Construction of ships without the pile
The essence of this method is to assemble the hull of the set of blanks of such form that when connected between a receiving a predetermined shape. Thus it is possible to build boats of different sizes and purposes: and a small rowing Dinghy with a length of only 2 meters, and motor boats, and even cruise boats with a length of 7… 8 meters. Of course, the technology imposes known limits on the contours of the ship — they should be unfolding on the plane, that is, those that can be flat sheathing leaves. It is best suited for this purpose, flat-bottomed hull type “Dori”, Chine type “Sharpie” and dahskova (Fig. 3).
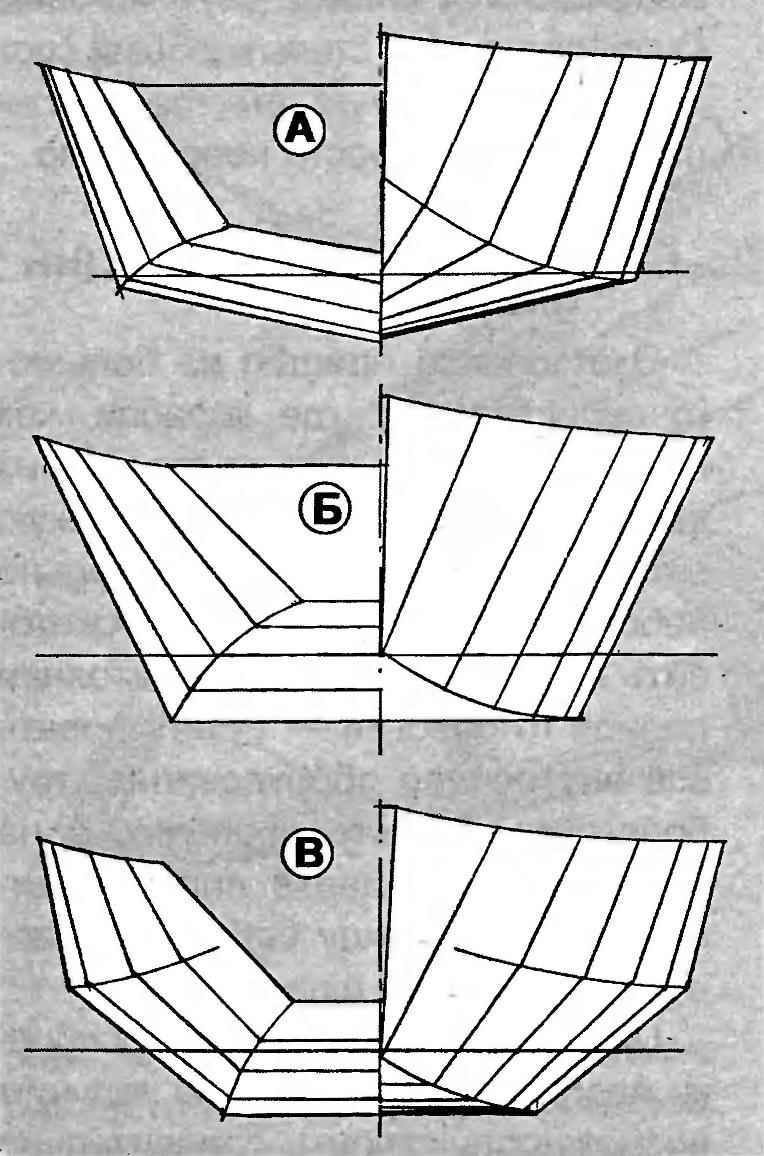
Usually the construction is conducted in the following order. First, on the theoretical drawing made samotnie frames and bulkheads. They installed the bars for mounting beds, shelves and lockers, cut the slots for the keel, Midel’veys, fenders strakes and bilge stringers. Further sheets of plywood, stacked to the required size, is applied to sweep the sides and bottom (Fig. 4).
