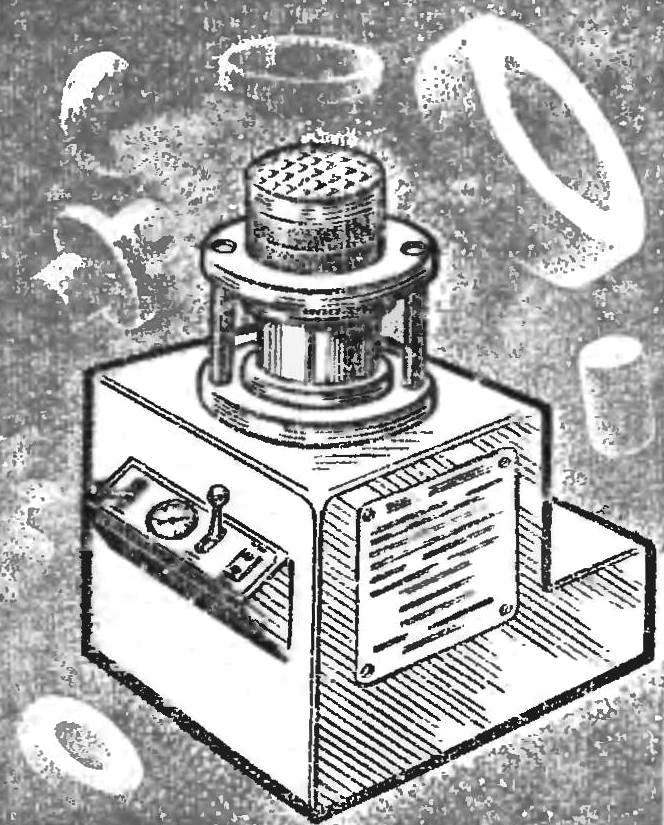
In our smoke, with wide application in the construction of pre-cast concrete parts, the old way has suddenly found a new use — at the production of NZ concrete: slabs, panels, blocks.
The fact is that they receive little to fill in the solution form — it is necessary to condense. For this purpose, use various kinds of rammers, vibrators. However, this technology is multi-stage and is quite expensive. That’s why at the Kharkov Institute of engineers public works have aimed to simplify and merge in a single operation, laying and compaction of mortar.
Here, we developed an original and quite simple to install (see photo and Fig. 1), which is a process similar to the work of plasterers, concrete with a strength in sprayed form at the same time compressed under the action of the kinetic energy imparted to it by working bodies of the Assembly.
The installation consists of a rotary propelling head, the bunker with a concrete mixture and a belt feeder. All this is mounted on a stationary frame, under which runs a trolley with forms. The operation is as follows.
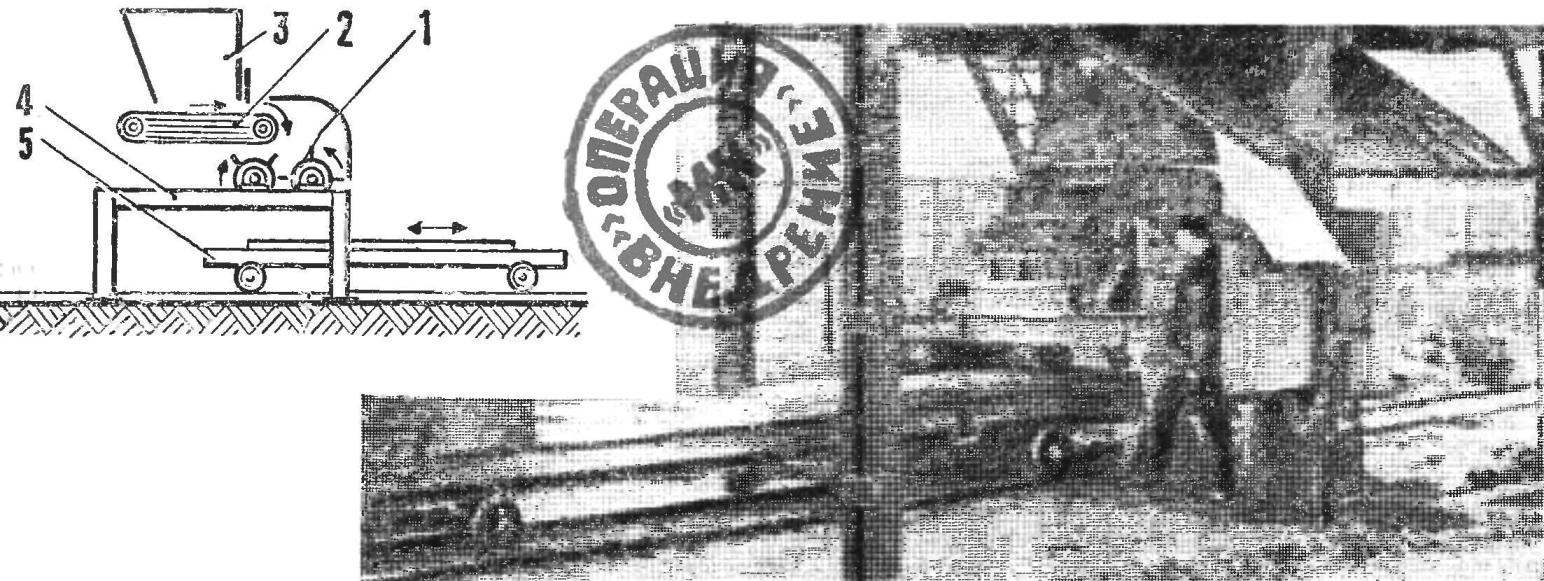
Fig. 1. Metonomy (scheme and appearance):
1 — throwing head; 2 — belt feeder; 3 — bunker; 4 — static frame; 5 — cart form.
Concrete mix from the hopper through the belt feeder is fed to the throwing head, which has two lobed rotors which rotate towards each other. Thanks to them splashing occurs and the temporary separation of the concrete mixture: granules of mortar bed first, and hammered into them, like hail, the grains of coarse aggregate.
