The bed design is offered to the readers of the magazine, outwardly differs nothing from the purchase, but has dignity, and to connect that our furniture industry is still unable lightweight, strong and collapsible. The bed is easy to manufacture, does not require high carpentry skills, there is no metal products, except screws. It consists of the following main parts of the frame-frame, podmatrasnye panel (deck), front and rear backrest and four legs.
In the above drawings are the dimensions of the parts made me beds. However, the proposed design allows to make the bed more or less (in this case their dimensions will change accordingly).
The longitudinal side frames made of boards, they should not have noticeable defects on the outside. As a material well suited pine, spruce, larch. However, larch due to strong colistete is difficult to be processed, but has a very nice texture. At the upper edges of the longitudinal boards from the inside out quarter 20×10 mm under the boardwalk (podmatrasnye panel).
For the legs material can be pine, spruce, larch, oak, beech, maple production Technology of these parts is clear from the drawings Prior to cutting the grooves under the crossmember need to disassemble the legs in pairs so as to ready the beds, they were beveled sides inside, flat outside (sides and backs), we Collected pairs of legs vzaimponimanie.
Stops the legs on the frame are made of plywood, which you can buy in hardware stores (in the form of kitchen cutting boards) or glue from thin sheets (to desired thickness).
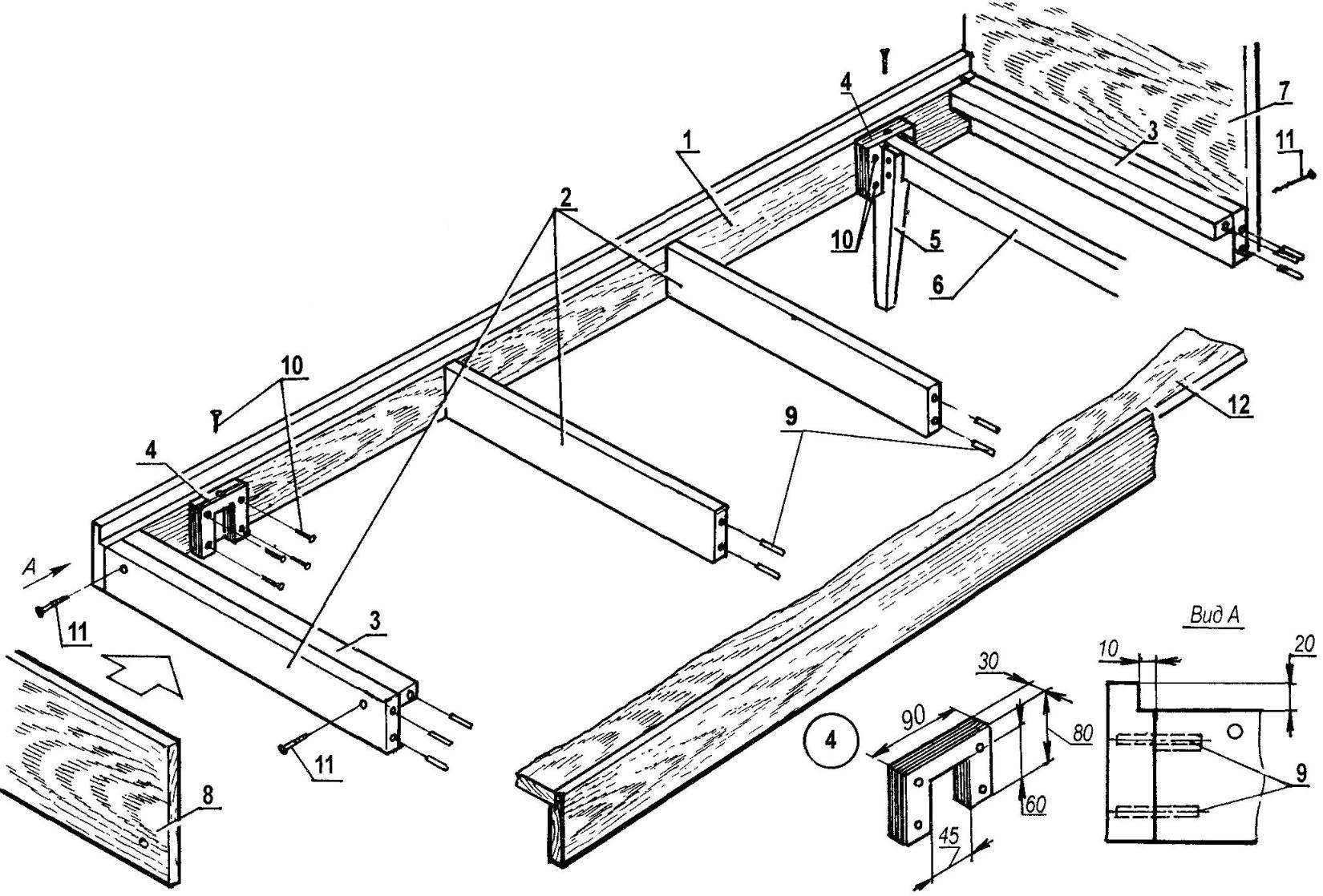
Fig. 1. Portable bed:
1 — side panel frame (Board 1900x100x20, 2 PCs), 2 — frame crossbars (Board 700x80x20, 4 units), 3 — pole-gain (rake 70x40x20, 2 PCs), 4 — stops of the legs (switching 90x80x30, 4-piece), 5 — foot (blank 330x45x45, 4-piece), 6 — crossbar pairs of legs (700x80x15 rail, 2-piece), 7 — front back (chipboard 745x360x20), 8 — rear backrest (DSP 745x250x20), 9 — panel (50 mm Ø10, 20 piece), 10 — fastening of supports of the legs to the side boards and legs to the cross members (screws 40, 45 mm 36 PCs), 11 — mount backrests (60 to 70 mm screws,4 PCs), 12 — flooring (podmatrasnye panel, plywood, hardboard)
Back — of furniture boards or boards, the latter are selected according to the texture pattern of the Joined edges of boards well prifugovyvajut to each other and are fastened to the shield on the pins and glue the Assembled billboards to prostragivat and Polish cloth.
