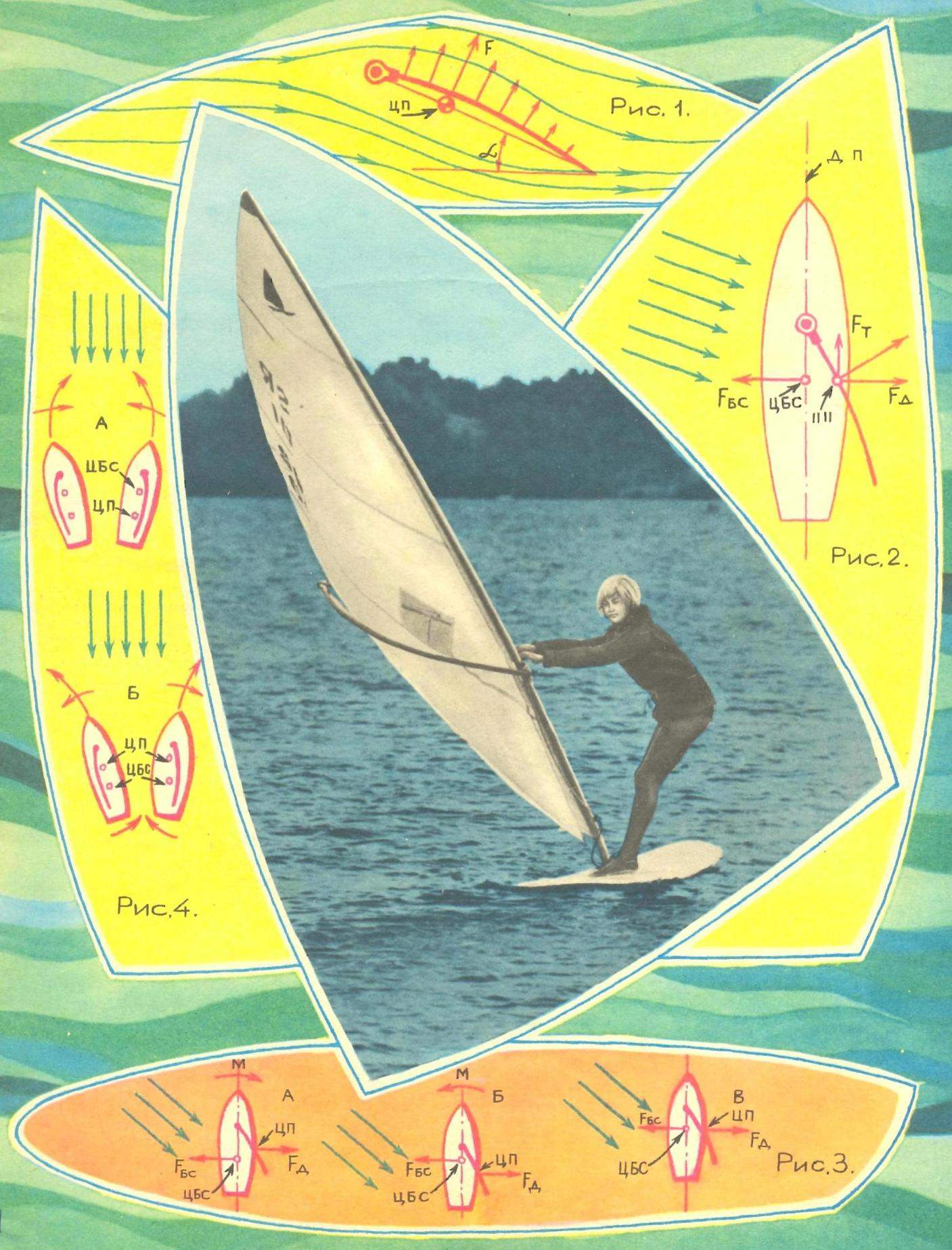
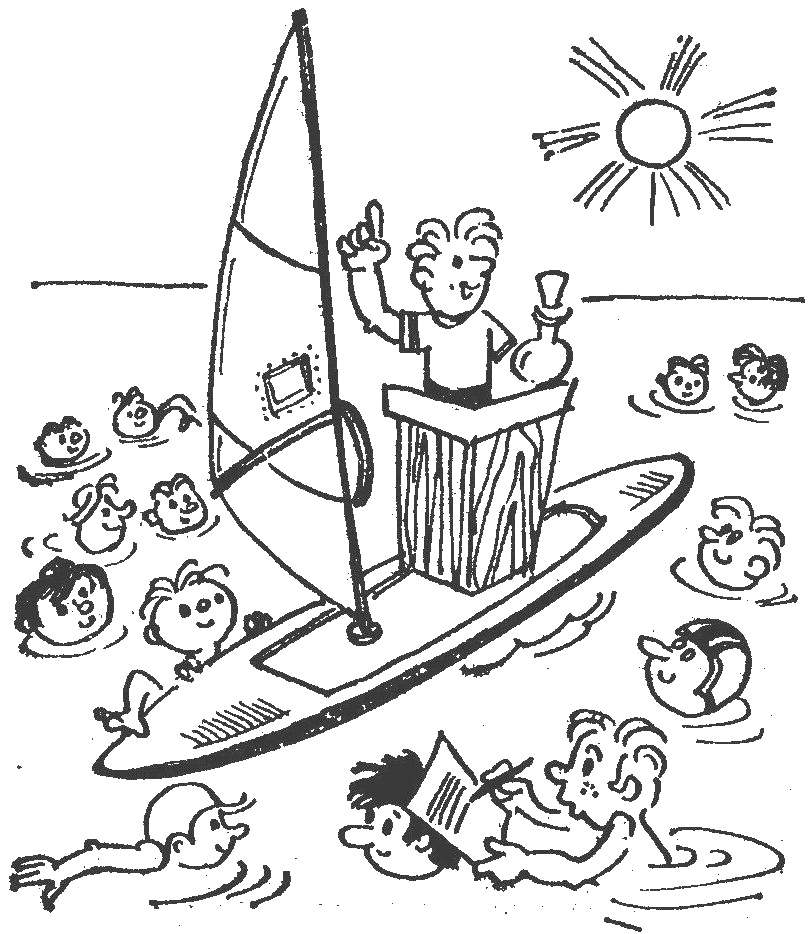
Windsurfing has absorbed the advantages of sailing, water skiing and the classic surf. Moreover, in contrast to the latter to engage them in any pond. Ride quality rider to match the ancestor in a good wind, the athlete rushing at him at speeds up to 20 knots.
The essence of Windsurfing combined: “Board — sail — man.” The elements of this triune formula, that is, the Board-case (how and what to do), sail (how to tailor and sew) and finally about the person (how to learn to glide across the water, overtaking the wind), tell the pioneers of Windsurfing, the founders and organizers of this sport in our country. The first word we provide to the Chairman of the Committee on Windsurfing at the sailing Federation of the USSR Georgiy ARBUZOV and member of the technical Commission of the Committee, the coach of the Moscow section of alle ARBUZOVA.
The design of the windsurfer (Fig. 1) is simple, the layout requires no special comment. The main elements of the surfer: foam, laminated fiberglass boards-case with a fixed fin and a retractable centerboard, mast with hinge and steps, a boom and a sail with battens. In this issue we’ll explain how in a small “industrial area” in the apartment, the school workshop — you can make a Board case, consistent with the “Provisional rules of construction and measurement windsurfers”, approved by the Committee in Windsurfing at the sailing Federation of the USSR.
Board, built, for the following technologies have several advantages in comparison with bead, matrix, etc. They are lightweight, durable, the surface can be brought to any degree of smoothness, they do not allow the water and convenient for transportation. Many athletes are doing the Board this way, we tell our readers.
