What would be a good tool or even the machine had craftsman in the house, just drill a hole or accurately process the workpiece by holding it with pliers, and even more in the hands of, quite frankly — impossible. Therefore, in the Arsenal of anyone, even a beginner DIY enthusiast, there is Vice. However, and this adaptation is not always thus, what is required, especially when high dimensional accuracy of the parts, strict parallel, or perpendicular to its surfaces, etc., etc.
So I decided to make a vise, so to speak, at his own request. Made and I use them for a dozen years. Their appearance is now badly spoiled by careless handling, but its function vise perform still, and I’m happy with them. And they want to share their design with the readers of the magazine.
Before proceeding to describe the fixtures, I want to note that here is a slightly different version of its execution than the one depicted in the photos. The proposed design is more simple to manufacture, but not less functional. This is especially true of the configuration of the movable jaw. Operation of the clutches showed that this item is made needlessly complex and could be simplified considerably without losing any reliability or practicality.
By design, my grip screw, parallel to each other. They are made mostly on the model of the machine (machine tool) vise. But the main difference from similar devices in commercial production, of course, — small dimensions. In this case they have rather large flat sponge (and strictly parallel to each other) and a large footprint for set of workpieces, which is strictly perpendicular to the vertical planes of the jaws.
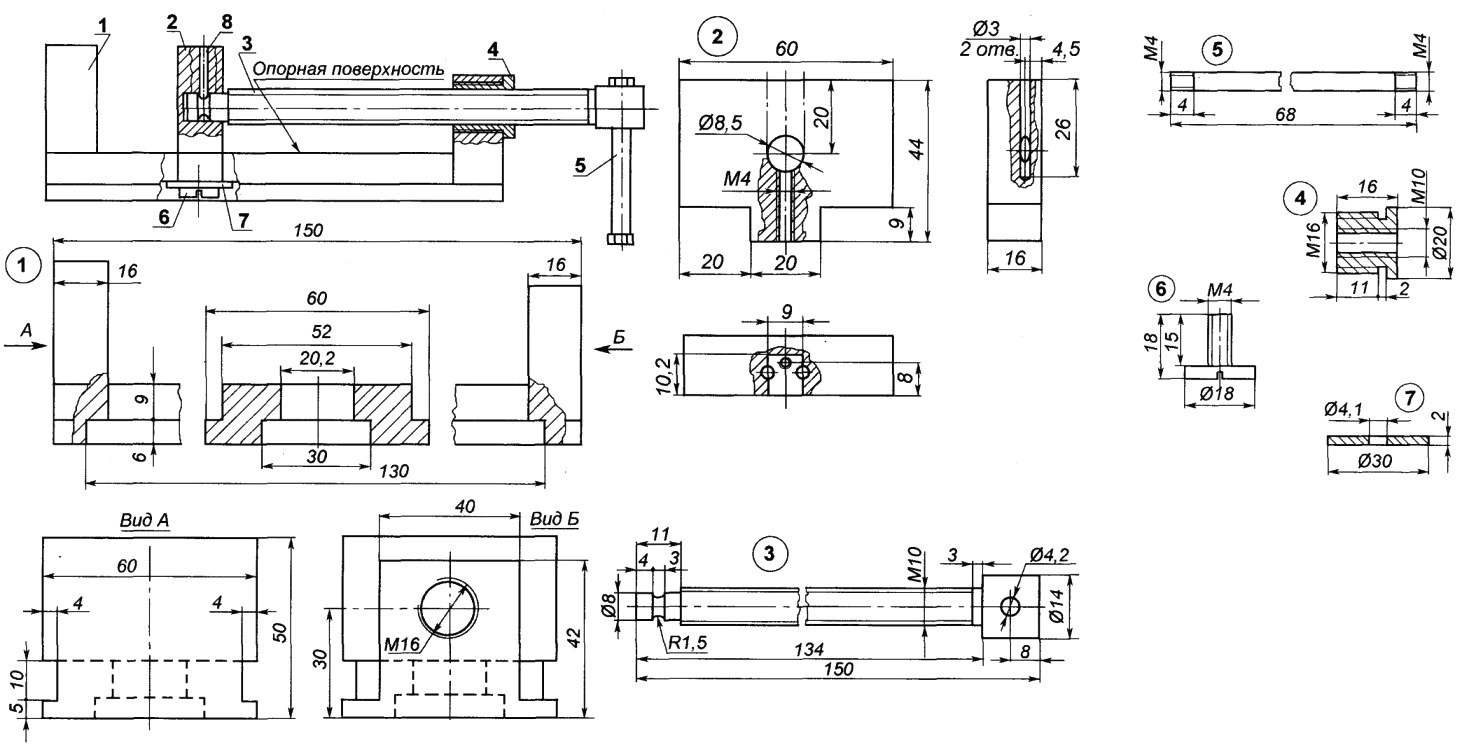
Fig. Mini-vise for machining parts high precision:
1 — base (St45); 2 — movable jaw (St45); 3 —screw M10 (St45, round 14); 4 — threaded bushing M16 and M10 (St45, circle 20); 5 — knob (St45, stud with two nuts M4); 6 — M4 screw fixing movable jaw (St45); 7 — spacer 30×4,5×2 (St 10 circle 30 or the sheet s2); 8 — pin (steel wire Ø3,2 PCs.)
Clutches consist of the following main structural elements: the base, movable jaw, screw. The most difficult to manufacture part — the base. It is made in concert with a fixed sponge and hard stand, also has a sample from the side of the sole and a longitudinal groove. In the manufacture of the base without a milling machine can not do, and turning in the manufacture of the threaded sleeve and screw. Although, if you do not expect heavy use of the grip, the threaded sleeve can not be done by running the thread under M10 screw directly into the thrust stand.
The movable jaw is detail simple, and spindle and you can pick up ready-made standard, a little refined.
Accessory details: knob lead screw, the fastening screw of the movable jaw, the washer and the pins — also it is easy to choose from ready-made hardware, and make their special problems will not make even a beginning homebrew.
In the manufacture of makes sense to adjust the movable jaw to the fixed and sanded them together on three sides: the top and sides. In addition, you should ensure that the tongue of the movable jaw went in the groove of the base easily but without any play.
The hole for the lead screw (threaded sleeve) in resistant Desk base & socket (blind hole) in a moving sponge, too, are drilled together. The end of the lead screw in the slot of the movable jaw also should walk freely but without excessive play.
After making parts all their sharp edges (edges) is needed to blunt, and the movable and fixed jaw, spindle and threaded bushing — tempering to a hardness of 30 HRC. When assembling the friction surfaces are preferably lubricated with a thin layer of grease.
Y. KURBAKOV, Tula