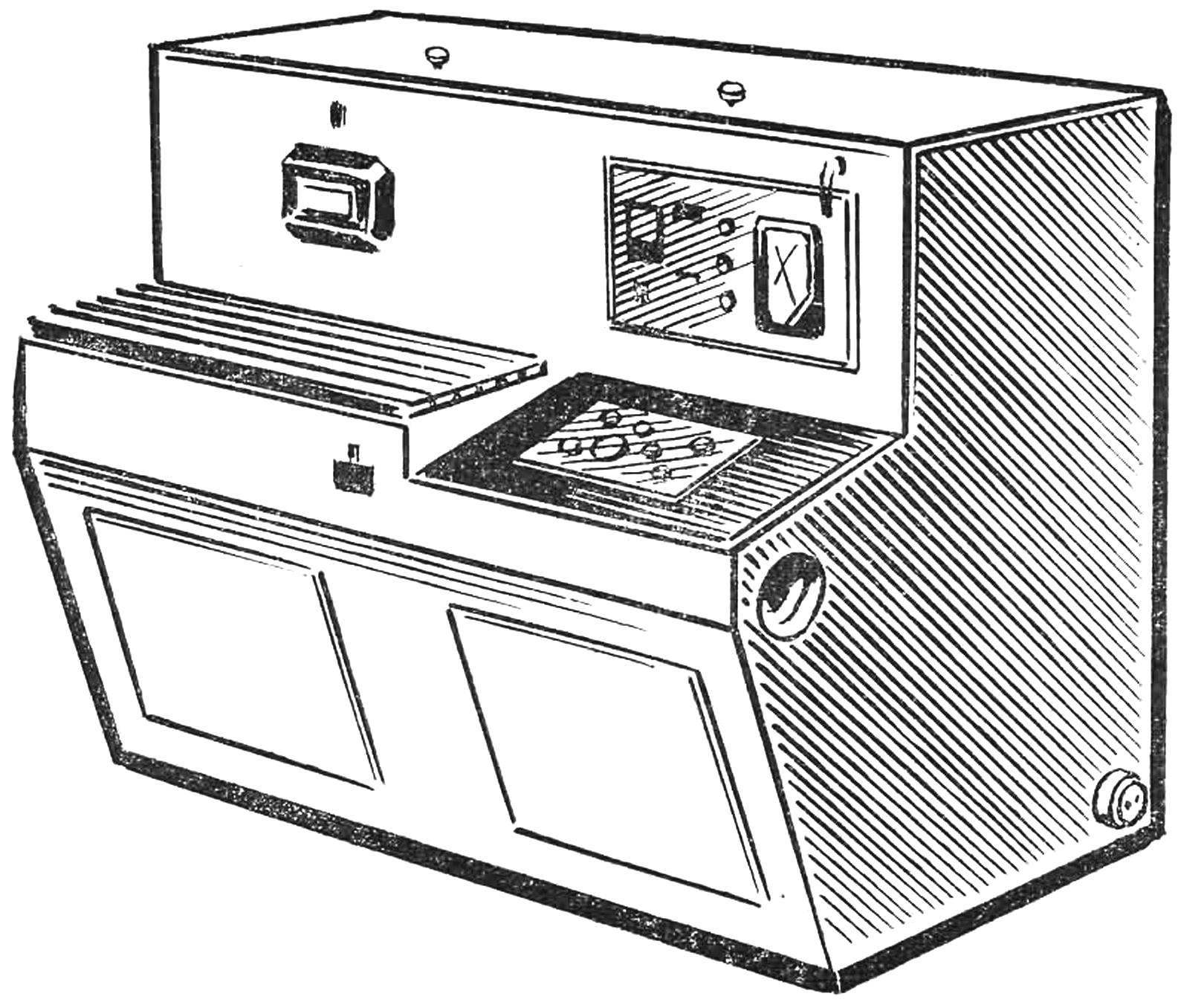
Of particular interest is a new direction in the use of magnetic devices for water treatment and… metal. Not coincidentally these topics periodically devotes a special exhibition of USSR national economy, is continually causing great interest of innovators and rationalizers.
