
Similar diked facilities — ol (underground, buried, aerial — how will allow ground conditions) are often satisfied with the beekeepers for wintering bees in the far apiaries and in our days.
Now the word “basement” is called the deep underground under the house, and the superstructure of the specified type is called an artificial grotto. Use the caves in the summer heat as restrooms, and in winter as a store of household equipment.
Meanwhile, modern construction materials and construction make such structures a significant area and volume, while increasing functionality. For example, it is possible to build a workshop, garage or both under one roof.
The benefits of diked structures over traditional are obvious. In this building at all times of the year remain relatively stable humid and thermal conditions. So, at the seasonal outdoor temperature changes from +35°C in summer and -35°C in winter change it inside does not exceed 15°. Means of heating the room up to comfortable conditions in cold weather, need very little energy (although working in such workshop, not cold and no heating).
Another important advantage of diked structure of its fire safety. It is comparable, perhaps, with the fireproof safe: fire is not easy to penetrate inside the buildings, as, indeed, to escape from it out.
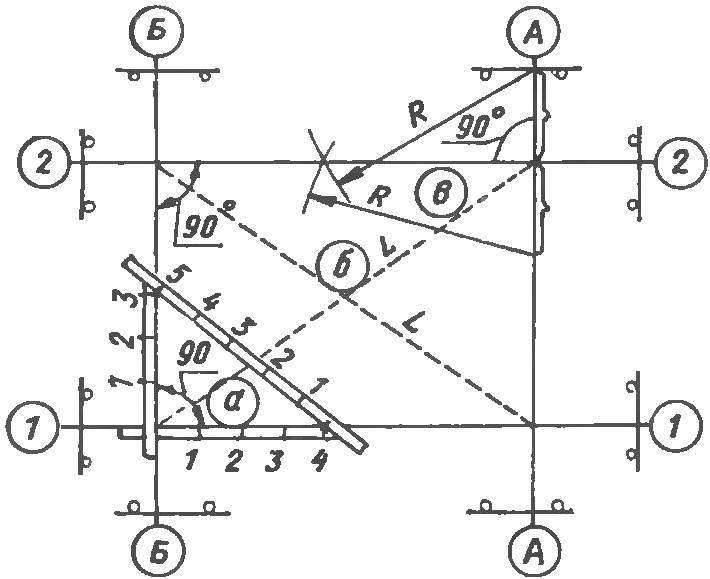
Diagram of the device of the rags of the pit. Three ways to split angles on the ground:
and — with the help of the triangle of Pythagoras; b — equal diagonals, by way of radial notches
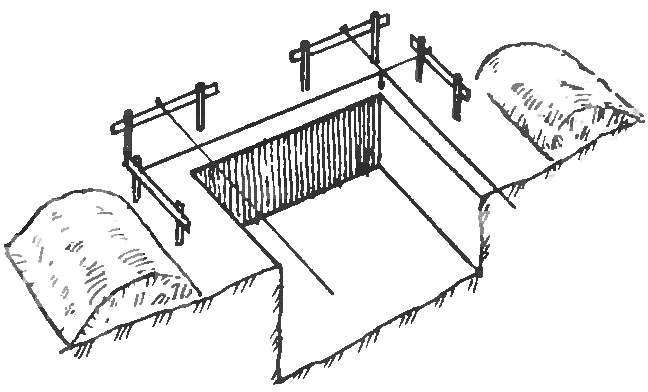
View of part of the pit with obnosku
Diked design of buildings in most cases be more economical than (and significantly so) than open-ground, as in the construction of the grottoes are not required quality (appearance) of the construction product. The materials used are mostly local: turf, clay, sand, crushed stone, crushed stone, gravel, including what is extracted from the pit during its development.
The main saving is that the Foundation and walls employed in the conventional constructions of the support elements, there are also the main walling.
Erection of garage-grotto like any other building, preceded by some negotiation with the local administration and obtaining her permission. For the successful completion of this procedure, you need the passport object, which must be at least drawings of the plan and facades of the future structure and main architectural and construction solutions.
As these drawings are fairly simple to prepare them yourself. But do not be superfluous and more profound preliminary study of the construction paper until the sketch design with the help of relevant literature. This will help to avoid many unforeseen situations: inconsistencies of elements, rework, cost overruns or the acquisition of surplus materials, etc. and at the same time to accurately calculate the requirements for the necessary structures, main and auxiliary materials, devices, mechanisms.
