Dear editors! I am a long-time subscriber of yours, I have used many of the practical publications for home use and I eagerly await the next magazine every time: will there be something useful for DIYers there again?
In the February issue I was interested in the article about protecting country buildings from lightning. I would like to continue the topic by reading additional recommendations on the installation of a lightning rod system in individual construction.
V. SMIRNOV
Lightning protection (lightning protection) of a house and outbuildings, especially in rural areas, is very desirable, first of all, for buildings with flammable roofing (roofing felt, plastic, etc.). Lightning most often strikes roof ridges, chimneys, dormer windows, edges of gables (from the ridge to the lower slope of the roof). Taking this into account, you should take care of installing at least the simplest lightning protection system. If necessary, you can seek advice and assistance from local (district) branches of a voluntary fire society.
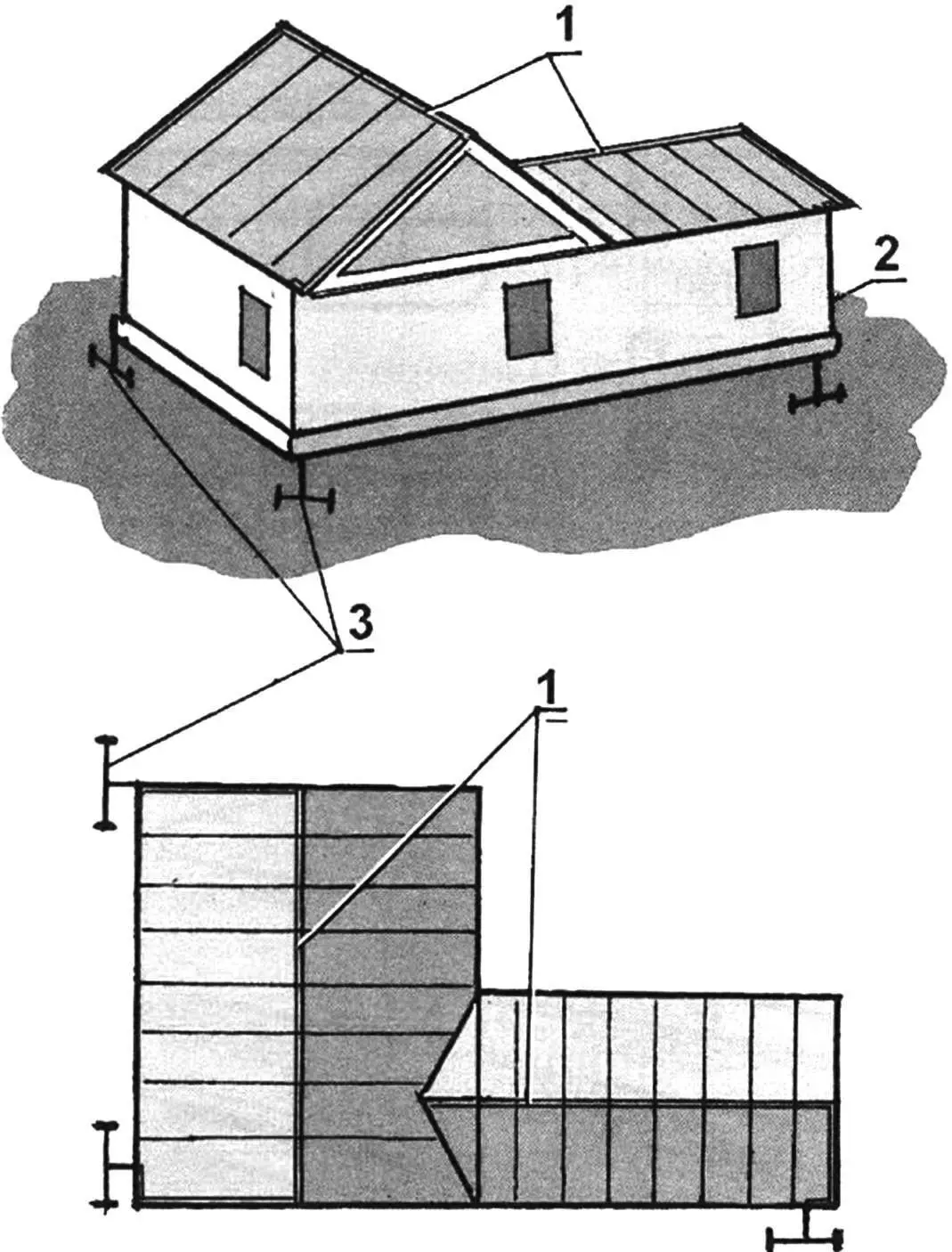
1 — lightning rod; 2 — down conductor; 3 — grounding conductor
The lightning protection system usually consists of three main elements: a lightning rod, a down conductor, and a grounding conductor. For their installation, copper or steel wire (rod) with a cross-section of at least 8 mm is required, as well as steel rods of different profiles, an angle, a strip, a pipe of the required cross-section (see Fig. 5, g – e). It is advisable to use galvanized steel materials; non-galvanized ones should be painted with waterproof paint, varnish or bitumen.