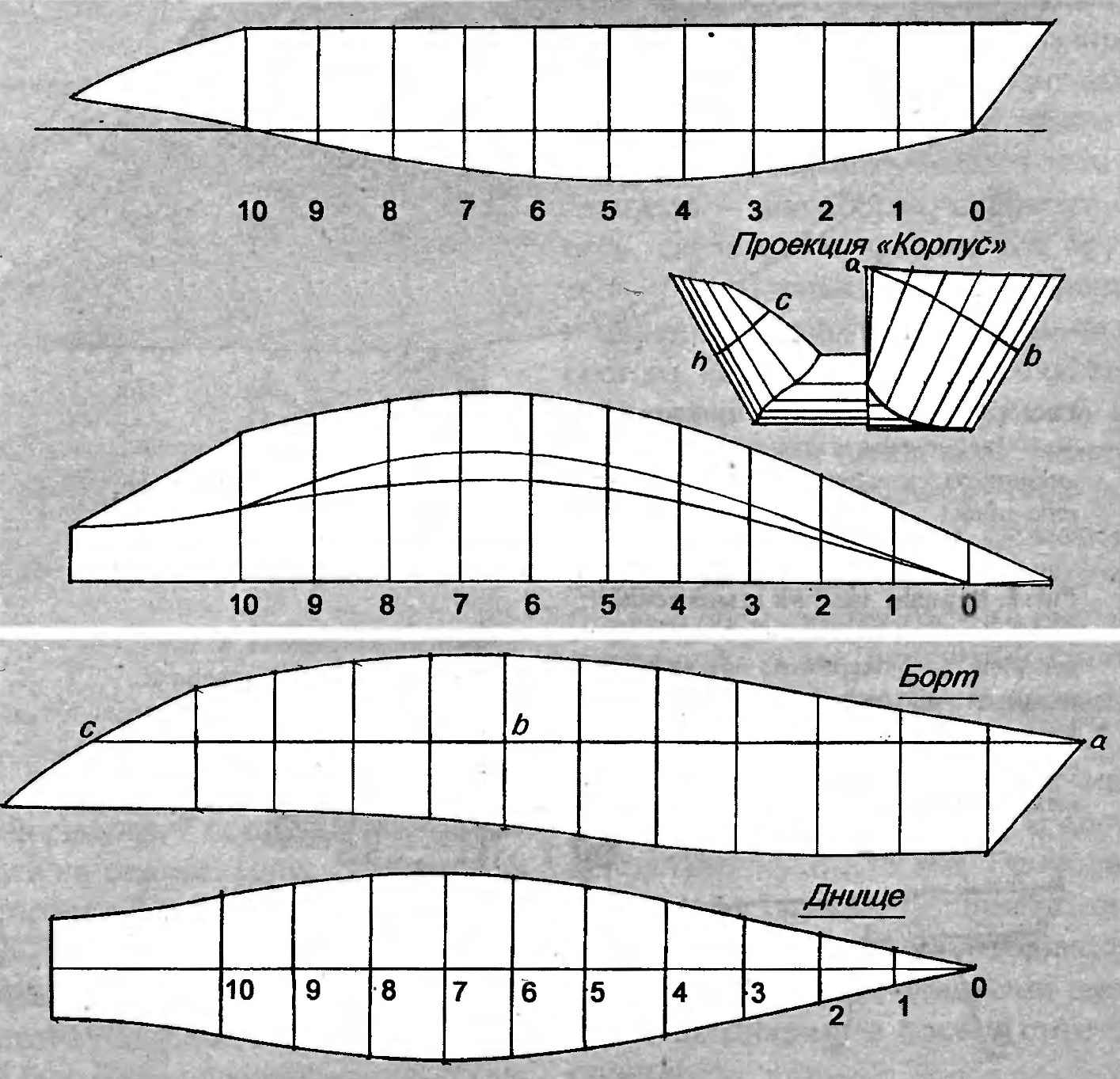
To cut the blanks marked the exact locations of the frames and bulkheads.
Salemore billet boards are installed on the flat ground and connected by a stem and a transom harness. Put a medium frame. Housing is already taking its shape (Fig. 5 A).
After this, marked on side marking set the rest of the frames, from the midsection to the extremities. In the pre-cut grooves stacked RUB rails milliways and deck stringers. After checking the correctness of the contours can be mounted inside equipment, beds, cabinets, etc.
The next step is to install and mount a set of deck sheets of the bottom of the cockpit and transom (Fig. 5 B).
Further, the case is reversed, the previously cut grooves to fit the keel and bilge stringers. The latter is put in place the bottom sheet of the covering (Fig. 5).