Develop a conceptual design of buildings is preceded by site selection and study of its engineering-geological and hydrogeological conditions.
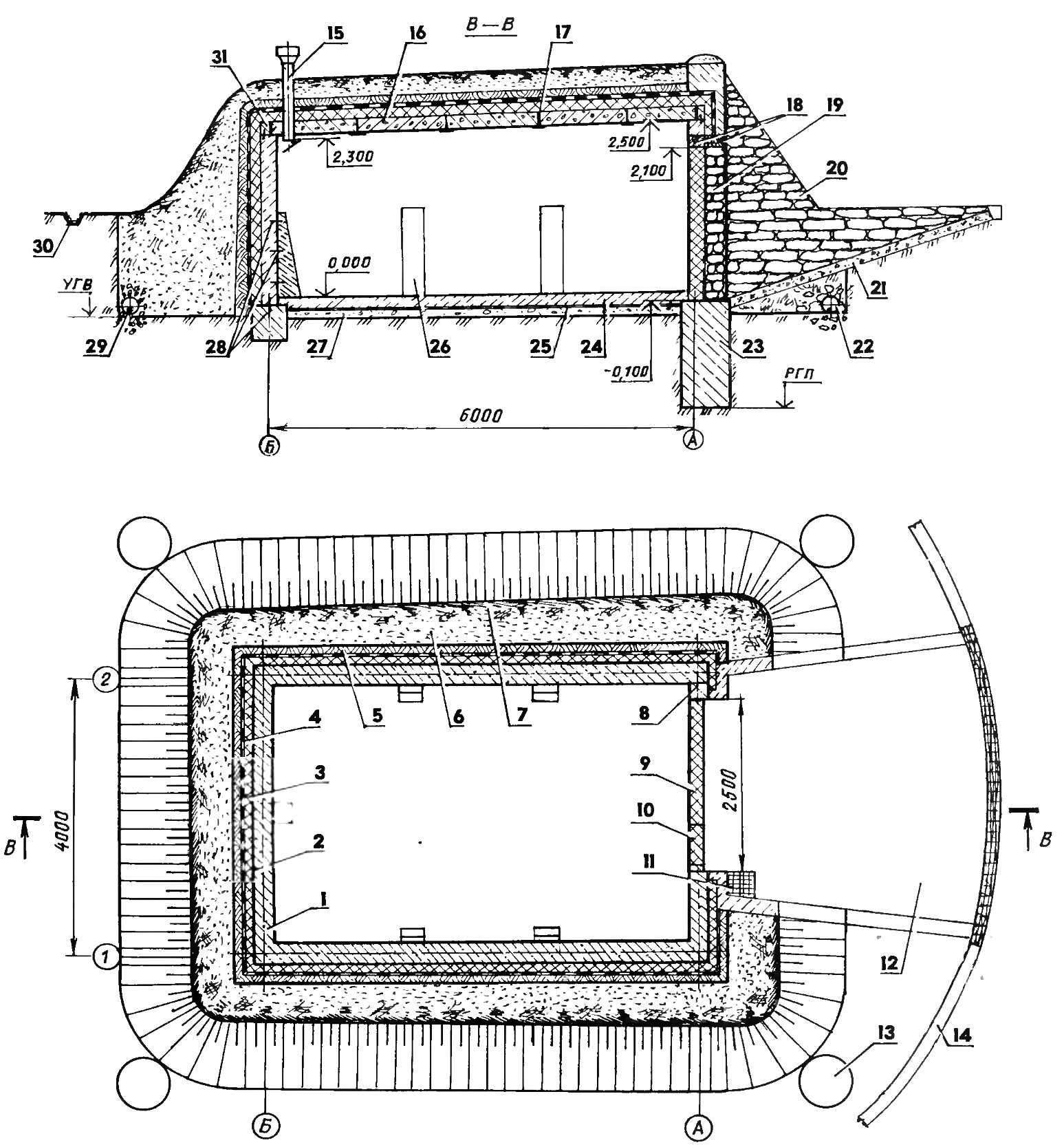
Garage workshop:
1 — wall (concrete M300, b150); 2 — bituminous coating; 3 — insulation (b50…150); 4 — – waterproofing (waterproofing); 5 — clay castle (b100… 150); 6 — made ground embankment; 7 — cut surface of the dike; 8 — the internal wall of the portal (concrete M300, b150); 9 — steel box-shaped insulated gate (2500х 2200×100); 10 — insulated door in the gate (b100); 11 – concrete drainage pit; 12 — exit ramp; 13 — observation drain well Ø800; 14 — drainage ditch; 15 — vent vent pipe (asbestos-cement Ø150); 16 — slab (reinforced concrete 1200x500x100, 40 PCs.); 17 – transverse beam (t No. 10, L4000, 4 pieces); 18 — concrete door lintels; 19 — the outer lining of the portal (of the rubble); 20 — retaining wall (masonry of rubble stone); 21 — pavement of the ramp (concrete); 22 — drainage; 23 — gantry part of the strip Foundation; 24 — floor (concrete M300, b150); 25 — waterproofing (2 sheets of roofing material on bitumen mastic); 26 — buttress (concrete M300, 5 PCs); 27 — cushion of sand-gravel mixture: 28 — steel anchor pins (Ø10, 3 items per buttress); 29 — the cleaner drainage pipes (galvanized wire Ø3 — Ø5); 30 — the drainage ditch; 31 — monolithic belt
The main factor is the groundwater level (GWL). It determines the possible depth of the garage: it is desirable that the constructive layers of the floor were above them. Also, we must remember that during the period of snowmelt or prolonged autumn rains, their levels will rise. To lower the underground water level and to protect the Church from them, around the Foundation drainage arrange.
Another important point is property of the soil, which will be the Foundation of the garage. It depends on the design of the Foundation, or rather, the area of the sole. As shown, on such soils as smooth clay fine silty sand and peat or silt, it is better not to build anything or to specifically strengthen them.
Both can be identified by digging at the place of construction of constructions, a hole or wells drilled at least two feet below the maximum depth of seasonal freezing of the pound in the construction area. This indicator can also be determined in any local design and construction organizations.
