Is made whether furniture or other woodwork — home of the wizard there is a desire to decorate their curly reliefs, patch convex pattern… Here it would be bailed out lathe. But the store to buy today is expensive. Do it yourself is another matter. The Bulgarian magazine “Young designer” offers to remember the simplest design, which was used by our grandfathers. It is attractive because it is available in the manufacture of almost everyone, has no complicated components and does not require any scarce materials. As possible, despite the “old days”, is no worse than any of the purchase options: after all, fine examples of folk art, which we admire in the local history and ethnographic museums were created about the same machines.
The first thing that you notice looking at the proposed design — it has no motor. Drive serve as a foot pedal and a crankshaft, the United articulated metal (although it can be hardwood) thrust. The crankshaft is fixed to the flywheel, promoting uniform rotation of the workpiece clamped between the shank and the headstock taper of the rear. As the flywheel will fit, for example, the massive wooden round (cut stem of suitable diameter) or recruited from thick boards (two or three layer) drive, respectively, treated with hacksaw, files and sandpaper.
With the flywheel rotation is transmitted via a leather or rubber strap (or cord) on the drum headstock. Since the latter has at its entire length the same diameter, changing the speed of rotation of the workpiece depends on the working pressure of the pedal. If the drum to perform a series of pulleys of different diameter, the desired speed can be obtained by a simple throwing of the belt. But then you need to come up with a device to tension the belt when converted from larger pulley to smaller one.
