CAR – FOR WHAT?
Do you need a car? Which one exactly? This question arises before anyone who intends to purchase a factory-made car. But, as you know, the choice of the type of car you need is limited. This question becomes even more relevant if you decide to build the car yourself.
For example, I really need a car for everyday travel at any time of the year, regardless of weather and road conditions. Is, say, Moskvich suitable for this? Not quite. The sedan-type body layout has many disadvantages—this has been mentioned more than once in the press. We started producing station wagon cars relatively recently.
Next: starting a liquid-cooled engine in severe frost is very troublesome, especially for an individual owner. In addition, winter operation quickly renders the car unusable due to corrosion from salty snow slush and dirt. It is no coincidence that my fellow owners of Moskvich, Volga and Zaporozhtsev cars keep their vehicles laid up for most of the year. It is in cold weather and bad weather, when a car is especially needed, that they become pedestrians. And I use the car I built at any time of the year.
WHAT SHOULD A “CITY” CAR BE?
In order to stay overnight in a sedan on a long journey, you need to remove all the luggage from it or specially rearrange it, which takes a lot of effort and time. There’s nothing to even think about spending the night for the four of us. But for me, this option does not present any difficulties, just like, for example, transporting a refrigerator, TV or washing machine.
For the sake of all these conveniences, I deliberately gave up many of the undeniable advantages of the same Moskvich: comfort, quietness of the engine, soft suspension, high speed and good throttle response, availability of service and spare parts. I just needed another car.
A book by Yu. Dolmatovsky helped to come to this decision, which, by the way, was called: “I need a car.”
In the amateur micro-automotive industry, in my opinion, three main directions have now been identified. The first is to make a microcar “like a real one,” that is, similar to some industrial design. The second, more promising direction is new constructive solutions, search in the field of design. The best examples of the latter are the well-known KD series cars, created with the participation of artist-designer E. Molchanov, as well as the car of the Shcherbinin brothers.
From this group, in recent years, another direction has emerged as an independent branch, which could conditionally be called “functional”. This is the creation of vehicles with non-standard layouts, intended for operation in certain conditions: off-road – off-road; with water obstacles – amphibious all-terrain vehicles; for crowded city streets – agile tricycles and so on. By the way, the current “Technical Conditions” for the construction of home-made cars do not provide for the construction of such cars, limiting the search by a number of indicators (dimensions or body shape, engine displacement, etc.), however, without interfering with interesting (obviously, for the national economy) work.
I also set myself certain goals when conceiving this design. As can be seen from the list of requirements given at the beginning, I needed a station wagon that, with a minimum of technical costs, would have maximum advantages and, with a minimum of external dimensions, a maximum of internal volume. That’s why the name “Minimax” appeared. There are a lot of opportunities here for self-expression, for the full realization of your ideas. This gives great moral satisfaction. And work done with your own hands, in my opinion, is the best break from your main activity.
“MINIMAX” – CAR LAYOUT
Amateurs began building carriage-type microcars relatively recently. This was undoubtedly a sign of the technical maturity of the authors of the new designs. The development of such a scheme is presented in the following order: “Squirrel” (the so-called agricultural version, USSR), “Pininfarina” (Italy), “Ant” (USSR).