The development of the pit
It begins with the preparation of the construction site: the device is a hand-me-downs, “pinning” it to the axes of the future construction, removal and warehousing outside the site of turf and humus (fertile) layer. Further excavation of the pit produced with storage of the soil on the sides so that it does not crumble himself and had not violated the walls of the excavation, and in Cavaliere (the shaft of the extracted species) remained gaps for haulage of construction materials. If the development of the pit is mechanized, it is important not to bury below the design level, otherwise the primer will not only fill up but also to condense. Better not digging a few centimeters, and the remaining soil choose manually just before the Foundation is built. If the pit is on a slope, with the upper hand it is necessary to dig a drainage ditch.
The Foundation and drainage
The most appropriate type of Foundation — tape (concrete or rubble concrete) buried. It does not require special calculation and will more than provide reliable support even a one-story building with concrete walls. However, the width of the sole must be 200 mm (100 mm on both sides) more than the thickness of the walls, even in the case where it is required by load or bearing capacity of the soil.
In case, if the structure is buried so that its floor is below the maximum of soil freezing, it is advisable the device a solid Foundation in the form of reinforced concrete slabs: it will serve as the floor of the garage-workshop. The calculation of the square foot basement is also not required. It is only necessary that the plate protrude from the wall by 100mm. the Reinforcement in its middle part it is possible to make the weakened — just as a binder.
If the pounds of the base of a structure and wet clay under the Foundation (strip or plate) it is advisable to make a sand or sand-gravel cushion. When near the pound and water, it makes sense to lay on a pillow under slab waterproofing layer of two sheets of roofing material on bitumen mastic or one coat gidrozo La. These same structural layers of the device a separate concrete floor.