For side frame and backrest you can take the Board with defects, but to thanervice them About the technology of veneers will be described below of Course, in the case of CPD they also need to paste (bed in this case will be somewhat heavier) frame Cross-beams — boards any material For the reinforcing slats, it is desirable to take the hardwood Pins are also preferably made of hard wood (oak, beech, maple) flooring (podmatrasnye panel), you can use plywood or hardboard (MDF) Flooring can be solid or composite.
Some practical tips from my experience making the bed.
In order to accurately drill the holes for the pins, it is desirable to collect the pattern conductor according to figure 4 do Not take the time which will spend for its production, it will be compensated during Assembly.
When drilling holes pattern superimposed side bounded by four strips, on the end of the cross Board, and the reverse side to the inner side of the longitudinal boards (along the lines of markup) to control the hole depth on the drill bit it is desirable to put a restrictor in the form of a tube (rubber, vinyl chloride or reel of tape).
The holes for the pins should be such that the round ship was entered by hand with force, If too large a hole, the peg will not hold, if too small can crack the Board When assembling the frame must be greased with glue Nagel, holes and the abutting surface of the Pair of legs going on the screws and glue.
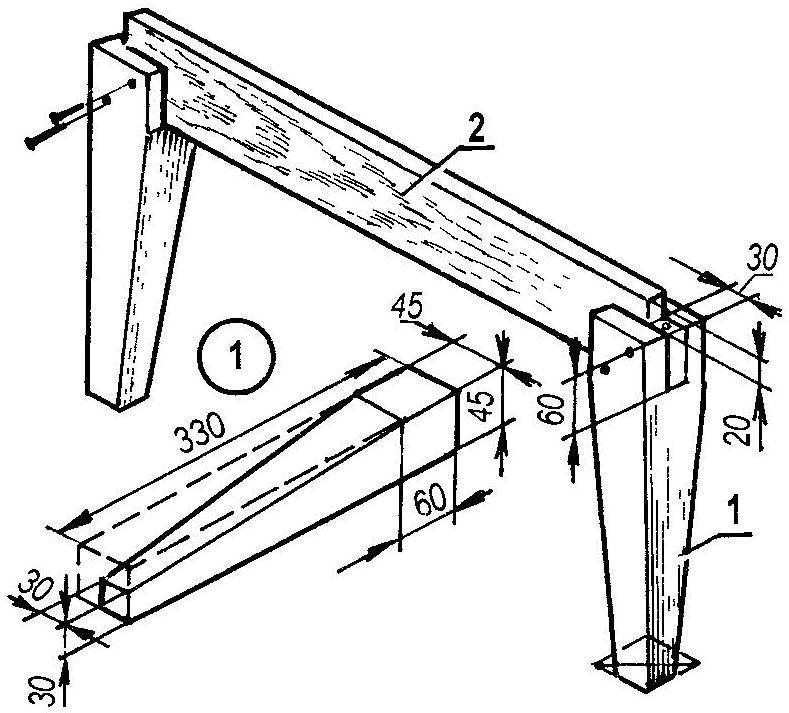
Fig. 2. Legs:
1 — legs, 2 — crossmember

Fig. 3. Option collapsible brackets:
1 — leg, 2 — legs emphasis, 3 — wedge, 4 — bolt 5 — nut
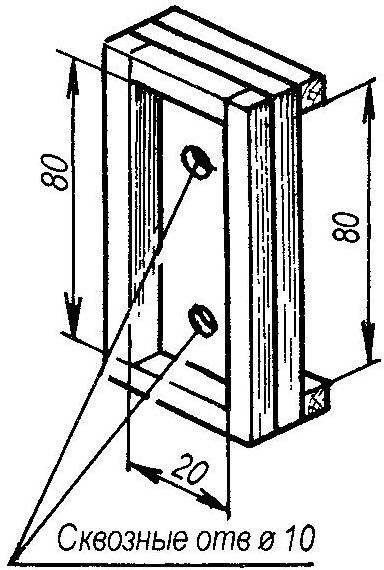
Fig. 4. Template-conductor
For disassembly of the bed while preparing it for transportation or storage, the blocks of the legs are placed inside the frame, the Upper ends of the legs still in the manufacture must be customized so as to fit into grooves of thrust with a slight interference fit of the Inserted legs are fixed from falling out by screws (see figure 2) figure 3 shows another variant of the focus, where the legs are clamped by means of the wedge.
