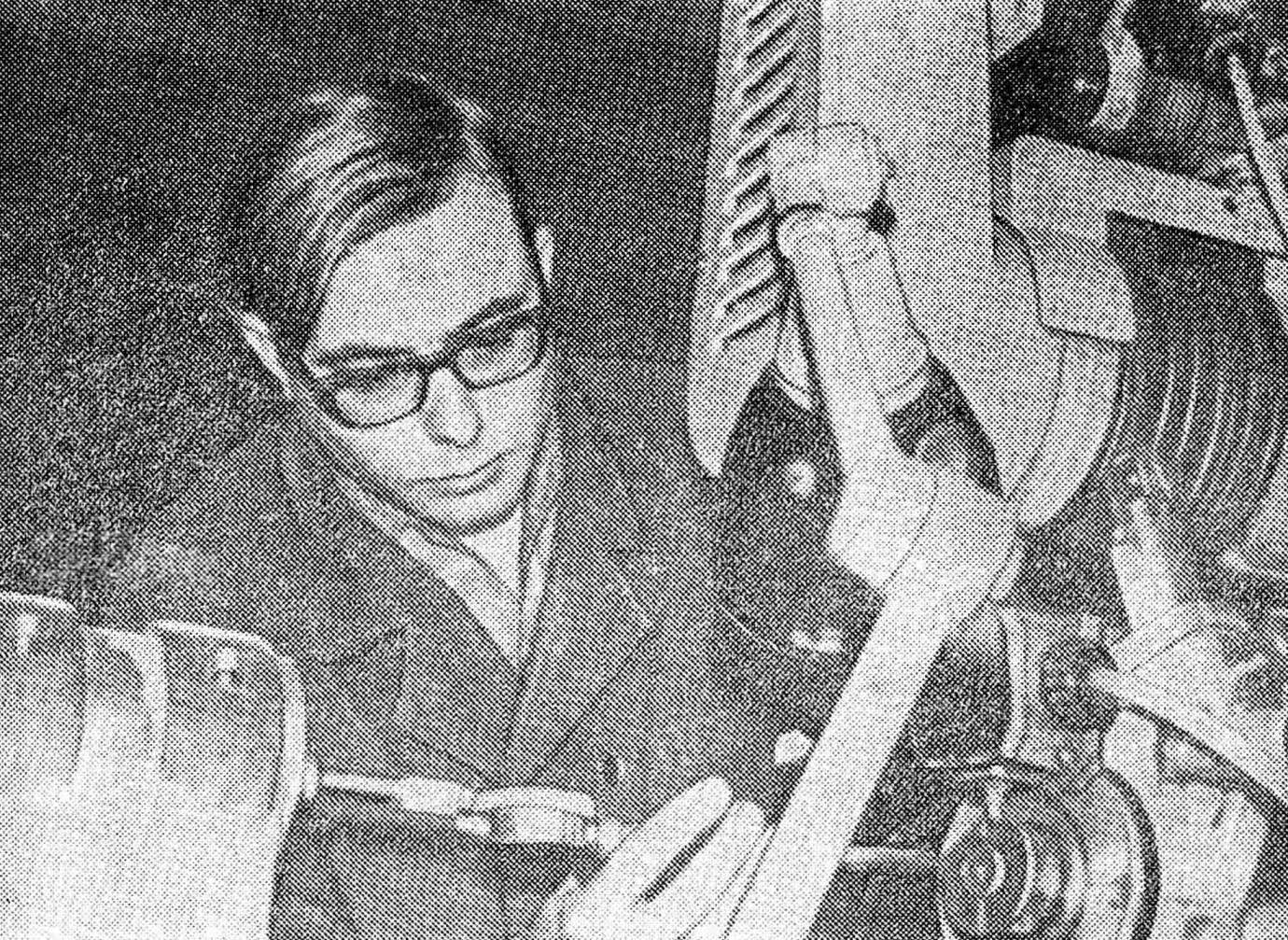
What are these shares of micron? How to catch them? And is it possible to rely on technique, even the most complex and “smart”? Yes and no. And the best proof of this is the story of grinder tool shop of the Moscow plant “Caliber” drummer Communist labor Vladimir PISKUNOV.
— Winged words “with pinpoint accuracy” if you think about it for a long time already does not apply to modern industry. In fact, those old masters, from which matter is the expression, was able soshlifovat from the facets of a precious stone high microns (although he didn’t know what it is): much to achieve manually! We are also in the manufacture of measuring instruments have to catch is not something that is ten — hundredths of a micron.