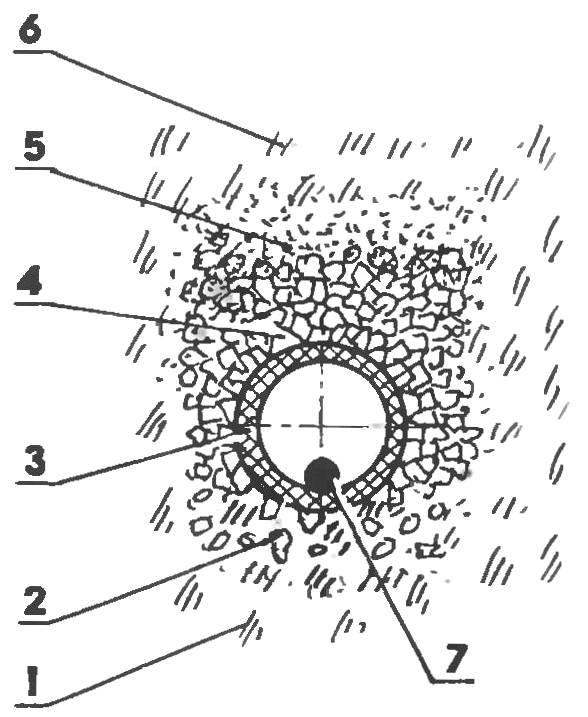
Drainage device:
1 — ground; 2 — crushed stone, recessed into the ground; 3 — drain; 4 — gravel fraction 10…20 mm; 5 — coarse-grained sand; 6 — soil backfill; 7 — galvanized wire Ø3 — 5 for pipe cleaning
Portal construction and Foundation under it, even in the construction of diked remain available frost. Therefore, the sole Foundation in this place should be lowered to the calculated depth of freezing (RSE) of soil, measured from the floor of the garage. The walls of the portal also advisable to make a thickened or layered with insulation on the inside.
During construction of Foundation (strip or plate) until the concrete has hardened, it is necessary to stick it in the corners and along the axes at intervals of 1 — 1.5 m vertical steel pins for connection of the Foundation with walls. Well, if the pins are at full height walls.
Drainage is arranged at the bottom of the pit around the perimeter of the structure outside the Foundation with a small (less than 0.3 percent), but a constant slope toward the spillway (ravine, ditch, river) or water tank (specially made sump) pump. There are diverted rain and melt water is trapped on the exit ramp.
Drainage pipe (ceramic, asbestos cement, plastic) is laid on the prepared base of the 50-mm layer of crushed stone, recessed into the ground. On top of the first pipe backfilled with gravel or crushed stone, then sand. In the pipe, for cleaning during operation, is introduced galvanized wire. Its ends are fixed in observation wells, arranged in sharp bends of pipes of drainage.
The construction of the walls
Materials for walls are the most common: concrete (precast and monolithic), solid ceramic brick, rubble stone. Technology of construction of these enclosing structures is also traditional — the same as any other basement. When the clutch makes sense in 5 — 6 rows to lay the grid or longitudinal (horizontal) reinforcing bars, attaching them to the vertical pins embedded in the Foundation.
