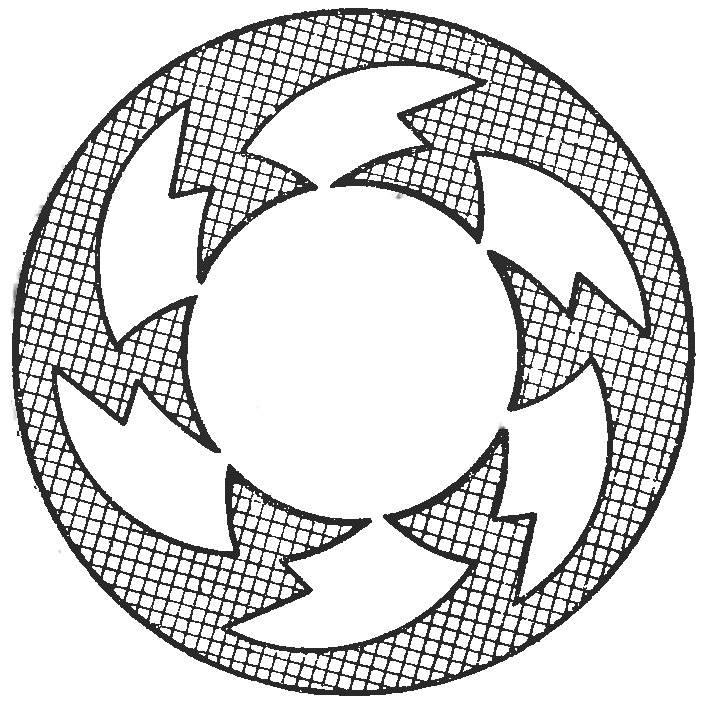
However, at the Exhibition of achievements of national economy of the USSR of great interest to innovators has triggered new types of bearings, marked by a series of patents. They were presented at ENEA USSR Institute of mechanics of metal-polymer systems, Academy of Sciences of the Byelorussian SSR is one of the participants of a large exhibition dedicated to the 250th anniversary of the Academy of Sciences of the USSR.
Researchers at the Institute used to develop bearings modern materials — plastics and a new set of properties, absent from previous designs.
Today we introduce young innovators from units of the NTTM, the enthusiasts of the introduction of new techniques with these exhibits VDNKH, which opens great opportunities and resources to save scarce metals, for improving the durability and reliability of constructions of various machines and devices.
“SWING” FRICTION
He’s like a technical puzzle: and on the shaft is not mounted, and the ring of the housing is not pressed and at the same time about it, it is reasonable to say both the first and second.
This bearing is called “improvisationalist” (Fig. 1). It is a nylon bushing with longitudinal outer and inner grooves that is installed between the shaft and the bearing housing. Fit moving, with small gaps. These gaps and the properties of polyamide plastic lies the secret of bearing. And it is what it is.
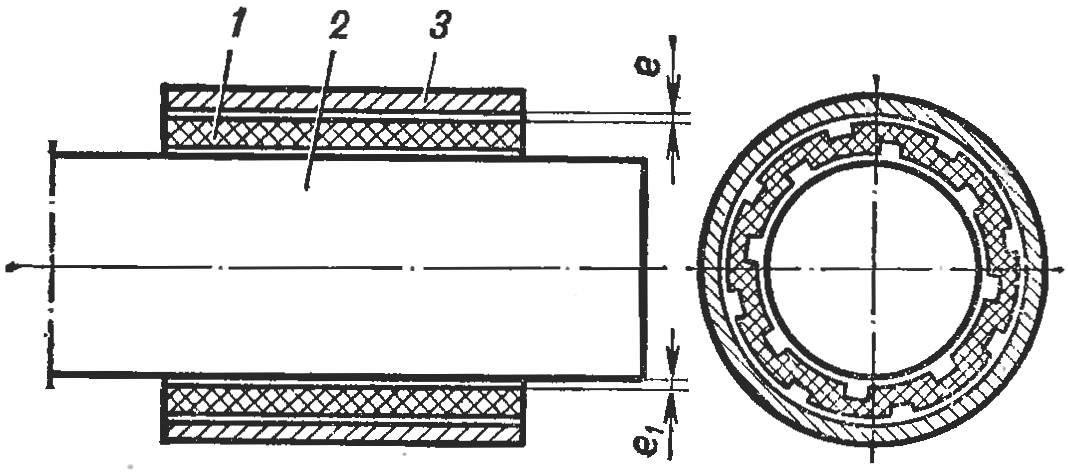
Fig. 1. Improvisationalist bearing:
1 — nylon bushing; 2 — shaft; 3 — the bearing housing; e is the clearance between the bushing and the housing; E1 is the clearance between the bushing and the shaft.
In the initial period of operation of this node, a slip occurs on the inner surface of the sleeve: it still rests against the case, and it glides, spinning, shaft — “works” clearance “E1” (see Fig. 1). But from the friction temperature of the inner surface of the sleeve increasing due to their expansion, the clearance “E1” disappears — Bush “seized” to the shaft and begins to rotate along with it, sliding its outer surface within the bearing housing: “earned” the gap “e”.
