Starting the story about a home-made car, I note that before that I had several factory production cars: “Zaporozhets”, and “Moskvich”, and “Zhiguli”, and “Niva” – each at one time.
But on occasion, quite inexpensively, I bought a UAZ-469 car. Frankly, I’ve been eyeing the UAZ for a long time: an all-terrain vehicle like a Niva, unpretentious like a Zaporozhets, and most importantly roomy like a minibus – this is what I, an avid lover of “quiet hunting” (a berry-mushroom picker), needed . Well, the “gluttony” in fuel consumption was compensated by the low and cheap grades of gasoline used.
True, the condition of the UAZ was such that even it could be considered satisfactory only conditionally. The steel body, and especially the floor, was hopelessly rusty and had to be replaced entirely. But there was no money for this. Therefore, having assessed my capabilities, I decided to make the body myself, using the UAZ chassis as the basis.
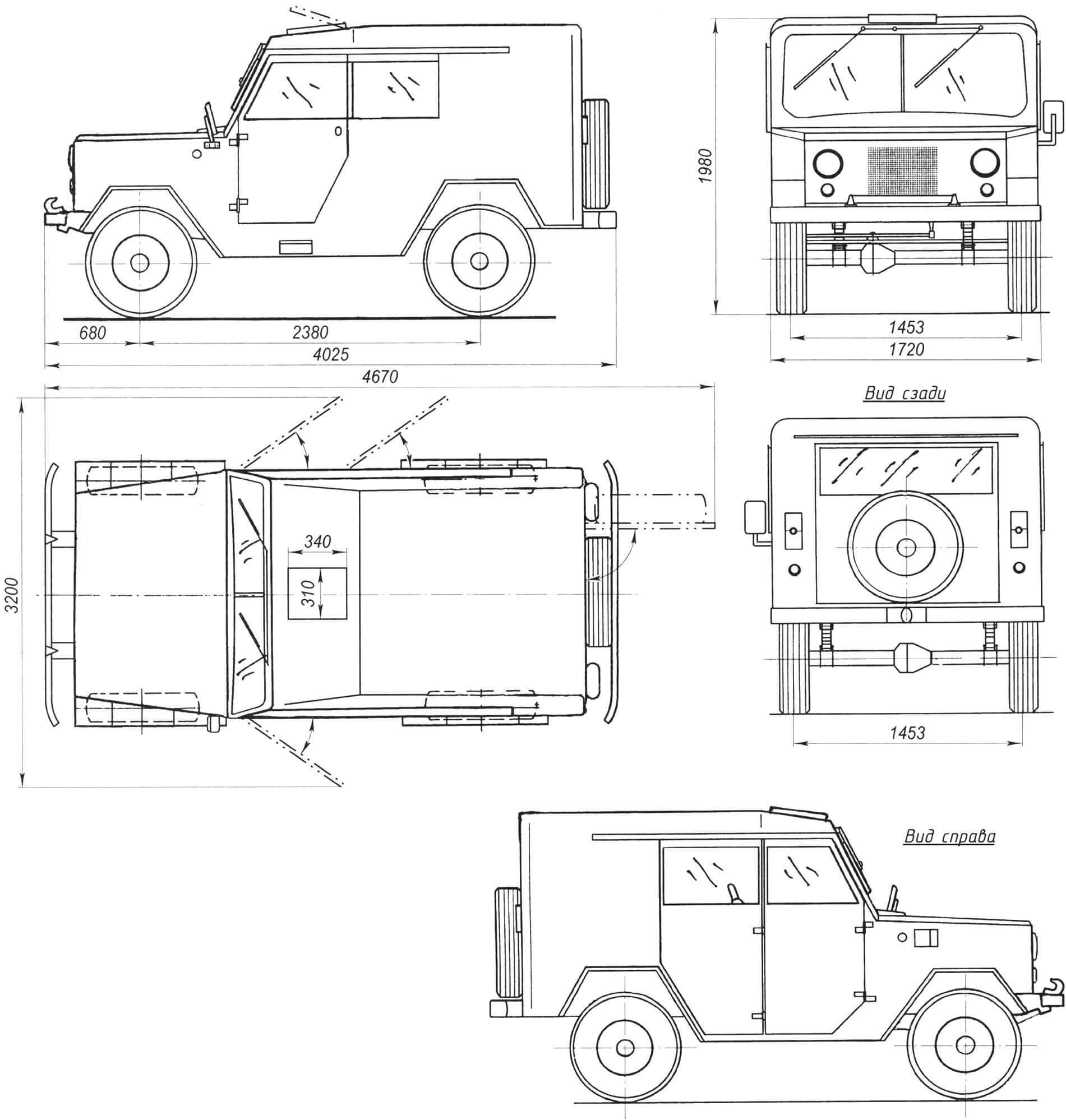
There was almost no question about what kind of body to make: fiberglass or steel. Of course, for durability, fiberglass would be the most suitable – it is simply, figuratively speaking, too tough for rust. But I didn’t have such experience, and I didn’t have time to study. But I was quite confident in the craft and skills of a welder. Therefore, I chose the second option – to make a metal body.
