Once upon a time, the Earth was inhabited by dinosaurs, brontosaurs and many other strange animals that did not need paths or roads – they made them for themselves. And at the All-Terrain Trophy last year (see detailed report in M-K No. 11-2018), we met their modern descendant – PTZavr’oM – an all-terrain vehicle of a very original design, built by off-road tourism enthusiasts from Petrozavodsk (which, By the way, it is reflected in the title). His crew received the main prize from the “Modeler-Constructor” magazine, since this work seemed to us one of the most interesting among the homemade products that arrived at the competition. Now, as promised in the report, we are publishing a detailed story about this curious machine, prepared by its creator.
We have been familiar with off-roading for a long time. First we traveled in UAZs, then in foreign jeeps, and we drove both a Mercedes Unimog 406 and a GAZ-66. Many times we took part in the iconic off-road sports events “Karelia-Trophy” and “Ladoga-Trophy”, organized both serious hikes and fun “rides”. However, we have been convinced from our own experience that increasing the size of a car, which gives advantages in the habitability of the car and the ability to transport an additional amount of things useful away from home, at the same time creates certain problems.
The large weight and dimensions did not allow us to travel where it would have been easy to do with compact equipment. And if you get stuck, which happened often, then “pulling a hippopotamus out of the swamp” is not easy in all respects.
So, gradually, we came to an understanding: we need a small vehicle capable of transporting two people through the forest, which in most cases is fairly swampy, or through virgin snow – in a word, without any road. Of course, with such initial data, a good margin of reliability is very important, but since any equipment can break, in our case it must be such that it can actually be repaired in the field. And she must be able to swim, since in Karelia we have even more water than mud.
They considered an ATV as a “rogue”. However, you can’t go on a serious hike on it together. You can still pick up a passenger, but without tourist belongings and not far. In addition, even if they have enviable cross-country ability, “quads” do not float. Not our option!
Then they became interested in UTV class vehicles. Two people are already traveling quite comfortably here. The situation with luggage transportation is noticeably better than on an ATV. But the cross-country ability is worse. Perhaps this projectile is more intended for riding on dry forest paths. And the issue of overcoming water barriers remains unresolved.
As a result, going through possible types and types of transport suitable for our tasks, we turned our attention to all-wheel drive amphibious all-terrain vehicles with the formula 6×6 and 8×8. The most famous brands among them are the Canadian Argo and the American Max. In our country, they have not become noticeably widespread due to their high cost and not the best reliability during serious use. However, in general, we liked the layout and driving performance of these cars, and we decided to build something similar ourselves.
To begin with, we made a full-size model of the future all-terrain vehicle from chipboards in order to “naturally” evaluate the possibility of loading it into a cargo minibus for delivery to the place of active use. Accordingly, both the shape and dimensions were selected based on this requirement. The length of the car “loomed” at 3200 mm, the width along the wheels was no more than 1350 mm, and the height was 1600 mm.
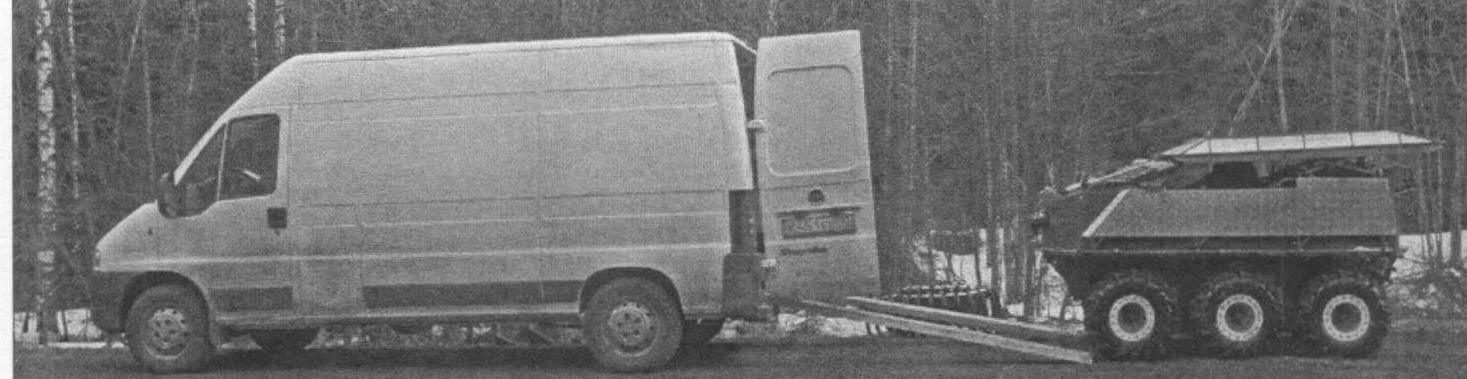
The power unit was borrowed from the Daewoo Matiz compact car. Three-cylinder engine with 51 hp. mated to a five-speed gearbox. The weight of this kit together with the cooling system radiator is 120 kg.
We welded a temporary frame to assemble the all-terrain vehicle chassis on it and check how everything would work. The internal combustion engine was installed transversely in the front part. From the output shafts of the gearbox, the torque is transmitted by two double-row chains (1:1.58) to the transfer case (TC) from the Niva car. It has been modified accordingly: a rigid drive shaft with output on both sides has been installed. This scheme allows you to relieve the gearbox by sending power flow through two branches. The transfer case is also placed transversely and distributes thrust over two sides. Double-row chains with a pitch of 12.7 rotate the wheels of the middle and front axles (1:1.52), and from the middle axle the chains stretch to the rear wheels (1:1).
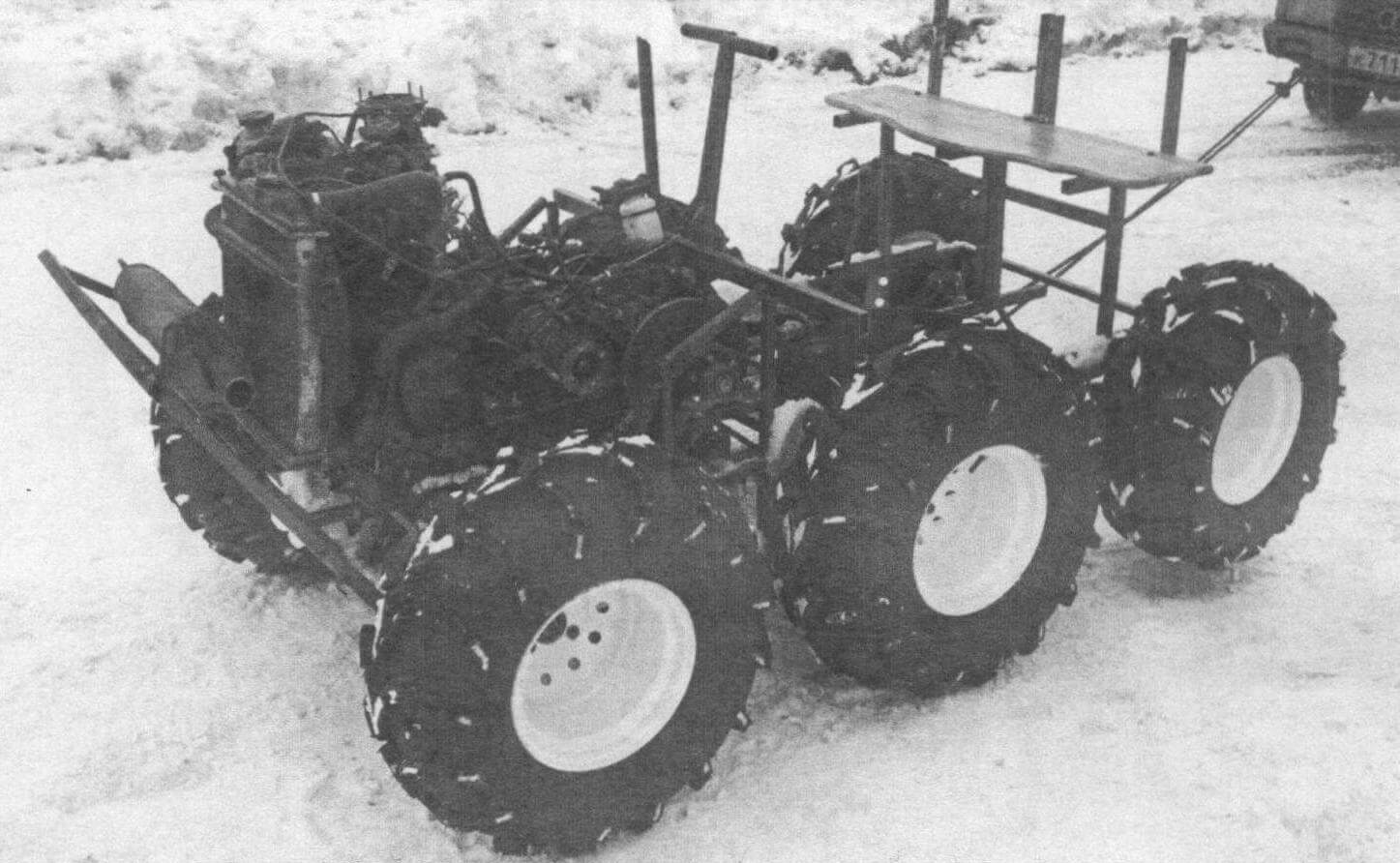
The wheels were taken from an ATV with 27″ tires on 12.5″ rims. The RK of the VAZ SUV has a differential, so it is obvious that the all-terrain vehicle has received an on-board differential control principle. You just need to install brakes on the output shafts of the RK. That’s what they did – they installed homemade discs, and took the calipers from the VAZ-2108.