According to the materials of these exhibitions, we have a lesson in our school of young innovators, participants NTTM and pledges of the Komsomol “operation Implementation”: the campaign for the rapid development of new machinery and progressive technology.
BRACELET ON TAP
In the past century, one a foreigner, having been in Russia, announced then that he was able to solve the mystery of the Russian samovar tea made of it is especially tasty because the Russians coated the inner walls of the samovar clay and then fired.
In the old samovars do, no matter how shining they are outside, inside, sometimes all covered with some kind of porous layer, similar to ceramics. However, it is not baked clay, and many years of the scale layer, which for a long time did not know how to fight.
In cooling systems of engines and in steam boilers on the walls, too, constantly deposited a layer of salt, myprivacy of boiling water. The scale has high peel strength, which is more difficult to clean. With its increase deteriorates the temperature regime of the engines, reduced the capacity of the boilers, and this leads to excessive fuel consumption, premature stop teploagregat on the flush repair and other undesirable consequences.
To combat this scourge recently used… magnet. It was found that by passing the water through a static electromagnetic field dissolved salts lose their ability to deposition on the walls, and comes in the form of loose sludge — sludge that is easily removed when flushing the engine or blowdown of the boiler.
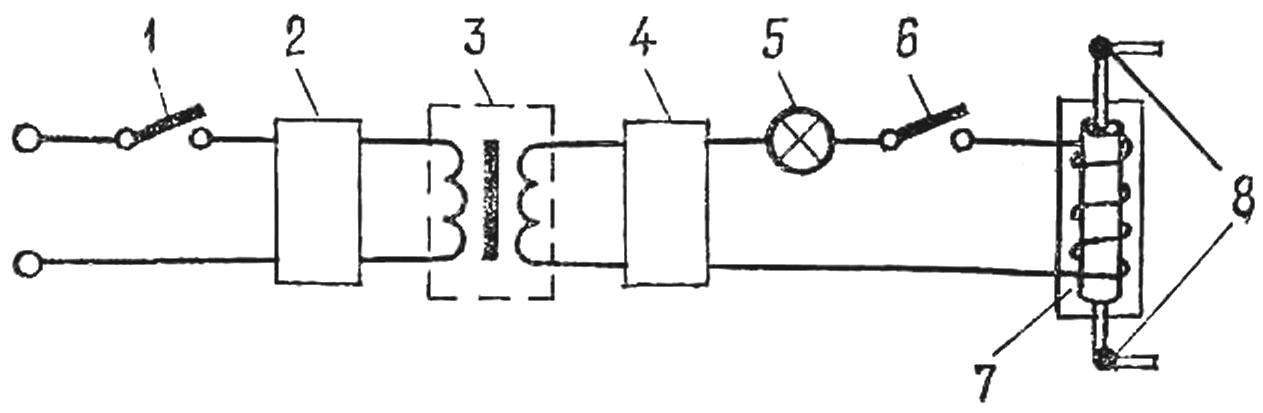
Fig. 1. Driving device for magnetization of water:
1 — circuit breaker, 2 a voltage regulator SFN-20 “VEGA”, 3 — transformer 220/100 V, 4 a rectifier BCA-111, 5 — control lamp, 6 switch, 7 — electromagnetic filter for 8 — taps.