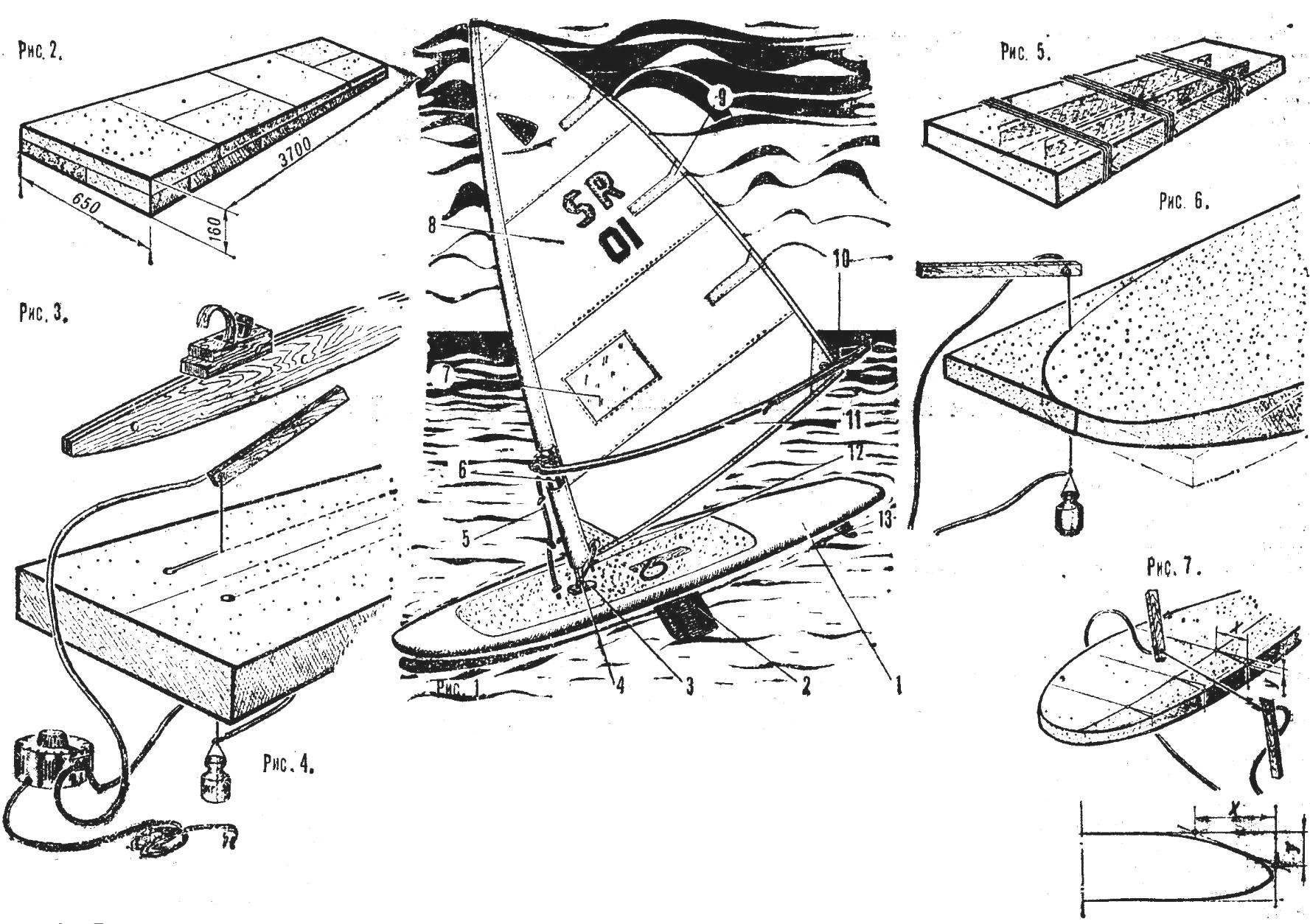
Fig. 1. The layout of the windsurfer:
1 Board-case, 2 — retractable centerboard, 8 — hinge, 4 — steps, 5 — start-sheet, 6 — mast, 7 — window, 8 — sail, 9 — armor, 10 — brace 11 — hicok, 12 — quickdraw, 13 — fin.
Fig. 2. A foam blank Board (unit).
Figure 3. Joint processing of the spars.
Fig. 4. The recess grooves under the side members nichrome wire (bottom left — Latr).
Fig. 5. Gluing in spars.
Fig. 6. Cutting along the markings.
Fig. 7. Processing of curved surfaces of the body by a method of approximation of the tangent.
A template for the body of the windsurfer we will call “block”. Pick up the pieces of foam so that the foam to the box (Fig. 2) with a length of 3650— 3700 mm, width of 650 mm and a height of 140-160 mm (nominal thickness is 138 mm).
