The proposed design is a four-section, three-man boat with load capacity of 320 kg In tourist trips she, being dragged to the Bank, turns in a fairly spacious “tent”, especially if you throw on top of a piece of plastic film. The boat is so simple that it can make even a person unfamiliar with shipbuilding and have only basic skills working with wood. To manufacture do not need special equipment and space, the whole boat is going in the room of a city apartment. It is made from widely available materials that can be Purchased in stores construction And household goods. The cost is Approximately 20-30 rubles (in passing it should be noted that for the registration of boats is necessary to keep all checks and receipts).
The choice of dimensions (3. 3X0. 98X0,32) due to the need to carry a “Crab” on the trunk, the desire to make the ship suitable for a wide variety of sailings a group of 2-3 people.
The boat is designed as a propeller, but due to the reinforced transom can be fitted with outboard sail area of 3.5 m2 or outboard motor type “salute”.
The housing consists of five compartments — the “boxes” that fit together when assembled and upholstered in steel cable. From the shift of the side sections prevent the protrusion and a socket in the side stringers (RUB the bars). This design allows to collect a boat in a cropped, double option: middle (third) section is not installed, and the cable covering is taken shorter.
Bottom stringers are installed on the outside of the boat — this creates the effect of the keels, which increases the stability of the boat on the course.
Rise fore and aft provided a small blockage inside of the abutting sections (4-5 mm) when adjusting, greatly improves seaworthiness.
Start building should be making a paper pattern of all side, bottom and bulkhead plywood parts. Then proceed to cutting of plywood, given that all the pieces should be cut along the grain of the outer layers (shirt). Made a small allowance for the end treatment. Details of the sides and bulkheads are cut in pairs. Then cut slats for longitudinal and transverse framing. Blanks should be marked by double numbering: the first digit — number of the section, and the second n items (e.g., 3-11, 45, etc.). Pattern pencil apply precise contour seats attaching parts kit (strips). Both surfaces are lubricated with adhesive, they are pressed against the rail. Joints connect “vpoldereva”. To protect from slipping the corners temporarily primatyvajutsja small nails (not completely). Immediately until the glue not frozen, the Board is flipped and the plywood slats reinforced with screws 10X2 “snake” with a step of 50-60 mm.
