At the organization of ship modeling circle head meets with a problem: where to start? Introducing a new section, the editors attempt to facilitate the selection of practical material for modelers of the second year.
Here is the drawings, recommendations and practical advice will help young designers in the design and construction of floating models of ships and vessels, with which they will take part in exhibitions, contests and competitions.
In the second year of the course the majority of members in the club better to work with ready, used the blueprints, and only the most prepared can be trusted with the production models of their own design. It must necessarily follow that when developing the drawing of the model and its design took into account all the requirements for this class of models, described either in terms of exhibitions and competitions, either in the Uniform all-Union sports classification models and Rules of the competition.
Today we give drawings and a description of the river of the monitor with rubber motor — the first of five models that are designed, built and tested in the ship model laboratory of the Moscow city Palace of pioneers and recommended for groups.
In the future, the journal will be published models of dry cargo barges motor missile boats with motor, river passenger vessel with a rubber motor and the submarine with a rubber motor. They are all simple to manufacture, have good forms, showed high performance and “fit” in ship modeling standards.
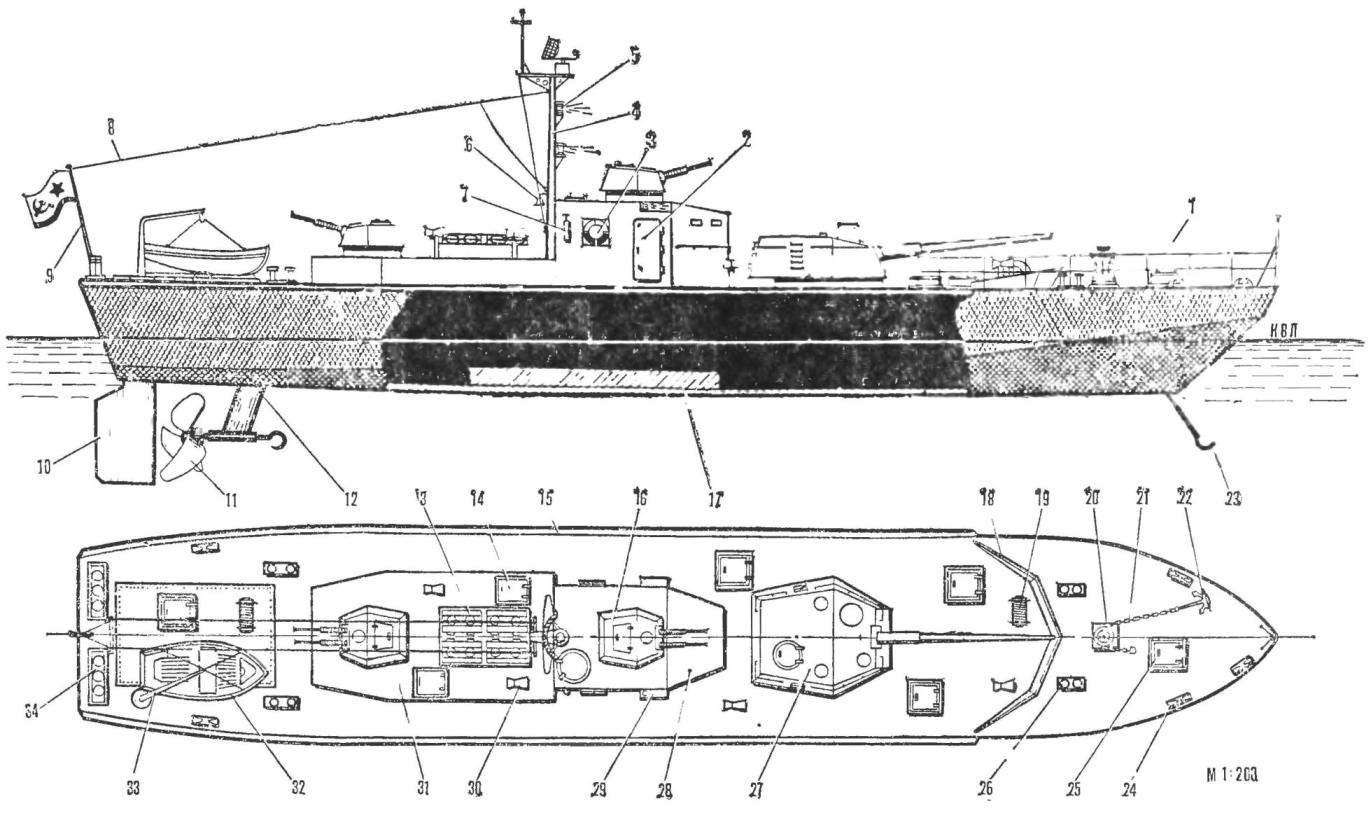
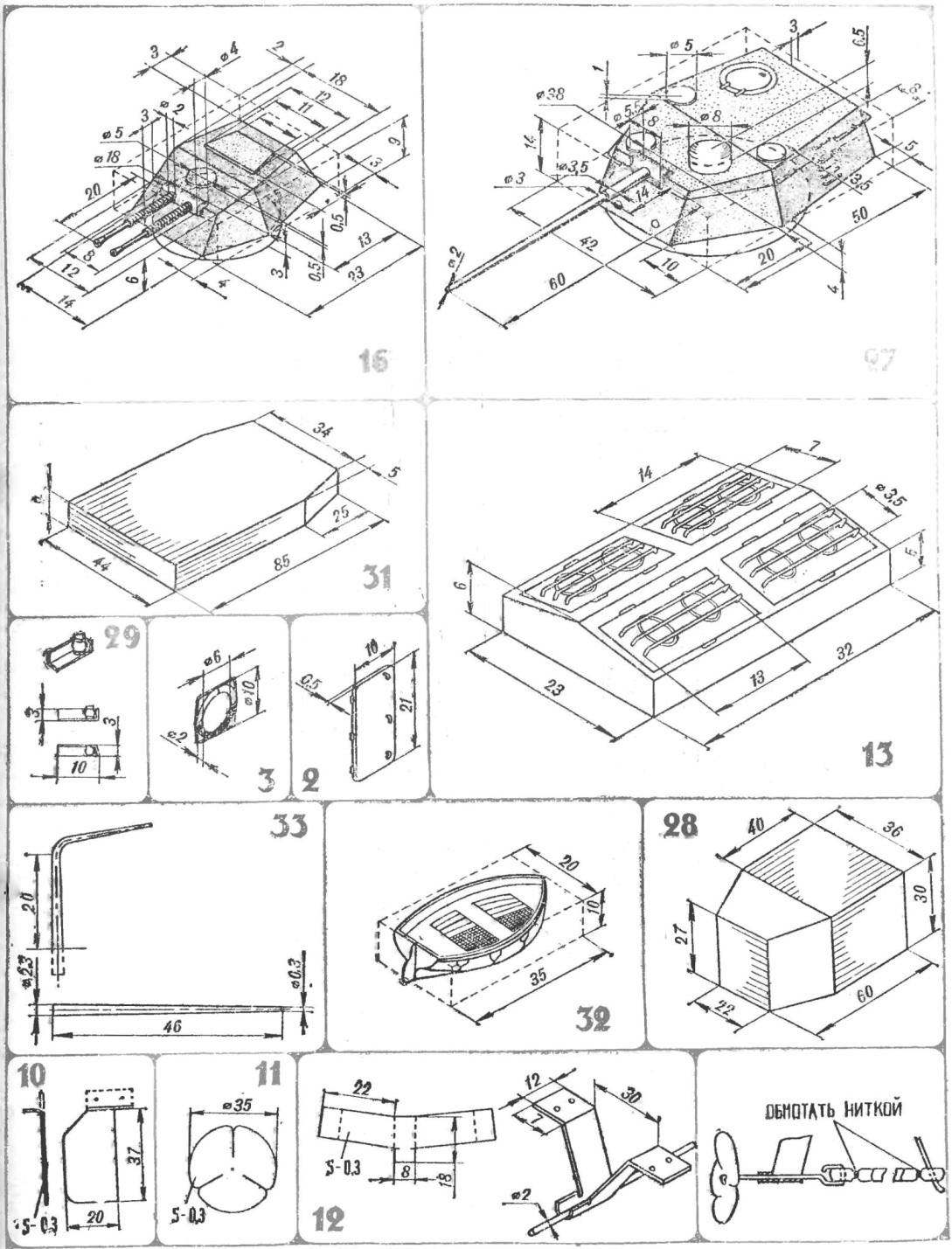
Fig. 1. General view of the river monitor:
1 — rail, 2 — door cutting, 3 — lifeline 4 — mast, 5 way lights, 6 — bell, 7 — extinguisher 8 — antenna, 9 — pole 10 — wheel, 11 — screw, 12 — bracket, 13 — light-Luke 14 — Luke 15 — fender, 16 — tower coaxial machine guns, 17 — cargo (lead), 18 — walnutwood, 19 — view of 20 spire 21 — 22 anchor chain — anchor, 23 — the front hook of the rubber motor, bale straps 24 25 the forepeak, a 26 — cleats, 27 — universal tower, 28 — combat tower, 29 lights, 30 — vent mildew. 31 — machine cap, the 32 — boat, a 33 — davits, 34 — flue instrument
The feature of the first four — used in their construction are the same universal body, which is done by way of manual forging (extrusion) sheet of polystyrene plastic, these models Differ in their purpose, design add-ons and colouring. Sensible things and chassis parts they need to manufacture and install on the hull in accordance with the drawings of this model.
