The history of the creation of the all-terrain vehicle is quite long. First, I began to adapt the Niva-2121 for movement on our off-road terrain – I installed it on the largest wheels from a Jeep. We rode it with a neighbor (also, by the way, an avid fisherman and hunter), but the cross-country ability was not enough for our area. We bought wheels with tires from Shaina for the Niva. We trimmed the arches in the body, installed protruding fender liners to prevent dirt from being thrown onto the windows, and off we went again. In general, I liked it, but there is not enough space in the cabin and the car does not float on water. I wanted more.
One hunter I know suggested replacing the Niva with Trekol tires with UAZ-31514 axles and a bunch of various spare parts. We agreed, and then it all began: we decided to make a car that could go where no one had gone before! Then the search began on the Internet and technical magazines (including in “Model Designer”) for various information on the construction of all-terrain vehicles. In about four months I looked through and read everything. The project for the future all-terrain vehicle has also matured.
It took another 2-3 months to assemble the components. We bought used UAZ-31514 for 10 thousand rubles and VAZ-2109 for 8 thousand rubles as donors.
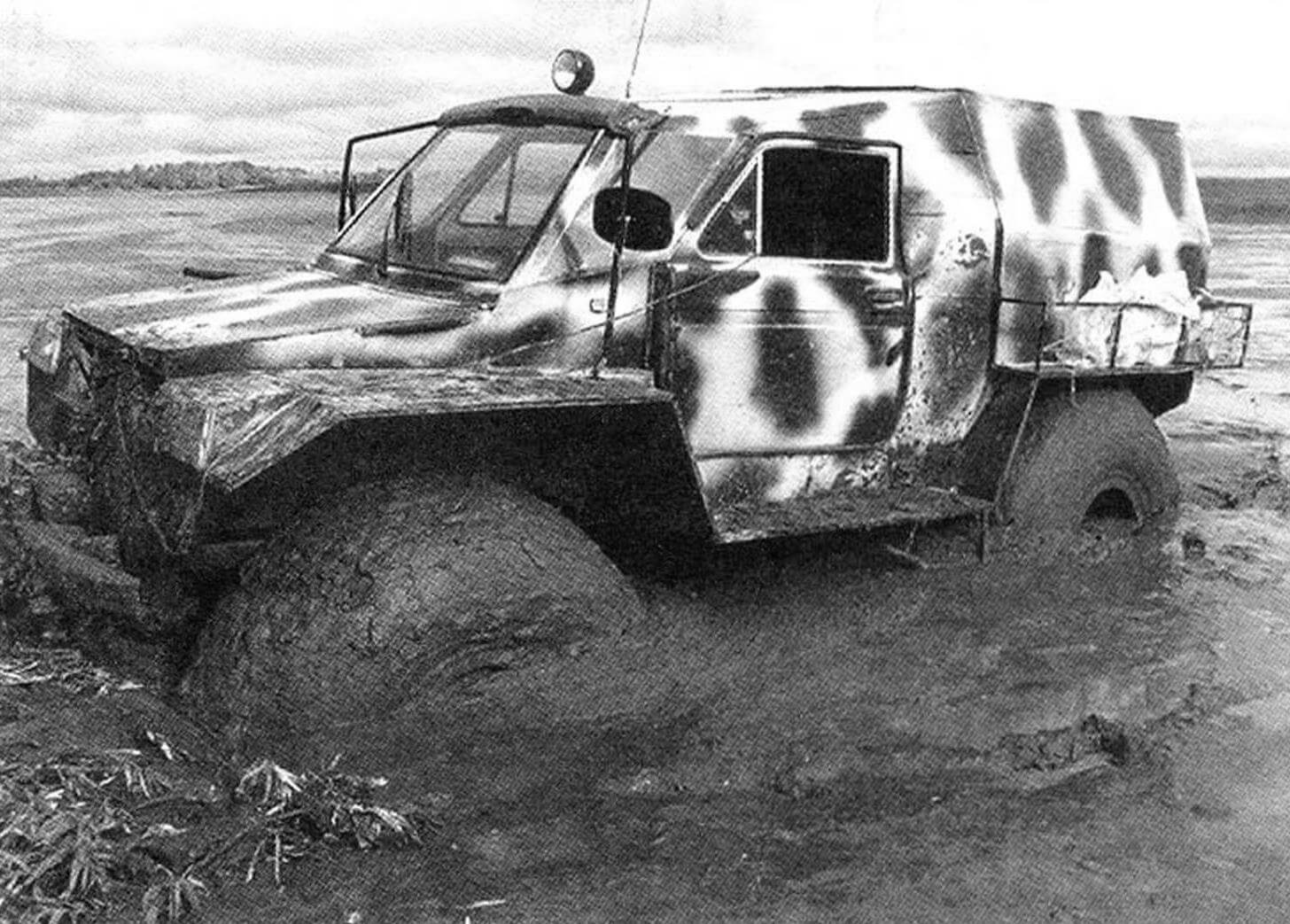
Construction began in May 2008, and in September of the same year the all-terrain vehicle already passed its first tests, and as it later showed, we coped with the task! In two years we drove more than 7000 km. There were never any serious breakdowns; we always got back to the house under our own power.
As is clear from what was said earlier, the engine has a power of 70 hp. and a working volume of 1500 cm3 in a block with a clutch and a five-speed gearbox was used on an all-terrain vehicle from the purchased VAZ-2109.
First of all, we welded wheels (disks with rims) for low-pressure tube tires from Trekol with dimensions 1300x600x533, designed for operating pressure from 0.08 to 0.5 kgf/cm2. They used UAZ wheels. The discs were left unchanged, and the rims were widened to 390 mm.