Of course, without complex and precise machines it was impossible. Take a look, how does today’s grinder. Secured in the caliper detail, put on nonius required for permit processing, programmed mode, the time — and it’s like gone. But the machine is the machine of discord, and one dissimilar metal to another and even between two parts, made of the same metal as the twin brothers look like… And control devices will notice the difference between them, if they’re doing two different jobs on different machines.
Paradox! The most accurate technique and it is difficult to assess such factors as experience, subjective knowledge of metal and its properties.
No, not a paradox, and the real state of today’s precise production, which organically combines modern technology and are not afraid to say engineer working qualifications, a rigorous formulation of metal treatment and creative ways of grinding.
This is our profession, is a profession of our “Caliber”, which sets the parameters exactly, without exaggeration, the entire industry of the country.
Here is a simple example. In some repair manual is this sentence: “the Piston pin is pressed and the piston and connecting rod with an interference fit”. And now imagine that it is treated not with a very high precision, with tolerance equal to a tenth of a millimeter. You began to repair your bike, and a finger that does not want to go into the piston or, on the contrary, enter into it freely and falls out the other side. And it’s just a motorcycle — a car is relatively rough. What precise processing tolerances must be present in the optical industry, medical equipment, other modern industries! And how to measure them? What!
Those who have been on such giants as Uralmash, “Zaporizhstal”, ZIL, our “Caliber” will seem small, modest, even some quiet company. Or you spolokhov of glass or heroic strikes powerful forging machines, no humming of the conveyors. Clean, small, silent machines behind them are my friends, intently bent over a little, one might even say, tiny details. Meanwhile, without “Caliber” would not have been able to work a ZIL, or “Uralmash”, or any other company. Because “Caliber” is the most accurate measuring tool — from friends all “stangely” measuring calipers — up to electronic micrometers, is able to determine the imprecision of a few hundredths of a micron. These devices in the hands of the worker, the master, the TCI controller will allow the processing to bring the details to the required normal size, discard those that do not meet the standard. It is clear that every such device is a lot of small parts, made according to the highest accuracy class. Because any error of the micrometer, a measuring bracket, tiles Johansson will panagitsa for hundreds or even thousands of unhealthy details, which will need to use the smelter, turn into thousands of losses for the national economy. That’s why we have a “Caliber” are specialists of the highest qualification, that is why young people here are taught gently, lovingly and carefully.
The honor of the factory marks. How can you not say a few words about it. To fight for quality products call on the stands installed at the plant, this topic is devoted to regular meetings of party and Komsomol groups of the workshop. I think about her every hour, and enterprise managers, and workers — those who are directly dependent on the quality of products reaching the domestic industrial enterprises and almost 45 foreign countries. Care about the honor of the factory marks and permeates all the daily work of the hero of our story, Vladimir Piskunov.
— I’m not that green! — With these words Vladimir Piskunov started in 1961, his first conversation with a master teacher, is famous not only for the plant but also throughout the industry as a sander by Yefim Jakovljevic by Zamurueva. And I must say that some of the grounds for such a categorical statement he was.
The most common fate of this fellow workers. Good working-class family was taught him work skills. Attentive teachers in school before noticed the young man with a love for physics, engineering, mathematics. It was also the third summand of the formation of his character — circle design microvesicles. In those years, Volodya lived close to ENEA, where the housing Department worked an old teacher, a passionate designer of various technical projects albert M. Laur. To Laura flocked the boys of several neighborhoods, because here did not simply model, is not engaged in sawing shelves or tiny boxes, little “men” — and he at that time was 11 years old — designed microvesicle. From the first steps in the circle, they knew that for a long rough work, with abrasions on his hands and clothing smeared emerges a day of joy when you first sit in the saddle themselves constructed the car and proudly drive it, attracting envious admiration of your peers. No matter how bad the hardware mug, but the guys still managed to get here with the basic skills of metalwork and turning, to learn the basics of design and, most importantly, to learn independently, to think creatively. Five cars were constructed in a circle for a while until it worked Volodya. And each of them was a large proportion of his work.
That’s why when it came time to go to the factory, and it happened after the end of 8th grade, Volodya already knew, which leads him to working profession. It only remained to choose what to become — a lathe, a milling machine, a Scriber or grinder. Volodya felt that each of these specialties may be subject to him. In school Volodya liked to bring detail, that is, to the condition, to make every tolocka, each clutch not only worked well, but was beautiful in its completeness.
