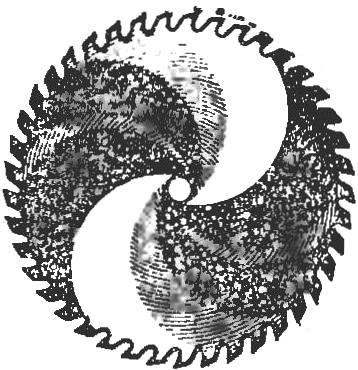
For the fabrication of this machine required single-phase electric motor with capacity of 150-200 8T, making 2500 — 3000 rpm, AC electric motor, which combines two of the three phases using the “paper” capacitor 20-40 MF, designed for a voltage of 500 — 600 V. the Reverse of the motor is carried out by phase switching.
The design of the circular saw shown in figures 1 and 2, designed for the use of the electric motor with output shaft on both sides of the body.
Ka loom set circular saw, and in their absence it is possible to use a disc cutter — Ø 75-150 mm and a thickness of 0.8—1.5 mm.
The lathe bed is made from solid bars of wood in front of section of 30×30 mm and going to the spike on the glue. Two lateral walls, cut out of plywood with a thickness of 4-5 mm:<Leena in selected bars pile. The other two are retractable, and one of them has a gap under the motor shaft.
To the lower frame of the frame is attached to the base thickness of 10 mm. On it with the help of bolts and nuts installed on the motor.
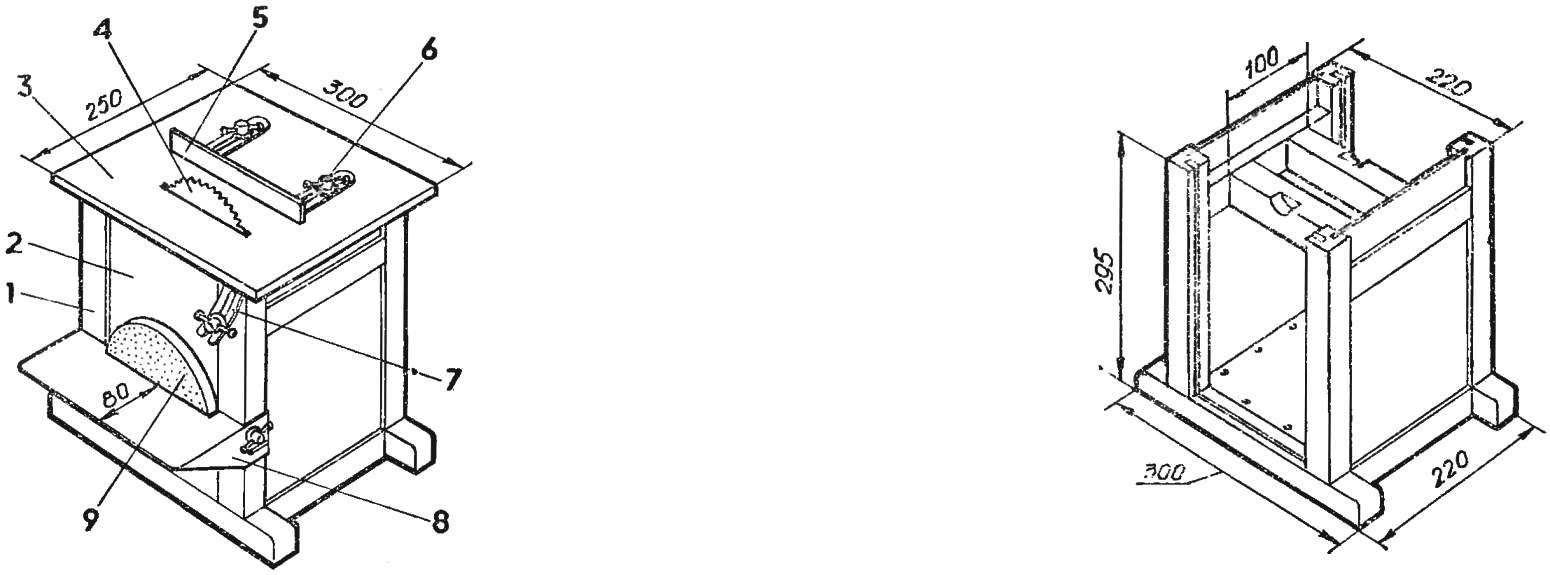
Fig. 1. General view of circular saws and frame:
1 — bed, 2 — sliding wall (plywood), 3 — table (plywood), 4 — circular saw or milling cutter Ø 120 — 150 mm, 5 — the guide ruler (steel), 6 — screw-lock washer 7 — track (steel) 8 — bracket (steel), 9 — in grinding wheel.
The dimensions of the frame are determined by the dimensions of the motor. One end of the shaft should protrude for nozzles abrasive or polishing wheel.
The top connecting bars of the frame serve as the basis for the shaft of the saw. In the places of their installation hollowed out by the nest to a depth of 5–6 mm. the Bearings are radial, homogeneous, with an internal diameter of 12-15 mm and max 40 mm; mounted brackets from steel sheet of thickness 2— 3 mm.