1. MANUFACTURER OF PUNCH AND DIE FOR STAMPING BODY. The plug cut from a rectangular bar of soft wood — Linden, alder and aspen. Work is being done on a carpenter’s workbench. Cardboard templates for the sides and deck of the space bar, and then treat it, finally finish with a file and emery paper and start stamping corps of polystyrene.
The matrix is made of plywood of size 600 X 250 X 5 mm. On the middle of the sheet deck down superimposed punch and fortified with a pencil. Then planned allowance for the material thickness, the contours are cut with a jigsaw, then processed with a file and sandpaper.
2. BODY. A piece of polystyrene or a copolymer with a size of 500 X 250 mm and heated drying oven or over the stove until it softened, is applied to the press punch and the matrix, while the body does not take the desired shape. Wipe with a damp cloth shape on top, pressing the polystyrene to the punch.
3. PROPELLER MOUNTING AND STEERING GEAR FOR MODELS WITH RUBBER MOTOROM. Rotor group of models consists of a rubber motor, front and rear brackets, screw and rudder. For the manufacture of rubber engine uses a special rubber thread a cross section of 1X1, 1X2, 1X4 mm. Length of rubber motor in unstrained condition is about 400 mm when the number of threads from 16 to 24.
The rubber motor is collected as follows: on a distance corresponding to its length in the Board hammered two nails. Rubber thread or tape laid out smooth, without tension and loops. Ends linked site. To the resulting coil can be put on the hook and attach it to the propeller shaft, should make the lugs as shown in Fig. 11. Secure them by tying a tight string.
The front bracket is bent of steel wire Ø 1,5—2 mm and fixed in the bow of the hull on a boss of wood.
The rear bracket is cut from sheet tin or brass according to the drawing and is mounted on the bottom of the case. To do this, in the aft part of the bottom cut two holes. There are inserted the legs of the bracket, straighten and pressed small pieces of polystyrene and Dereza, missed glue.
The screw is cut from a circle of sheet metal or a ton of brass Ø 35-40 mm. the Outer ends of the blades are bent at 40-45°.
For installation of the screw to the place needed a piece of wire Ø1—1.5 mm and a length of 40 mm to insert into the hole in the rear bracket and solder the screw; the other end is bent in the form of a hook.
Steering device the model simple. The rudder is cut from sheet metal and fastened to the housing, as shown in the drawing, with a wooden boss.
4. PROPELLER MOUNTING AND STEERING GEAR FOR MODELS WITH ELECTRIC MOTORS. Rotor group consists of engine and drive shaft. The deadwood is the tube length of 110 mm, outer Ø 3-4 mm and 2-3 mm. internal Ø of tin or thin brass cut with scissors three-blade propeller Ø 25— 30 mm screw Shaft can be made of spokes Ø 1.5—2 mm. Deadwood is fastened in a pre-cut s the case the hole on the glue. The propeller shaft connects to the motor with a piece of the vinyl chloride pipe with a length of 20 mm or a soft spring.
The rudders are cut from sheet metal, and both plates are sealed with a shaft (core wire). Inside the case is pasted a boss, which strengthened the rudder stock.
5. PRODUCTION OF A SUPPORT (CELLBLOCK). The stand consists of two rods, sealed struts, cut from plywood in the thickness of 4-5 mm. the Recess of the case make the form of the latter.
6. ADJUSTING AFLOAT. The test model is to regulate stability and creating the necessary precipitation. To do this, use lead ballast. The case is put on the water and check on-Board and the bow roll. If you run the model out to the left, the rudder should turn right and Vice versa until the model will go straight ahead. The selection of the number of threads in the rubber motor to achieve maximum speed.
Monitors (sometimes referred to as armored) — more numerous class of warships in the composition of the river fleets. They have sufficient seaworthiness, so you can swim in large lakes and coastal areas.
Monitor — a small ship, its displacement reaches 60 tons shallow draft for easy movement on the rivers. Big speed (up to 14 nodes) ensures rapid application of fire strike. For protection against artillery fire, the cabin, deck and a vital part of the body armored.
We will build a monitor based on the universal case, the manufacture of which has just been discussed.