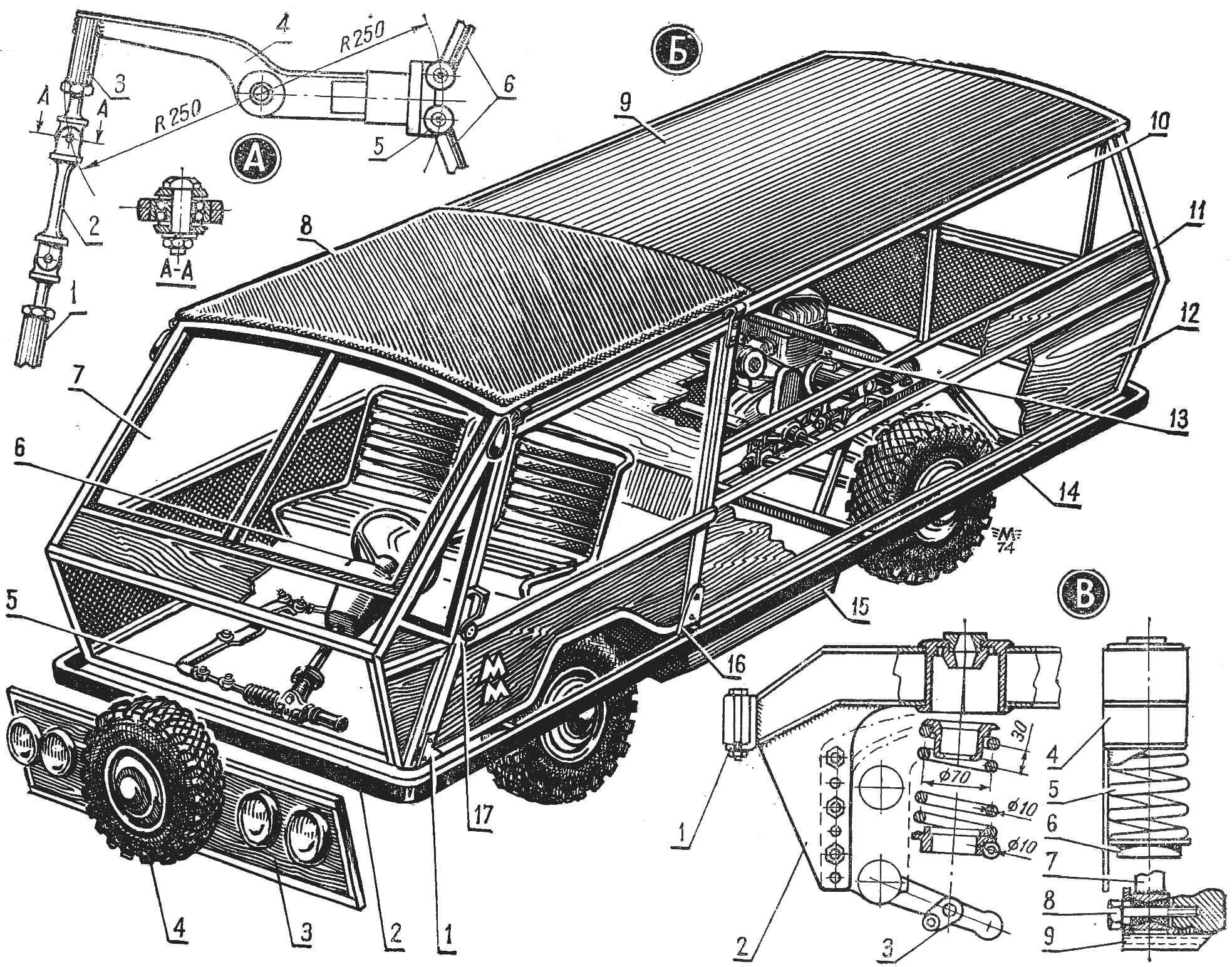
A — steering gear rocker: 1 — rack rod C3A, 2 — intermediate link, 3 — rocker threaded bushing, 4 — rocker, 5 — ball ends, 6 — steering rods; B – body preparation: 1 – sliding door, 2 – frame, 3 – front panel, 4 – spare wheel, 5 – steering mechanism, 6 – steering post and instrument panel, 7 – windshield, 8 – opening part of the roof (Aviasent ), 9 — hard part of the roof, 10 — glazing of the rear part of the cabin, 11 — body edging (duralumin corner), 12 — side panel, 13 — S3A engine and main gear, 14 — longitudinal frame member, 15 — bottom of the cabin, 16 — door guide, 17 — door lock; B – front suspension: 1 – trapezoid leg, 2 – gusset for fastening the front axle C3A, 3 – reinforced bracket for fastening the lower ear of the shock absorber, 4 – upper cup, 5 – spring, 6 – lower cup, 7 – lower ear of the shock absorber, 8 – figured bolt, 9 — reinforcing tube.