Let’s consider several options for lightning protection.
House with non-metal roofing
It requires a rod lightning rod (Fig. 2). The support for it is made from a pole or beam 100-120 mm thick and is attached to the roof rafters in the middle of the ridge. If the length of the house is no more than 15 m, and the height from the ground to the ridge is 7 m, it is enough to raise the lightning rod above the ridge by 5 m. If a line is drawn from the top of the lightning rod 1 at an angle of 45° to the ground, then everything inside this cone is reliably protected from lightning.
A steel wire with a diameter of 8 mm or more can serve as a lightning rod and a down conductor at the same time. A loop is made at one end (see Fig. 5, a – b), raised above the top of the rod (at least 150 – 200 mm), attached to the down conductor (Fig. 2), which is passed along the roof and wall, then buried in a ditch at least 1 m deep. In this case, steel angles or profiled steel, pipes and thick steel strips with a cross-sectional area of at least 50 mm 2 can serve as grounding conductors.
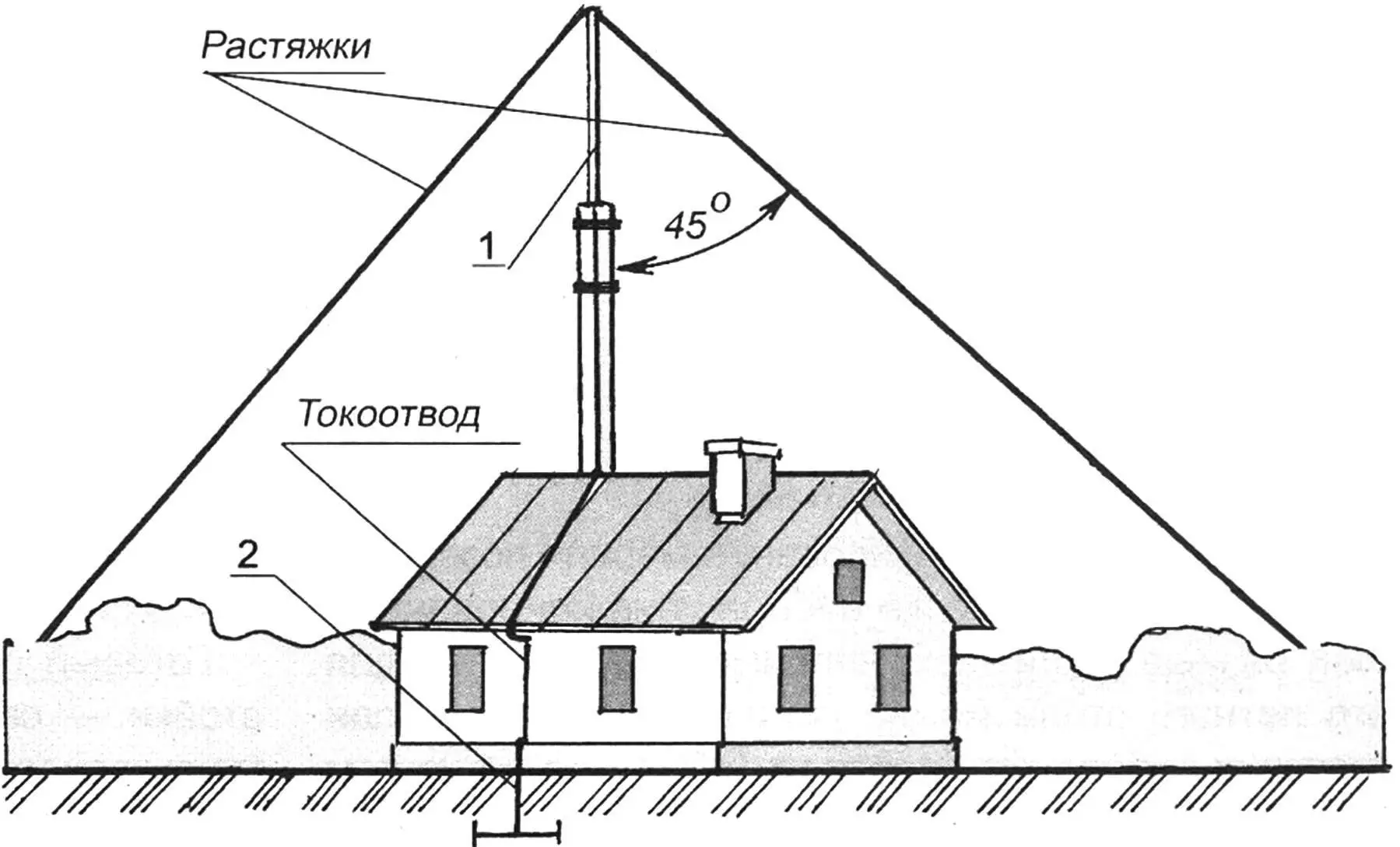
1 – lightning rod; 2 – grounding electrodes
If the roof is tiled or made of asbestos-cement slabs, the lightning rod and down conductors are attached close to it, then run along the walls to the ground electrode.
Lightning rods and down conductors should not come into contact with roofing made of wood, tar paper, or roofing felt. The distance between them and the roof should be at least 150 mm. The wire should be fixed to steel or wooden pins made of a peeled pole or planed wooden block (preferably triangular) attached to the sheathing, painted two or three times with oil paint. The lightning rod or down conductor is placed on them, with pieces of rubber hose placed underneath as an insulator. Ungalvanized parts should be painted with waterproof paints, varnishes, or bitumen. Steel cables for down conductors are undesirable due to their rapid corrosion.
