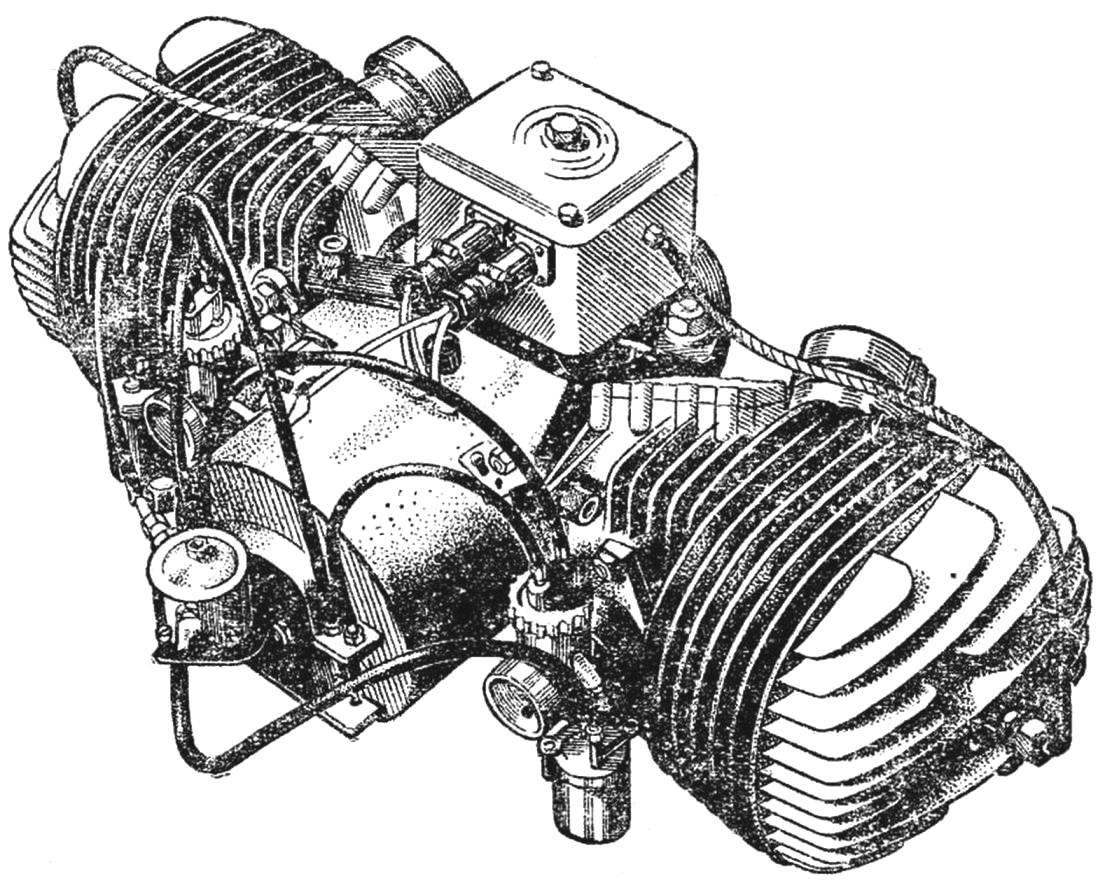
The most radical way of solving problems — making homemade motors using parts from the production motorcycle. The readers of “M-K” is known for such motors: BB-1 design Hand-and L. G. Buyanova, engine L. Komarov and V. Fedorov, AG-1 designed by A. Gerashchenko.
Here we describe the principles of designing and manufacturing two-cylinder boxer engines also with maximum use of standard parts. An example would be an engine built and tested by A. Antipin from the village of Priyutovo, Bashkiria (Russia).
It should be mentioned that the circuit of the motor A. Antipina when it is developed in OKB “M-K” made a number of upgrades. Their goal is to increase the reliability, the desire to simplify machining and to exclude certain technological operations. In addition, design modifications significantly improve the accuracy of manufacturing of main parts, which increases the service life of the engine.
There is no doubt that two-cylinder engine with opposed cylinders has a number of advantages over inline-Sparky from two single-cylinder and single-cylinder even more. It is much better balanced because the reciprocating motion of the two pistons counter, and hence the moments of the forces of inertia are mutually balanced. It also improves reliability and facilitates starting of the engine. Minor problem in one of the cylinders not pulling the engine down, and, at least, there is always the opportunity to “hold on” to the place of repair. I say less weight and size, ease of ignition system, as well as good conditions blowing both cylinders and you’ll make a conclusion: it is necessary to take on “oppozit”!