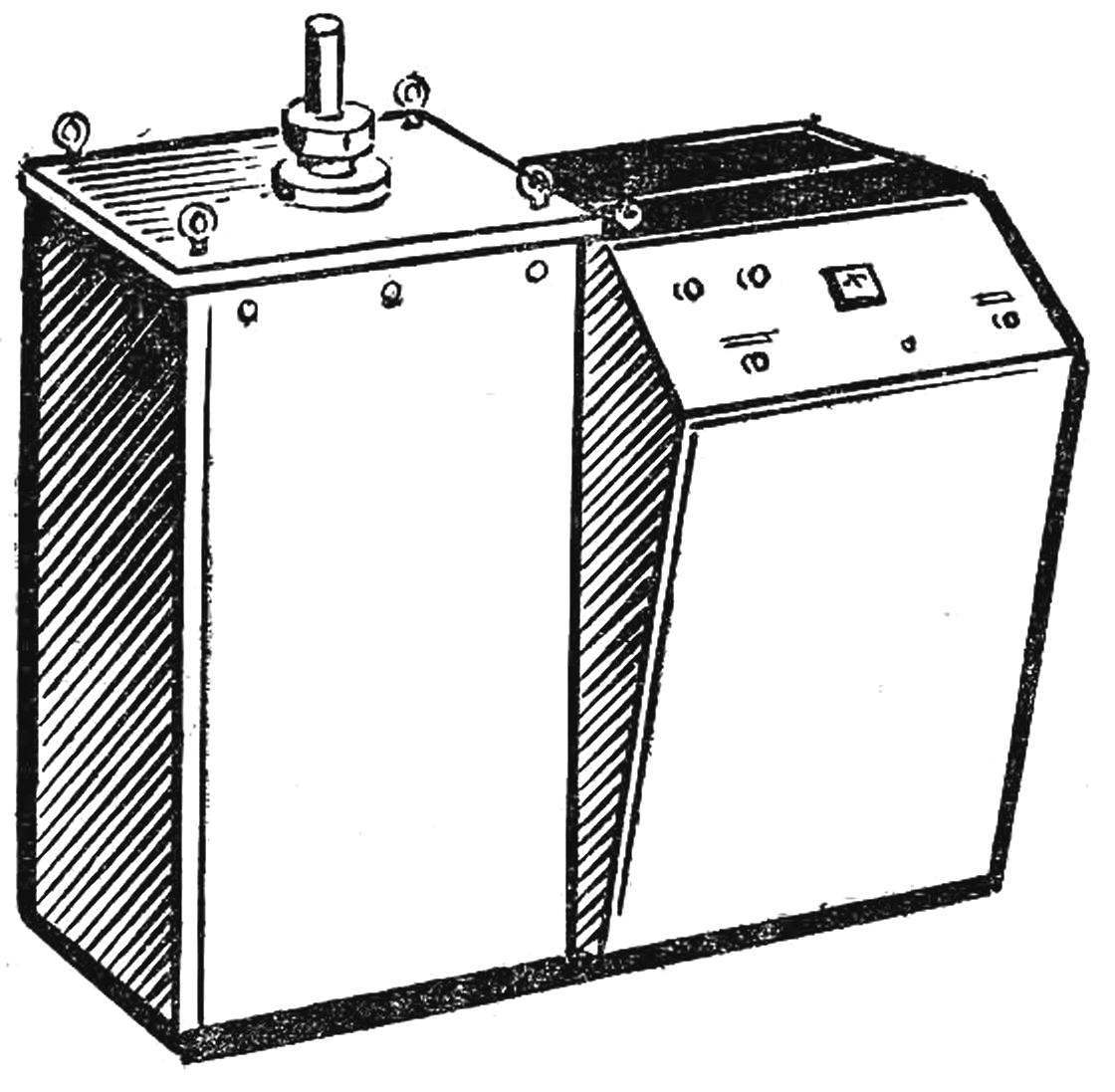
Fig. 2. Magnetic “anvil” — pulse set-Miu-6/1.