The minimum thickness of walls for single-storey buildings is not so much the strength of their material, but the technological possibilities it’s Hard to make concrete from brick or rubble stone sheer smooth 2-m wall thinner 120 mm.
However, the most appropriate wall material in this case will concrete with a density of 700 — 1000 kg/cm3. At an appropriate thickness it will replace two of the structural layer: main (concrete) and thermal insulation.
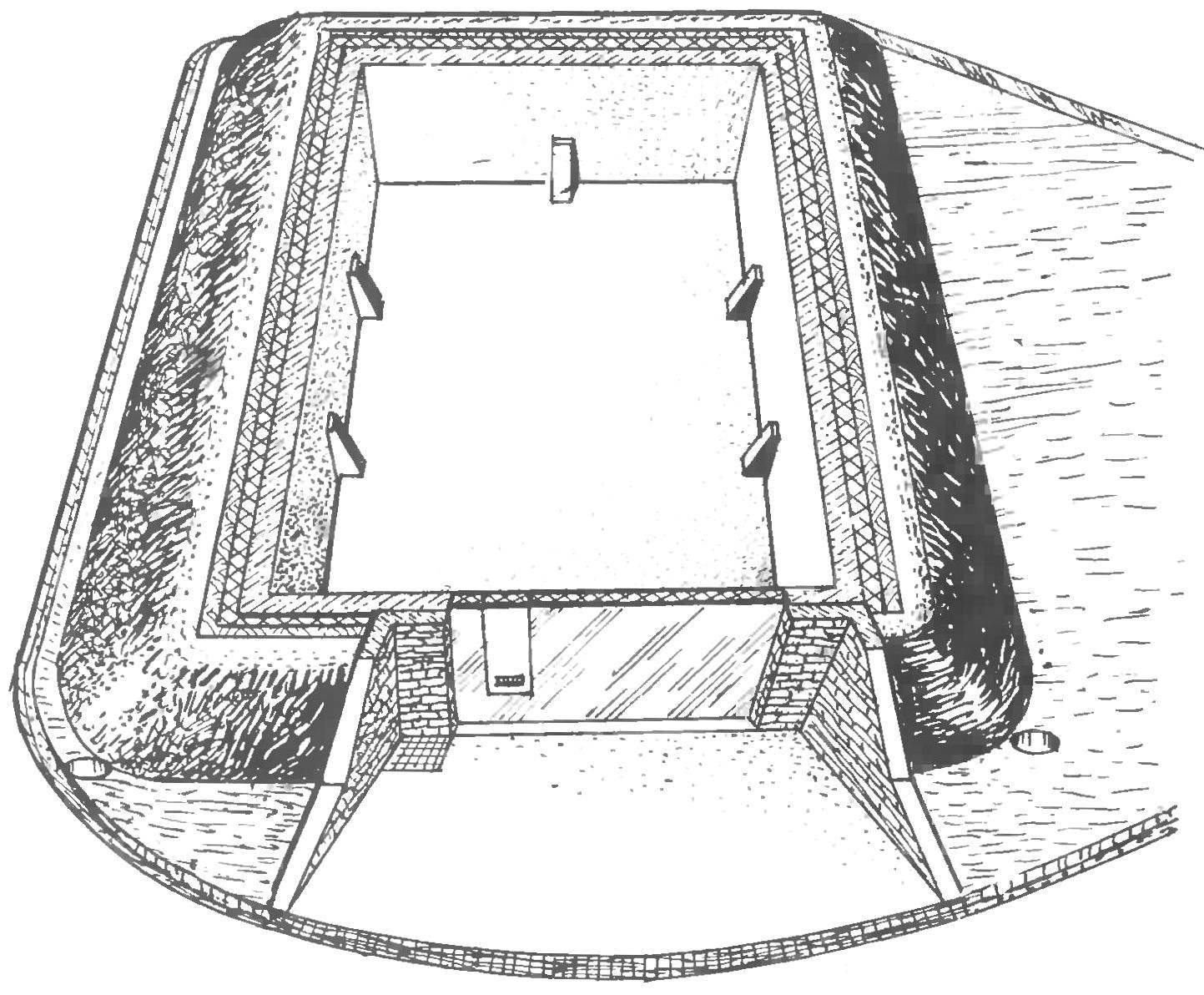
Comprehensive plan structures
And even If the structure is constructed without calculation of the wall shear (like a wall), relying on intuition and practice, makes sense from the inside, simultaneously with the construction of the walls, put (simonaityte) around the perimeter at intervals of 2 m buttresses with a height equal to the depth of the walls. In the operation of the premises, when the walls are workbenches and cabinets, they will not interfere, but will provide even greater reliability of the facilities If the room is already narrow, it is possible to make the outer anchors securing them in the soil backfill
Subsequently, the wall can be plastered and, if necessary, (to quickly warm the room) to further insulate from the inside.
Plates a portal on the wall should be placed a little higher than the rear, to provide a bias to the upper layers for a natural flow with them precipitation.
Coating
Work on the device cover can only be made after a concrete wall attains the necessary strength — in about a week after their erection.
For coatings it is better to use plates factory manufacture both smooth and ribbed. Of course, for their installation will require a crane. It is advisable to buy or order the plate which overlaps the walls would not completely, but only to axes. Then, after the device a circular monolithic belts associated with the walls of the reinforcement pins, the overlap will fulfill the function of spacers that lined the structure is not superfluous. If possible, the zone of better simonaityte simultaneously with the construction of the walls.