The design of the proposed engine (Fig. 1, 2) is simple. It can be assembled based on parts from the engine of the motorcycle IZH-P-2, IL-W-3 or IL-56. For this engine, you want to make yourself only the crankshaft and crankcase.
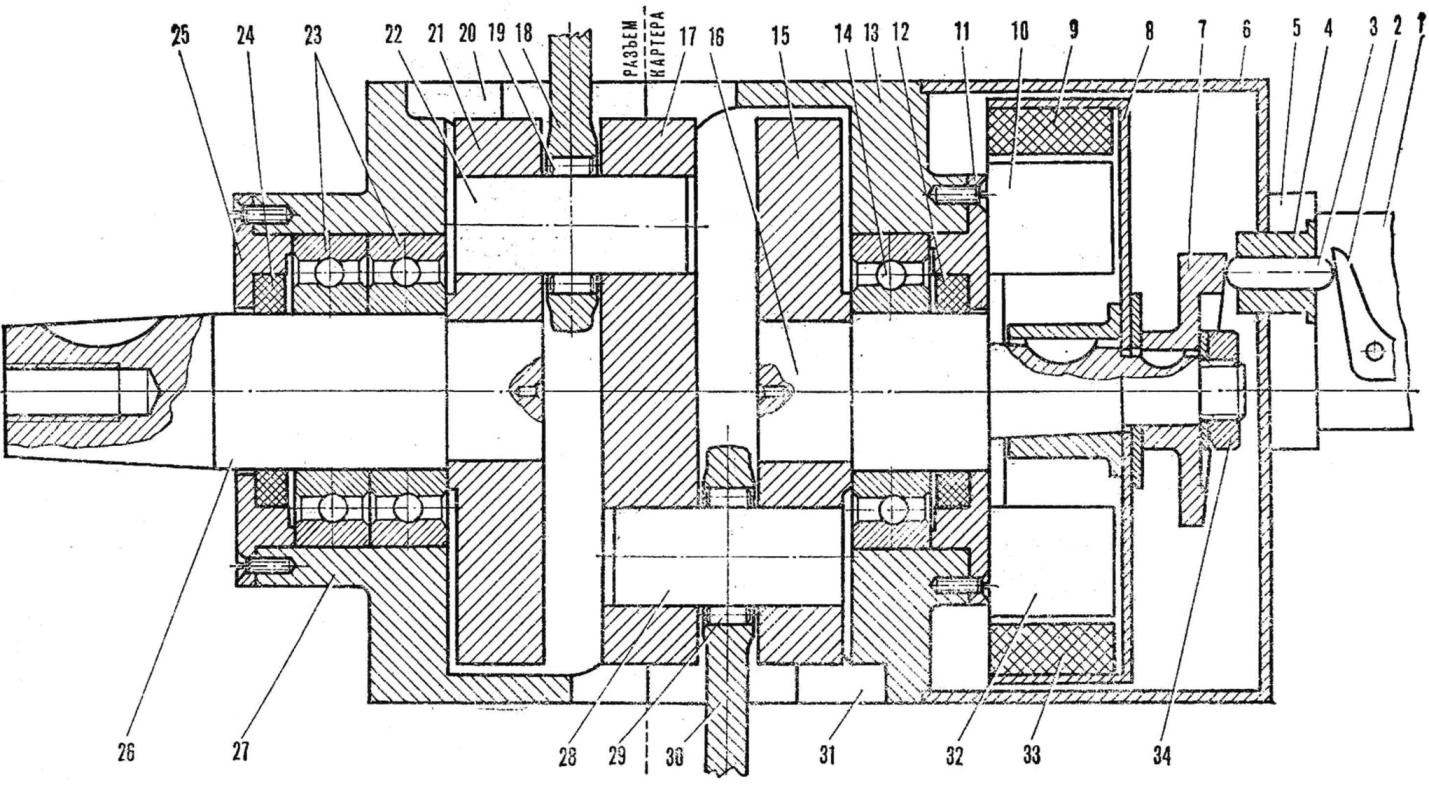
Fig. 2. The layout of the engine:
1 — body pump, 2 — the lever of the fuel pump 3 to the rod drive pump, 4 — bushing, 5 — spacer, 6 — cover maggino, 7 — eccentric fuel pump, 8 — piece anchor maggino, 9, 33 — magnets of the armature 10, 32 — armature winding, 11 — front cover crankshaft bearing, 12, 24 — glands 13 — the front half of the crankcase, 14, 23 — crankshaft bearings No. 208, 15 — front cheek of the crankshaft, 16 — radical front axle crankshaft 17 — average cheek of the crankshaft, 18, 30 to the connecting rods, 19, 29, the rollers of the lower connecting rod bearing, 20, 31 — holes for cylinder liners, a 21 — rear cheek of crankshaft 22, 28, the fingers of the lower connecting rod bearing 25 cover rear crankshaft bearing, a 26 — rear axle is a radical of the crankshaft 27 is the rear half of the crankcase 34 — nut of fastening of a Cam of the fuel pump.