To connect the listed parts and assemblies in a single structure serve wooden posts in turn supported on wooden glides. And they themselves stand, and the glides are made of the same boards in the thickness 20…25 mm. the Longitudinal strength of the structure to attach the lower and upper cords. In one of the lower —the one that is longer, combining all three stands (pipe or bar), is hinged pedal. And above it, on the top of the bundle (Board, like the racks, but at half their width) is set caliper, which will be the base machining tool: chisel, chisel, file or sanding block. The caliper can move horizontally and to be fixed in the right place due to the bottom placed eccentric with handle. All the parts of the caliper are made of solid wood.
The node — H-shaped housing; it can be executed in whole or from bars. The upper groove is inserted into a bearing for the tool (the bar), and the lower bar slides along the top of the screed machine, fixing its position the Cam is a metal disc with an off-center square hole; the same hole and handle strap. Included in them is the pivot-axis has the same square section as the middle part of the shaft headstock, install the drum drive. Head headstock ends with a tooth that holds the workpiece.
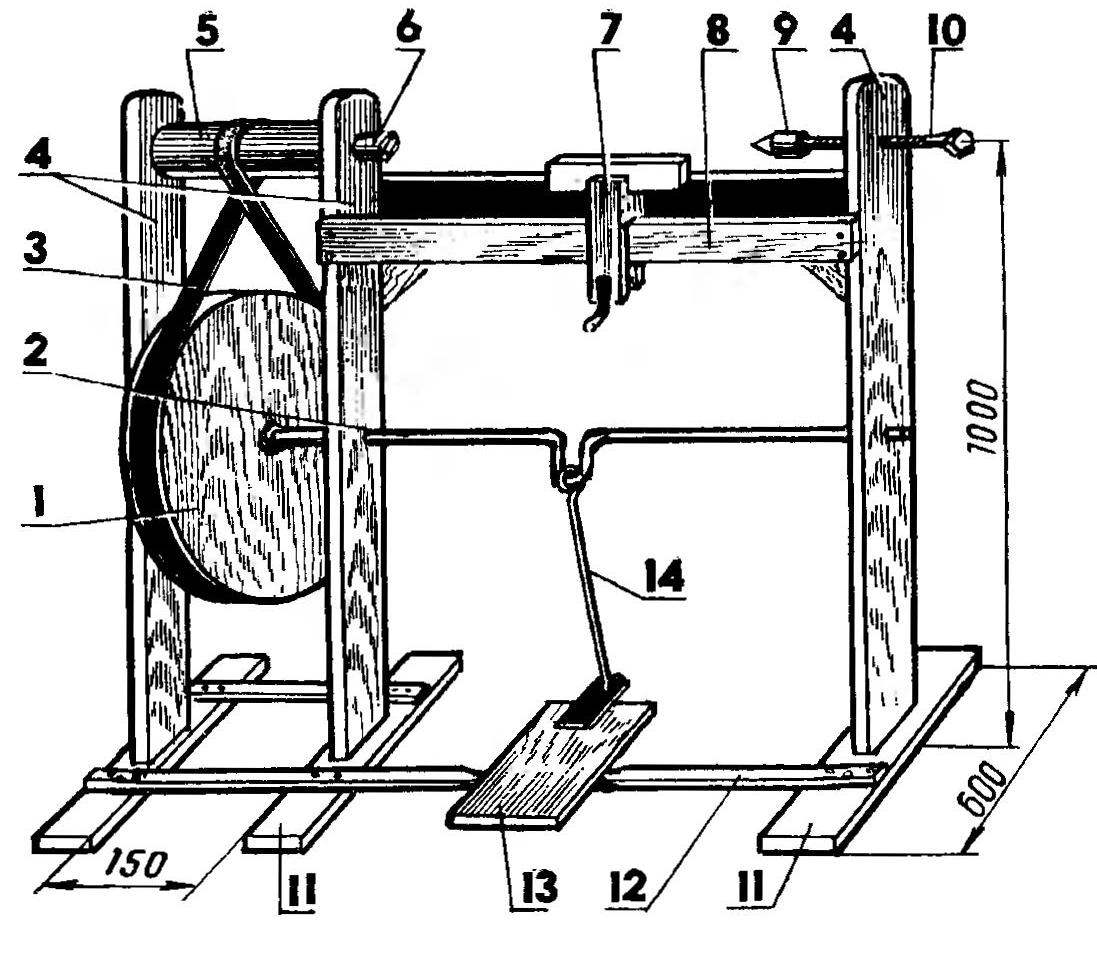
Treadle lathe for wood:
1 flywheel, 2 crankshaft, 3 — belt 4 — rack machine, 5 — reel headstock, 6 — shank headstock, 7 — support, upper tie (guide saddle), 9 — head tailstock, 10 — bolt tailstock, 11 — glide racks, 12 — lower tie bar (pedal), 13 — pedal 14 — pull of the pedal.
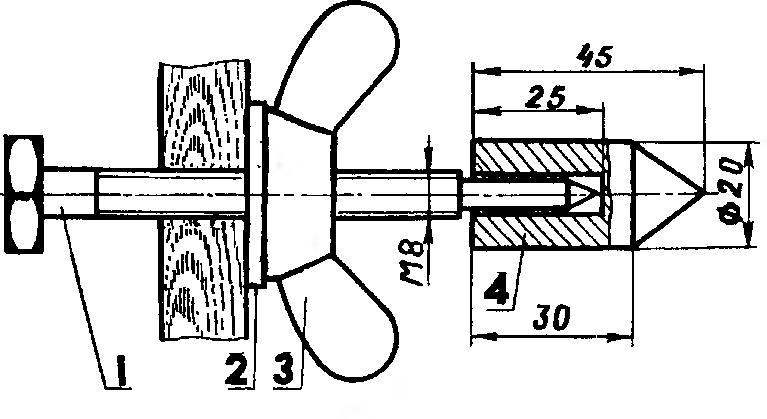
The tailstock of the machine:
1 —the thrust axis of the head (M8 bolt), 2 — balance shaft 3 — wing nut adjustment, 4 — head grandmother.
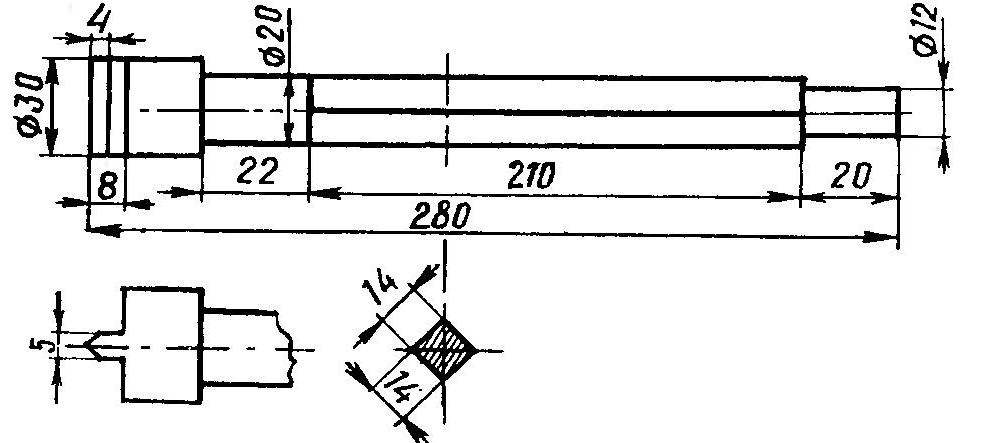
The shaft of the headstock.