A loop must be installed around the perimeter of the chimney and connected to the lightning rod running along the ridge. Instead of a loop, a rod 200-500 mm high can be installed above the chimney and also connected to the lightning rod.
House with metal roof
In this case, the simplest lightning protection is made from wire with a diameter of at least 8 mm. First, it is laid along the ridge of the roof, to the dormer window and to the extension (Fig. 1). It plays the role of a lightning rod. At the opposite corners of the house and the end of the extension, the wire is laid along the walls, forming down conductors to the grounding conductors.
Sometimes they dig a trench 0.8 – 1 m deep and lay a wire along its bottom, which serves as a grounding conductor. The down conductor can be made of a thinner wire, but in this case it must be firmly attached to the lightning rod and grounding conductor.
To divide the lightning current into parts, several down conductors are connected in parallel; their cross-sectional areas can vary from 25 to 35 mm 2 . The cross-section of all parts of the lightning conductor must be such that they do not melt or heat up strongly under the action of the lightning current.
It is recommended to lay the lightning rod down conductors along the shortest route, without creating loops or sharp corners along the way. They are attached to the supporting structure (wooden walls, poles, fireproof roofs) every 1–2 m, provided that they will not heat up when lightning current passes through them. It is better to hang the down conductors on insulators or pieces of rubber hose (it is possible to use strip rubber rolled into a tube).
