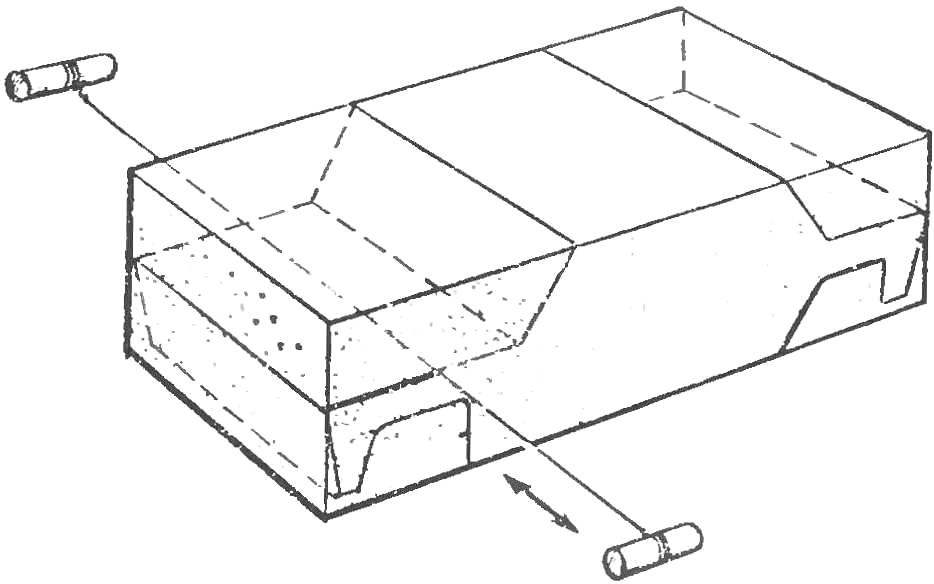
Some of the homebrew I can say that the foam, for example, is not strong enough. But try to build such a “sandwich”: consistently glue epoxy resin sheet in millimeter plywood, the foam sheet thickness of about 20 mm and another sheet of plywood mm (Fig. 1). After polymerization of the resin, the bending strength of this “sandwich” will be commensurate with the strength of the boards the same thickness.
Like any other material, foam has its secrets, knowing that it is possible to significantly expand the scope of its application to develop your designs.
First, you need to learn how to make bricks from foam blocks of any size that are selected foam blocks, prifugovyvajut to each other, of which “dry” block is made and then “inokichi” contact rubber harness or ropes.
To enter the unit in the desired dimensions, it is easiest to use the plane, just keep in mind that the foam is very Sensitive to the sharpness of the grinding tool. From a plane with a blunt piece of metal, the surface will succeed with ragged shells and bullies. It is best to handle the special foam plane. The slot under the piece of metal it is with the axis of the plane angle about 45° (Fig. 3).
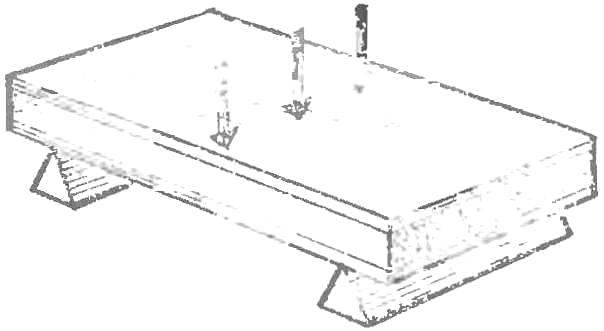
Fig. 1. Foam, reinforced with plywood, not so easy to break.
