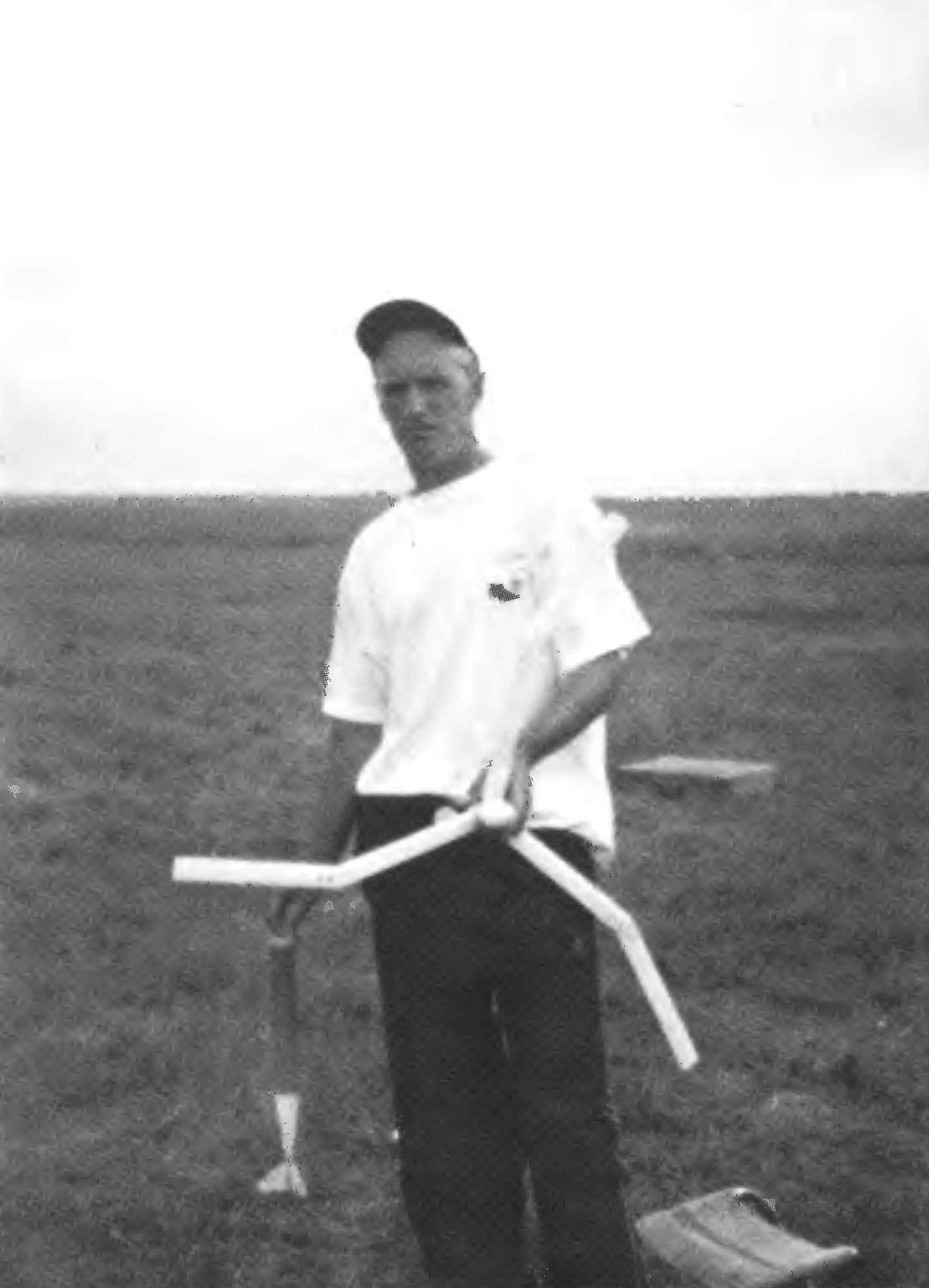
The container rotachute performed at the famous “Chelyabinsk” scheme and technology. In piercing the mandrel with the greatest diameter 40 mm two layers of glass, of a thickness of 0.03 mm into the tube — billet housing with a motor compartment. After drying, its surface is lightly treated, then polished, clamped in the Chuck of the lathe, and cut, having the dimensions: 150 mm (length of the engine compartment) and 405 mm (total length). In the lower (thin) part of the hull fixed three of the stabilizer. They cut balsa veneer with a thickness of 0.8 mm, reinforced side surfaces and slightly round off the edges To the body butt glue them with resin VC-9.