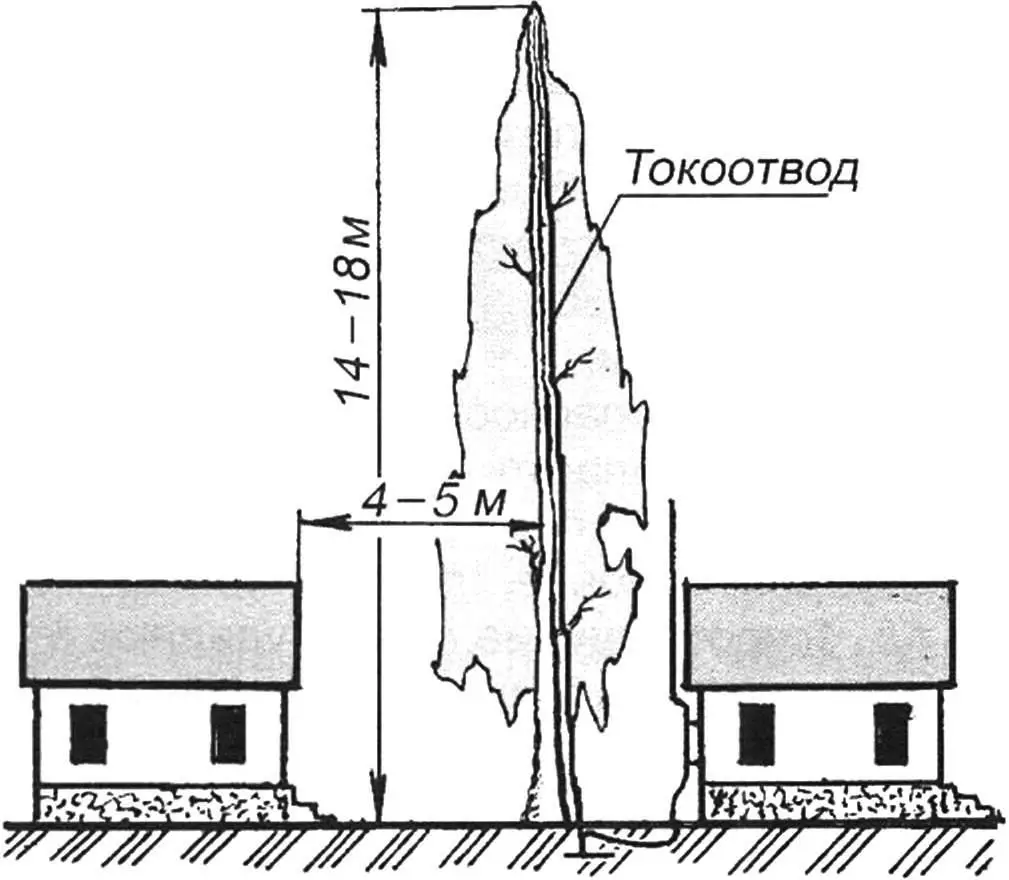
If a tree 2–2.5 times higher than the house (counting from the ridge to the ground) grows at a distance of 4–5 m from the house, a lightning rod made of steel wire (Fig. 3) can be laid along it to a height of 14–18 m.
One lightning rod can also protect a second house standing nearby, if it is at least 4-5 m away from the tree. In the part of it that is closer to the tree, a steel wire with a diameter of 8-10 mm is laid from the ridge along the wall and connected underground to the ground electrode. The wire protects the second house from catching fire when lightning “jumps”.
If there is no tall tree near the house and it is impossible to install a lightning rod on the roof, a lightning rod can be installed on a mast using a log or a pole 9-13 m high. The mast consists of two parts – the lower one, 6-8 m long, 160-180 mm thick, and the upper one of the same length, 100-120 mm thick. They are joined at a length of 1.5 m, fastened together with two or three clamps and the lower one is buried in the ground by 2 m.
It is better to bury reinforced concrete step-posts and attach wooden poles to them. The wire along the mast is laid using wire staples with fastening every 1 m.
House with metal roof, radio antenna and telephone line
Lightning can strike a radio antenna, roof or telephone wires. A strike to a steel roof is not dangerous if it is reliably grounded (Fig. 4). For grounding, down conductors are attached to all corners of the roof (see Fig. 5, 3) and connected to ground electrodes. Metal drainpipe funnels are reliably connected to the roof with wire, and the ends of the pipes are connected to the ground. Roof grounding is not less than 10-15 m along the perimeter of the building.