We conducted sea trials, which immediately clarified a lot. Firstly, the engine power is abundant. Secondly, it is necessary to firmly secure the power unit. Being installed on rubber pads, it is attracted to the RC, the chain sags and jumps over the teeth, which is no good, of course. Thirdly, the differential principle of rotation is a completely workable thing, but we did not discover America here – a similar scheme has been tested by many home-made people. You only need to “add the throttle” when turning, which after 15 minutes of riding already happens reflexively.
Also, along with the positive aspects, disadvantages were also noted. For example, with this vehicle it is impossible to turn while in a rut. You have to back up and choose a different trajectory. But on flat surfaces the maneuverability is excellent. True, when driving in second and third gears, making a sharp turn, you literally fly out of the seat. When switching to 3rd and 4th gears, skill is required, since the car slows down quite quickly. It is better to control the gas manually, since sometimes you have to drive standing or half-sitting – this is necessary in order to go over uneven surfaces at speed. Almost like riding a motorcycle or bicycle. And even on serious off-road conditions, it is sometimes useful to be able to control an all-terrain vehicle from the outside, walking next to it.
At the end of the tests, we noticed that the frame moved a little. Fortunately, that’s why it’s temporary—it became clear what and where needs strengthening. But the deformation of the wheel hub fastenings showed that the applied solution, when the wheels are mounted on a cantilever, is erroneous. We’ll have to give it up. Due to the curvature of the hubs, the chains on the double sprockets were observed to jump. Moreover, once stuck in a snowdrift, slipping and digging the wheels to the ground led to a significant increase in the load on the transmission, as a result of which the drive chain of the right wheel of the middle axle broke. The all-terrain vehicle somehow made it to the workshop on one right and three left drive wheels, but this incident finally convinced that the design of the vehicle needed to be seriously improved.
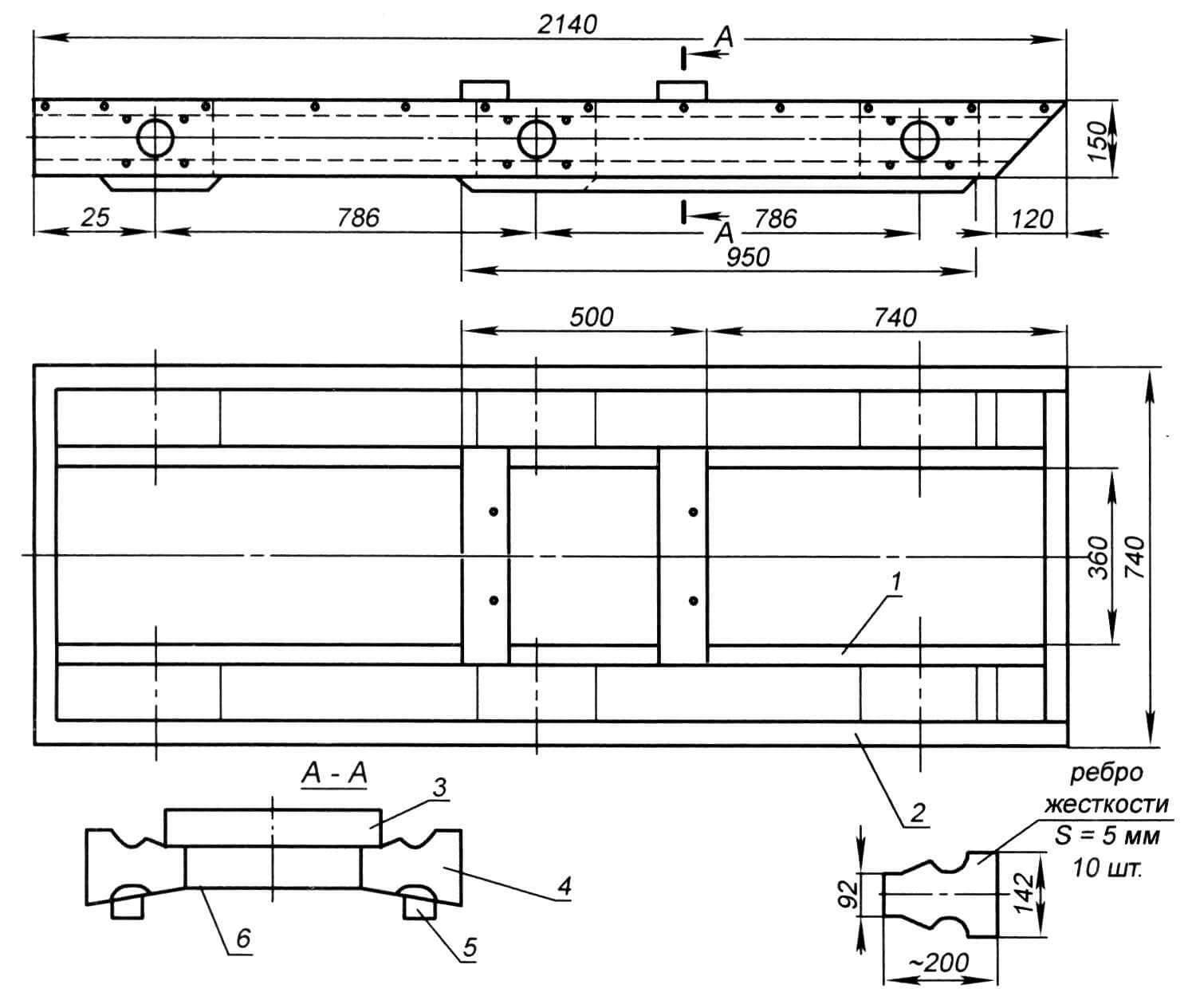
First of all, all six wheels were secured differently: instead of using the front-wheel drive hub of the VAZ-2108, which was connected on one side to the wheel disk and the other to the chain drive sprocket, they machined an axle for two bearings, the outer races of which are fixed in the sockets of the frame. Double sprockets were replaced with single-row sprockets for a powerful chain with a pitch of 25.4. For the reason stated above, we thought about how to completely get rid of the primary chain transmission (from the gearbox to the RC). As a result, the entire chassis design has changed dramatically.
According to the new concept, the power unit was “registered” at the rear and positioned longitudinally. The cardan, connected to one of the gearbox outputs, transmitted thrust to the final drive gearbox from the Ford Scorpio, which had convenient flanges at the output – brake discs and a couple of sprockets were mounted on them. Now the differential in the gearbox is naturally locked. From the gearbox, one pair of chains transmits torque to the wheels of the middle axle, the second – to the wheels of the rear axle (1: 1.8). The front axle receives drive from the middle one (1:1). The sprockets were used from agricultural machinery (specifically, from a potato digger made in Belarus) – it turned out cheap and the quality is acceptable. The chains were purchased at the store. Chain tensioners are not provided, and practice has shown that they are not necessary.
The frame is welded from a square profile with a cross-section of 40×40 mm (internal load-bearing frame) and 25×25 mm (external parts). The outside was sheathed with steel sheets (v. 3). 2 mm thick on the bottom, 1.5 mm thick on the front and back, 1.0 mm thick on the sides. Tests have shown that everything works as it should, but the ergonomics of the driver’s seat are not good. You glide along the bench as you turn from side to side. It’s impossible to hold on because you have to manage to pull the control levers. And being mobile, they do not give the hands the necessary support.
Further improvement of the machine went in two directions. Firstly, instead of a transverse bench, they installed two seats from the same Daewoo Matiz, which have lateral support. And secondly, the control levers, characteristic but not mandatory for equipment with an onboard turning principle, were replaced with a motorcycle-type steering wheel, deflected left and right at slight angles. Gas control – rotating handle. Now you can hold on to the steering wheel, which is especially appreciated when moving over very rough terrain and when making sharp turns. It is now possible to operate while standing, which is sometimes required. In addition, the winch remote control has also been moved to the steering wheel – it has become much more convenient to use it and at the same time help with the wheels. In addition, a more collected driver’s position, coupled with new controls, made it possible to increase speed, and this, in turn, improved cross-country ability. For example, it became possible to jump over snow tracks, sliding on the bottom, practically without the help of wheels, which was not possible before.
