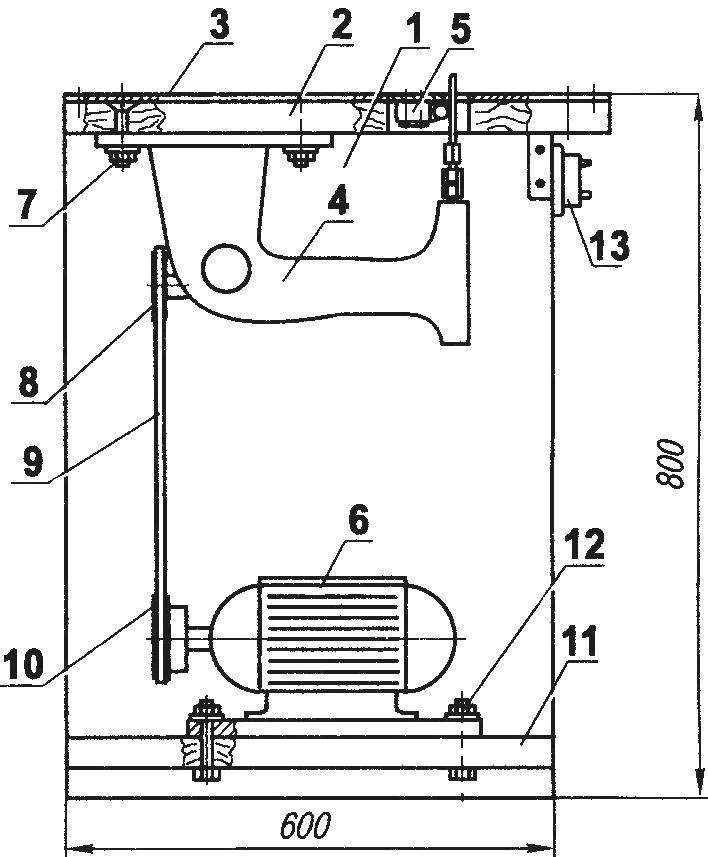
On the protruding end of the main shaft mounted pulley with a diameter of 80 mm for belt transmission (you can take from the old foot operated sewing machine only it is necessary to counterbore under the belt). Such a pulley, but a bigger diameter (100 mm) mounted on the motor shaft. Motor — single-phase (220V) with a power of 180 watts and a speed of 1,350 per minute together with the pulley used from an old washing machine.
The electric motor is secured on the lower platform of the pedestal, made from quite durable bakelitovogo of plywood 20 mm thick, as in the pedestal of the platform-the floor was not. The platform pre-installed on the holes in the legs of the motor cut out elongated slots to move the motor with the purpose of tensioning the drive belt.
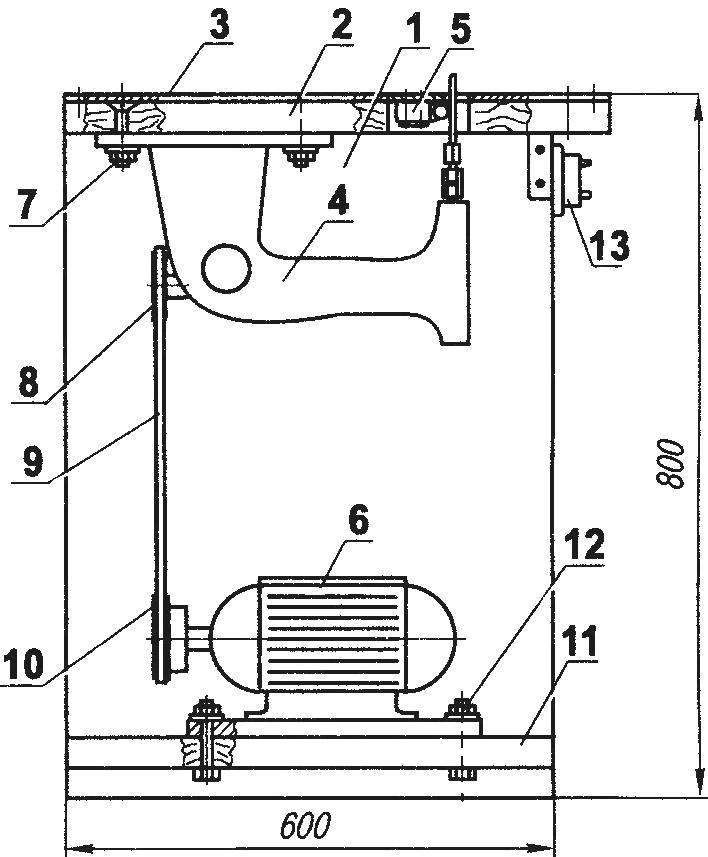
Stationary scroll saw wood from a sewing machine:
1 with the side wall of the Cabinet (foot operated sewing machines, 2 PCs.), 2 — top tables (from the foot of the sewing machine), 3 — coverage table tops (steel or aluminum sheet of 1.5 s), 4 — case (sewing machine), 5 — sawing the node, the 6-phase motor of N = 180 W, n = 1350 rpm (washing machine), 7 — mount housing to the table top (M10, 4 pieces), 8 — a driven pulley Ø80; 9 — V belt (profile 0), 10 — drive pulley Ø 100, 11 — platform (plywood s20), 12 — mount the motor to the platform (bolt MI2, 4-piece), 13 — starter
The most complicated to manufacture, requiring some experience working with metal, is the sawing site. But precision (very accurate) performance it requires, therefore, its details, down to the nail files, too it is possible to do yourself. Sawing the node shown in the figure. On the needle bar fits over the mandrel with the slot, is made of a hexagon, which is fixed by lock screws. The slot in the mandrel is inserted the nail file on a hanger which fits over a pre-washer with a slotted hole and groove. The washer is in its groove rests on the shoulders of the blade. Then put on Union nut and carefully tightened. In order for the blade did not break, a node resistant roller. To do this, the cover propisyvaetsya hole size 65×13 mm. Above this hole to the cap symmetrically fastened with screws with countersunk head plate. Under it is dolicocephaly. Fixing is by countersunk screws and a plate with two threaded holes. The roller, made of steel, is mounted in the slot of dolicocephaly and fixed with a rivet-axis diameter of 3 mm. Plate must be installed flush with the surface of the lid, so you need to choose the recess under the plate with a chisel.