Thus, the “repectively” throwing head solution receives in the form of the second seal, “bombarded” the escaping particles of gravel or expanded clay “shrapnel” that are included in the concrete mixture.
Installing RB-2 for power spraying of concrete is suitable for mass production of prefabricated structural elements with rectangular cross section. The performance is 40 to 50 m3/h.
The machine control is carried out with a General remote. There is also the possibility of working in automatic mode according to preset program.
“CHANDELIER” ABOVE THE QUARRY
Each of the light source, whether it’s a flashlight, table lamp, spotlight, light has its own “spot” — the area in which he can win from the darkness. To increase it, to cover a large area, it is necessary to add a certain number of such sources. In manufacturing, this means additional costs for trenching, laying of cable and installation of poles, installation of brackets, wires, lamps, the cost of operating them. Another thing is the sun: its light is a “spot” half of the globe!
A kind of artificial sun created recently in the Moscow energy Institute, at the Department of lighting engineering and light sources. One such “chandelier” is quite enough to illuminate the shop, Plaza, stadium, quarry.
For this we used a strong tubular lamp of the type Dist a capacity of 20 and 50 kW and the original chandelier is a parabolic reflector composed of flat and long mirror strips.
Plate Central and marginal parts, and also mirror insert combine to form a powerful flow of light that can cover a huge area, with a length of 12 km.
The Institute has developed a series of plate for lighting of industrial areas, construction sites, mining, mines, pits hydroelectric power stations, major river and sea ports.
