I want to offer readers of the magazine an interesting, in my opinion, and useful device – a portable wind power station. In the summer, my family and I often relax on the shores of the Azov Sea. Everyone understands that vacation becomes much more comfortable if there is a source of electricity. After the windmill was manufactured, there was no longer any need to save on the on-board network of the Zaporozhets car; it became possible to constantly use the radio, lighting, Sapphire-401 TV, and during even a slight wind, the car refrigerator.
I have made several versions of wind power plants. The one currently offered is the simplest and most accessible.
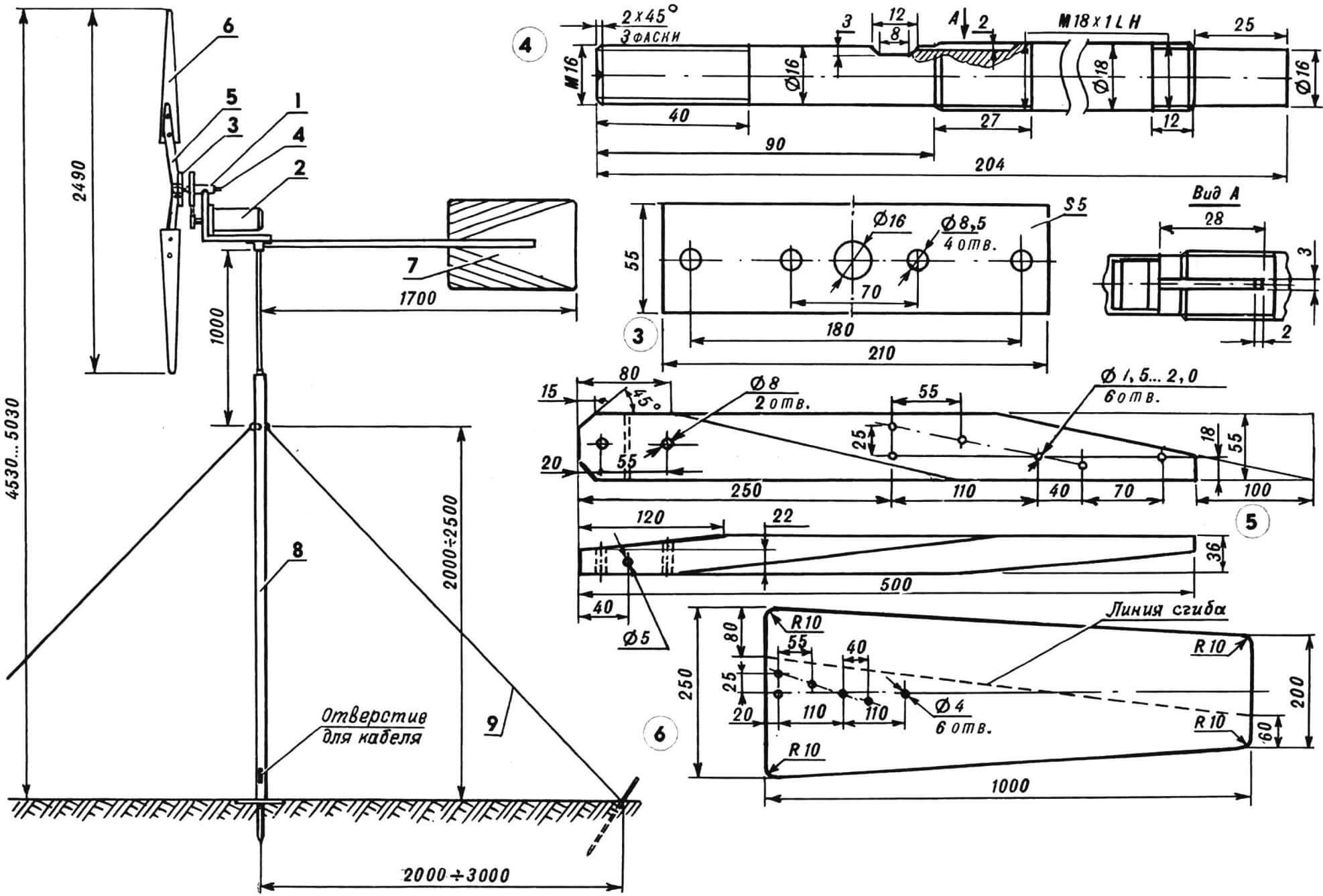
1 – frame, 2 – generator, 3 – plate, 4 – shaft, 5 – spoke, 6 – blade, 7 – stabilizer, 8 – mast, 9 – guy wires.
