The student design bureau of the Mari Polytechnic Institute named after A. M. Gorky is known not only in its native lands, but also far beyond the borders of the republic. Original snowmobiles, hovercraft, backpack aeropropulsion and other developments, which have been discussed more than once in M-K, invariably attract the attention of specialized organizations.
OKB has existed for almost a quarter of a century. Today this is a more powerful scientific and experimental division of the institute; research is conducted here on a number of topical problems, and most importantly, the OKB ensures the massive involvement of students in research and development work. Now there are seven groups, each developing its own theme. Organized 4 years ago, SKB-7, specializing in the design, manufacture and testing of sports cross-country cars – buggies, is the youngest student association of the institute. The first two cars with the MPI brand were born in the spring of 1984 and immediately got off to a successful start: Polytechnic motorsportsmen V. Shcheglov and V. Ershov took a number of prizes in the largest competitions of the year. The victories achieved were largely determined by the successful design of the machines – what was included in their design during design. We asked the head of SKB-7, Vyacheslav Mikhailovich SHCHEGLOV, to tell us about the MPI buggy.
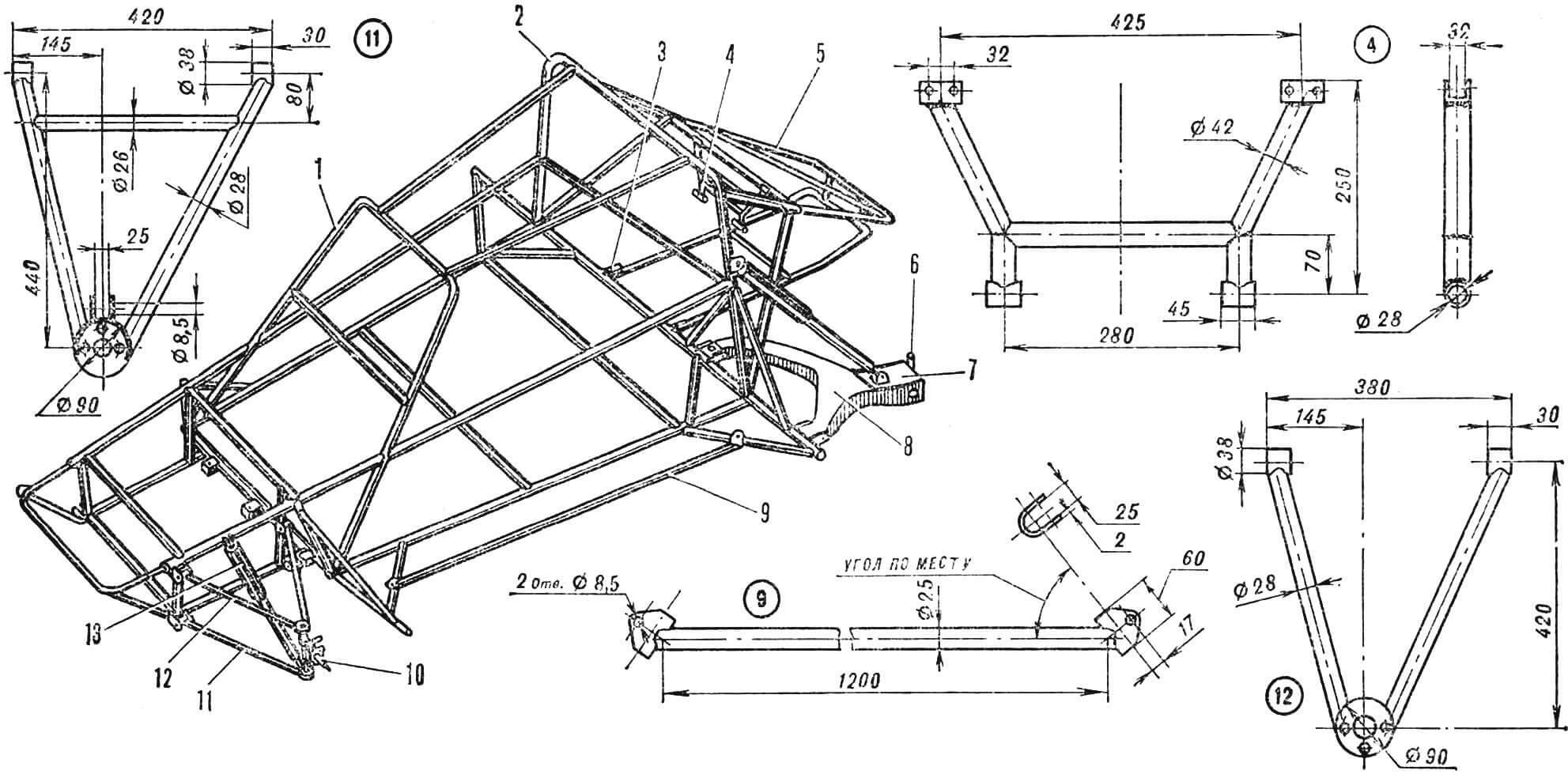
1, 2 — roll bars, 3, 4 — engine mounting brackets, 5 — protective frame of the power unit, 6 — rear lever stop eye, 7 — lever reinforcement, 8 — rear suspension lever, 9 — removable bump stop, 10 — steering knuckle, 11 — lower arm of the front suspension, 12 — upper arm of the front suspension, 13 — shock absorber.
