Universal walk-behind tractor designed by V.N. Arkhipov is simple to manufacture and convenient to use. Use our drawings, and a small metal plow will take on the most labor-intensive work in your suburban area.
As evidenced by the mail, the “Small Mechanization” section is very popular among people whose work is somehow connected with agricultural production. Readers show a special interest in self-propelled mini-tractors – walk-behind tractors. After “M-K” published the description and drawings of “Vyaticha” (see No. 7, 1981), built by engineer S.A. Ilyichev, enthusiasts of agricultural design have been writing and calling the editorial office, asking to continue the conversation on this topic.
Today we are talking about the design proposed by V.N. Arkhipov from Kaluga.
Arkhipov is a participant in the first stage of the review of amateur tractors and walk-behind tractors, held last summer in the Moscow region in Solnechnogorsk as part of the All-Union competition of young scientists and specialists in the development of small mechanization tools (see “M-K”, 1981, No. 10).
The machine is simple and easy to replicate. But its main attractiveness is that it has an original suspension of soil cultivating tools, unusual wheels, and also a luggage carrier (which no walk-behind tractor known so far has).
For five years now, V.N. Arkhipov has entrusted all the cares of cultivating potatoes in his suburban area to his mechanical assistant. With the help of a homemade walk-behind tractor, he plows, harrows, plants and hoes potatoes, digs up tubers, gathers tops, transports the harvest and fertilizers.
The walk-behind tractor is a single-axle two-wheeled self-propelled machine with an engine from a VP-150M scooter. Arkhipov chose this engine because it has forced air cooling of the cylinder head, which is very important: after all, the walk-behind tractor has to work at maximum loads at minimum speeds.
Most of the parts are industrial. Part of the engine suspension, part of the frame (double arch), chains, handles, and control cables are also taken from the scooter.
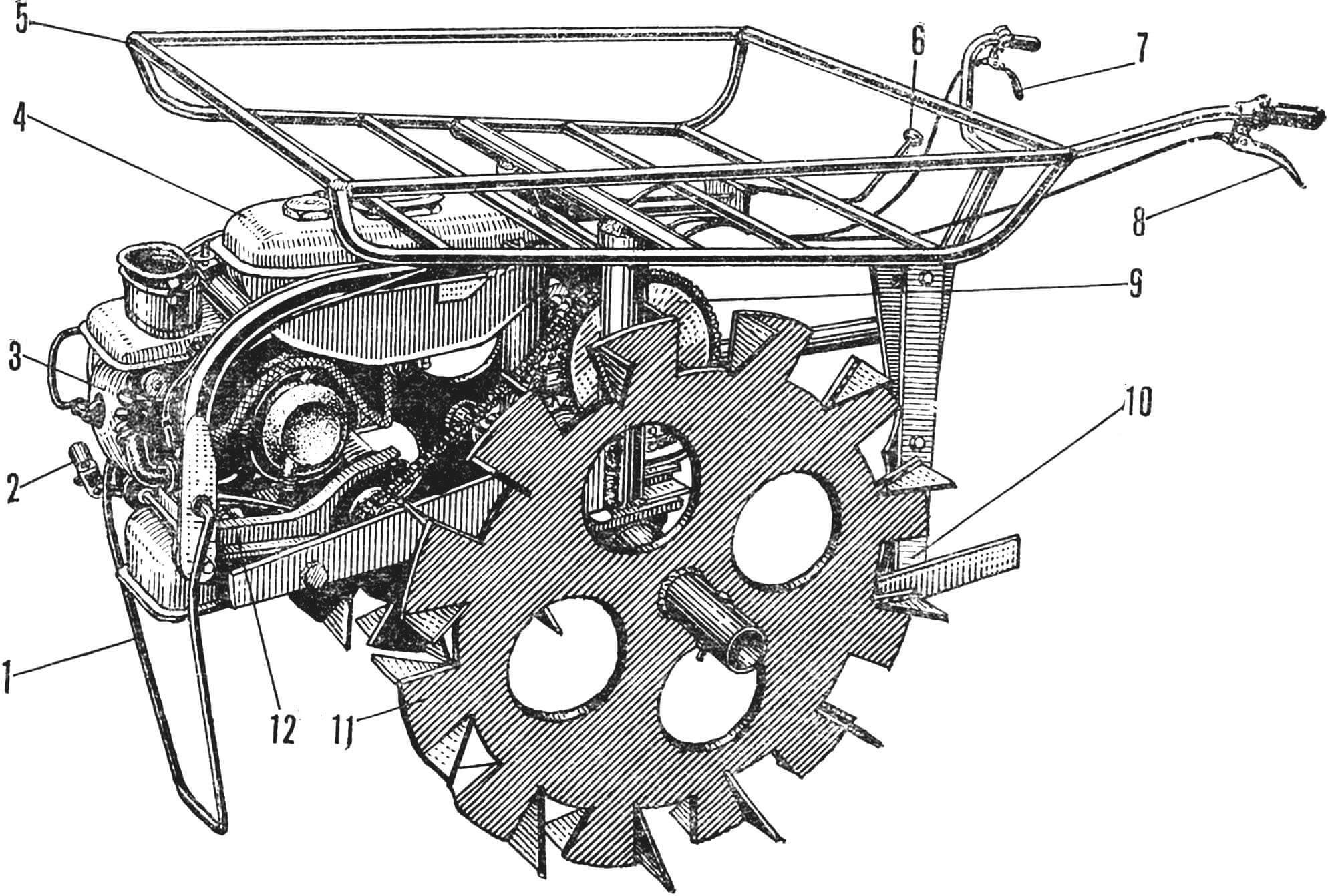
1 — folding support, 2 — kickstarter pedal, 3 — engine, 4 — fuel tank, 5 — luggage carrier, 6 — gear shift lever, 7 — clutch lever, 8 — throttle lever, 9 — secondary shaft sprocket, 10 — plow, 11 — wheel, 12 — engine suspension.