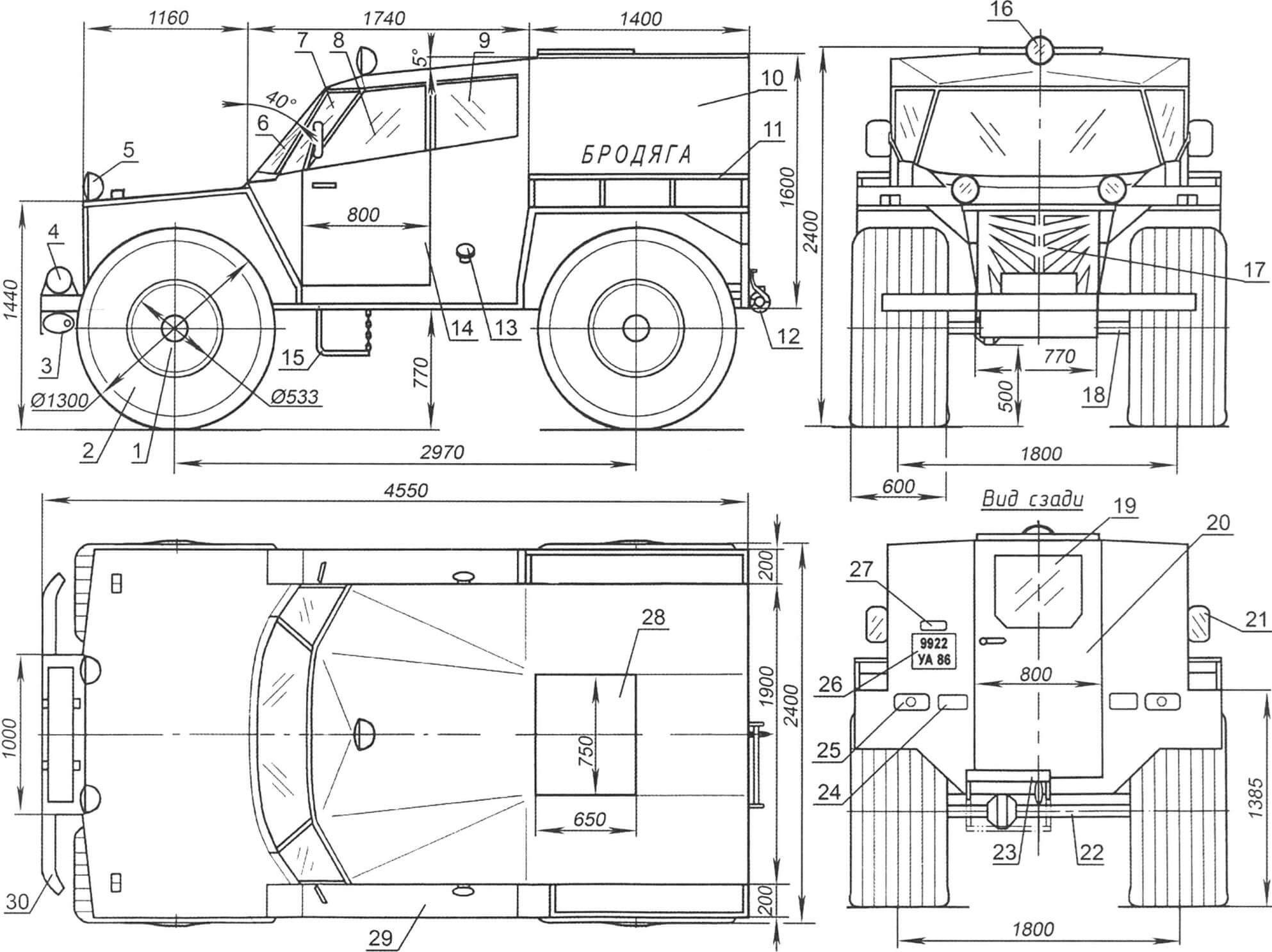
1 — wheel (Trekol company, 4 pcs.); 2 — low-pressure tubeless tire with dimensions 1300x600x533 from Trekol (4 pcs.) 3 — muffler; 4 – winch; 5 — traveling headlight (from the tractor, 2 pcs.); 6 — windshield (from VAZ-2109); 7 – window; 8 — door glass; 9 — side glass; 10 — body (duralumin sheet s0.8); 11 — side trunk fencing (pipe 20×20); 12 — forklift (from UAZ-469); 13 — fuel tank filler cap (from VAZ-2109, 2 pcs.); 14 – side door; 15 — suspended step (pipe Ø22 with chain, 2 pcs.); 16 — searchlight; 17 — radiator lining (steel sheet s0.8); 18 — front axle (from UAZ-469); 19 — rear door glass; 20 — rear door; 21 — rear view mirror (from UAZ-469, 2 pcs.); 22 — rear axle (from UAZ-469); 23 — folding rear step; 24 — reversing lamp (2 pcs.); 25 — combined taillight and turning lights, as well as a brake light (2 pcs.); 26 — state license plate; 27 — license plate light; 28 — interior hatch cover; 29 — side step (2 pcs.); 30 — bumper (from UAZ-469)
Just as the construction of a house begins with the foundation, so we started all the estimates with the chassis: we assembled axles from a UAZ-31514 car with homemade wheels and factory-made Trekol tires. The axles were placed from each other at a distance equal to the future wheelbase (2970 mm – according to estimates, this was optimal for our all-terrain vehicle) and they began to try on a frame on a suspension of semi-elliptical longitudinal springs and hydraulic spring shock absorbers, all from the same UAZ.
The frame is welded, simple, rectangular in shape. It is based on two longitudinal load-bearing elements—spars, each consisting of a pair of steel pipes of rectangular section 60×40 mm with a wall thickness of 3 mm. The pipes were connected to each other by means of spacer stands made from the same pipe. As a result, each spar turned out to be a truss. The spars were connected to each other at the ends by front and rear cross-beams made of steel channel No. 6.5, and in between by several cross-beams made of rolled products of different sizes. The front crossmember is reinforced with a pair of struts – for safety in the event of a frontal impact. In addition, a winch for self-pulling is mounted on the front bumper attached to it. The transfer case is located on the hanging posts of the central cross member, so it is also reinforced with struts, and this unit is an entire additional subframe.