I didn’t think too much about the design of the car – the car was needed not for ceremonial drives, but for trips through the valleys and hills, picking berries and mushrooms. I decided to settle on a form that is close, if not to the serial one, then to the one that is made to order – replacing the canvas awning with a wooden cabin.
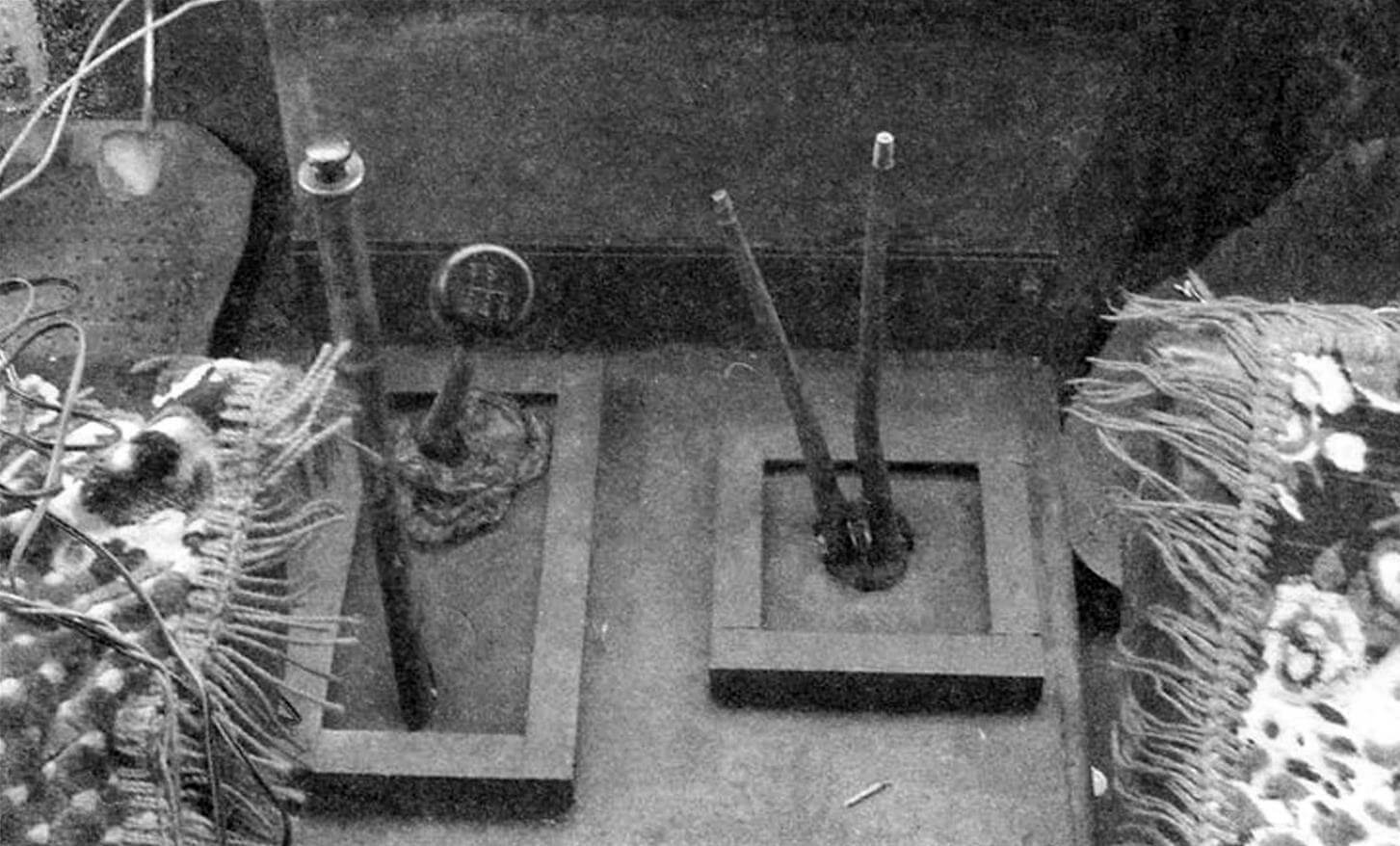
The basis of the body was a frame made of rolled steel of various assortments, both what I had in stock and purchased again. But I tried not to expand it (the range) too much. So, all the racks and upper jumpers are made of a square 25 mm pipe, the lower cross members are made of channel No. 5, the door and opening edging is made of a 25×25 mm angle, and the fender and wheel arch edging is made of a 35×35 mm angle. To cover the sides and doors, as well as for the roof, I used a steel sheet 1.2 mm thick, but the floor was laid out of 2 mm galvanized sheet. Of course, all this increased the weight of the car, but so did its durability.
