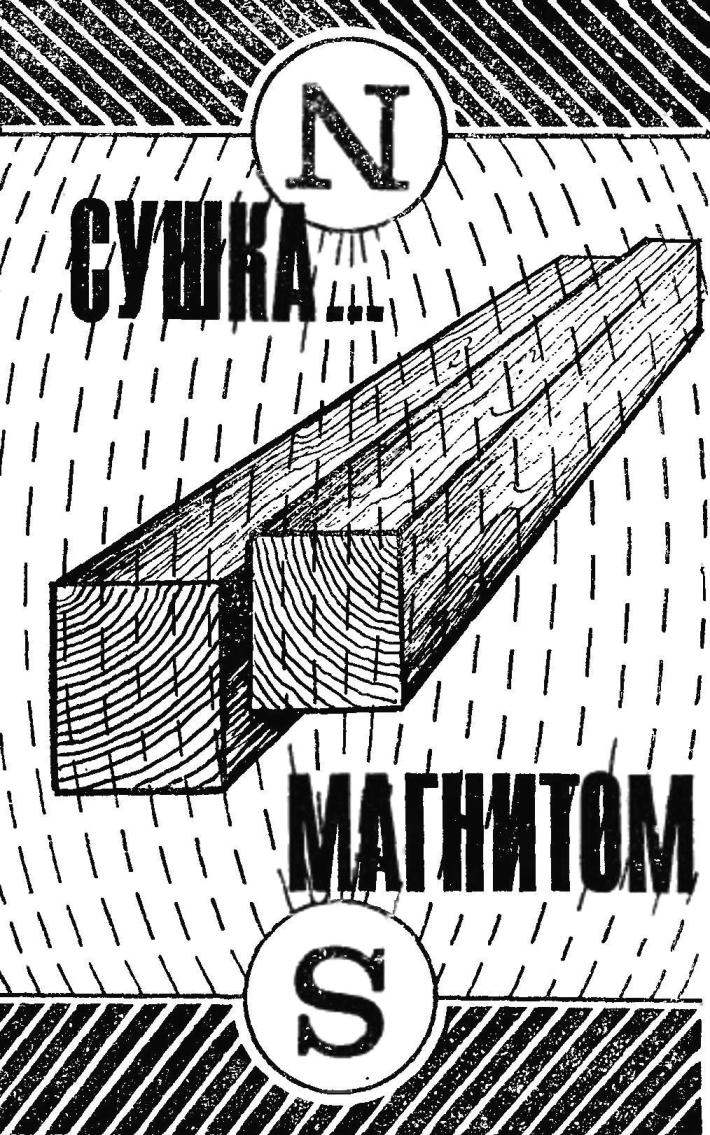
Soft rocks also find wide application in the national economy. So we continued the search for solutions, increasing the intensity of heating and drying of wood and gives it a certain targeted properties.
The result was developed and implemented another method of dehydration of lumber — in an electromagnetic field, where heating is achieved through a ferromagnetic heat-generating elements. To do this, in a thermally insulated chamber (Fig. 1) equipped with a multiturn solenoid, put the cart to a stack of lumber (Fig. 2). Pre between their ranks according to a certain scheme laid ferromagnetic fuel elements (TFE) in the form of gratings or grids (Fig. 3).
When turning on the alternating electric current of industrial frequency in the solenoid formed by an electromagnetic field which, acting on the steel grating of the TPV generates them warm. The transfer of heat from the TPV to the lumber is due to conductivity.
The principle of heating of TFE based on the known physical phenomenon, when heat is generated due to the eddy currents generated in the ferromagnetic material under the action I of an alternating electric field.
In the school course of physics the heating of a ferromagnet under cyclic magnetization reversal is illustrated by a simple experience: two equal size rod, steel and copper, mounted on a wooden tablet, on which is placed a coil from a universal transformer. Then use the wax on the rods at the same height are attached 2-3 matches. After turning the coil through the variable resistor matches with steel core fall, and the copper remain.
