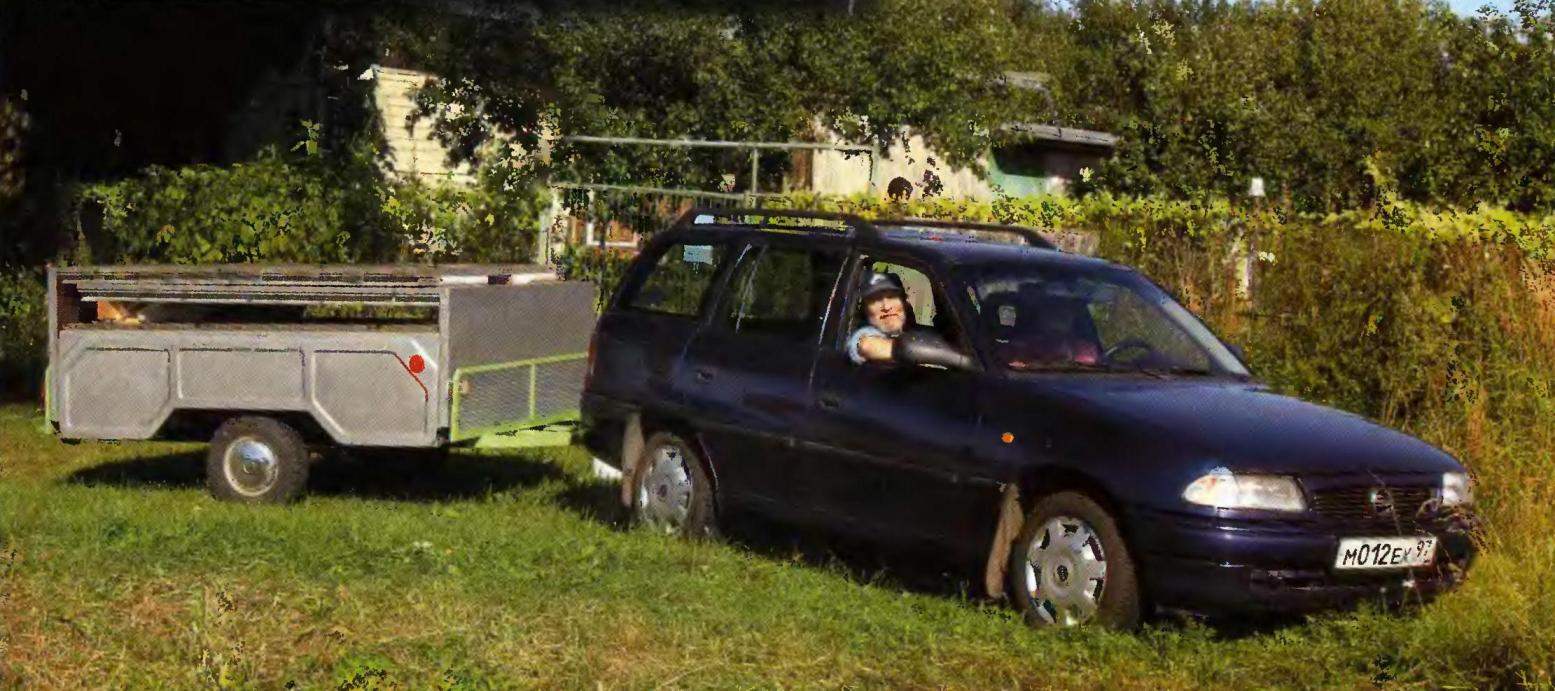
The idea to build the cottage-trailer came up during a previous operation, is also mobile (see “modelist-Konstruktor No. 5, 2005). Let me remind you, the house was prefabricated with a soft top and a smaller size, since it was initially tied to the dimensions of the trailer “SKIF-2M”. Although each element was easy to collect the cottage had everything well together.
New cottage—folding-folding. Boards of its walls attached to the frame of the trailer is hinged (hinged to it by hinges card or piano). To bring the wall to its working position it is necessary to raise them from the stock pile to open like the petals of a flower Bud. Just the process of unfolding takes not hours, but minutes. All installation operations can accomplish alone. And only sometimes need a “third” hand, but it happens in strong wind (or when the cottage is set on the hillside). In these cases, will always help the household.
