Many do-it-yourselfers gained initial experience in automobile construction by converting motorized strollers. And in general, the entire domestic “automobile” industry grew up on vehicles with motorcycle engines. Moreover, a beginner is attracted to this technique not only by the availability of purchasing initial components and assemblies, but also by the relatively short period of time to bring his brainchild to the level of “passenger transport”.
The design of both models of motorized strollers (SZA and SZD) is frame, and their body is not lightweight, so there is always the opportunity to significantly reduce the weight of the future machine. One way to achieve this is to abandon the closed “coupe” and doors, choosing as a prototype a large family of jeeps, the popularity of which is explained primarily by their versatility. (Let’s just remember the famous “Jeep”: let’s say, in the USA it regularly served in army reconnaissance, and as a command “horse”, and as a tractor for a field gun, and after the war, as a microtractor on small farms.) Due to this simplification, as well as careful adherence to weight discipline when re-equipping the vehicle, it is possible to keep the total (dry) weight to 400 and even 350 kg, which will allow for a corresponding increase load capacity, speed, maneuverability.
Three-seater mini-jeeps “Istra-3” were manufactured in the town of Istra near Moscow under the direction of the author and were intended for country trips, hiking, fishing, and hunting. Predominantly summer operation determined some design features: a folding awning and a folding windshield. As a result, the car turned out to be very convenient to store: if you remove the battery, it can be placed vertically on the bumper – in this case, it will take up no more than 1 m 2 of space in the shed.
The car body, with the same track as the SZD, is slightly wider than the serial one. This made it possible to install another double seat next to the driver’s seat or the ability to place a load with an area of 0.8×0.7 m and weighing up to 200 kg.
The design of the mini-jeep from the SZD motorized stroller uses the lower part of the frame with the floor, as well as the sub-motor part of the main frame. These elements should be cut out very carefully so as not to damage the control mechanisms and electrical wiring. The frame with the windshield was also taken from the motorized stroller, although it can also be borrowed from the windshield of the GAZ-69.
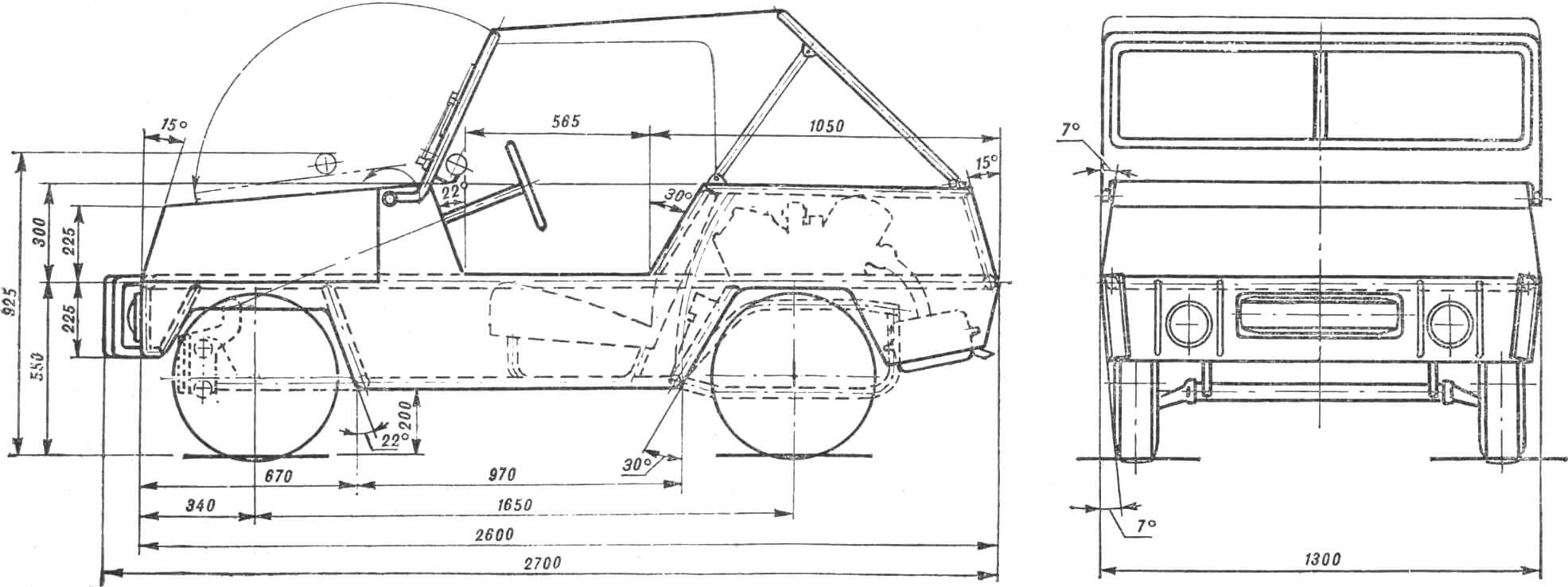
For further work, you need to install the frame (with the entire chassis) on stands in a horizontal position. Horizontality, both longitudinal and transverse, should be checked to a good level. To be sure that the extreme positions of the wheel suspension are taken into account, it is better to immediately raise the car so that all the wheels are suspended – this will be the lowest position of the suspension. Then the frame is loaded (for example, with bricks or cement blocks) – so that when each wheel is pressed up, say, with a jack, the frame does not rise – this will be the upper position of the wheels. In this position, the freedom of rotation of the front wheels is also checked.