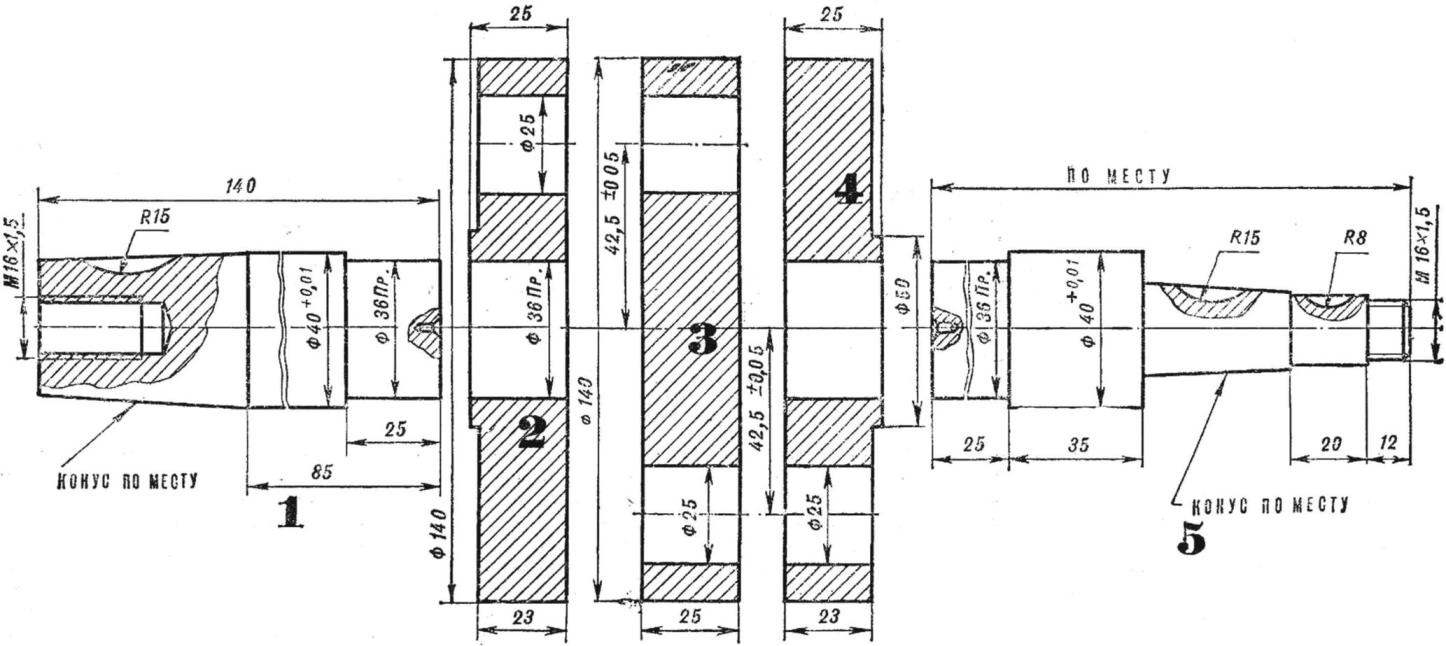
Fig. 3. Crankshaft:
1 — rear axle, 2, 4 — external cheeks, 3 — average cheek, 5 — front axle.
The crankshaft (Fig. 3) is composite. The root axle and the lower connecting rod fingers placed on it during Assembly. For all the details recommend steel 18ХМЮА or 40S.
Procurement of indigenous axles with center holes are machined on a lathe and have the allowance on the further processing of 1.0 mm on a side (with the exception of the seats, intended for pressing in the cheeks of the crankshaft — they are chiseled right up to nominal size). Three discs — billet cheeks of the crankshaft — also have the allowance of 0.5 mm on a side. They are then polished on surface grinding machine and mark the holes under the root axle and the fingers of the lower heads of the connecting rod. The hole is drilled and chiseled to the nominal dimensions on the faceplate or in chetyrehochkovym the Chuck of the lathe. However, note that the mating of these holes parts pressed into them, so the size of the holes should fit to the press fit.