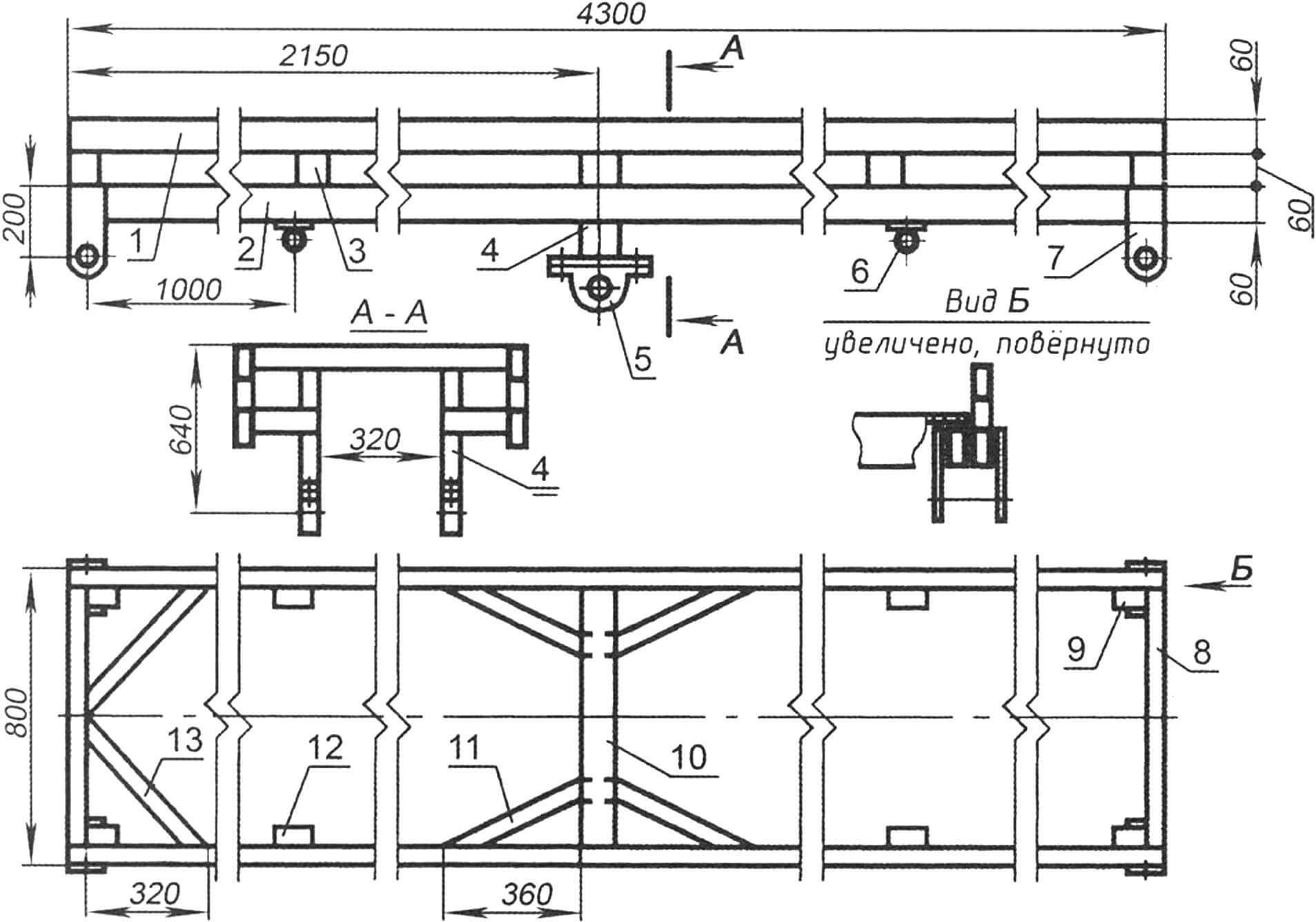
1 — upper chord of the spar (pipe 60x40x3, 2 pcs.); 2 — lower chord of the spar (pipe 60x40x3, 2 pcs.); 3 — inter-belt spacer of the spar (pipe 60x40x3, 10 pcs.); 4 — transfer case suspension (pipe 60x40x3, 2 pcs.); 5 — bushing for attaching the transfer case (2 pcs.); 6 — silent block bushing for fastening the spring earring (4 pcs.); 7 — bracket-eye for the silent block for fastening the spring (4 pcs.); 8 — rear traverse (channel No. 6.5); 9 — remote eye spacer (pipe 60x40x3, 4 pcs.); 10 — central cross member (pipe 60x40x3); 11 — suspension strut (pipe 60x40x3, 4 pcs.); 12 — bushing heel (steel sheet s3, 4 pcs.); 13 — front traverse strut (pipe 60x40x3, 2 pcs.)