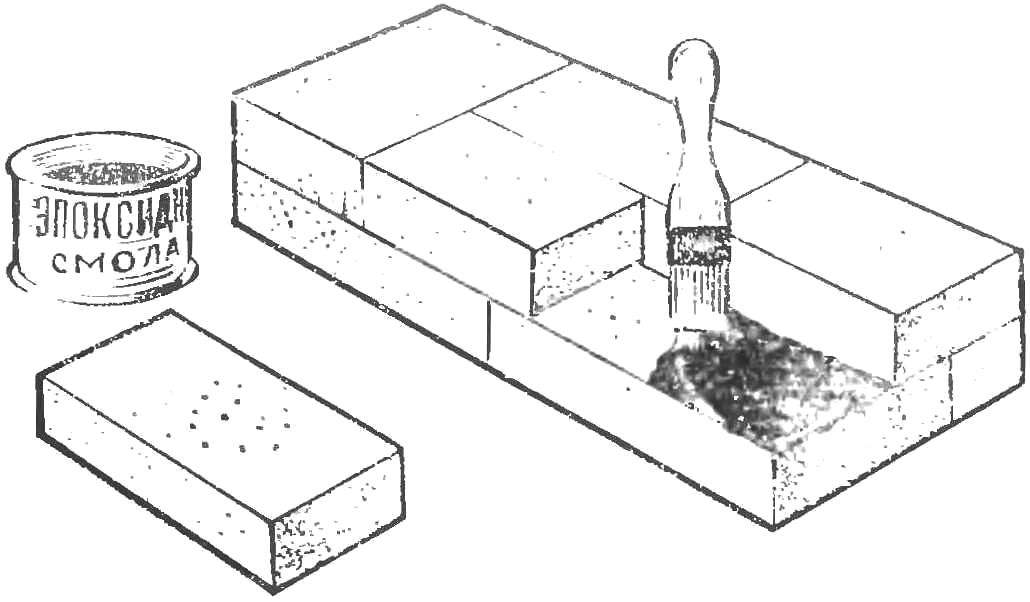
Fig. 2. Block of the required size you can glue the separate “bricks”
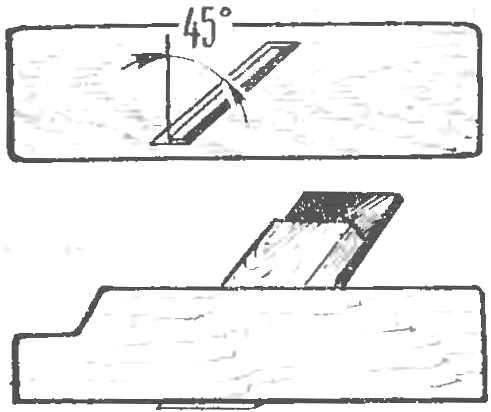
Fig. 3. For foamed polystyrene boards more suited to such a plane.
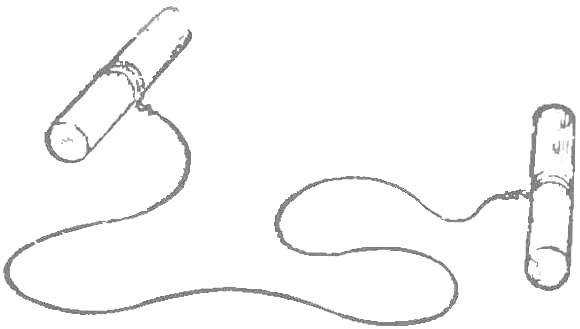
Fig. 4. “Saw” foam.
And now from the foam block should be cut conceived detail. No, for a saw to take not worth it, it will come in handy when cutting wood. For our material, “the saw” it is better to construct yourself — you will only have a metre piece of wire OVS Ø 0,5 mm and two round stick (Fig. 4). You’ve probably seen in grocery stores sellers cut cheese and butter. Similarly, you can cut the foam. Do it best together. Draw on both sides of the foam block line — traces of the surface of cutting and begin to cut (Fig. 5). After the first two or three movements “saw” is heated and begins to be melted through the material and can follow that wire was exactly in the planned lines. The cut surface has a satisfactory purity.