Before gluing the pieces of foam are cut and adjusted to each other. If the unit is connected from 2-4 pieces, you can use epoxy glue, when using a greater number of pieces it is better to use benzene. It is applied by brush to the surface of the pieces and then connect them, clutching to each other. As in subsequent operations, it is necessary to remember that the weight of the body should remain in the range of 16 kg extra weight will dramatically reduce ride quality rider.
INSERT SPARS
You can now taken over the production and inset in the block rib-spar that give the body longitudinal stiffness. Their profile can be obtained if the Board is a body to dissect on the theoretical drawing planes parallel to the DP (diametral plane) at a distance of 100 mm in both directions.
The spar is drawn on the plywood thickness of 3 mm (wire two standard sheet, affixing it with nails; joints “in condition” should not be done). Processing of spars do it.”the package” (Fig. 3) to have their profiles turned out exactly the same. Spars prepared for bonding into the hull.
Previously on the block, mark the location of future spars and the ends of scribing the lines drill the hole, relieving the stress concentration. In one of the holes introduces a nichrome filament (Fig. 4). Through Latr it is energized, and its magnitude is selected so that the thread doesn’t became red-hot. The groove is formed by burning, or rather, the penetration of the foam blanks with a hot thread when you move it from one hole to another.
Then, each of the spars is spread on two sides with epoxy glue and insert into the kerf so that the side walls do not protrude beyond the envelope of foam blanks and was not skewed in it. Making sure they are inserted correctly, the unit, tightening the rubber tourniquet (Fig. 5), which ensures correct bonding of the spar.
PROCESSING UNIT
Start treatment unit under the contours of the hull of the windsurfer.
On the lateral sides of the block on both sides is marked the profile of the hull on the DP. The extra foam is cut by a nichrome filament from the deck and floor. Then on the block is plotted as a planned projection of the body again and cut off excess material (Fig. 6).
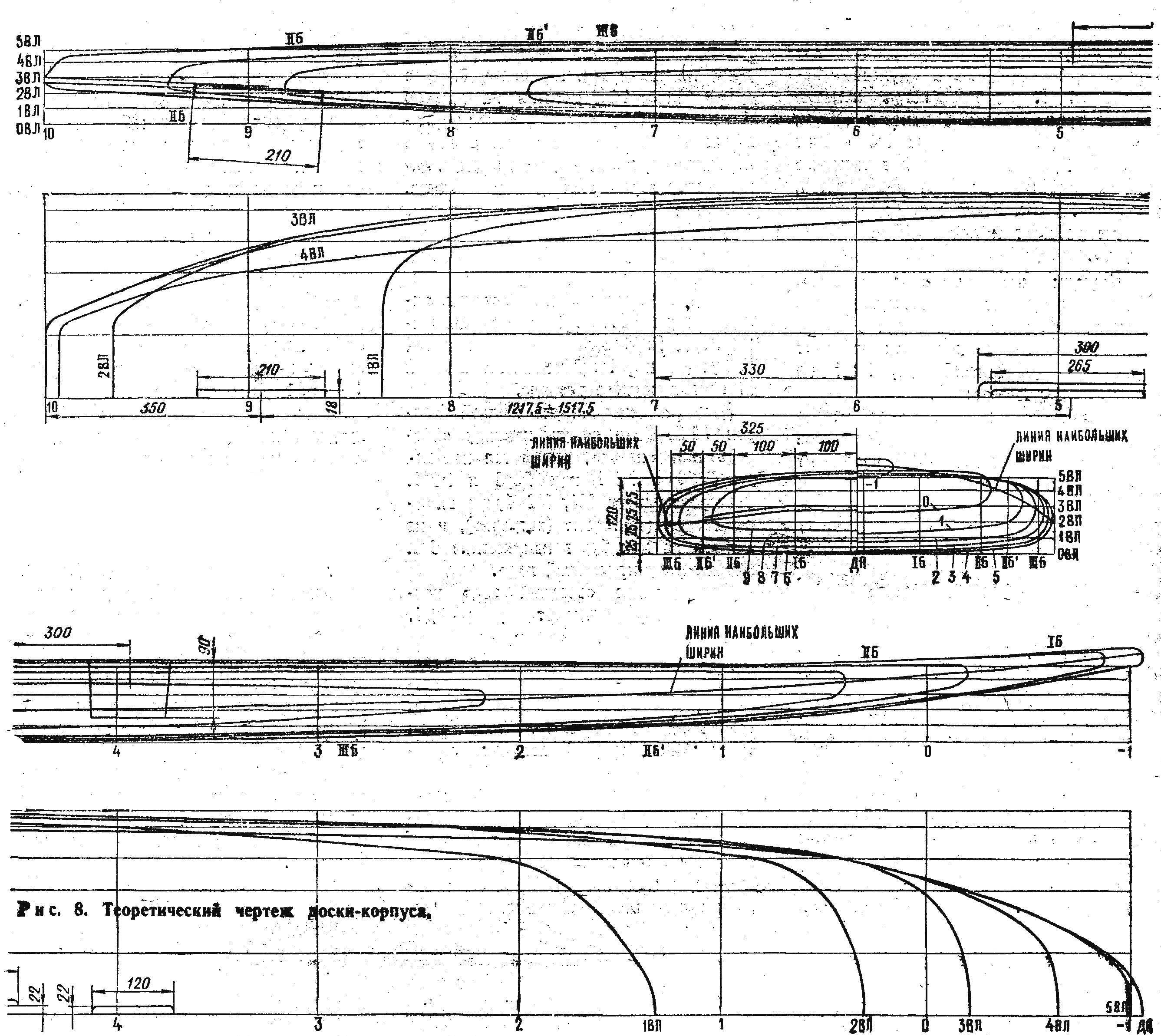
Fig. 8. The theoretical drawing Board-hull
To build the contours of the boards on the theoretical drawing a number of tangents to the surface of the body nd the coordinates of these tangents are transferred to the surface of the foam block with a pre-marked theoretical sections. Connecting the coordinates of the tangent, we will get lines on which to cut the foam (Fig. 7) to bring the block in form to the body of the windsurfer.
The surface is treated by a bastard file or a rasp, and then glass paper to get the desired contours.