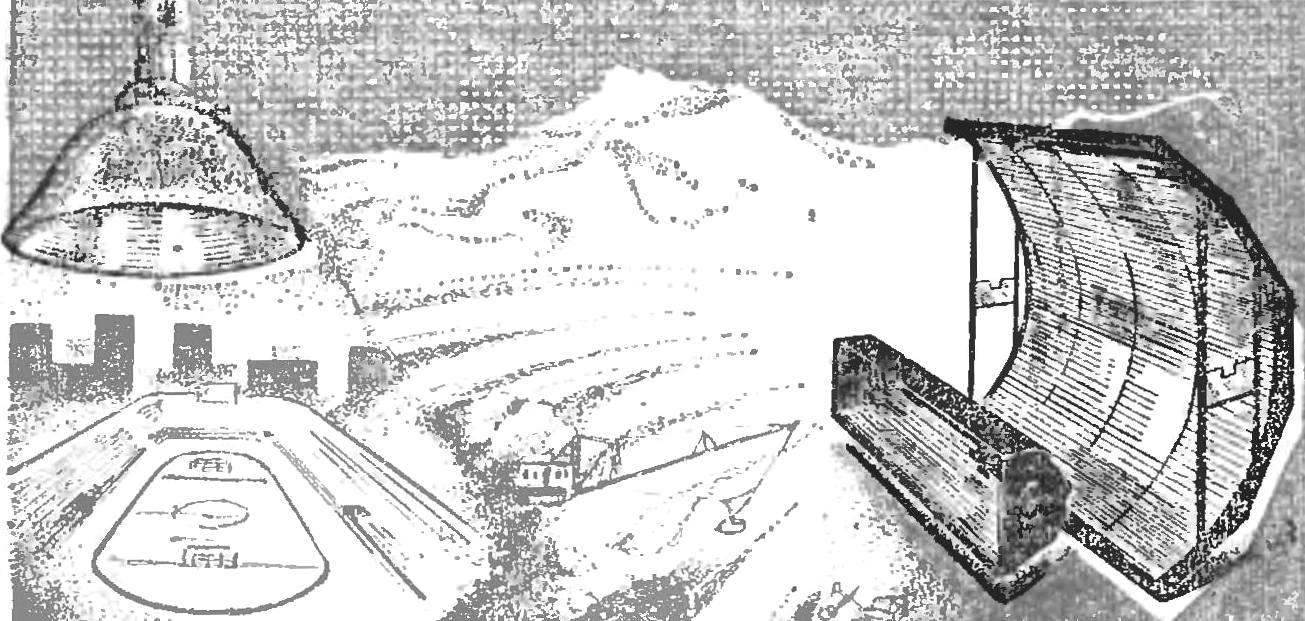
Fig. 2. Heavy duty lights: “the bell” (left) and plate mirror.
Here created another series of lamps shaped like a bell, with lamps such as XRD of various capacities from 400 to 1000 watts. “Bell” is a mirror troglocimmerites lamp having increased “light output”. The convenient profile it is possible to produce similar lamps for automatic forming machine.
These chandeliers are connected via a throttle to a conventional power supply.
Their design provides higher manufacturability, and also has improved performance characteristics compared to similar devices. The new design of knot of fastening of the cartridge helped to reduce the metal consumption and improve the manufacturability of the Assembly to facilitate connecting the network live. The total complexity of installation of the lamp is reduced by 30%.
AND THE PRESS, AND HAMMER
The original system for the molding of products of non-metallic powder materials and refractory masses developed in the Vinnitsa Polytechnic Institute.
It combines the technological operations of two units: the press and a blacksmith’s hammer. This is achieved by the clever design decision (copyright certificate № 429877 and 443219). Due to the peculiarities of the plant material being processed, filled into a mold, subjected to the double exposure. First compression in the time course of the trunk up under the action of the pressure pulse of the fluid. Then the shock from moving machine parts during the return stroke under the action of elastic elements. This significantly decreases the required specific pressure force.

Fig. 3. Inertial vibrating hammer.
Pressed powder material is filled with a separable mold for receiving the item and placed in the working area of the installation. All of these operations and seizure of finished products are carried out by means of special devices and the installation kit. Fixtures can be replaced depending on the shape of the pressed products.
Installation, or hydraulic inertial vibrating hammer (IITM), has small dimensions (1.5 X 0.8 X 1.2 m), increased performance and versatility.
“FOUR -” CRANE
The building cranes on the car during a small load. But even the most “weak” of them can become many times stronger if it will have an unusual four-stage missile, developed in Makiivka civil engineering Institute.
It is a hinge chetyrehdverny held strelovym chain block. When lifting one of the peaks of this chetyrehdverny (shoes sevra) rests on the base. This creates the ability to use all of the support-suspension crane as congresa.
To move the crane within the construction site, and installation of the boom to the desired position of support of chetyrehdverny tightened up the auxiliary pulley.