Roller, pulley, step washer under the cutter, and nuts machined from steel. The shaft journal fitted to the internal diameter of the bearings.
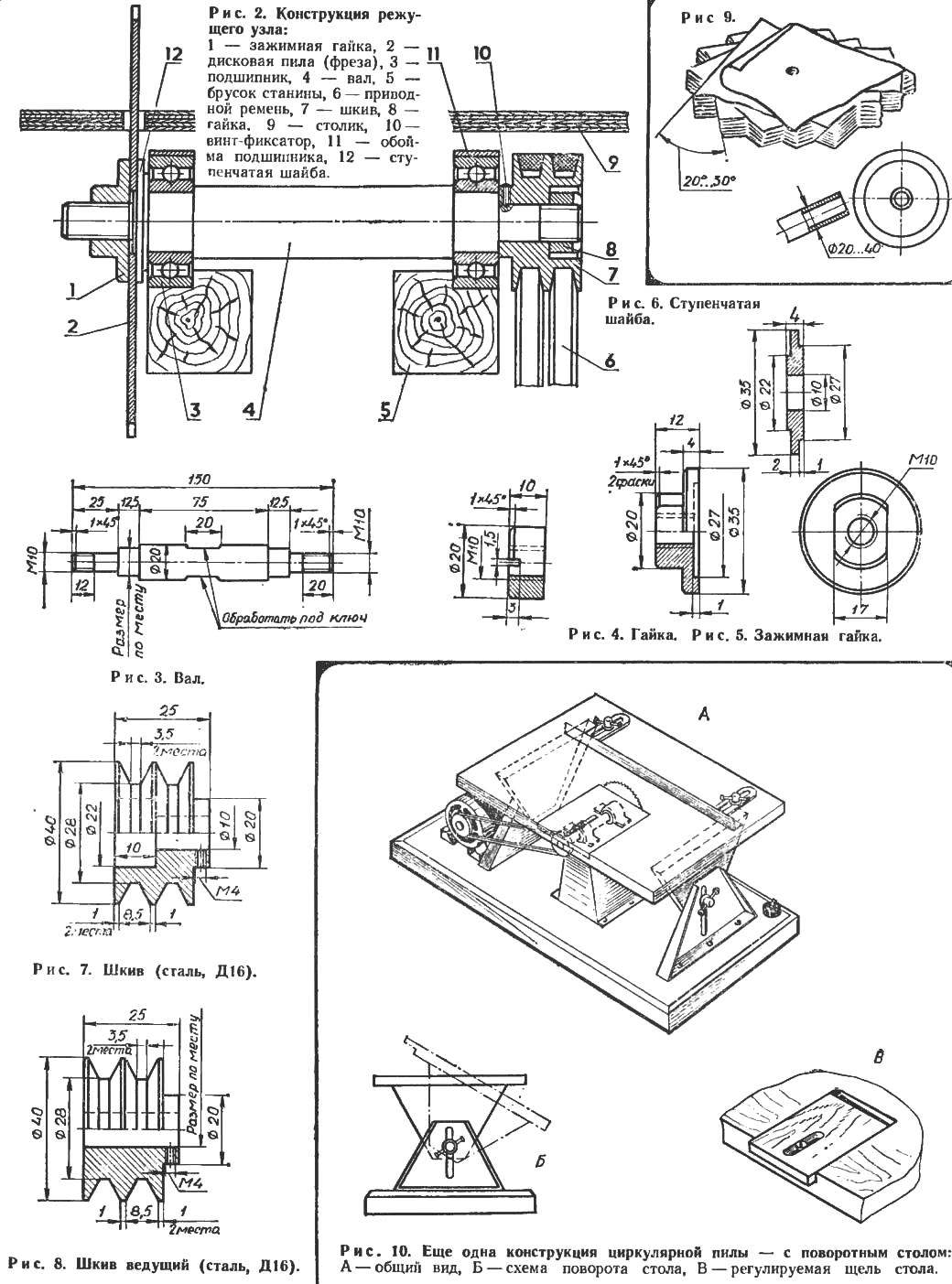
The washers are made of two flange under the hole in the cutters of Ø 22 and 27 mm, or the diameter of the inner hole of the saw blade. This design allows you to use one washer for different cutters.
The pulley is mounted on the motor shaft with the lock screw M4.
For the manufacture of rails on the table of a circular saw is secured by two clamping screws mobile guide line.
Height adjustment of output circular saw blade for cutting through the piles and spikes carried by the lifting table. The latter is made of plywood thickness 6-8 mm, plastic, or sheet metal with a thickness of 4-5 mm. One side of the table is attached to the uprights of the frame on hinges (up to 30 mm) other supported arcs with slots that are skipped two locking screws M5 with washers.
Between the pulleys circular saws and electric motor drive belts stretched. For this you can use a belt of circular cross-section of the actuator foot of the sewing machine.
For removal of sawdust under the saw blade to the frame is attached to the trough, bent out of sheet metal. In the mast output chute in a plywood wall with slotted window.