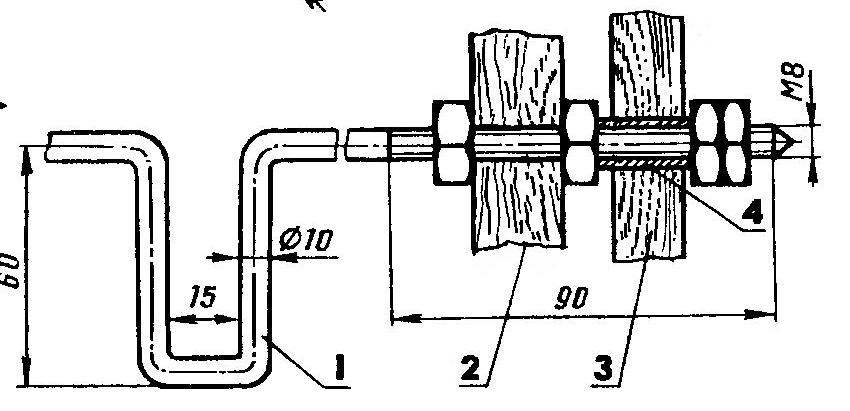
Node installing the flywheel:
1 — crankshaft 2 — flywheel, 3 — strut, 4 — Bush.
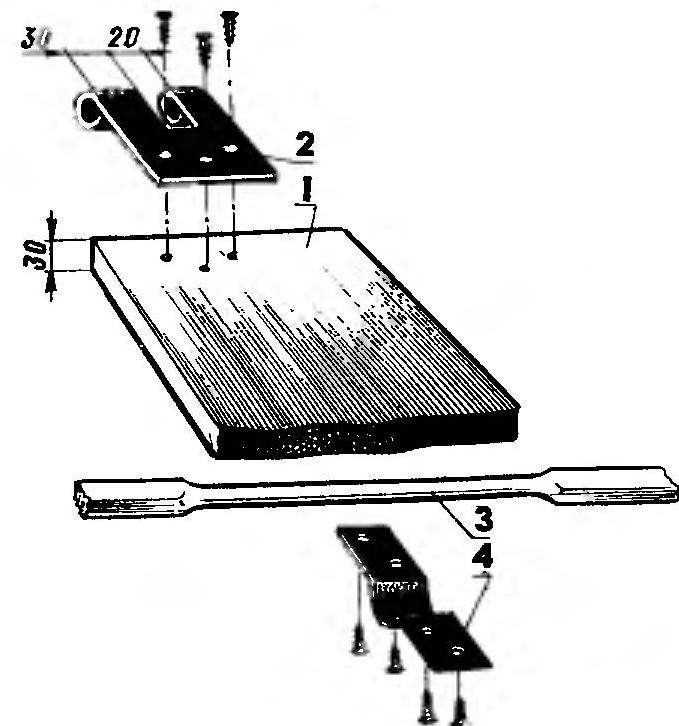
The pedal Assembly:
1 — pedal 2 — loop thrust 3 thrust bearing, tie racks, 4 — hinge-hinge pedal.