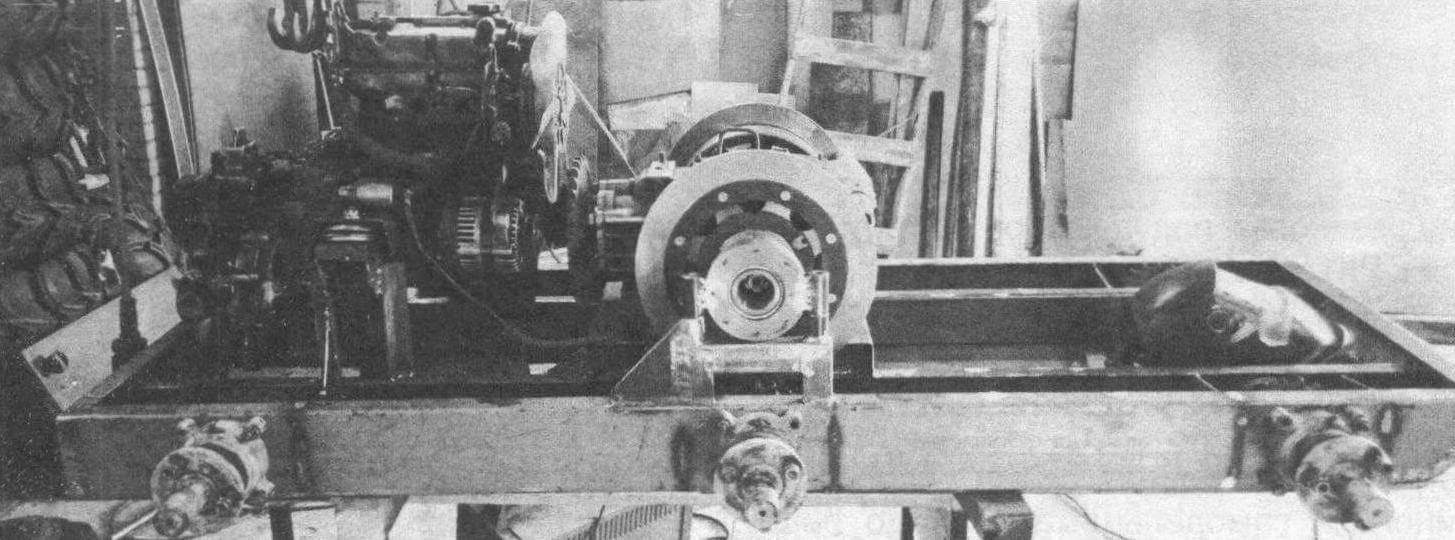
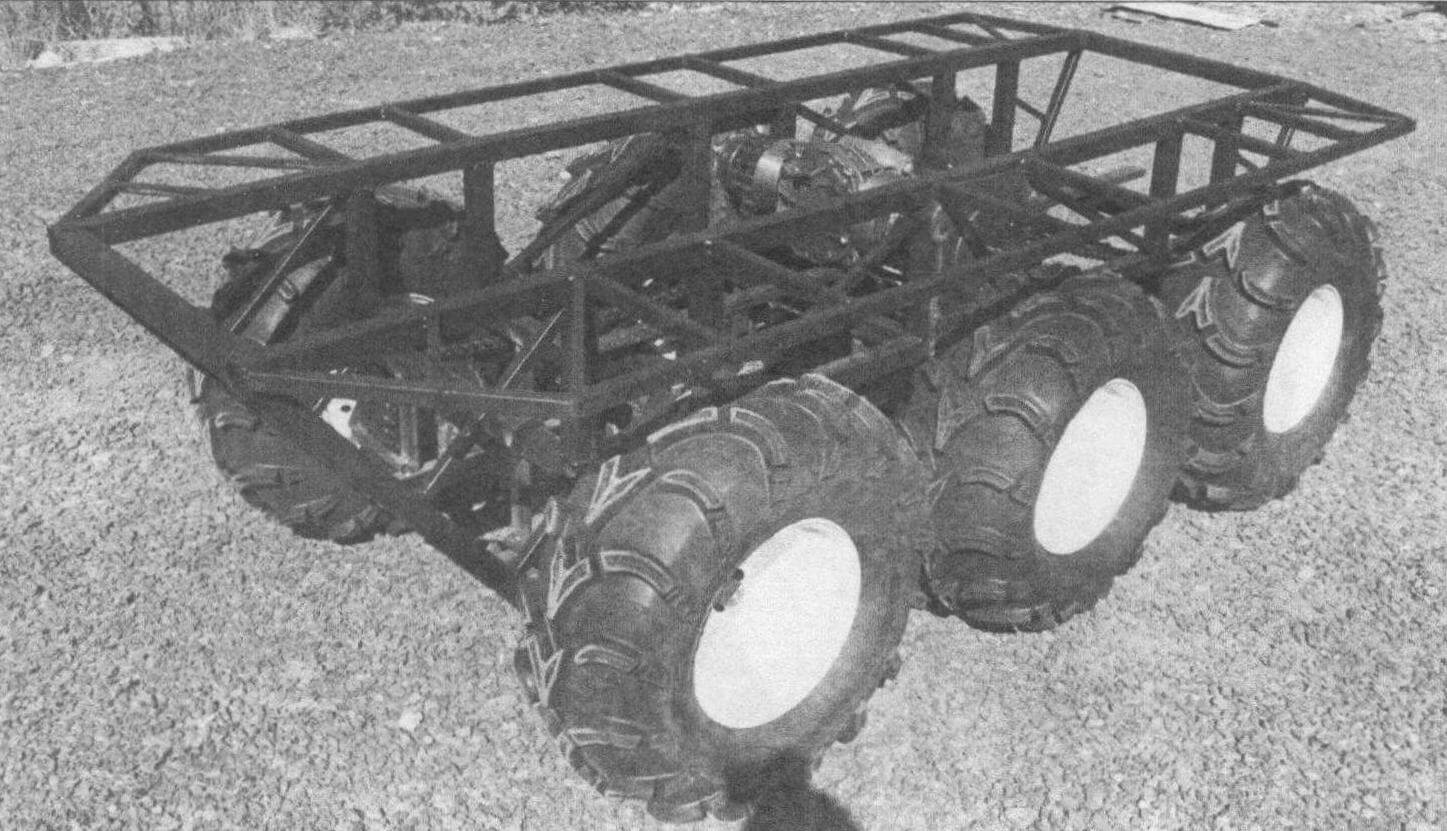
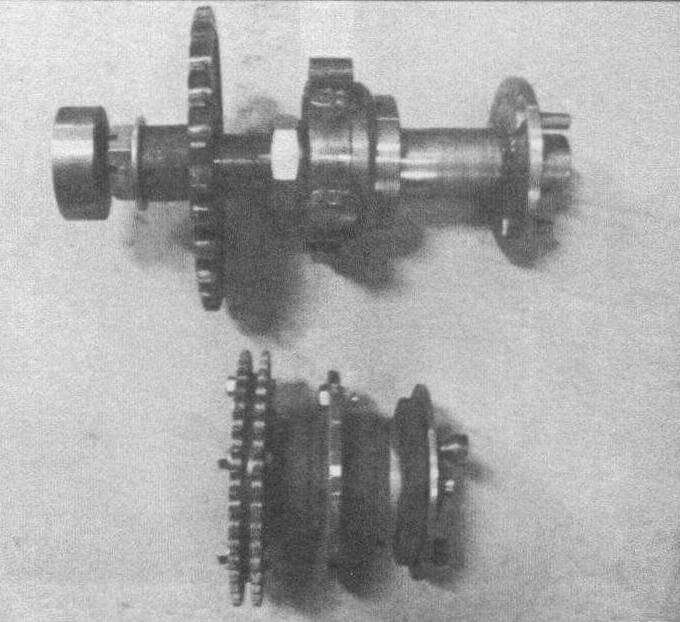
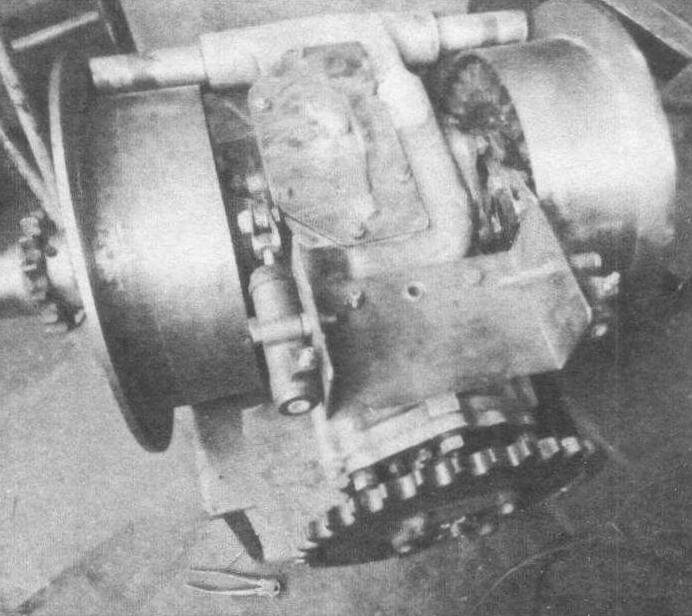
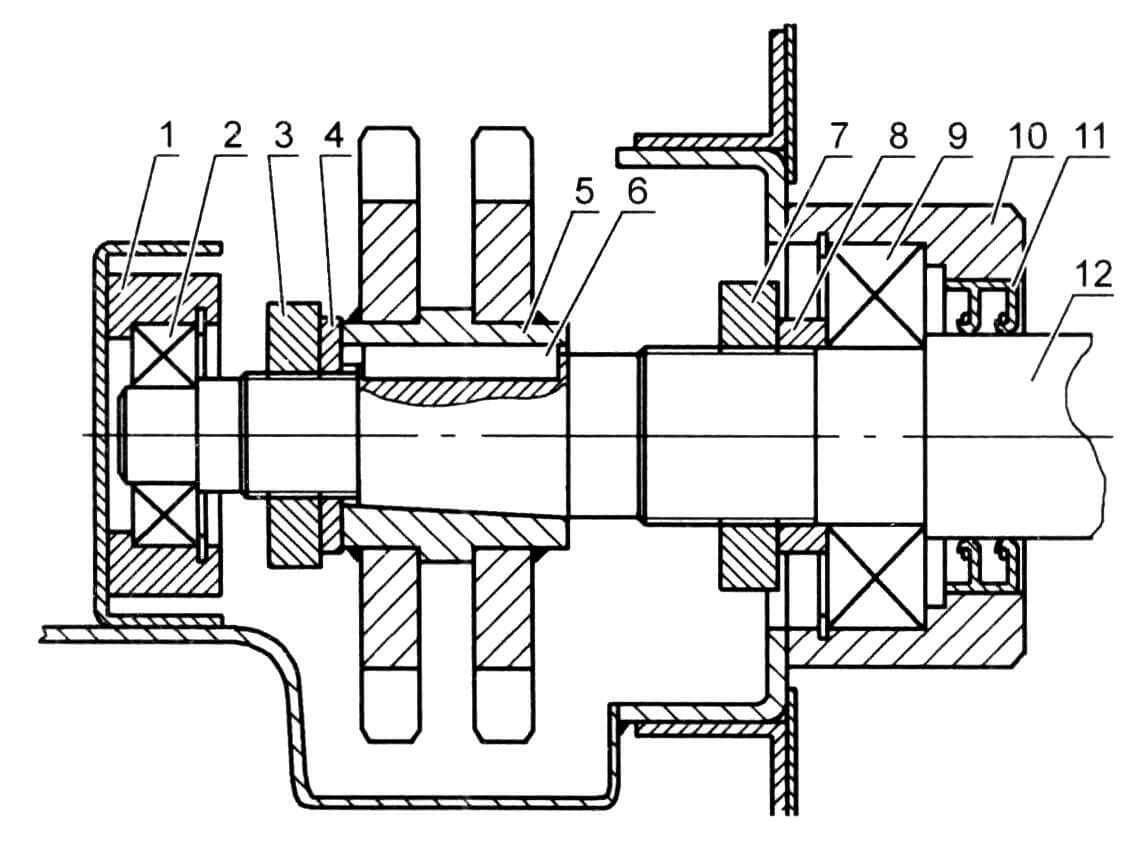
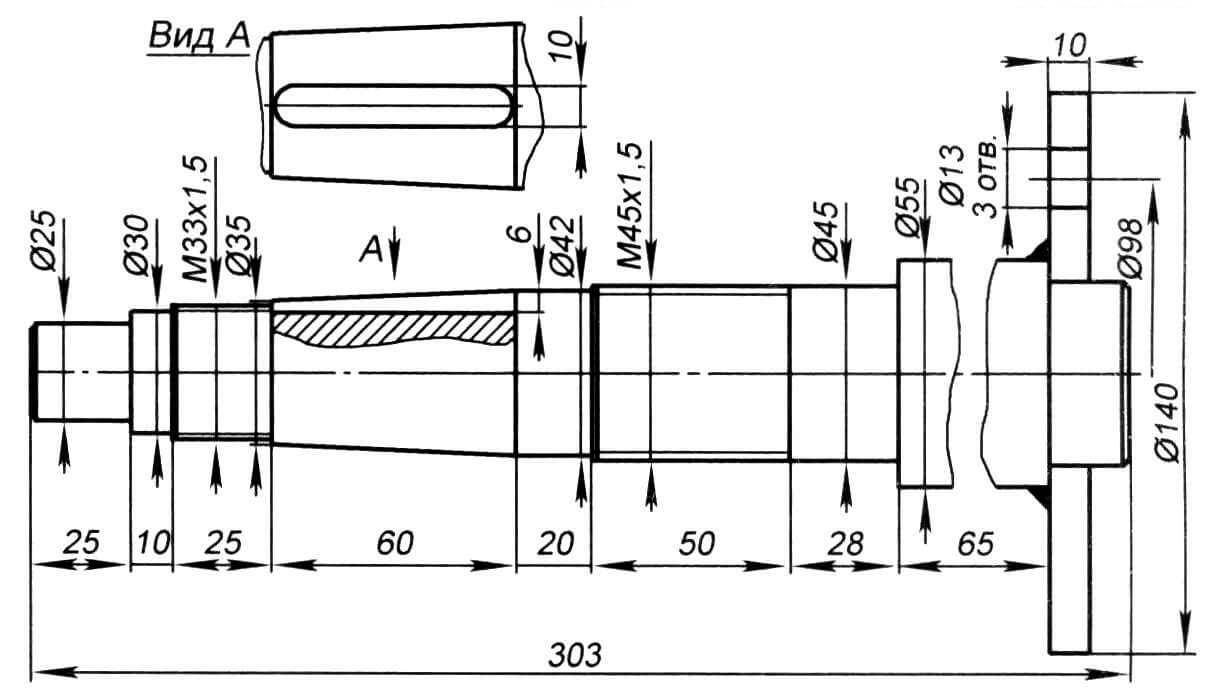
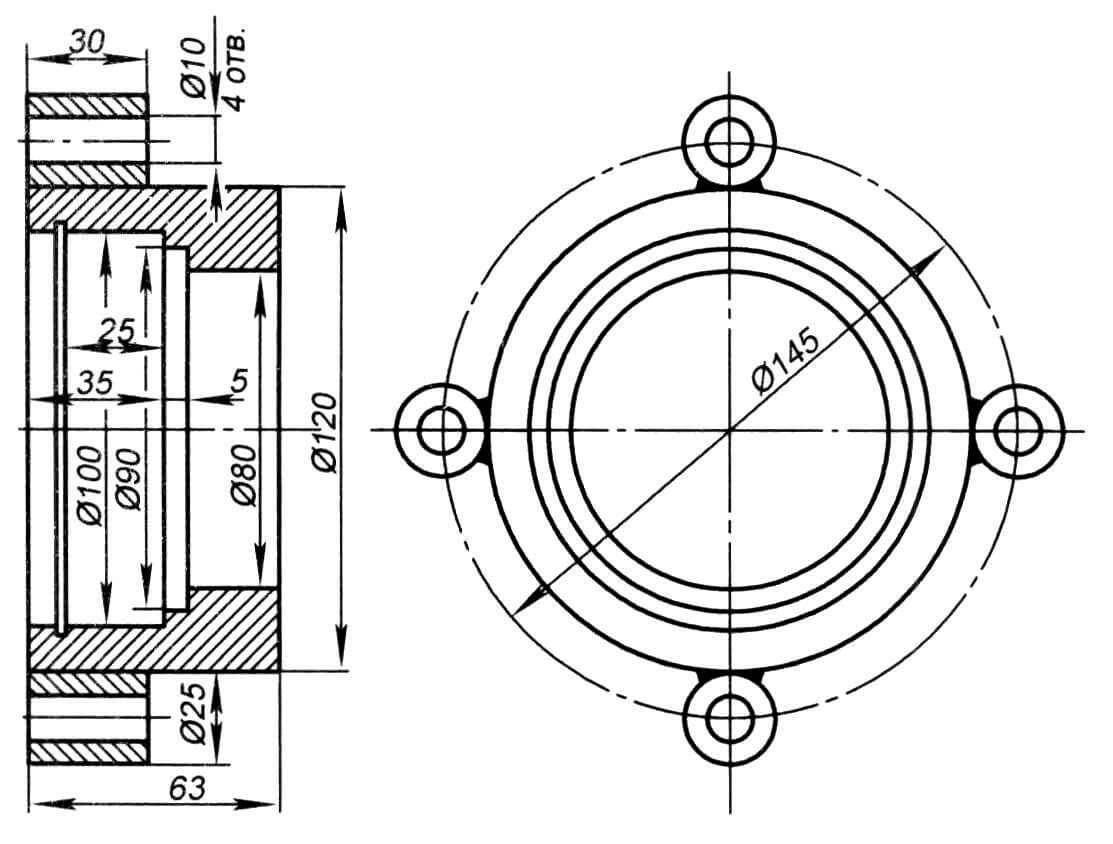
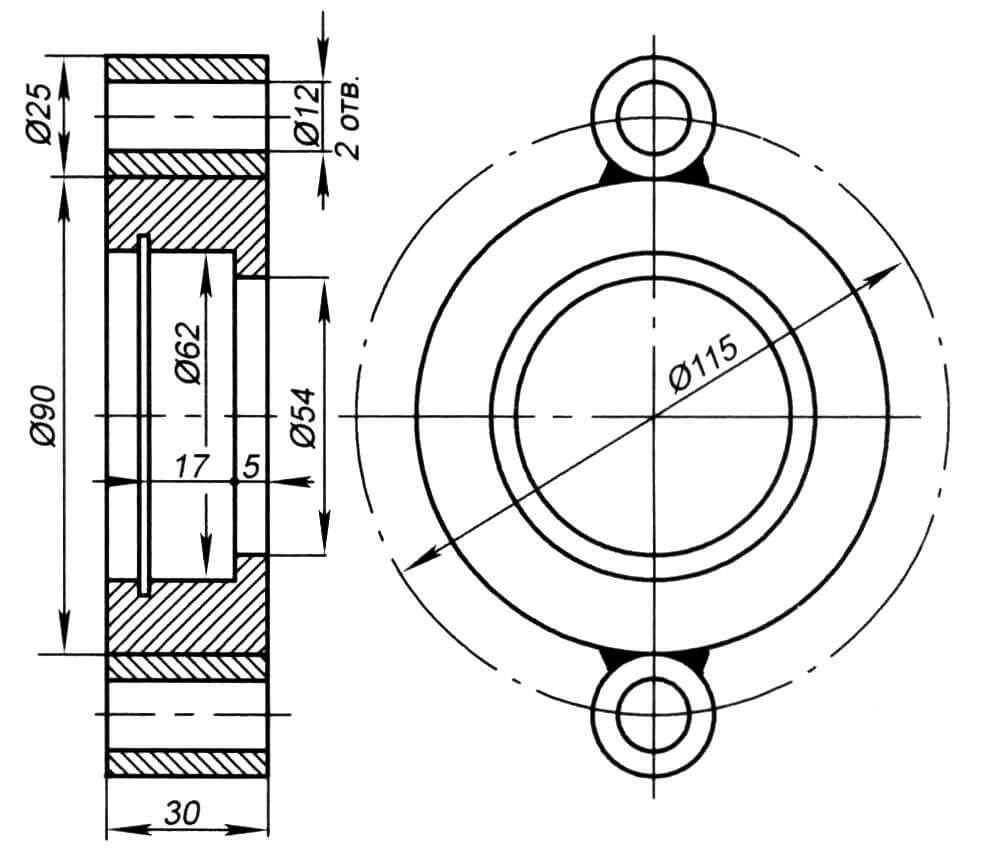
Having learned to drive normally on land, we began “water procedures.” In Karelia these are mainly rivers and lakes. Right within the boundaries of Petrozavodsk there was a gentle beach with sand – that’s where we started. The first swim took place on an all-terrain vehicle with low sides. Due to the rotation of the wheels, he swam poorly. We hung a 5 hp boat motor. to the rear transom and tried again. However, the results were again not encouraging: it was difficult to reach the tiller, but most importantly, the PLM was of little more use than the wheels, since the resistance of the hull affected it. The draft seemed deep, but at the same time the car swayed from side to side, trying to scoop up water over the side. In general, the crew felt very insecure on such a “ship”.
We continued to study the issue using a boat motor. To increase stability, two pontoons from old boilers of 160 liters each were added to the sides. As an experiment, we tried to install the PLM not at the back, but inside the all-terrain vehicle, for which we cut a hole in the bottom for the “leg” of the motor and welded a well, the upper cut of which was 100 mm above the waterline. With cylinders on the sides, stability has increased significantly; it