The body is four-door. However, the location of the doors is like in modern minibuses (now they are called minivans): on the left there is only the driver’s door, two passenger doors on the right (this is better for safety). There is another door – a cargo-passenger door – at the back. It is also made to be hinged (the UAZ had a hinged hatch cover).
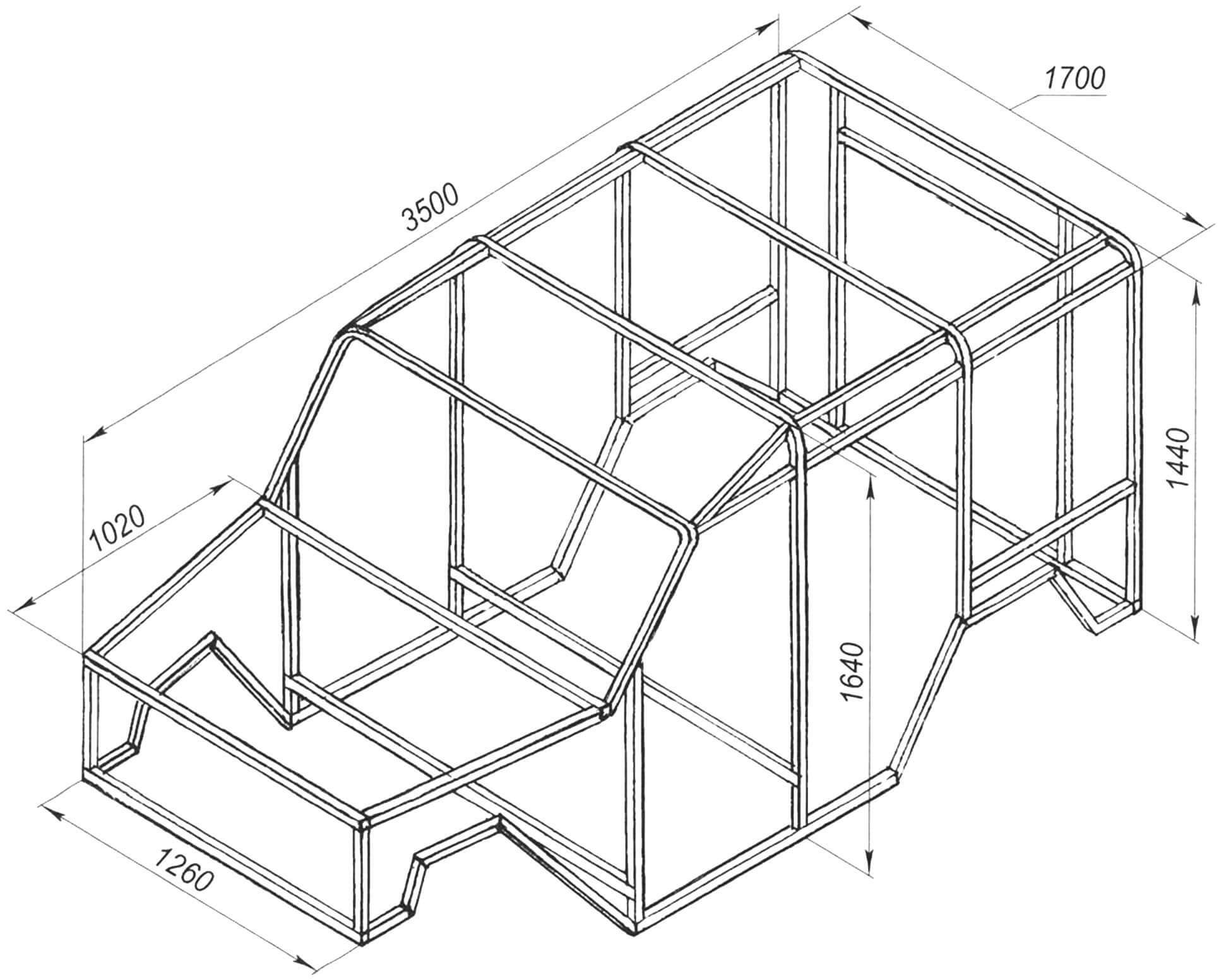
Welding the tubular frame did not present any particular difficulties – it only required careful verification of the relative position of the frame parts, mainly perpendicularity and parallelism. Pipe bending was done using a hand-held device. All bend radii were the same – 200 mm. If there was not enough length of pipes for individual parts, I butt welded them, after grinding off 45-degree chamfers at their ends.
