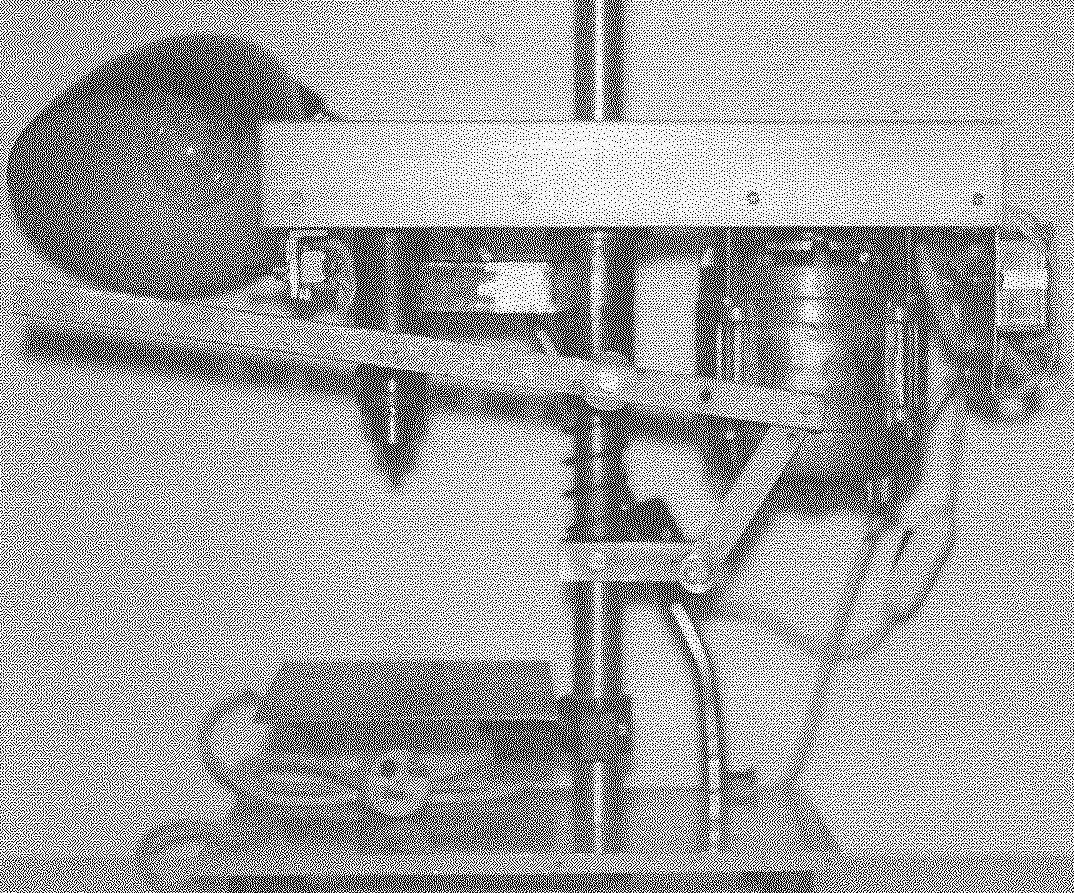
I decided to use the first option.
Machine design is quite simple, and the size was relatively small height x length x width — 410х315х250 mm. the Latter quantity is determined by the width of the base (Desk clerk) made of duralumin sheet thickness of 10 mm. Foundation “sprung” rubber feet from some of the devices that are attached at the corners at the bottom. On the basis of the attached steel rod with a diameter of 28 mm and a height of 400 mm, which contains all the mechanisms.
As for the mechanics of the machine, it can be divided into three main nodes drive, drilling head and feed mechanism of the tool to the workpiece.
The basis of the drive motor from obsolete and unneeded because of the washing machine “Tula”. Motor power 180 watt 1370 rpm. It is mounted on one shoulder of the rocker — steel plate 4 mm thick. by the Way, the engine didn’t even need repairs, and only maintenance is cleaning the manifold and remove the graphite dust from the slightly worn-out brushes.
