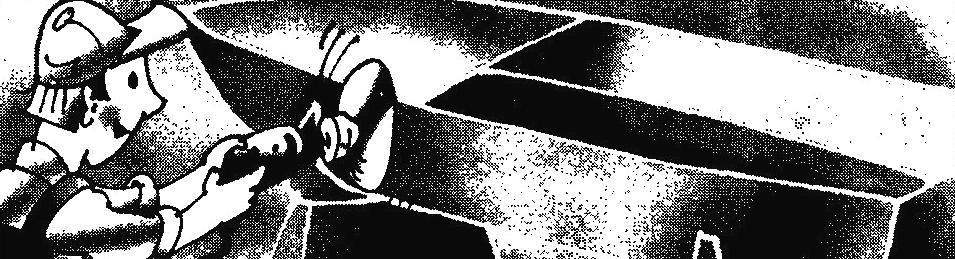
The most widely treatment with the use of electric drills. In its cartridge is clamped to the mandrel on which the rubber is mounted sanding disc on fabric. However, the complexity of polishing the fiberglass remains quite high due to the significant mechanical strength of the treated surface, and low resistance grinding materials (disc, tapes etc.).
To facilitate the processing of fibreglass is recommended for the manufacture of the additive in the binder (epoxy, polyester resin) 8 — 10% talc: this makes the material more pliable abrasive, but at the same time practically does not change the mechanical characteristics of fiberglass. With the same purpose, widely used grinding fiberglass waterproof skins for heavy wetting with water.
Good results are obtained also in the wetting of the treated surface with white-spirit, possessing high lubricity. However, upon completion of the polished surface should be degreased, as the remnants of white spirit interfere with the adhesion of subsequently applied on the body paint materials.
Practice has shown that the use of sanding discs paper backed irrationally as their durability under 2000 rpm spindle drills does not exceed 3 — 5 minutes.
In the circle of hydrocortistab Donetsk obsut have been designed, fabricated and tested a special sanding disc for machining of fiberglass, the main difference from existing products is a special arrangement of the abrasive grains, and the use as a binder epoxy resin, thus increasing the radial stiffness of the disc.
As the workpiece used a standard grinding disc on the basis of tissue with a diameter of 200 mm (TU 18-20-82, article 53-28, grit — 25). Of the same disks (preferably used) are cut additional discs with a diameter of 90 mm and 100 mm, respectively. They are glued to the outside surface of the standard disk. For the remainder of the applied layer of glue EAF (TL6-15-1070-82), prepared according to the instructions attached to it, but which added 10% of talc. The thickness of the adhesive layer is 0.5 — 0.8 mm. Then from the waste of grinding wheels with the value slippery in diameter 50 — 100 mm (the size fraction 500 — 1250 µm) is removed and sieved on glued surface of the disk layer of the abrasive grains (in the design used abrasive grain E9, К37).
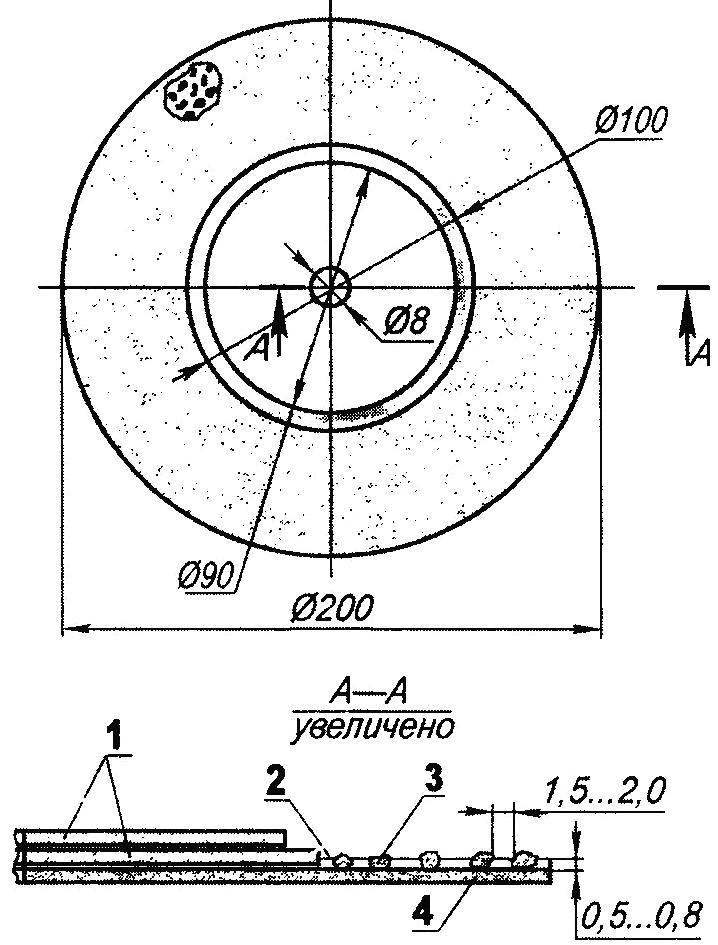
Combined grinding wheel:
1 — pasted additional disks of smaller diameter; 2 — layer epoxy glue; 3 — abrasive grain; 4 — core grinding wheel
The density control the location of grains on the disk surface is carried out visually. The average distance between them is 1.5 — 2.0 mm. is a Perfect disk with a very low density, which looks like a gravel track.
After polymerization of the adhesive disk is ready to work. If the glue will be applied epoxy resin of type ED-6, it is necessary to plasticize the introduction of castor oil or dibutyl phthalate with the purpose of increasing the elasticity of the disc.
The existence of glued more fabric disks greatly increases the radial rigidity of the grinding tool. Using the same stock standard ROM allows to combine in a single product the different abrasive properties of regular and self-made tool that facilitates the work in the finishing operations of a number of surfaces of the housing.
As shown by the exploitation of the thus produced disc, their durability is 140 — 160 minutes at a rotational speed of a spindle electric drill 3000 rpm.
Additionally, it was noted the lack of damage to the grinding wheel in place attaching it to the rubber part of the mandrel that can be attributed to increased friction forces between rubber and abrasive coating of the disc. In General, we can note the increase of tool life 5 to 6 times compared to a standard cloth. In the same way it is possible to produce grinding wheels of other sizes as well as abrasive blades for machines such as “ELEKTRA” and others.
In the case that the disk surface becomes clogged with food processing, it can be easily cleaned by rinsing in acetone.
Should pay attention to the safety warnings at the time of manufacturing disks, and work with them using the electric tool.
Work with glue EAF should be done with good ventilation, rubber gloves. When using the tool it is necessary that the clothes were not waving parts, and the cuff was buttoned-down. A prerequisite is the use of protective goggles and a respirator (or at least a gauze bandage). Before you start, you need to check for a faulty electrical tool.
Polishing fiberglass, cover the face mask, and neck scarf (small pieces of fiberglass and resin, once on the skin can cause intense itching). To remove the products of machining from the grinding zone it is recommended to use a vacuum cleaner.
TERTERIAN S. A. BULAKHOV, Donetsk