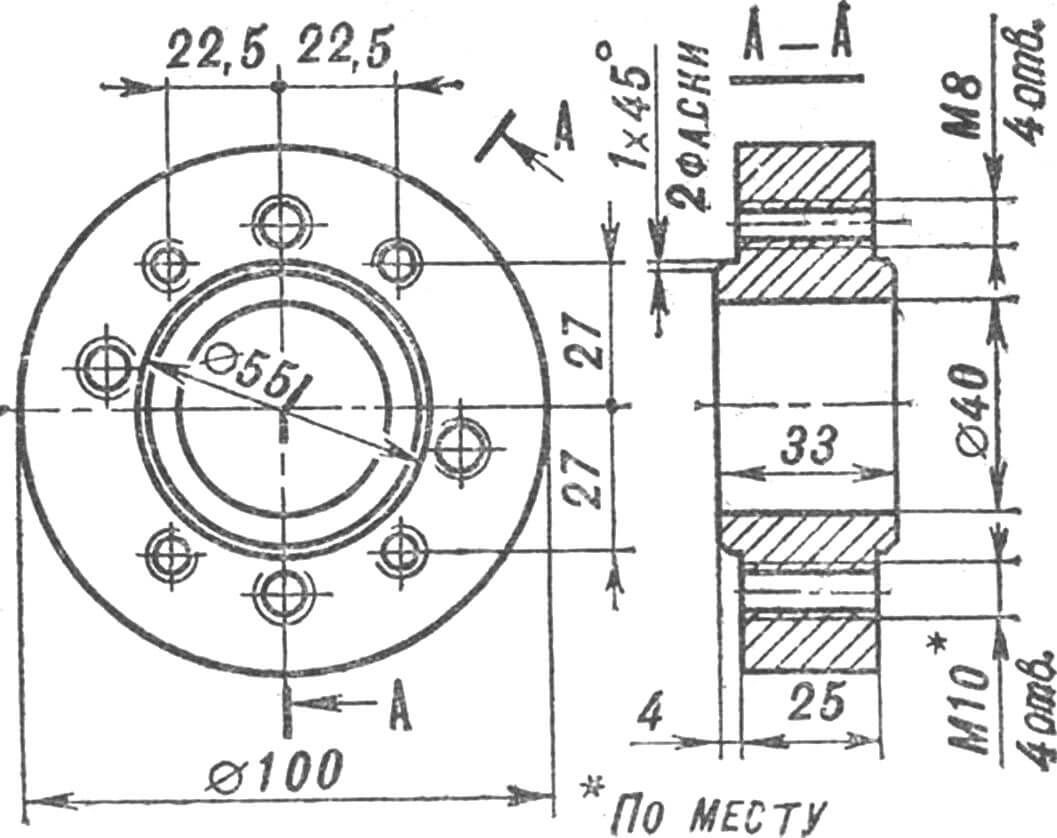
In addition to springs, there are telescopic shock absorbers. With rubber-metal hinges of the tanks, as on the Zhiguli, they are attached to the rear axle brackets, and with casing hinges – to the pins on the intermediate cross member of the frame.
Torque from the engine to the rear axle is transmitted by a driveshaft from the Volga GAZ-21. The choice of this particular type is due to the fact that it is simpler and more reliable and does not require special care. True, the mounting holes do not coincide, so adapters are machined to attach the shaft to the flanges of the gearbox and axle.
They are steel washers Ø 100 and 33 mm thick, in which eight through holes are drilled. Four, corresponding to the holes in the flanges, have M8 threads, the rest – M10.
The cardan shaft is shortened – after measuring the distance between the adapters, it is installed in the centers of the lathe and trimmed: at the place of the existing connection of the pipe with the rear fork and at the place of their future connection. The excess was removed, and the parts were welded at four points, and after checking the shaft for axial runout, they were finally welded.
As for the front axle, it is completely homemade. When designing it, Khopshanosov was guided by his favorite principle of “simplicity plus reliability.” The line of reasoning was something like this: the front axle is a very important unit. It provides motion control; the “health” of the entire car depends on its “well-being.” Therefore, the fewer parts and moving joints it contains, the better.
Three years of operation have shown that the decision was made correctly. Whatever stones and potholes fell under the front wheels – nothing mattered. This is how the bridge works.
Its main element is a thick-walled seamless steel pipe Ø 60 and 1100 mm long. Spring cushions, shock absorber mounting pins and support pads for the ball bearings of the front suspension are welded to it.
