“I read in Modelist-Konstruktor about the continuation of the “Small Mechanization” competition and decided to take part. I offer a simple and compact micro-mill. Its dimensions can be judged from the photo: the entire construction fits in the palm of my hand. It’s a universal device — designed for producing both coarse and fine corn flour, grinding various grain waste, and preparing compound feed for livestock and poultry in a private household.
Any hobbyist with experience on a lathe and drill press can make it.
The working components of the mechanism are a rotor and a stator with ribbed surfaces. The rotor, driven by a 180-watt electric motor, rotates inside the stator and performs the function of millstones.
The general layout is as follows: a steel plate base (6–8 mm thick) supports the stator (the fixed working part) and a washing machine motor. Both units are mounted using 25×25×4 mm angle brackets. The stator can be adjusted transversely relative to the rotor’s axis, while the motor can be adjusted longitudinally. These adjustments are built into the mounting assemblies. The motor shaft is connected to the rotor shaft with a coupling on prismatic keys. The rotor shaft, with a flange for rotor mounting, is installed in the stator on a #203 bearing. On the motor side, the bearing is covered by a cap made from 3.5 mm steel plate. A movable rotor is mounted on the Ø 65 mm shaft flange with three M6 bolts. I made two versions: a heavy and a light one, allowing for grind quality control — the heavier the rotor, the finer the result, and vice versa.
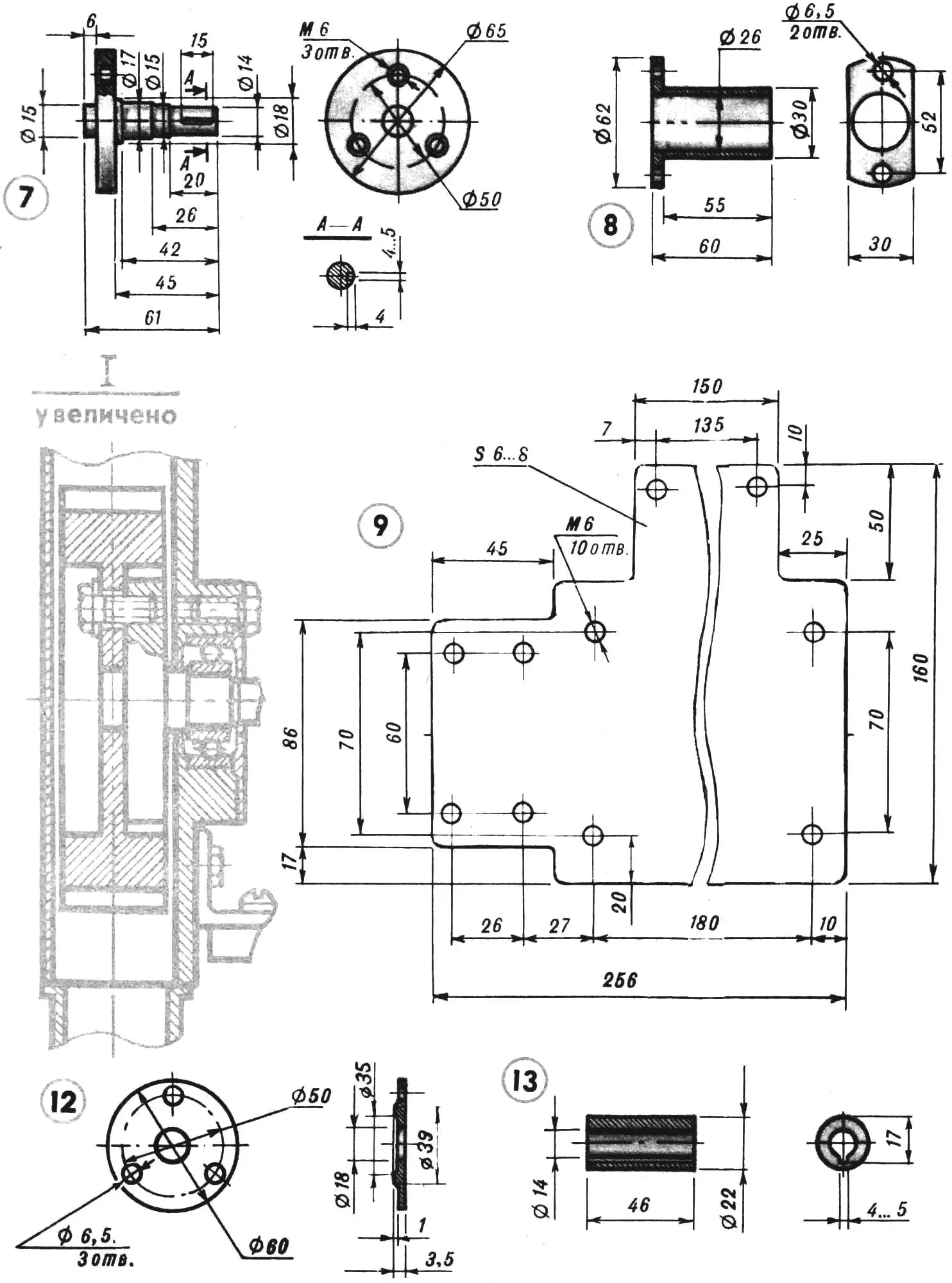
1 — feed hopper, 2 — M6 bolt, 3 — intermediate plate, 4 — stator, 5 — stator cover, 6 — rotor, 7 — rotor shaft with flange, 8 — discharge pipe, 9 — base plate, 10 — stator bracket, 11 — motor mounting brackets, 12 — bearing cover, 13 — coupling, 14 — plugs, 15, 17 — studs, 16 — electric motor, 18 — handle, 19 — handle bracket, 20 — safety cover, 21 — bearing #203.