For cutting you can use nichrome wire, glow or electric shock. Cutting material with a hot tool makes it easy to obtain such details, the implementation of which in any other way would be very time consuming. For example, the production of ribs or even zernoproduktovy wings model airplanes and gliders. To do them the traditional ways, you have to spend a lot of time and effort, and there is no guarantee that the ribs or the console will work exactly the same. Well, if you use the device, shown in figure 6, then quickly made several sets of parts. The advantage is that after processing of hot-surface of the foam formed
melted crust that give the parts rigidity and smooth surface, almost do not require additional machining. The rigidity of the console would improve considerably if the paste epoxy’ in the wing surface one or more glass strands (Fig. 6).
Unfortunately, the foam parts sufficient surface hardness: any sharp object can leave the surface risks furrows or punctures. There is enough to coat part epoxy resin: it will close the surface pores, giving the piece a smoothness and stiffness. If using the same resin paste over the product two or three layers of fiberglass, the stiffness is more increased. The combination of foam with epoxy resin allows to make the hull of ship models, models of car bodies, parts and interior. Some of the crafts shown in figure 7.
An interesting effect is obtained when coating of foam materials such as leatherette or faux leather. Do it best glue “88”. Note that the foam stamps PS (polystyrene) dissolves this glue, so for pasting selected foam PVC (PVC) leatherette Cording allows, in particular, to do “brand” the box housing for tape recorders and radios, dashboard and interior details of the cabin in a makeshift car (Fig. 8).
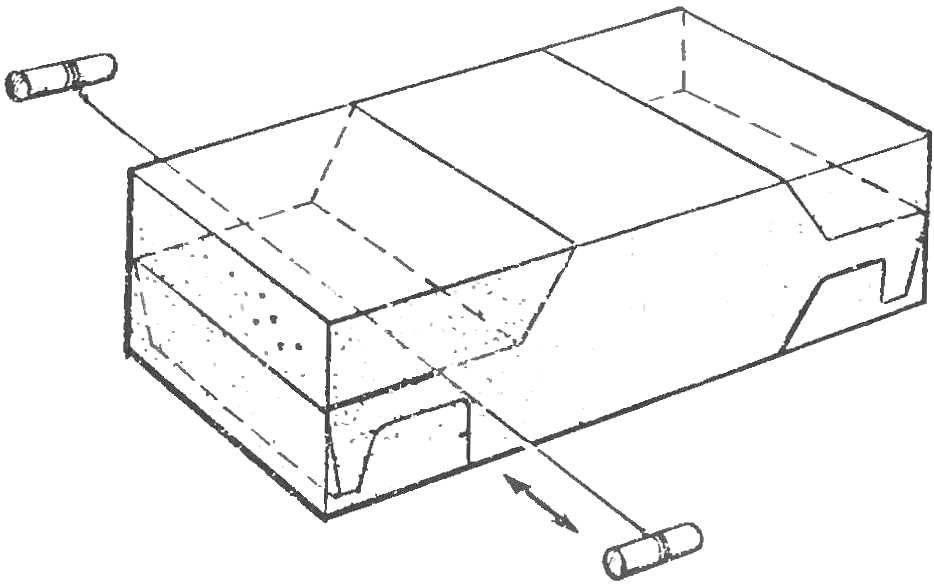
Fig. 5. Cutting foam with steel wire.