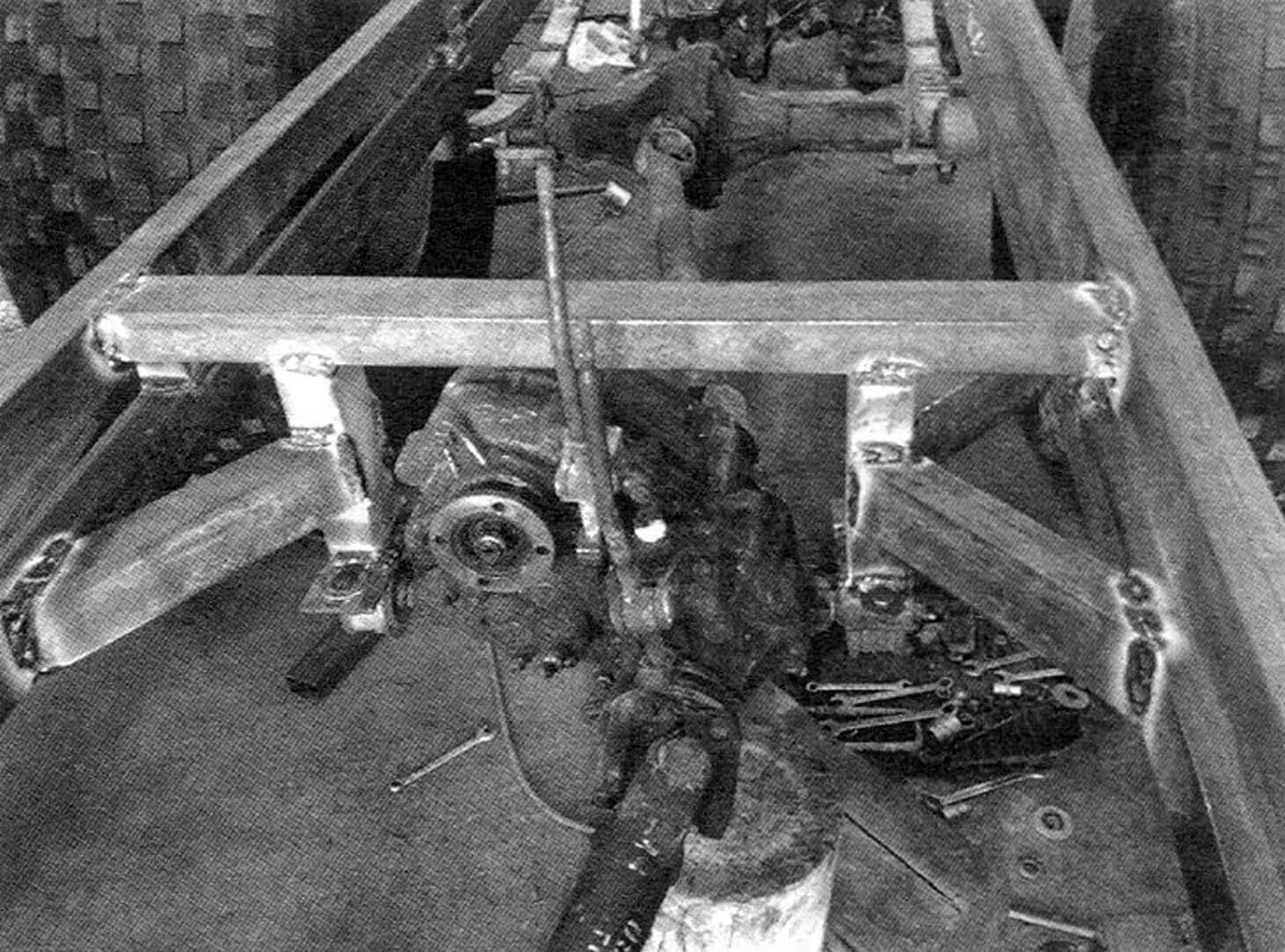
After that, they installed it on the frame and verified the position of the engine in the block with the clutch basket and gearbox. To attach them to the frame, suitable brackets were welded in place. The mounting brackets for springs and shock absorbers, assemblies and control mechanisms, the brake system, etc. were welded in place to the side members and cross members.
Upon completion of the layout and installation of the units, we moved on to the manufacture of the body frame. It was cooked “on site” from steel tubes with a cross-section of 20×20 mm and a wall thickness of 1.5 mm. The body frame was covered with 6 mm plywood. The plywood was painted in four layers on the outside and one layer on the inside. A hatch was cut in the ceiling of the body and closed with a hinged lid.
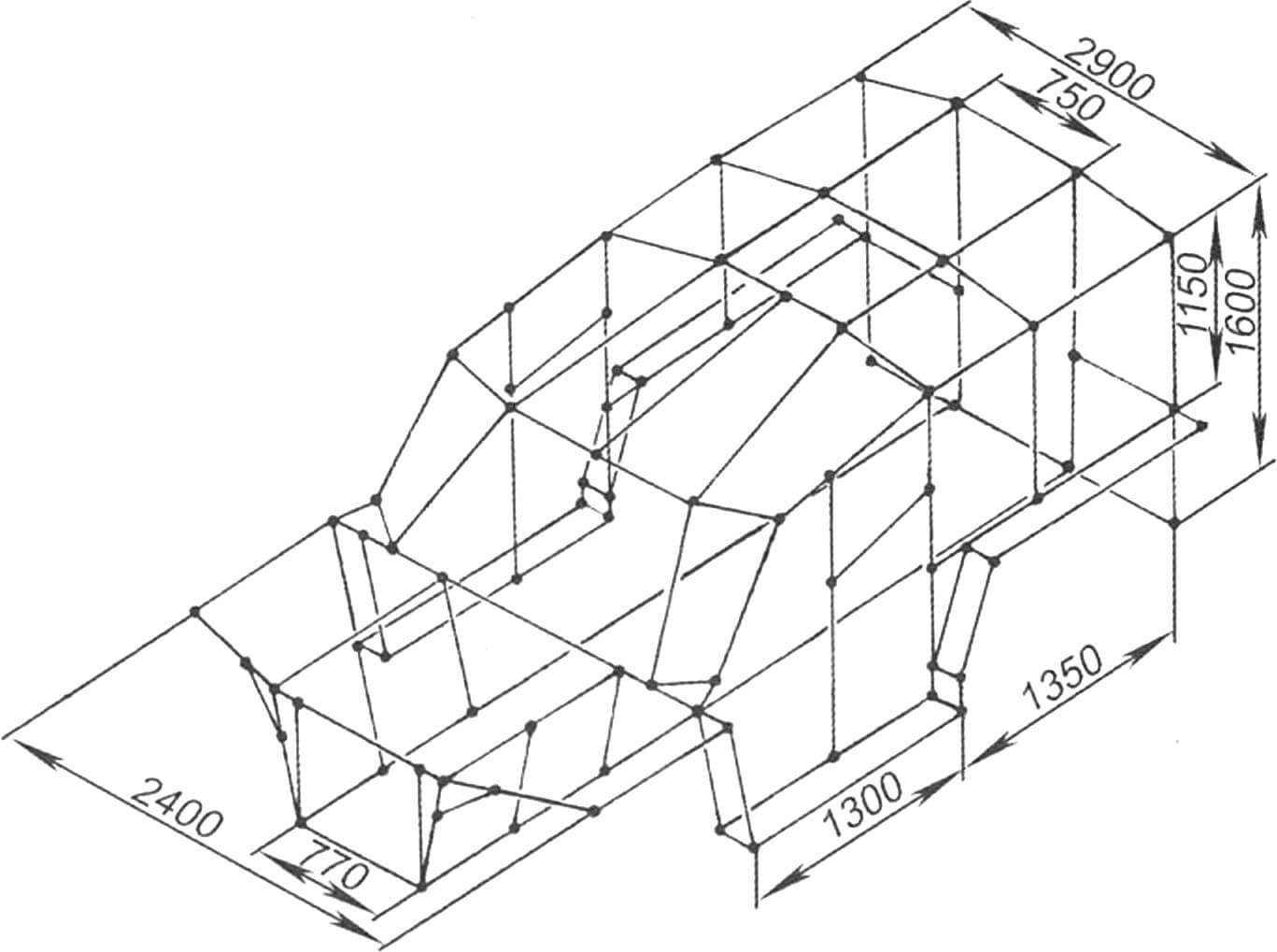
There are two side doors in the body, for the driver and the front passenger-navigator. In the original version, “Niva” doors were used. But they turned out to be too heavy for our all-terrain vehicle, and subsequently we replaced them with homemade frame ones. For other passengers, there is a hinged door in the rear wall of the body.