For grinding wood products onto the motor shaft fits over the removable flange, to which is attached by four screws washer plywood glued with coarse sandpaper. The flange washer is fixed on the motor shaft retaining screw.
On the grinding wheel can be processed not only plane, but also parts with outer radius curves.
To the frame by a circular Pipa two screws e, washers mounted removable bracket of sheet steel 2-2,5 mm. He is a lock for sanding details. In the place of installation of the legs of the bracket cut and mounted with screws to the frame strips, each of which has a guide pin, preventing rotation of the bracket.
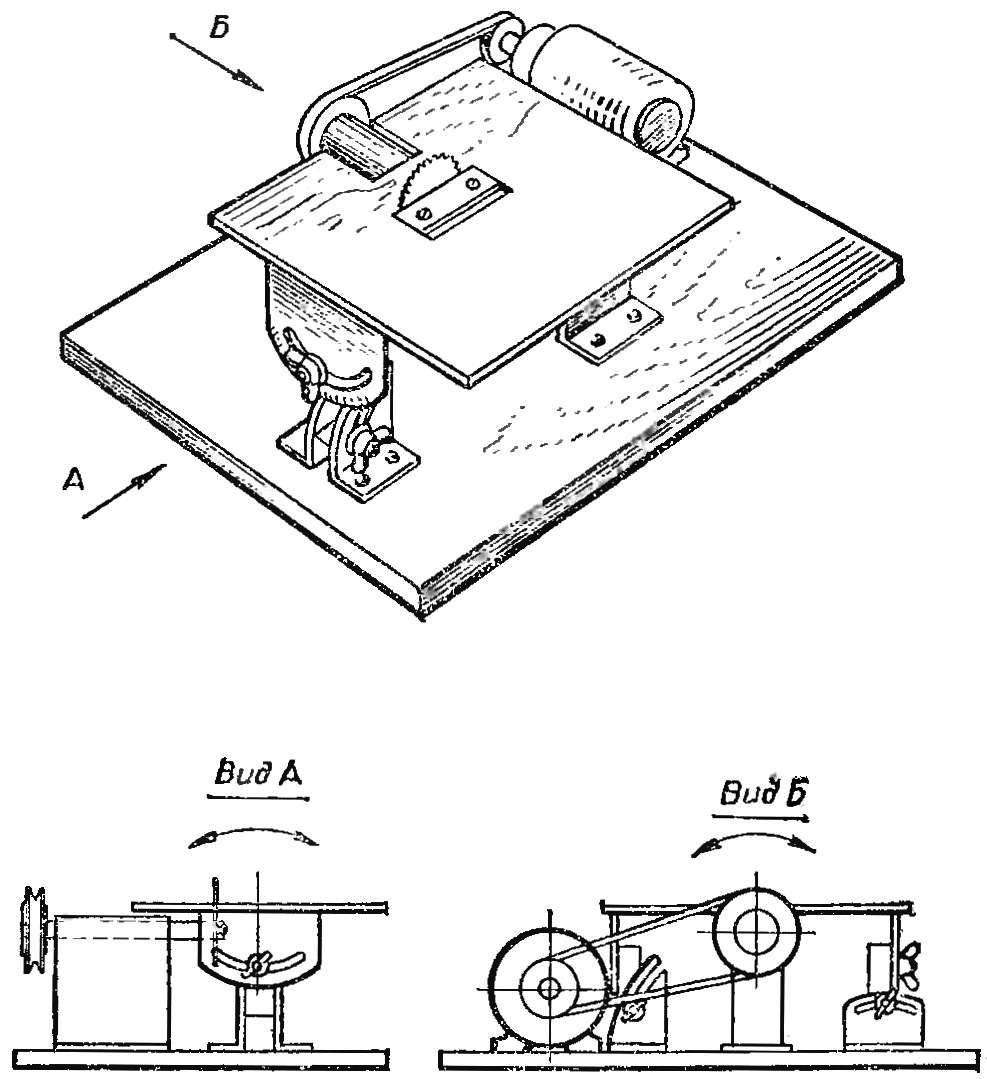
Fig. 11. This table circular saw can be rotated in two planes.
When the polishing is grinding and polishing the washers is placed a circle on nesdca. Nozzle with the polishing circle fits on the shaft of the electric motor and fixed with M4 screw, the Diameter of polishing wheel for the engine at 2500 — 3000 rpm is 100 — 150 mm.
Polishing wheels are made from individual square pieces of calico or other cotton fabrics, stacked one upon the other, as shown in figure 9. The thread direction of each subsequent layer should not coincide.
New buff wear on the motor shaft and including a motor, a pipe line its surface (Fig. 9). Separate the ends of the strands are separated, and the other razlohmachivayutsya around the circumference. The circle is applied polishing paste and start polishing. In order to avoid accidents polished parts can not be hold in hands. They should be firmly strengthened in the mandrel-holders, exposing only the polished surface.
Installing on the shaft of the electric motor of a small emery wheel, it is possible to sharpen tools and grind metal parts.
If the motor has only one end of the output shaft, the buff is put in place of the saw blade. The table in this case do that; removable.
A. KOCHERGIN, A. EFIMOV