The uniform technical requirements and design experience of many teams, logically, should have long ago led to the development of some “ideal” buggy design. But it’s unlikely that even today you will find two identical cars among the cars that arrive at any competition. And it’s not surprising: each team, if it is truly creative, has something of its own, special, and everyone’s capabilities are different.
We hope that our experience will be useful primarily to young sports teams. According to the current classification, MPI buggies belong to the 1st class and are built from the most affordable units and components included in the kit supplied by DOSAAF. This power unit allows you to design an excellent motocross machine. Its rear location ensures loading of the drive wheels, which is very important for a vehicle of this type. Neither boosting the engine nor reducing the overall weight of the structure will noticeably change the acceleration dynamics if there is no loss of traction between the drive wheels and the support. But overloading the rear axle is also impractical: handling and longitudinal stability will become worse due to the weakening of the traction of the front wheels with the road. In our car, the weight distribution on the front and rear axles was 40 and 60%. This ratio, according to our calculations, is close to optimal. In addition, the rear engine installation made it possible to position the driver more comfortably than in a buggy with a classic transmission. The seat is placed exactly along the Longitudinal axis and is shifted forward in accordance with the selected weight distribution. In this position, the driver controls the car more accurately, and when turning corners with a skid, he moves along a smaller radius.
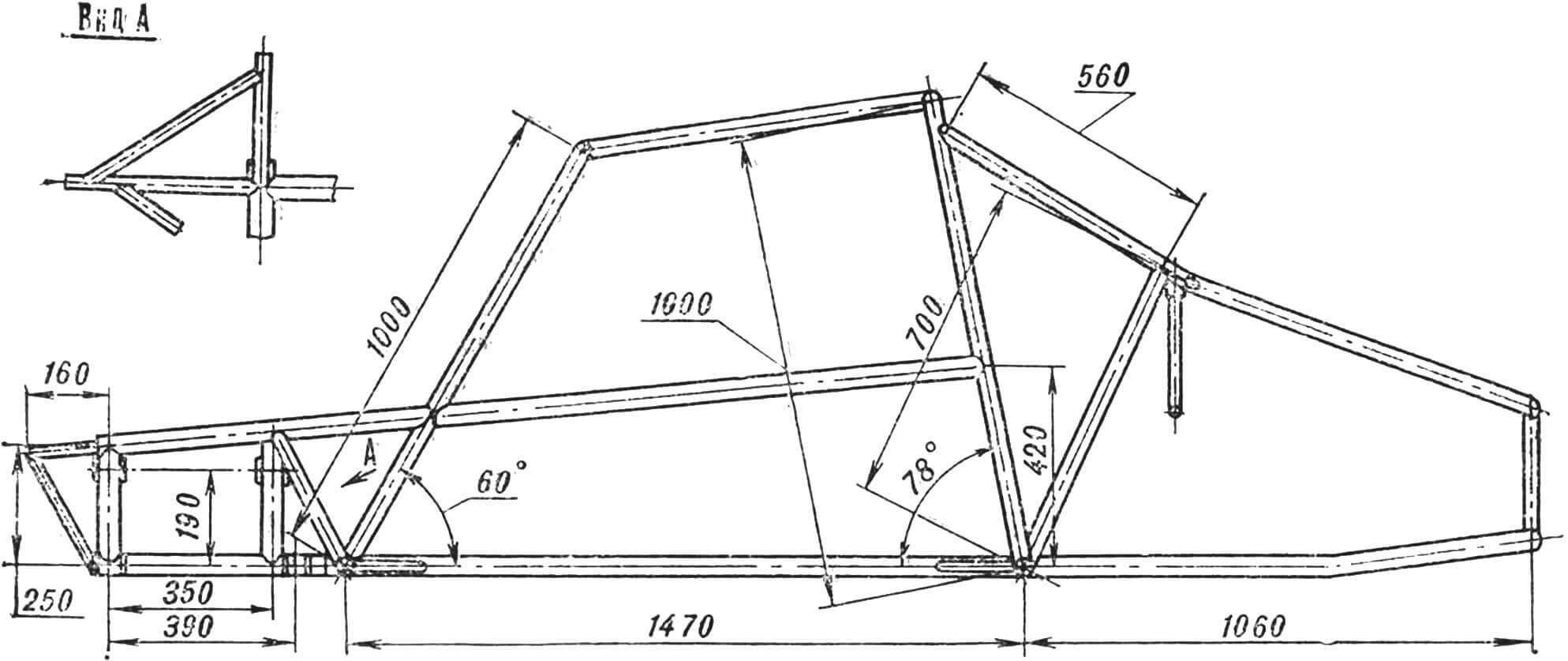