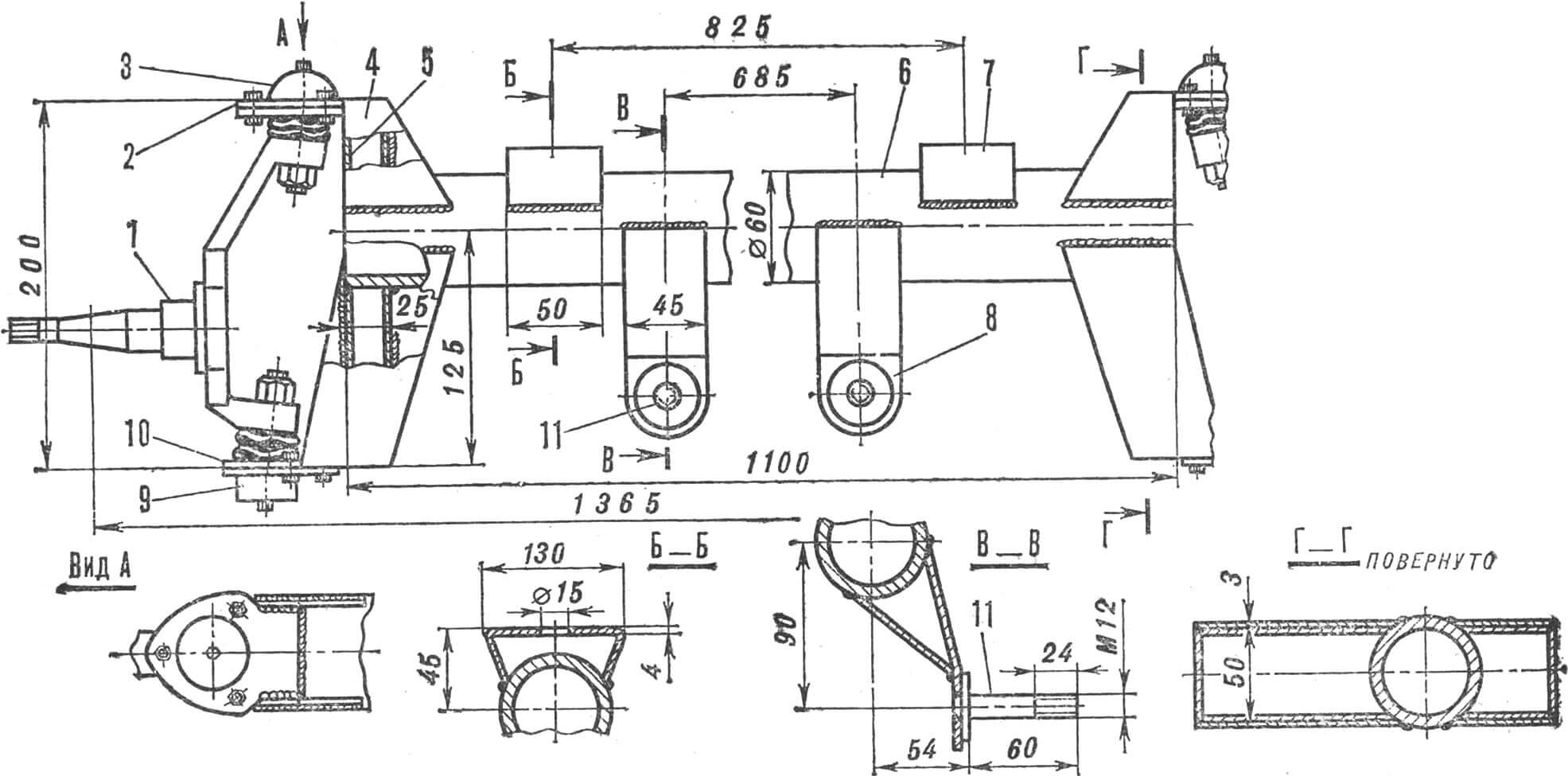
1 — rotating axle, 2 — upper support platform, 3 — bolt and upper ball bearing, 4 — lining, 5 — pipe 50Х25 mm, 6 — main pipe, 7 — suspension platform, 8 — shock absorber axle bracket, 9 — bolt and lower ball bearing, 10 – lower support platform, 11 – shock absorber trunnion.
When assembling the front axle, it is necessary to take into account the camber of the wheels, so the support platforms were attached to the pipe in a certain order. First, the lower ones were welded and the (also lower) ball bearings of the steering axles of the Zhiguli wheels were screwed onto them. The upper platforms were first attached to the corresponding ball bearings of the steering axles, and then welded to the pipe. Moreover, the camber angle was 0°20′ – 0°30′, which corresponds to a 2-3 mm difference between the dimensions taken from the edges of the wheel rims to the vertical (the pipe is horizontal), and was set using a plumb line.

1 – hatch, 2 – handle, 3 – guide, 4 – roof, 5, 6 – gutters.
The front axle is attached to the body frame in the same way as the rear axle – with springs (four leaves in a package) using bolts and clamps and telescopic shock absorbers, the rods of which rest against special brackets on the front side members.
The toe-in of the wheels is adjusted by a steering rod (from the Volga GAZ-21).