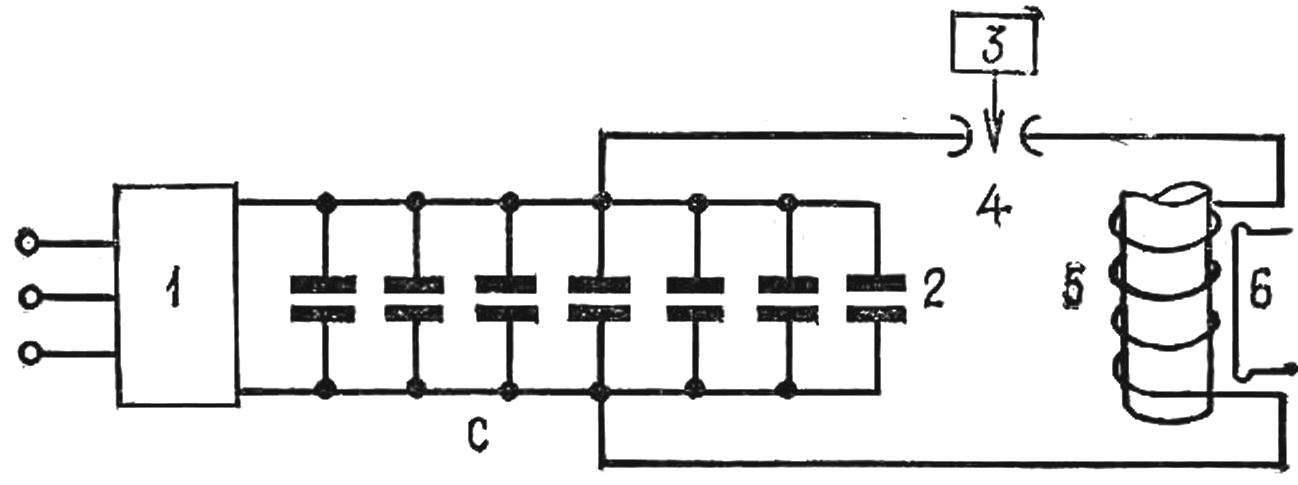
Fig. 3. Schematic diagram of the magnetic-impulse installations Miu-6/1:
1 — charger, 2 — capacitive storage device, 3 — preselection voltage, 4 — three-electrode arrester, 5 — inductor-tool, 6 — piece.
ENEA has repeatedly shown a variety of devices for magnetization of water. We present a simple scheme of such device, which was used in the motor transportation enterprises of the Orenburg transport management. Fixture design was developed by a group of innovators for coppers like TMZ, MMZ, VTT-28 and showed good results: the scale on the inner walls of the cooling jackets of the engines, boilers and pipes now not formed.
The results of long-term production tests enable to conclude that the application of magnetic water has a positive effect on the work units.
The main nodes of the setup — selenium rectifier BCA-111, voltage regulator SFN-20 “VEGA”, a step-down transformer 220/100 In capacity 0,16 kW and electromagnetic filter.
The filter consists of core, electromagnet, casing and housing. The core is made of steel and 35 is a room with corbels in the form of longitudinal slots for the windings of the electromagnet. Coil of an electromagnet made from wire marks PEL-1 0 3 mm, wound on a core in several layers, between which is laid a cable paper. The number of turns in each coil is 1500. All six coils are connected so that the polarity of the poles of the coils alternates.
The electromagnet is placed in a housing made of a nonmagnetic metal and filled with transformer oil. The cover has a sleeve for the entrance of wiring. Filter housing 3 made of steel, has two flanges, which is mounted in the water pipe. The walls of the casing of the drilled bolt holes, centering the casing with the electromagnet.
Electromagnetic filter embedded in the pipe system through which water under the action of feed pumps is fed to the boiler or a water main is designed to fill the cooling systems of engines.
When the plant water from the water network is supplied through the annular gap between the housing and the casing. Thus it crosses field lines generated by the coils of the electromagnet, cleared of salts.
A VISE WITH A SECRET
This machine in the pavilion “engineering” crowded and even the non-professionals: everyone wanted to touch their own hands unprecedented detail, which is almost at the same time were free to move at the slightest touch and then tightly to freeze in place, as if welded.
However, the secret was not in the details, and in the magnetic table on which she lay.
This Institute “Olstein-prom” showed
new designed universal adjustment and adjustable magnetic fixture that without any clips allow to fix the workpiece on the machine at any desired treatment position.
Among these devices there is an unusual vise — magnetic, model 7209-0001. They are designed for installation and fixing details on surface grinding machines. Magnetic block them, carefully holding the fragile item. Enough to turn his special key and the grip are in the position of the clip, parts are attracted to their magnetic vertical and horizontal planes.