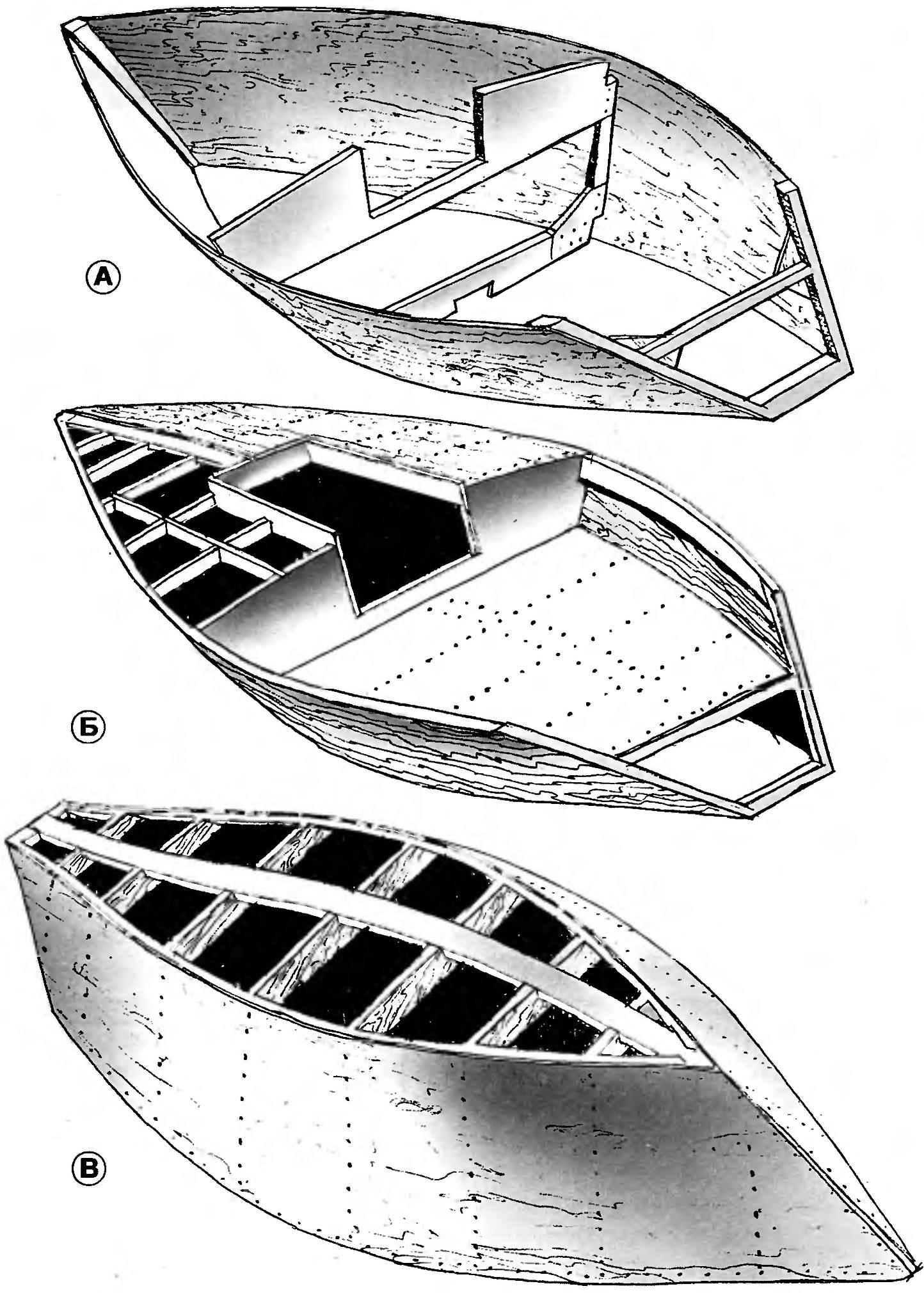
The construction of vessels, this method gives greater time savings. Suffice it to say for example that the hull cruising racing yachts with a length of 7.8 m and a width of 2.8 m was made in just four months. The work was done on Saturdays and Sundays by two people. It is obvious that in such a short time to achieve this result in the traditional way is simply impossible.
The Assembly of prefabricated sections
This method came from the big shipbuilding, where ships tend to gather on the stocks of several sections. Each such section having a relatively small size, can be fabricated in the shop and bring it to a state of full readiness to mount all the internal equipment, piping, wiring, and Assembly on the site only to connect the modules to each other and to carry out fitting-out works.