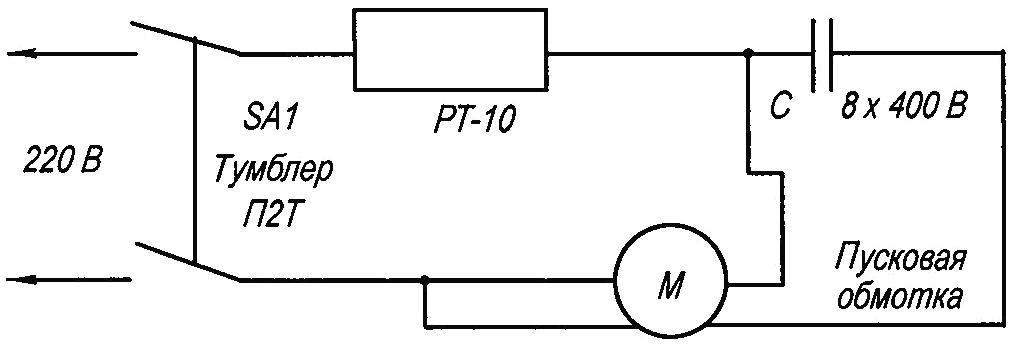
The electrical circuit connecting the motor to the alternating current network with voltage 220 V
On the motor shaft planted firmly keyed drive pulley V-belt transmission. The driven pulley similarly mounted on a shaft the drill head located at the opposite end of the rocker arm. The torque from the pulley to the pulley is transmitted to the annular wedge belt profile to “0” and a length of 750 mm. Belt — industrial manufacturing, and pulleys — homemade, dural, two. Turning or moving the pulleys on the shafts of the motor and drilling head, you can get different rpm of the cutting tool.
Drilling head — the most important site of the machine. In its manufacture it was necessary to follow a strict alignment of all parts to minimize the runout of the tool and to provide the required tolerances for fit bearings. And therefore, having no lathe, no experience on it, ordered this node to specialists.
The shaft in the drill head installed in two 201-x bearings. Tool holder — Chuck with taper No. 2 — industrial manufacturing.
The actuator is mounted on the yoke, and the yoke, the middle portion is attached with four M4 screws to the main bushing on the rod rack.
For security V-belt drive is closed from above by a cover made of 2-mm dural sheet.
Drilling head with the rocker only docked; but rather attracted to it a long screw-tapping screw through the console connecting the bearing housing of the head with the main bushing. But the frame, bracket and bushing are connected rigidly by welding.