Design conceived by the mobile giving with a fairly impressive size made it virtually impossible to use-she ready (produced by industry) of the trailer. Serial trailer would still have required a significant rework, so it is cheaper and even easier to make the trailer yourself to be what you need. But the question—any, resolved immediately. I had to think “on paper”. In the end I designed it according to the type of dissolution (with a sliding drawbar and rear subframe) in the transport position, it is not longer than a normal trailer, but the work conforms to the dimensions of the garden But the layout of the elements of the garden also had to break a head, though in the end everything turned out quite simple.
Having defined the size and layout of the component parts of the cottage, proceeded first to the manufacturer of the trailer. The trailer is two-wheeled, but without a common beam bridge. Each wheel suspension—independent, trailing arms. Leverage self-made, rather massive. Their swivel mount to the frame not implemented via silent blocks (rubber-metal bushings), and two ball bearings No. 80205. So the leverage is very easy to “work out” all the bumps in the roads Each spring arm suspension with shock absorbers from the front suspension of the car “Moskvich-2140”
So first disclosed by the wall-“petal”… and the last
Put the second half as the roof…
and giving ready!
The frame of the trailer is welded, douglasiana with five crossbars. All sleepers (except medium) are made with console releases. Editions connected with each side of the lower studs of the framework is rigidly attached to the frame side walls. On top of their lean trim the middle part of the side wall after Assembly of the cottages in the working position.
Front and rear Board have a largely decorative purpose than a practical one except for the fact that they are attached to the reflectors and back—and even light. These side is also rigidly welded to the power elements of the trailer: the first to the pole, and the second to the rear (also retractable) to the subframe.
The side walls are constructed from standard rolled steel rectangular pipe section 65×40 mm, and the cross—pipes cross-section 55×40 mm. Of sortimenti pipes are made and the scope of the boards. But the feathers of the drawbar forks and rear sub frame had to be fabricated from longitudinally welded corners. The fact that each feather had to go inside the spars freely, but without large gaps. Suitable pipes to find it and failed. However, the greatest difficulty in the manufacture of feathers was not fitting their outer cross section to inner cross section of the spars, and the straightness of feathers—very much they “took” from welding. For this purpose, the feathers had to be very carefully to align, and where necessary, and sew on the sandpaper.
Frame front and rear flanges are welded too, from the standard rolling tubes. To harness tailgate even welded the bumper from a square tube 40×40 mm with automotive rubber buffers, and in front on the drawbar is mounted towbar industrial manufacturing (the use of improvised not allowed in the technical requirements).
It remains to decompose the foldable furniture in the room from the patient and to install the equipment in the kitchen behind the sliding door. Things you can hang on the rod in the alcove to the right
The wheel suspension is simple but reliable and effective
As such, the country is stored. To save space, the trailer can be mounted on the back Board
The frames of the front and rear sides of the trailer sheathed by dural sheet and the sidewall is laminated of fiberglass on a self-made matrices.
Floor villas compound. The middle part of it is made of (Finnish) plywood 12 mm thick, faced on both sides with plastic. Here the floor is attached by M6 screws with countersunk heads to the frame corner brackets.
Front and rear part of the floor is made simultaneously with the respective end walls as a single corner unit in the form of a Latin letter L, which serve as a base part of the floor and vertical wall. During Assembly they are installed on the feathers of the drawbar and the subframe via a rubber pad glued to the floor.
The L-shaped element part of the floor and front wall are assembled on a lattice of wooden bars. Only in the bars of the grating are fitted flat against the wall, that is addressed to them more than the wide side, and a semi—edge. In the corner joint of the rail—total, done with a fold. The floor is lined on both sides with 8-mm plywood, coated with outer sides with epoxy-involved in it with the aluminum powder. The walls outside are lined with plastic sheets (PCB) with a thickness of 2 mm, and the inside—the same 4-mm plywood as the floor, only plywood protonirovanie stain. In all elements of the cavity gratings between the wall slabs filled with construction foam P-40.