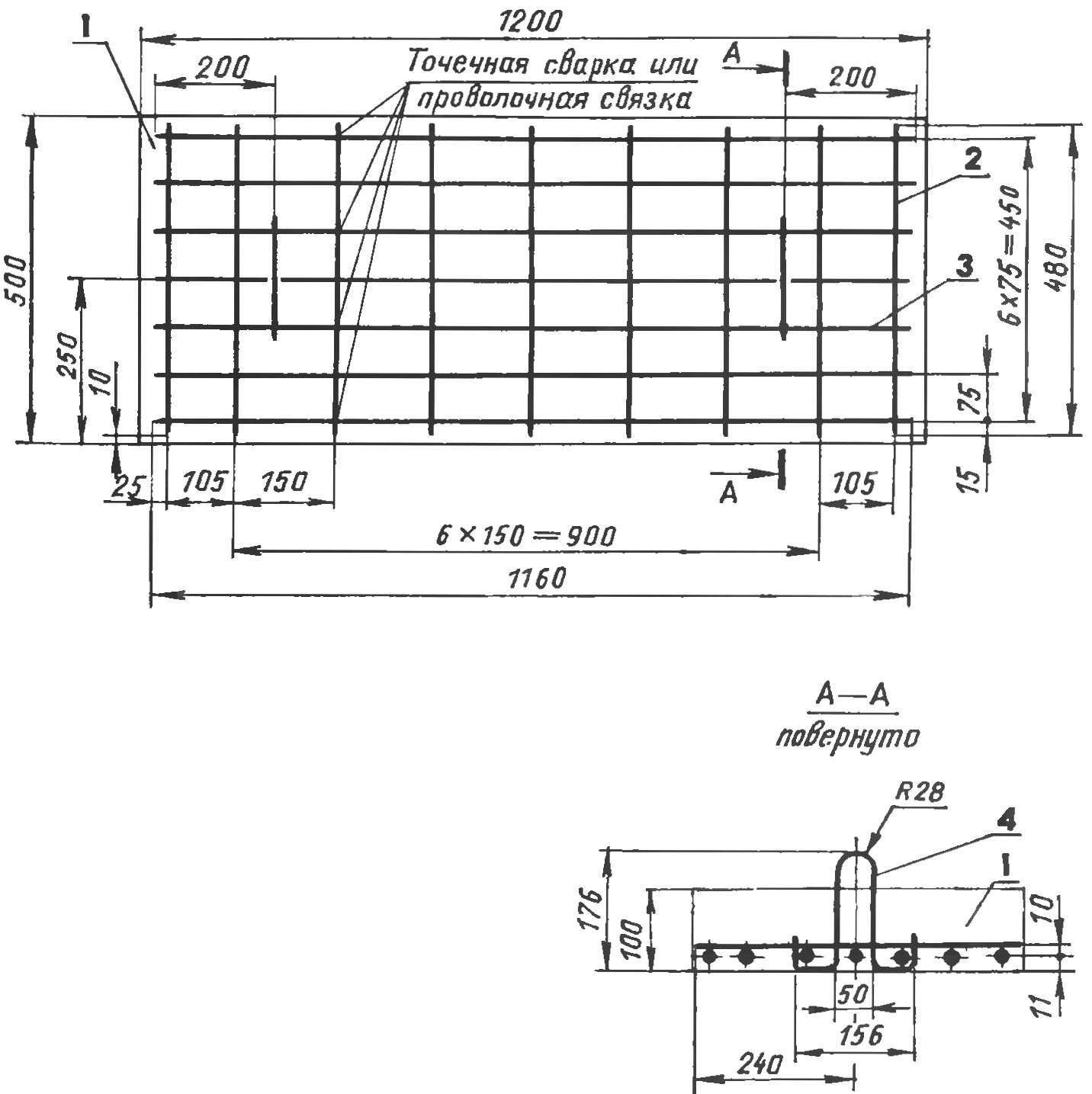
Reinforcement plate cover:
1 — cooktop cover — imposed projection (concrete M400); 2 — cross-stud reinforcement mesh (rod Ø10, 9 pieces); 3 — longitudinal rod (rod Ø10,7 items); 4 — mounting loop (wire Ø6, 2 PCs.)
If circumstances do not allow you to purchase the finished plate coatings, they can be tformat independently on the construction site, strictly observing the technology of making and giving time for the concrete to gain the necessary strength (in the warm season — about a month). In this case it makes sense to utformat plate of such size that they could subsequently install the manually, making the installation of the transverse beams (see longitudinal section). If the production of slabs made without calculations, it is necessary to secure and produce them increased reinforcement. Reinforcing bars must be placed at the bottom layer of the slab, but the rods did not reach the external surface 10 to 15 mm. rods need to associate the reinforcing wire (or weld between themselves and the length, if they are composite). In an extreme case, as the rods can be used steel pipe, profile steel. At the back wall in covering it is necessary to leave (or punch) vent.