Bush has the ability to freely (without excessive play) to move downward under the pressure of his hands on the handle-lever, and upwardly under the action of the spring.
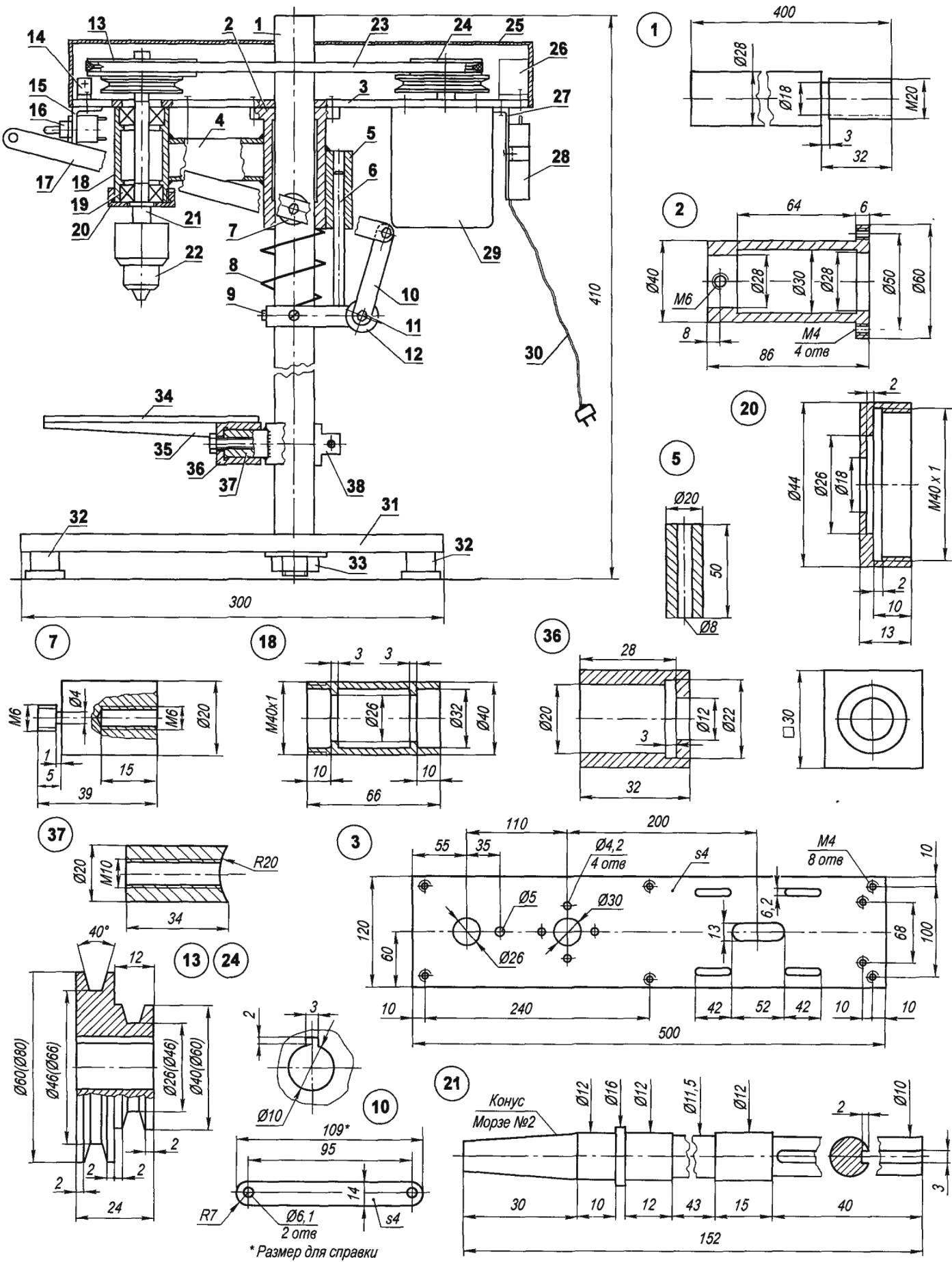
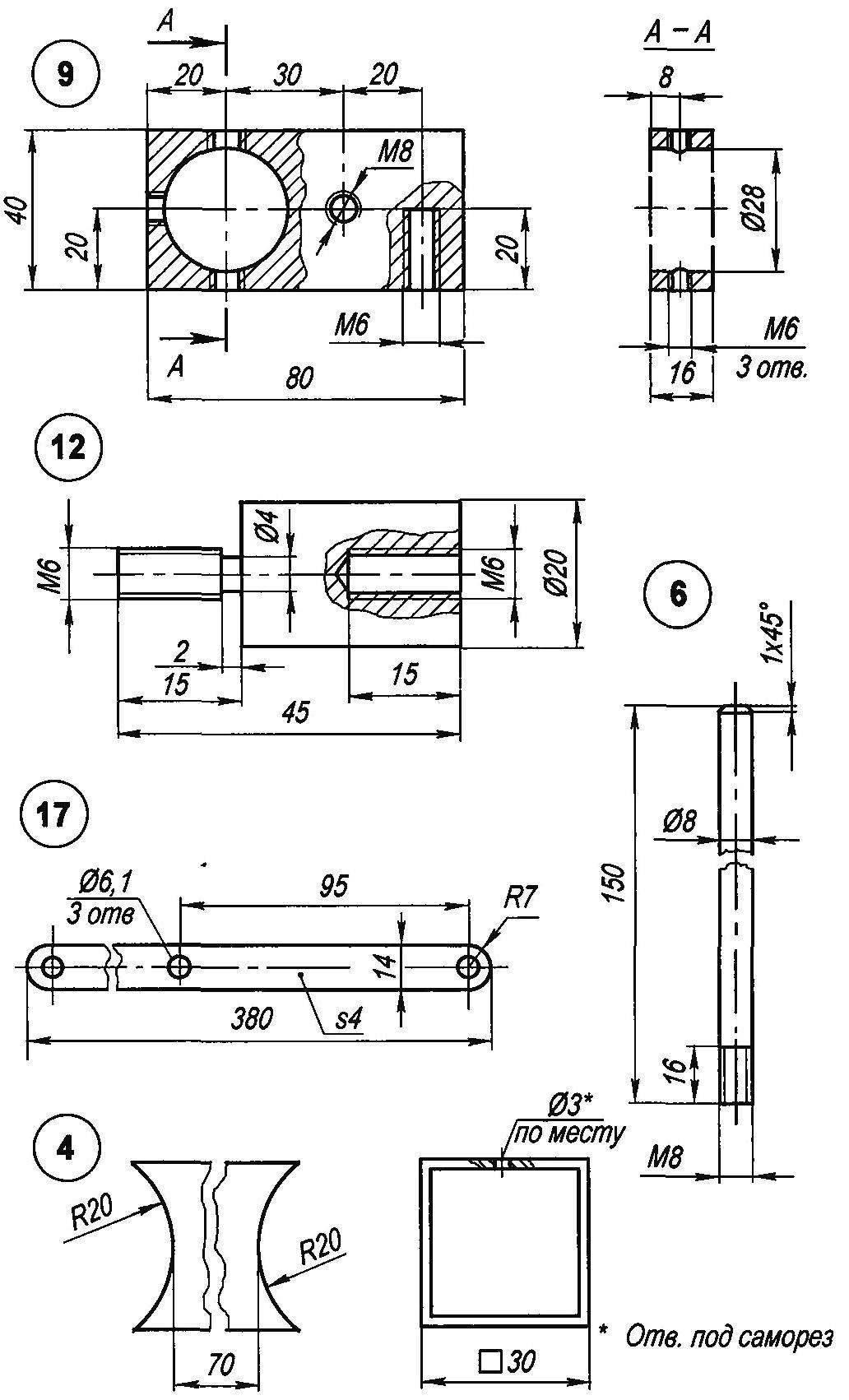
Lapping mini-lathe:
1 — the main support leg (steel, lap 28); 2 — main bushing (steel, circle 60); 3 — rocker (steel, sheet s4); 4 console drilling head (steel pipe 30×30), 5 — guiding bushing (steel, circle 20); 6 — guide pin (steel, lap 8); 7 —spacer arm (steel, round 20), 8 — a spring normally decompressed, 9 — clamp (steel, sheet s16); 10 — thrust (steel strip 14×4), 11 — axis hinge (screw M6, 3 piece); 12 — spacer, thrust (steel, round 20), 13 — driven pulley (duralumin D16, circle 80); 14— an arm of fastening of a casing (dural area 15×15, 6 PCs); 15 — mounting bracket toggle switch (dural area 30×20); 16 — switch П2Т; 17 — the lever-arm (steel strip 14×4); 18 a bearing housing (steel, lap 40); 19 — 201 bearing (2 PCs); 20 — cover housing bearing (steel, circle 44), 21 —shaft (steel 45, range 16), 22 — cartridge No. 2; 23 — V belt (type 0, L=750), 24 — drive pulley (duralumin D16, circle 80); 25 —a drive housing (aluminum, sheet s2); 26 — thermal relay RT-10; 27— panel mount capacitors (steel, sheet s2); 28 — condenser 8 мкФх400В; 29 — motor n=180 