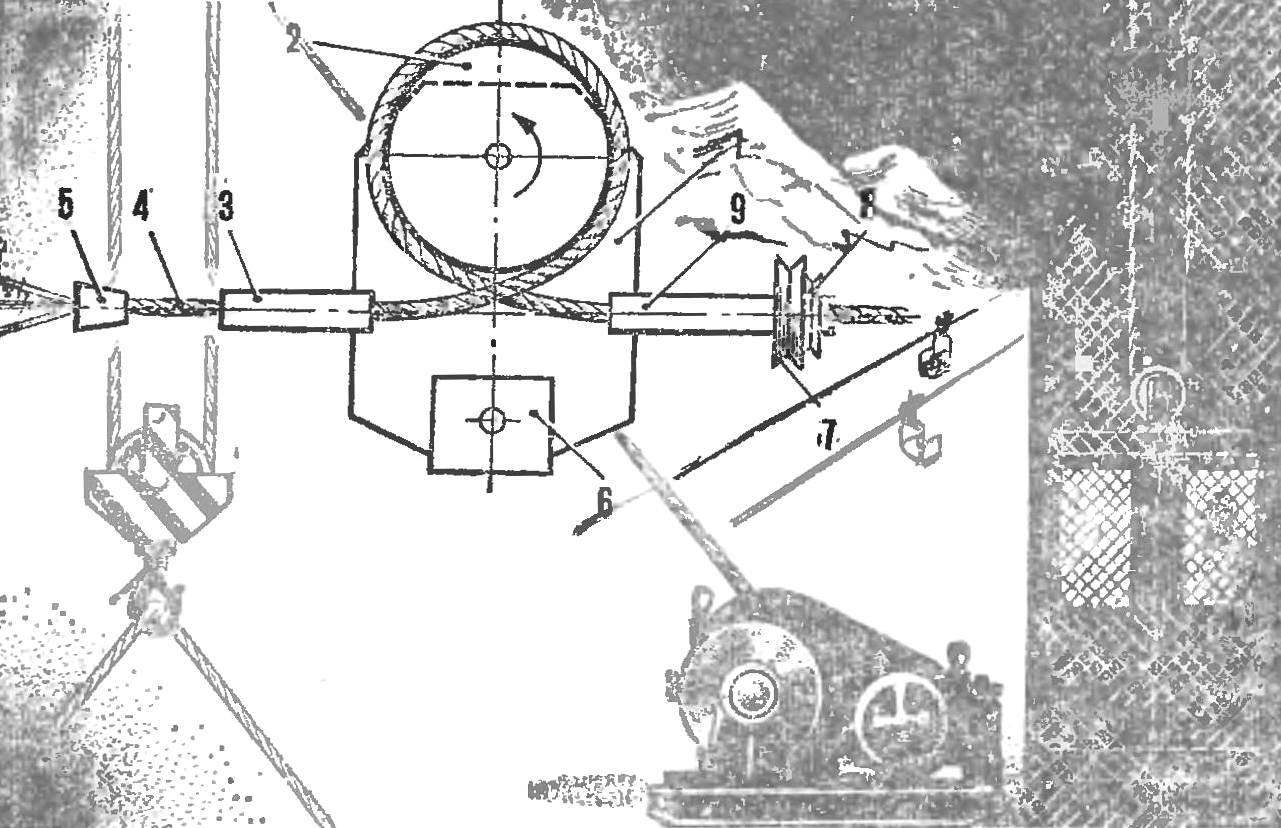
Fig. 4. A deformer, “correcting” the ropes:
1 — base; 2 — a pulley for the twisting of the rope; 3, 9 — a hollow support; 4 — rope; 5 — the gauge of the die Kanatova machine; 6 counterweight; 7 — a pulley belt transmission; 8 — clutch.
A four-stage boom can be used as replacement equipment for jib cranes with chain increase not only capacity, but also the height of rise of the load. It is indispensable when lifting particularly heavy or dimensional structures and technological equipment: eliminates the need for special taps. It provides up to 14 thousand rubles. annual savings for each tap.
The prototype four-stage crane boom on the basis of MCG-25 made in the Slavic boiler mechanical factory, and has passed industrial tests in the trust “Donbassstalkonstruktsiya”. He was able to lift loads up to 50 tons; the biggest lifting height is 25.2 m.