A DC electric motor (U=48 V, I=15 A, n=1200 rpm) is used as a generator, the main unit of any power plant. The rotor rotates at a frequency of less than 500 rpm, and as the wind increases, the speed does not increase, but the charging current increases. A chain sprocket (Z=10) from a D-6 bicycle engine is installed on the generator shaft. The driven sprocket (Z=48) and the entire carriage assembly are taken from an adult bicycle. The frame had to be sawn and shaped into the desired shape, and then welded. The generator is attached to the frame using M8 bolts.
Before installation, the roller chain with a pitch of 1–2.7 mm must be boiled for several minutes in engine oil and then wiped with a rag. It is better to use a motorcycle chain: its service life is much longer.

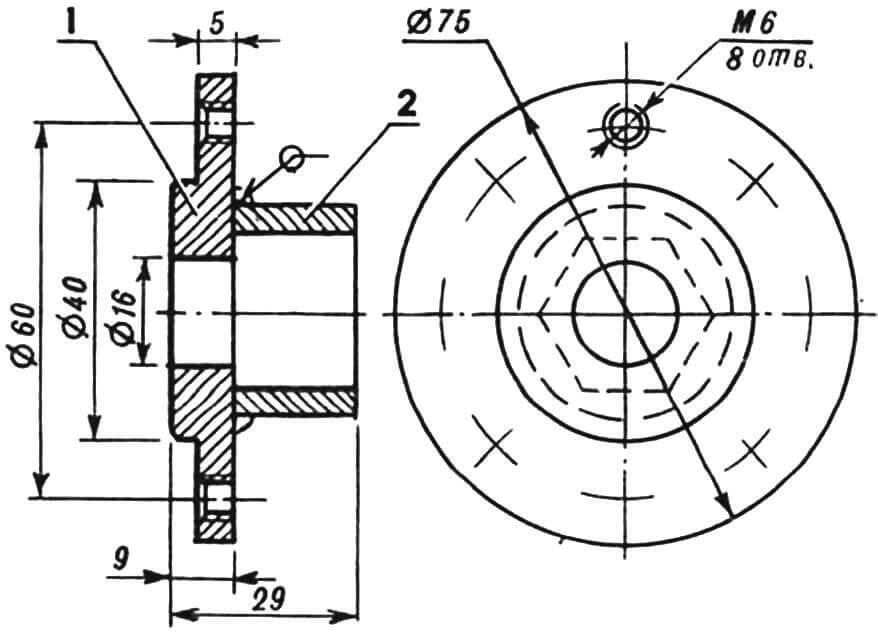
1 – disk, 2 – glass (socket wrench head 24).
I machined a new, longer carriage shaft. When assembling the carriage assembly, it is necessary to lubricate the bearings with Litol-24 or CIATIM grease. Then an M16 nut is screwed onto the shaft until it stops, a flange is put on (Fig. 3) and clamped with another nut. The disk is attached to the flange with eight M6 bolts (Fig. 4) so that the protrusion of the flange Ø 40 mm fits into the hole in the disk. The flange is made as follows: a disc is turned from steel on a lathe (Fig. 3, item 1), then the head of a 24mm socket wrench is cut off from the side of the holder to a height of 20 mm, both of these parts are aligned with each other coaxially and welded. In this case, if only two blades will be used, the disc and flange can be replaced with a steel plate (Fig. 1, item 3).