A winch is mounted on the front bumper (from a UAZ-469) for self-pulling in hopeless situations when the wheels are spinning and the car is stationary. But in one of the swamps, during self-pulling, this winch burned out, and we replaced it with a homemade one – from a VAZ-2109 starter.
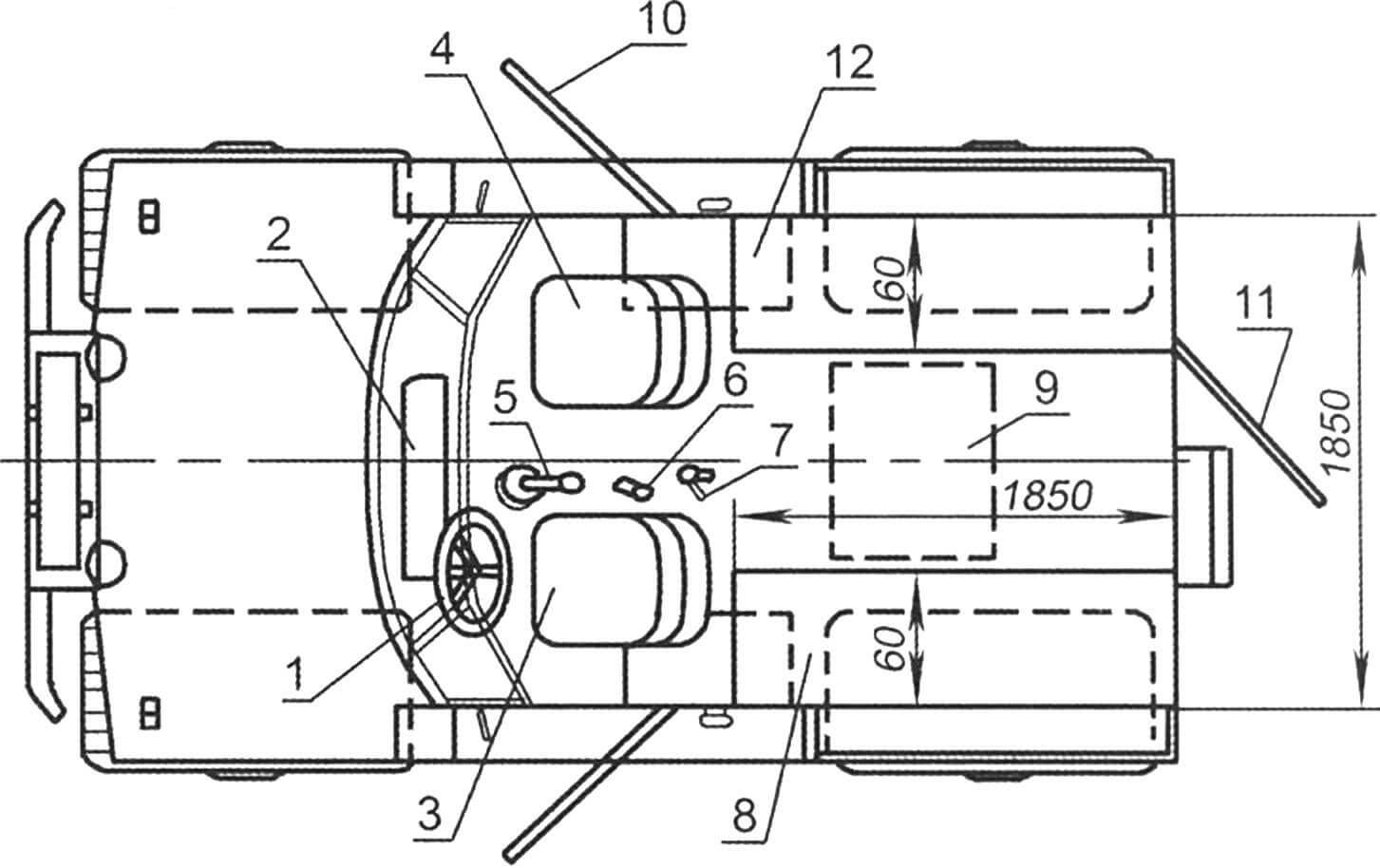
1 — steering wheel and controls (from UAZ-469); 2 — instrument panel (from VAZ-2121 Niva); 3 — driver’s seat (from UAZ-469); 4 — navigator’s seat (from UAZ-469); 5 — gear shift lever; 6 — center differential lock lever (from VAZ-2121 Niva); 7 — downshift lever (from VAZ-2121 Niva); 8 — passenger seat-lounger (2 pcs.); 9 — sunroof (superimposed projection); 10 — side door (2 pcs.); 11 — rear door; 12 — fuel tank (from VAZ-2109, 2 pcs.)
The brake system with a vacuum booster is standard from the UAZ-469. The steering with hydraulic booster of an integral type and all the pedals are from the same car. The steering column is shifted a little to the right, but you quickly get used to it.
In the front of the cabin there is a stove from a VAZ-2108 – it blows on the windshield and heats the driver and co-driver, and under the front passenger seat there is a second stove, from a Gazelle car – the air flow from it is directed to the feet of the rear passengers. The cabin is warm even in 40-degree frost. There is a lot of space in the cabin, and during group trips for fishing or hunting, we most often relax in our all-terrain vehicle – six people can accommodate freely. There’s just no table yet. There are no storage compartments in the cabin yet—we place small items in cardboard boxes behind the front seats.