The order of Assembly of the crankshaft next. First, using a screw press in the extreme cheeks of the shaft planted the root axle. Further, half of the crankshaft is mounted in the lathe centers for treatment of the cheeks, cones and seats on the axles to the nominal size. After this, in extreme cheeks zapressovyvajutsja fingers lower heads of the connecting rod going to the lower connecting rod bearing and Central drive of the flywheel zapressovyvajutsja fingers lower heads of the connecting rod. The holes in the cheeks of the flywheel is not broke, chamfers, they are not removed, and to ensure the entry into them of fingers the ends of the latter are rounded.
Assembled crankshaft is mounted in the lathe centers (rods in this case are fixed) for the treatment of middle of the disk of the flywheel to the nominal size. Then the cones are milled keyway and at the ends of the shanks of the shaft threaded. Before installing the connecting rods and bearings Assembly all parts (fingers of the lower heads of the connecting rod, bearings, washers, pistons, rings, piston pins), be sure to choose the weight: the difference between sets of the left and right cylinders should not exceed 2-3 g. failure to comply With this condition, the inevitable imbalance of the engine and unwanted vibrations during its working.
Carter (Fig. 4, 5) is a machined on lathe and milling machines casting of aluminum alloy AK-4-1 (can be melted also outdated automobile pistons). Treatment of this part of the special equipment is not required. The inner diameter of each half (see Fig. 5) Carter and seats bearings chiseled on a lathe with a single installation. Then the parts are joined and they drilled the holes for the tie rods and the landing sleeve. Further, holes zapressovyvajutsja grommet half crankcase studs shrink, after which the outer surface of the casing are milled.
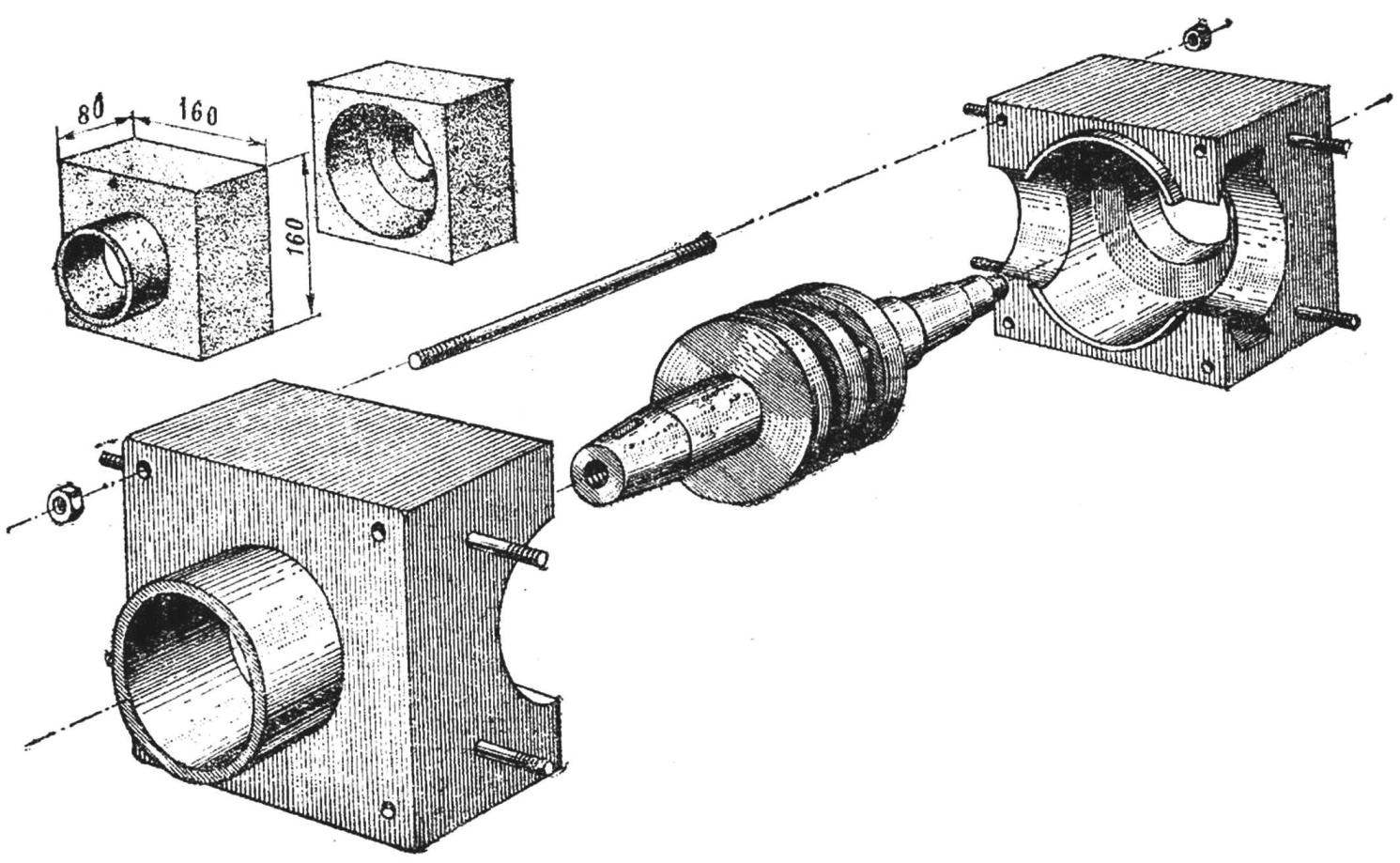
Fig. 4. Billet halves crankcase Assembly diagram
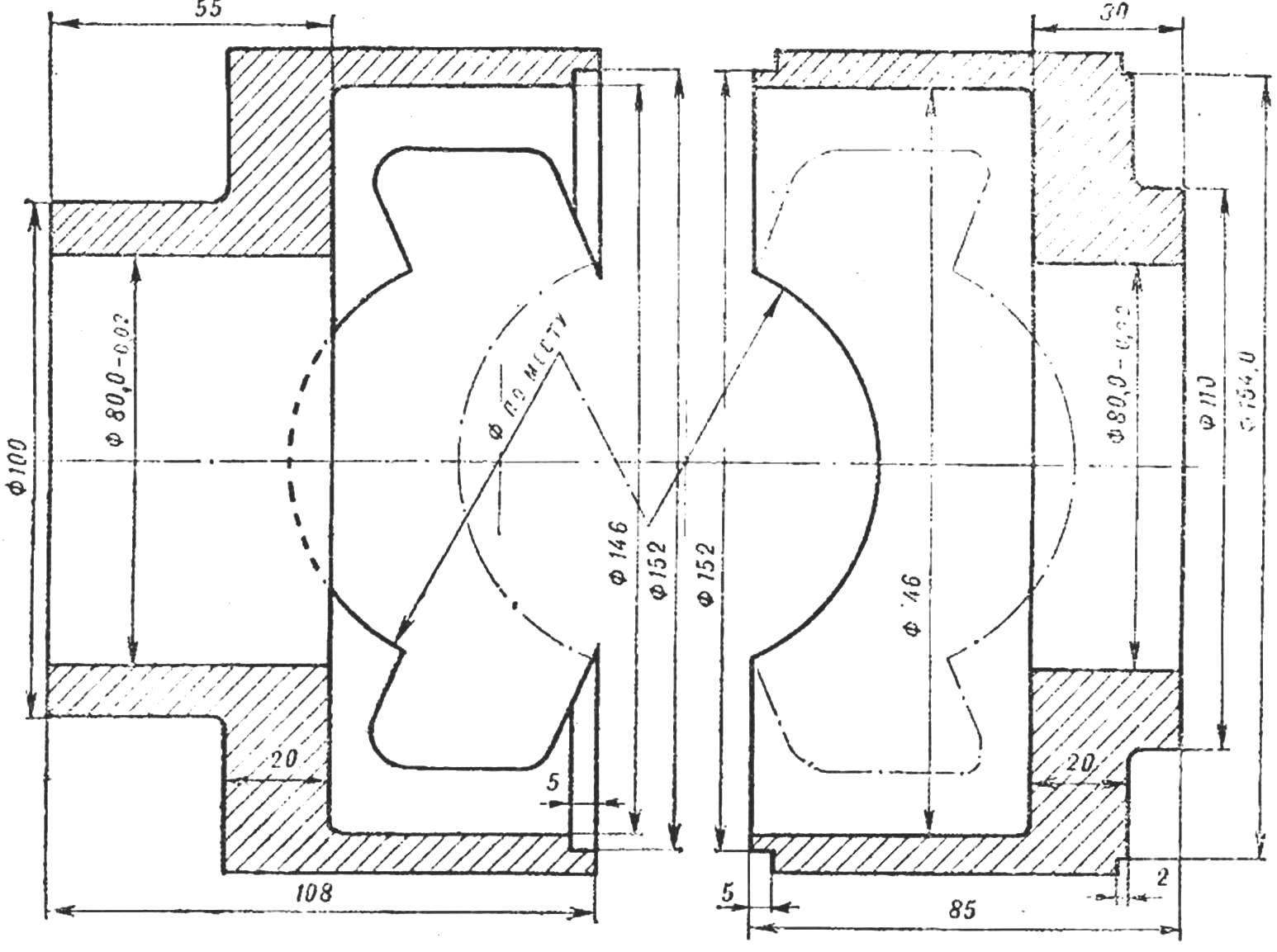
Fig. 5. Front and back of the case.