The observed phenomenon that some are trying to explain the effect of the eddy currents. However, elementary calculations show that the eddy currents heats up more brass rod. If the same size rods in them indoctinate fields with the same E. D. C. But the resistivity of copper is about eight times less than steel (RM = 0,0175; RS = 0,15), so it is natural that the value of the magnitude of the eddy currents in the copper rod is so much more than steel.
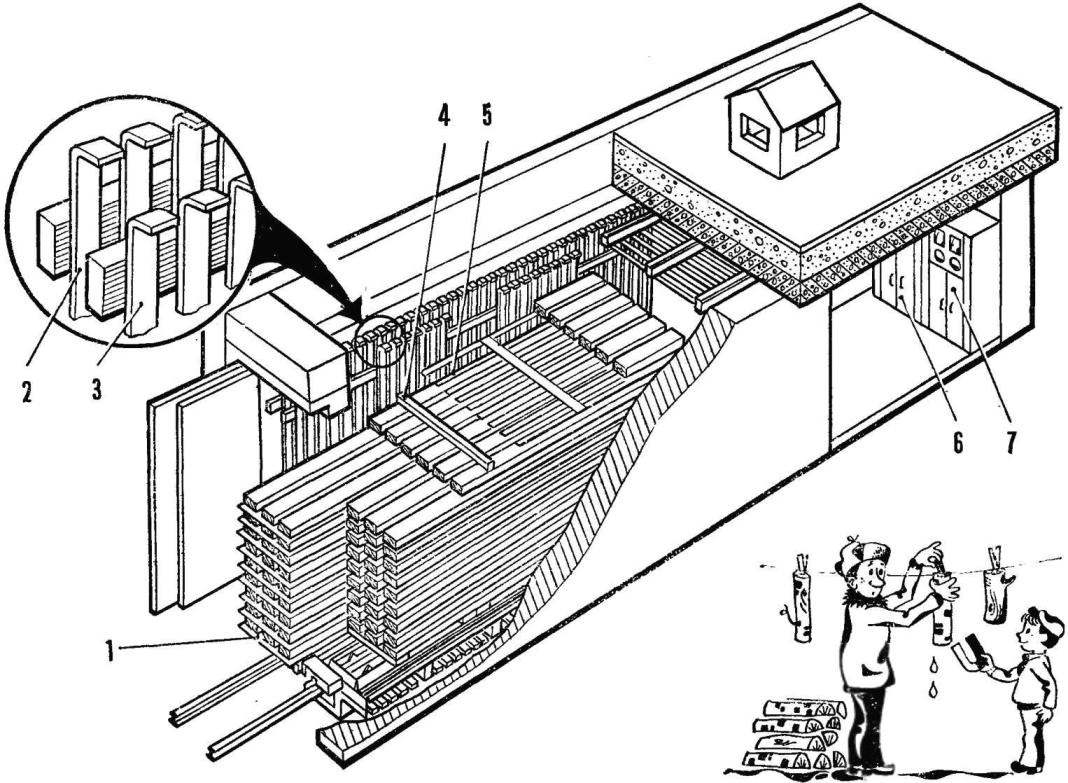
Fig. 1. Electromagnetic chamber for drying wood:
1 — cart with a pile of lumber, 2 — primary winding, 3 — extra coil, 4 — cross strip, 5 — ferromagnetic lattice, 6 remote control 7 remote control devices.