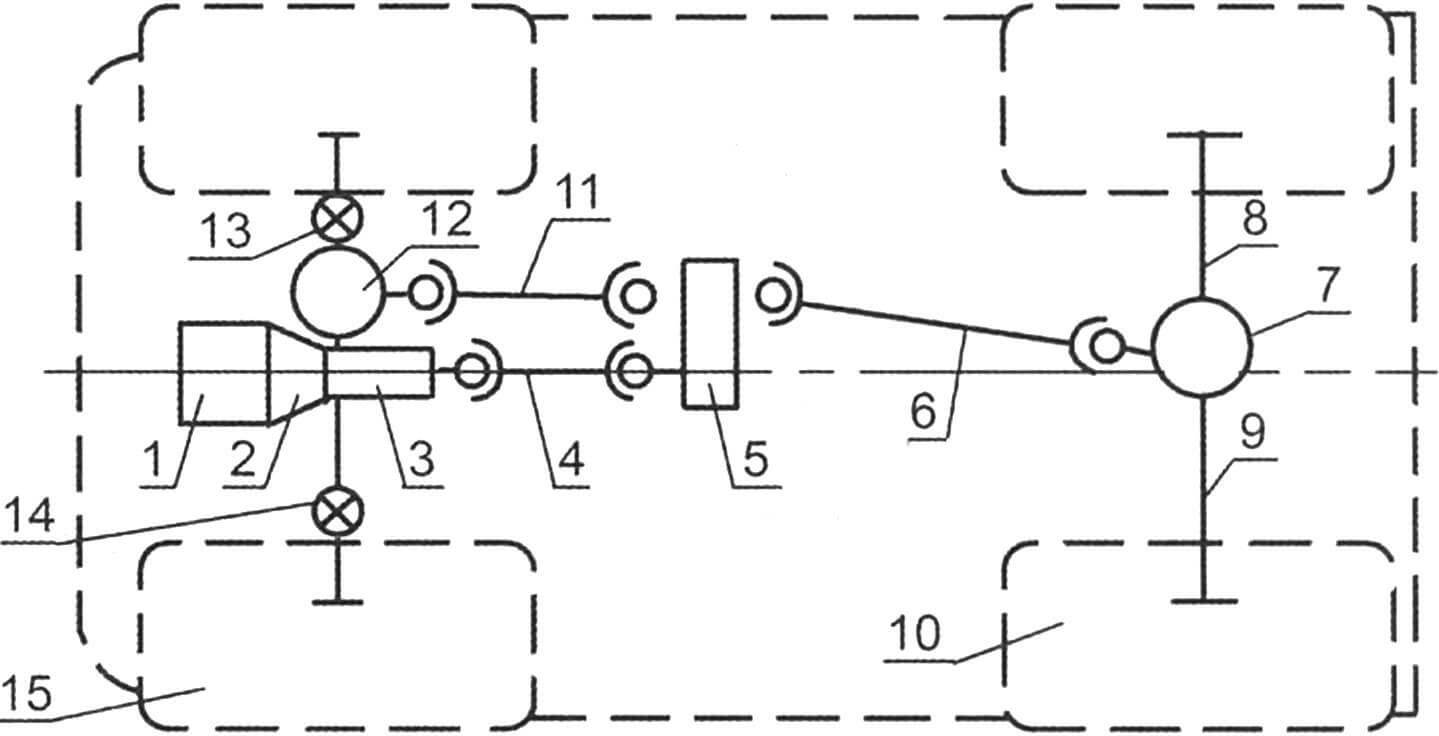
1 — engine (from VAZ-2109); 2 — clutch basket (from VAZ-2109); 3 — gearbox (from VAZ-2109); 4 — transfer case driveshaft; 5 — transfer case (from VAZ-2121 “Niva”); 6 — rear axle driveshaft; 7 — main gear of the rear axle (from UAZ-469); 8 — short axle shaft of the rear axle with a wheel mounting flange; 9 — long axle shaft of the rear axle with a wheel mounting flange; 10 — rear wheel (2 pcs.); 11 — driveshaft of the front axle; 12 — main gear of the front axle (from UAZ-469); 13 — short CV joint (from UAZ-469); 14 — long CV joint (from UAZ-469); 15 — front steered wheel (2 pcs.)
In general, everyone likes “Brodyaga-Yugra” both in terms of design and technical capabilities. But most of all – in terms of capacity.
There were certain difficulties in obtaining documents for the car, that is, in “legalizing” it. But in the end, these issues were resolved.
The all-terrain vehicle passed a technical auto examination at the regional organization of the All-Russian Society of Motorists and was registered with the State Technical Supervision Inspectorate. The state number of the vehicle has been received.