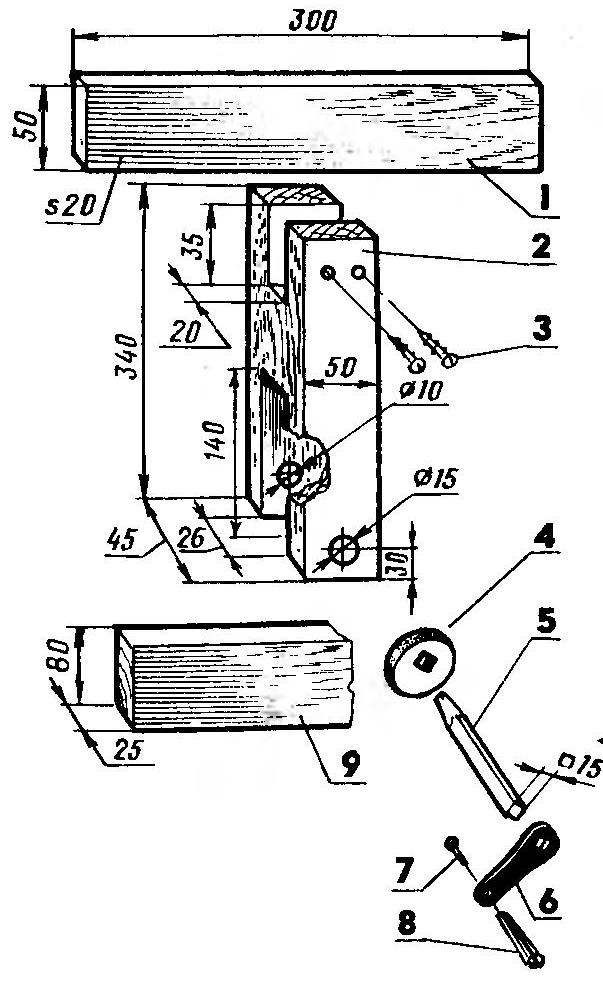
Caliper:
1 — support, 2 — N-shaped body, 3 — screws of fastening of a support, 4 is the clamping disk-Cam, 5 — axis Cam, 6 — handle strap, 7 handle screw, 8 — handle, 9 — upper tie bar of the machine.
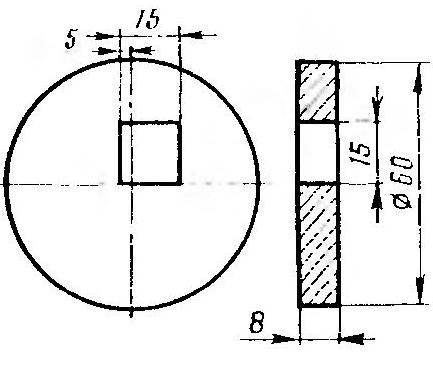
The eccentric caliper.
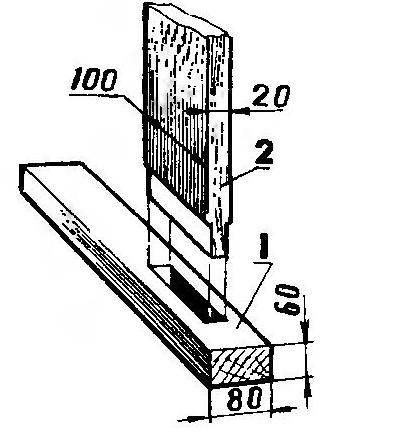
The rack clamps:
1 — bearing stand with a window under the tongue, 2 — limit switch stands with spike.
The crankshaft is made of steel rod with a diameter of not less than 10 mm At its shank is a sleeve —to protect the wood stands in the place of rotation of the threaded portion.
Connecting struts with the thrust bearings and fit the pedal is clear from the drawings. Tailstock in the hole of the stand can be without additional protecting sleeve as rotating part it is only the conical nozzle. The main detail — the axis — is a M8 bolt with a wing nut and washer abutting the strut when the clamp parts; the limit bolt is tapered to facilitate rotation of the head head (instead you can use a mortgage steel ball).
The workpiece does not have to be rectangular, otherwise inexperienced “Turner” without injury, because the instrument is not secured, supported only by hands and caliper support. Therefore, feeding of crafts from scrap materials the last place to protecive should be gradually and very carefully. If it is necessary to grind the bar, then you first need to fillet it rough with a file (on the same machine), and only after that use the tools.
Ready sawn chiseled detail in half, you get two beautiful embossed lining for decoration of flat wood panels, furniture, window frames or shutters in the country, various frames, built-in cabinets, doors. Before mounting such workpiece are carefully processed cloth, the stain (before lacquering) or painted with oil or enamel paint.