The frame is a welded tubular frame. In its manufacture, pipes from available structural steels were used: for the main frame, safety arches and the main load-bearing elements of the beam suspensions – pipes measuring 42X2.5, for the side protection – 35X2.2, and for the remaining, less loaded elements (protection of the power unit, bump stops , wing brackets) – size 32X2. Frame assembly begins with the lower frame. In the front part, the brackets for the lower arms of the front suspension are welded to its short longitudinal pipes, and the brackets for the arms of the rear suspension and the ears of the front support of the power unit are welded to the transverse beam on the opposite side. The operation of the chassis components depends on the geometric accuracy of the assembly of all elements of the lower frame, so welding is carried out on a slipway made of steel channels. Then two U-shaped safety bars are welded to the frame. Connected on the upper and middle levels by longitudinal pipes, and on the lower by transverse ones, they form a rigid frame. The front part of the frame is wedge-shaped. Its dimensions allow you to accommodate the steering mechanism, control pedals and fuel tank. On the low struts of this part of the frame, brackets for the upper arms of the front suspension are welded, and between them on the side member there are support lugs for the shock absorber. The part of the frame behind the rear roll bar serves to secure and protect the power unit.
The car’s suspensions are independent. The front is on triangular wishbones welded from steel pipe 28X2.5. The lower arms are reinforced with a longitudinal crossbar and have a bracket for mounting the shock absorber. Installation on the frame – through standard rubber-metal silent blocks. The ball joints and steering knuckle are “Zhiguli”, but the knuckle axis is machined to the dimensions of the Zaporozhets axle, since the wheel hubs were taken from this car.