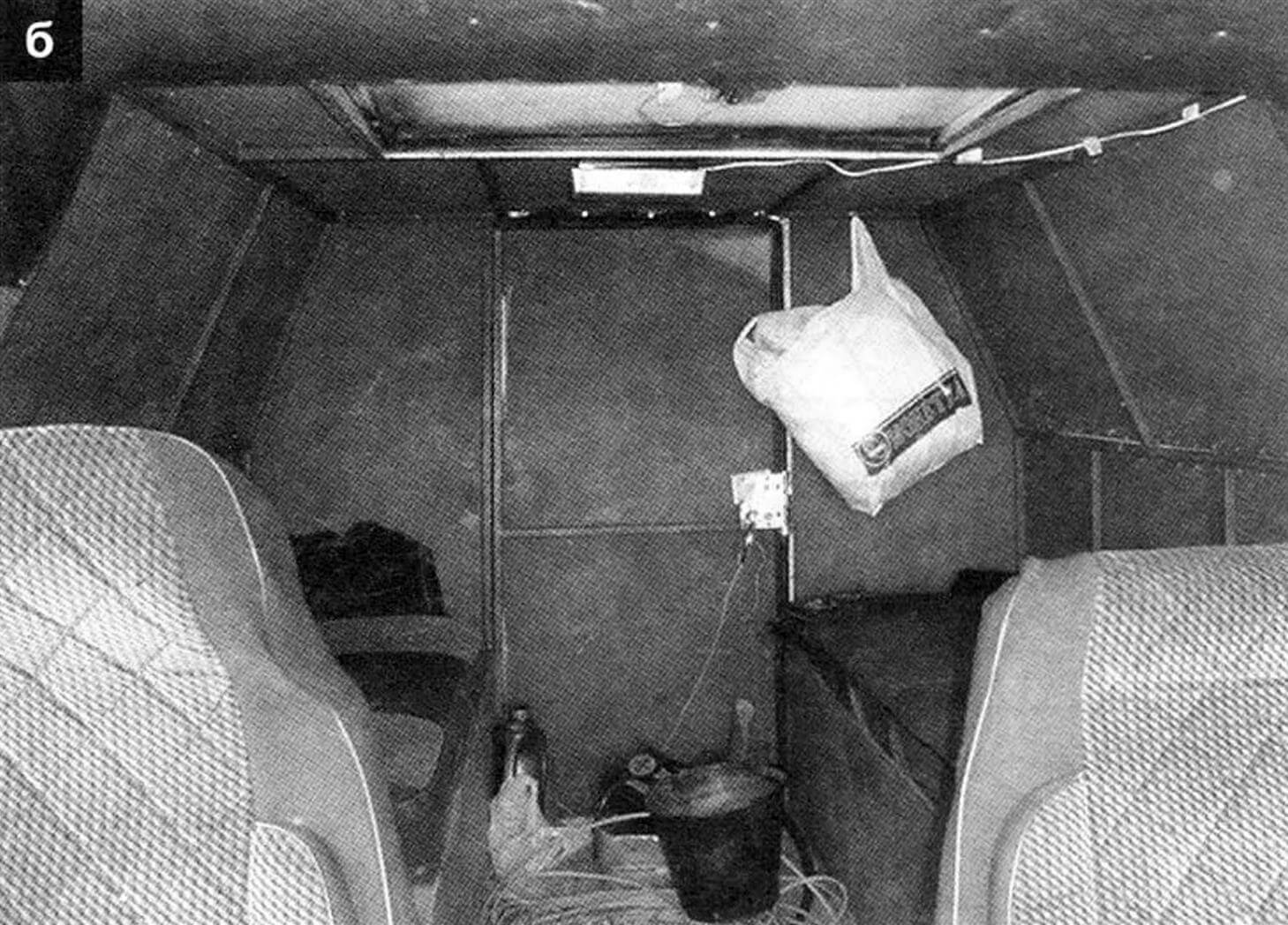
Nevertheless, we continue to improve the all-terrain vehicle. In the summer of 2011, we changed homemade wheels (rims) to industrial ones, and tube tires to tubeless tires from the same Trekol company and with the same dimensions 1300x600x533 (the last size is the landing diameter) with a working pressure from 0.08 to 0, 7 kgf/cm2. The engine was overhauled. We went through the transfer case (it turns out that we drove for some time without oil in it): we changed all the seals, and attached the housing to the frame on four pads. Under the front panel they made so-called “glove compartments” – small storage boxes. The body trim was replaced from plywood to metal made of 0.8 mm thick duralumin sheet and the interior was additionally insulated.
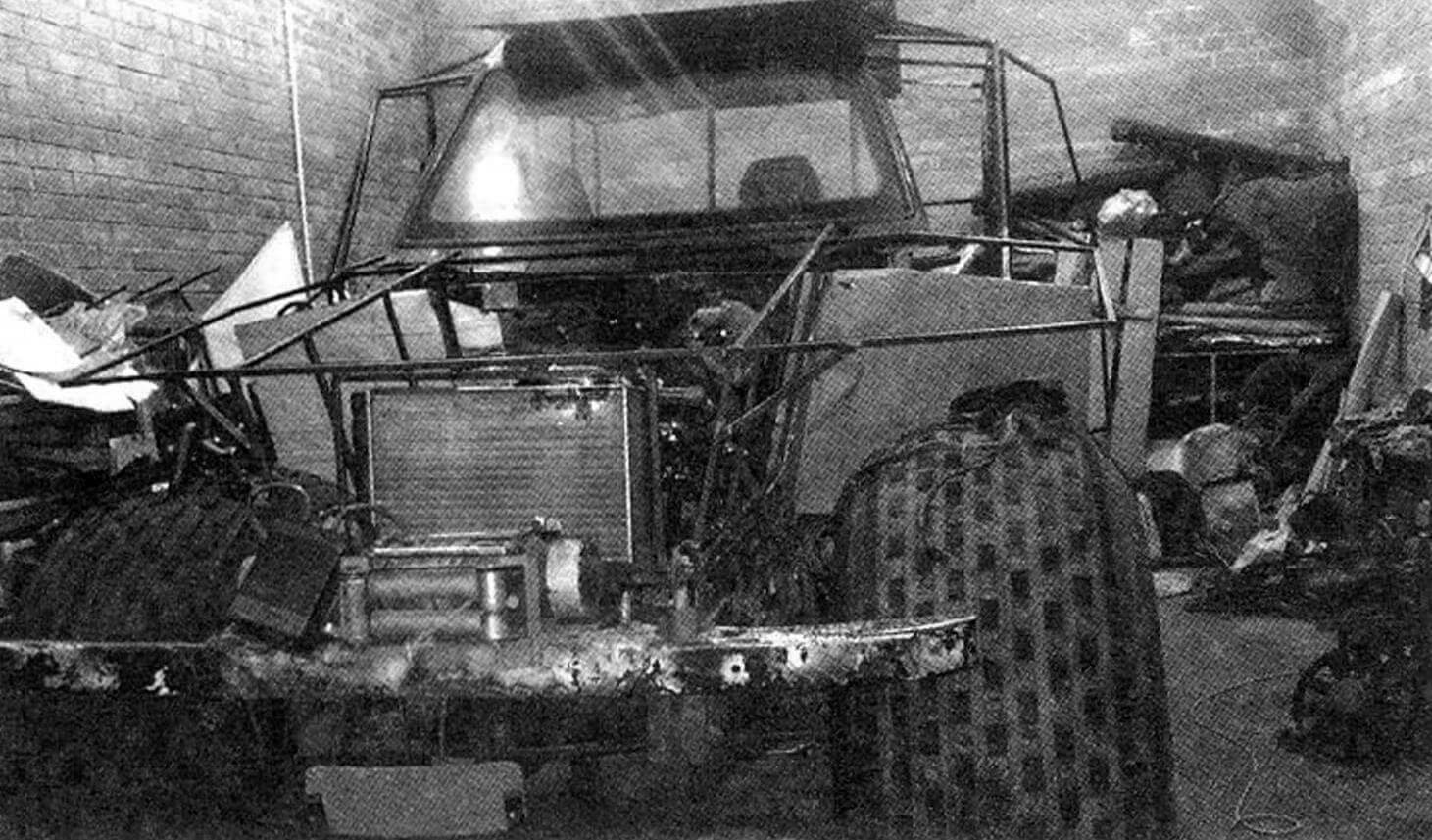
The hood was redone, now it opens forward to make access to the engine more convenient, the interior was redone, and the rectangular headlights were replaced with regular round ones. In general, the structure was lightened by about 300 kg. After this, the cross-country ability increased “manifold” (the all-terrain vehicle can confidently overcome even virgin snow up to half a meter deep) and is not inferior to similar all-terrain vehicles, whose price is incomparably higher (about 1 million rubles). The construction of our all-terrain vehicle took 140 thousand rubles, not counting the cost of the wheels. In principle, for two it’s a completely feasible budget option.