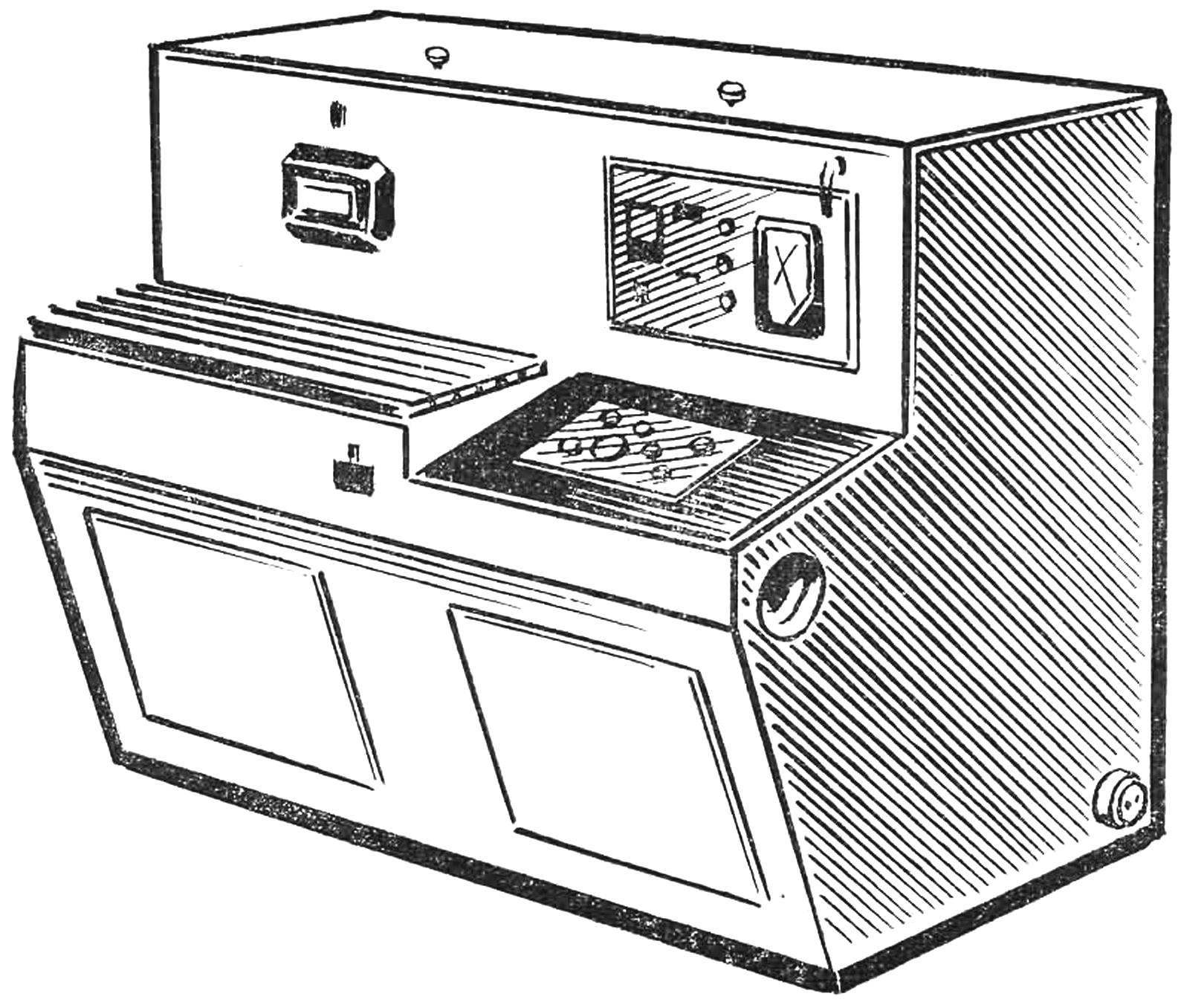
Fig. 4. Magnetic-impulse installation Miu
The vise can be installed both on the lower and any of the three main planes. Having a removable base plate allows you to mount the vise to the machine table with screws.
Use magnetic vise gives you the opportunity to obtain high precision machining planes and to reduce the auxiliary time for docking and undocking of details. Weigh the grip is much smaller than the usual locksmith is just 11.2 kg.
For drilling machines is developed by floating the table on air cushion with magnetic mount — model 7309-0003. Thanks to it is easy and convenient moving of heavy parts, drilling them holes on the markup or in jig for vertical drilling machine.