THE FORMATION OF THE RECESSES FOR THE STEPS AND SVARTBY WELL
Chertovy the pit and the groove under the steps must not pass water, so special attention should be paid to insulate them from the water.
The groove under the steps and seizure svetovogo well do so.
Wood made models svetovogo wells and recesses for the steps. On them, covering them separating layer (“Edelvays”, wax), vyklevyvajutsja of two or three layers of fiberglass are laid at the same time, chertovy the pit and the groove under the steps. After polymerization of the resin model is immersed in hot water, the wax melts and the laminated items can be easily removed.
Now the resulting forms should be pasted in the body. To do this, after marking their position on the deck in the hull nichrome filament erupt through holes.
The forms are then lubricated on the outside with epoxy glue and inserted into place. In this case, note that the hole for the key steps not end-to-end: the bottom is sawed earlier, the piece of foam glued into the groove side of the bottom.
To give the deck the extra stiffness in the area of fill between the spars with a thin layer of foam is replaced with a plywood overlay.
When gluing parts, it is necessary to monitor strictly preserved their vertical position and alignment relative to the DP.
TAPING FIBERGLASS
First, insert the body ready fin, watching his vertical position relative to the surface of the bottom.
The time has now come stitched with fiberglass. Pasting is carried out in two or three layers, and the first layer takes the so-called stekloreza — thick cloth, providing a shell of high strength and good adhesion with the foam of the hull, while subsequent thin satin weave. For the outer (decorative) layer is good to use bright printed cotton: you can eliminate time-consuming and difficult operation color.
It is necessary to consider that in the area of movement of the athlete deck must be especially strong, therefore, strengthen its middle with several layers of stalloreggi.
Each layer of cloth should be pasted in one go, so the epoxy adhesive must be diluted in such a quantity that it was enough for the entire operation. Glue is applied to the deck surface rubber spatula. Then the casing is applied and smoothed steklobloka from mid-body to nose and stern, and from the DP to the edges. Be careful to avoid bubbles and blistering. To smooth the surface of newly-applied layer of epoxy resin and thoroughly rubbed into the fabric (stains unacceptable!). Next, the fiberglass is trimmed to the perimeter of a wood-hull, leaving a seam allowance of 3-5 cm, which is smeared with glue and bent on the bottom.
After polymerization of the resin deck again treated with sandpaper, removes bumps and redness. Also under the deck covering the second layer.