The rotor is three-bladed. Blade — foldable, when in plan view (top) have a sweep of 26°.
The angle “V” double: 2° between the prism and the root element of the blade and 13° — between the root and console elements. The angles of sweep and “V” are provided with the respective treatment elements contact the ends of the blades. Cut the blades out of balsa veneer with a thickness of 3 mm, profile (profile — PLANO-convex) and cover with two layers of nitrocellulose lacquer. The length of the root elements — 246 mm, cantilever — 213. Between the hinge elements connect the strips of fabric with a width of 20 mm, pasted on the lower surface. In the console element of the blade, stepping back 25 mm from the inner end, glue a hook from steel wire with a diameter of 0.5 mm for the elastic opening. And the root element at the distance of 35 mm, make two holes with a diameter of 0.8 mm for wiring and fixing.
From below to the opposite end of the root element of each blade, glue “biscuit”. It is a balsa wedge with a length of 30 mm and a width of 15 mm and maximum thickness of 4 mm. Processing bottom plane “crackers”, to achieve equal inclination angle of all three blades. Then, pasting strips of fabric on the bottom of the “crackers” and prisms, hung hinge of the blade. At a distance of 35 mm from the prism in the root element fastened on top of the hook for the elastic return of the blade in flight (authoritywide) position.
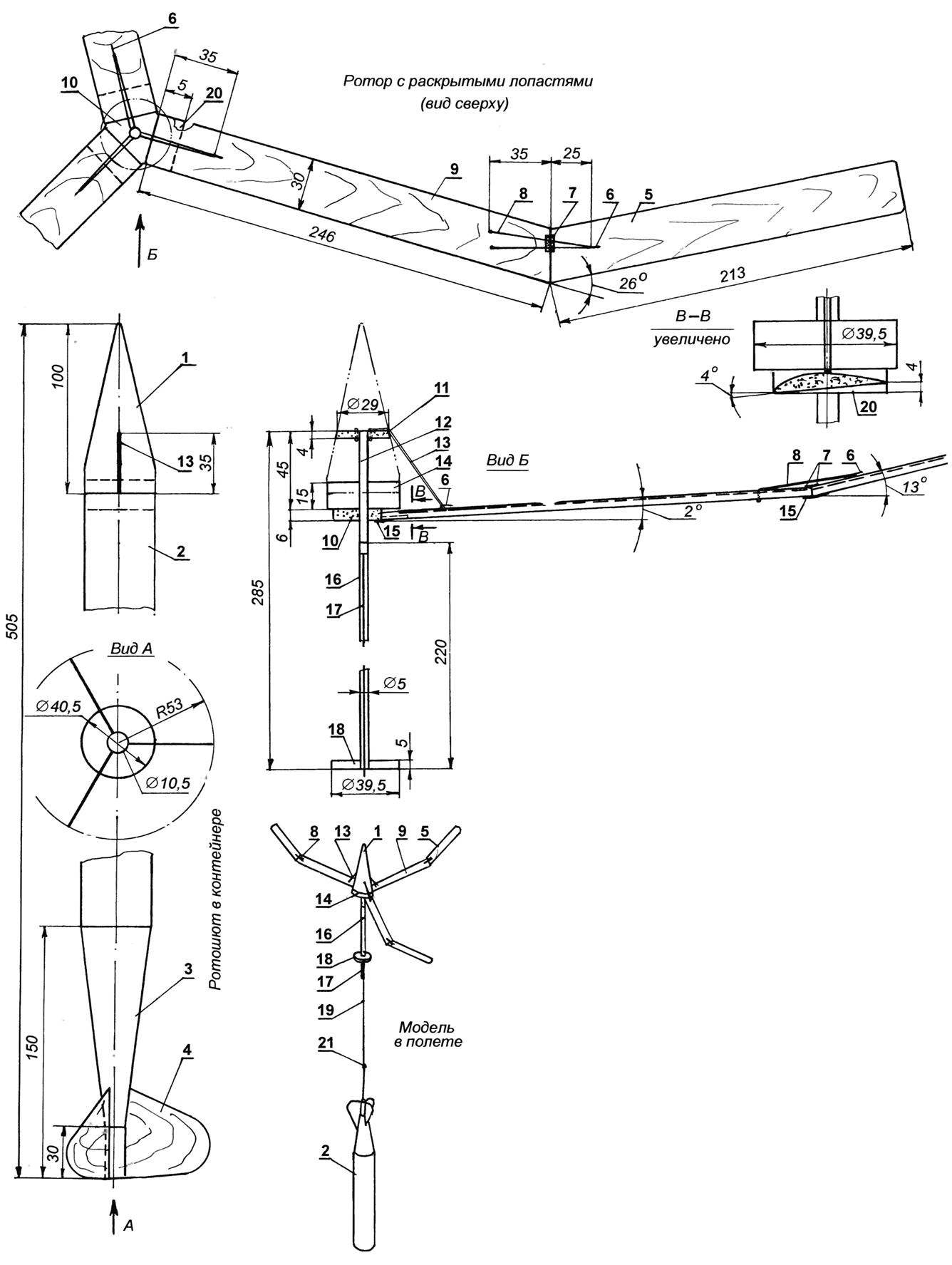
Fig. 1. Model rotocut class S9B A. gryazeva (Chelyabinsk):
1 — fairing; 2 — body; 3 — engine compartment; 4 — stabilizer (balsa veneer s0,8, 3). 5 — the console of the blade (balsa s3, 3). 6 — hook (steel wire Ø0,5, 6 items); 7 — pad; 8 — band disclosures of the blade; 9 — the root element of the blade (balsa s3, 3). 10 — prism (balsa s6); 11 — power frame (balsa s4); 12 — front rotor; 13 — the elastic return of the blade; 14 — planting Bush (foam); 15 — hinge; 16 — rod (fiberglass, pipe Ø5, L220); 17 — attenuator (hat elastic); 18 — protective frame (balsa s5); 19 thread suspension (steel cable); 20 — “biscuit”; 21 — bearing (swivel); material parts 1,2,3 — fiberglass