SPINNING WHEEL FOR ROPE
Where not only used steel ropes — from elevators and cranes to cable cars and suspension bridges. For their manufacture constructed various machines, the most productive of which are the so-called cigar. But they have a major drawback: the steel strands are exposed here only the simplest, one-sided lay. This reduces the strength and durability of ropes, they wear out faster or even spin.
To eliminate this “weak spot” production of ropes, Sevastopol instrument-making Institute has designed a simple device for deformation of the torsion ropes (Fig. 4). And the additional “neutral” spin, which then assumes the technological torque.
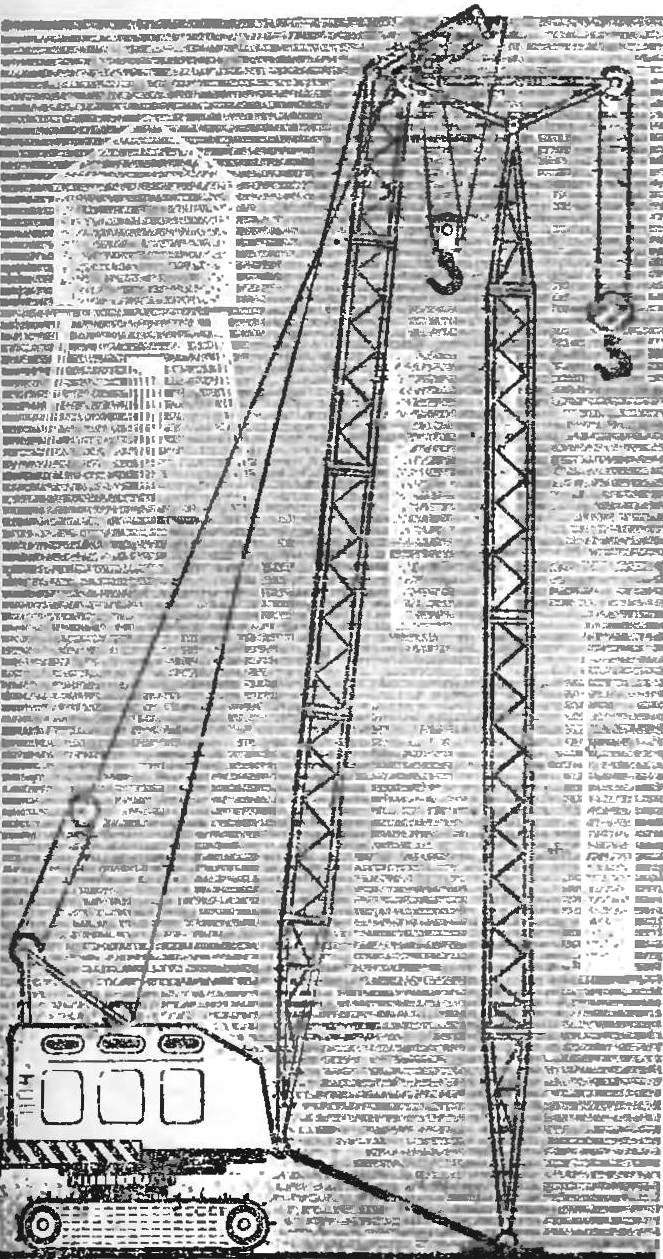
Fig. 5. A crane with a four-stage boom.
The deformer consists of the case-base, fixed, as if on an axis on the hollow supports. Rope gauge dies recoiling machine is fed into the hollow support extends around the pulley located in the housing of the deformer, is the second hollow support having a pulley for belt transmission with friction clutch, and enters an exhaust mechanism Kanatova machine (not shown). Deformatter rotates around the axis of the rope, twisting it between dies bearing and pulley to the desired angle. After the deformer, the rope will unwind now only “provoked” them a place. The performance of this unit — 3000 m/h.
Device for deformation of the torsion ropes have been successfully tested on the Oryol steel-rolling factory. Experienced ropes, manufactured with the use of the deformer, showed good form on the lifts mines plant “Tuppal”. The durability of the rope has increased by almost 1.5 times. In the manufacture this way every 500 tons of ropes provides an economic effect of up to 110 thousand rubles. per year.