This is what has determined the final selection of a worker. Tried initially, plumbing, Vladimir became a student-grinder for surface grinding machines.
— You know, this is a very interesting thing — grinding, — said Volodya. — Interesting primarily to the fact that you, so to speak, crownest their work a long chain of transformations of metal before it becomes a detail. If I make a mistake, will come to nothing work of dozens of my friends who worked with that piece of metal to me. Can you imagine what a responsibility! And that sense of responsibility not only to the technical control Department (I work without QCD), and especially in front of many friends at work, perhaps one of the most characteristic features of this grinder.
And the metal — he’s cranky, all the time he puts in front of you the tasks that need to be addressed, resorting to the help of dozens of reference books, consult with more experienced producers. Here we talk about the need to REMOVE two microns; it is particularly difficult if you have to work on intragrinding machine — processing the internal surface of the part. Yes, we have very precise machines, CA which we do this work. Yes, on many occasions we have reference. And yet modern grinding business requires special skill, special creative approach to work.
Grinding for third-party look less spectacular than, say, turning, or milling work. Those changes that contribute to the detail of the wheels, not visible to the eye. And speed of processing is not the same: to remove unnecessary microns sometimes much harder than to whittle away two to three inches. Maybe that’s why and competitions for the best profession is held among the grinders of the plant without much fuss, without the bright lights of the newsreel. But are carried out regularly. And Vladimir Piskunov today — a recognized leader among the finishers a “gauge”.
What is that leadership?
In the same way as in the circle design microvesicles, from the first steps at the plant Volodya was taught to think. Because the job of a grinder is not a mechanical up once and for all established operations. Every detail puts its puzzles, requires a different approach. One Turner took off less metal, more on the other. That means we need to calculate what range it is more rational to handle it. This skill Volodya received from their mentor teachers, perhaps the majority of today’s “aces” grinding Yefim Yakovlevich Zamurueva. An inexperienced worker will take fine grit and will process the item for a long time, stopping her so overheating did not affect the configuration. So, in fact, encouraged technologists. Piskunov solves the problem in two stages: rough machining (rough, of course, is relative — we are talking about the same micron) and fine final sanding.
Such small and significant rationalization of a process born in the shop very often, especially when there’s new products. Of course, not all of this is made in the form of improvement suggestions, but did not conceal secrets here, every notion instantly becomes the property of the shop.
That is what the friends of Volodya in the shop — Miller Anatoly Aleshin, Vladimir Orlov, Turner, mechanic Boris Ivanov, dozens of other leaders. Nuggets of excellence, born in the shop, carefully collected and spread throughout the plant members of the VOIR, not worth the side BREEZE. A lot of them, such rationalizations, improve the quality of products of your Calibre contributing to the fulfillment of the plan. And that is important — they all testify to a new level of thinking with which comes the modern worker, that the creativity is in the process of production more and more the place that without continuous technical creativity directly in the workplace today is simply unthinkable qualitative growth of the company’s products.
— Each of us — says Vladimir, — have, for example, a long time to learn that the color of the spark determine how much Microm removes the circle, But each metal spark their own! Here, for example, recently born I have one improvement proposal. Treated I detail conical shape — made internal grinding. For a long time to try — picked modes, tool. You see, inconvenient, low-tech to handle it on my machine: much time is spent ka workpiece and can not provide the precision machining that is required; the spark “shows”: circle takes a little more than required “weave” micron. Helped knowledge of the turning of the case and another memory: as we in the circle design mikromotivov polished overflow window. Lathe plus sandpaper — it was enough to get the required clearance.
Some puzzles have to solve every day.
* * *
Thirteen years spent on the “Caliber”. There was a break, not the army, the other years in the same shop, same machines.
— Not boring?
— How can that be boring? — the question at issue meets Volodya.— Here I talked a lot about how he became a grinder, but, in addition, I had over the years to master the use of lathe, milling, localwiki (and not only me, but many of my comrades, because we have in the shop interchangeability is the norm). And each new specialty was, if I may say so, in my main piggy Bank, expanded my horizons.
— In short, for life — grinding?
— Only way more Interesting profession I can not see for themselves.
* * *
Conventional biography, the usual fate of our contemporaries, to get acquainted with the technique as a child and not intentional to leave her life. To this we can add only what Volodya modestly silent, and what his companions say with pride and respect. Permanent YCL, excellence in socialist competition in recent years at the plant, and, today, arthropods instrumental. Here the public face of Vladimir Piskunov — ordinary service exactly one hundred masters of the famous “Calibre”.
Yu BEKHTEREV