All the connecting bars of the grille designed on epoxy glue. The leaves are facing, both external and internal (and plastic, and plywood), glued to the grills and the foam “dots” of epoxy glue. Part of the floor of the corner portions of the free ends of the docked flush to the middle of the floor and attached to it three card loops each. If necessary, disconnecting the hinges and removing the L-shaped elements, it is possible to use the trailer like a regular truck.
By the end walls on the vertical sides of the swivel hinges attached to the sash, the extreme parts of the side walls. Piano hinge installed along the entire height of the valves and for sealing pads still covered with leatherette. The joint between the sash and the average side wall in all areas covered by the respective folds (quarters) made in the edges of both parts. To the seam taped seals from thin foam (soft foam or use special rubber).
The middle parts of the side walls is made at the end. The supports for them are the upper edges of the sides with which they are also connected with piano hinges with sealing plates.
In the Central parts of the side walls arranged in a large “blind” Windows, and the front end wall is an opening window: it is edged dural channel covered at the top and a small visor leatherette.
The same vents designed into the rear folds of the side walls, but carved until only one is left. As shown by the operation in the kitchen-hallway gets enough light through one window and the sunroof. Although, frankly, the window need on the other hand, exhaust—in fact there is installed a gas stove and preparing food.
On the back wall is carved doorway, and carved parts are made with non-opening door window. The door is hung on three hinges with overlays of synthetic leather, and its vestibule and the stroke limitation are inside, like the vents, due to the edging.
