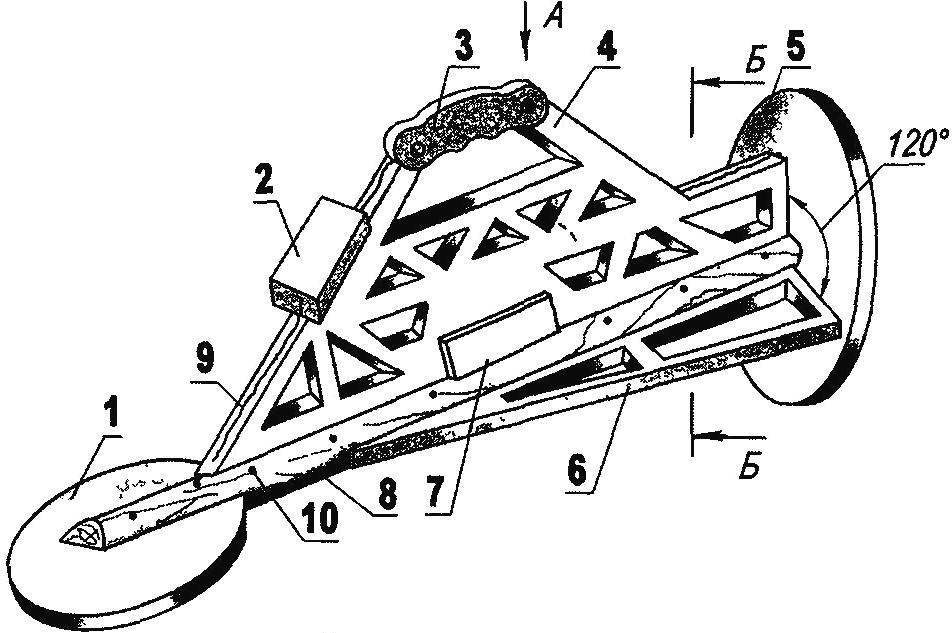
To deep metal detectors are the devices that can “tighten” in the earth on depth more than 40 cm in order to detect large metal objects. In this publication, as well as in the previous one, is not considered an electronic security device. To all whom it may concern, I recommend the book Osipova and Shadrin “metal Detectors”.
Structurally, the deep metal detectors can be divided into two types. In the first sensor magnetic anomaly and meter combined in one housing and the second inductors are separated. Below to the attention of interested readers is invited to the construction of the device of the second type (with separate sensor and transmitter) that allows you to search large metal objects and ignore the petty, lying on the surface.
The experiment was made ruler of such structures with the “base” between the sensor and the emitter to two meters. As an example, the design of a nominal base 1200 mm Other sizes are fundamentally no different from the ones shown. As can be seen from the drawings, the device of the metal detector is very simple and easy to manufacture even novice DIY.
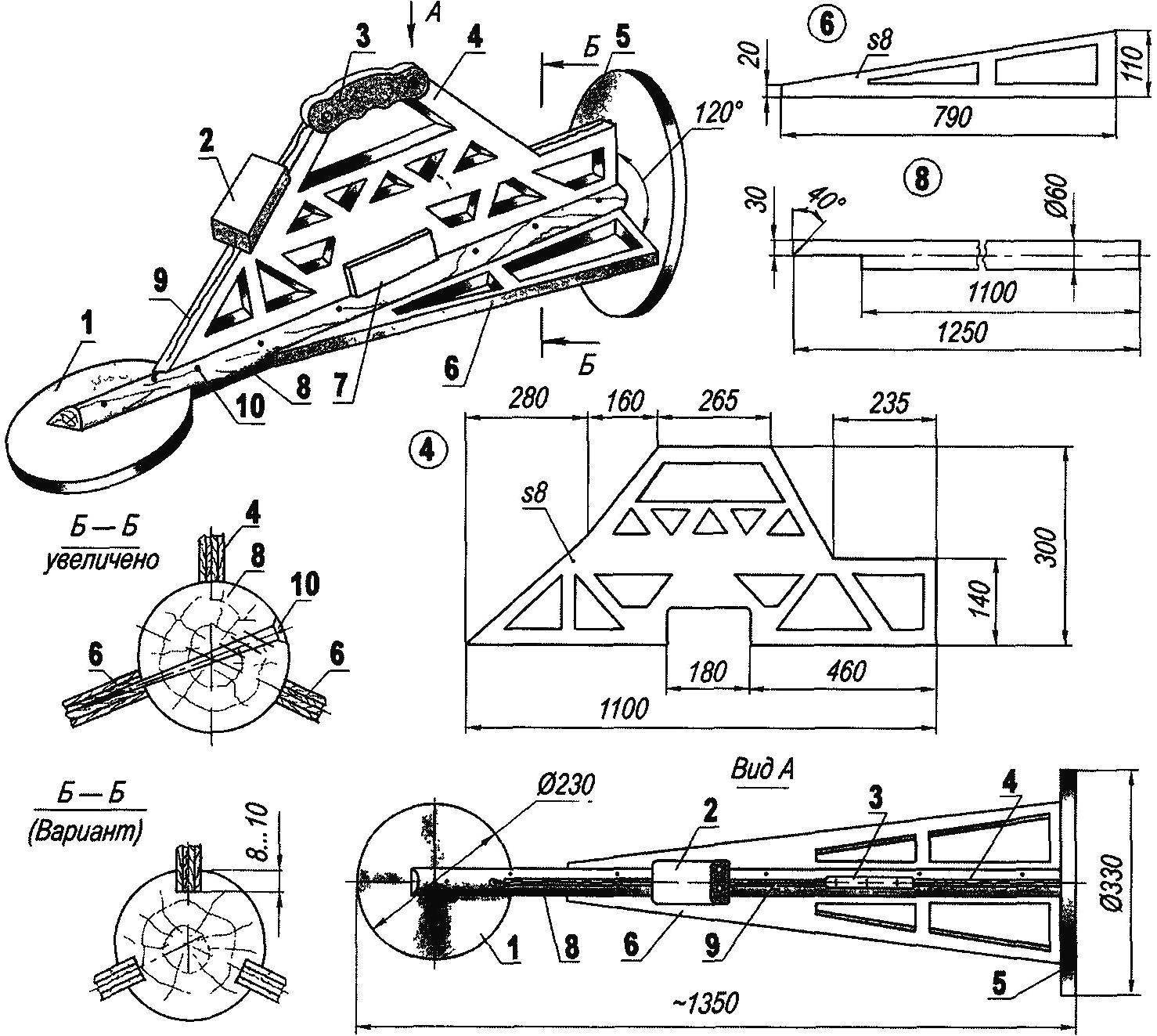
Deep dvuhmatchevyh metal detector:
1 — sensor, 2 — electronic unit; 3 — lever; 4 — the main edge (plywood, s8), 5 —radiator; 6 — the stiffener (plywood, s8,2); 7 — power supply; 8 — beam (Linden, circle 60), 9 —operating the actuator of the sensor and emitter; 10 — fastening of the ribs (4×90 screws, as required)
The materials used are abundant and cheap For the frames of the emitter and sensor, the ribs and the main ribs will need plywood 8 mm thickness, the beam can be made of wooden logs (preferably lime), to isolate the sensors will go thin (3 — 5mm) foam, normal fabric and nitro. For fastening elements of the design will need screws and waterproof glue (or epoxy). Fabrication is performed using a minimum set of hand tools that will certainly be in the Arsenal of any home workshop.