When creating the Minimax (Fig. 1), I additionally solved the following problems: transition to a completely closed body; expansion of internal dimensions without much increase in external dimensions, simplification and lightening of the power circuit; expansion of doorways; modernization of the steering mechanism.
Of course, along with great advantages, the carriage layout has its drawbacks (otherwise cars of this type would have already become more widespread). First of all, it should be noted that the driver is not in the “comfort zone”, near the center of gravity of the car. Therefore, it “swings” much more than in classical machines. If you make the suspension softer, this will lead to an increase in “galloping” – the longitudinal rocking of the car, which is generally characteristic of carriage layouts that have a small base and dispersed masses. This is especially noticeable when driving over rough terrain, which is why I had to slightly increase the stiffness of the front suspension.
The front position of the driver in a carriage-type car is also more dangerous in the event of a collision with an obstacle. Therefore, the Minimax has adopted the location of the spare wheel on the front panel of the body – it can, to a certain extent, work as a shock absorber. The key decision in order to increase safety was the choice of frame: in the form of a closed load-bearing frame extending beyond the dimensions of the body along the entire perimeter, located at a height of 400 mm from the road surface,
DESIGN FEATURES
The flat frame (Fig. 2) is made of steel welded pipes of rectangular section 50X25 mm, with a wall thickness of 2.5 mm, forming a rectangle 3200X4500 mm with four transverse crosspieces and two additional longitudinal elements. The frame is essentially the main assembly jig: all other components of the chassis and body are bolted to it.
Minimax has sliding doors. With a carriage body this is easier to do. In addition, this design allows them to be made much wider, without increasing the required parking dimensions, which is inevitable with swinging doors. And wide doors for a minicar with a carriage layout mean additional convenience for the driver and front passenger. In this sense, the Minimax has certain advantages compared, for example, with the Fiat Multipla carriage-type microcar. Through the wide door, passengers in the back seat enter the Minimax; The cabin can easily accommodate a refrigerator or other large luggage. The dimensions of the rear hinged door also contribute to this.
The carriage layout imposes restrictions on the size of the wheels: after all, the driver’s seat is located above the front axle. In addition, increasing the machine’s center of gravity negatively affects its stability. In addition, it is necessary to comply with existing technical requirements that limit the height: no more than 1450 mm.
The 5.00-10 tires of the C3A motorized stroller fully satisfy all the conditions, although they limit the total weight of the vehicle to the permissible load: 250 kg per wheel.
The use of these tires prompted the use of motorcycle axles – the front one was based on the C3A suspension, mounted on two longitudinal welded box-section cross-beams mounted on the first two transverse crossbars of the frame. The required rigidity is achieved through additional spiral springs mounted on the shock absorbers. At the same time, the attachment point for the lower ear of the shock absorber has been strengthened. The preliminary preload of the springs is adjusted in the same way as recommended for the Zaporozhets (Za Rulem magazine, 1970, No. 2).