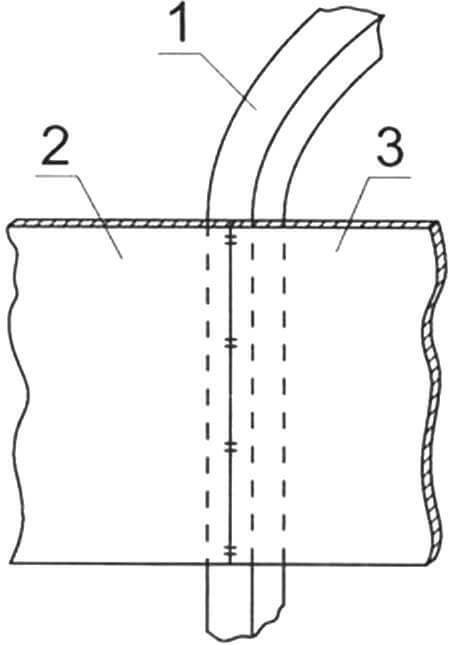
1 — frame stand; 2.3 – joined sheathing sheets
I cut the body skin sheets so that the joints necessarily fall on the frame pipes (at the middle of their thickness). Welding was done spot-by using a thin electrode with a diameter of 3mm – however, even this one turned out to be too thick or it made dots too often – in some places the sheets of metal were still “warped” (warped) and had to be leveled additionally with putty.
The interior finishing of the body was carried out with sheets of laminated “wood-like” hardboard (fibreboard) on one side. Bending the hardboard where the sides meet the roof turned out to be difficult – the material would burst, so I covered these places with a flat strip set at an angle of 45°. I attached the panels and strips to the roof posts and lintels with self-tapping screws.
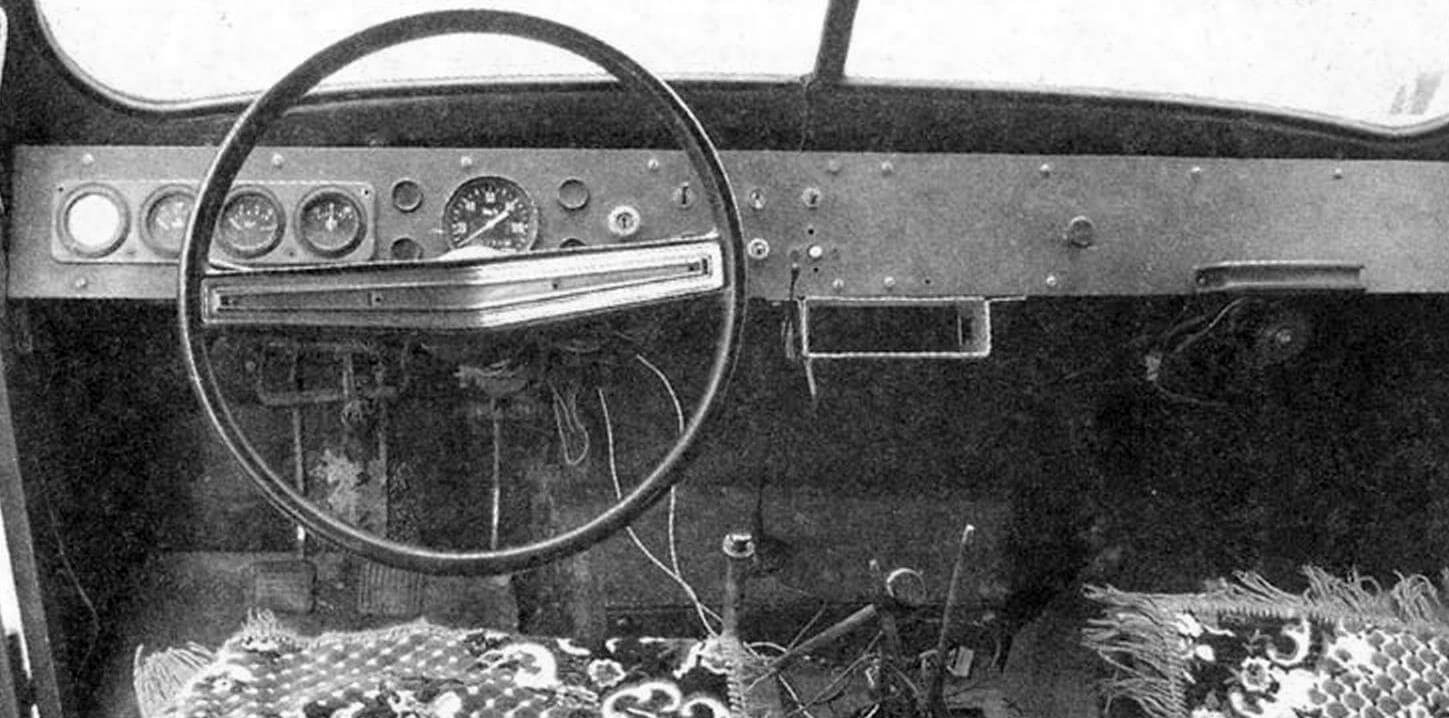
The equipment was mainly used from an old UAZ. I just replaced the reflectors in the headlights – although they were not rusty, they became almost matte. The glass, except for the driver’s windshield, was used from the passenger windows of the bus and was adjusted to the location. They cannot be opened, so I made a hatch in the roof for ventilation. The floor was covered with linoleum.
