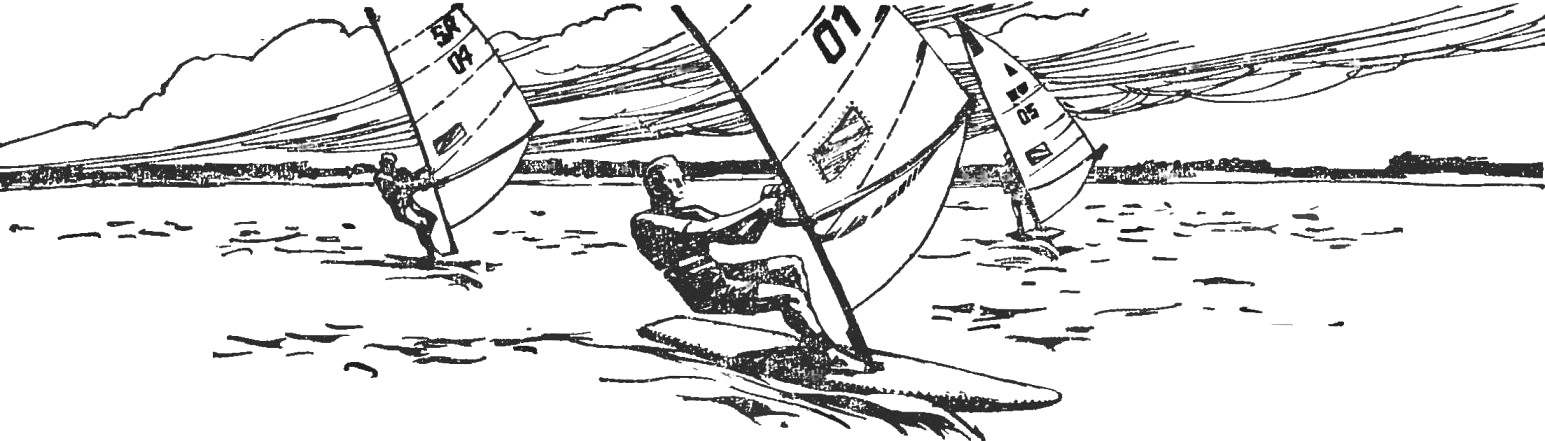
Gucci rider is two arcs, glued wooden slats and the United front a metal band, framed with a soft rubber bumper. Shkotovo (rear) ends Guchkov have holes through which the sheet (rear) corner of the sail go to the ends of the nylon stoppers — sheets. The stopper is placed on each gig in a convenient pull-up or weakening of the Scots place — it allows on-the-go to increase or decrease “belly” of the sail.
For the manufacture of Guchkov needed to make the slipway. Its base is a heavy wooden shield on which are plotted the theoretical arc of the profile of the gig. On its outer side two or three nails are nailed wooden lug size 40Х60Х100 mm in increments of 150-200 mm. the same boss kill on the inside, retreating 10-15 mm from the bow. To fix the one nail that they can be self-installed in the wedging of the package of strips. External and internal bosses are arranged against each other. To slats not glued to the slipway, between the lugs is laid a strip of plastic film. Every hicok is assembled from four strips according to the scheme: oak — pine — pine — oak. Reiki smear epoxy, put between the lugs of the bench and pull together with wedges. It is necessary to ensure that Reiki is not bulging up.
After gluing both Guchkov they are treated with a plane, then with a file and sandpaper, following the form shown in figure 1.
Strip of metal bent and drilled holes for rivets. The same holes are doing in Gecko, but on opposite ends — and even the holes of the sheets.
A curved strip of metal with a rubber bumper attached to Hickam rivets with epoxy glue.
On the lower side Guchkov put metal retainers (see Fig. 1), fixing them with screws epoxy glue.
After Assembly of Gucci must be well proolifit and if they were going on a casein glue, varnish.
You can make Gucci and of duralumin tubes, however, they are less convenient than wood: slippery, thin and do not have buoyancy.
MATERIALS:
Reiki oak or beech 40x10x3000 mm— 4 PCs.; pine slats 40x10x3000 mm—4 PCs.; metal plate 30x500x2 mm; rubber strip 10 mm thick in size of the metal plate; rivet Ø 10Х35 mm — 4 PCs.; paint oil; varnish; adhesive: casein, VIAM-BR or epoxy.
TOOLS:
plane, files, sandpaper of different, saw, drill.
DO THE MAST
Mast is one of the responsible elements of the windsurfer. It can be made of dural tube brand D16T Ø 36 to 40 mm with a wall thickness of 2 mm or wood. Acceptable and combination mast from the dural tube (bottom) and wood (top).
But the most suitable for windsurfer should be the mast of fiberglass on epoxy or polyester resin. It should be conical bottom Ø 53-54 mm and the upper 25-27 mm.
First, you need to whittle wooden tube-lugs of the specified diameters, length 250–300 mm Then takes a thick paper with a width of 150 — 200 mm and a length of 20 m, rolls up into a roll, and from the middle the sky, the cone paper “stick” (Fig. 4, A) so that its larger and smaller diameters correspond to the diameters of the prepared bosses. The length of the “sticks” — 4300 mm. Lugs should be easy to get in paper preparation.