TABLE PLATOVYM Y BOARD-THE BODY OF THE WINDSURFER
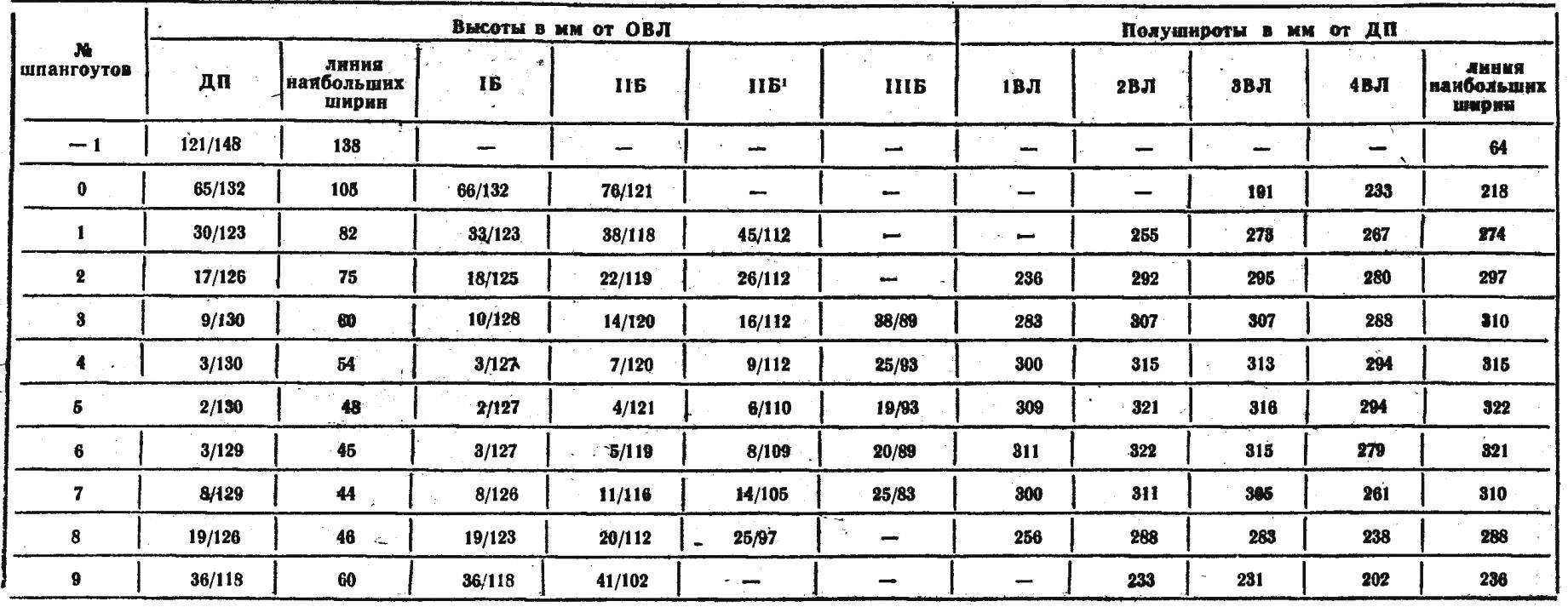
The Board’s surface in the zone of movement of the athlete should not be slippery. That’s why the last just applied the layer of epoxy adhesive should be sprinkled with cork dust or fine sawdust.
The bottom is covered with cloth — as well as the deck, stock, remaining after cutting the fiberglass for the circuit boards, 3-5 cm should go to the deck surface. Thus, on the sides of the windsurfer, that is, in the zone of maximum shock is a layer of glass is double thickness. When working on the bottom please pay special attention to its surface to make smooth. Pits, grooves must be carefully putty and then apply another layer of tissue.
After treatment of the case surface again is cleaned and painted.
MATERIALS:
foam stamps SS-4, PCB, or a combination thereof;
epoxy adhesive with a plasticizer (dibutyl phthalate, toluene, castor oil) to glue small pieces of foam – benzene;
fiberglass or any other sturdy fabric, cotton — for decorative top coat;
plywood with thickness of 3 and 6 to 8 mm;
epoxy or nitroshpaklevok;
any pigment or synthetic dye.