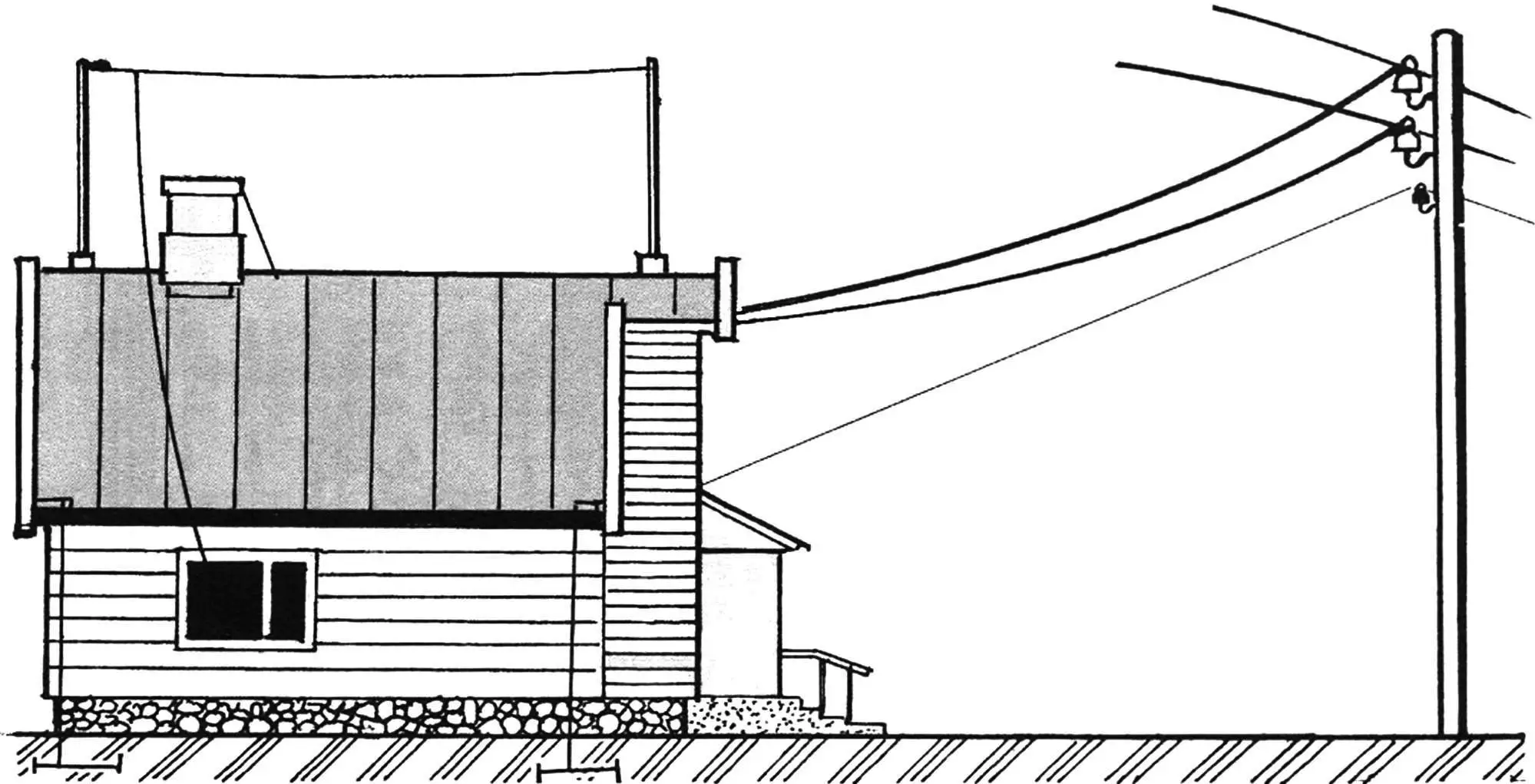
The chimney is protected by a metal cap connected to the steel roof. If there is no cap, an 8-millimeter wire is placed along the perimeter of the upper edge of the pipe and secured to the roof.
Current conductors
They can be made of any grade of steel, single- or multi-wire. To pass the entire lightning current, their cross-sectional area must be at least 50 mm 2 . If the down conductor branches, the cross-sectional area of its branches can be 25 – 35 mm 2 .
The lightning rods and grounding conductors, as well as each other, are connected in different ways. The strongest and most reliable connection is welding with a one-sided or two-sided seam at least 100 mm long (Fig. 5, g). A bandage connection (Fig. 5, h) with a wire of 2-3 mm in diameter over a length of 150-200 mm is also possible. The ends can be tightly twisted over a length of 200 mm or special clamps (Fig. 5, i) 80-100 mm long can be used and secured with two bolts.
The current conductor can be attached to the ground electrodes and lightning rods by welding (Fig. 5, k), as well as two bolts or three rivets (Fig. 5, l). In the case of bolted connections, the end of the current conductor is placed on the ground electrode for a length of 120 mm, and in the case of riveted connections, 150 mm. The connected ends of galvanized wire should be freed from dirt and dust, and non-galvanized wire should be cleaned to ensure good contact.