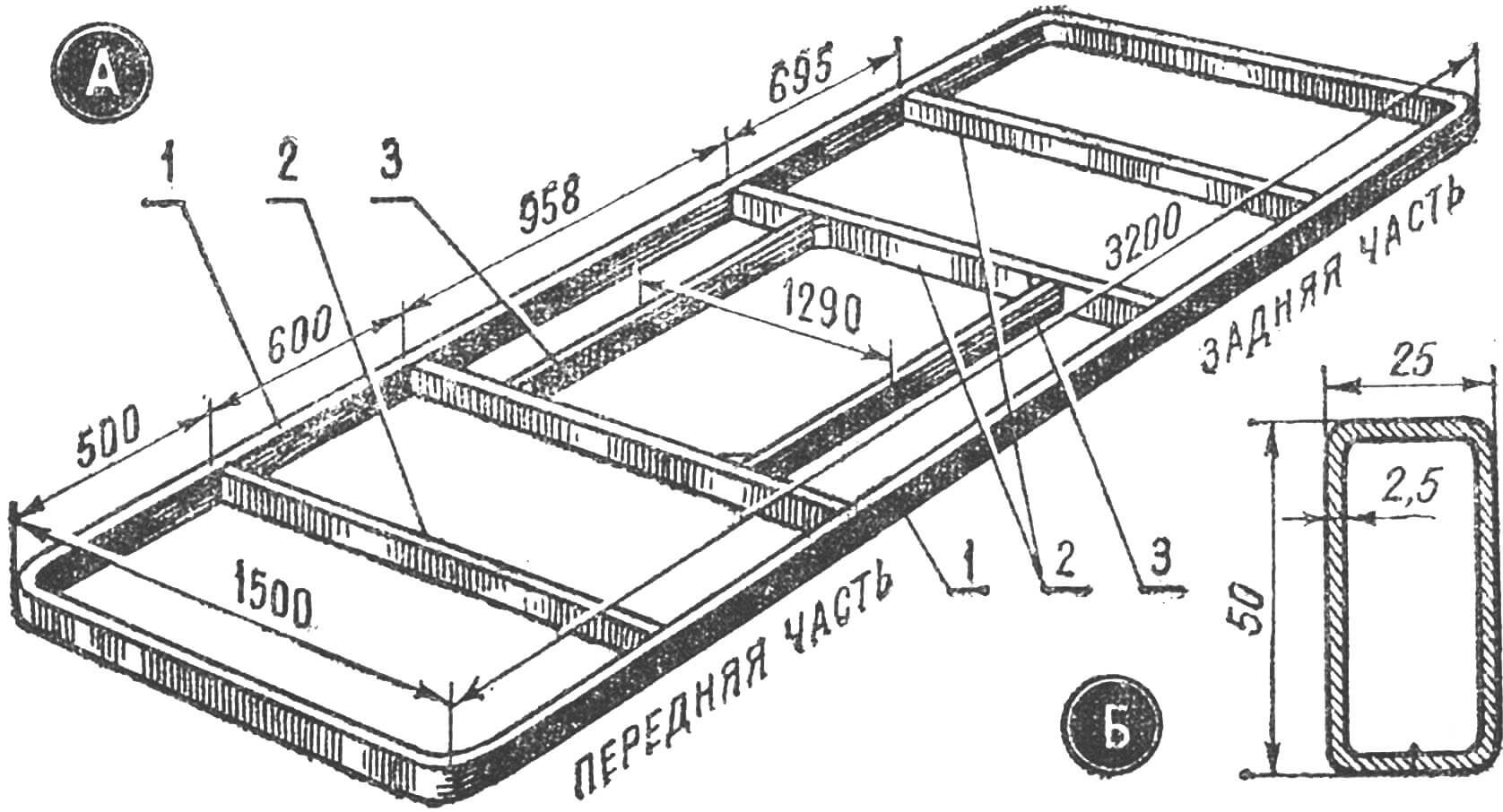
A – general view: 1 – longitudinal bars, 2 – cross members, 3 – bridge mounting spar; B – pipe section.
The layout of the engine compartment provides for the possibility of installing the Zaporozhets ZAZ-965 power unit. However, the first version of the Minimax is equipped with a C3A power unit, with a slightly increased compression ratio (up to 7.8); At the same time, the rear part of the C3A frame with the engine, final drive and rear wheel suspension balancers is fully used.
I consider it my duty to warn followers that the use of the C3A (or C3D) chassis, even with the correct distribution of the load between the wheels, limits the running weight of the vehicle to a maximum value of 1000 kg. With the dry weight of the Minimax being 640 kg, the payload thus does not exceed 300 kg. Therefore, on a long tourist trip, taking into account travel items, only 2-3 people can travel in the car. The task of keeping the weight to 640 kg is not easy if there is no strict control over the weight of the parts during the creation of the machine. Indeed, often home-made products have a dry weight of about 800 kg (or even more), which leads to extremely rapid wear of rubber and suspension parts. For this reason, many home-made machines subsequently have to be almost rebuilt from scratch.