has become possible to even stand on the rear trunk without causing dangerous rolls. It was also possible to reach a speed of up to 4 km/h, but practice has shown that in comfortable mode it is better to move at a speed of no more than 2.5 km/h.
The next stage of work took place under the sign of increasing the waterfowl properties of the all-terrain vehicle. So that you can walk for a long time and confidently along a body of water with average waves at a speed of at least 6 km/h. For this purpose, pockets were made above the wheels, which was supposed to reduce the resistance of the underwater part of the hull. The pockets were made of foam, adding additional buoyancy to the car. And inflatable cylinders were hung on the sides. Once on land, they can be quickly rolled up and the brackets folded. But neither the side floats nor the pockets in the wheel arches proved their worth. Flat folding foam pontoons turned out to be more practical. Bringing them into working position or folding them when going ashore is faster than fiddling with cylinders. The main thing in terms of increasing the amphibious properties of the all-terrain vehicle was the replacement of the PLM with a stationary but retractable propeller driven by the vehicle’s engine.
The two-blade propeller with hollow blades is welded, as they say, “on the knee” with approximate observance of the angles. Its diameter is 700 mm, and its pitch is about half a meter. The bracket with the screw rises up and is fixed on the rear side when there is no need for a water propulsion device, that is, on land. On the water, it leans back, while its drive shaft engages with the clutch, which is based on the VAZ-2108 wheel drive. The clutch rotates constantly, if any gear is engaged, the shaft goes to it from the free output of the gearbox.
The next test tests showed that now the maximum speed on water is 6.3 km/h, comfortable – 4 km/h. This is already something! Two people hanging on one side with the side pontoons folded down cannot overturn the all-terrain vehicle. It is optimal to walk through a body of water by engaging 4th gear in the gearbox and maintaining engine speed around 2000 rpm. In 5th gear, the engine is clearly overloaded and overheats.
During one of the swims, the wheels caught the muddy bottom and the car stopped. The wheels did not help, but in 3rd gear, after giving the gas, I managed to get out using the propeller. By the way, once later, already on a hike, we successfully overcame about half a kilometer of solid silt. When hitting aground or rocks, the propeller drive simply jumps up and then lowers itself. But the vibration in some operating modes of the propulsion system was annoying. It turned out that at 500 rpm and above, rapid “boiling” of water around the propeller begins. The problem was solved by widening the blades by 50 mm on each side and reducing the diameter of the propeller to 540 mm. Several routes taken have shown that this all-terrain vehicle is quite successful as an amphibian, and there is no point in working in this direction anymore, so as not to spoil it with improvements.