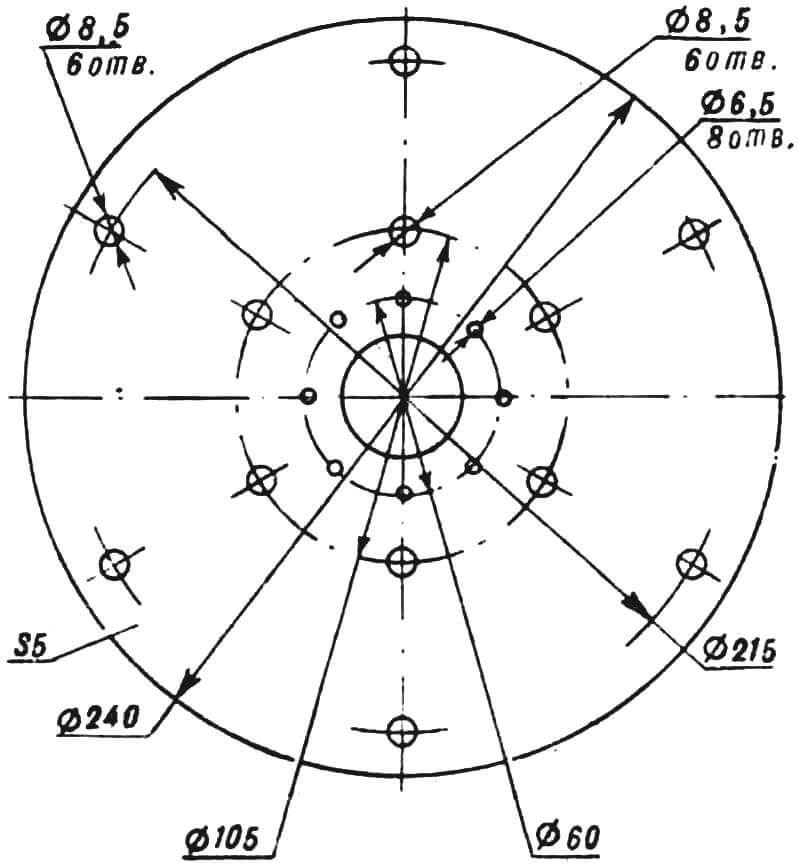
The blades are made of 2 mm thick duralumin. After manufacturing, they must be given an arched shape. To do this, the blade must be placed on something round (for example, a pipe Ø 800 mm and at least 800 mm long) and bent along the line shown in the drawing. Then the blade is attached to a wooden spoke using six screws, which is made from a planed wooden block 36X55X500 mm. The spokes, in turn (using two M8 bolts each), are attached to the disk or plate.
To use weak winds, 5-8 m/s, I made six identical blades. In strong winds, I recommend using only two. But even with a small wind with two blades, a windmill produces a current of 4-6 A at a voltage of 14 V. In principle, the length of the blades can be reduced to 80 cm.
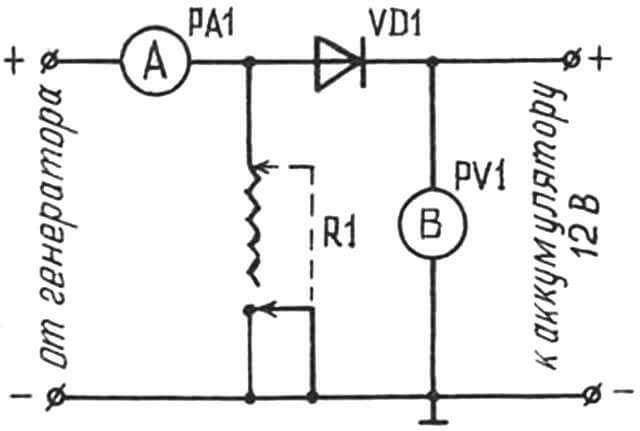
A pin (a piece of pipe 120-150 mm long) is welded to the bottom of the frame, which fits into the mast pipe with a small gap. Before installation, it must be lubricated and a brass washer placed on which the entire assembly will easily rotate in a horizontal plane and, with the help of a removable stabilizer, stand against the wind.
The mast, 3–3.5 m long, is made of a water pipe Ø 34 mm (at least). A support platform (S 2-3 dm 2 ) is welded to the bottom of the mast, at the end of the pipe, to which, in turn, a pin 150 mm long and Ø 12-15 mm is welded. When installing the mast, the pin is simply stuck into the ground. At a distance of 1 m from the upper end of the mast pipe, along its circumference, I welded four M10 nuts to secure the guy wires. It is better to make the mast in two parts – for ease of transportation on the trunk of a car. In stationary conditions, it can be made from a different material and longer. The installation of a wind system is well described in the article “ Wind Daisy ” (“M-K”, 1988, No. 4).