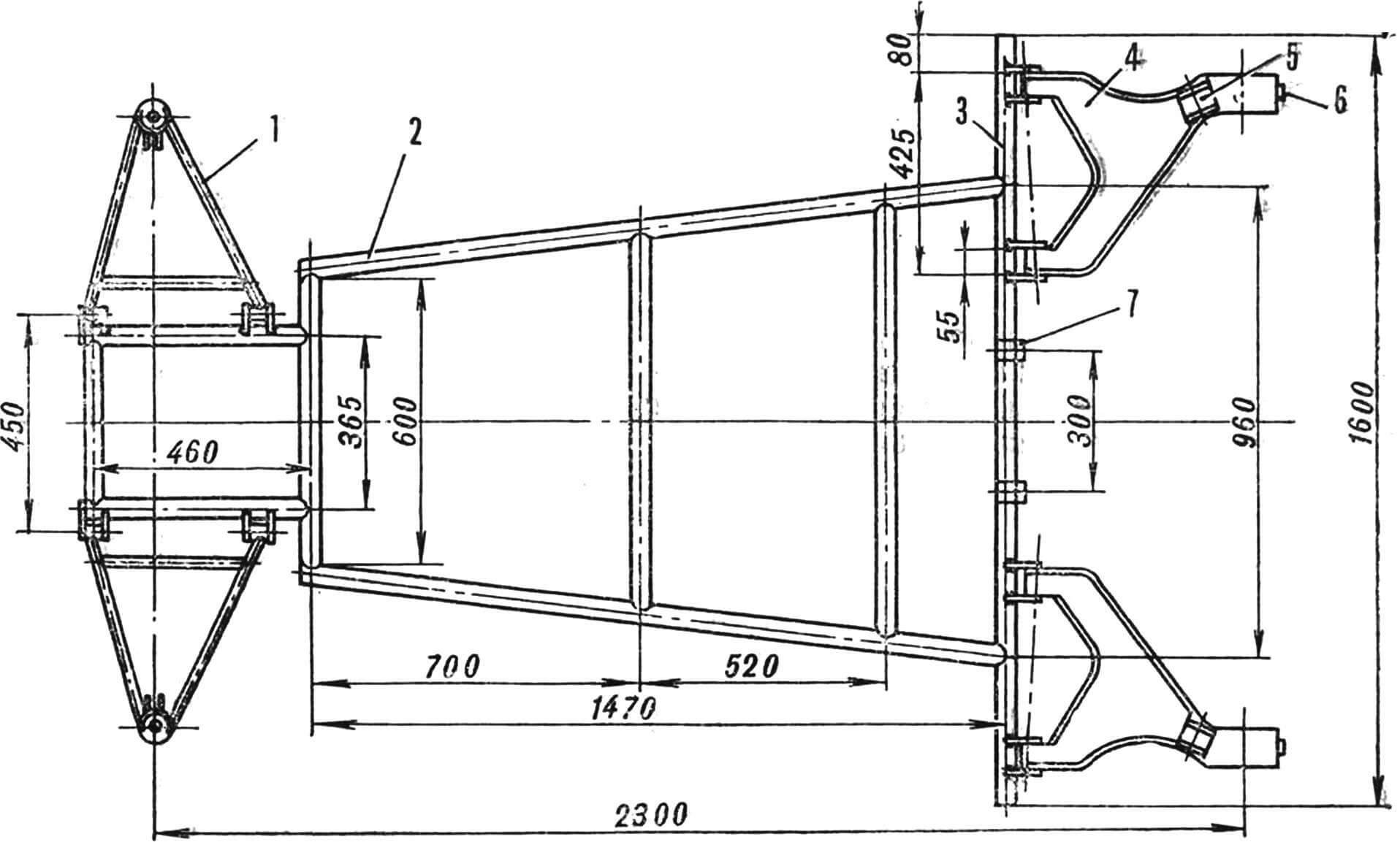
1 — lower arm, 2 — spar, pipe 42X2.5, 3 — transverse beam, pipe 42X2.5, 4 — rear suspension arm, 5 — shock absorber bracket, 6 — limiter eye, 7 — engine bracket.
The rear suspension is mounted on standard ZAZ trailing arms. Reinforcing steel plates 4 mm thick are welded onto their ends. The shock absorber bracket and the eyelet for connecting the maximum lever stroke limiter belt are also attached to them.