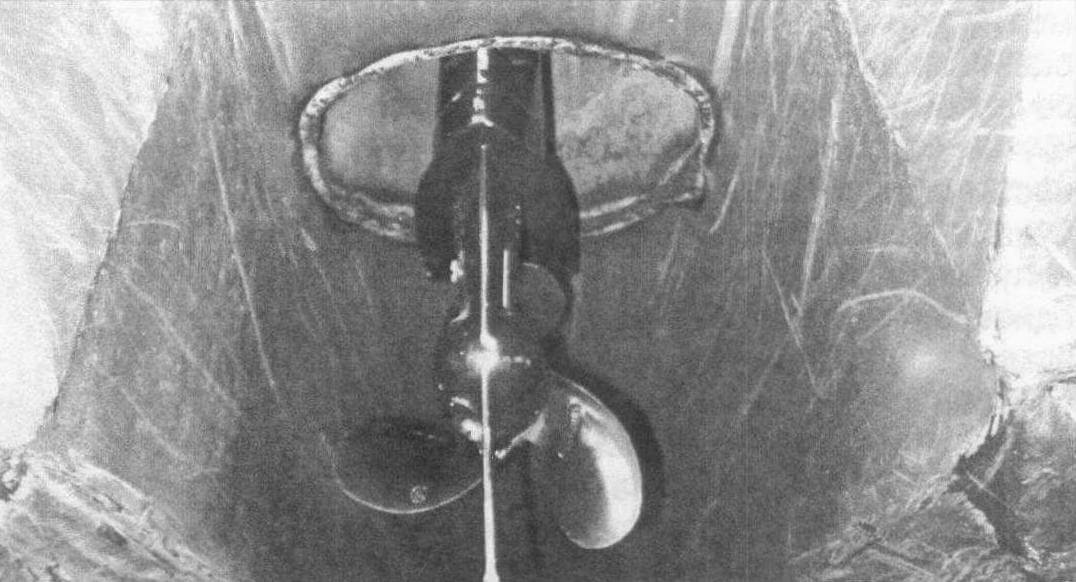
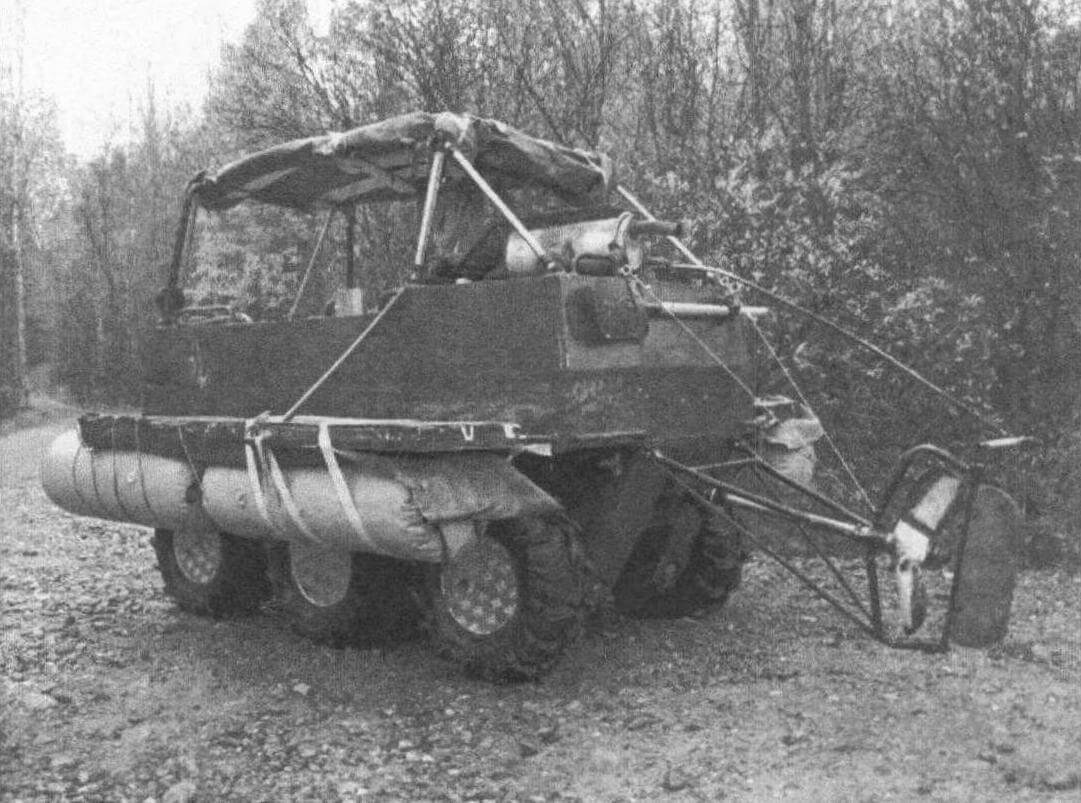
In this form, the car successfully drove us around for four years, and by and large it suited everyone.
But, as you know, there is no limit to perfection! At one point we started thinking about serious modernization. The main goal is to move away from differential steering to frictional steering, which is used on serious, industrially produced tracked vehicles. The fact is that the design with the differential is simple in implementation, but has a significant drawback – does not provide 100% of all -wheel drive on the wheels of both sides. For example, if you climb a hill with obstacles, then when hitting on the irregularities of the wheel of one of the sides, the clutch is lost and immediately scrolled. This causes a stop, because on the wheels of the second side the craving immediately falls. With proper dexterity, this can be foreseen and change the trajectory in time, but sometimes there is no place for maneuver, then you have to go back and start the race again. A similar picture is observed when climbing the sand. When performing a turn on slightly carrying soils, say, in a swamp, the all -terrain vehicle slows down until a complete stop, and sometimes it is already impossible to move after that. And when using the on -board control mechanism of the friction type, just turn off one side and not to slow down: due to the high resistance, the machine turns itself, practically without losing the course. And finally, the conical differential from the car is simply not intended for such operation. A little earlier or a little later, but it will certainly break due to the wear of the crosses and satellites. Moreover, it is impossible to predict such a breakdown, but if it occurs, then the machine will completely lose the move! ( Approx. Ed. In the instructions for some cars, it is even indicated that one of the wheels should be avoided, since this can lead to the output of the differential out of order. What can we say about the “on -board” all -terrain vehicle with such a node in the transmission when an undesirable mode of operation the latter arises regularly.)
The friction-type rotation mechanism is borrowed from the GAZ-71 caterpillar conveyor. He controlled control from mechanical rods to hydraulics, using the clutch cylinders from the VAZ-2101. Ribbon brakes are replaced by disk. The gearbox itself, according to the terms of the layout, is reversed by rearranging the driven gear of the main pair to the other side relative to the host. It was required to put the case so that the gear did not hurt for it. Half of the springs in the baskets of clutches was also removed to reduce the force on the steering wheel: after all, the shoulders of the steering wheel are much shorter than floor levers in the conveyor.
The steering shaft was shifted relative to the steering machine (four main hydraulic cylinders from the Lada, control of frictions and brakes). The steering wheel became closer to the center, due to which the space under the right leg increased. This is especially true in winter, when the driver in thick warm clothes, and even in felt boots.
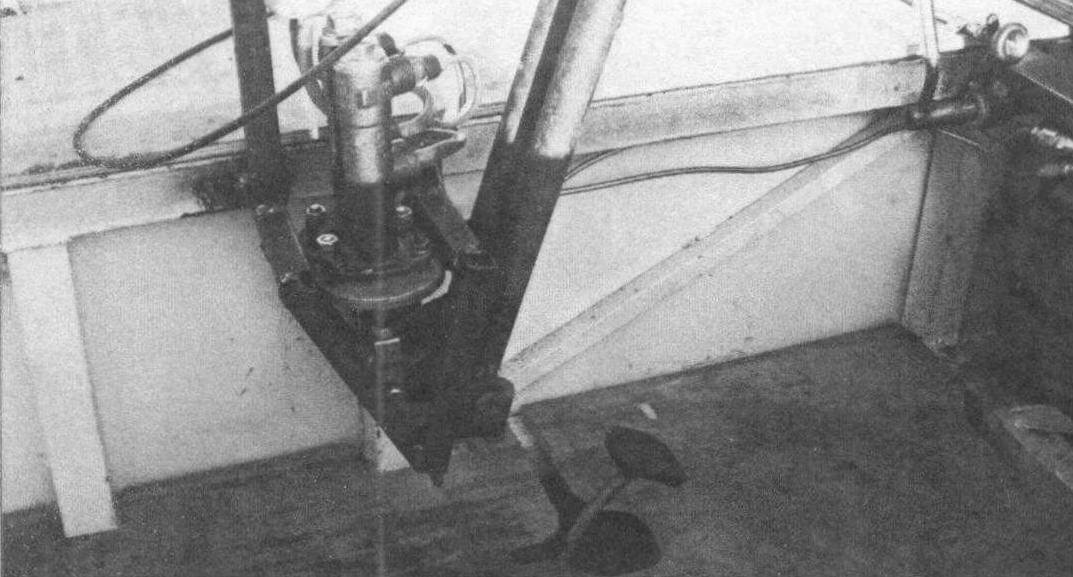
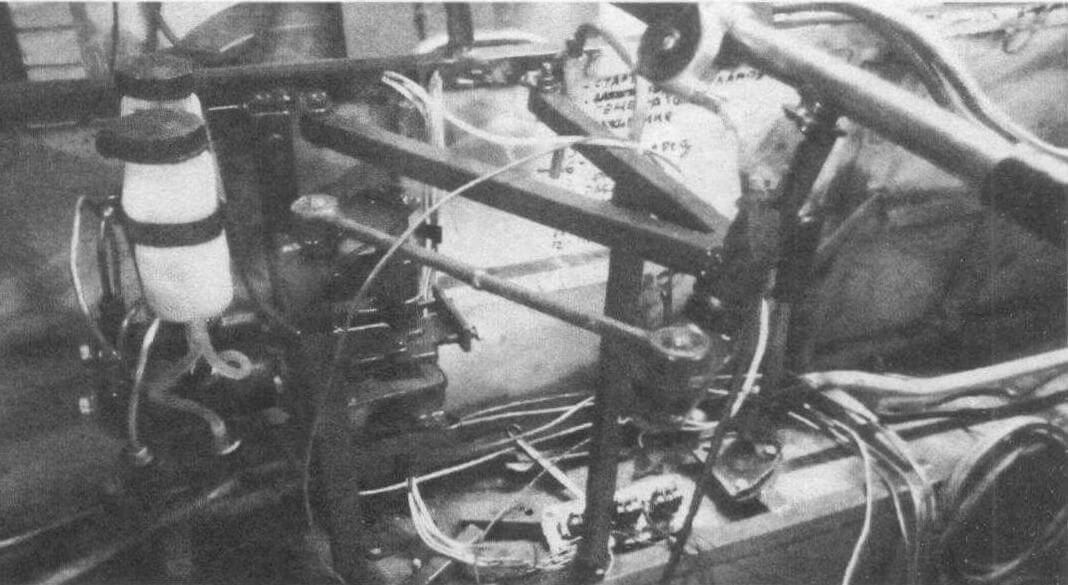
The bottom of the all -terrain vehicle at first was not flat, but had a deep tunnel in the middle. It seemed to us that with a continuous wide bottom, the car would stick to them in a swamp or in the snow, and then helplessly rotate with all six wheels. And with this form of the case, there is a chance to slip an ambush place, sliding as if skiing. But the expected positive effect was not observed, therefore, during the modernization of the all -terrain vehicle, the bottom became almost flat.