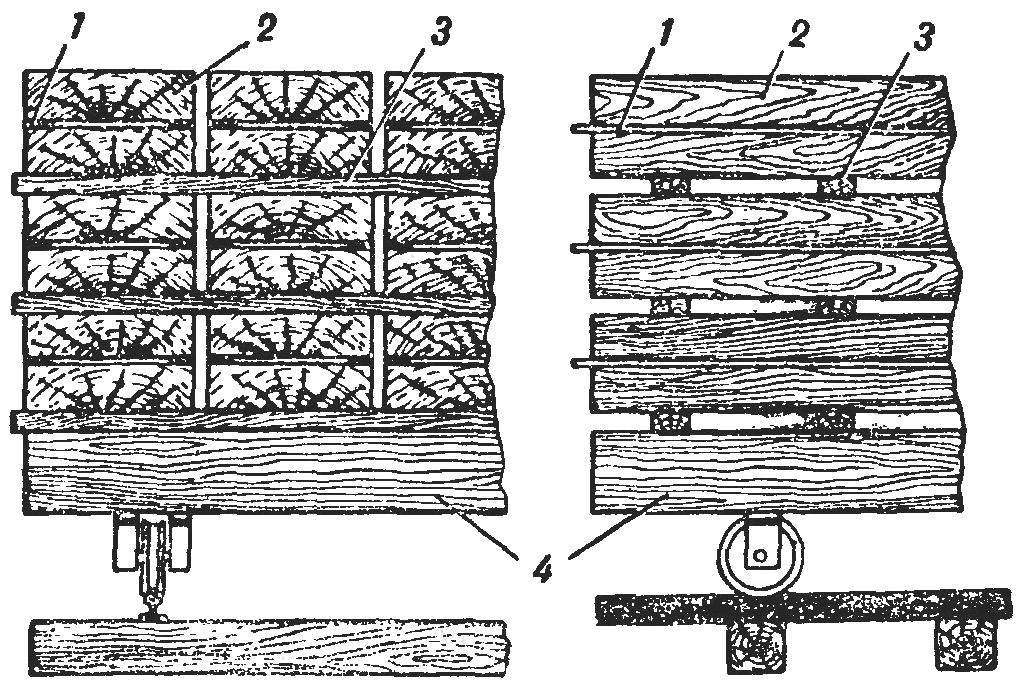
Fig. 2. The pile on the cart:
1 — ferromagnetic lattice, 2 — wood, 3 — gasket, 4 — cart.
Therefore, the cause of the observed effect of heat is the switching (cycle of magnetization — demagnetization, the so-called “hysteresis loop”). And while there are eddy currents, which depend on the current exciting the coil of the solenoid, its frequency and the configuration of the body.
In accordance with Ohm’s law the current in the solenoid depends on the applied voltage and active and reactive resistances of the solenoid and the frequency of the current, since the total impedance: Z2 = R2 + (ωL)2, or Z = R + jωL, and the voltage at the terminals of the solenoid: U = I(R + jωL).
In these expressions, R — active resistance of the conductor; ω = 2πf — circular frequency (π = 3,14; f — frequency current); L — the inductance of a solenoid; j is the current density.
With the inside of the solenoid conductive body is a metal rod — active and reactive resistance of the solenoid is changed, and then U = I1(R1 + jωL1).
The change in R and L depends on such physical properties, such as conductivity, magnetic susceptibility of a body placed in the solenoid field, and even its geometrical shape.
This, in turn, changes the current in the solenoid, which affects its magnetizing force and magnetic flux.
Now back to the question of heating and drying wood in an electromagnetic field. As can be seen from the drawings, the TFE is made in the form of lattices (see Fig. 3) mild steel — St. 3. Why the grid?
The fact that the intensive development of the drying process required a method of supplying heat to the material, which would not reduce the active surface evaporation. If you run TFE and the form of continuous sheets, the area of moisture is significantly reduced; in areas of contact with the workpiece TFE will start the drying of the material will increase thermal resistance to heat flow and significantly decrease the thermal conductivity of the layer. In contact with the material surface rapidly increase the temperature to occur undesirable destructive processes in wood, accompanied by loss of structural-mechanical properties.
For this reason, the contact (conductive) heat supply, despite the great advantages, has not found wide application except for the drying of sheet materials — paper, cardboard, fabrics.