High demands are placed on the chassis of a cross-country vehicle. The main task of suspensions is to ensure maximum contact of the wheels with the ground in difficult driving conditions and effectively dampen the resulting vibrations. On the MPI buggy, the front and rear suspension arms are equipped with aviation-type hydropneumatic shock absorbers, ensuring operation with a maximum travel of 240 mm for the front wheels and 300 mm for the rear wheels. But more affordable spring-hydraulic shock absorbers with springs from the ZAZ front suspension and shock absorbers from trucks also behave quite satisfactorily here.
The steering mechanism is rack and pinion. It is lighter and more compact than a worm gear, has a smaller gear ratio (1:10) and is therefore more convenient for a sports car.
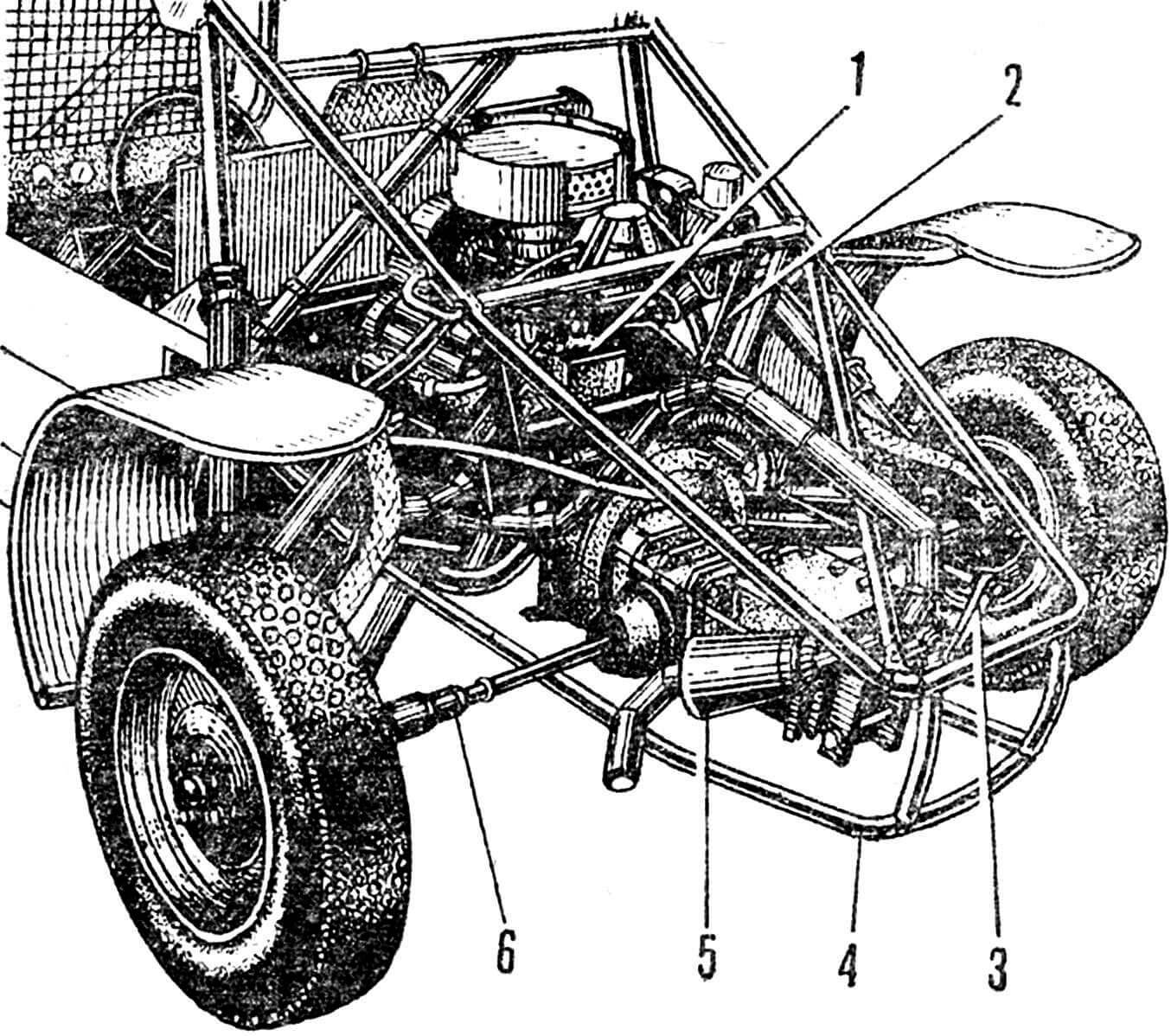
1 — engine, 2 — engine bracket, 3 — gearbox control lever, 4 — protective frame, 5 — exhaust system, 6 — extended axle shaft.