The walls of the villas are identical in thickness and design’ is based on a lattice of pine bars section 40×24 mm. The bars in the grilles of walls laid flat against the sheathing, that is addressed to them more than the wide side. The outer covering of all walls are the same from sheets of plastic (PCB) with a thickness of 2 mm. Niche lattices between the skins is filled with foam P-40—it does not burn and does not absorb water, but serves as a good thermal and sound insulator. The inner lining of the walls of the kitchen part of the room is made of “refined” (lined with plastic) plywood with thickness of 2 mm, and in the residential part from the usual, tinted with stain and covered with natural lacquer. I believe that this finish is a living room designed for sleep, the most environmentally friendly.
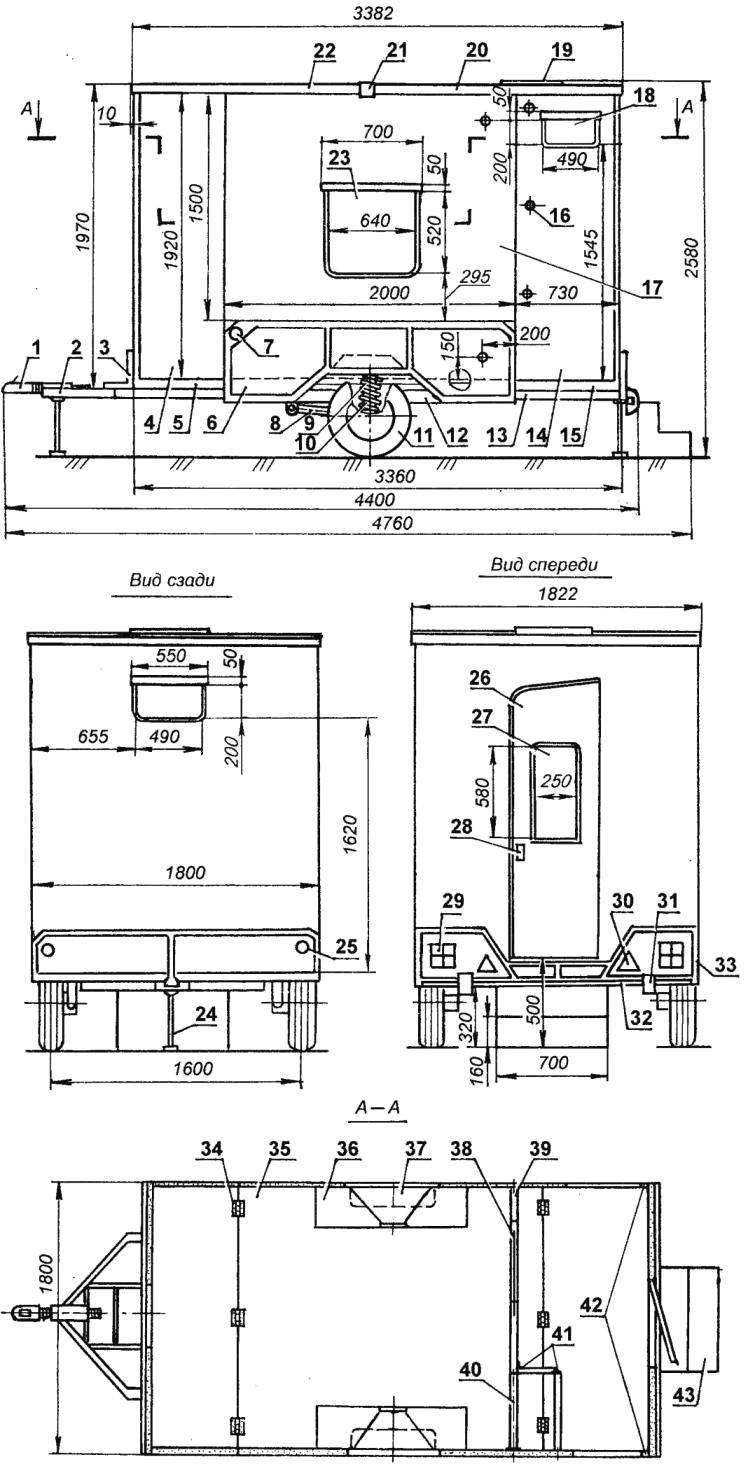
Folding dacha-trailer:
1—hitch (industrial manufacture); 2—pole; 3 — front; 4—front fold of the side wall (2 PCs); 5–front L-shaped element (part of the floor and lateral wall); 6— lining the side of the trailer side (laminated GRP); 7 — side (yellow) reflector (2 PCs); 8…….the lever arm (2 PCs); 9 – spring suspension (from the GAZ-21 “Volga”, 2); 10-shock absorber suspension (from the car “Moskvich-408”, 2); 11 – wheel R12 (sidecar, 2); 12 — frame of the trailer; 13 — rear subframe; 14-posterior fold of the side wall (2); 15 — rear L-shaped element (part of the floor and end стtнка); 16 – a bolt M8 (10 PCs.); 17 -side wall (2); 18 — pane (Plexiglas, bordered by dural profile, with the visor leatherette 3 PC; 19 —flanging Luke; 20 rear half of the roof; 21—trim (leatherette); 22 — front half of the roof, 23—window, dwelling (Plexiglas, bordered by dural profile with the visor leatherette, 2 pieces): 24 — backup or Jack; 25 — front (white) reflector (2); 26—entrance door; 27—window door (Plexiglas, bordered by dural profile); 28—door-handle-grip; 29 —rear signal lights (2 PCs); 30–rear (red) reflectors; 31 buffer rear bumper (rubber. 