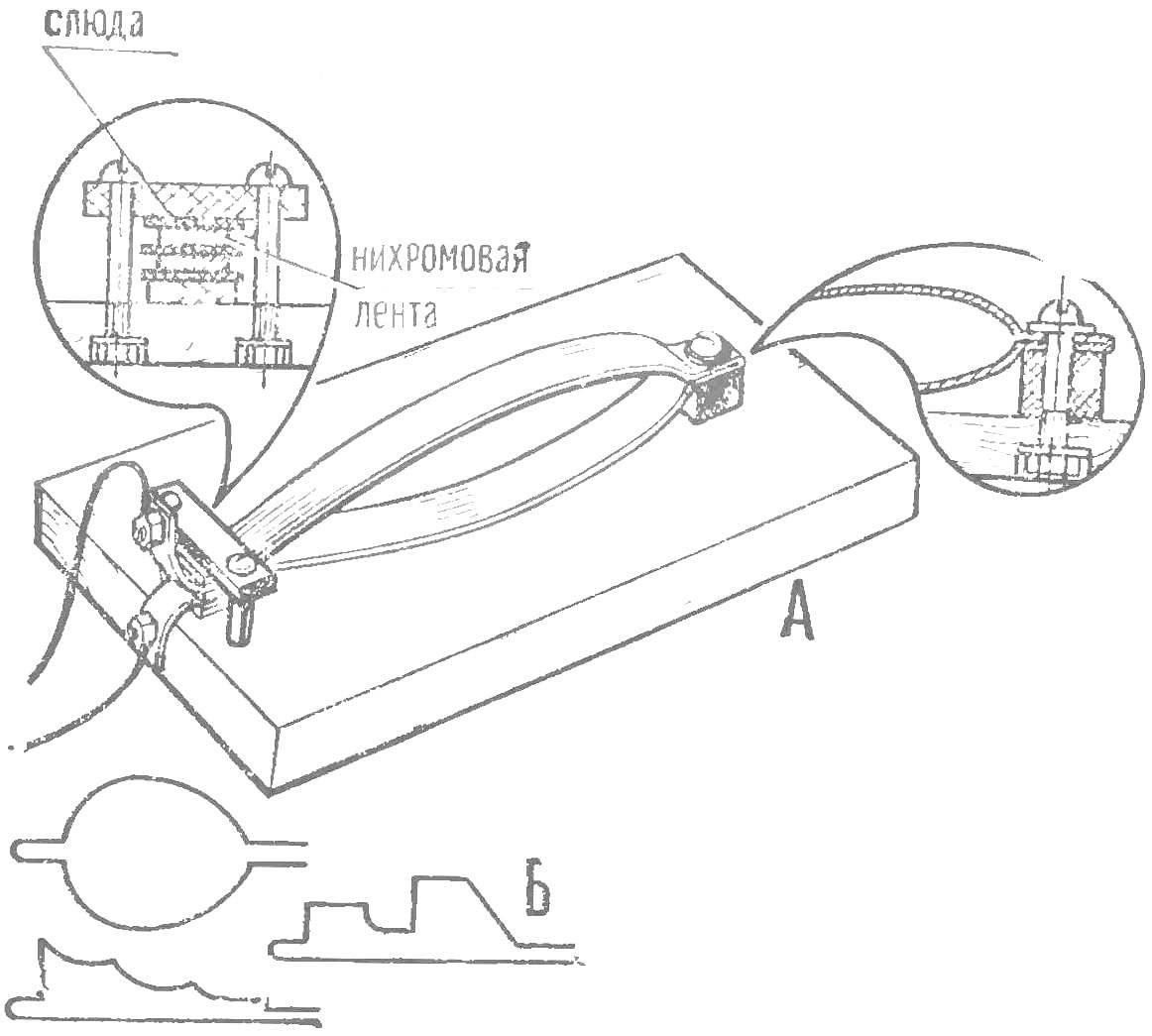
Fig. 6. Method of manufacture of consoles and ribs hot:
A — thermofiller, B — options profiles of working tool thermofisher.