The steering, in addition to the units borrowed from the C3A, has a longitudinal rocker, the front end of which is connected by a rod to the steering rack. The steering linkage ball joints are attached to the rear end of the rocker.
Drum brakes are installed on all four wheels. The handbrake only applies to the rear wheels.
The body is assembled from several separate units. The frontal part consists of two lower longitudinal rectangular pipes 50X25 mm, to which racks are welded, and transverse steel profiles attached to them with bolts, sheathed at the bottom (floor of the front compartment) with 7 mm thick getinax, at the front with 4 mm textolite, at the back and on the sides with sheet metal steel 1 mm.
The front glazing frame is welded from bent corners 1.5 mm thick and 15X1.5 mm tubes (upper contour and middle pillar). The windshield is made up of two halves cut from triplex.
The sides are assembled with M5 bolts from aluminum profiles and 3.5 mm getinax sheets. They are connected by the middle bulkhead (between the passenger and engine compartments) and the rear side. The sides and middle bulkhead are attached to the frame, and the front edges of the sides are supported by racks made from the same 50X25 mm rectangular pipes. In the upper part, the edges of the sides at the front and back are connected to each other by arcs welded from 25X2.5 mm pipes.
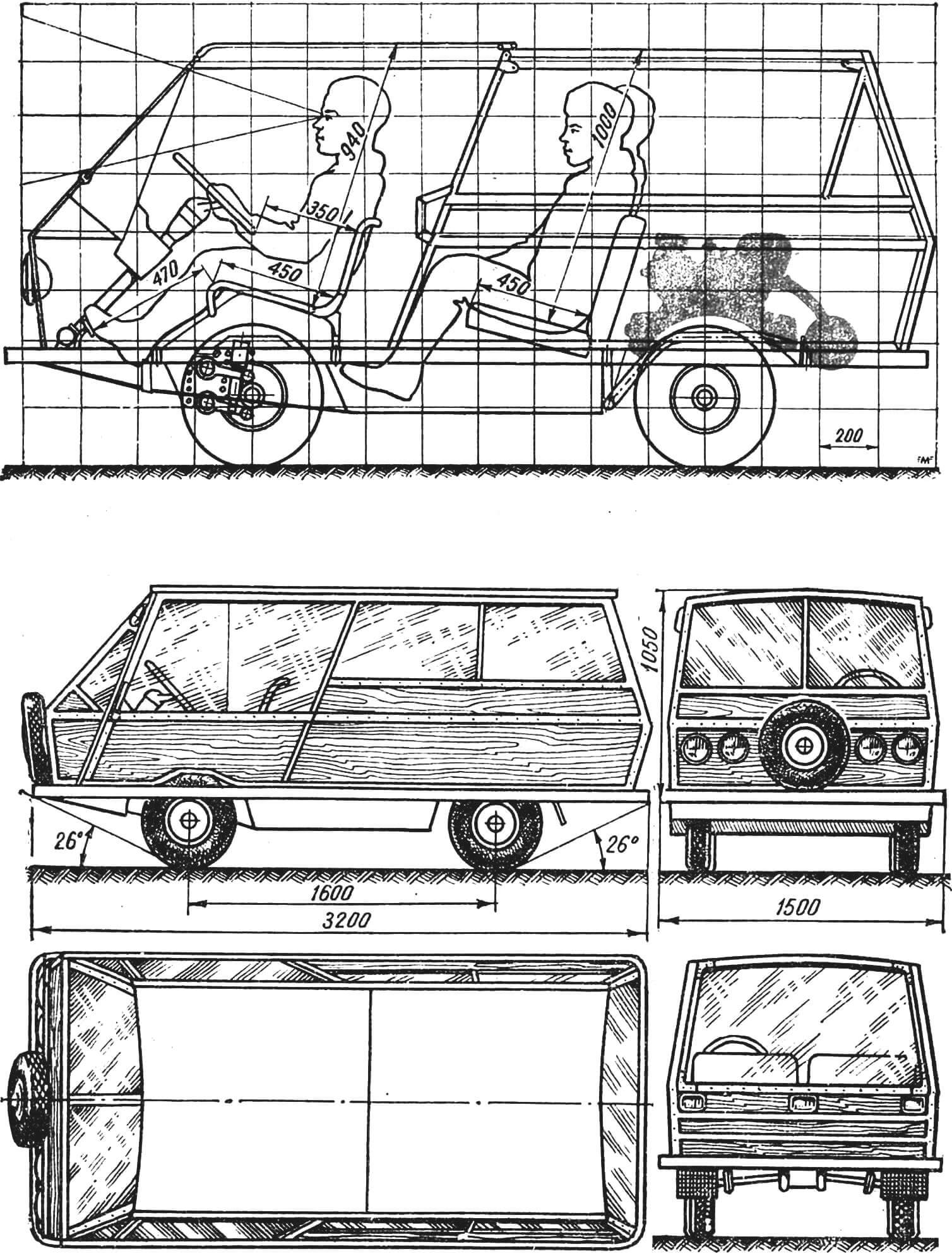
The longitudinal contours of the roof are formed by aluminum profiles with a rectangular section of 40X20 mm and a protruding shelf, which serves as a drainage system and a guide for sliding doors. The profiles are fixed to the front glazing frame and to both arches.