The rotor hub consists of a pillar fixed on her prism, a landing sleeve and the power frame. Prism is the main detail of the hub of the model rotor is made of balsa plate with a thickness of 6 mm in the form of an equilateral triangle with sides equal to 32 mm. the Landing sleeve is a cylinder of foam with a diameter of 39.5 mm and a length of 15 mm. On it, after assembling the entire model, install the fairing and fix the three needles.
On top of the stand is glued of the power frame 4 mm thick, which fix the rubber for the disclosure of the blades. From the bottom to the free end of the rack cable attenuator — cut the hat, the bands and put a rod tube made of fiberglass with a length of 220 mm and a diameter of 5 mm. At the lower end of rod glue protective frame. To the lower end of the shock absorber emerging from the rod, fix the thread pendants, steel cable, connected to the container via a bearing (swivel).
Fairing is laminated of two layers of glass, of a thickness of 0.03 mm by conventional techniques on a conical mandrel. At a distance of 35 mm from the lower edge in the side surface, there are three holes with a diameter of 1.5 mm through which pass through the elastic return of the blades. In my opinion, is the lack (defect) model: gum outside. But at the same time — they are always under control.
Before running the model rotocut check the angles of the blades. If there are deviations — they eliminate. Then fix the rubber bands of the disclosure and return of the blades. The length of the rubber bands must be the same to ensure equal tension. Then fold the blades, bending of cantilever elements down and place them along the rod and the rack. Next, put the prepared design into a container, after putting back the wad.
The mass of the model without MRD — about 30 g.
V. ROZHKOV, Honored coach of Russia