Applying this method for the Assembly of boats and yachts we will be able to build a relatively big swimming facilities in limited spaces. It often happens that the Amateur shipbuilder has a small room where you cannot place a boat the right size. It also happens that the room is spacious enough, but the gates it does not allow to extract the ship ready. In these cases, rescue only the Assembly of prefabricated sections.
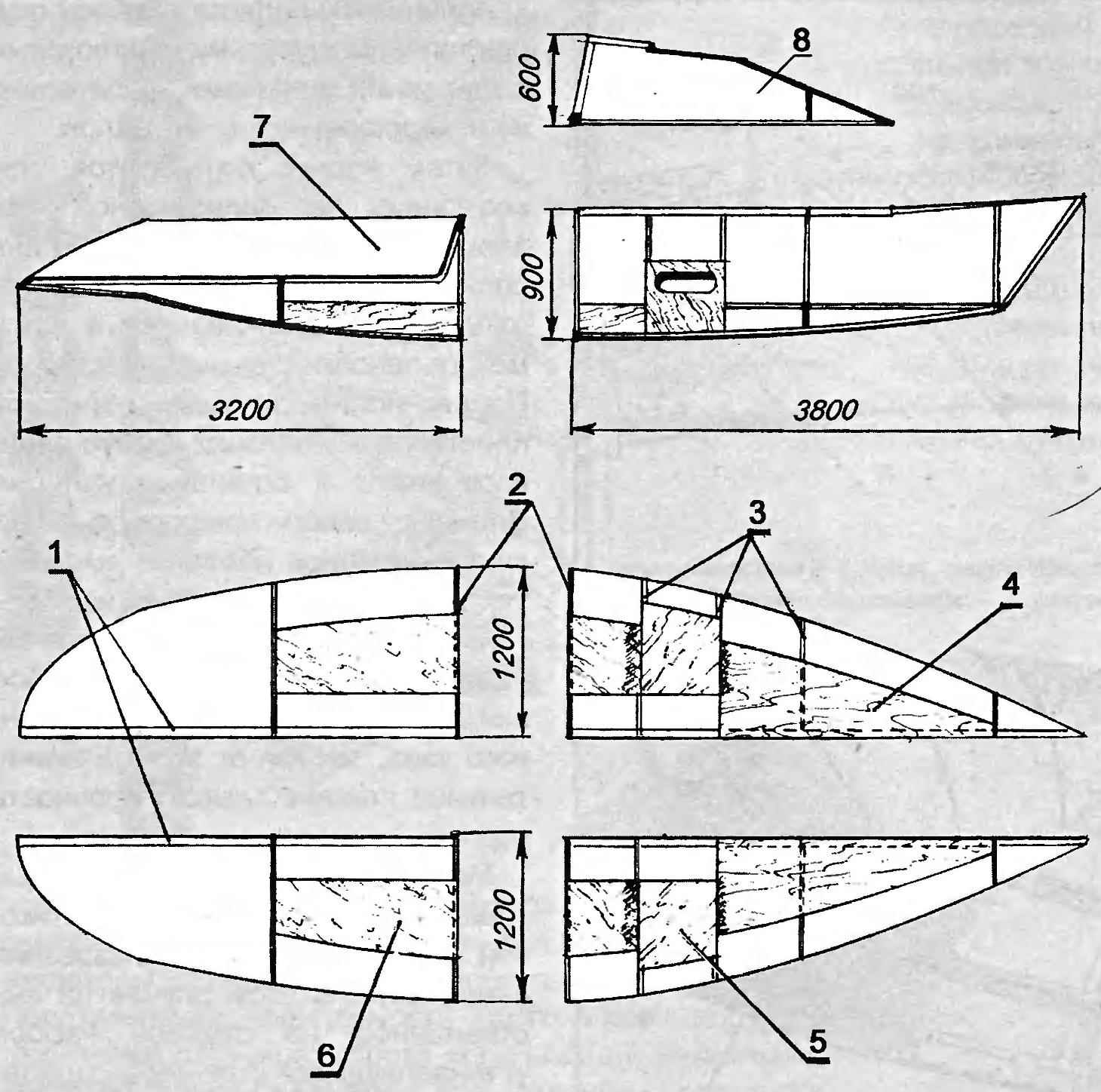
Figure 7 shows an example of division into sections of the hull of a small cruising yacht. Overall dimensions of each section does not exceed 3,8×1,2×0,9 m, and for their construction enough space 5×2,5 m. Before final Assembly, each unit needs to bring to a state of complete readiness. It needs to be mounted all the components and parts — bulkheads, deck beds and lockers, cupboards etc. it is Desirable to perform the interior finishing, and if necessary to plaster the outer surface with fiberglass. Then at the Assembly area will only connect modules, proshpaklevat and sanded the joints and paint the finished hull. One of the variants of connection of the sections shown in figure 6. It should be noted that all work must be carried out with high precision in order to avoid problems when docking.
