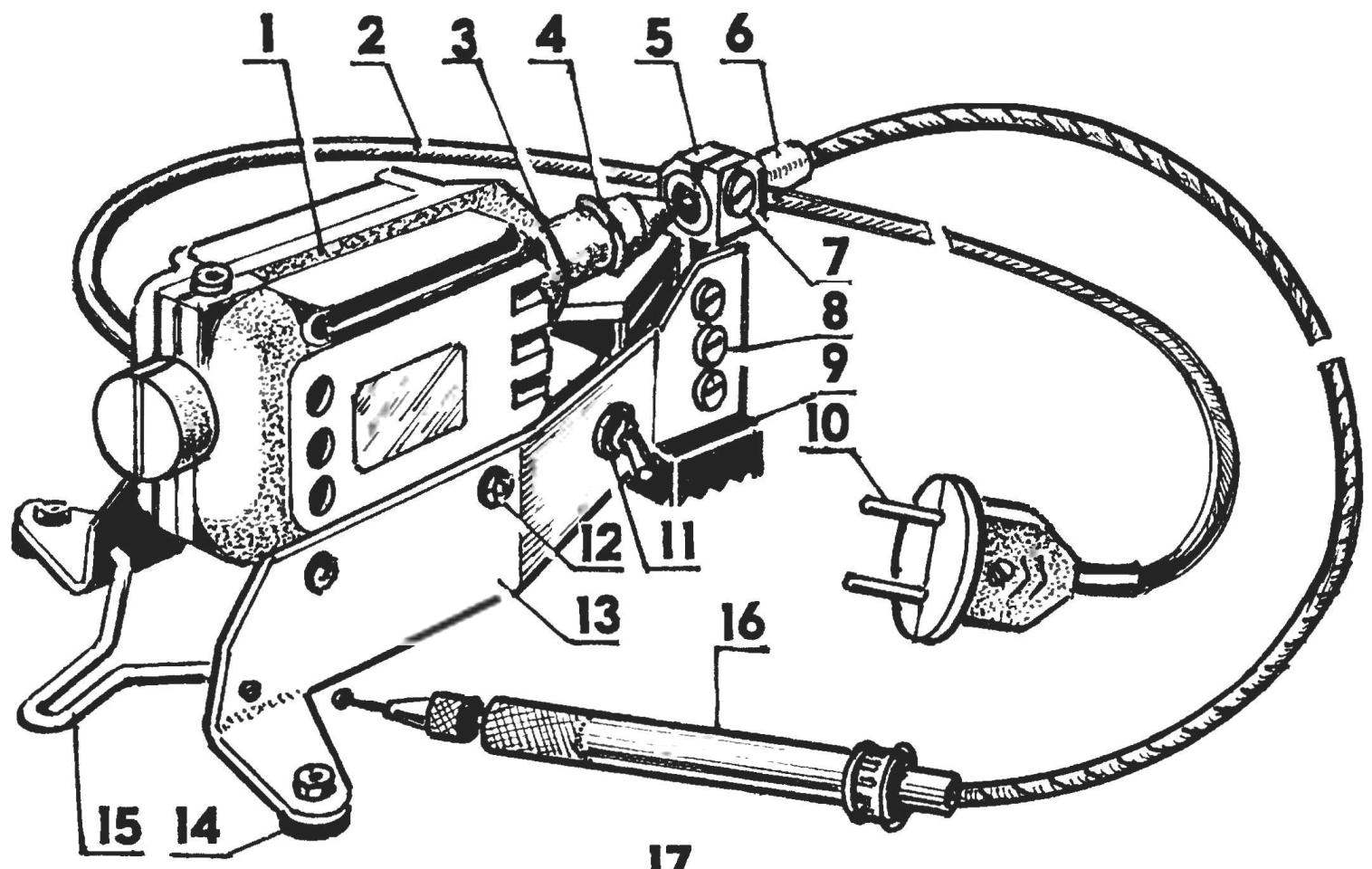
Constructively manual “electrofresh” (so often called the handpiece technicians) consists of the actuator, a flexible shaft and a control arm, which holds the tool.
The drive of the drill used motor MSH-2 designed for household sewing machines of the class 2M-4.