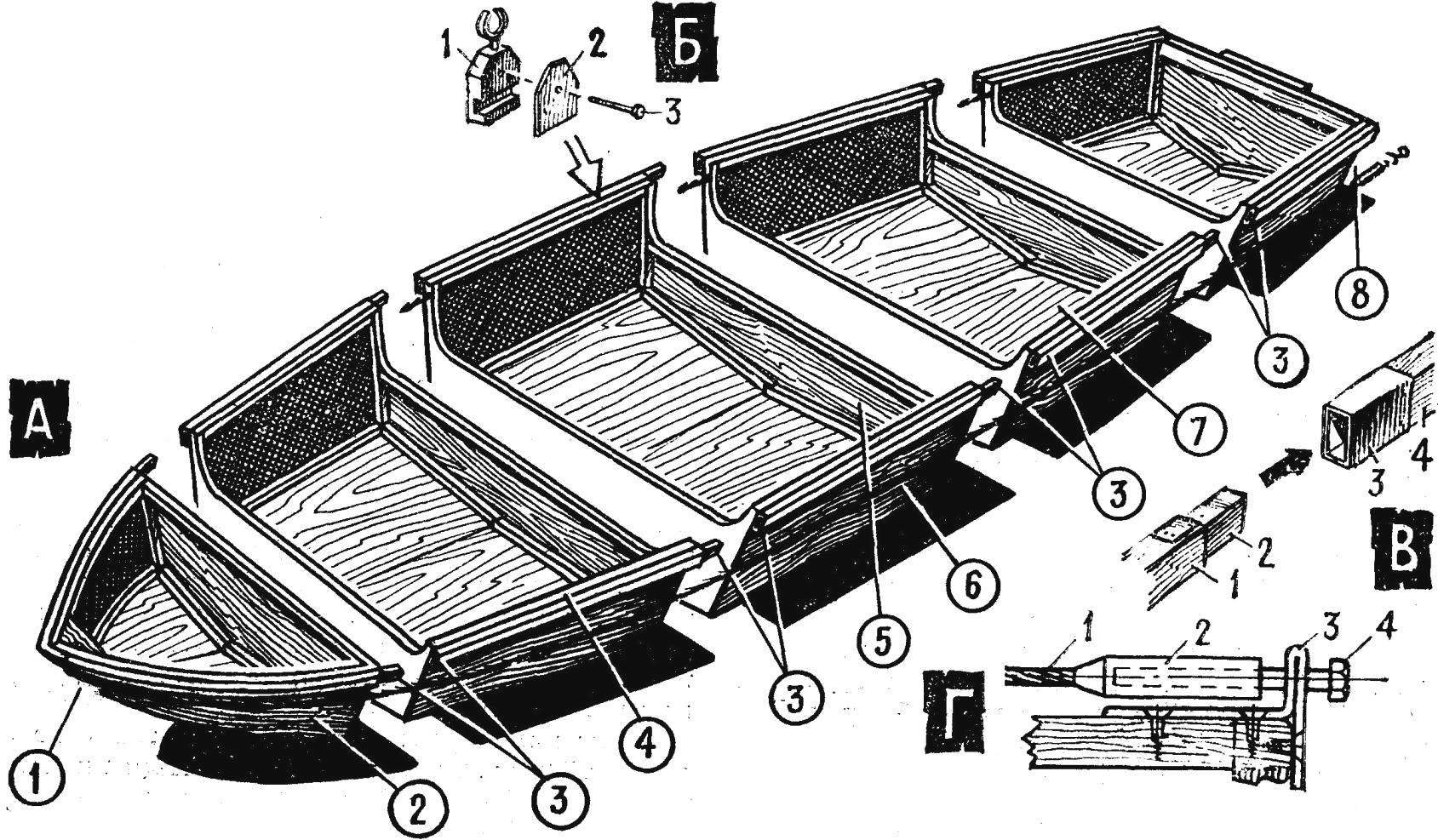
Fig. 1. “Crab” — General view and design details:
A — body (in one piece): 1 — cable tie, 2 — nose section, 3 — butt nodes of the outer fendering, 4 — inner fender 5 — end partition (membrane), 6 — sheathing Board (plywood with a thickness of 3 mm), 7 — plating bottom (plywood thickness of 4 mm), 8 — tensioning device. B — mount oarlocks: 1 — podulichny, 2 — panel, 3 — pinch bolt. In the design of the butt of the node of the outer fendering: 1 — fender 2 — spike, 3 — socket (roofing iron), 4 — fender the following section. Mr. crimper cable: 1 — wire, 2 — threaded sleeve, 3 — bracket, 4 — tension bolt.
Similarly, are done harvesting the internal bulkheads and transom.
For the forward section of rectilinear rods cannot be used — they are made of laminated plywood. To do this, cut into 16 narrow (30-32 mm) strips of plywood with a length of 650 mm. thick Board size 700X200 mm draw life-size outlines of the upper (fender) and the bottom (bilge stringer) slats. The contour fill 75 mm nails to a depth of 15-20 mm. Then strip-blanks lubricated with glue and inserted into the pattern formed by the nails. So tightly to pull the strips during drying, the top of the nails is skipped snake twine. A second pair of blanks are glued similarly. Edge glued blanks are treated with a file and sandpaper.
Oak vytesyvajut the stem bar (bow bar). It made the inset grooves for the fastening of the ends of fenders strakes and bilge stringers. Then bilge stringers, stern and bow bulkhead are joined with glue and screws, and the top of the stem communicates with the top of the bulkheads with a temporary strap for the screws. Then immediately glue and screws to put the workpiece on the sides and top of their “embrace” of the workpiece fenders bars. You need to check the symmetry of the whole structure.
The next day, when the glue “grabs”, place the bottom of the deck, where a pre-cut hole 180X200 mm for the rear hatch.
Then on a sheet of paper (preferably graph paper) draw one inside the other squares and the contour of the bow section corresponding to the size of the Upper part of the section the future of the boat — this will facilitate the gluing of the sections and eliminates the need to correct the distortions.
On the floor on a sheet of paper — the pattern going on glue and screws all sections — first, the sides and bulkheads, and then the bottom leaves. Then adjusted and installed RUB rails (with the studs and sockets) and the boat is going to temporarily bolt the tie-rods and processed with a file and sandpaper. This operation should be undertaken twice.