The table consists of the base and the top faceplate. On the mirror base located nozzles, which through the subtle channels compressed air is applied under pressure 3— 4 ATM. In the upper faceplate mounted magnetic blocks that may be attached faceplate or unpin.
The faceplate dimensions are in millimeters: 455X115.
Also created a magnetic cartridge (model 7109-60001) that allows you to secure parts during turning and grinding. The specific force of attraction of the cartridge 12 kg/cm2. It weighs only 6.75 lbs. per cartridge can be installed replaceable linings, for which the mirror of the cartridge there is a special sleeve and threaded holes. Lining can be strengthened with the necessary form corresponding to the particular detail.
SMITH-INVISIBLE
For thin-walled cylindrical workpiece is not touched none of the known instruments, and it is literally on eyes turns into a convoluted tube. Plastic or ceramic item easily is pressed into a metal housing.
It becomes possible, even the machining of the part enclosed in sealed glass or plastic covering. All these opportunities are created in recent years, magnetic-pulse installation for metal forming magnetic field.
This so-called devil-forging forming method using strong pulsed magnetic fields. The process is based on conversion of energy stored in a capacitive storage — battery high-voltage pulse capacitors, — the work of plastic deformation.
When enabling the magnetic-impulse installations in the network, the capacitive storage device via a charging device dials a predetermined voltage. Then on the auxiliary electrode three-electrode spark gap served an igniting impulse.
The spark gap between main electrodes breaks and the capacitive storage device is discharged by the inductor tool. Pulse Tokorozawa, passing through the working coil of the inductor-tool, creates a powerful pulsed magnetic field, industrous in the conductive workpiece eddy current. In the interaction of the field coil with a field of the workpiece, forces deforming the workpiece.