The engine is attached to the base of the two side members by a pair of transverse studs M4 with lock washers and nuts installed instead of the standard bracket with the same thread. Base — tricycle. Support — rubber: two rear (same) inserted into the holes in the spars otkrylsia rear, and one front mounted between the spars in the front. Here, just above, is fastened with two bolts MB support bracket, a flexible shaft, which is a steel cable in budenovskoy braid. The flexible shaft is borrowed from the speedometer of motorcycle MMVZ (you can use a motorcycle “IZH”). The support bracket has kremowy clamp, in which is fixed the end sleeve braid. And tightening the bolt in the clamp performs the role and retainer (do not allow the bushing to pop out of the terminals, even when the flexible shaft will pull), and retainer (prevents the twisting of the braid during the rotation of the flexible shaft).
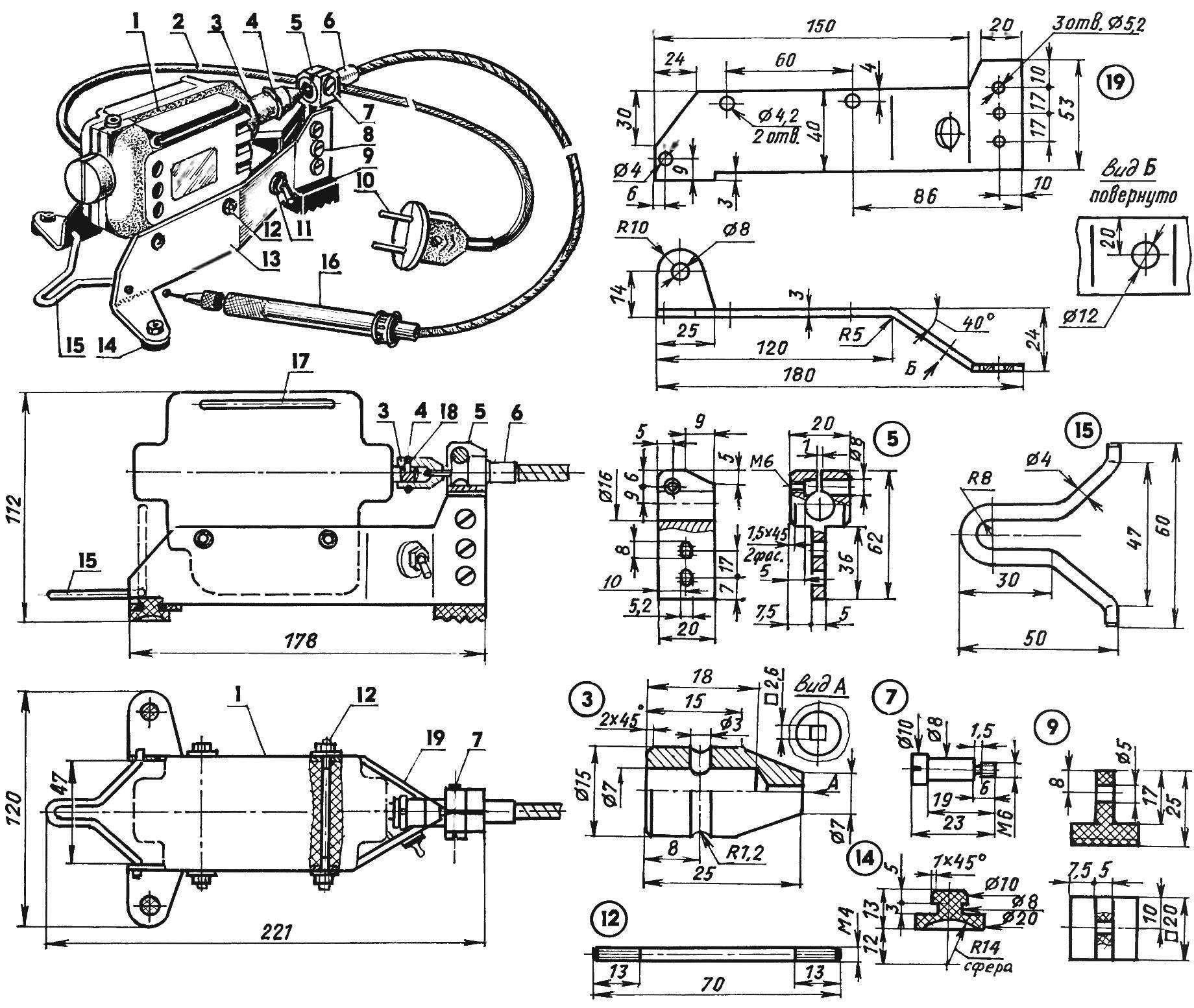
Fig. 1. Drill:
1 — motor for MSH-2 (for sewing machines); 2 — power supply cable brand PRS (cross-sectional area of 1.5 mm2 wires); 3 — adapter sleeve (steel 45, the range Ø15); 4 — snap ring retention poleshift (spring wire Ø1,5); 5 — bracket (St3); 6 — flexible shaft budenovskoy braid with end sleeve and a coupling nut M 18×1,5 (a motorcycle MMVZ or “Iz”); 7 — special M6 screws; 8 — M5 bolt with captive washer (3 set); 9 — front rubber bearing; 10 — a network plug power supply cable; 11 — switch TP1-2; 12 — M4 stud with lock washers and nuts (2 sets.); 13 is a right side member (St3 sheet s3. 2); 14 — rear rubber bearing (2 PCs): 15 — hanging bracket (spring wire Ø4); 16 — an arm; 17 — bracket M4 lock washers and nuts; 18 — poleshift; 19 — left side rail (on the top view, Fig. 17 is not shown)
Torque from the electric motor to the flexible shaft is passed through the makeshift bushing mounted on the output shaft of the motor, where it is fixed by polystigma; and the latter (not out) — served with a springy ring. At the end of the sleeve is made a square hole in which is inserted the tip of a flexible shaft having a corresponding square cross-section. The other end of the flexible shaft is inserted into the same square hole of the tip shaft of the handle and fixed by a nut braid, screwed on the housing handle (not shown).