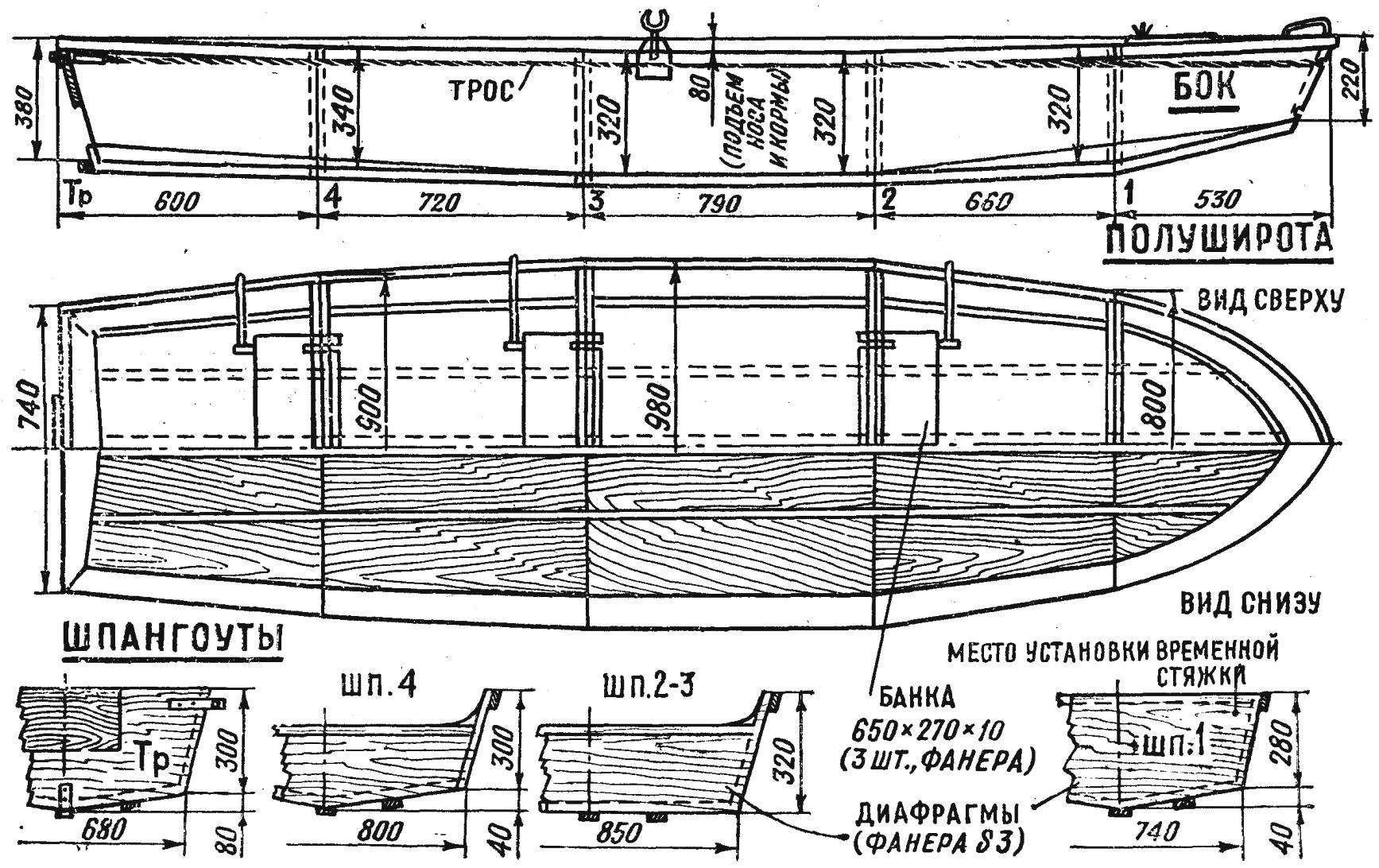
Fig. 2. The principal dimensions of the boat “Crab”, the construction of the hull and frames.
All sections and blanks the bottom of the double-stringers are impregnated with hot linseed oil and after the second impregnation aged 4-5 days. Dried sections lightly cleaned with sandpaper and once again gather together for the final control of all joints. Then section outside wiped with a swab soaked in petrol or white spirit, for degreasing of the surface.
Then the bottoms of all five sections are pasted over with fiberglass on epoxy glue with the addition of 10-15% of acetone as diluent. The edge of the fabric folded over and down to side to 50-80 mm. at the same time narrow strips — scraps fiberglass on the same epoxy glue fixed all external corners of partitions. Immediately, until the resin has not hardened, on the bottom overlap oiled the same glue the bottom stringers and are secured with screws 15X3 with step of 80-100 mm.
Two days after curing the resin the boat again treated with sandpaper (especially at the edge of the glass), and then painted the first coat of paint. After the paint dries, install all the metal parts and the wiring is tightening the cable, fitting seat — cans and the cover flap.
Holders oarlocks are made by sclavonian of pieces of duralumin suitable thickness. In the extreme case of oak or beech wood with wrought steel strip.
Paddles (collapsible, hinged) from three cuttings from shovels, aluminum tubes of suitable diameter, tightly entering one another, and aluminium blades size 150X400X1,5 mm.
In the second, third and fourth sections it is desirable to make light Elan yo length sections width of about 400 mm. They are made of strips 10X15 mm in increments of 25 mm, connected by three narrow transverse strips of duralumin.
The cable is fixed by a loop in the tensioner from the keel point of the transom; he further goes on both sides of the keel stringer to stem; on the stem double-cross lines in the grooves under the pad, and returns to the stern on the sides under the fenders timbers; the ends of the rope fixed in the lanyards — tensioners in the upper corners of the transom.
Time to build a boat will require approximately 150-200 hours (it depends on the carpentry skills of the Amateur).
I. MALEVICH