Homemade welding machines are engaged not the first year. In their manufacture into account the advice and recommendations of the “Model construction” and other well-established technical publications and reference literature. Started with “Welding baby” (No. 11, ’87), using the Latr ready with the primary winding. For secondary — recommended magazine, Shino-wire not found. Dare to wind the desired number of turns of the flexible stranded wire 6 mm2 in vinyl insulation. And what? Of course, such a device quickly overheated even when welding of cellular electrode. To somehow solve the problem associated with cooling, have decided to omit the “svarochnik”… in the water. Came from the fact that the secondary winding is great for insulation. And primary, which went before the slider wasn’t exposed as proactively managed to cover it in several layers of protective varnish.
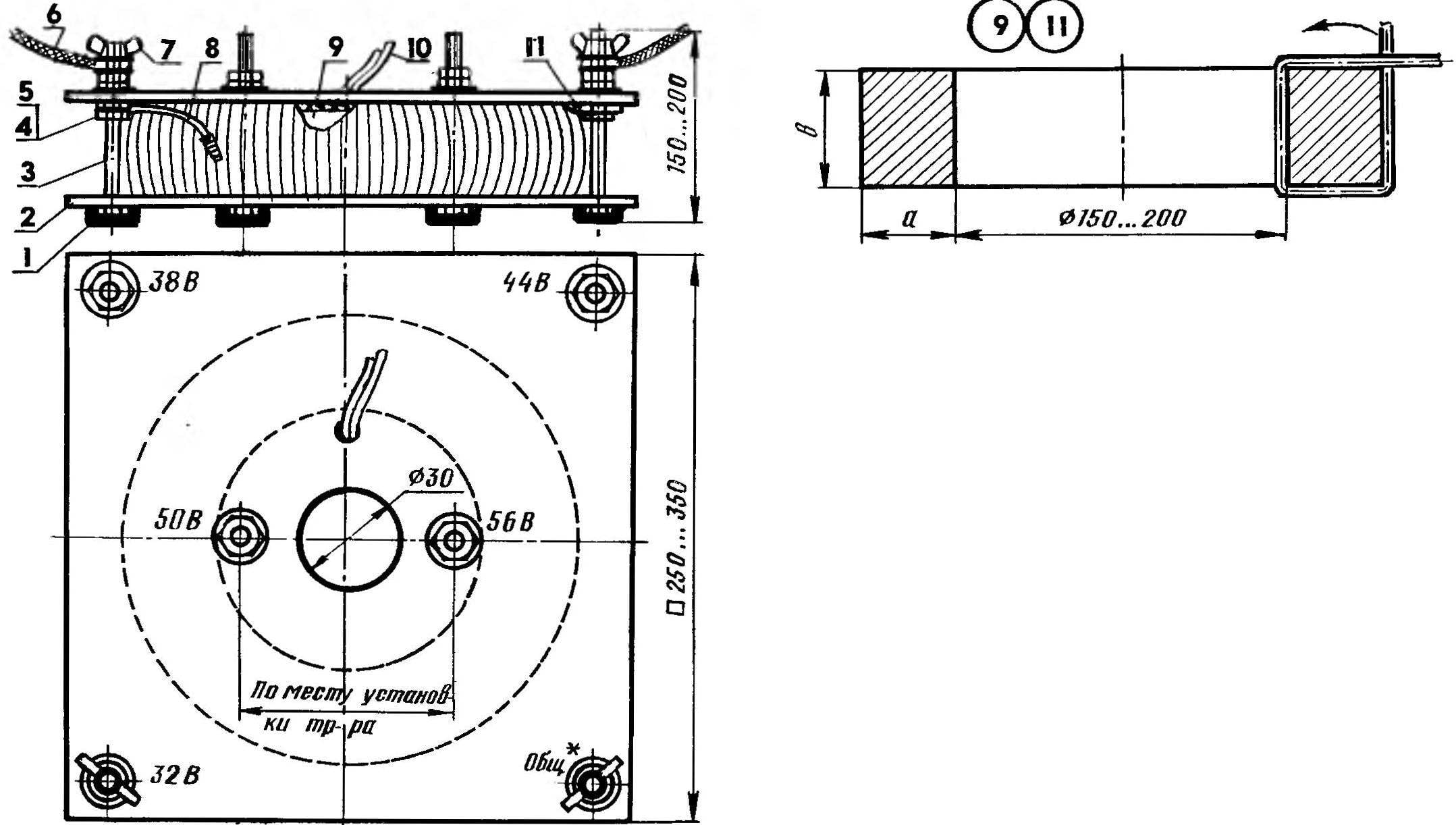
WELDING WITHOUT CHARTS AND FORMULAS
Camera fell in water-filled plastic bucket with a capacity of 20 l (metal is more dangerous) and give the output during the welding 140 A. However, with the use of 10-15 electrodes with a diameter of 3 mm, the coolant is heated to 60° C. so occasionally had to turn the machine off to the Bay again with cold water and “kerf” in the network, to continue welding.
The following devices I have had “dry” — is made on the basis of the stator of the electric motor. Saw: best to use the appropriate magnetic three-phase asynchronous machine with capacity of 4-5 kW. To release such a stator of the Cabinet shell is easiest with a hammer or heavy hammer, hitting the weakest spots.
Then removed the winding. And — in two steps. First clean it with any one side, using a hacksaw. Although it can be used for the same purpose hammer with a chisel, directing the impact force at a tangent to the diameter of the stator. Well and then, going from the opposite side, begin with a pair of pliers to pull the segments of the “half ragged outer” wires from the grooves. Released from the winding, the magnetic core will become toroidal core of the welding transformer.