The shaft arm is made as one piece together with the collet (split spring sleeve), which holds the drill or other machining tool and is fastened by the clamping of the sleeve (the inner cone of the sleeve corresponds to the outer cone bushing).
The shaft in the housing of the handle is mounted in two ball bearings No. 24. The bearings ‘ lubrication is made with grease (e.g. petroleum jelly) that fills the cavity of the handle between them. That grease when working will not escape from the cavity, and the cavity did not get the dust, the bearings are used with two shields, and before tip fit for another valve stem Teflon washer.
Installation and removal of the tool in the collet Chuck are made the same way as in the hand drill, without using the key. Loosening-tightening the sleeve it is necessary to keep from turning both the shaft flange and the handle. On the outer cylindrical surface of all the details to apply knurling on the handle and the sleeve — diagonal mesh at the flange — straight longitudinal.
To drill is not always possible to find a suitable tool. So much of what you may need, it makes sense to make yourself. For example, a good cutter out of the broken drill bits to the creation of the desired profile in the “winepress” (the grinding machine with abrasive wheel). And debris from abrasive wheels of medium hardness could make a good grinding head. First chip a carbide or diamond drill bit is being prepared hole nest with a diameter of 2.6 mm. Into the socket on epoxy glue zamonolichivat mandrel made of steel wire with a diameter of 2.6 mm and a length of 30 mm. After curing of the adhesive is excessively exposed edges of the stone chip off on the sharpening abrasive coarse solids around the final surface of the grinding head form a carbide tool.