The outer body frame with dimensions of 2600X1300 mm can be welded from ordinary water pipes with a cross-section of Ø 33.5×3.25 mm. Even better are thin-walled pipes Ø 33X2 or Ø 32×2. The weight of this frame with four struts in the first case is 23 kg, in the second – 14 (9 kg lighter!). In all such cases, it is necessary to save as much as possible on the weight of the vehicle, because the power of the IZH-P2 engine is small.
After welding the outer frame, you should check the dimensions of the diagonals – they should differ by no more than 5 mm, the skew in the free state should not be more than 10 mm.
The finished frame is also placed on stands, positioning it relative to the chassis according to the dimensions indicated in the drawing. In this case, it is convenient to use threads with weights lowered along the perimeter of the outer frame at the right points: here it is also important to maintain the horizontality of both the main frame and the outer one. After this, the wheel arch braces are installed (from the same pipes; the length of the blanks is 320 mm) and fixed by welding. After additional inspection and alignment, final welding is performed. It is advisable to entrust this important operation to a professional welder.
Auxiliary elements of the body frame are made from lighter pipes, for example, Ø 20X1.5. The sequence is the same: fitting the workpieces into place, fixing them with clamps (possibly wooden ones), tack welding, straightening, final welding. After welding, the seams are cleaned, degreased (at least by wiping with rags soaked in gasoline), and thoroughly primed.
The body is sheathed with sheet steel 1 mm thick, or even better – with rigid duralumin (D16T) 1 – 1.5 mm thick. Fastening the sheathing to the frame pipes with M5 screws with a pitch of 80-120 mm. After marking, the holes are well punched, drilled Ø 4.1 – 4.2 mm and cut with M5 taps. To increase the rigidity of the panels and reduce noise when driving, it is necessary either to first make longitudinal ridges in the blanks, or to lay plywood from the inside in a shape that follows the panel, retreating along the perimeter by 20-50 mm and securing it with screws or rivets in increments of 150-200 mm.
The front lid (trunk) can be secured with “gramophone” locks: two in front and on the sides are enough. The engine compartment cover is done in the same way, but if you plan to equip a luggage compartment above it, then there should be more locks, and the cover itself must be reinforced with profiles or thicker plywood.
Other parts of the design are not so important, and everyone can solve them on their own. This applies to the placement of headlights and light signaling, the arches of the awning and the fixation of its panel, the installation of the windshield in the main and lowered positions, etc.
Use ready-made controls from a motorized stroller. If you can’t get them, copy or borrow from “Zaporozhets” or “Moskvich”.
Of course, when building your own car, it is not necessary to repeat the appearance of Istra-3. However, do not forget that your car must have its own “face”. Often in such cases, do-it-yourselfers resort to “props”: for example, they imitate a radiator. It would be appropriate to quote the famous architect Corbusier: “Beauty is in functionality.” In Istra-3 the “face” is functional. The spare wheel, for example, serves as a clear buffer (real, not decorative!) in the event of a frontal impact. The arches of the headlight guards, together with the dimensional handles (for pulling the car out of ditches or ditches), create a rather expressive, different from others, appearance of the jeep. This feature of Istra-3 was also noted at the home-made car competition, where two such cars were presented.
You can also use a jeep as a mini-tractor: for this, the rear wheels should be equipped with lugs of any type.
Instead of 5.00-10 tires from a motorized stroller, you can put 4.00-10 tires from a scooter on the same wheels. On relatively wide rims, motorcycle roller tires get an interesting “arched” appearance, and the fit to the road surface improves (this is done with a 5.00-10 tire in a buggy, for which purpose the rims are specially widened). This significantly improves the smoothness of the ride, which, as is known, depends on the ratio of unsprung to sprung masses, and the weight of a wheel with scooter tires is almost twice as light. For the same purposes, it is better to take SZA wheels, which are lighter than those of the SZD (with hydraulic brakes): for a lightweight car, a mechanical brake drive is sufficient, especially if it is installed on the front wheels. And the appearance of a jeep with such “unrecognizable” wheels is much more interesting. True, cross-country ability and speed will decrease somewhat.
The speed of a mini-jeep with a motorized carriage chassis is approximately 60 km/h. Operating the all-terrain vehicle in specific conditions will reveal whether there is power reserve. This will be revealed by an increase in the number of revolutions at full throttle – the engine “roars”. This means that it is necessary to reduce the gear ratio, which will increase the maximum speed to 70-80 km/h (depending on the condition of the engine). In a sidecar, the ratio of the number of teeth of the drive sprocket (on the output shaft of the engine) to the driven one (on the input shaft of the main gear box) is 20: 16 = 1.25. But you can replace the drive sprocket with one of the Izhevsk motorcycle sprockets with the number of teeth 17 or 18, or remake the driven sprocket by grinding off the old ring and welding on a new one, cut from the drive sprocket of the sidecar, thus bringing the gear ratio to unity. You can also attach a crown from any other Izhevsk sprocket Z = 15 – 18. Since replacing the sprocket itself is not difficult, it is nice to have replaceable ones: for example, for long trips the gear is 15:15 = 1, for garden work – 20:15 = 1.33.
The figures show the conversion of the SZA model as more complex: if the SZD is used as the original model, some of the alterations are simplified due to the use of some body trim elements.
P. ZAK, engineer