In this mode, the rotation is also critical to the heat of friction of the outer surface of the sleeve, and the inner, “clinging” to the shaft, cools. Again comes the time of the change of friction pairs: sleeve rests on the bearing housing and the shaft gets a chance to spin inside her.
Changing modes of polyamide bearing occurs so automatically, alternating in these kind of “swing” friction depending on the increase or decrease in temperature in the area of the friction surfaces.
This alternation promotes the removal of excess heat from the bearing through the metal elements: the shaft, the body. This increases the durability and longevity of the bearing, which can operate successfully without lubrication.
THE CASTLE OF THE “PETALS”
To improve the workability of Assembly and disassembly of the friction Assembly in which the bearing uses a polyamide sleeve, Belarusian scientists suggested its original design, eliminating the need for pressing or the use of any stops, restrictive washers and other auxiliary parts.
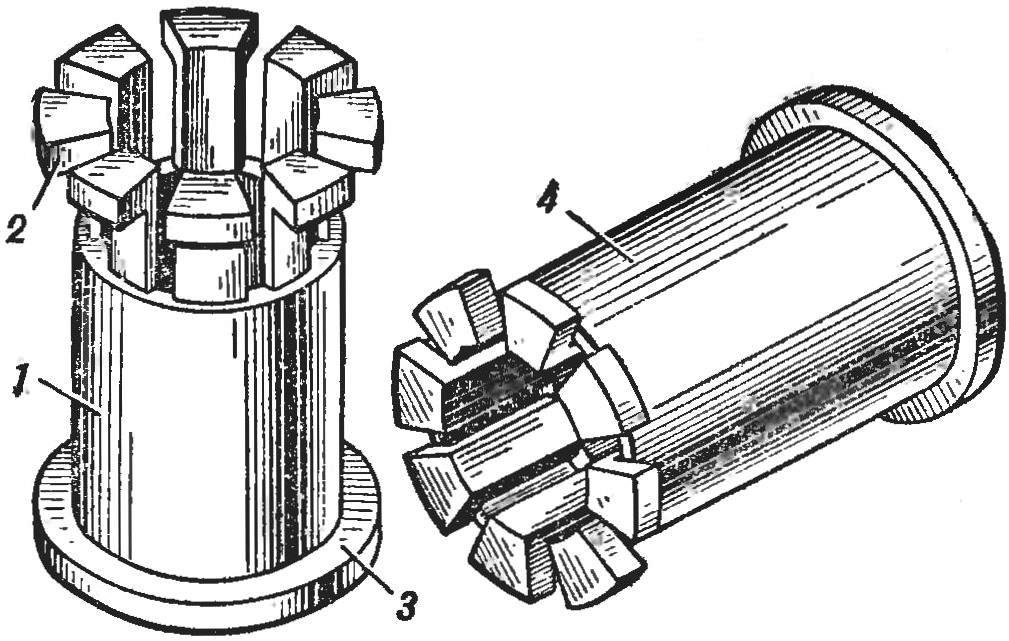
Fig. 2. Locking collar bearing:
1 — nylon bushing; 2 — section-petal rim; 3 — continuous bounding rim; 4 — body of the friction unit with bearing (complete).
For fixing the sleeve in friction and prevent axial displacement of this polyamide cylinder has two end restrictive side. One of them is a groove and slits, which divide it up into separate sectors, connected with the working part of the elastic legs of the “petals”. Compressed to the minimum diameter of such section-“petal” rim passes freely seat. With a slight click the “petals” are straightened, bypassing the edge of the hull, and, like a castle, latched to the outside, forming the second side. This ensures reliable fixation of the sleeve in the housing of the friction node.
SOFT BEARING
Among the plastics with a small coefficient of friction and high wear resistance polycaproamide the elastic. It has been successfully used to create an unusual “soft” bearing. It is indispensable for rapidly rotating shafts, where the working conditions require high damping capacity of the friction unit.
Damping characteristics of a bearing are amplified by its design. It is quite simple, despite the apparent complexity: this kind of bearing can be manufactured in a conventional mold.