The layout of the seats did not change, nor did the seats themselves. In the rear (luggage) part of the body, just like in the UAZ, I installed folding seats along the sides. The rear seat, as you know, of the UAZ-469 is foldable.
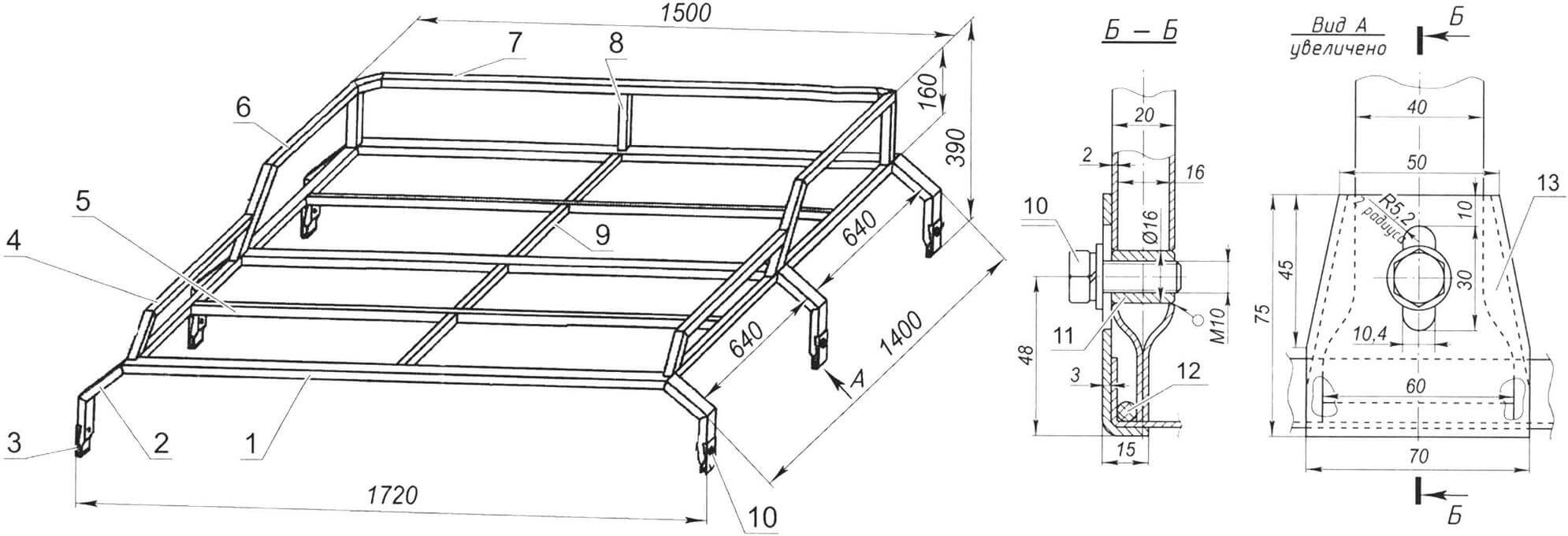
1 — main beam (pipe 40×40, 3 pcs.); 2 — leg (pipe 40×20, 6 pcs.); 3 — clamp (sheet s3, 6 pcs.); 4 – low longitudinal fence (pipe 20×20, 2 pcs.); 5 — auxiliary beam (pipe 40×20, 2 pcs.); 6 — high fence (pipe 20×20, 2 pcs.); 7 — rear fence (pipe 20×20); 8 — stand (pipe 20×20, 3 pcs.); 9 — middle spacer (pipe 20×20, 4 pcs.); 10 — fasteners (M10 screw with split and flat washers, 6 sets); 11 — threaded bushing M10 (6 pcs.); 12 — seal (cable); 13 — body drainage groove (furnishings)
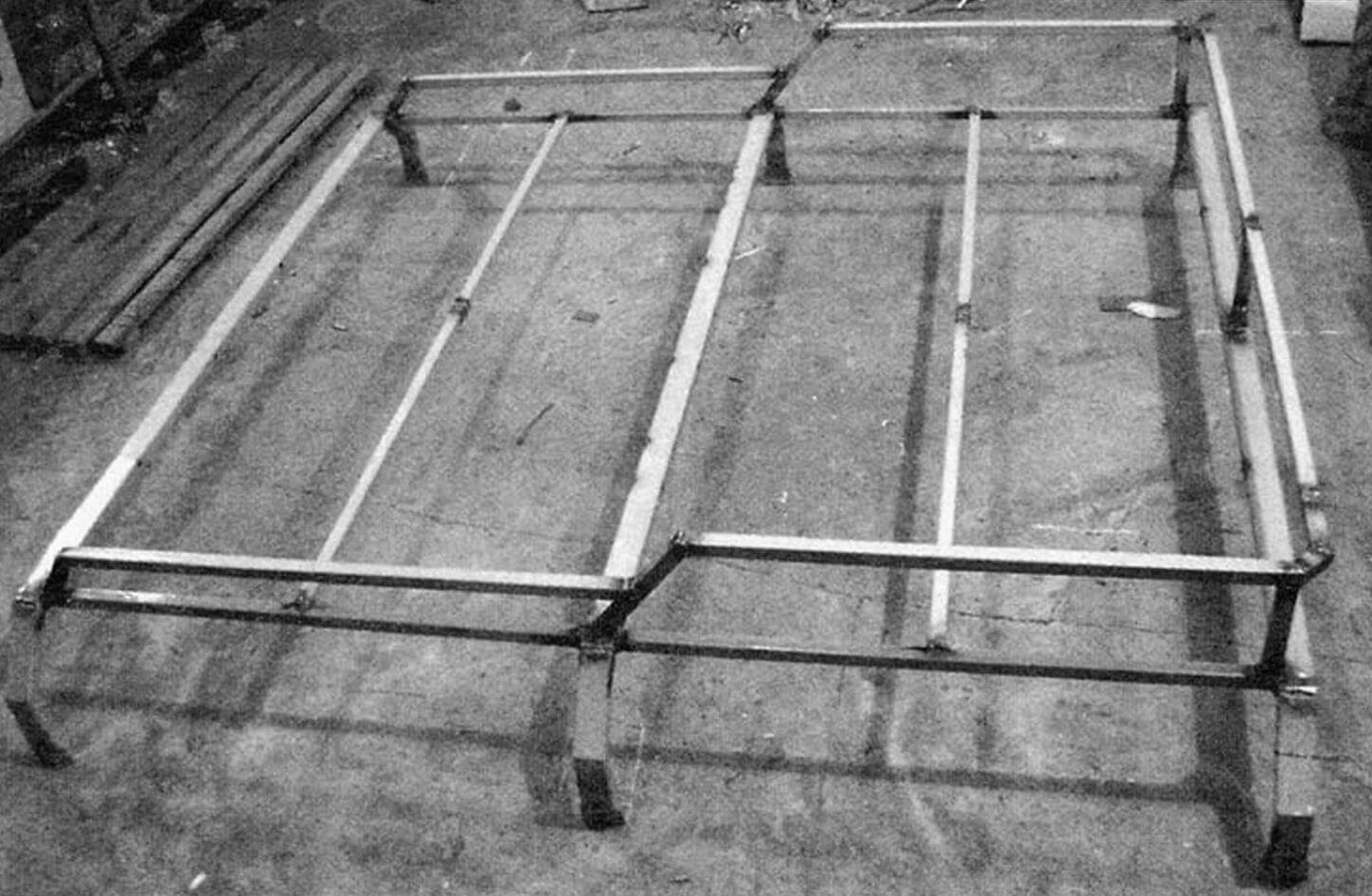
I also had to replace the steering wheel (the standard one was simply cracked) – I installed a GAZ-24 from Volga. The remaining components and assemblies: the engine, transmission, brake system and control system – I simply inspected and repaired what was necessary.