The ZAZ-968 engine has a power of 40 hp as standard. pp., however, it can be increased by 30-50%. The forcing techniques are standard. Pistons and connecting rods are adjusted according to weight. Balance the crankshaft with flywheel and clutch assembly. Improves filling of cylinders with combustible mixture. To do this, the intake and exhaust channels in the cylinder heads and pipes are carefully cleaned and polished. The joints between the head and the collectors are checked for the absence of “steps”. Of the carburetors used on the ZAZ-968, we recommend choosing the DAAZ-2101-20 – it is easier to adjust. Set it to a slightly over-enriched composition: so that the engine runs without “dips” and spins up quickly. Attention should also be paid to the air purification system, monitoring the condition of the VAZ air filter element. When competing in dry weather, it quickly becomes clogged with dust and impairs the performance of the power system.
Another reserve for boosting the engine is adjusting the exhaust system. It is known that resonance phenomena in the exhaust pipe can be used to improve the cleaning of cylinders from exhaust gases. This is done by selecting the size of the exhaust pipes. Our machine has successfully used one of the “four-in-one” methods. It is calculated using an empirical formula and refined experimentally. You can read about this in detail in the books: Nazarov M. M. Special cross-country cars – buggies. M., DOSAAF, 1980; Morozov K. A., Chernyak B. P., Sinelnikov N. I. Features of working processes of high-speed carburetor engines. M., 1971.
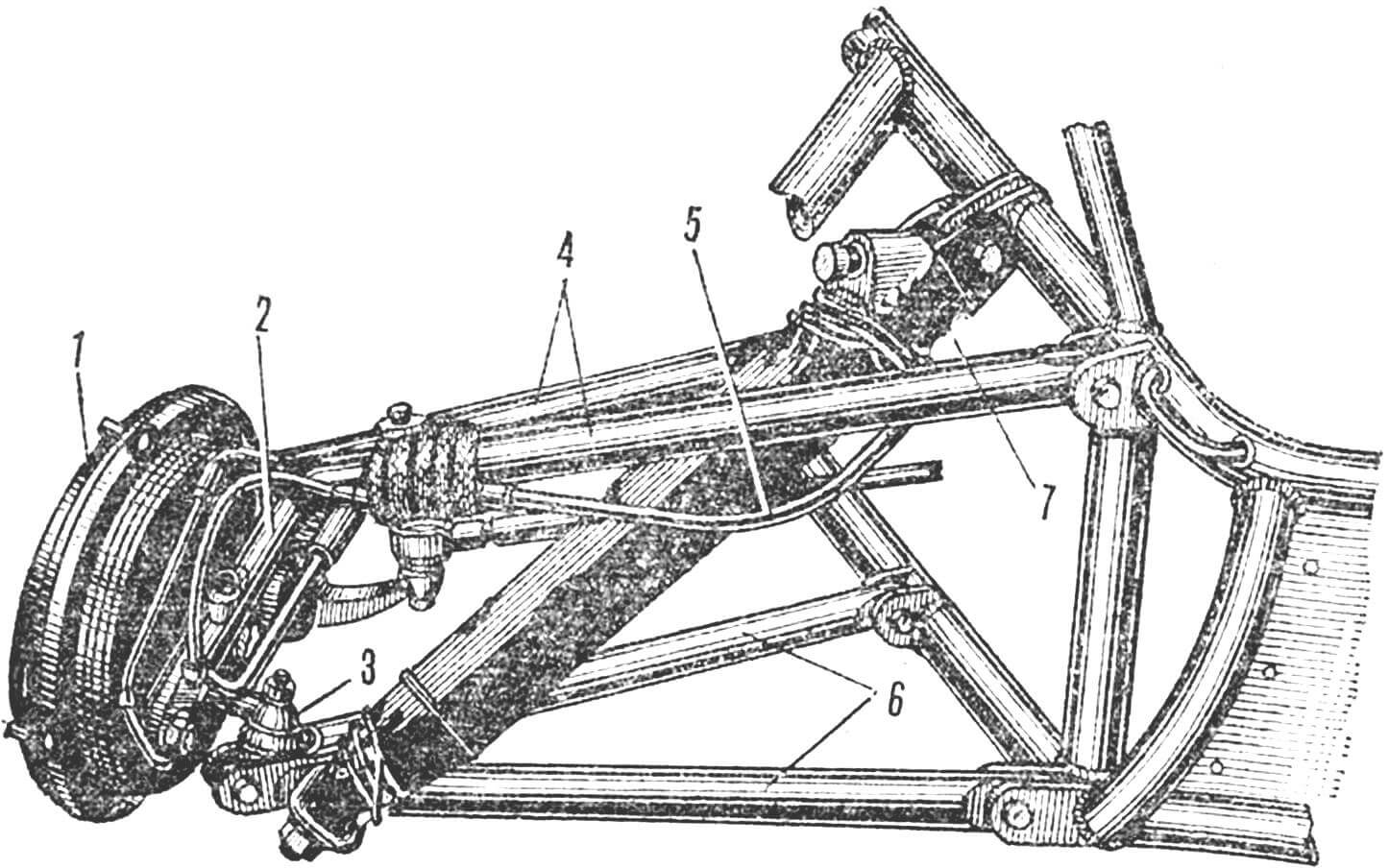
1 — wheel hub, 2 — steering knuckle, 3 — ball joint, 4 — upper arm, 5 — brake hose.
The standard gearbox is unsuitable for a cross-country car. There is practically no need to use fourth gear in a race, and the interval of gear ratios between second and third is too wide. Therefore, we installed the third gear instead of the fourth, and instead of the third, a homemade spur gear pair. The improved gearbox has the following gear ratios: I—3.8, II—2.118, III—1.75 and IV—1.409.
The wide track increased the stability of the car, but forced the axle shafts to be lengthened. To prevent them from disengaging with the main gear when the levers are in the lowest position, the travel of the suspension levers was limited by strong canvas belts. The same limiters are installed in the front suspension.
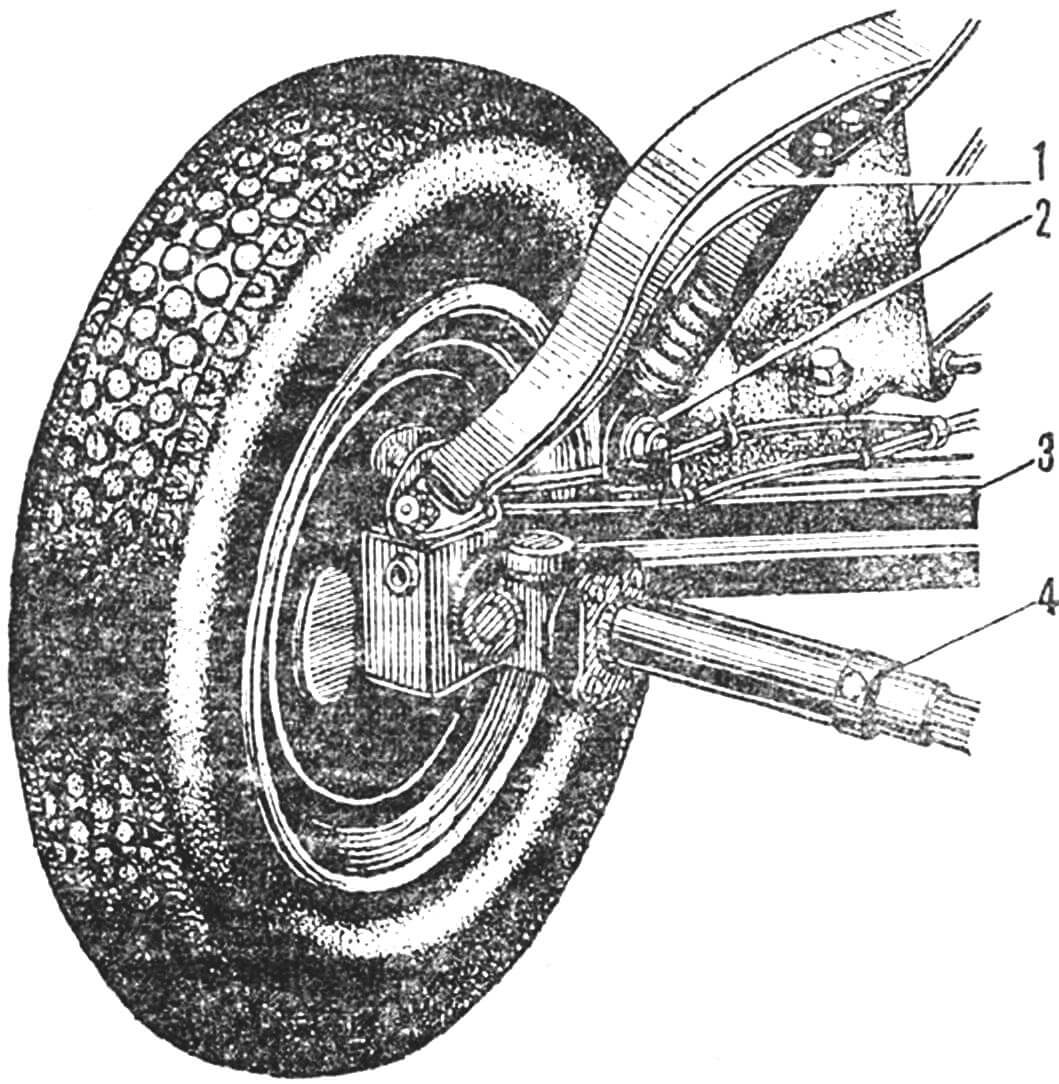
1 — limiter, 2 — shock absorber bracket, 3 — suspension arm, 4 — axle shaft.