2); 32—rear bumper; 33—rear Board; 34-card swivel hinge (6 PCs); 35 — the middle (main) part of the floor (plywood, faced on both sides with plastic); 36 — steel insert floor (s2 sheet-4 pieces); 37—cover of the wheel housing (steel sheet s2); 38 — sliding door (plywood, s10); 39—internal partition; 40—connecting rod (pipe Ø28, 2); 41 —piano loop swivel (6 PCs); 42—angular swivel with a sealing lining (piano loop, leather, 4 pieces); 43 — side porch
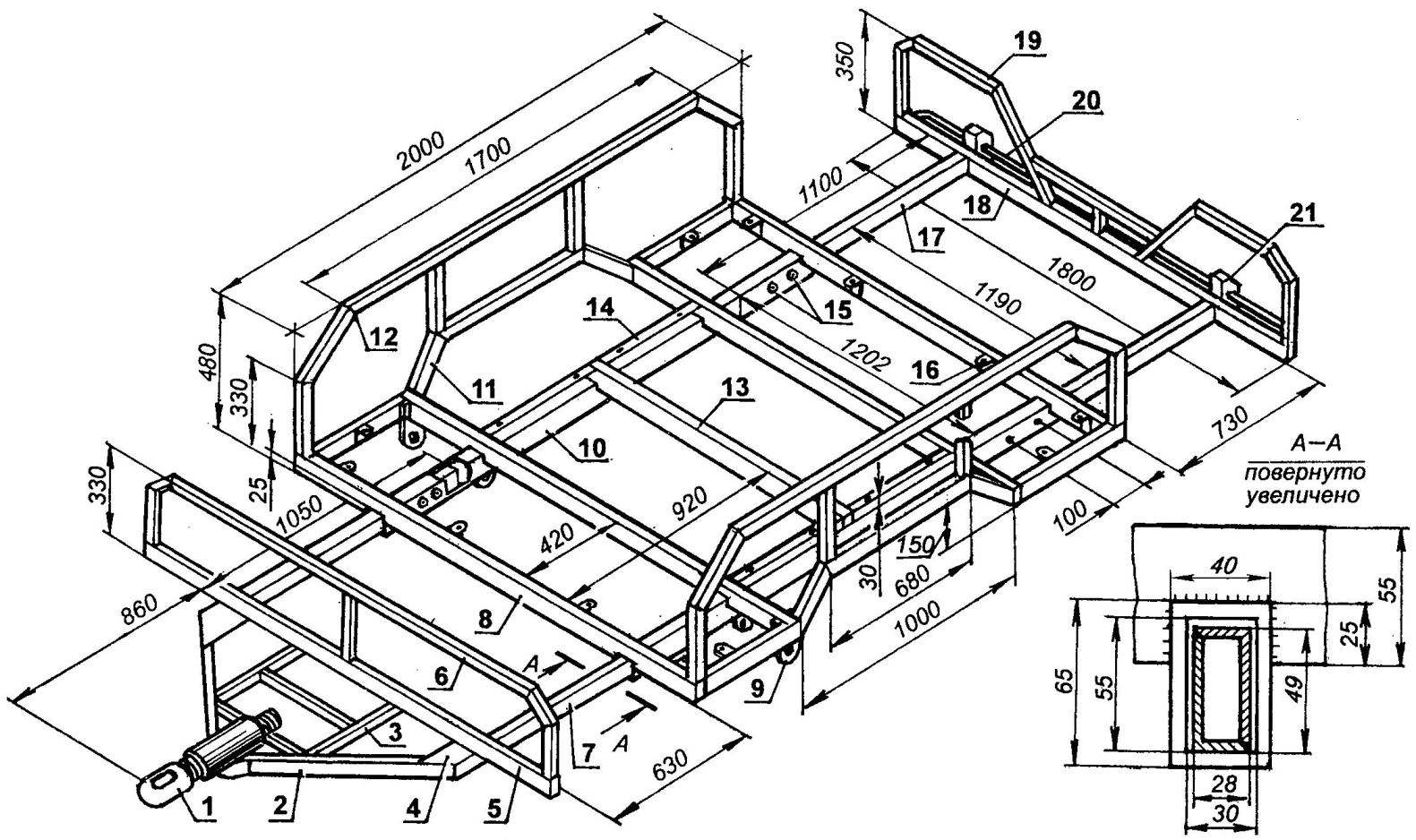
The frame of the trailer:
1 — coupling; 2 — beam beam (pipe 55×25, 2); 3—supporting frame for spare wheel (25×15 roll-formed channel, steel sheet s2); 4 – gusset plate (steel sheet s2, 2); 5 — piping front side (tube 40×25); 6— arc front side with stand (tube 20×20); 7 — feather tongue (trumpet 49×28 — welded along the two corners 45×28); 8 — transverse ordinary frame (55×40 tube, 2 PCs.); 9—eyelet arm (steel, sheet s5, 4 PCs); 10—longitudinal (coarse 65x40x5, 2); 11 – rail side walls (pipe 40×25, 2 pieces); 12—arc side Board with racks (tube 20×20); 13—the average cross member (tube 55×40); 14—supporting shelf of the middle part of the floor (bent area 30×20, sheet s2,4x); 15 — M16 kills to build welded to the side members (8 PCs.); 16— mount the middle part of the Iola (bent area 30×20, sheet s2. as required); 17-a feather of the rear subframe (tube 49×28 — welded along the two corners 45×28); 18—piping the rear side (pipe 40×25); 19 —arc tailgate with a bunch and stand (tube 20×20); 20-bumper (tube 40×20); 21 buffer (rubber, 2 PCs.)