So, for example, magnetic-impulse installation Miu-6/1.
It can be used for different operations of processing of metals by pressure, cutting holes, flaring, shallow forming, overmolding, Assembly of units. Magnetic stamping best lend themselves to flat, conical or cylindrical workpiece of nonferrous metals and their alloys.
Rational field of application of installation, the stamping of parts up to a thickness of 0.1 mm and a diameter of 100 mm. Supply three-phase alternating current with voltage of 380/220 V.
In the USSR national economy was demonstrated and another magnetic pulse installation, Miu-20/3. It is a large three-sided Cabinet, before which are set wide bedside table with monitoring devices, and Desk on the top panel. This pilot plant, developed in the Kharkov Polytechnic Institute named after Lenin. She is also able to perform various types of processing of metals by pressure of a pulsed magnetic field: cutting holes, beading, shallow hood, flanging, crimping, splicing and Assembly of sealing units, even welding.
In such a setting it becomes possible to perform technological operations difficult in other ways: for example, zapressovka metal parts to fragile glass and ceramics, the pressure treatment of parts enclosed in a hermetic shell of glass or plastic, machining of alloys, hard wrought by conventional methods.
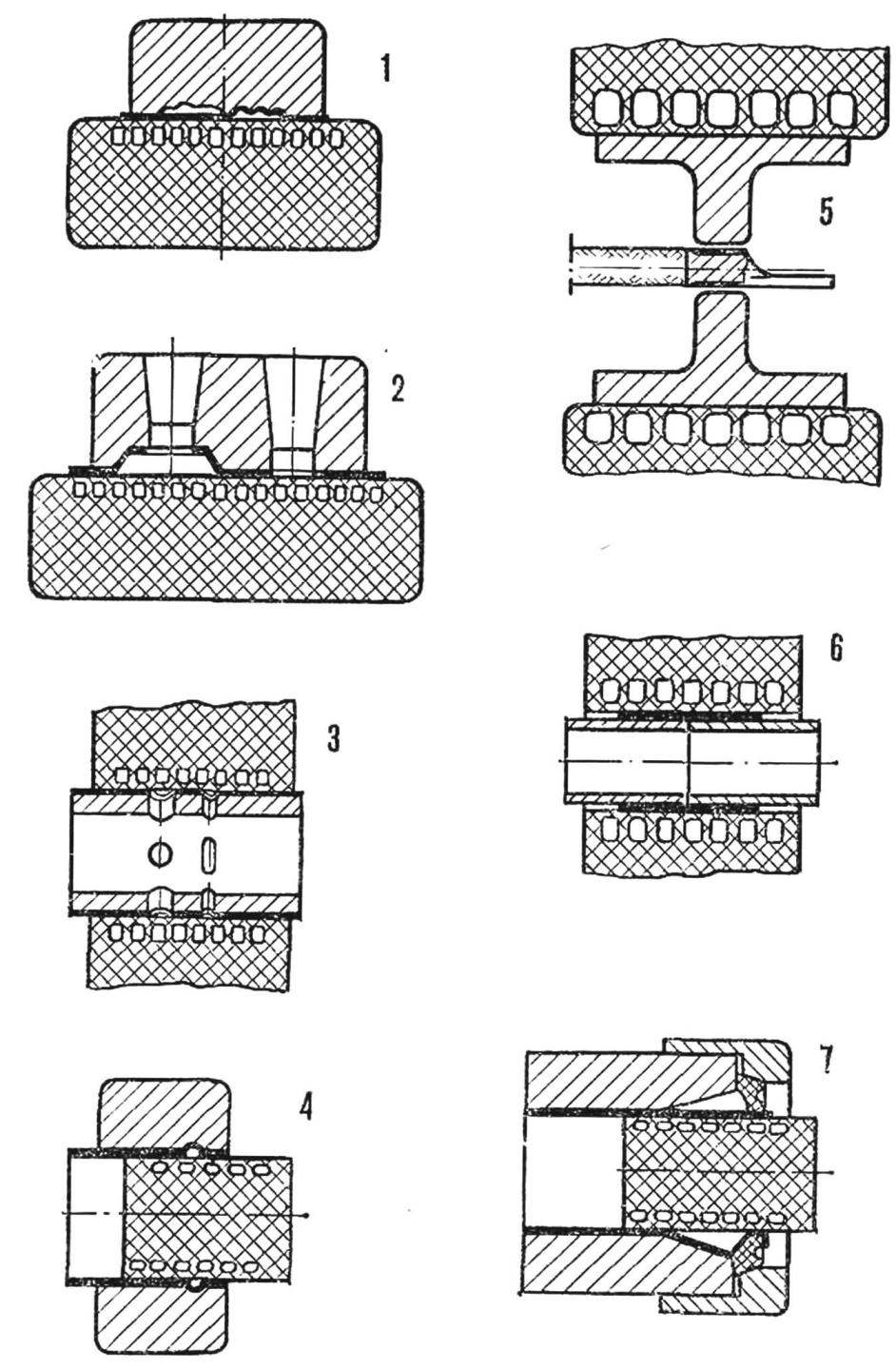
Fig. 5. Scheme of technological operations of the magnetic forming:
1 — formed, 2 — cutting along the contour, 3 — hole punching, 4 — distribution of housing, 5 — press, 6 — a compound moulding, 7 — the distribution on a cone and rolling rings.
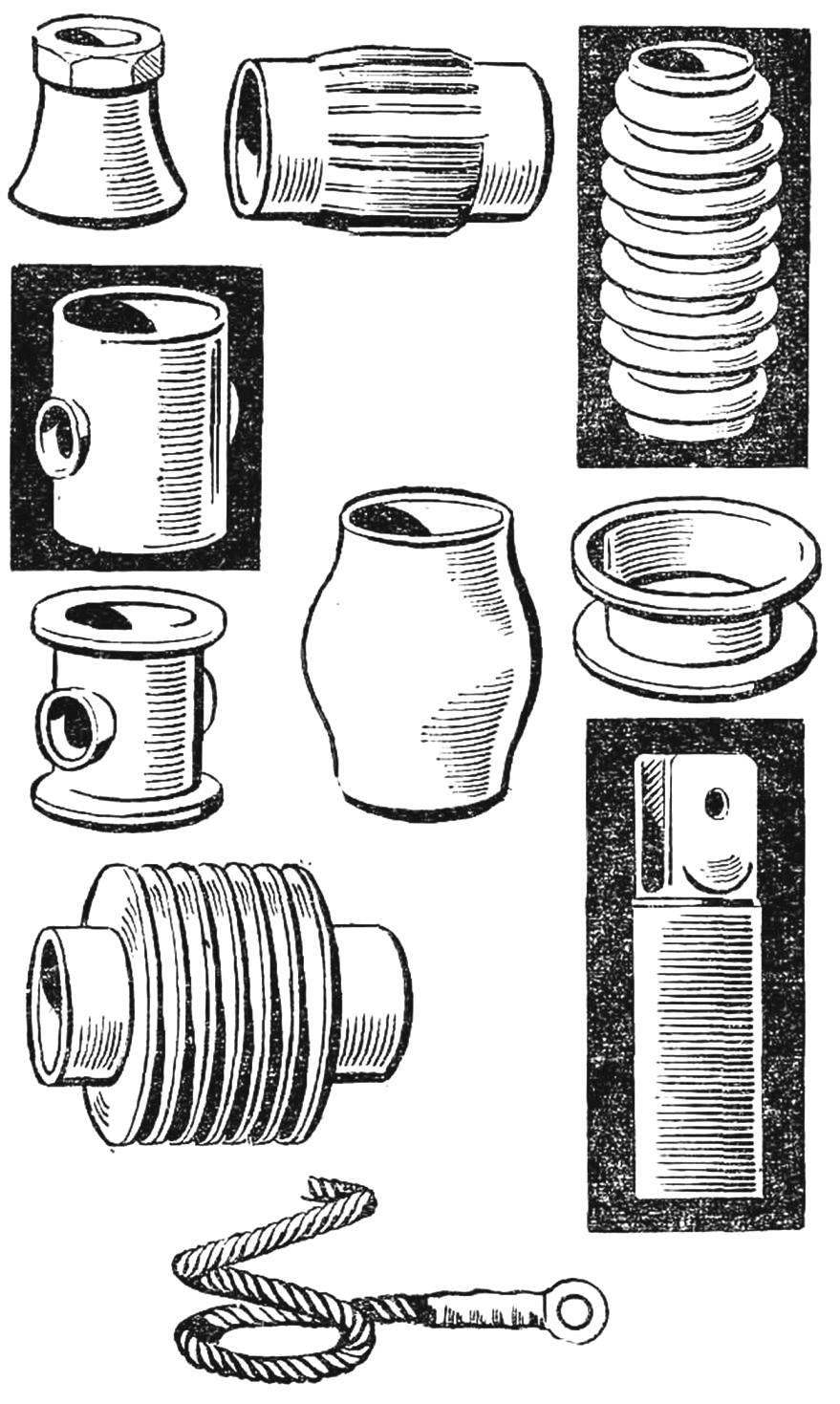
Fig. 6. Samples of parts produced by the method of magnetic forming.