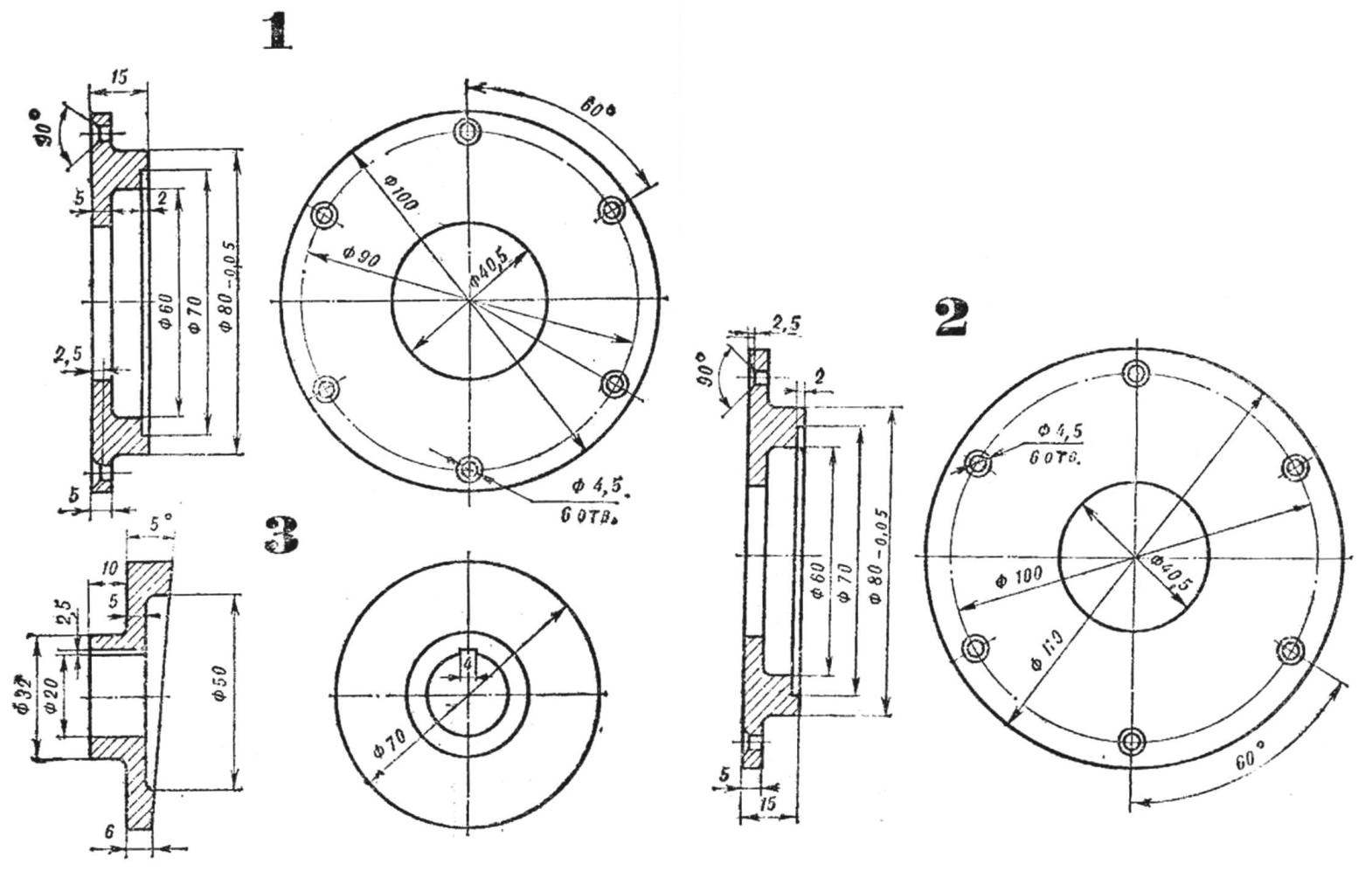
Fig. 6. Homemade engine parts:
1 — the lid of rear main bearing, 2 — cover, front main bearing, 3 — Cam actuator fuel pump
Boring seats under the magneto cover crankcase must be installed in chetyrehochkovym Chuck of a lathe and center the holes the bearings. It remains to mark the holes for the cylinder liners, pins and the bypass window and cut them up on lathe and milling machines.
