Readers of “M-K” have long been familiar with the enthusiast of homemade soil cultivation equipment, amateur designer from Nizhny Tagil, Grigory Ivanovich ODEGOV. He was the one who managed to develop one of the most efficient motor winches, which outperforms power tillers, motor cultivators, and even microtractors in terms of productivity. And all this despite the fact that the engine of Odegov’s motor winch is nothing more than the power unit of an old “Vyatka” scooter.
Today, we present two pedal-powered cable winches. One was developed by G.I. Odegov, and the other is a modernized version of Odegov’s original design, developed in the creative laboratory “Eureka.”
According to the designer of the pedal winch, this soil cultivation unit with foot drive is significantly more effective than both a shovel and a towed plow operated by one or two people.
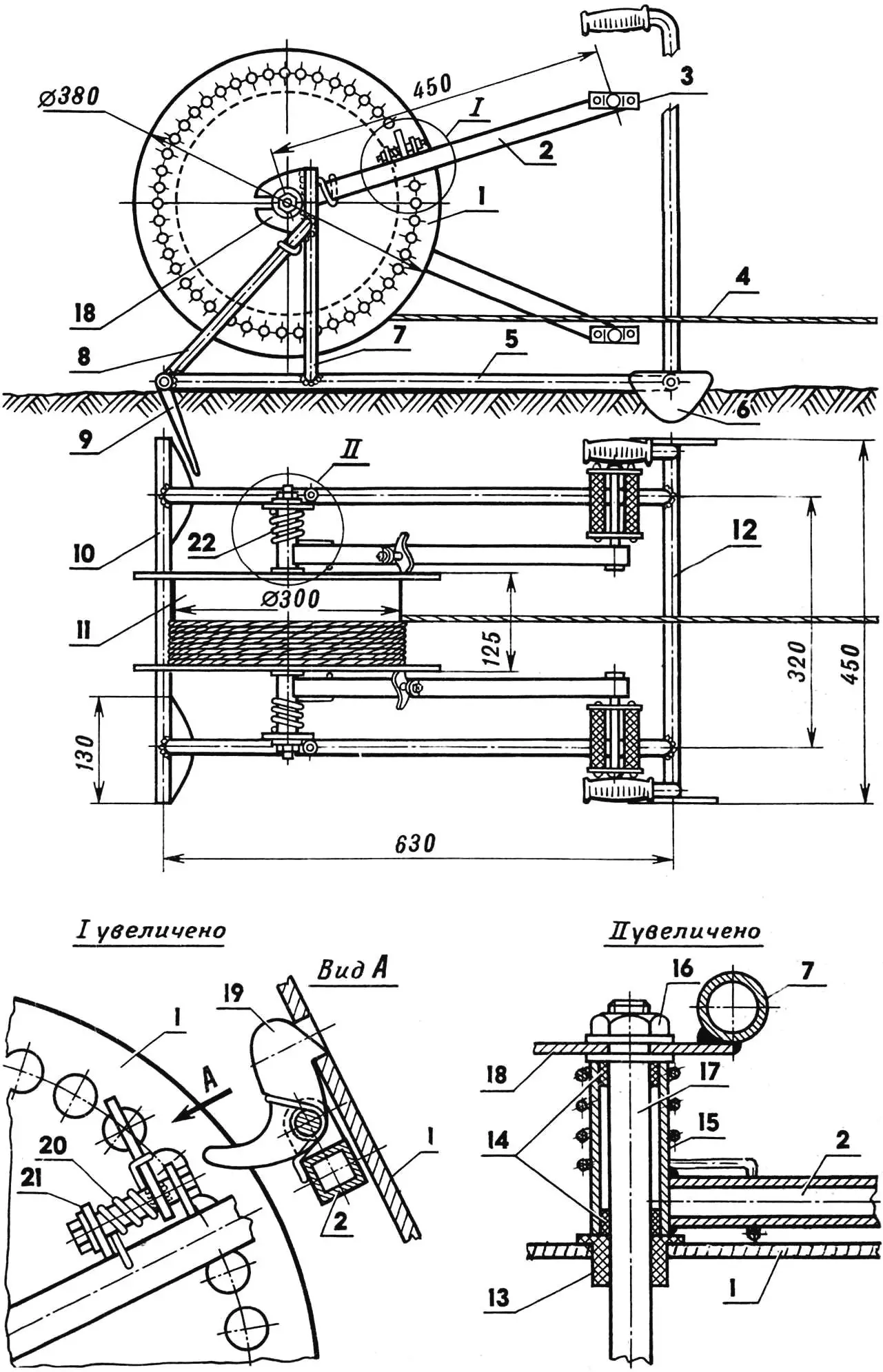
1 — drum cheek, 2 — drive lever, 3 — pedal, 4 — cable, 5 — longitudinal frame element, 6 — latch, 7 — stand, 8 — brace, 9 — anchor, 10 — rear crossbar, 11 — drum, 12 — front crossbar, 13 — drum bushing, 14 — inserts, 15 — drive lever hub, 16 — nut with washers, 17 — drum and drive lever axle, 18 — flange, 19 — ratchet pawl, 20 — ratchet spring, 21 — lug, 22 — return spring of drive lever.
G.I. Odegov’s pedal winch is built as follows. Its base is a lightweight tubular frame that supports a drum whose cheeks are ratchet wheels. Swinging pedals with ratchet latches are mounted on the same axis. Both pedals are spring-loaded to return to the top position, and the ratchet latches are also spring-loaded.
The winch frame is welded from steel pipes with a diameter of 22…32 mm. The drum is made from a section of pipe with an outer diameter of about 300 mm, to which two steel discs are welded, each with a diameter of 380 mm and a thickness of about 4 mm. To turn these discs into ratchet wheels, G.I. Odegov cut asymmetric teeth around their circumference — each tooth about 5 mm deep and spaced approximately 10 mm apart. In fact, the job could be simplified by cutting every second triangular notch — this is sufficient for proper ratchet function.
It is also possible to make a simpler ratchet, as shown in our illustrations. This involves drilling holes with a diameter of 8…10 mm around the circumference of the drum cheeks. Of course, this changes the ratchet design as illustrated in the modernized pedal winch drawing.
The drive levers of this unit are welded from steel pipes, either round or rectangular in cross-section. A bushing — a short piece of steel pipe with a 20 mm inner diameter — is welded to one end of each lever, and pedal axles to the other. The easiest option is to use ready-made bicycle pedals, though it’s not difficult to make homemade ones from a steel strip about 3 mm thick bent into a U-shape. For DIY pedals, threaded studs welded to the outer sides of the levers can be used as axles.
The drum and pedal lever axle is a 20 mm diameter steel rod, with its ends machined to 30 mm and threaded for M14 nuts.
The drum of the modernized winch is a section of steel pipe with an outer diameter of 300 mm, to which two steel discs are welded — 3 mm thick and 380 mm in diameter. Holes of 30 mm diameter are drilled in the center of each disc, and nylon bushings (or PTFE, textolite, or bronze ones) are press-fitted into them.
The pedal winch can work with the same plow that G.I. Odegov developed for his motor winch. It operates in two cycles: a working cycle and an idle return cycle, when the plow is pulled back to the start of the plot; during this, the ratchet pawls are disengaged and the drum spins freely. However, a continuous (looped) cable and a pulley at the far end of the plot (opposite the winch) can be used to make both plow passes productive.