In places where the down conductor is attached to the steel roof, the paint is removed, one end of the down conductor is bent into a hook or loop, washers are placed on both sides and tightly tightened with a bolt.
The connection points (except for welding) are wrapped in several layers of insulating tape, then with thick fabric, which is tied with a thread and painted. For better contact, the ends can be soldered.
Lightning rods
They are made of steel wire of the same diameter as the down conductor, or of a steel pipe of 20-25 mm in diameter with a wall thickness of at least 2.5 mm, the upper end of which is flattened or welded into a cone. A plug turned into the shape of a needle is sometimes inserted into the upper part of such a pipe and welded. The pipe can be replaced with an angle, strip or profile steel with a cross-sectional area of at least 50 mm 2 . The height of the lightning rod should not exceed 2 m. It is attached to a tree or pole with two clamps so that the wind does not blow it off.
If the lightning rod is made from a steel wire with a diameter of 10 mm, first bend it into a loop and tightly tie the end with wire, creating a bandage (see Fig. 5, b). The length of the end of the lightning rod varies from 200 to 400 mm.
Grounding rods can be made of steel wire with a diameter of at least 8 mm, steel pipes with a diameter of 40 to 60 mm (larger diameter is better), steel strips with a thickness of 4 mm and various profile steel with a cross-sectional area of 50 mm2 or more. Good grounding rods are made of galvanized materials.
When grounding lightning rods, remember: the lower the grounding resistance, the better. The resistance of a material to electric current passing through it is determined by Ohm’s law. In places where people will be during a thunderstorm, the grounding resistance of lightning rods should not exceed 10 Ohms. If the presence of people or animals near the lightning protection device is excluded, the grounding resistance can be within 40 Ohms.
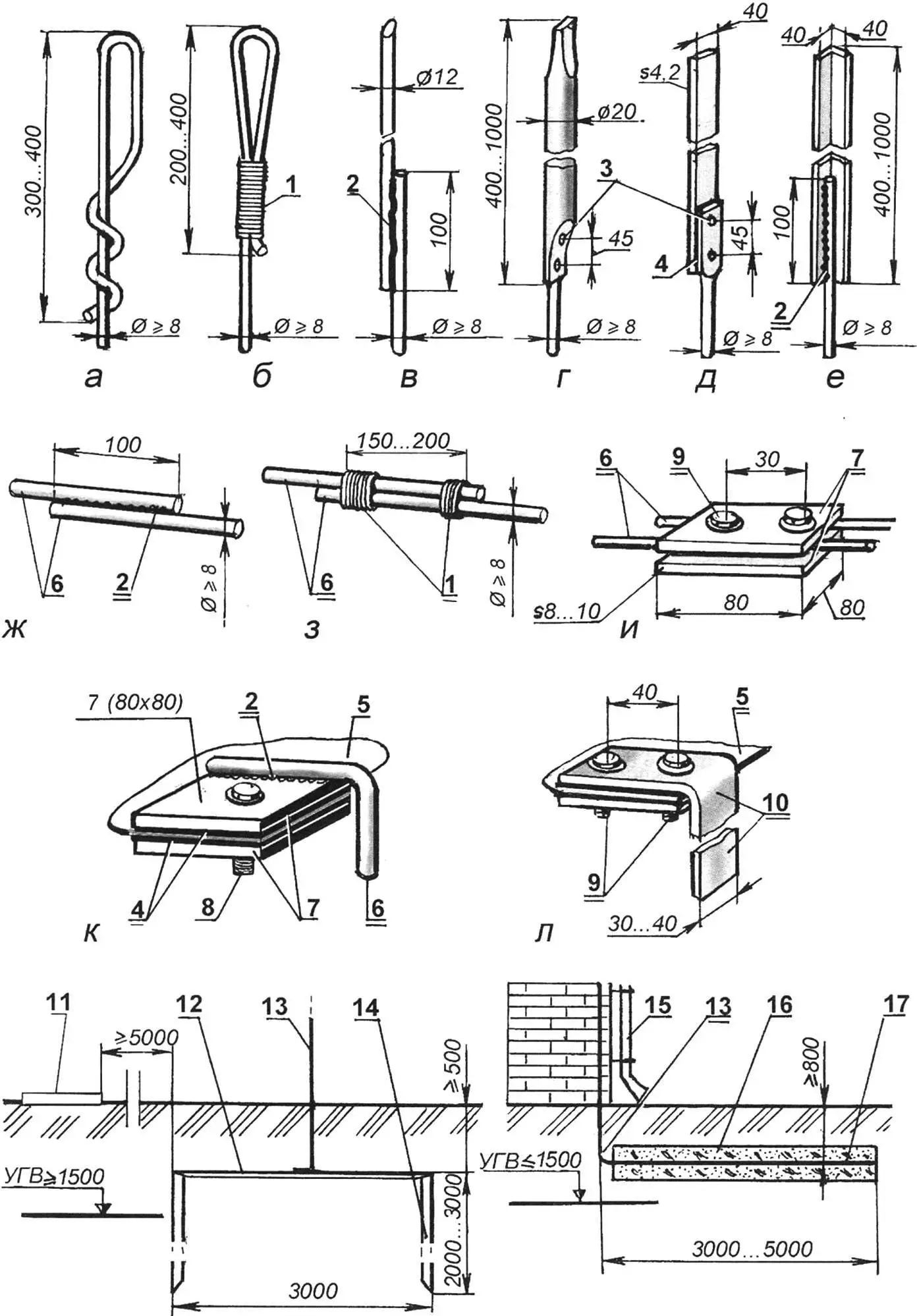
a, b — lightning rods made of steel wire; c — the same, made of round steel; g — the same, made of water and gas pipes; d — the same, made of strip steel; e — the same, made of angle steel; g — methods of connecting down conductors using welding; h — connection of down conductors using a bandage; i — connection using clamps; k, l — roof grounding devices;