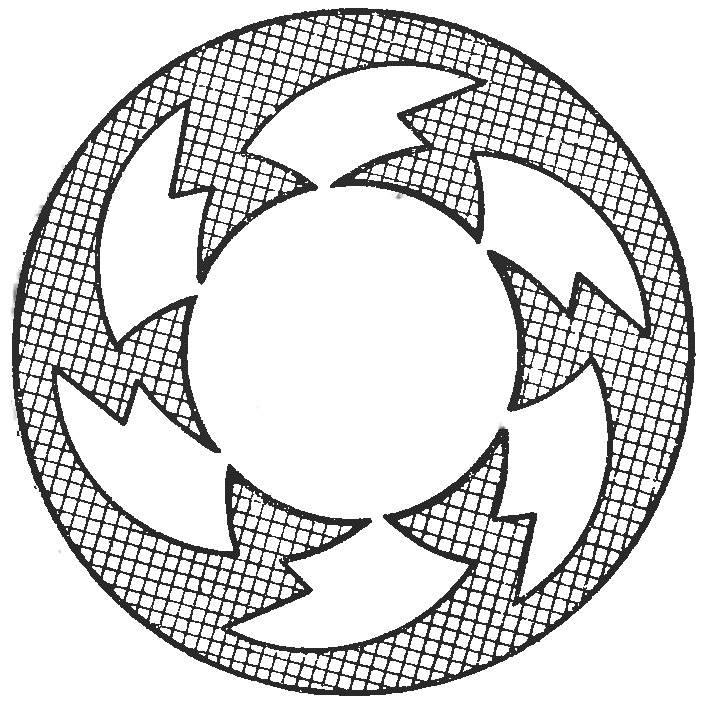
Fig. 3. Polycaproamide damping bearing.
Its body forms two rings. Internal cut into several sectors, each of which is connected with the outer ring, zigzag foot, with different thickness. This device allows to compensate for large dynamic effects in all directions. In addition, planted without clearance, “vnatyag”, “soft” bearing due to the spring legs supporting sectors will, despite the partial wear of the rubbing surfaces, also positioned close to the shaft.
When working without lubrication on the shaft to install blade: banishing air through the bearing, they will provide cooling.
THE UNION OF WOOD AND POLYMER
They resemble bracelets in yellow, like ivory, a ring of polymer dark brown squares inlay cut small wedges of wood. These matched bearings are most effective in large friction, special where there is contact with the abrasive-corrosive environments where other materials are short-lived.
The bearings consist of wooden inserts turned end to the working surface and bonded to the thermoplastic polymer: nylon waste, poly-
formaldehyde, polypropylene. Liners are also made from wood waste industries, so the bearings get much cheaper than traditional and last longer. It is important that their design allows to simplify and automate production, and hence, increase productivity.
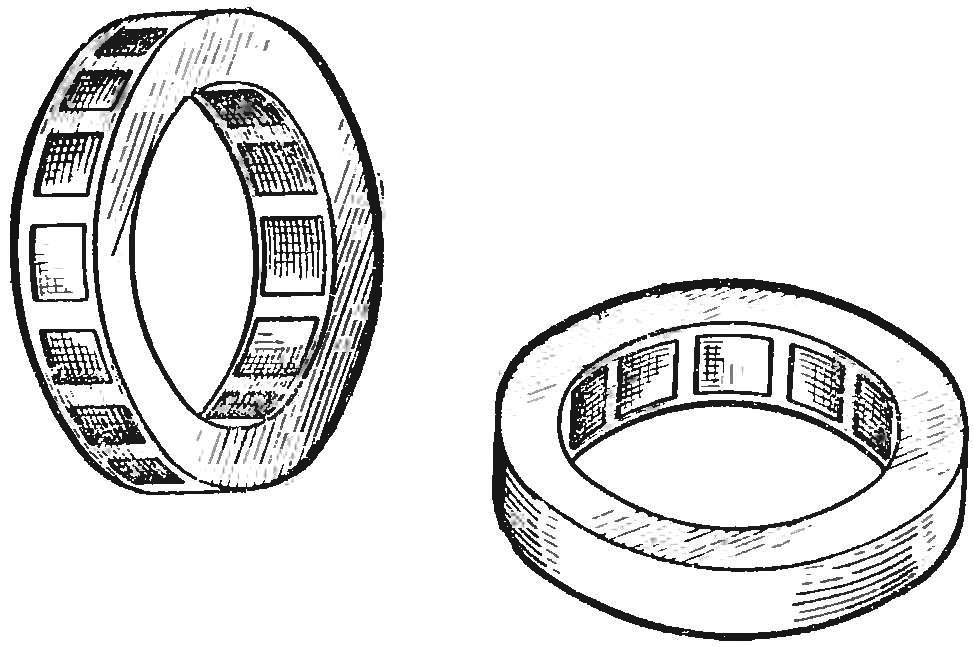
Fig. 4. Matched bearings are made of wood and polymer.
The Institute developed the technology of making entirely wooden bearings. Here created for this special material apoa-1, which is a pressed wood, filled with hot refractory lubricated with motor oil and of polyethylene powder. Such impregnation, filling the capillary system of the workpiece, dramatically enhances the thermal stability antifriction properties of wood. Bearings of material apoa-1 work on self-lubricating.
Gomel enterprises, for example, the new bearings are used in units of friction of various conveyors instead of roller bearings n 204. This simplified the design of the unit, made unnecessary the cover and the bearing housing, saving two and a half tons of metal for every thousand bearings. The lifetime of the node is increased 2 times.
Manufacture bearings from the material of the apoa-1 can be arranged at any of the logging, wood processing and similar enterprises of squared waste production that will give a considerable economic effect.
L. P. IVERSEN