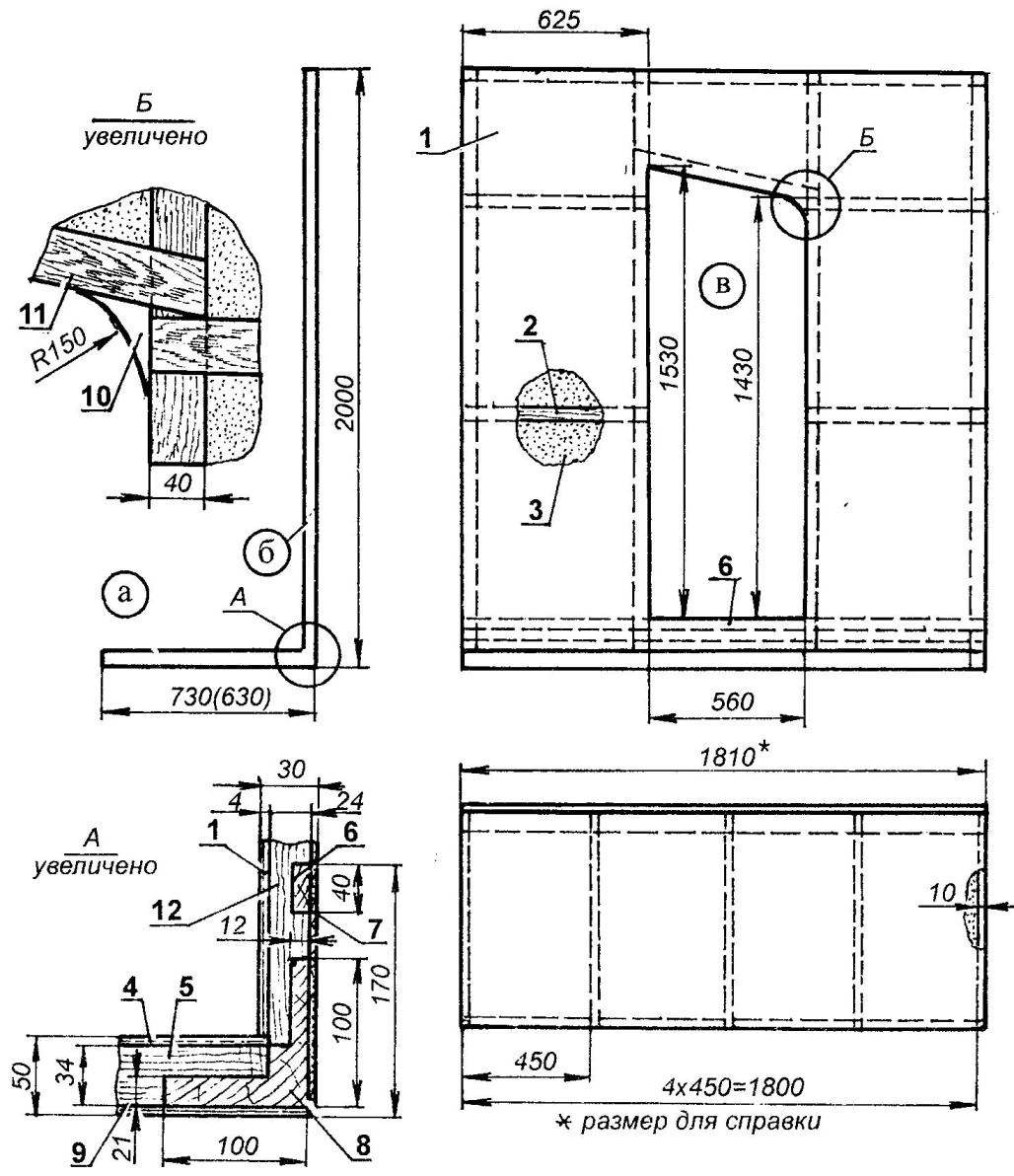
Corner element (a part of the floor; b — the end wall; the doorway):
1 — internal paneling (plywood, s4); 2—grille end pieces (bar 40×24); 3 —sound-filler (foam P-40); 4 — internal floor covering (plywood s4); 5 — edge-bars of the grid floor (plywood s10, 5 items); 6—threshold (bar 40×12); 7—outer casing end walls (Micarta, sheet s2); 8-package (100×100 timber rebated); 9 — the outer covering part of the floor (plywood s4); 10 -figure insert (Board s24); 11 — lintel (the bar 40×24); 12-front wall (bar 40×24, 4 PCs.)
