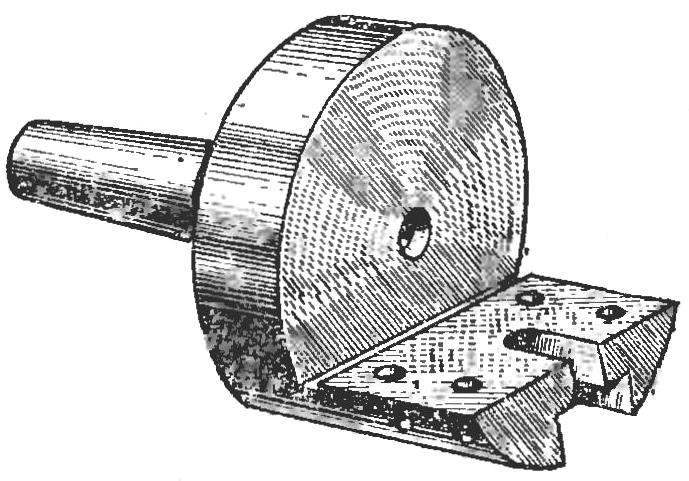
The device consists of faceplate-gon with Morse taper (for mounting in the spindle of a screw-cutting lathe), prolonged screw and mandrel for fixing the workpiece. The plane landing is lowered below the center line 22-25 mm, which is enough for boring holes in crankcases and gearboxes.
Perpendicularity and concentricity of the holes depend on the accuracy of the performance and cleanliness of the Seating surfaces of the fixture. It is made of steel 45, cast to hardness 48-50 LDCs, then produce grinding all Seating surfaces.
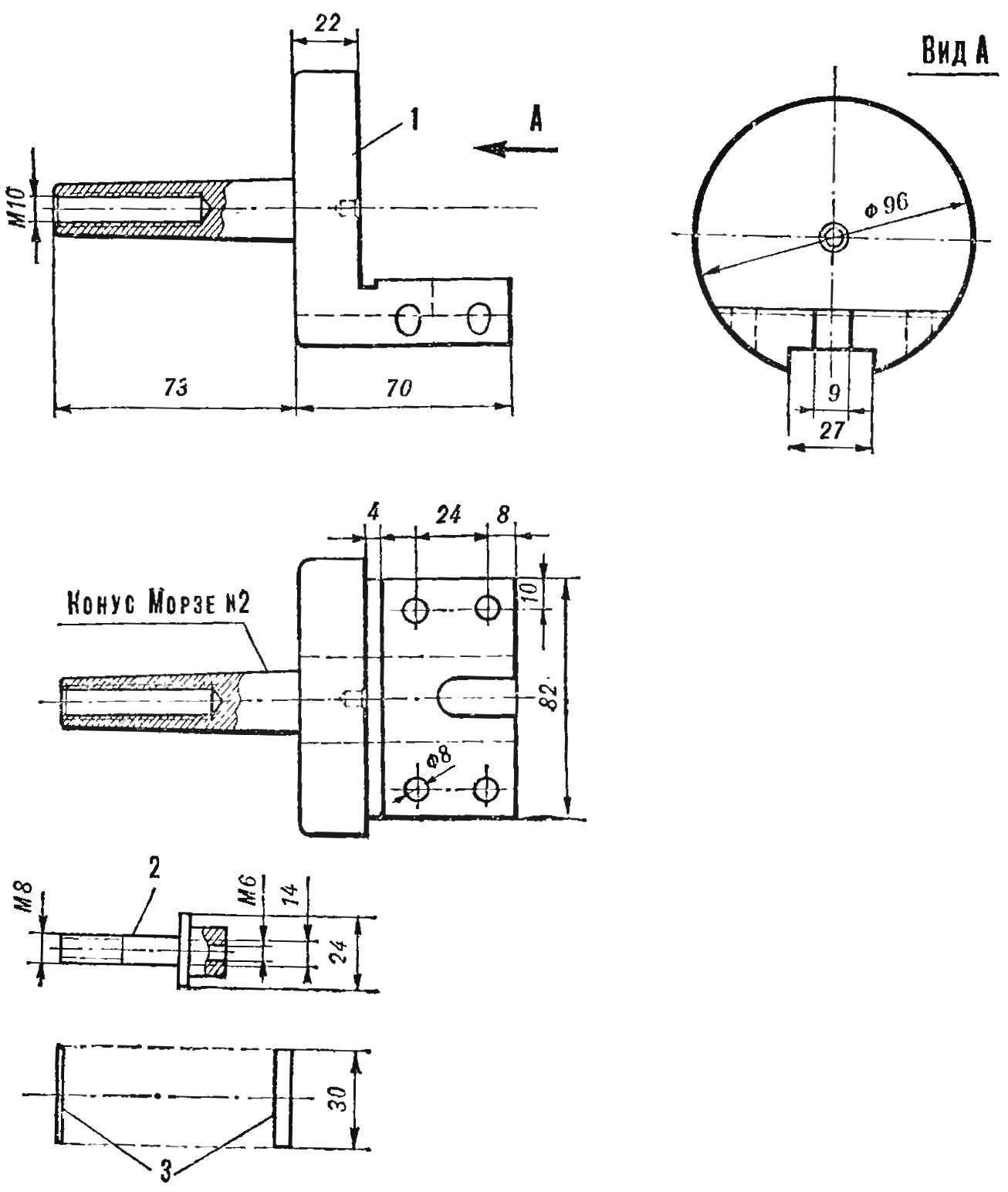
Fixture for boring the crankcases of engines:
1 — faceplate-gon, 2 — bar, 3 — the adjusting washer.
The technology of bore holes the next. First, on the universal screw-cutting lathe (without adaptation) process one of the holes parts and the adjacent plane (in the future it will serve as the baseline). Then Carter or the gear housing are installed using a pre-prepared Opanki ka plane of the device (see drawing). Installation washers put the center height rascacielos holes and fix the item. Further working surfaces shall be processed in the device.
Universal square-faceplate allows you to rastakat holes of any configuration with high accuracy.
V. OGIBENIN