It’s no secret that the UAZ-469 car was nicknamed the “goat” from the very beginning of its production (in fact, this nickname appeared earlier – with the advent of the GAZ-67B) – for its too “stiff” suspension – even when there were two or three people in the cabin, the driver and passengers “felt” every pothole on the roads, not to mention the potholes on the country roads. In order to somehow “soften” the suspension, drivers carried a bag of river sand in the trunk in winter (it could be useful in icy conditions), and in summer they carried a flask of water (both for washing themselves and for washing the car).
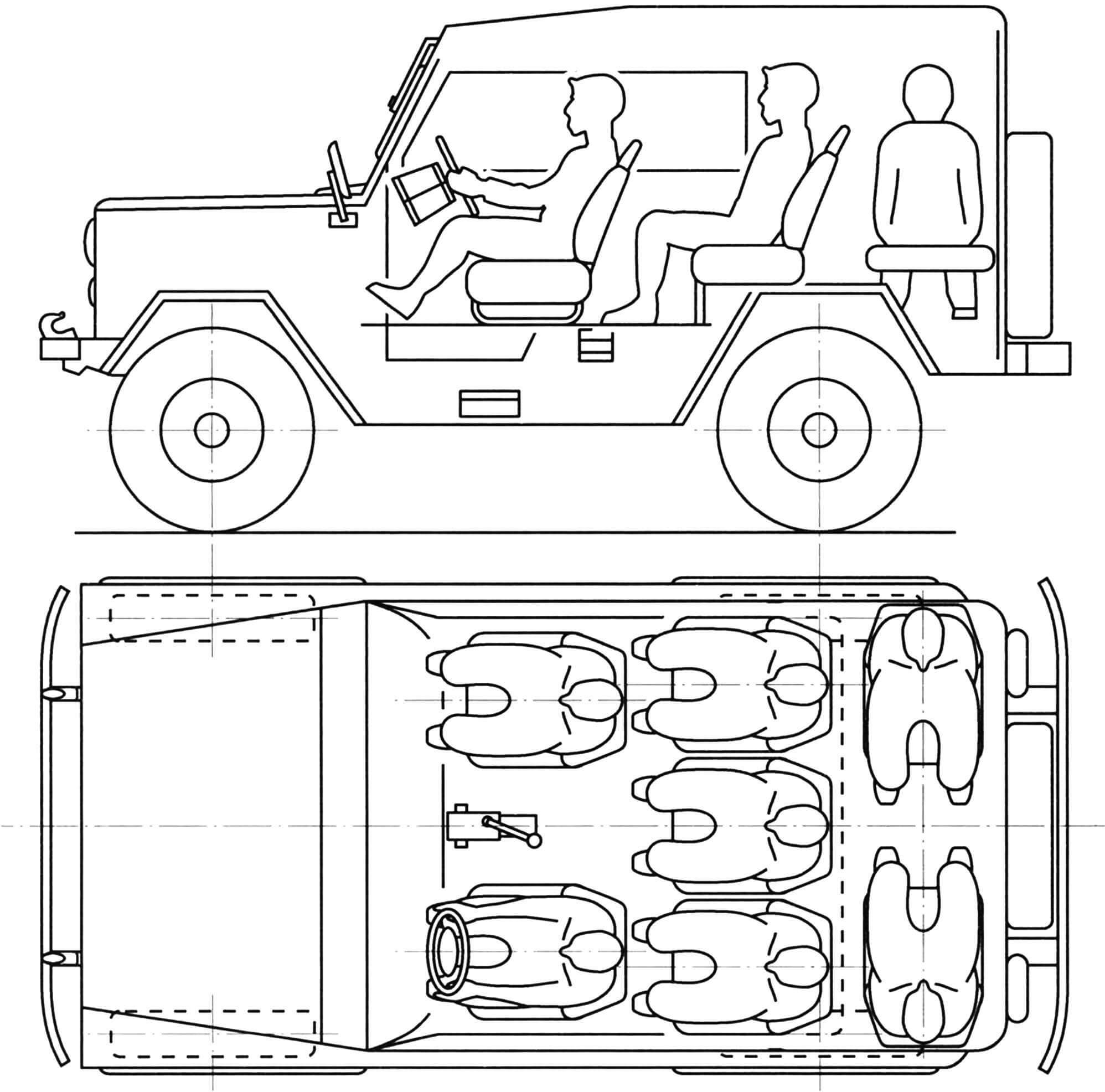
“The Goat”—that’s what the garage owners in our cooperative called my car—gained a hundred kilograms in weight compared to the production car, and its ride itself became much softer. Subsequently, I added one more leaf to the rear springs. The fact is that the capacity of the car is almost like that of a minibus – seven people, and, as a rule, they went on a mushroom “hunt” in full, and also returned with “trophies”. At the same time, the main increase in weight still fell on the rear axle, and then the additional sheet became completely unnecessary.