All the rest is made independently. The wheel axle is turned on a lathe. The P-shaped frame is welded from Ø 60 mm pipes. The luggage rack is made of pipes as well. Homemade three hinges of the main and adjusting rods, connecting the walk-behind tractor with the plow and the handlebar. Homemade gear shift mechanism. A steel pipe with an axle is welded to the frame. A rocking lever for tensioning the cables going to the engine gearbox is installed on the axle. The gear shift lever is also a section of a pipe welded to the lever.
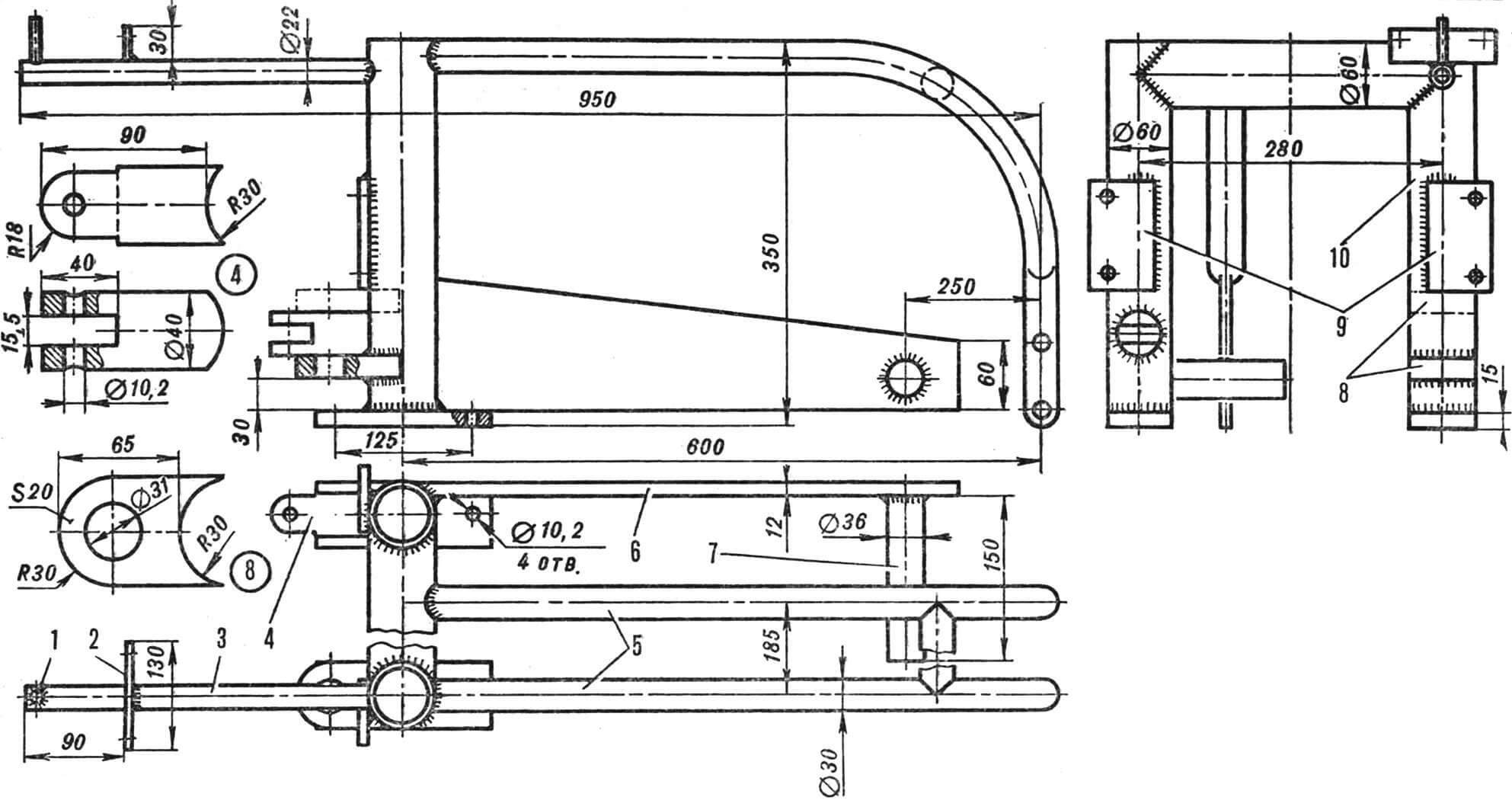
1 — rocker arm axis, 2 — support plate, 3 — pipe, 4 — fork for attaching the adjusting rod, 5 — arc-shaped pipes, 6 — bracket, 7 — engine suspension axis, 8 — unit for attaching the main rod, 9 — platforms for attaching the bearings of the secondary shaft, 10 — P-shaped frame.
The walk-behind tractor uses chains with pitches of 12.7 and 15.9 mm. The number of teeth on the sprockets: engine output shaft – 11, secondary shaft – 60 and 20, axle shaft – 40.
The assembly of the walk-behind tractor is as follows: on the axle shaft, a sprocket is installed (it is welded), housings with bearings, freewheel clutches acting as a differential, wheels, and then the frame. The telescopic rod with the handle and plow is attached to the latter.