The ribbed rotor is made as follows. On the flat end of a cylindrical steel blank, mark a pitch circle of Ø 104.5 mm. Equidistant hole centers are marked on the circle. Then drill Ø 10 mm holes at the marked spots. Continue machining on a lathe: turn the outer surface to match the pitch circle and bore the center to a depth of 10 mm. Flip the blank and bore the opposite side in the lathe. Finally, drill the central hole for the Ø 15 mm shaft and three Ø 6.5 mm mounting holes. The heavy rotor is complete. To make a lighter version, repeat the process and drill additional holes in the working surface on a drill press to reduce weight.
The most complex part is the stator. Like the rotor, it requires lathe and drill work. On a steel blank (Ø 154 mm, 43 mm thick), mark a pitch circle indicating the chamber size and the hole centers that form the ribbed surface. Outline the top and bottom windows. Carefully mark and drill the holes (depth 28 mm) according to the drawing. Then bore the central working chamber hole on the lathe and flip the part to machine the seat for bearing #203. Drill holes for the intermediate plate, pipe, bearing cap, and stator mounts, then attach the stator to the base plate.
The rotor’s working chamber is covered from the outside with a 1.5 mm sheet steel cap. The feed hopper, mounted through the intermediate plate to the stator’s upper window, is funnel-shaped and made from 1 mm sheet steel. I used four bolted plates, but other designs are possible. The stator’s bottom window has a discharge pipe where a hose can be attached to guide the milled product into a bag or container.
The electrical components — capacitor, thermal relay, and toggle switch — are mounted on a dielectric plate held by small brackets next to the motor. Before operating the device, adjust the stator position with bolts so that the rotor rotates freely without jamming.
The micromill is placed on a stool or chair, the motor is switched on, and the hopper is filled with grain. The ground product is discharged from the outlet pipe into a container. Practical use has shown the following results: a bucket of corn is milled in 6–7 minutes, and wheat, millet, and buckwheat are processed 1.5 to 2 times faster.
This portable micromill has been in operation for over three years without breakdowns or failures. I believe many rural residents will want to make one for themselves.
A. BAKLANSKY, Kremenchuk, Poltava Region, Ukraine