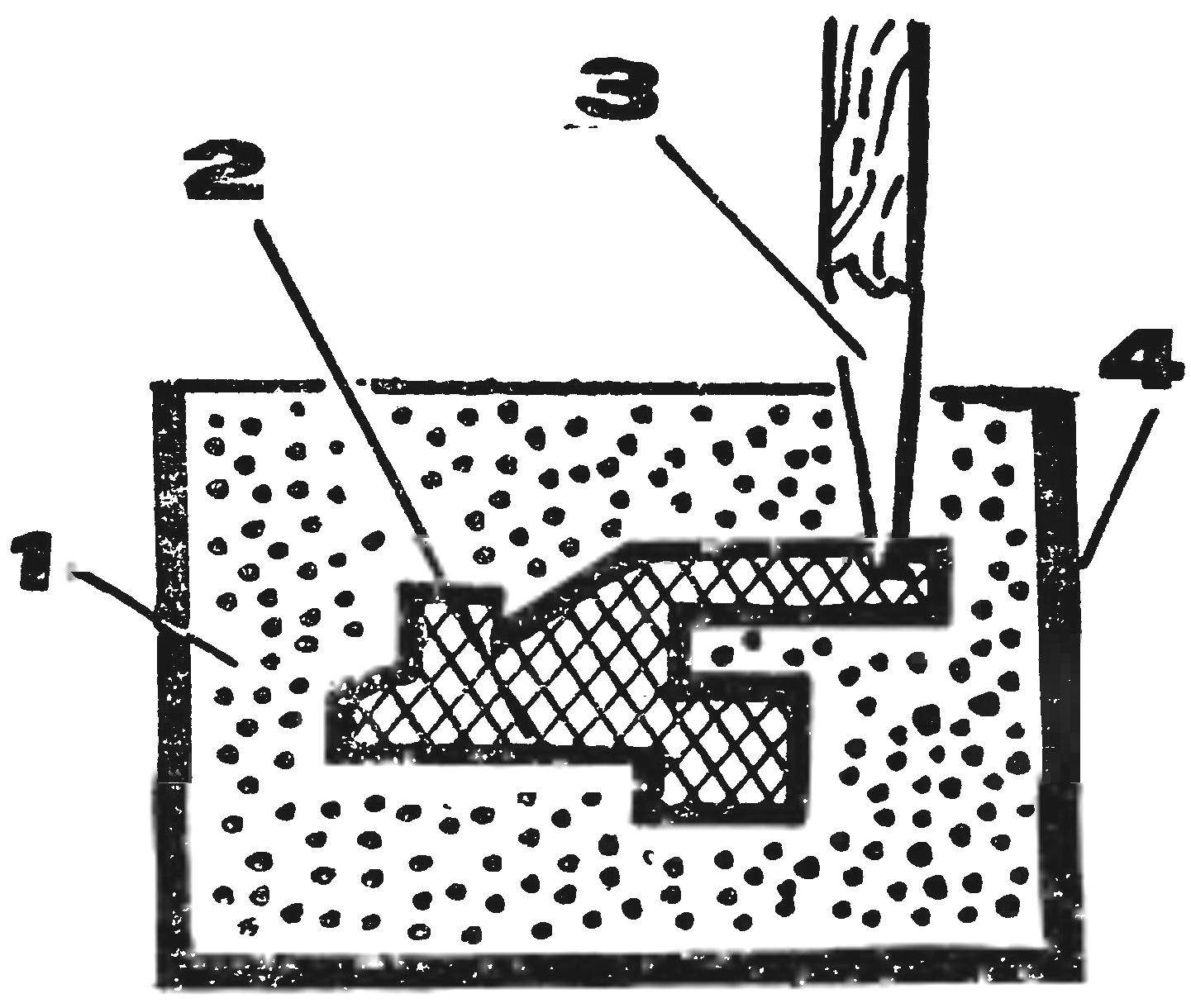
If the part is symmetrical and has a simple configuration, for example an anchor, wheel or a life preserver, a form more convenient to make the folding of the two halves, which can be used repeatedly.
Molding or metal casting patterns pressed into the not yet hardened plaster to a symmetry plane (connector) and allow to harden. The second half of the mold is filled, moisten the bottom part with mild soap and water to facilitate the separation of the halves. The top part of the form needs to have a through hole: Ø 3-4 mm for filling with plastic and the release of excess her during polymerization. Removing the casting model and the folding of the two halves, pull them together with twine or rubber — and the mold is ready.
For the manufacture of parts of complex configuration is needed form, consisting of three and more parts. It is better to use the method used in precision casting — lost wax casting model.