Should not be surprised that in the drawings no engine many sizes: most of them depends on the finished parts.
Figure 6 shows drawings of the bearing cap and the eccentric of the fuel pump (engine car “Zaporozhets” or boat motor). Using the latter will allow to get rid of the eccentric drive. Besides the magneto cover will in this case be made of any suitable material (e.g., fiberglass). As you know, the fuel pump of the boat motor works from dilution in the crankcase, so that its drive enough to punch into the crankcase fitting and connect it to the pump by a flexible hose.
The ignition system is best to use a contactless, transistorized, from scooter “Vyatka-Electron”. This scheme is well proven in operation, it is stable in operation, has a reliable and powerful spark. Necessary in the distributor on this engine because the pistons move in it and the flash counter in the cylinders occurs simultaneously.
Power boxer motor of about 28 HP, but it can be increased. Perfected methods of speeding up a single-cylinder motorcycle engines of the class 350 cm3 can be found in the sports literature for the preparation of motorcycles for competitions, but we think it is useful to briefly touch upon them here.
On the pistons it is necessary to remove the flats (Fig. 7). The shape of the combustion chamber should be changed to offset hemispherical with a displacer (Fig. 8) — this will improve conditions of the purge, a cleaning of the cylinders from the exhaust and provide a more uniform burning of the working mixture. There are two ways of reconstruction of the combustion chamber to make the cylinder either re-brewing old camera aluminum alloy with argon-arc burner with the subsequent turning of the camera on a lathe in accordance with the drawing. In the intake Windows and cylinders are removed partitions and increase their cross-section, as shown in figure 9, the lower part of them at the same kruglitsa.
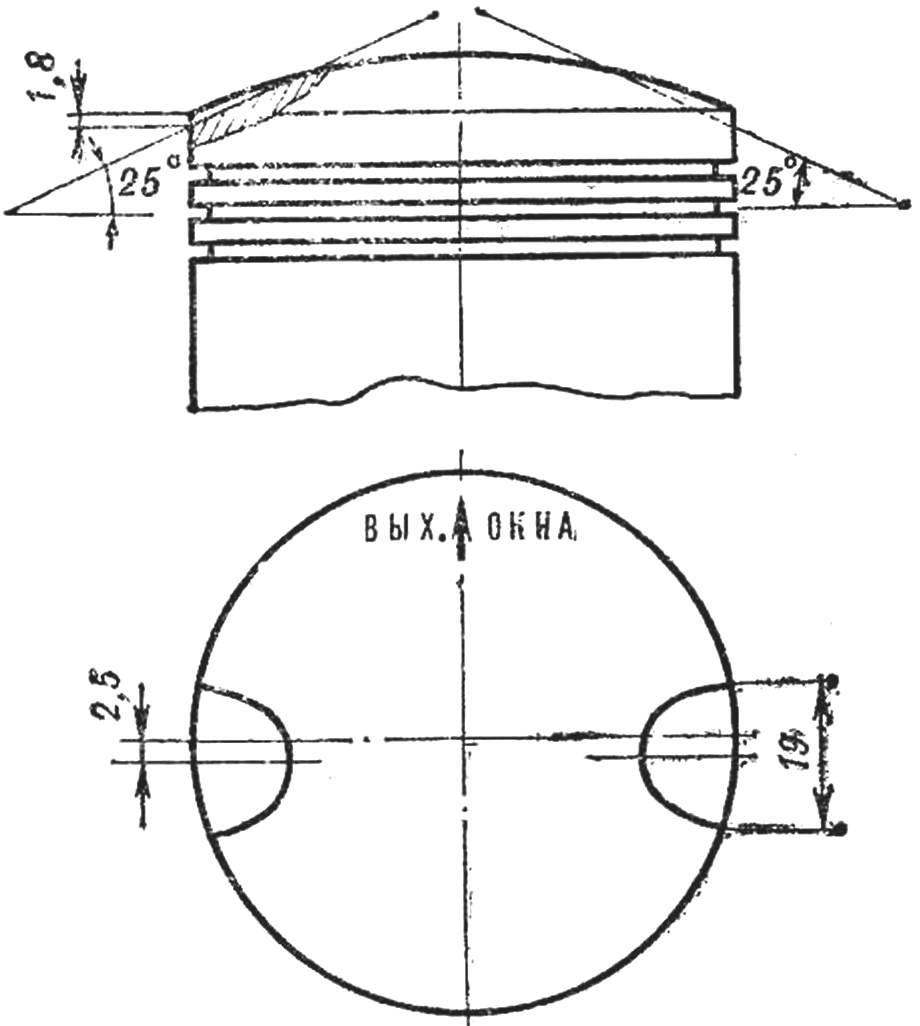
Fig. 7. A refinement of the piston.