For the beginning of the harvests according to the drawings all the necessary details In the fins to facilitate cut notched holes of arbitrary shape — most importantly, to maintain the necessary strength and rigidity of the whole structure. In the main ridge on the bottom center additionally cut a rectangular slot under the power supply In the frames of the emitter and sensor in a circle to select a gutter with a semicircular shape. This can be done at the winepress or in the absence of that, manually with a file of the appropriate section.
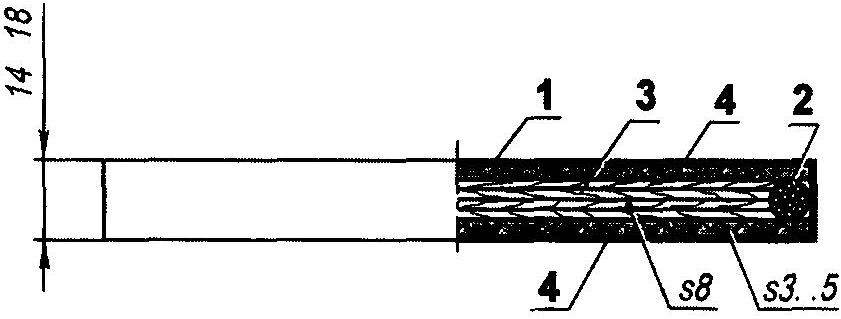
Sensor:
1 — external insulation (fabric coated with nitro enamel), 2 — the working wire of the sensor and emitter; 3 — frame (plywood, s8); 4 — top and bottom drives internal insulation (foam, s3 — 5)
The assembling of the structure start with the installation and fixation of ribs; the top of the ridge I-beam mounted main edge, and at an angle of 120° — ribs. This can be done in two ways. First — simpler: on the beam, in the place of installation of the ribs, carefully plane or a rasp, remove the flats with a width of 8 mm to 10 mm and glue them to the docking ribs, followed by additional mounting screws. The second option is a bit more complicated, but provides a more durable and rigid connection of the parts in the beam in the same places and at the same angles saws shallow (8 — 10 mm) grooves with a width of 8 mm and have them glue the ribs installed. To make the grooves can be milled (if possible), on a circular saw or manually with a chisel (the last option is more time consuming and requires a certain skill). As you can see, each option has its advantages and disadvantages — you choose.
Hereinafter, the sensor and emitter On a plywood frame around the circle in the gutter to the varnish of the winding wire work (what and how much — a separate conversation, and in this work not considered), top and bottom for insulation stacked foam circles the entire structure wrapped with cloth and cover with nitroenamel. The sensor is fastened with screws to the console of the beam, and the other to the rear end.
Next install the control unit, power supply and carry out final adjustment.
All the device is ready for operation. A successful search!