The most effective setting can be used in the processing of metals with high conductivity: copper, aluminum, and magnesium alloys. The mechanical impact on the workpiece is produced directly by the forces of the electromagnetic field, without the aid of any auxiliary solid, liquid or gaseous bodies. this setup compared to other models doubled the energy resource part, by bundling its special low-inductance capacitors type MEOM-2 at a voltage of 10 kV or 20 kV, explosion-proof. The installation has a perfect scheme of automation, protection and measurement, increasing the reliability of its work.
The creators and developers of press-forging machinery demonstrated on VDNH USSR magnetic-impulse installation Miu—20/5—2, the range of technological operations which includes punching, forming sheet material, compression and various Assembly operations.
Particularly effective are materials with low ohmic resistance — copper, aluminum, brass. The thickness of the workpiece can reach up to 3 mm, the surface area up to 400 cm2. Metal has higher resistance and is better handled small-sized items.
Magnetic – impulse installation universal and easily can be integrated in an automatic line. It serves one person. Mode of operation — manual and automatic. Special locking system ensures safe maintenance of the installation.
Form of stamped parts and the scheme of technological operations depends on the design of the inductor and snap. For example, stamping from sheet metal and thin-walled tube (forming, deep drawing, cutting, punching) is performed using cylindrical inductors.
Magnetoimpulse application of the method of manufacturing parts in a number of technological processes gives a big economic effect. Reduced costs of tooling operations forming, punching, embossing, significantly increases productivity at the Assembly operations.
I. IRGER