The Zaporozhets discs, hubs and brake shields were used unchanged. Tires are either from Volyn (LuAZ), or special ones – NK-9. The latter provide reliable traction when driving through mud and at the same time self-clean well, but on dry surfaces they require more skill from the driver: due to the reduction of the contact patch, the car “holds the road” somewhat worse.
Covering the frame with duralumin sheets performs not only a decorative and protective role. It also serves as a strength element of the structure. The driver’s compartment trim sheets, sides, front and rear partitions, as well as the bottom are attached to the frame tubes using aluminum adhesives. This increases the rigidity of the frame. The thickness of the sheathing sheets at the bottom is 1.5 mm, along the sides – 1.0 mm, the rest of the sheet elements are 0.8 mm. For greater rigidity, the sheets are zigged. Connecting the skin with rivets takes longer and is more difficult than with bolts, but such fastening is more reliable and does not become loose due to shaking. Only the wing skins are bolted to their tubular frames: ease of repair or replacement in case of accidental damage is more important here. For the same reason, the tubular fenders attached along the sides of the vehicle are removable.
TECHNICAL DATA OF THE MPI BUGGY:
Base, mm – 2300
Track, mm:
front wheels – 1530
rear wheels – 1500
Ground clearance, mm – 250
Engine power l. With. — 60
Weight, kg – 450
Weight distribution along the axes,% – 40/60