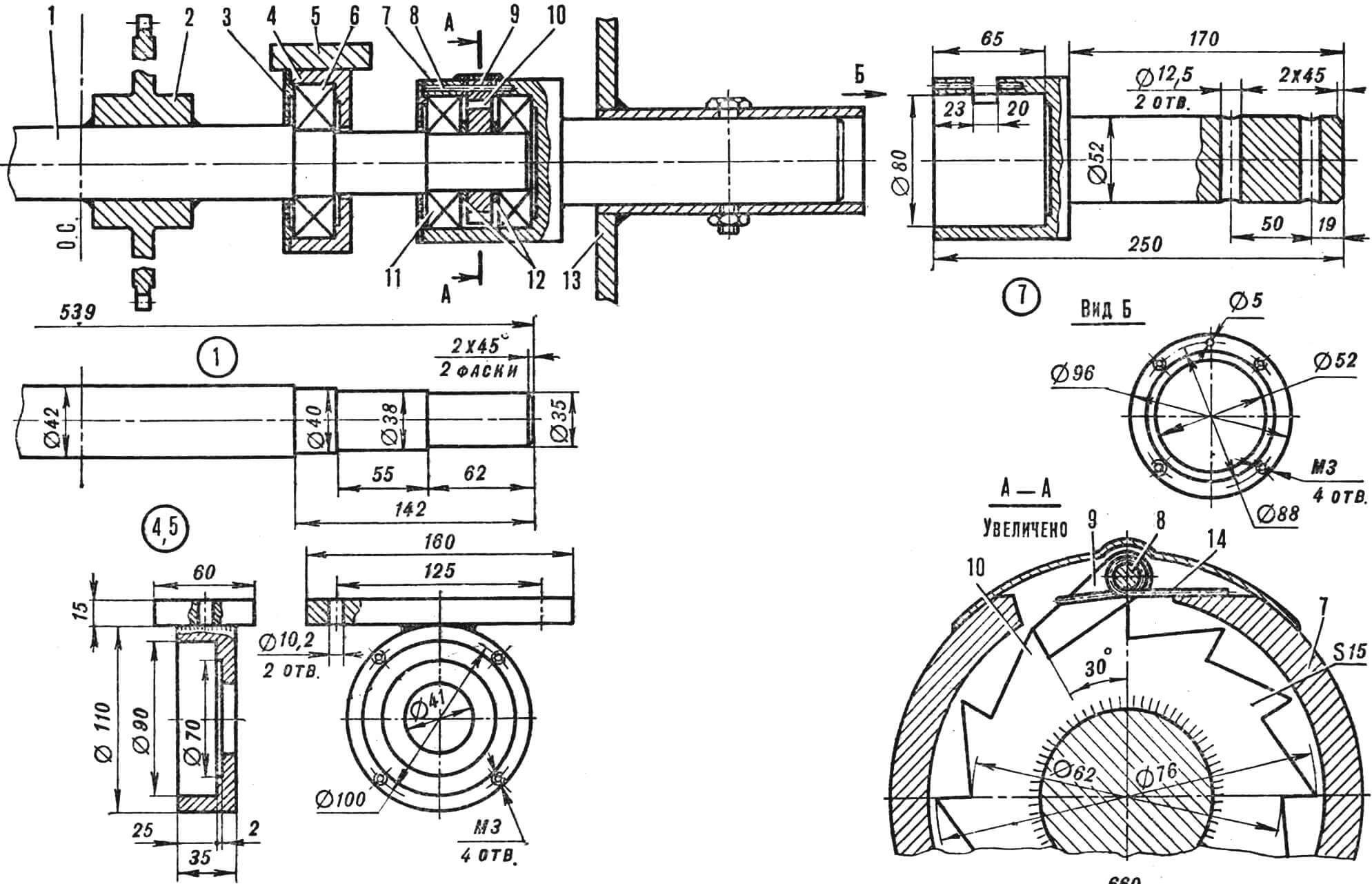
1 — shaft, 2 — sprocket, 3 — cover, 4 — bearing housing, 5 — support platform, 6 — bearing No. 308, 7 — freewheel clutch housing, 8 — dog axis, 9 — dog, 10 — ratchet, 11 — bearing No. 307, 12 — washers, 13 — wheel, 14 — dog spring.
Now about the wheels. Thanks to their special shape, they have better traction with the soil and do not clog with earth. Unlike rubber wheels, these wheels practically do not compact the soil; on the contrary, they loosen it.
Two arc-shaped pipes from the scooter frame connect part of the engine suspension and the frame of the walk-behind tractor. A fuel tank is placed between the pipes.
Next is the engine. A bracket is console-welded to the P-shaped frame on the left, having a transverse steel axle Ø 36 and a length of 150 mm at the end. The engine, together with the suspension, is hung on this axle and attached to the arc-shaped pipes of the frame. The secondary shaft is installed in its place, and the chains are tensioned. Control cables are pulled. Compared to other designs of a similar type, Arkhipov’s walk-behind tractor has several design advantages. Before it, tractors and cultivating tools were rigidly connected, which made turns difficult. Arkhipov came up with a hinged connection that allows “holding” the furrow or changing the direction of movement within small limits without removing the plow from the ground.