The lattice design of the TFE contributes to the active heat and moisture exchange (Fig. 4) allows you to simultaneously create a relatively uniform, powerful heat supply, and to provide active moisture at the locations of heat sources.
Interestingly, in conventional, convection drying (e.g. hot air) the flow of heat is directed to the material and uneven washes the pile. In electromagnetic the camera is the opposite. First of all heated by the wood pile and there is an allocation of evaporating moisture. And then the flow of ambient air moisture is carried away from the camera. The temperature of the material is higher than that of the environment.
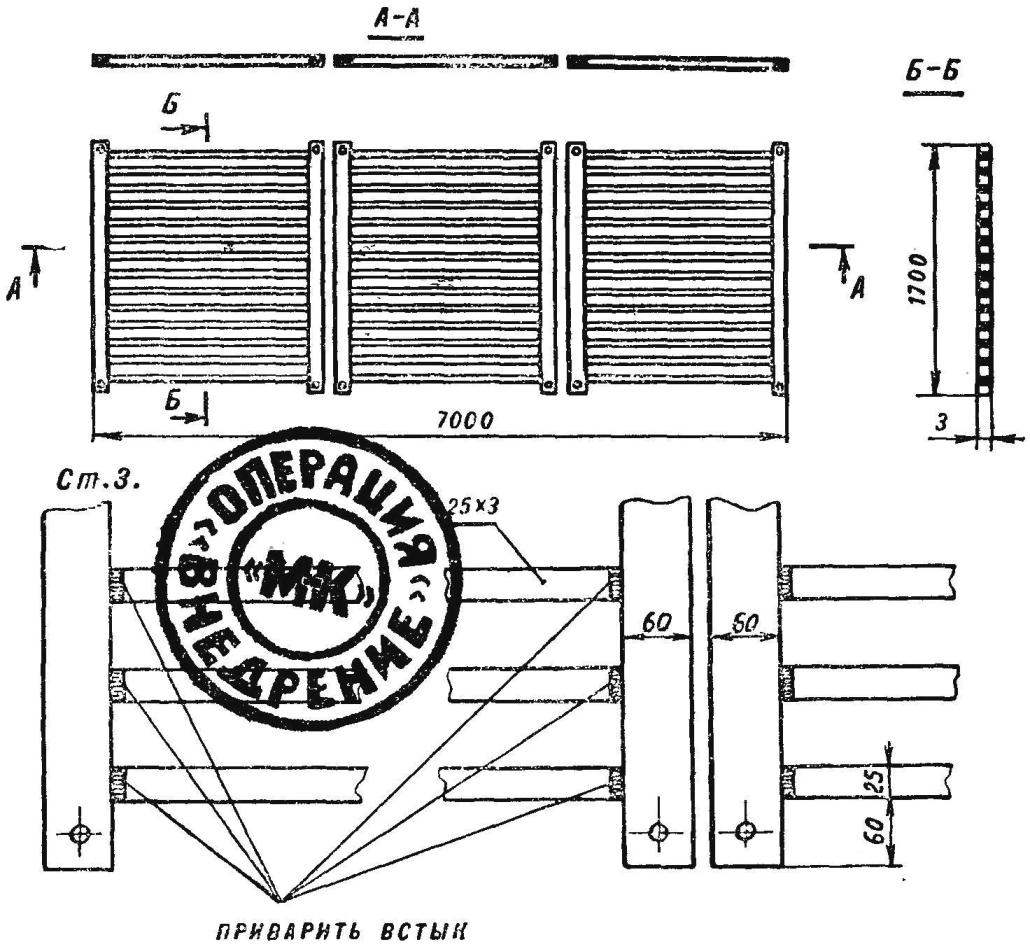
Fig. 3. Fuel ferromagnetic lattice.