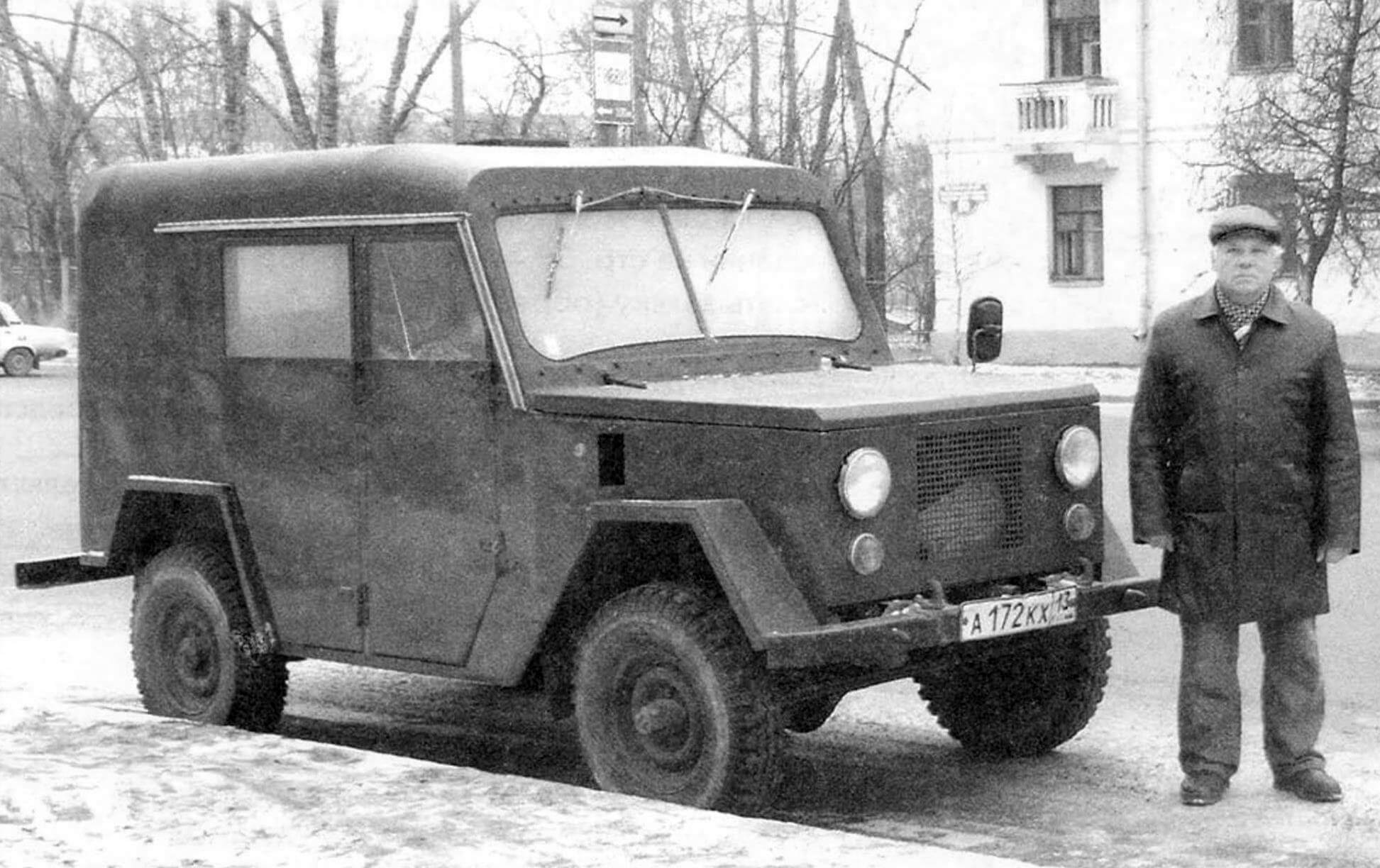
He began reworking the car in 1995 and expected to complete it in a year (at most, in a year and a half). But this process took twice as long, and the car was registered only in 1998. In the documents, special notes indicate that the machine was manufactured as an individual technical creation.
Often mushroom hunting was successful, but it had to be stopped due to lack of space for trophies inside the car. And then one day in a garage cooperative, in a container for scrap metal, I saw a discarded, collapsing universal roof rack for a passenger car. I collected everything that was left of it, and on the weekend I welded a trunk for my “Kozlik”.
N. GORDEEV, Saransk