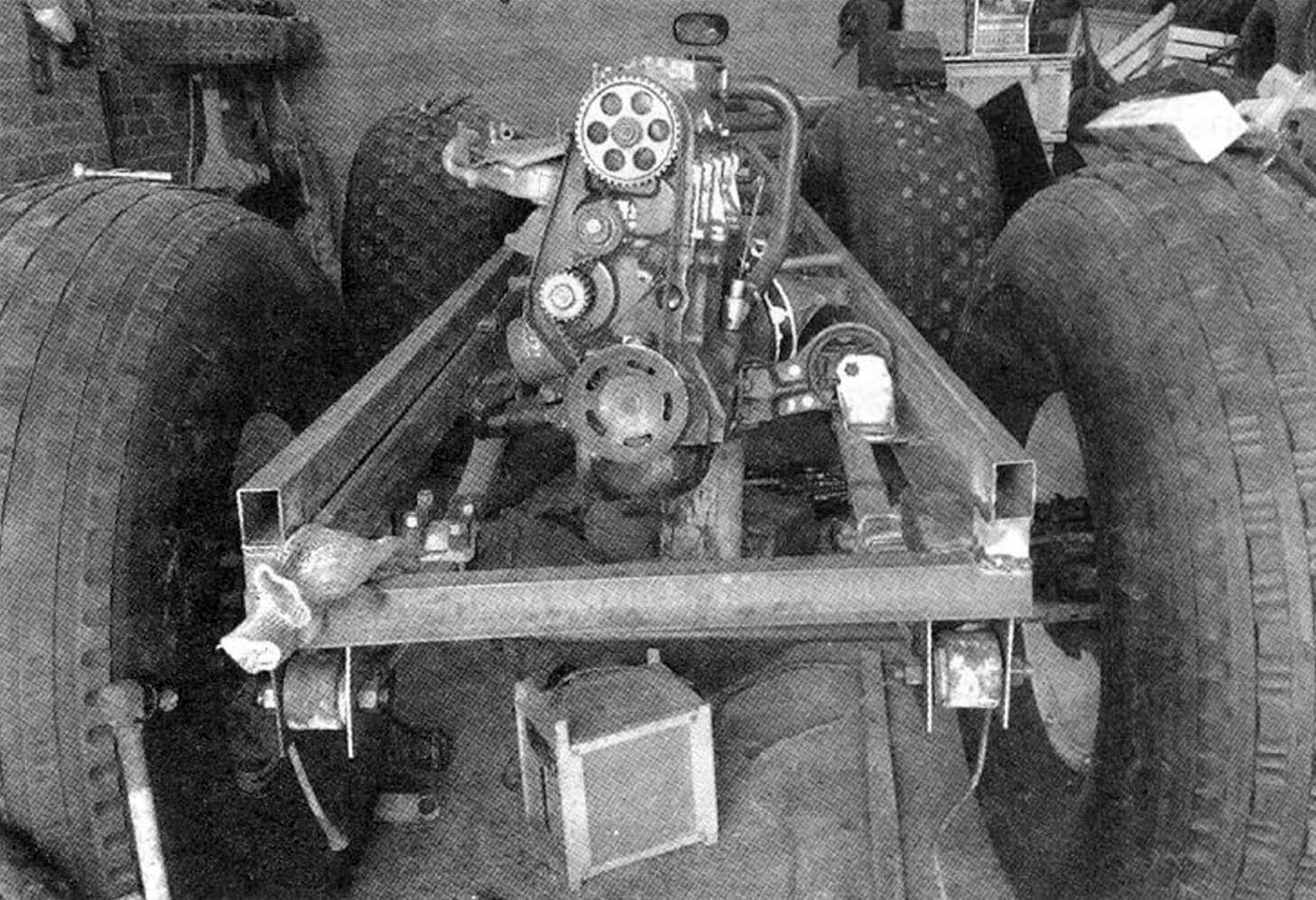
Well, what else to add to the characteristics of the all-terrain vehicle? The longest journey is 300 km through the swamp, not counting the road along the highway. The most extreme trip is fishing in frosty temperatures of 40 degrees. There is only one drawback: even after modernization, it is still a little heavy – 1200 kg, but it is convenient to travel with friends on hikes or long journeys (five people can sleep at full height). In the future we plan to build a slightly smaller all-terrain vehicle: for 2 – 3 people and weighing up to 800 kg. In general, the real all-terrain vehicle has now traveled more than 10,000 km without serious breakdowns; at least, they always returned home under their own power, and sometimes they had to take “distressed” fellow travelers in tow.
As it became clear from the design description, the all-terrain vehicle was created on the basis of domestic VAZ and UAZ vehicles, which makes its maintenance and operation easier and cheaper.
Concluding the story about the all-terrain vehicle, I note that the initial version of the body design, in my opinion, was better, but later we took the path of ensuring maximum internal space and making the vehicle lighter.
D. SCHEMBERGER, Khanty-Mansiysk, Tyumen region.