1 — galvanized wire bandages with a diameter of 1.5 — 2.5 mm; 2 — weld; 3 — bolt or rivet; 4 — lead gasket; 5 — roof; 6 — down conductor wire (rod) with a diameter of 8 — 10 mm; 7 — steel plates; 8 — bolt M16; 9 — bolts M8 — M10; 10 — strip steel; 11 — footpath (passageway); 12 — cross busbar; 13 — down conductor; 14 — vertical rod (electrode); 15 — drainpipe; 16 — moisture-absorbing lining; 17 — horizontal earth electrode; GWL — groundwater level
For safety, grounding conductors should be located at a distance of at least 5 m from roadways, sidewalks, lawns, playgrounds, etc. Current-conducting drains are removed from the entrance to the house or other buildings and from the foundations of the protected building by 0.5 – 0.8 m.
Lightning rods are usually grounded using rods made of profile steel or pipes. Two or three such rods 2.5 – 3 m long are driven vertically at a distance of 3 m (or more) from each other. Then they are connected with a steel strip with a cross-section of at least 50 mm2 or a rod with a diameter of at least 8 mm, which are fastened to the rods by welding, bolts or rivets.
The wetter the soil, the higher the conductivity, and vice versa. In summer, as is known, the top layer of the earth dries out significantly, the resistance of the ground electrodes increases. Therefore, the strips should be laid at a depth of at least 0.8 m, and the rods should be driven in so that their upper end is at a distance of 0.8 m from the surface (see Fig. 5).
The resistance of different electrodes in the same soils is not the same. If a vertical ground electrode 2.5 – 3 m long is driven into clay or black soil, its resistance will be approximately 30 Ohms, and the resistance of a horizontal strip 5 m long, laid at a depth of 0.8 m, will decrease to 25 Ohms.
Maintenance of lightning rods
Every spring, all places where individual lightning rods are attached to supporting structures are inspected. Corroded lightning rods and down conductors, as well as grounding devices, are replaced with new ones if their cross-sectional areas have decreased by 30%.
After three years, the serviceability of all connections between the down conductor and the lightning rod and the strength of the lightning rod attachment to the lightning rod or tree are carefully inspected.
After five years, the grounding electrodes and buses are opened and the depth of corrosion and the strength of their connection points are checked.
The distance between the attachment points of the down conductor horizontally is 1 m, vertically – 1.5 – 2 m. During inspection, the paintwork of the lightning rod and down conductor is restored, but not the grounding conductors.
Proper installation and timely maintenance of lightning rods ensure protection of the house and other buildings from lightning strikes.
V. SHMATOV