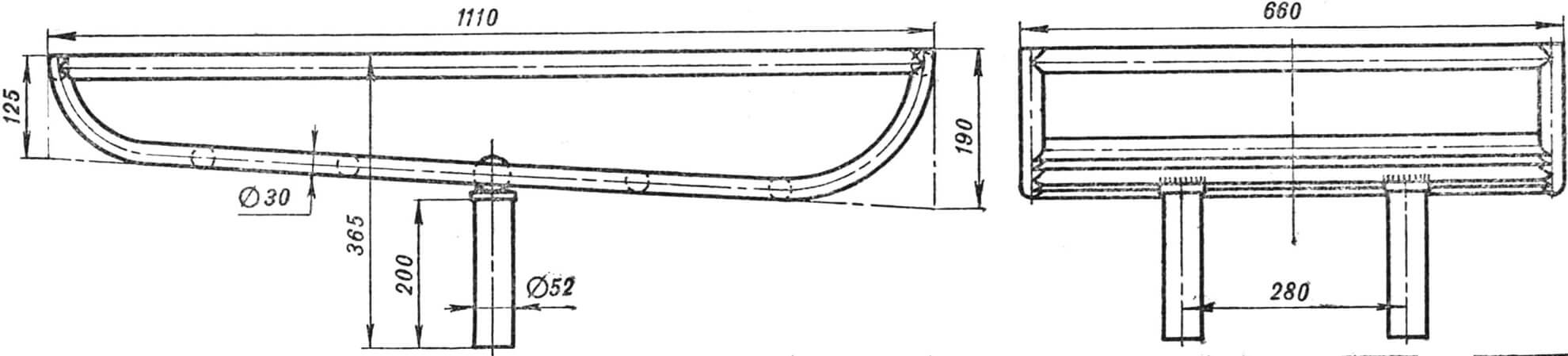
This element provides another advantage – maintaining a constant depth of plowing without applying additional efforts. The necessary plowing depth is maintained not by lifting and lowering the plow but by changing its angle relative to the furrow, which happens automatically: if the plow starts to bury itself, the lifting force created by the field board acts on it; if the plow emerges from the soil, the attack angle increases, and it again sinks into the soil to the specified depth, ensuring stable balance.
During operation, the plow, overcoming the resistance of the soil, often drifts to the side, and the plower working with a rigid structure walk-behind plow has to make considerable efforts to level the furrow. Arkhipov eliminated this inconvenience: the axis of his plow is positioned at some angle to the direction of movement. This position is adjustable by three linkage hinges. The walk-behind tractor is slightly turned to the left during plowing, compensating for the drift.
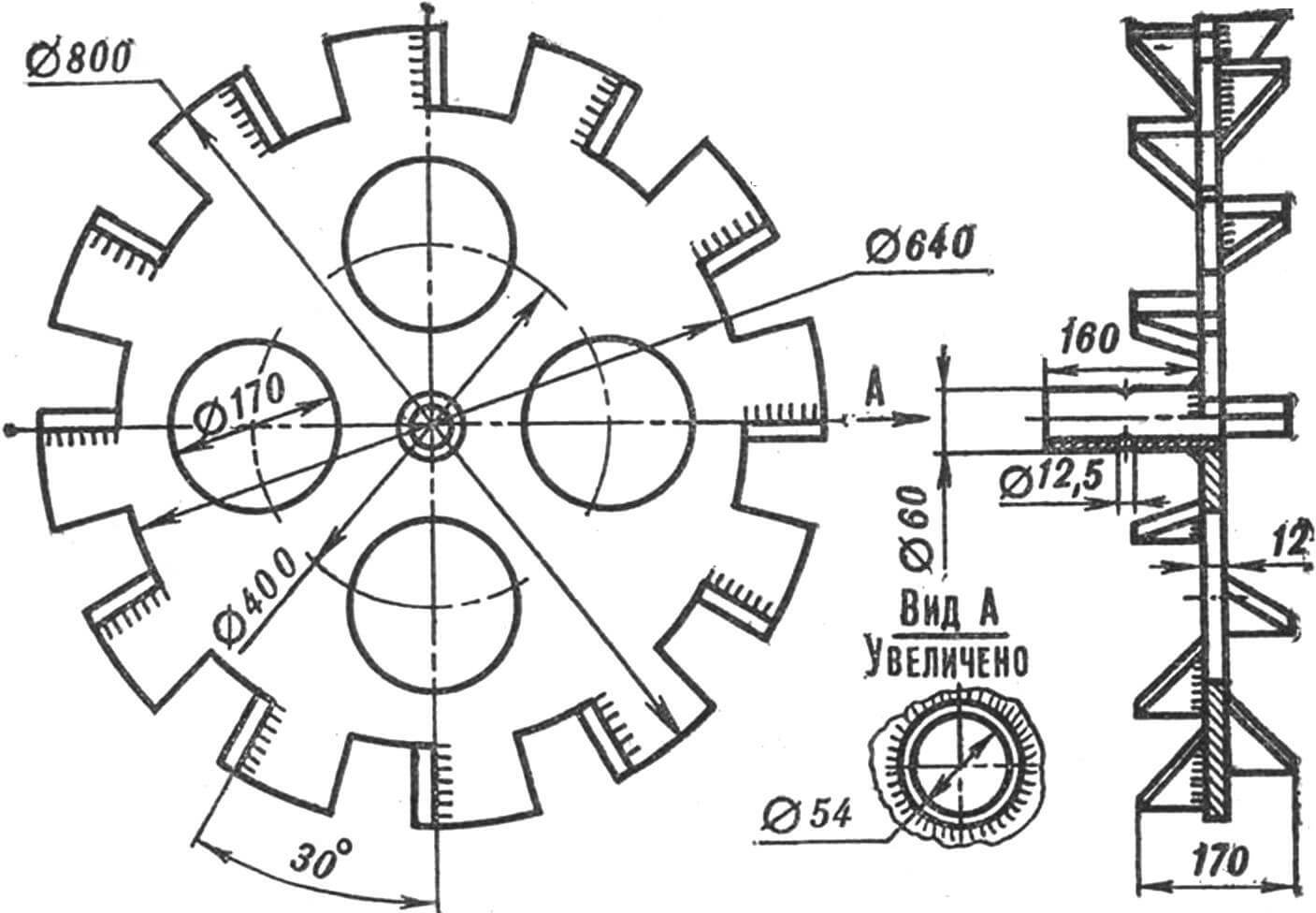
During the first furrow (the most crucial moment), it is necessary to maintain a straight direction manually with the plow itself because the control handles are rigidly connected to it, not to the walk-behind tractor. When they are turned with slight effort, the entire device changes the direction of movement. Suppose you need to turn right. The plower deflects the handles in… the opposite direction. And since the plow cannot move there—it is as if fixed in the ground— the traction, following the handles, turns the walk-behind tractor to the right.
On the second and subsequent furrows, control is simplified because the right wheel follows the furrow like a copy.
The cultivator, harrow, and rake are set by the adjusting rod exactly in the middle of the furrow. They are fastened with the same two bolts as the plow. The brackets of these tools are slightly turned in the vertical plane to compensate for the angle at which the plow was set. The bracket for the harrow is welded vertically in the middle. With such a harrow, the plower can control, lowering one or the other edge as needed, breaking up large clods of soil.