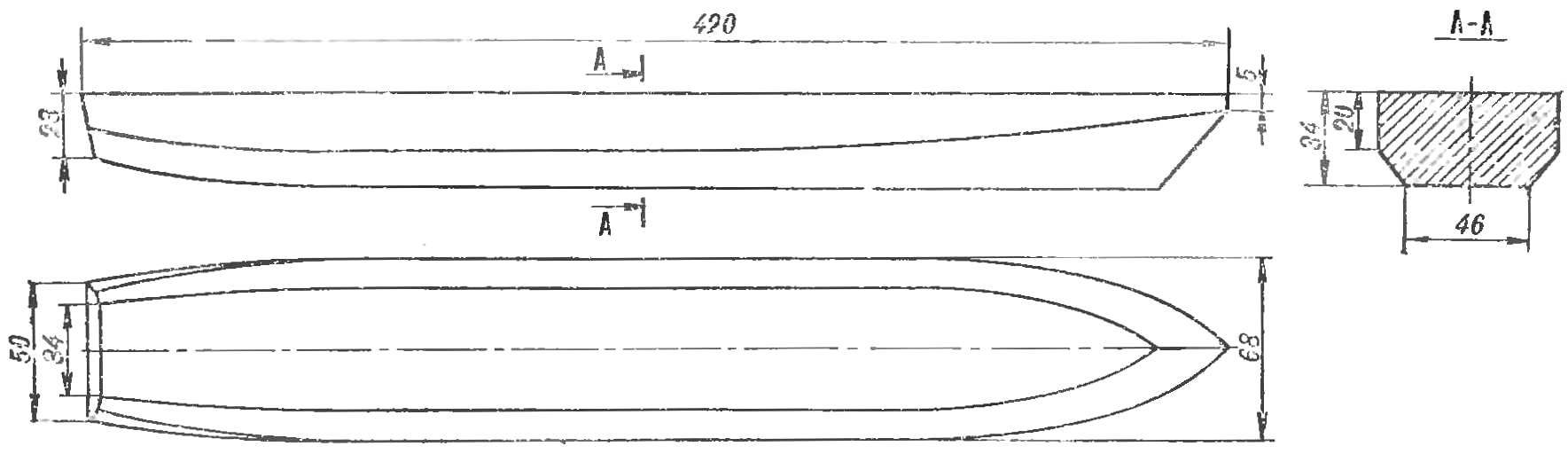
Figure 2. Case — blank monitor.
Combat tower is set in the middle of the deck. It can be made from a block of wood or foam or glue pieces of thin plywood (polystyrene, Plexiglas, celluloid, kartoch).
The side walls of the cutting to hang a door and install grab handles from fine wire stranded electrical cord. Behind the wheelhouse on the deck paste machine cap — superstructure above the engine room. It is a skylight. It is used for day lighting and for ventilation of the engine room. Simulators fans are machined on a lathe or cut from round slats.
Access hatches and deck space made of thin plywood, or celluloid, Perspex, polystyrene. Hinge caps and Flex handle from thin wire.
Artillery armament of the monitor consists of one of the guns caliber 76 mm, installed in the tower before the combat operation, and four heavy machine guns in twin tower installations. The tower gun is made from bars of wood or foam or stamped from polystyrene, the same as the hull.
The barrel of the weapon to carve on a lathe or cut from wooden slats (pine, bamboo). Rail round out, smooth out with a file and sandpaper. Under the tower doing Barbet disk of plywood (cardboard, celluloid).
The barrels of the guns — thin nails or pins, which are strung on a spiral of thin wire-veins.
Aft installed equipment for smoke-screens. This wooden cylinders placed three on each side on special stands-holders from the wire.
Chassis (distinctive) lights are used to determine the direction of movement of the boat at night. On the sides of the cutting set side lights: left red, right green. The rest of the lights are attached to the mast.
The mooring device consists of bollards, views and tilting of the laths. Pipe bollards are machined on a lathe or cut out. The base is made of plywood, or celluloid. Drums views carved out of celluloid. Of the rack and the wire make the cheeks and cylinder. Celluloid (you can use cardboard, plywood), make the side stand. Then all glued together in accordance with the drawing.
On the roof of the wheelhouse, install the mast with ray and jaw. Details of the mast (mast) — of bamboo or pine slats, radar from metal or plastic mesh.
But how to make a life preserver. First on the rod wound wire, then cut the resulting spiral. Paint them, dipping in up to half of the jars with white and red paint.
Leer protect the deck of the boat on Board. Rail rack is the pins going into the deck. Them solder the thin veins of electrical wires or glue thread.
The monitor is painted in three colors: the underwater hull green, red or black, surface — superstructure, hangars, masts, anti-aircraft guns and deck details and superstructure — ball (grey) color. Waterline bounces whitewash. You can also glue a thin line of strips of celluloid, polystyrene, Whatman. The deck covers a brown or dark green paint. Anchor painted in black color.
A. ALESHIN