At the site of the central tunnel, a compartment for things was organized, moreover, it became possible to lower the ICE and thereby lower the center of gravity of the machine, which is also not bad. Along the way, we decided to make the main lower frame removable along with the power plant installed on it and the rotation mechanism – this noticeably facilitated maintenance and repair.
Let me sum it up. The all -terrain vehicle turned out to be good, quite relevant to the tasks, but at the moment this project, it seems to me, has completely exhausted itself. The next stage of our work is the construction of a new machine of a similar type, but with a suspension, since without it it shakes so much on the bumps that the ride becomes not a joy.
“Gusyanka”
So, we made an amphibian who is not afraid of dirt and stones, knows how to swim, but in deep snow our all -terrain vehicle refused to go: he simply went to the bottom, after which he helplessly rotated with wheels. A similar effect was observed on a very soft swamp. Meanwhile, the way to correct the situation has been known for a long time – it is necessary to “wrap” the wheels with caterpillars. Even the branded models of the mentioned brands can be understaffed with such removable additional movers. They stand, like all options, of course, is expensive. We set ourselves the goal of making them independently from light, inexpensive and affordable materials. And since the all -terrain vehicle still spends most of the time on wheels, these caterpillars should quickly and without the use of significant efforts to mount the car in the field, and it is also easy to act. Well, of course, they must be compact enough to be carried with them.
The first option was made of polypropylene water pipes with a diameter of 25 mm. Each path of this version consisted of a horizontal site, to which vertical tails were attached on both sides. Plus there were short processes through which a polypropylene rope was passed, connecting the tracks into a single tape. We filled the internal cavities of the tubes with construction foam. It turned out that one such track weighs 297 grams, and he not only swims himself, but is also able to keep an additional 200 grams of cargo afloat. And this means that the caterpillars of the car that appeared on the water will give it to it, although insignificant, but additional buoyancy.
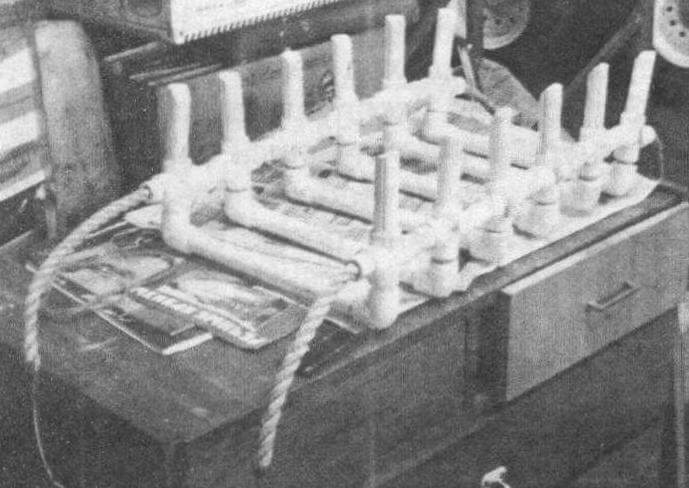
To implement this design, a fair amount of connecting “crosses” was needed, and we had to cleanly buy them in all the nearest plumbing stores. The connection of the elements with each other was carried out with standard welding of plastic using the appropriate heating machine.
The distance between the tracks is 100 mm. The rope is used with a diameter of 14 mm. To connect the caterpillar is a castle, which is a detachable path from a steel profile pipe. The rope in each half of the castle can be allowed and clamped – this is necessary to pull the caterpillar, which is especially relevant in the initial period of operation.
After the first caterpillar was collected, they ran into it during frost at minus 8 degrees. There were fears that plastic could not withstand the cold, but everything went smoothly.
Having gathered a full set of motors, they conducted more serious tests. The load is 3 people, the temperature is about 10 degrees below zero, the snow is up to 60 cm, without infusion, loose. While driving to virgin lands on a rolled road, they realized that the speed decreased markedly compared with the movement on wheels. But they went very confidently along the untouched deep snowdrifts. Although, to be honest, there was practically no margin of course, and the turns were difficult. And after a while, the wheels began to slip inside the caterpillars – it was even visually noticeable that they stretched out and the tracks icled. The side ropes were pulled by 40 mm and rushed into the snow again. Rides! The all -terrain vehicle falls about 30 cm, and the snow between the tracks is not squeezed out. And when they crossed a ditch filled with stones, they broke one path, but this did not affect the further movement.
They were glad that after four-hour tests of wear or any critical damage to the tracks were not found. Therefore, we were even more surprised by the fact that during the next test one of the caterpillars unexpectedly … fell apart for no apparent reason. 26 tracks on the one hand collapsed! After watching the video later, they determined that the tracks did not get to the wheel, it went along the side stops – and here is the result. They wrote off a breakdown on their own carelessness.
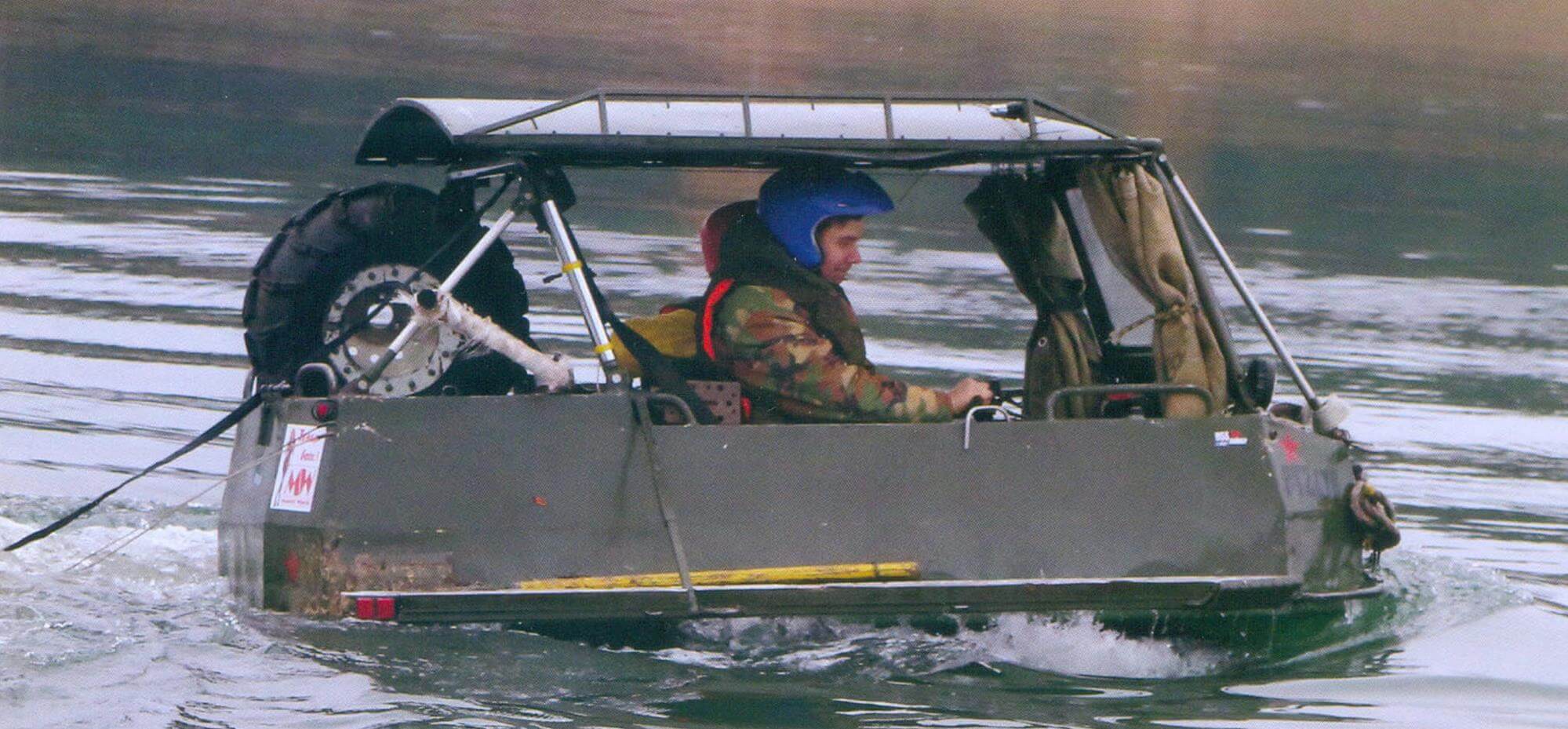
The next use of home -made caterpillars took place in the summer during a complex campaign. A great thing, however, turned out! For two days of movement along swamps with a load of 1.5 tons, we have never stuck. Excellent clutch, good buoyancy, there is no need for constant suspenders. True, on stones and logs you must be neat.