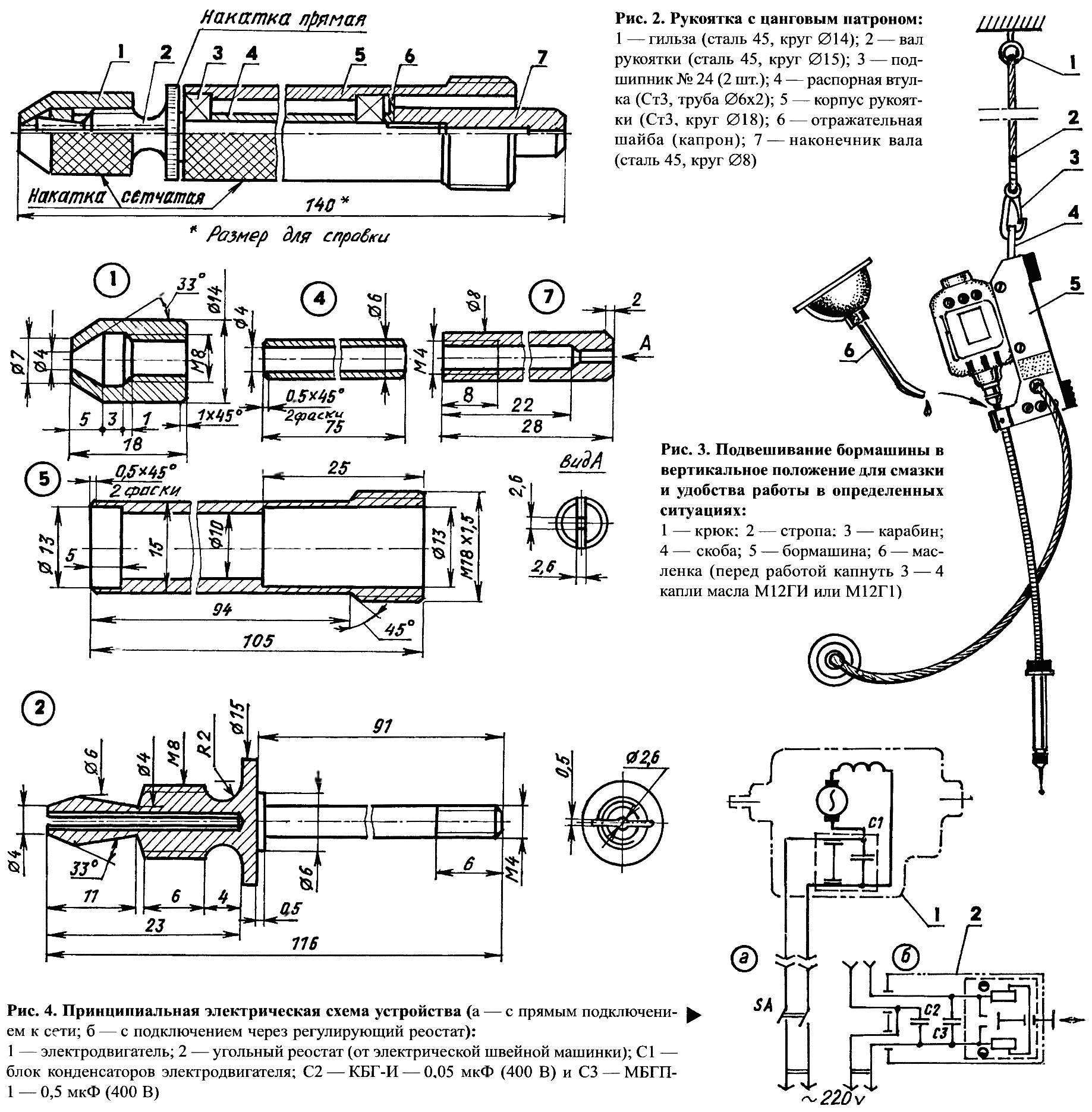
To change the speed of rotation of the cutting tool (which corresponds to the number of revolutions of the motor shaft) to the motor supply voltage circuit of the ballast introduced a carbon rheostat. The rheostat is taken normally, the sewing machine It allows you to change the speed of rotation of the shaft (and tools) virtually from a few dozen to 6000 rpm. If rheostat is not available, the motor connects to the network via the switch, as displayed on the bulkhead (to the left or right as convenient to the master — depending, right-handed or left-handed). It is clear that to change the speed of rotation thus cannot, and it will correspond approximately to a nominal engine speed of about 6000 rpm.
Power supply cable — brand PRS with the sectional area of the wire 1,5 mm2. The supply cable through the hole in the spar and insulating nylon safety sleeve from the opposite tumbler side.
The main working position of the drill is based on rubber shock absorbers. However, when the “flexibility” of the flexible shaft is not enough to compensate for this drawback, the mechanism is suspended in a vertical position on a hook in the ceiling (or on a sling with a carabiner — if the ceiling is high). In the same position every time before the work is carried out lubrication of the flexible shaft with a few drops of machine oil М12ГИ or М12Г1. For suspension of the drill behind the motor between the side members inserted in the holes of the movable bracket from steel spring wire. Stored electrofret is also suspended on the wall.
Technical data motor:
the voltage, V………………………………………………………….220
— consumed power, W……………………………………………….40
— rated current, not more, And…………………………………………….0,5
— rotation speed, rpm………………………………………………6000
— mode of operation………………………………intermittent
V. PETROV, S. fish, Krasnoyarsk Krai