The outer surface of the plates cleaned of dust and thoroughly coat first cold liquid asphalt cement, and then hot bitumen. The mastic is prepared by combining the pieces of bitumen in kerosene, toluene or gasoline (diesel fuel for these purposes to use undesirable a long time to dry). The bitumen is melted and evaporated in a barrel, observing safety precautions, because the difference between the temperatures of evaporation and the ignition of bitumen is small: the first — 160 — 180°C, and the second is a little more than 220°C.
Device for heat-and waterproofing
The roof and walls it is desirable to insulate, otherwise you’ll have to pour the shaft of the earth thickness equal to the depth of soil freezing in the construction area. The heater does not have to be expensive. Quite suitable local: reed, straw, and somewhere a slag, pumice. For ceiling, you can apply one insulating material (loose), for wall — other (sustainable). Organic insulation, it is desirable to pre-process at least a liquid solution of clay and dry it (then it won’t rot and rot) or to make it unpressed Adobe blocks.
Insulation thickness is determined by a fairly complex calculation based on the thickness of the shaft and walls (and their material); if the insulation from local materials, based on the practice of construction in the area.
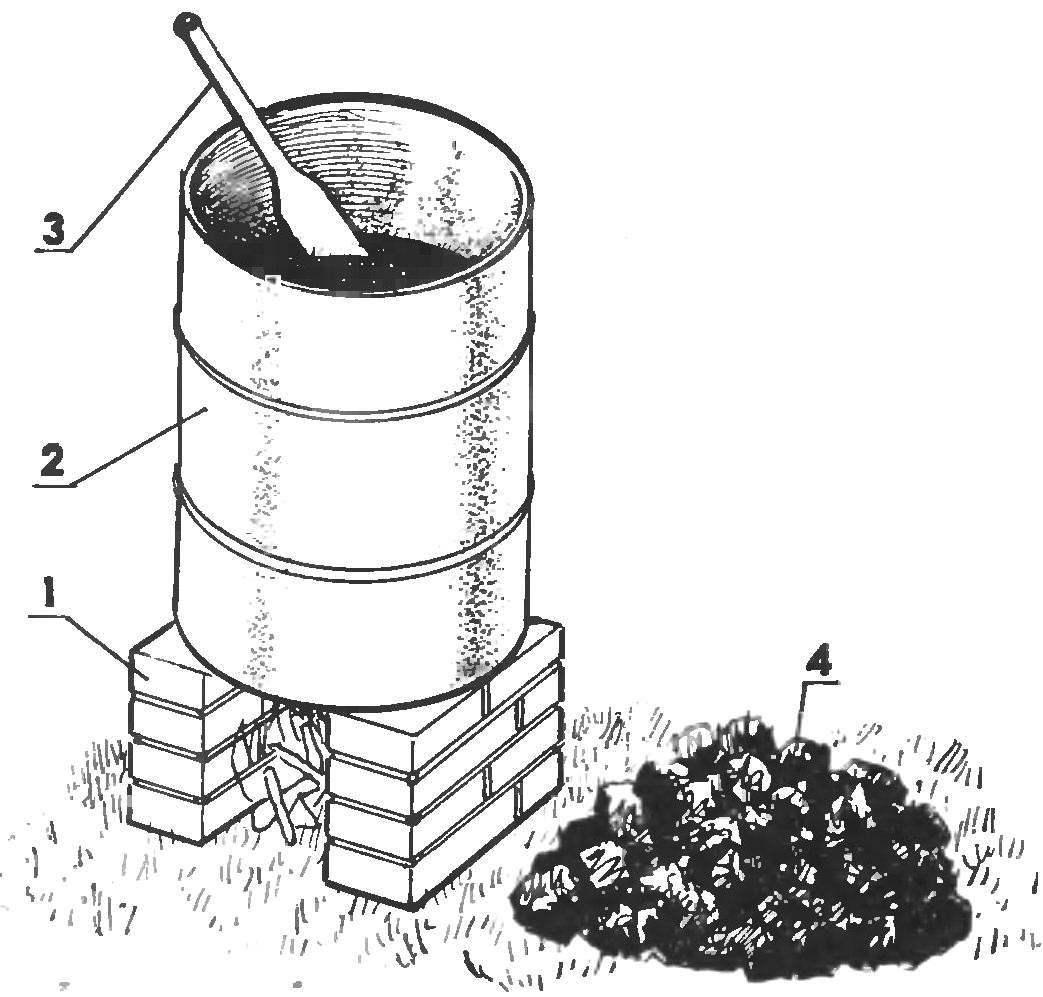
Device for heating bitumen:
1 — brick-lined hearth; 2 — capacity (200 l barrel); 3 — stirrer; 4 — bulk bitumen
A layer of insulation on the outside should be thoroughly sealed with waterproofing — it will not allow access to the heater nor groundwater, nor chemicals, protect the walls from freezing, and the room is cold.