The next winter, the caterpillars tried again. And … again a breakdown! Conclusion: This design is not suitable for winter operation. Another material for the tracks is needed and, possibly, their other design. I tested the option of making tracks from PND tubes. He bent their ends, warming up with a hairdryer. What can I say … It happened so -so. The wall is thin, the resource of such a track is clearly small. The tubes are needed thicker. And then I made the tracks two -layer: I inserted a pipe with a diameter of 32 mm into a pipe with a diameter of 40 mm. But with a hairdryer, such a sandwich can no longer soften. I had to make a tank in which the oil is heated. Having lowered a double pipe into it and warming up, you can then bend it. It was important to choose the heating temperature. The experimental method stopped at 140 ° C, and into the tank built the thermostat. And in order to bend the heated pipes (and, at once three), made a special pipe bend.
Inside, the tracks are filled with vilotherm (foamed with polyethylene). Slips of polypropylene pipes are inserted between the sections, inside of which the connecting rope is stretched. The castle is cooked from steel.
The new “gusy women” were checked with a 17-kilometer mileage along the frozen lake and forest. A lot was slipping on the stones scattered along the shores. There was little snow on the lake – it blown away, but there were definitely half a meter in the forest.
At first, the movement went with stops, but soon I realized what was happening. It’s just that the caterpillars stretched out, the sag between the wheels reached 100 mm, but they were not going to subside. He pulled it, and everything worked out. Although on the ice and the rolled road there was a sliding of the all -terrain vehicle in the transverse direction.
He noted that if you cure the caterpillar in the snow, cut off the already packed snow (for example, when turning), then the clutch, and therefore craving, falls strongly. Blowing on the slope, it is no longer possible to move again. Moreover, having rolled back, it is not possible to rise in its own trace. But next to him, along the new trajectory, this can be done without any problems. At the same time, there is no side sliding on the snowy slopes, the all -terrain vehicle holds well.
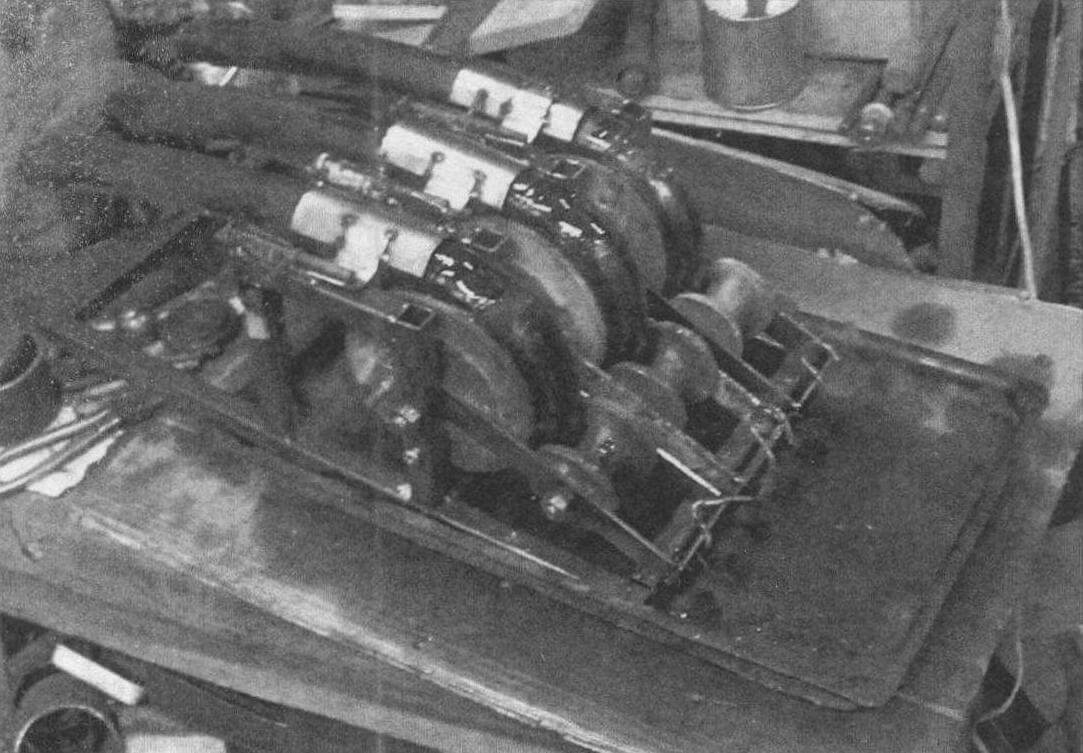
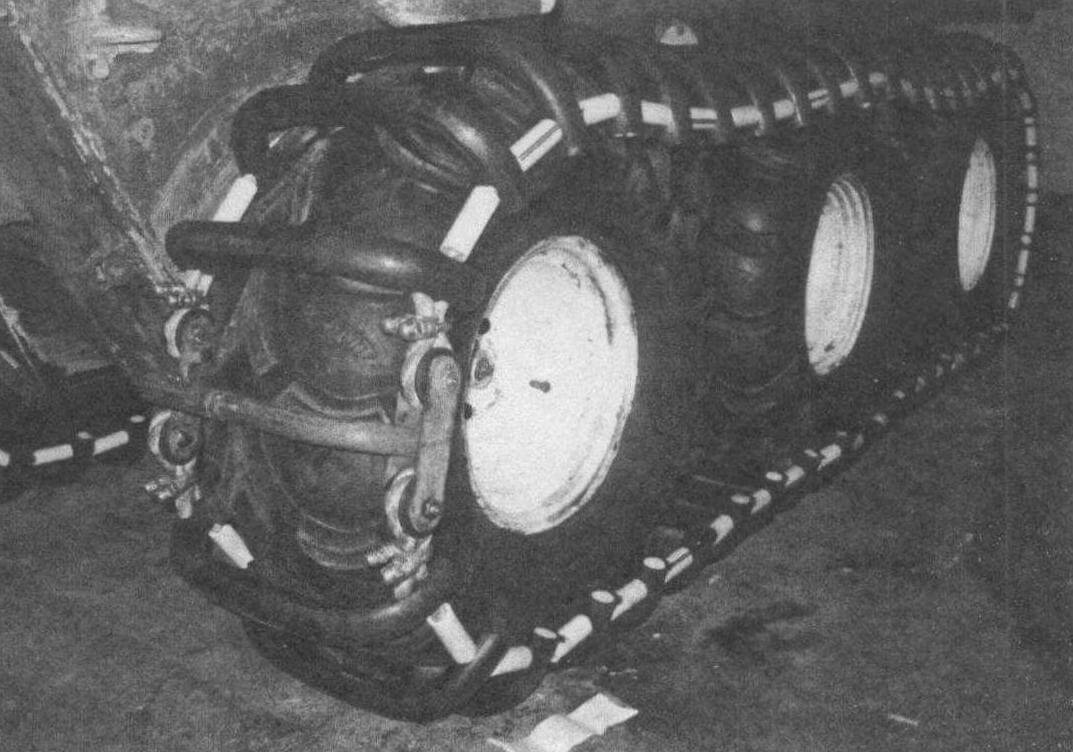
During the operating season, the tracks did not bother and did not erased, and in general the caterpillars did not require a single repair. It seems to me that we received additional movers for more than one year. They will come in handy on a new all -terrain vehicle. Their installation takes no more than 15 minutes, and the effect is colossal, which, in fact, was demonstrated on the “All-terrain vehicle-Trophy 2018”. Of course, the extra 32 kg on the upper trunk on the trip is not pleased, but now there are practically no barriers to our technique!
Alexey Soloviev, Petrozavodsk