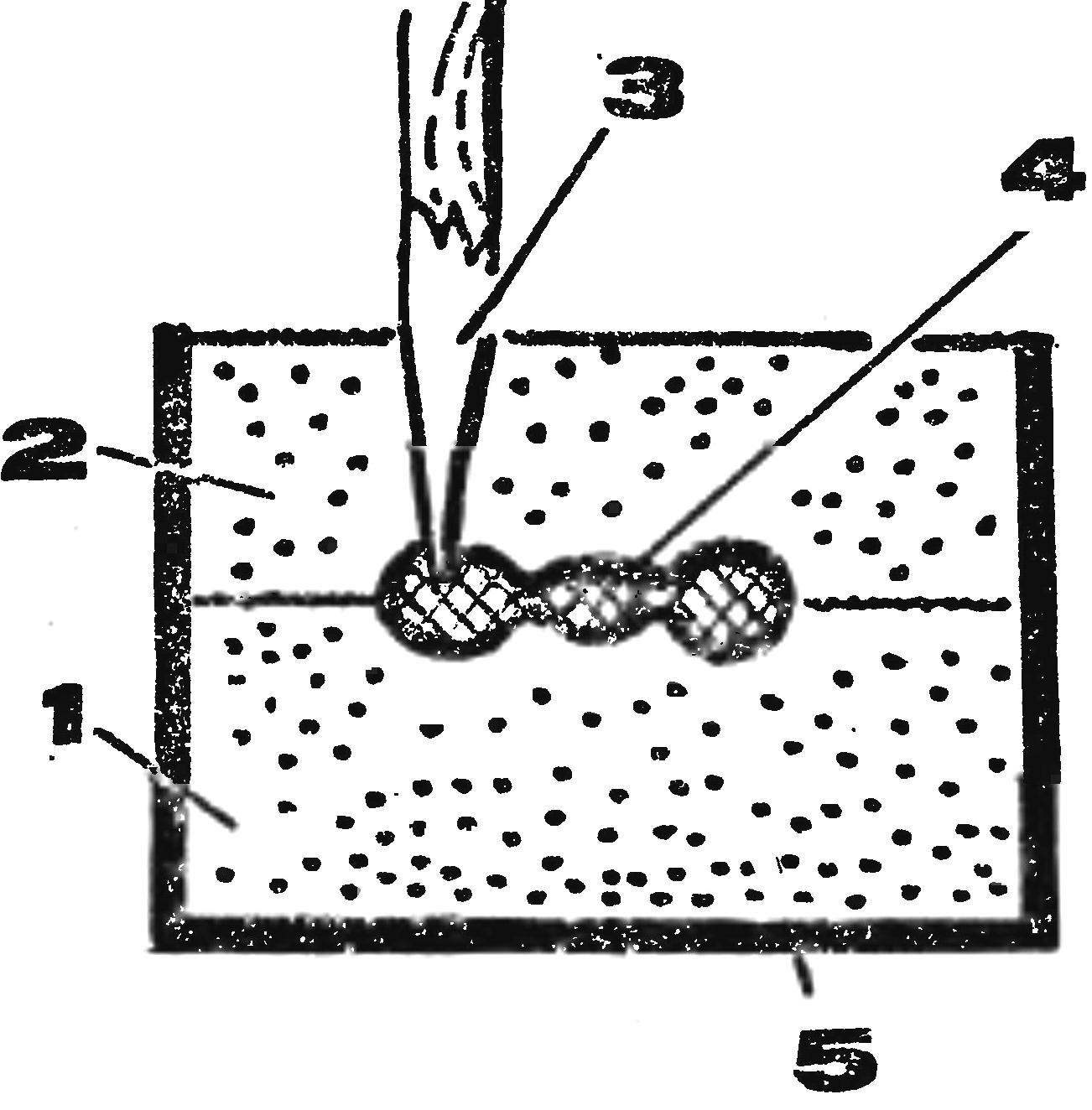
Fig. 1. Portable form:
1 — base; 2 — top half; 3 — mounting rod (tree); 4 — plastic model; 5 — cardboard box.
Form will all-in-one that is disposable. Model to obtain make out of wax, filled with gypsum mortar, with the uppermost part of a cylindrical or conical, extending up hole Ø 3-5 mm— gate. After 30-40 minutes the cured plaster mold is dipped into a bowl of cold water with the sprue upward and boil until complete melting of the casting model. Paraffin, as more light is displaced from the mold with water and floats to the surface. Then, without removing the form, water cooled and with its surface to remove the layer of solidified paraffin. Removal from the mold residue warming should be repeated.
This method obtained in a gypsum cavity, accurately reproducing the shape of the part. If inside the future details of desirable fasteners, it is necessary to embed them in paraffin casting model, so that when melting, they are not shifted. For example, if you want to be in the details of the metal nut, then put it from the protruding bolt and all the gypsum is poured. Then the free end of the bolt will be in the thickness of the plaster and after melting of paraffin will keep the nut in the right place.