The traditional material for waterproofing — roofing material on bitumen mastic or hot bitumen. However, the most effective material — waterproofing. When laying, it is less time-consuming, but also requires compliance with fire safety regulations, as attached to the ground by podplavlenie its surface torch gas torch or the flame of a blowtorch.
Clay castle in this case acts as an extra layer of waterproofing. Although our ancestors when constructing basements with its log walls of timbers (logs, split in half lengthwise) and slabs of podtovarnikom (or the same boards) only one layer and cost. But in times of heavy rains or permanent seepage of soil moisture to clay, although water retention, but she gets wet and moisture insulation, reducing or even nullifying its effectiveness.
Backfilling, bonding and Ternovaya
The filling of the recessed portion to the surface of the earth is layers of 200 — 250 mm, with thorough compacting each layer to density of surrounding soil, and possibly higher.
The above-ground part — a bench — organize without seal (in order not to increase the slope of repose of the soil), but also in layers around the entire structure. The shaft is kept for a week or two for the precipitation of soil, watering. The slope of the slopes, if necessary, recovering only cutting the top part but not bottom posypkoy: it will wash away the first good rain. Next, make the end of the shaft, filling the roof with the same soil and leveling the entire surface of the embankment with a slope of 3 to 4% on the roof from the middle to the sides, or the same General slope from the portal to the back wall.
Surface drainage
The latter operation is best performed in autumn or spring: up from the bottom poured a layer of fertile and produce the cover with turf or seeding grasses.
Drainage is provided with slopes, stored at embankment constructions, and the device of a drainage ditch around the building or the side. To use for these purposes, the drainage elements is not desirable. The bottom and sides of the ditch you can lay a stone or strengthen a rubble concrete.
Ventilation
It usually — the natural: the flow of fresh air is provided through an opening arranged in the bottom of the gate or gates. Window embedded bars, and in winter time it is closed by a piece of rigid insulation.
Hood through the hole in the ceiling and pipe to improve traction, it is desirable to raise higher or make its top a deflector or cap (see “modelist-Konstruktor” No. 8, 2002).
For traction control in the lower hole of the pipe it is possible to make a simple automatic shutter.
Entrance gate
For the sunken garage is best suited gate rising up. They have different designs of lifting devices (a few publications about them in our magazine). Such gates are not only modern, but in this case, and most appropriate. For swing gates will be required adjacent the horizontal platform so that you can open the door. In the winter, even after a light snowfall or a Blizzard, without prior clearing the yard from snow to open such gates will not be easy. The ramp also had to make a steeper or even to extend the entrance, which is also undesirable. And sliding gate to do here is not possible.
In lifting gates, usually there is no door here it is very desirable: first, to retain heat (or cool) at the entrance to the garage. Secondly, to be able to enter the garage when the approaches to it are covered with snow. Third, for added ventilation, and the fourth is for convenience, if you frequently need to log-out. At the bottom of the doors can make a barred vent, which in frosty weather it is necessary to close size piece of insulation.
As the gates rise up, it is desirable that the door opened outward. Gate (and the door with them) it is better to buy (or make) a metal, box-like structure, and cavity fill insulation: expanded polystyrene, mineral wool or foam. Another condition. The arches between the door and the gate, between the gate and jambs should be sealed, as in glazing. To seal the joints is not difficult, but to do this work efficiently we need to in the garage, even in extreme cold without heating remained above zero temperature.
* * *
The outer part of the portal gates and retaining walls would be good to impose a quarry stone — “avtogrot” would look almost natural cave.
A. POLIBIN