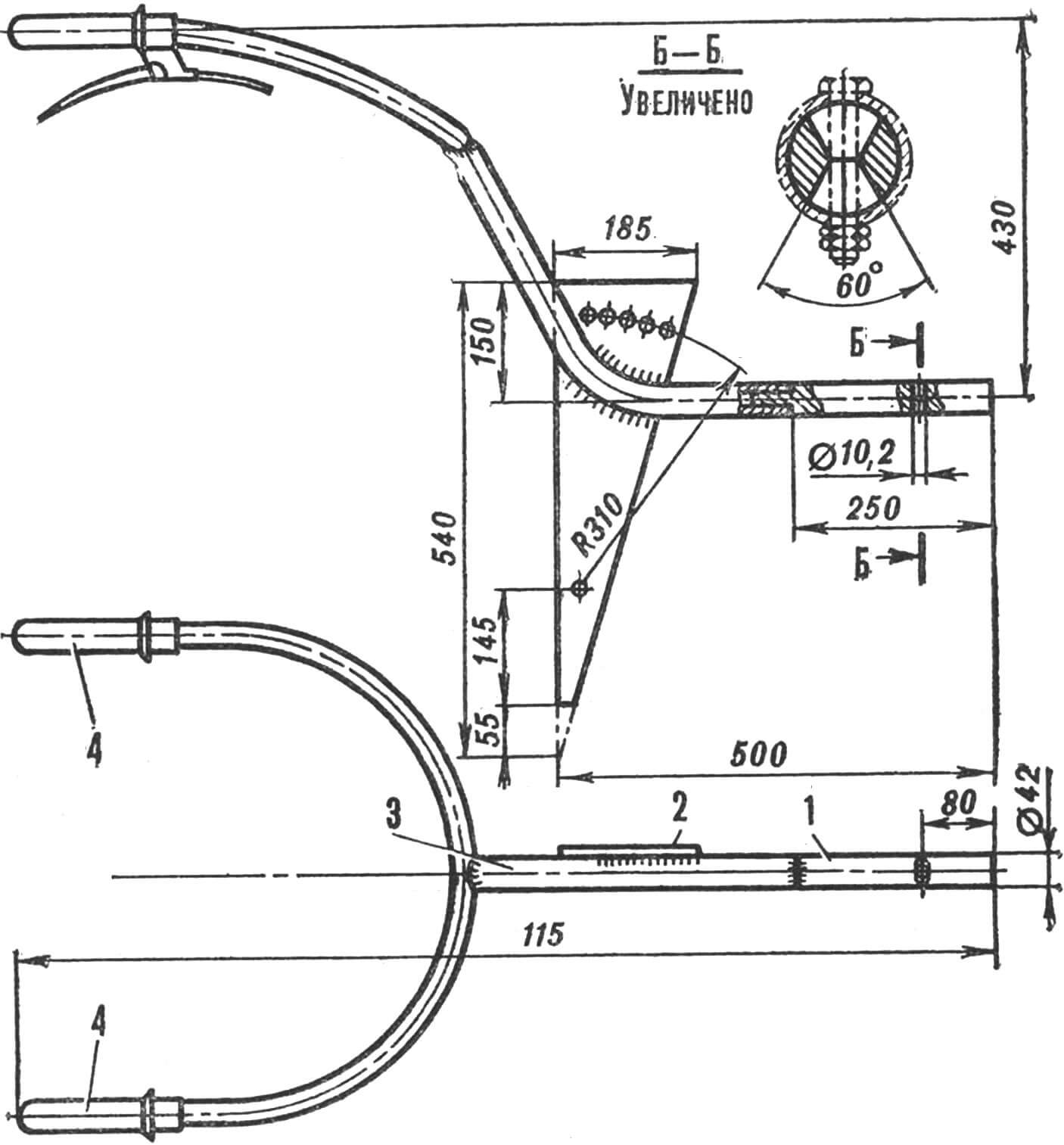
1 — connecting axle, 2 — plank, 3 — pipe, 4 — handles.
On uneven ground, the harrow does not react to different tilts of the walk-behind tractor. (With a rigid connection to it, it copies them, leaving defects.)
For planting potatoes, Arkhipov uses a cultivator with removed blades. Installing it in place of the plow, he makes furrows in the ground and places tubers in them. Then he puts the blades back in place and covers the tubers by letting the cultivator run between the furrows. Sprouted plantings are also hilled in the same way.
With the cultivator, Arkhipov also harvests the crop. The width of capture is adjusted with the blades.