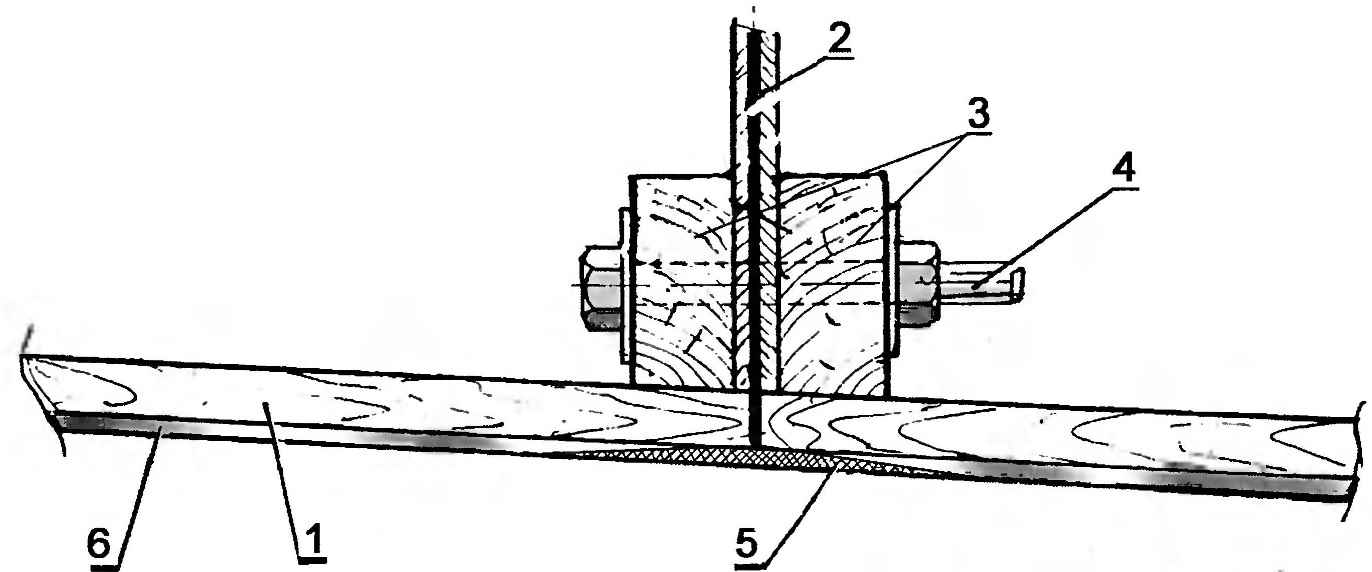
Building fiberglass vessels without snap
As already mentioned, the manufacture of tooling for forming glass – plastic housings — boob and the matrix is quite a complex and expensive operation. In recent years, increasingly start to practice ways to avoid it. One of them is the manufacture of composite buildings with a “Sandwich” plating (Fig.8).