Entrance door:
1 — trim doors (aluminum I beam profile cut to one or, sometimes, two shelves); 2—bar 40×24 grid; 3—sound-filler (foam P-40); 4—border window (dural channel); 5—window (plexiglass s5); 6—piano hinge; 7 — figure insert (Board s24)
The left-hand side wall (middle part) and left rear (right — mirrored and no holes with a diameter of 9) flap (front flap runs without a window, its dimensions in parentheses):
1 – the outer shell (Micarta, sheet s2); 2—grille (bar 40×24); 3 —thermal insulation filler(foam P-40); 4—inner sheathing (plywood s4); 5—piano loop
Internal partition wall (a door section; b—side section of the niche; the front section of the niche):
1 —paneling from the living room (plywood s4); 2—door (plywood s10); 3 — threshold of the doorway (bar 40×22); 4—doorframe (bar 40×22); 5—lintel of the doorway of the bar 40×22); 6 — rod (pipe Ø22. 2 PCs); 7 — bar 40×22 grille; 8—piano hinge: 9 — plate (steel plate 80x22x2, 6 PCs); 10—nut M8 (6 PCs.); 11 – screw (5×25, 12 PCs)
Ceiling-the roof (back half, front half runs without a hatch and lining):
1 — connecting beam (beam 70×52); 2 — pad (leather); 3-longitudinal slot of the beam (beam 52×52. 2); 4—transverse edge (plywood s10, 3). 5 — slot transverse beam (rail 52×52); 6 – Board hatch (plywood s10, 2); 7 — upper sheathing (plywood, sheet s4); 8— the lower sheathing (plywood, sheet s4); 9—sound-filler (foam P-40)
The laying pattern of the elements in the trailer for transport or storage:
1 —the frame of the trailer; 2–the floor of the trailer; 3 —folded double partition; 4—halves of the roof (rotated 90°); 5 — left side wall; 6—right side wall; 7—front angle element with folded wings; 8—rear hub element with folded wings; 9…..rear subframe in a retracted position; 10—drawbar in the retracted position; 11—solid spacer (as required); 12 soft padding (as required); 13 side Board
![Use of U-shaped brackets for mounting walls of the cottages]()
The use of U-shaped brackets when mounting the wall garden:
1 — side panel; 2 — fold; 3 — bracket-retainer (dural channel)
In terms of the area of the estate is divided into an inner partition into two rooms: lounge room and kitchen-entrance hall. The premises are connected by a doorway to sliding plywood (10 mm thick) door inserted inside partitions during its production (between the wall). The partition is breakable, consists of three parts, connected with hinges (the joints are covered with pads made of leather). After installation two short of the partitions form the side of the dwelling is small, but the height from floor to ceiling, niche for stuff. Part of the septum is assembled on wooden gratings of bars section 40×24 mm and covered from the kitchen leaves “ennobled” plywood, and the side of the room—the usual plywood (4 mm thick).
A few words about the production process of the walls. First is the bars. Her vpoldereva bars are joined and connected with epoxy glue. Then on flat ground (floor) unfolds one of the skin and to it is attached the grille and progreetsya on the curing time of the adhesive. Then the cells are filled with Styrofoam sheets of a thickness slightly larger than the bars. Previously on the inner surface of the covering applied dabs of glue. Giving time for the glue cured, level the surface of the foam flush with the bars using a hot nichrome wire, is applied on those other smears of epoxy and glued other trim. If you have experience of such work, operations can be combined.
