The electroforming technique of electrolytic deposition of metals on the surface of various objects (matrices) with the aim of obtaining accurate metal copies were first developed and applied in practice in 1838 by the Russian scientist, academician B. S. Jacobi. With his direct participation had made many great works of art, statues and bas-reliefs for St. Isaac’s Cathedral, Hermitage Museum, Winter Palace, Peter and Paul Cathedral, including the famous Quadriga to front of the Bolshoi theater in Moscow.
Electroplating is based on the crystallization of metals from aqueous solutions of their salts by passing through them a constant electric current. This process is called electrolysis.
Current is applied by two metal plates — electrodes placed in the electrolyte. Plate connected with the positive pole of the current source is called the anode. The other plate connected with the negative pole of the current source — the cathode.
In the electroplating cathodes are objects (matrix), which precipitates the metal, and the anode — plates or rods of metal that the object (matrix) cover.
Schematically, the process of electrolysis is shown in figure 1. When a current is passed through the electrolyte the anode attracts negatively charged ions, and the cathode — positively charged ions. When ions reach the electrodes, they lose their charge standing in the form of neutral atoms or groups of atoms.
Electroplating is widely used in industry for the manufacture of a molding, a hollow thin-walled tubes, complex parts with a wall thickness of from several microns to tens of millimeters. The dimensions of the parts are limited only by the amount of electrolytic baths.
The matrix is made of plastic, glass, stainless steel, aluminum, various fusible alloys, lead. On the surface of the matrix of insulating material pre-coated conductive layer.
Matrix are destructible and persistent. The first is made of low-melting metals and alloys of plastics. Material for the manufacture of the second are steel, copper, Nickel or aluminum and its alloys.
For the manufacture of metal tubes at home necessary bath of glass, ceramics or vinyl plastic, copper sulfate, sulfuric acid, the rheostat is 20 Ohms (maximum current 1 A), ammeter with a current maximum deviation of the arrow 1 a, power source, wire (copper, steel or of low-melting metals and their alloys, e.g. tin-lead) as matrix.
The wire diameter corresponds to the inner diameter of manufactured pipes, and the length of the first should be twice the length of the second.
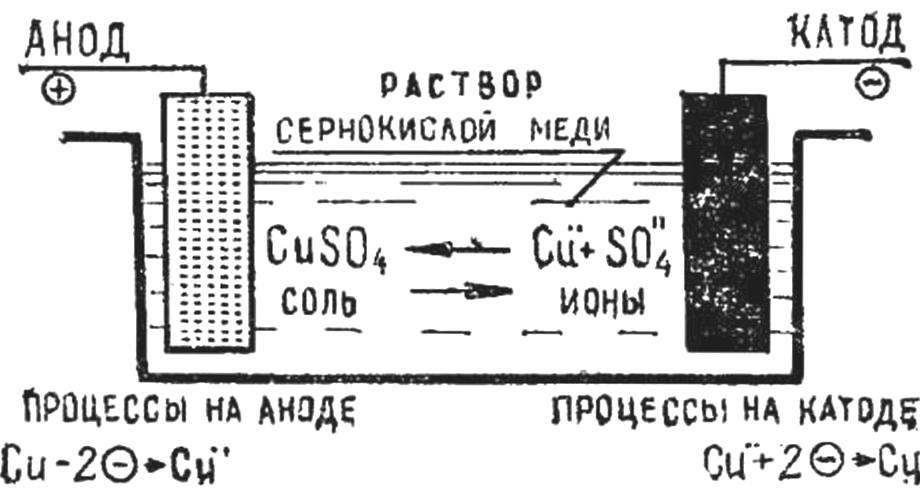
Fig. 1. Diagram of electrolysis.
If you need a tube with an inner diameter of less than 1 mm, as a matrix using a steel wire. In the manufacture of tubes with internal Ø 5 mm and the matrix is made from low-melting metals and their alloys (e.g. solder bar).
The wire should be smooth and even. To do this, it is sanded with fine sandpaper, and then bring microsource (“nulevkoy”). Then wire oblizyvaet, the excess solder is removed, stretching of the heated wire through clutched in the fist of a rag. Non-working areas of the matrix covered with clay.
In warm water (50-60° C) dissolved copper sulphate (200-250 g of salt per 1 liter of water) using the glassware. The supernatant electrolyte was filtered and then poured sulfuric acid from the calculation of 50-60 g per 1 l of solution.
It should be remembered that to pour the solution in concentrated sulphuric acid impossible. In contact with water, it causes a violent reaction with high heat and steam generation. The result may be a release of acid from the vessel. Therefore, it is necessary to pour acid in a solution of copper sulfate in a thin stream, stirring constantly with a wooden stick.