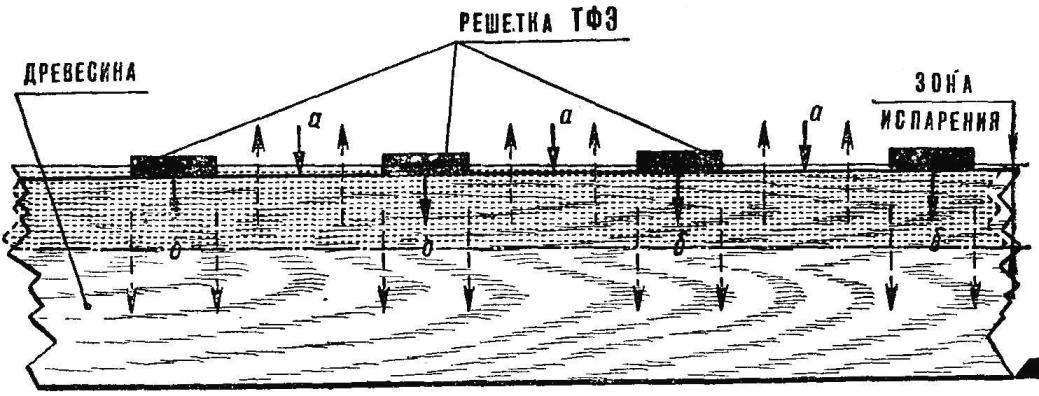
Fig. 4. Scheme of heat and moisture transfer:
and convection heating, b — contact, the dashed line represents the orientation of the evaporation.
The advantages of electromagnetic cameras are important not only for the intensification of the process of dehumidification and ensure high-quality materials, but also for automation of this complex thermal and technological process.
It is known that even the most careful and technically competent people is not always able to manage a large variety of process parameters and unwittingly violates a given coordination. Therefore, automating the process not only facilitates the work of operators, but also significantly improves the utilization of technology.
Based on the described principle of electromagnetic installation with the use of current of industrial frequency has attracted the attention of specialists not only in mechanical engineering, where the requirements to the quality of the wood is increased, but also employees, for example, inter-collective farm construction organizations, where steam for the kilns is absent, and electricity is available in sufficient quantity.
What are the feasibility and technological advantages of the electromagnetic drying? First of all, a significant reduction of the production cycle. In common steam chambers, drying of coniferous sawn timber thickness 60 mm occurs (for normative data) for 5.5 days, and when the electromagnetic teplopodachi just 50-60 hours. The consumption of electricity is given to the efficiency of power plants does not exceed 1400-1800 kcal/kg of evaporated moisture.
In steam dryers, the power consumption is 1600-3000 kcal/kg. Given the consumption of the energy wood dried from the initial moisture content of about 60% to the final 10-12%, and the total amount of evaporated moisture is about 205-210 kg/m3 (e.g., pine).
Investment cost, including production and transmission of energy in conventional meter-cubic meter of wood for 25-30% less than for convective cells. In addition, there is no need to build special powerful boiler houses, construction of which requires considerable investment in time and scarce equipment.
Experience shows that the construction of the electromagnetic block cameras, for example, in the conditions of the black sea shipbuilding plant took no more than 1.5—2 months. Therefore, there is a reduction in commissioning of new capacities. In addition, all electromagnetic systems are fully-automated, what can be said about the steam chambers.
Currently, electromagnetic installation for drying wood has already been implemented in many enterprises of different sectors of the economy. Its geography is very diverse : on the black sea and Kherson shipbuilding plants — the home of this method, at shipbuilding plants of Tyumen, Khabarovsk, they are used in the construction and inter-organizations in Ukraine, Belarus, Uzbekistan, the Russian Federation, Kazakhstan, factories, electrical industry, Tallinn, Minsk. However, it should be noted that the development of this method does not ignore the application of known, proven methods of drying — they should complement each other.
Engineers G. M. BALABAYEV, S. G. ROMANOVSKII