A few words about the use of technology of PVA glue, which, as I have seen, not all know the Glue is applied on the surfaces a thin equal layer and aged for 10 minutes Then fluff wet place another thin layer of glue, the parts connected and after 5 minutes, compressed with the help of clamps, a rubber strap or cargo Three or four hour aging at room temperature is enough to glued parts to work on.
The technology of veneer of small surfaces (backrest, side Board) with the use of PVA glue is quite simple and available at home as it does not require long exposure under pressure a thin layer of Adhesive is applied to faneruemuju surface and pre-customized strip of veneer At the same shutter speed should be at least 15 — 20 minutes Then strips of veneer superimposed on the intended place and prokleivayutsya a hot iron for 15 — 20 seconds Further drying is not required.
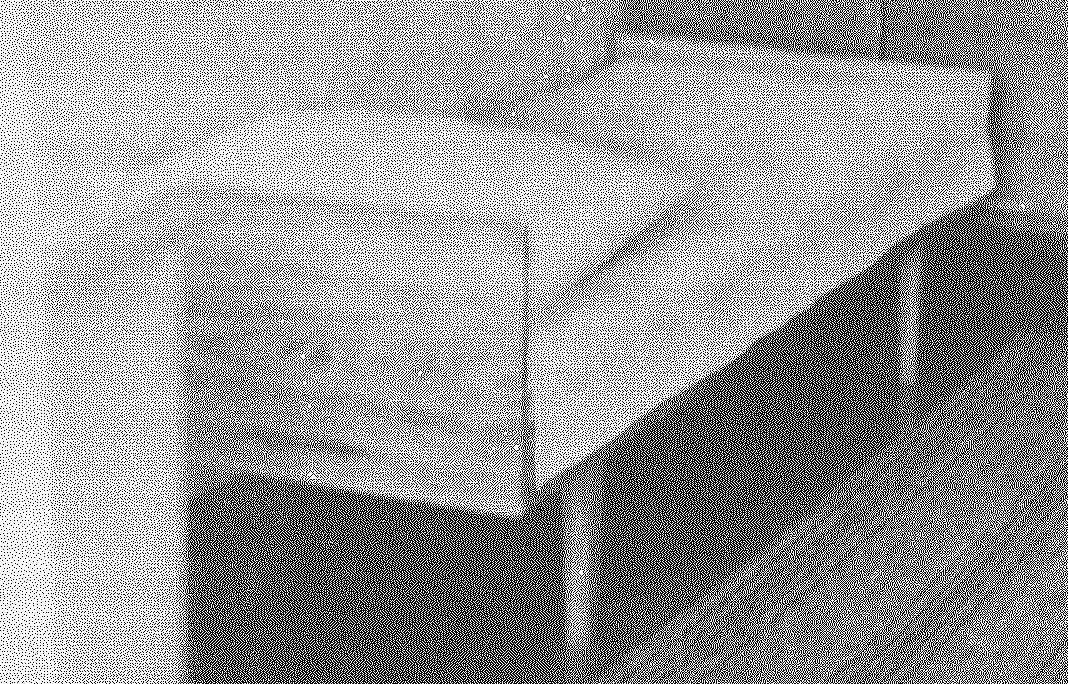
Bed assembled
And finally, varnish To obtain high-quality coating to withstand two conditions are smooth, well polished and cleaned of dust surface and at least three coats of varnish with intermediate drying and the obligatory sanding of the previous layer of fine waterproof sandpaper (pumice) is a Well varnished surface beauty is not inferior to polished, but it looks livelier in addition, old, dull varnish is easy to resume, unlike polishing which will not recover.
As the mattress I used two sheets of foam rubber 40 mm thick, lined with cloth to Cut the foam very well heated with a knife under a ruler.
V. VELMA, Dneprodzerzhinsk, Dnipropetrovsk region.