Copper to the sediment was dense and fine-grained in the electrolyte it is recommended to add a bit of ethyl alcohol (5-10 g on 1 l of electrolyte).
The prepared electrolyte is poured into the working tray where stacked matrix and copper plate or wire.
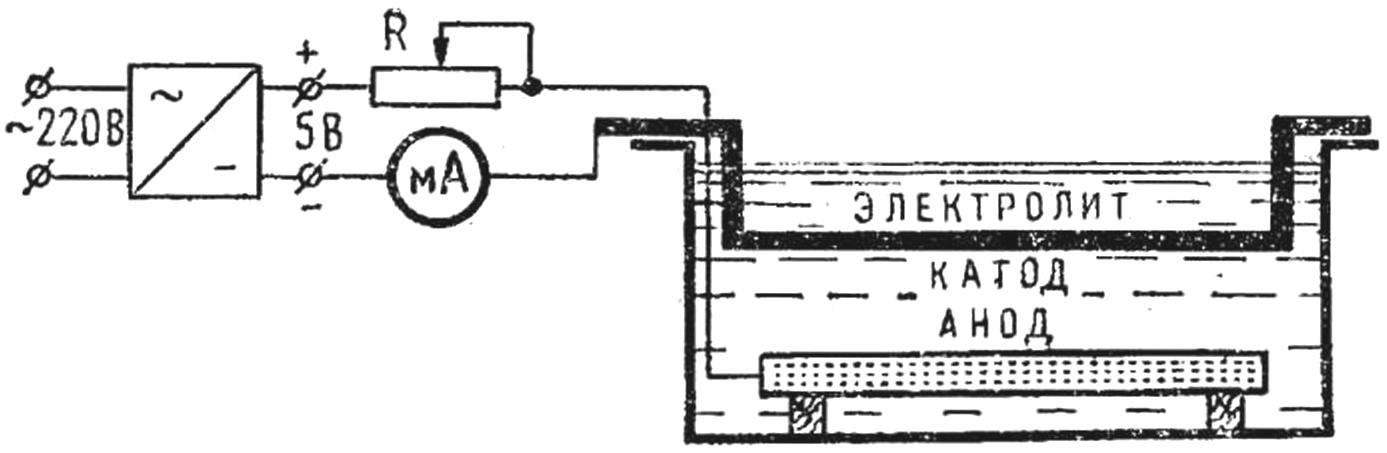
Fig. 2. The scheme of the electrolysis setup.
Of the matrix are connected to the “minus” and the copper disc or wire to the “plus” of the power source. The area of the anode should be 5-10 times larger than the area of the cathode.
The scheme of installation for home electroforming is shown in figure 2. The transformer of the power supply has the following data: core Ш20Х20, the winding of I contains 2200 turns of wire PEV-1 0,12 (220 V) or 1300 turns of PEV-1 is 0.15 (127) winding II—35 turns of PEV-1 to 0.8.
The process of electrolysis and the coating quality depend mainly on the composition of the electrolyte, temperature and current density.
The temperature of the electrolyte 18-25° C.
The current density — current per unit surface is calculated by the formula:
j=i/S,
where i is the current in the circuit, And,
S – the surface of the product, DM2.
In practice, j=1-1,5 A/DM2.
Example 1. To determine the value of the working current of electrolysis for the manufacture of pipes with external Ø of 5 mm and a length of 100 mm. Take the current density is 1 A/DM2, then
I=jS=1*3,14*0,05*1 =0,16 A.
The calculation of the exposure time of parts under the current in a galvanic bath to obtain a layer of thickness σ mm is determined by the formula:
t=σ*d*1000/j*C*η,
where t is time, h;
σ — tube thickness, mm;
d — specific weight of copper, kg/mm3;
j is the current density, A/mm2;
— Electrochemical equivalent of copper, g/A-CH; η is the estimated current output.
Specifically for our case are
d = 8,95 g/mm2, i = 1 A/mm2; C = 1,186 g/A-CH; η = 95.
Example 2. To determine the retention time of the matrix under the current in a galvanic bath to obtain a copper tube with a wall thickness of 0.5 mm.
t=σ*d*1000/j*C*η=0,5*8,95*1000/1*1,2*95= 40 hour.
After the estimated time the matrix is removed from the plating bath and washed with water. The end of the wire at a distance of 1.5—2 mm from biting the tube and after heating to a temperature of 200-250° With the extended tube can be easily removed from the matrix.
In the same way to produce tubes of Nickel, chromium and iron.
V. BUSHUEV, A. NOVIKOV, Voronezh