For the first taping cut a piece of fiberglass with a length of 5 m. its Width is determined by the lengths of the circumferences of the upper and lower bases of the conical workpiece and desyatikilometrovy an allowance on the overlap. In epoxy glue (300-400 g) is added 10% acetone. Paper procurement is carefully greased with this lineup (you must work in gloves), superimposed on a smoothly laid fiberglass and carefully rolled it (Fig. 4, B). The fabric is thus spread along and around the circumference of the workpiece. Then the surface covered with epoxy glue so Cuba was not potekov, and the junction had bumps and loose threads. During the polymerization of the epoxy resin, the workpiece should rest on the floor on plastic film. When using polyester resin technology vyklicky does not change, only glued the workpiece must roll in plastic wrap, since at normal temperature polyester adhesive polimerizuet bad air. After curing of the adhesive from the workpiece is removed streaks. The next stage of manufacturing the mast — pasting of the workpiece is pre-stressed layers of fiberglass. Before the workpiece is inserted wrapped by plastic film boss, which will be located in the workpiece prior to final fabrication of the mast.

Fig. 1. Hicok:
1 — hicock 2 — bar coupler with rubber bumper, 3 — stopper.
Fig. 2. Vyklevyvanija the gig:
A — stocks, B — wedging package of strips.
Fig. 3. Lower (1) and top (2) wooden parts of the mast.
Fig. 4. Vyklevyvanija the middle part of the mast:
A — formation of the frame of the mast of the paper roll, B — hanging the first layer of fiberglass: 1 paper frame, 2 — fiberglass; — pasting of the mast of a prestressed fiberglass: 1 — hook, 2 — blocks, 3 — glass, 4 — roll of plastic film.
Fig. 5. Hinge design:
1 — insert the lower mast, 2 — plate (stainl. steel S 2.5 mm), 3 — screw, 4, 5 — bolt M6 nut 6 — cross universal joint. 7, 8 — bolt of M6 with nut, 9 channel, 10 — puck. II, 12, 13 — bolt M10 with washer n nut, 14 — key steps.
Fig. 6. The centerboard.
Fig. 7. Fin.
Remaining from the first operation piece of fiberglass is cut into two equal parts, the previous operation is repeated but to wait for the curing of the adhesive is not Immediately to free pieces of fiberglass on both sides are tied the rope, one of them is pulled through the blocks, and the second is attached to some support (Fig. 4). The tension force should be such that could be heard the crackling of fiberglass. Then, without waiting for curing of the resin, a quick “bandages” mast throughout the length of the ribbon of plastic film, much its pulling. Thus it is necessary to smooth out the fiberglass under the tape until the complete disappearance of air bubbles. At the ends of the mast polyethylene tape is closed up with string, and in this condition the mast is left to complete solidification of the resin (epoxy — day, for polyester — two days). After polymerization of the adhesive tape is unwound plastic — the surface of the mast turns smooth and does not require treatment. The excess ends of the fiberglass to saw off the lugs. Also superimposed another layer of fiberglass, and the previous operation is repeated. Such “strained” layers of fiberglass should be at least five.
After gluing the last mast, the fifth layer of the “hard” fiberglass boss removed, the resulting billet is brought to the size of 4160 mm. the Surface of the mast slightly processed fine sandpaper and varnished. The plastic part of the mast ready.
Of hardwood made false upper and lower part of the mast. These inserts should proolifit and varnish or epoxy glue so they don’t swell and could be removed from the plastic part of the mast. This is necessary in order to be able to replace the plastic part of the mast in its breakage.
Hinge design of the mast is clear from the figure 5.
MATERIALS
(per mast): fiberglass rare (preferably diagonal) weave, an average thickness of 10 m; the paper is thick, of a width of 150-200 mm — 20 m; glue: epoxy — 2 kg, hardener -250 g. acetone — 10% (250 g) or polyester components is 1.5—2 kg; PE film width 100 mm — 20 m; oil varnish; nylon rope (for binding masts).
TOOLS:
blocks (to tension the masts), scissors, a saw.
NOW THE CENTERBOARD AND FIN
The centerboard rider should have a flat and smooth surface, tightly inserted into the well and at the same time easy to withdraw from it. He wikiepedia of three layers of plywood with a thickness of 6 mm. Plywood it should be positioned so that the fibers of the outer layers was along the centerboard, and fiber of the average — across. Bonding is done on a level surface under pressure.
Then cut the contour of the centerboard is treated by a plane (the direction of the plane diagonal of the centerboard), then a rasp and finally — sandpaper. The restrictive strap is attached to it by rivets or screws.
Ready the centerboard should be carefully proolifit, and then cover with epoxy glue or paste over chintz on epoxy glue with acetone. This coating will prevent the centerboard from the swelling. In the same way is made and fin. It can be removable or affixed to the body of the windsurfer.
MATERIALS:
plywood thickness. 6 mm; fabric (cotton); glue: epoxy, casein or VIAM-B3; wooden sticks (hardwood) 15×15 mm, length 250 mm (for restrictive straps centerboard); thick nylon rope length of 50 cm (for the centerboard).
TOOLS:
saw, plane, files, sandpaper, hammer, drill.
(Start at # 1. 1977) (to be Continued)
A. ARBUZOV, Serhiy ARBUZOV