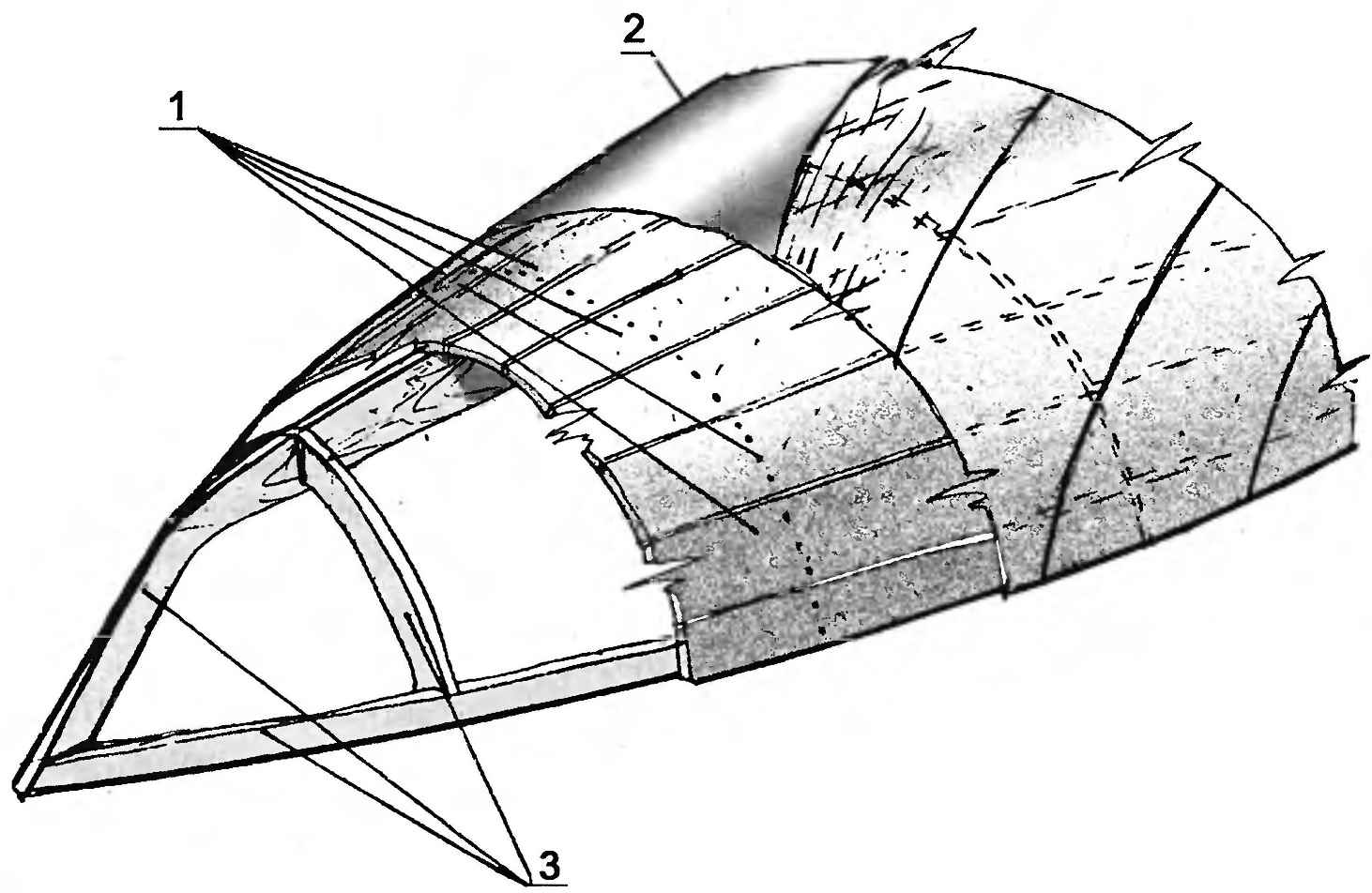
The elements of a set of such towers — bulkheads, frames, keel, and bilge RUB rails — are made of wood and plywood three-layer plating consists of two thin fiberglass shells — external and internal — and foam between them. The plating thickness is determined depending on vessel size and operating loads. Typically, the fiberglass layers have a thickness of 2…4 mm (outer layer, usually done in one and a half times thicker than the inner, to resist local loads and wear from friction), and a layer of foam — 8… 15 mm. Foams should only be applied on these marks, that do not dissolve epoxy and polyester resins comprising fiberglass.
The technology of construction is as follows. Originally on the stocks exposed wooden set of frames and bulkheads, and with the help of the keel and the RUB bars is connected in a rigid spatial structure Frame selected in the range 500…800 mm, Then the frame is sheathed with Styrofoam “boards”.
They are slitting sheets of foam with the help of simple of tormaresca containing nichrome wire heated by electric current. Between the “boards” should remain a small gap. Subsequently, they are filled with resin which will reliably connect the inner and outer plastic sheath (Fig. 9).

Mount the foam to the kit is the screws or nails with large heads, preferably of non-corrosive metals.
Then the body is glued fiberglass in polyester or epoxy resin. The first one or two layers of fabric with a wooden spatula are pushed in the gap between the foam “planks”. After polymerization, the outer plastic shell casing turned over and glued from the inside. The elements of a set privorovyvat to the inner shell of the “wet square”, consisting of several strips of fiberglass cloth impregnated with resin. You should pay special attention to the quality of this site, as it largely depends on the durability of the case.