The all-terrain vehicle control device is also very simple and reliable. By turning the steering wheel, the driver, through two shafts and two hinges (from the ZIL-130) located under the hood, acts on the steering mechanism mounted on the front beams in front of the radiator grille. Next, the force is transmitted by an unregulated rod to the double (welded from two) lever of the right rotary axle, and from it by an adjustable rod – to the lever of the left rotary axle.
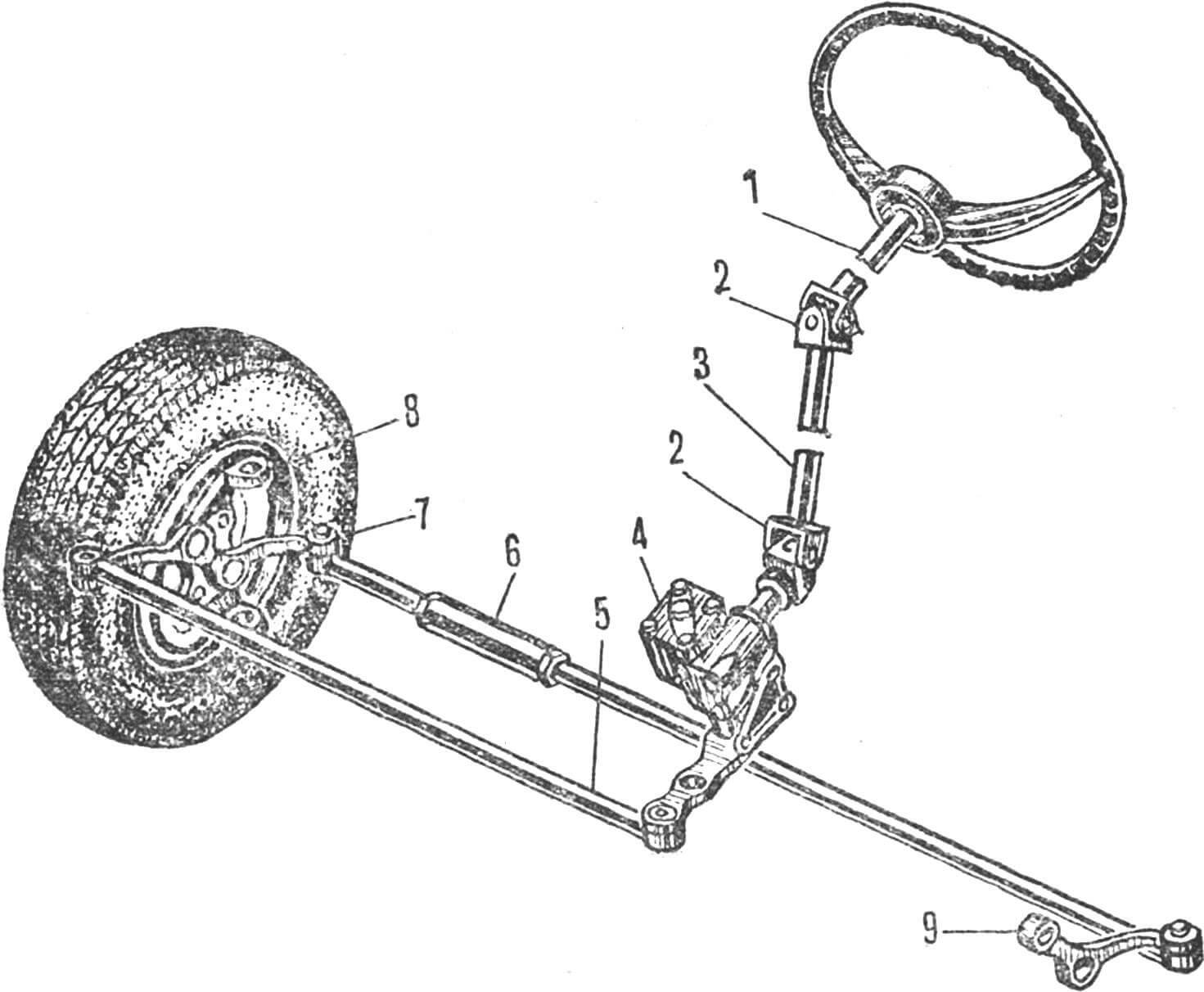
1 – steering shaft, 2 – cardan joints, 3 – intermediate shaft, 4 – steering mechanism, 5 – non-adjustable linkage, 6 – adjustable linkage, 7 – double lever of the right wheel, 8 – axle, 9 – single lever of the left wheel.
Briefly about the rest of the equipment of the all-terrain vehicle. The brake system, interior heater, headlights and electrical wiring are borrowed from the Zhiguli VAZ-21011, the rear lights are from the Skif sight, and the windshield wipers and control devices are used from the UAZ-469.
A. TIMCHENKO