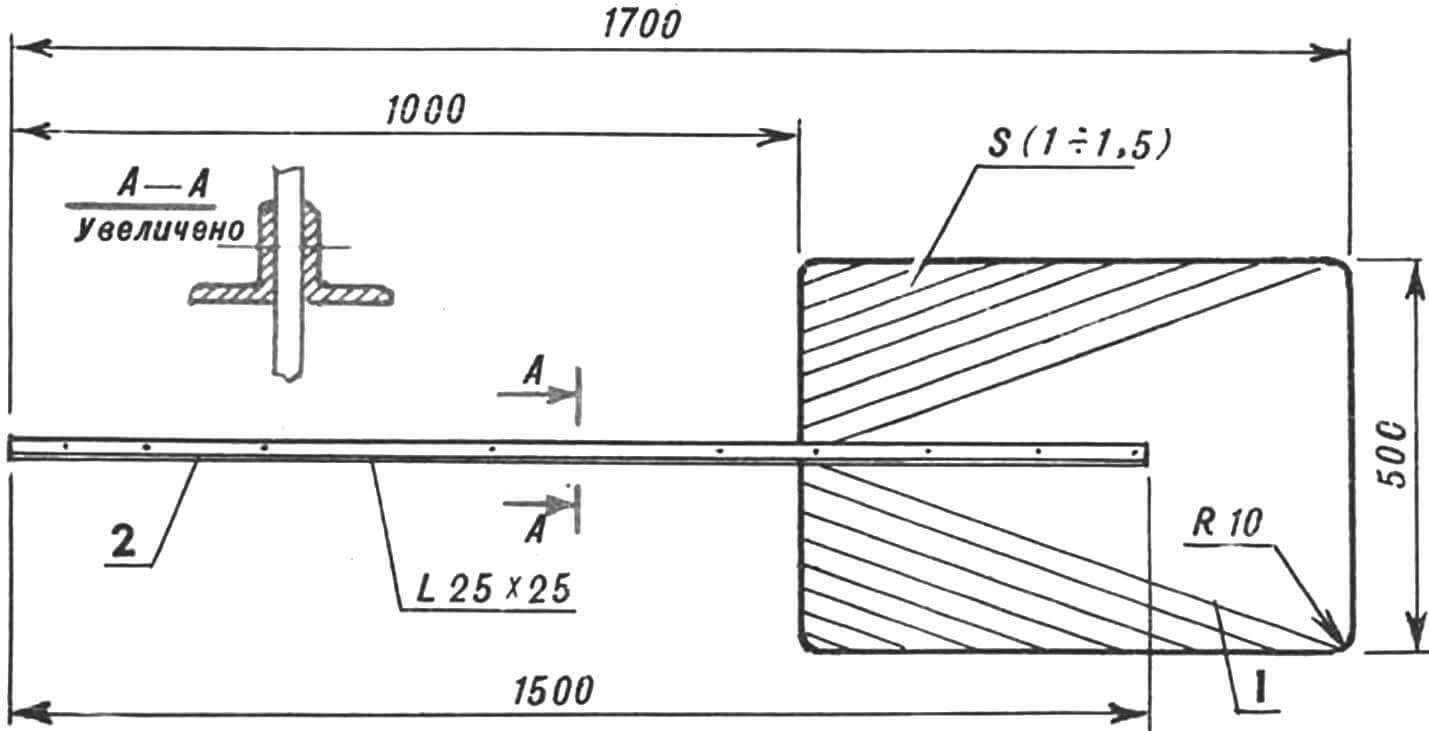
1 — stabilizer keel (duralumin), 2 — beam (angle, duralumin).
A few words about the remote control and battery charging. It includes any type of ammeter and DC voltmeter, but small sizes are better. An ammeter for a maximum current of 20-30 A, a voltmeter for 1 5-30 V (assuming that the car’s on-board network is 12 V). Decoupling diode – any type for a current of 20 A. As a rheostat, you can use a wire resistance type PPB-50G at 5-10 Ohms, 50 W with modification: you need to remove several turns of wire from the left edge so that the circuit is broken in the operating position. You can use any other resistor that can withstand a current of 20 A for a few seconds. This is why this is needed: if the battery is fully charged and the voltage on it has reached 14-14.5 V, then we short-circuit the generator with a resistor for three seconds and thereby stop it, while the current is 3-4 times less than the operating one. You can then tie one of the blades to the mast. It is impossible to short-circuit the generator abruptly, as the mechanism may break. Manually, even in medium winds, stopping by the blade is very dangerous. It is also impossible to reduce the charge current with this resistor, since it will burn out in a few tens of seconds. The charging current can be reduced by adding the number of lamps plugged into the socket. The current-carrying wire is any soft cable (preferably rubber-coated) with a cross-section of 3-4 mm 2 , which is passed inside the mast pipe.
Operation of the wind power plant for 10 days, even with two blades, showed that this energy is sufficient: after all, there is wind at sea almost every day.
V. KUKLIN, Zaporizhzhya