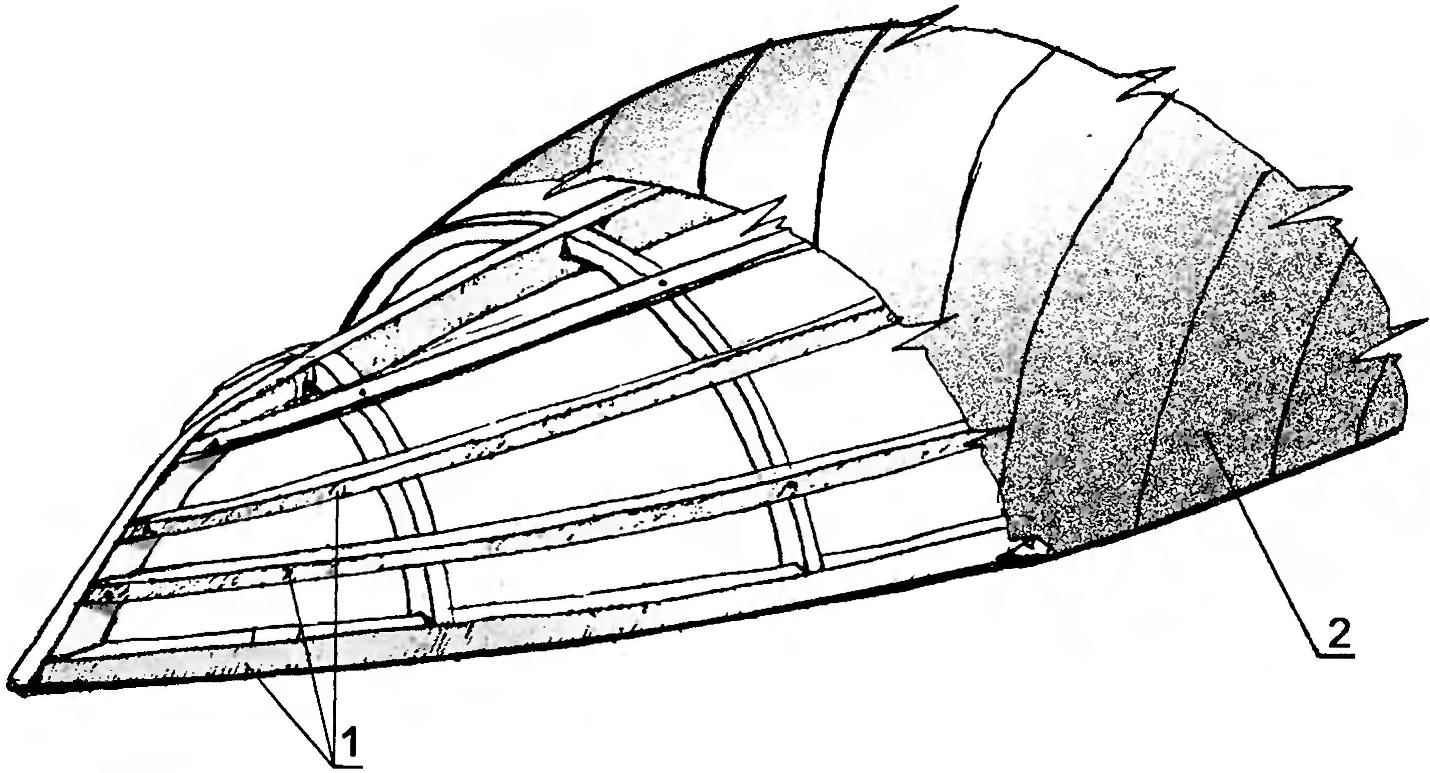
It is possible to make composite body and with a single layer of plastic covering, without the use of foam. In this case, put on the slipway kit installed the stringers with a pitch of 150…200 mm, Their cross section must be sizes from 15×15 mm to 30×30 mm, depending on the size of the housing. Then the frame is covered with a dense fiberglass, best stekloreza resin. The tension of the material should be large enough to eliminate the sagging between stringers (Fig. 11). Before molding the casing on, you need to give the first layer of “grab” that it is not subsequently deformed under the action of the weight of subsequent layers.