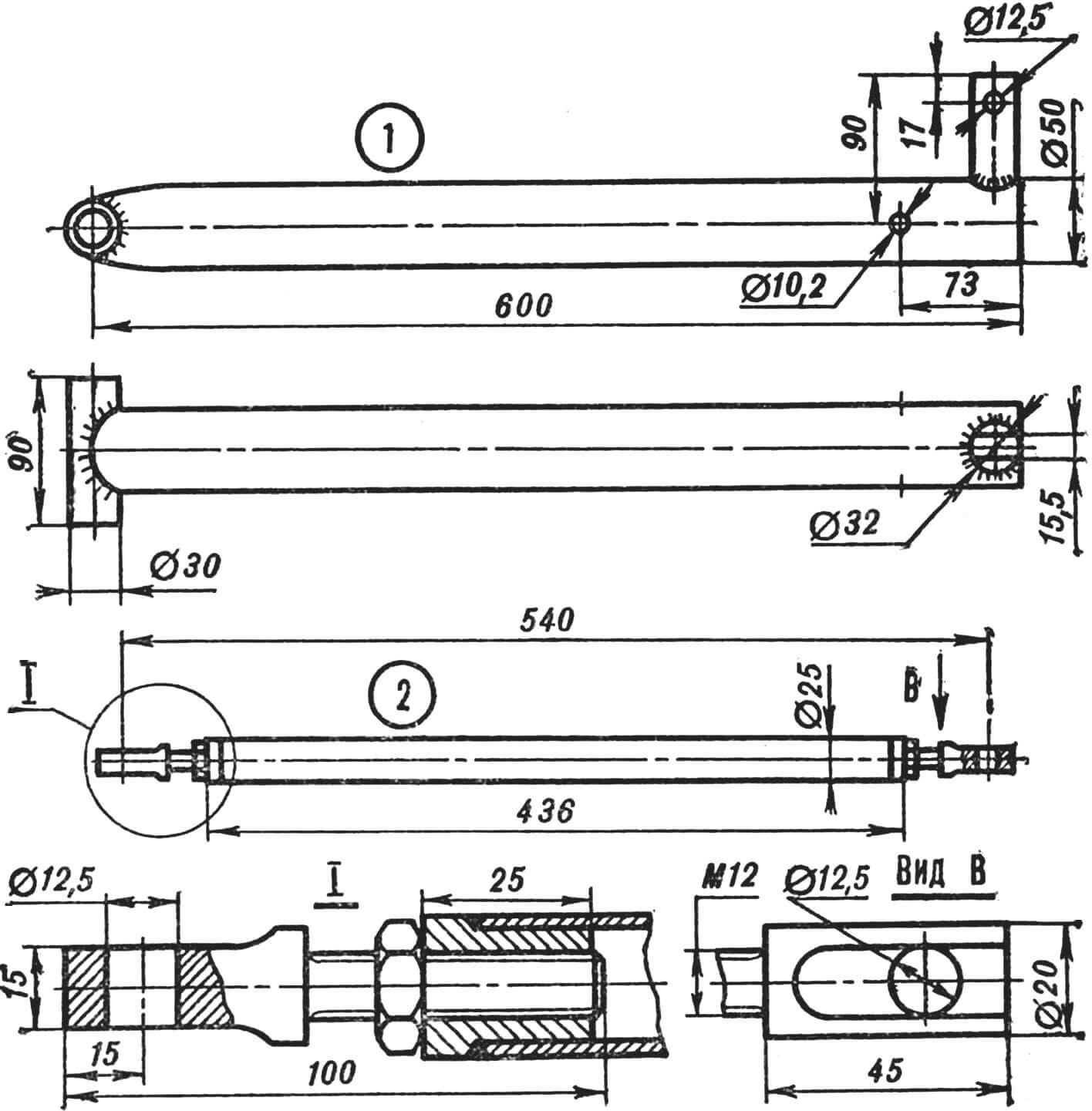
1 — main rod, 2 — adjusting rod.
The remaining stalks after harvesting, as well as any missed potatoes, are removed with a harrow or rakes. By the way, it is convenient to gather mown grass with the rakes.
In addition to agricultural work, Arkhipov’s walk-behind tractor is used, in particular, for snow removal. Only a small bulldozer blade is additionally installed. It is also possible to sweep sidewalks by installing an additional sprocket and a roller with a round brush.
Those interested can receive consultation from V. N. Arkhipov by contacting: 248025, Kaluga, Tarutinskaya Street, 2a, Apt. 1.
Yu. Solyaninov, Kaluga