When molded form a plastic prepared in a glass container, bringing to the consistency of liquid sour cream. Mix the mass with a glass rod, poured through sprue hole to the form. Polymer preparation and filling in the form is produced without delay, since the mass quickly thickens. At the time of casting, the inside must be moist, otherwise the surface of the finished part will turn out rough and porous.
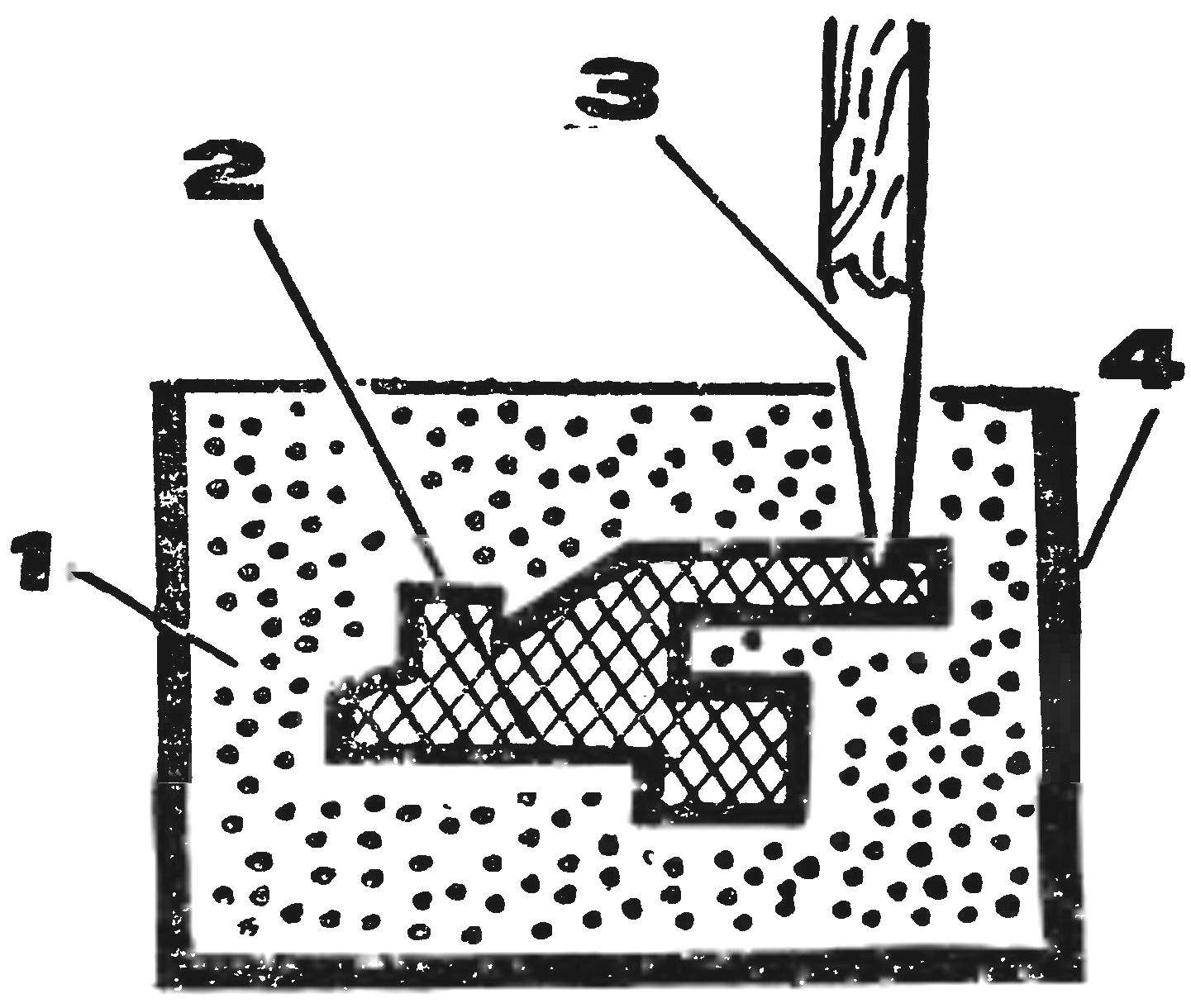
Fig. 2. Sealed form:
1 — plaster casting; 2 — paraffin model; 3 — mounting rod (tree); 4 — cardboard box.
The completed form is kept at room temperature 15-30 minutes until a thick rubbery mass. After which it is compacted via Gating the hole a glass or wooden stick. Compacted the surface of the mass should not reach the top edge of the forms by 3-5 mm, as in the polymerization of acrylate expanding.
Gating hole cover with moistened cellophane and a piece of plywood and tighten the clamp. Then form together with the clamp is immersed in a pot of room temperature water and gradually heat for 30-40 minutes bring to a boil. It should not be rapid and lasts at least 45 min. then heating is stopped and the form is aged in the pan for another 15-20 min. To obtain better quality castings should slow full cooling the mould to room temperature.