The ceiling and roof of the cottages combined are a single design, but consist of two halves (conventionally— front and rear, since they can be interchanged). The halves differ only in that one of them is attached a strip of waterproofing material, which overlaps the joint between the roof parts. Stacked bars slightly raised above the plane of the roof, forming cross ribs, intercepting and outlet got on the roof water.
There is another difference between the two halves of the roof. One of them made the hatch size in the world 450×380 mm flare above the roof (so that water would not flow). Through the hatch you can climb to the roof to sunbathe or carry out photo or video. The hatch lid made of yellow plexiglass, and therefore in the room even in cloudy weather seems to be Sunny.
Filling the roof with an emphasis on the front and rear parts of the floor: bars stiffeners section 52×10 mm made of 10 mm plywood and is also installed on the edge; niches filled with foam, lined with plywood. From the outside the roof is covered with two layers of fiberglass epoxy with zameshennoy it with the aluminum powder and the inner side are covered with sanitized 2-mm plywood white color.
The roof garden has an important and constructive: it connects all the walls and locks them in an upright position. To this end, the ceiling edges around the perimeter of the groove is made a groove width to the thickness of the walls (with minor allowances) and a depth of 30 mm.
In the stowed (transport) position of the cottage is laid in the following sequence. First, on the floor of the trailer, spreading a soft strip, it is folded in two partition, and the top (to just above wheel arches) blankets and mattresses (or set of remote pads). Then, one another, the halves of the roof, rotated by 90° relative to the position in the collection. Then close the sash (clamped to the end walls) and in turn down the side walls and the last—corner pieces: first the front and then the rear. Well and at the end of the spars to the limit and pushed through the joint holes are bolted M16 feathers of the drawbar and the rear of the subframe.
When laying the garden in the stowed position between the contacting surfaces of the stacked soft gaskets (or used “second term” clothes), and the between—spacers made from soft wood or hard foam. In the cavity between the niche and items to pack, inventory, etc.
Build cottages in the operating position is, as they say, in reverse order, but with some peculiarities. Before you select a relatively flat area, and such that and relax it was nice, a lot of damage is applied. First turn away the bolts in the spars, of which extends the rear subframe in the new situation, again, is fixed by bolts. Under the corners of the set stands or jacks. The feathers fall pre-committed “lift with rotation” of the rear L-shaped element. The same operation is performed from the front of the trailer with the drawbar and the end wall. Then rises one of the side walls, and to her opening, pressed against the sash. The same exercise on the other side.
When performing these operations to insurance, use of U-shaped brackets, clips from a small section of aluminum channel to lock the side walls from stalling under the pressure of the wind or the tilt of the trailer (brackets removed during installation of the roof). After that inside the garden of the mounted partition: with right-hand side it is bolted М8ц to mid side wall, and the left — to the back of the leaf; then fixing the rod.
In conclusion, from the floor up (above the walls) the first half of the roof (without the lining), rotates 90° (not to be confused—in what direction, and then have to turn 180°) and carefully, so that the upper edge of got in a groove, placed on the wall. The same is done with the other half of the roof, adjusting, if necessary, a protective waterproof overlay.
After installation, testify under corners of a trailer or the drawbar and the rear subframe are wooden poles or props from scrap materials. Can be used for these purposes, and the Jack that came with car. Near the door is a folding porch or a small cut banded from opposite sides of the logs, in order to make it easier to enter.
The living room is equipped with folding furniture, kitchen portable gas stove and refrigerator. In the tapered part of the kitchen (where acts of dwelling niche) is put on the pallet and arranged shower-wash basin.
V. WHEELS
Recommend to read
ECONOMICAL PN-70
As a stand-alone power source flash FIL-46 I use a voltage Converter PN-70, manufactured by Kharkiv enterprises "ECHO". In the process of operation of this device revealed its drawback:...
“FALSHSTENA” WITH A DOORWAY
Many citizens in the Soviet Union had to pass through the panel, "building", built in the second half of the last century. These homes are designed for 50 years of operation, will...