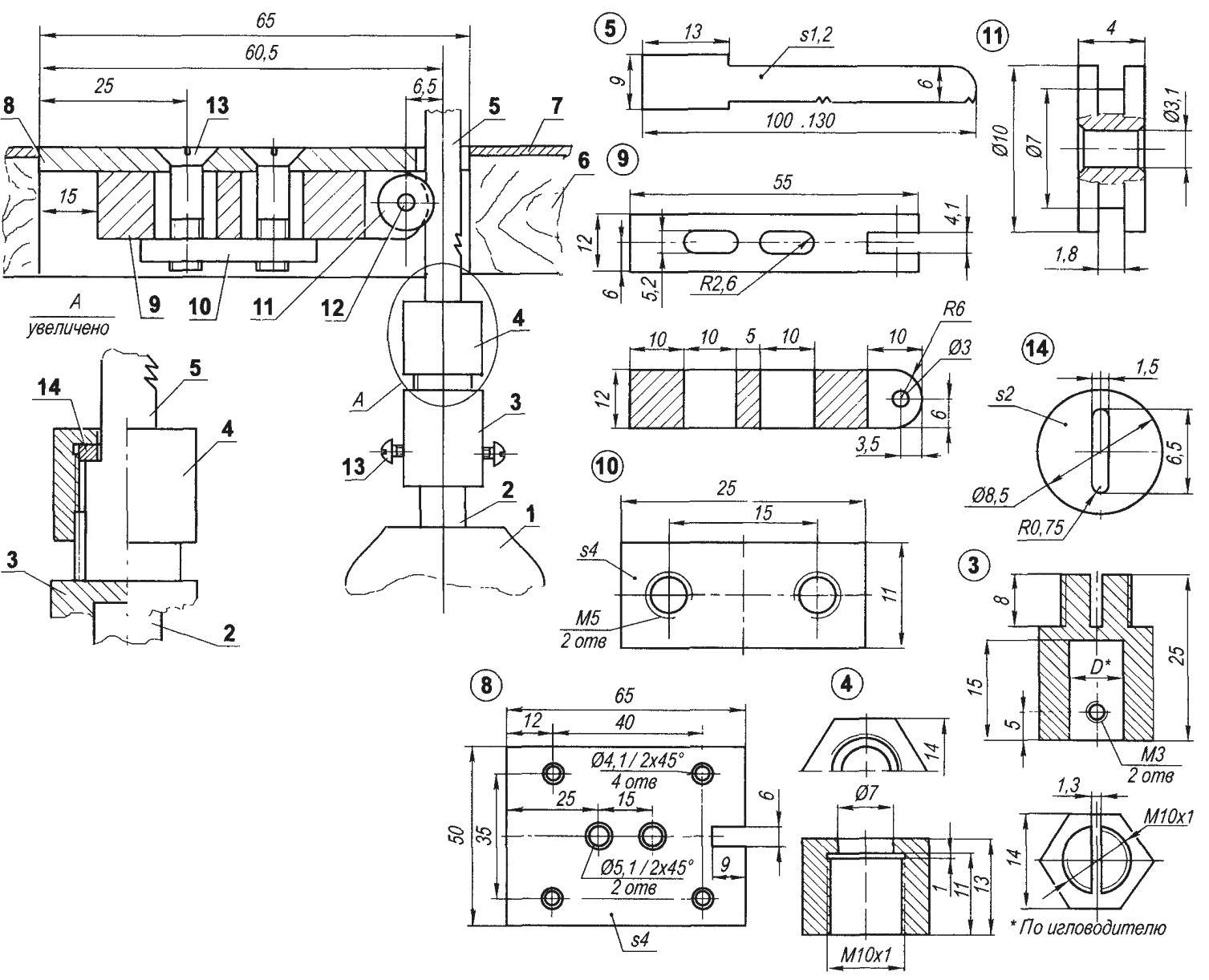
Fig. 2. Saw unit:
1 — body (sewing machines), 2 — needle bar (0t sewing machines), 3 — mandrel (steel, hexagon s14), 4 — nut (steel, hexagon s14), 5 — blade (purchased the product). 6 —counter, 7— finish worktops, 8 — plate (steel, sheet s3,5), 9 — roller-holder (steel) 10 — plate-nut (steel. sheet s3,5), 11 — roller (steel, circle 10), 12 — axle roller (steel wire Ø3), 13 — the stopper mandrel (M5 screw, 2 PCs.), 14 — a retaining washer (steel, circle 8,5)
The blade is made of carbon steel, if you do not purchase. Teeth cut out a small file and cut the same shape as the longitudinal hacksaw. The teeth should have a divorce, but as they are very small, to use for this purpose a special tool is almost impossible. Therefore, the leaf blade it is necessary to clamp in a small vise, then borodkom and hammer should be applied through the tooth thibaudia light strikes. Then turn the blade and in the same way, bend the remaining teeth. After sharpening the teeth have to be hardened.
At such a stationary scroll saw work easier and more productive than electric hand, especially with small blanks and the quality, in my opinion, is much higher.
Y. KURBAKOV, Tula