W, n=1370 rpm (from the washing machine “Tula”); 30 — network cable; 31 — base (made of anodized aluminum, the sheet s10); 32 — feet (rubber from devices, 4 items); 33 — nut M20 (with washer) securing the stand to the base, 34 — movable table (steel, sheet s4); 35 — Klondike (steel, sheet s4), 36 — rotatable bushing (steel, square 30); 37 — axis (steel, circle 20); 38 — kremowy clip with screw M6
Fulcrum positioning mechanism is a clamp, which had previously been put on the rack and fixed on her three lock screws M6. Depending on the size (height) of the workpiece “fulcrum” can be moved higher or lower on the rack.
The ability to rotate the fulcrum on the bar (and with it the drill) at a 90° angle and installation of the machine on the edge of the table allows to drill holes and long-length (length a little above the table) narrow the details and even at the edges wide.
For greater ease of handling small parts, hold in tisochki, or even pliers and made a small work table. It has the ability to turn around its axis and around the main stand. The first option allows you to drill holes in parts at an angle to their surface. He, like the clamp, is fixed on the main stand but not the screws, and klimovym clip.
Protecting from overload thermal relay and capacitors to ensure the start-up and normal motor operation, is also taken from an outdated washing machine “Tula”. Wires and switches of unnecessary appliances.
Y. KURBAKOV