THE BEARING OF ASPEN…
Yes, any piece of wood — will PI’s aspen, acacia, apga, maple — can compete with the best of metals and synthetic materials used usually for the manufacture of bearings. And that is where the working conditions these parts are the heaviest in the friction units of agricultural machinery, tractors, cars, press-forging and mining equipment, in metallurgy and chemistry, railway transport, and even on rolling mills.
Such opportunities wood gets thanks to the simple process of pressing. It receives the properties, as shown by special studies carried out at the Dnepropetrovsk Institute of chemical technology, allows wooden workpieces to replace not only the PCB with the nylon, but even the “Queen” of friction — bronze.
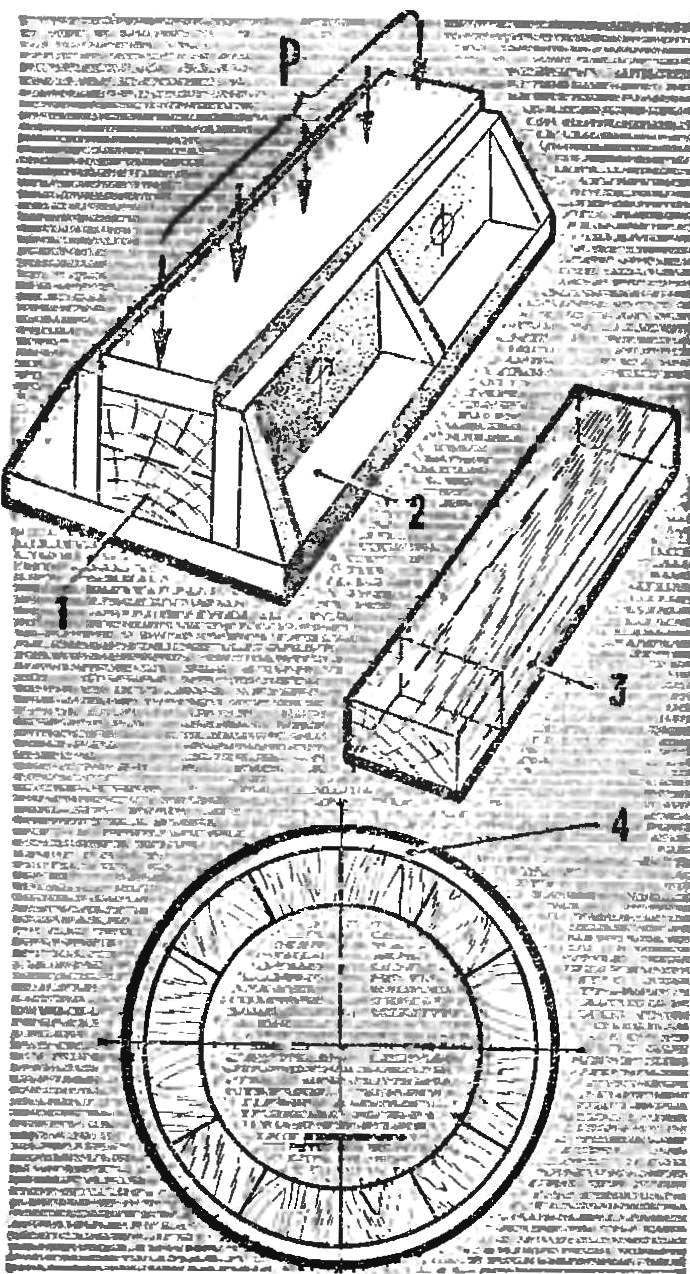
Fig. 6. Piece of wood (1, 3), the mold (2) and the finished bearing (4)
For “magical” transformations of wood you will need an autoclave (rasputnik) giving the temperature to 100— 105° C, press with a force of 150 — 200 kg/cm2, a simple mold and a drying Cabinet, providing heating to 105-110° C. the extrusion Technology is basically the same as described in No. 5 for 1974.
The bearing wood is not afraid of abrasive contaminants, absorbing them; works fine in Lara with steel shaft; easy lubrication: can be satisfied with… water. Impregnated with mineral oil or paraffin do not require lubrication, which facilitates and simplifies the operation.
The comparison showed that the bearing wood for sheet rolling mill, for example, is six times less textolite, and works as many times longer. Its durability is twice higher than that of bronze.