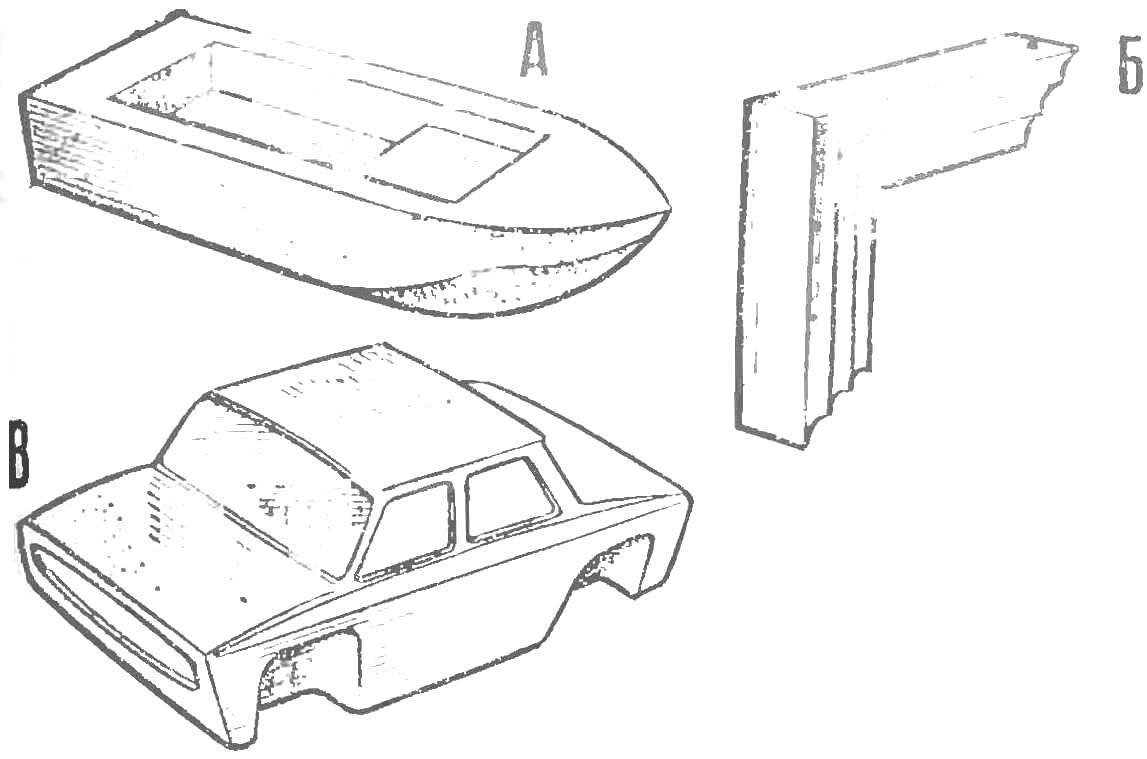
Fig. 7. These parts are made of fiberglass covered with foam.
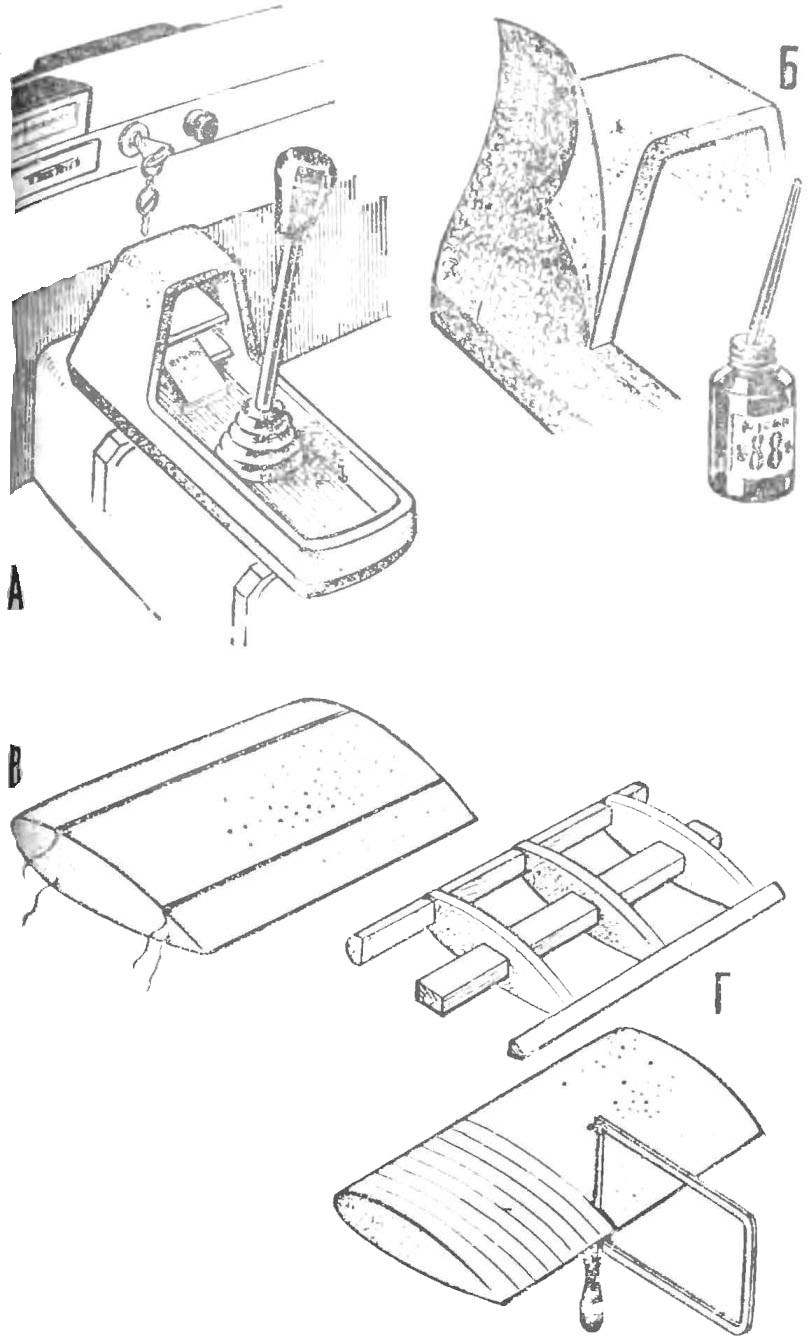
Fig. 8. These “trays” (A) make from foam followed by pasting leatherette (B), In this way it is possible to significantly increase the stiffness of the foam console; G — cutting “innerwar”.
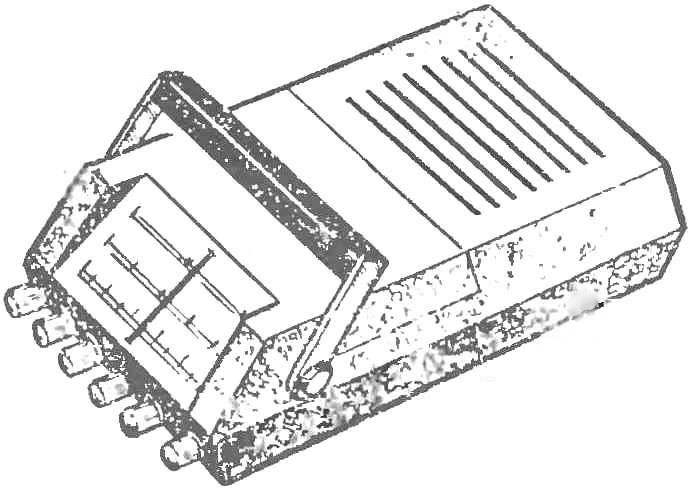
Fig. 9. Foam faux leather — that’s what made the box of the processor.
When the skinny leatherette surfaces with double curvature, account should be taken of the fact that such material good stretches in a diagonal direction. This allows without superfluous cuts and overlays the paste over the surface of a fairly complex shape.
Masking the formed joints you can use the nitro in the appropriate color. It somewhat dissolves the coating of leatherette, and the steps of the joints become almost indistinguishable.
Chemical based foams such as thermoplastic resin. Hence the ability to deform it in a heated state, to bend, to twist. Especially respond well to this procedure, thin sheets. For small plates as a heating device suitable soldering iron.
Painting foam plastics is rather complicated, even if you pick up the paint without dissolving the foam. The fact is that any paint gets into the pores and does not dry out in them for very long. Therefore, before painting the better the surface is treated by epoxy proshkurit. Shpaklevka on the basis of the same epoxy resin, in which the desired proportions are mixed with filling tooth powder, talcum powder, wood powder.
It must be remembered that the use of the polyester resin, as the resin included in the active components dissolve the polystyrene and polyvinyl chloride.