The roof consists of two parts: the back, between the arches, is made of sheet hetinax; the front one is soft, on a tubular frame, removable.
The side glazing is assembled within frames made of aluminum profiles. The doors are diamond-shaped and move on two upper rollers; each has a bottom guide. When closed, the doors fit tightly into the front groove of the frontal part and overlap with the rear edge of the body. The free movement of the doors is ensured by a special mechanism (see Fig. 1B): during the initial movement, the rear lower corner of the door slides in an oblique guide that moves the bottom of the door away from the body. The rear additional engine compartment door is suspended on two upper hinges.
The floor of the passenger compartment is made of 6 mm thick getinax sheet and fixed to the walls of 1 mm thick steel sheet, between the middle cross members and the internal longitudinal elements of the frame.
The frames of the front seats are welded from steel tubes 20X1 mm, onto which rubber strips from the Zaporozhets seats are stretched and leatherette covers are put on. The rear seat and its backrest can be removed (when transporting cargo) or rearranged into the plane of the engine compartment lid, resulting in a common sleeping area measuring 1900X1250 mm. At the same time, the front seats are not removable, and there is enough space for luggage in the lower part of the cabin.
The instrument panel is located on the steering column. The gear control is located next to the driver’s seat. Rods and control cables run in the central tunnel below the frame level, and in the front and passenger compartments they are covered with covers.
The body, outside and inside, is lined with plastic that imitates wood.
The shape of the machine was determined by the proportional composition of flat surfaces, most characteristic of wooden panels. At the same time, such planes are the most technologically advanced in relation to home production conditions. The lack of aerodynamics of the adopted shape plays practically no role, since in urban conditions the average (and even maximum) speed is low. From the point of view of technical aesthetics, it should be noted that modern design also makes extensive use of planes, replacing streamlined shapes everywhere. This circumstance in this case turned out to be so definite that attempts to fit the “panoramic” windshield of the Moskvich into the Minimax body on several models (on a scale of 1:10) clearly showed that the car looks much better with flat glass. The design of the upper guides and the rhombic door contour also fits well with the chosen body shape. As a result, while the length of the car was shorter than that of the Zaporozhets, its internal volume was greater than that of the Volga.
As the experience of using the car in Moscow and on the roads of the Moscow region (mileage over 30 thousand km) has shown, the design of the car was basically successful. Winter operation also convincingly demonstrated the great advantages of the air-cooled two-stroke engine.
Due to the high weight ratio, even with a 350 cm 3 engine, a car with two passengers has sufficient acceleration for driving in the Moscow “green wave”, and the maximum speed reaches 70 km/h. Low engine power is felt only on long climbs and when overtaking, or if two more passengers get into the car: throttle response drops noticeably. Therefore, if long tourist trips with the necessary luggage are expected, then it is advisable to install a more powerful engine.
P. ZAK, design engineer, NTTM laureate