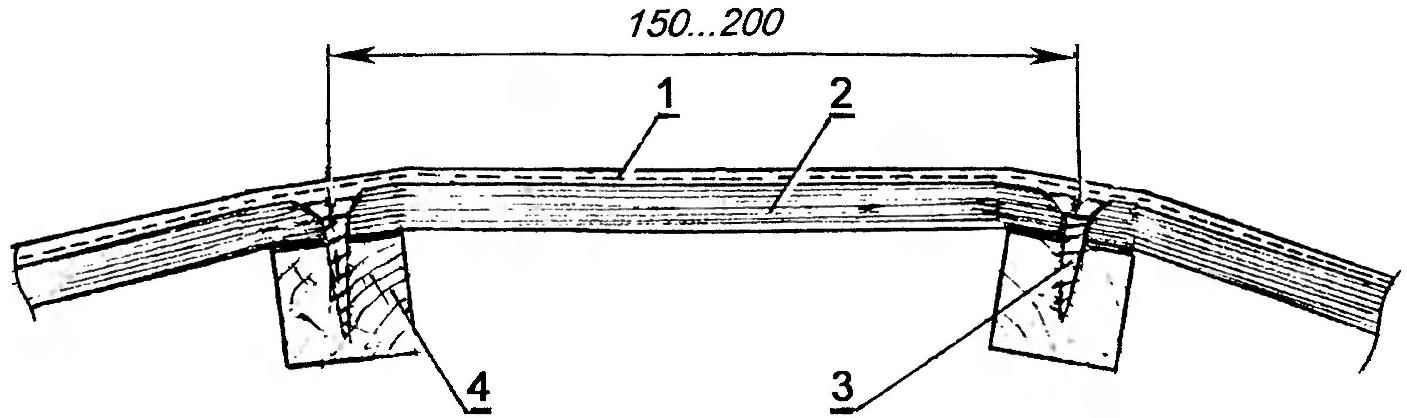
In order to increase the reliability of joining plastic trim to wood stringers need to secure it with small screws, and then hang one or two layers of thin fiberglass to cover the screw heads.
Of course, constructed in such a way that the case will be faceted contours, but it does not affect seaworthiness of the vessel nor its appearance.
V. MURNIKOV
Onoznaczenia:
Fig. 1. Set the hull of a wooden ship on the stocks:
1—frames;
2—keel beams;
3—stem;
4—berth rail;
5—fender.
Fig. 3. Diagram of the contours of the unfolding on the plane:
A—odnotonovye type “Sharpie”;
B—odnokla – tions of the type “Dori”;
In—dahskova.
Fig. 5. During Assembly of the hull from flat elements:
A—set the post, medium frame and binding of the transom;
B—has all the frames, mounted the deck and the bottom of the cockpit;
In—body is prepared for pinning bottoms.
Fig. 6. The option of sealing the junction of the sections:
1 —wooden covering of the body;
2—seam adhesive;
3—cross bars dual midship-frame;
4—pinch bolt;
5—additional coating of joint with fiberglass (3…4 layers);
6—fiberglass coating.
Fig. 7. An example of a split body sections cruising racing sailboat:
1—dual keel beams;
2—dual midship-frame;
3—a frames;
4—bow the bed;
5 is a chart table;
6—feed rack;
7—self-draining cockpit;
8—cabin.
Fig. 8. Composite body with a shell of type “sandwich“
1—foam “boards”;
2—fiberglass;
3—elements of a wooden set.
Fig. 9. Scheme of a covering of the type “sandwich”:
1—the foam “Board”;
2—fiberglass filled gap;
3 — the outer layer of fiberglass;
4—the inner layer of fiberglass;
5—wooden element of the set.
Fig. 10. Composite hull with fiberglass sheathing and wooden set:
1—wooden stringers;
2—fiberglass.
Fig. 11. The scheme is fiberglass paneling attached directly on the wooden body kit:
1—the outer layer of fiberglass;
2—the basic of fiberglass sheathing (3…4 layers);
3—brass or galvanized screws;
4—wood stringer.
Recommend to read
ANTENNA — A TIN CAN!
Viewers living in areas of new buildings high-rise buildings and besides, near the television station, I recommend to get a homemade antenna-loop. It works reliably even when the...
“BEGINNERS”: A UNIVERSAL SOLUTION
Despite various difficulties faced by modelers, RC aircraft are still interested in this most complex kind of modeling. Everyone who chose a specific type of equipment, immediately the...