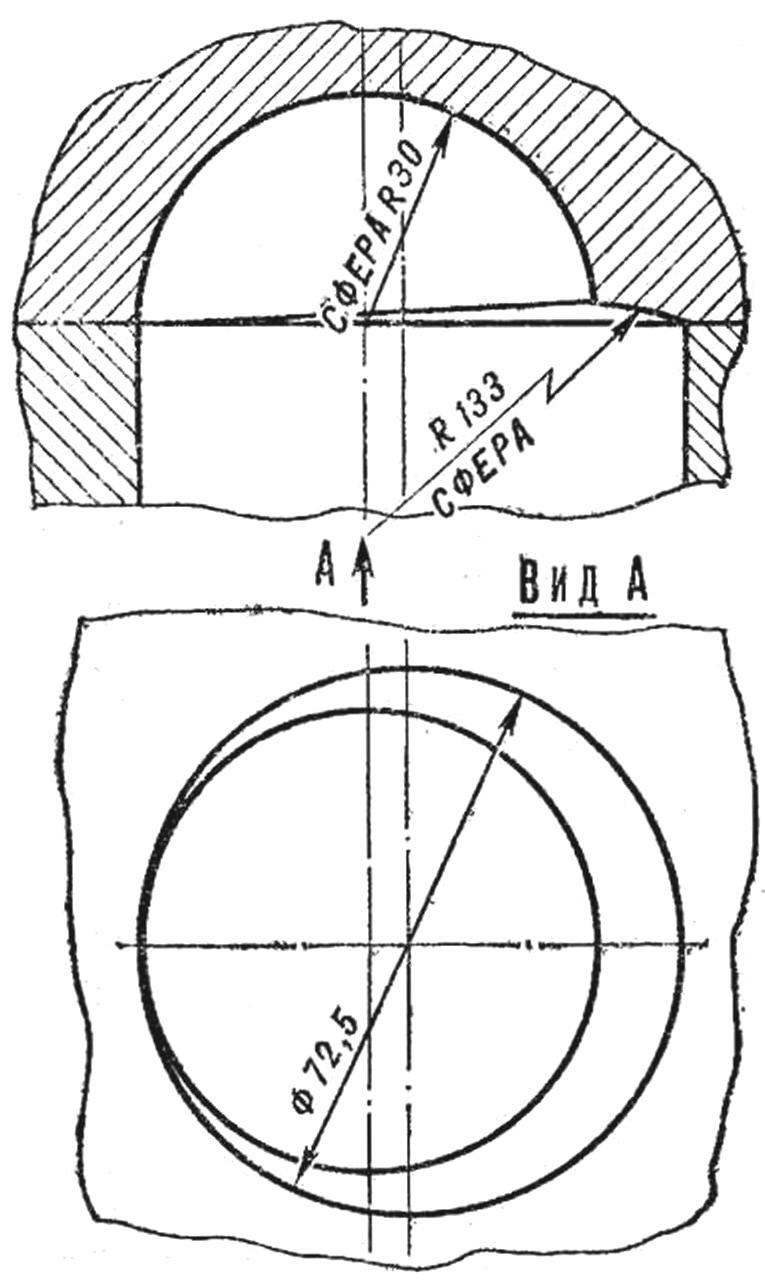
Fig. 8. The profile of the combustion chamber.
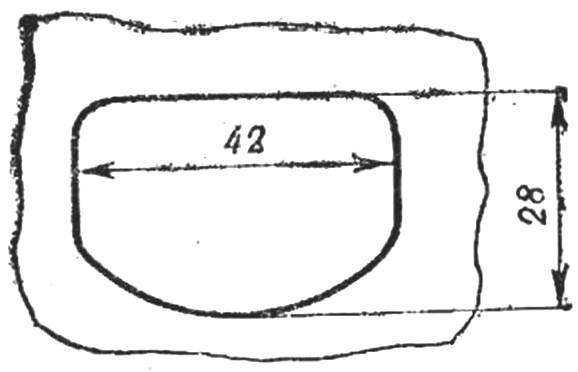
Fig. 9. Scan upgraded intake window.
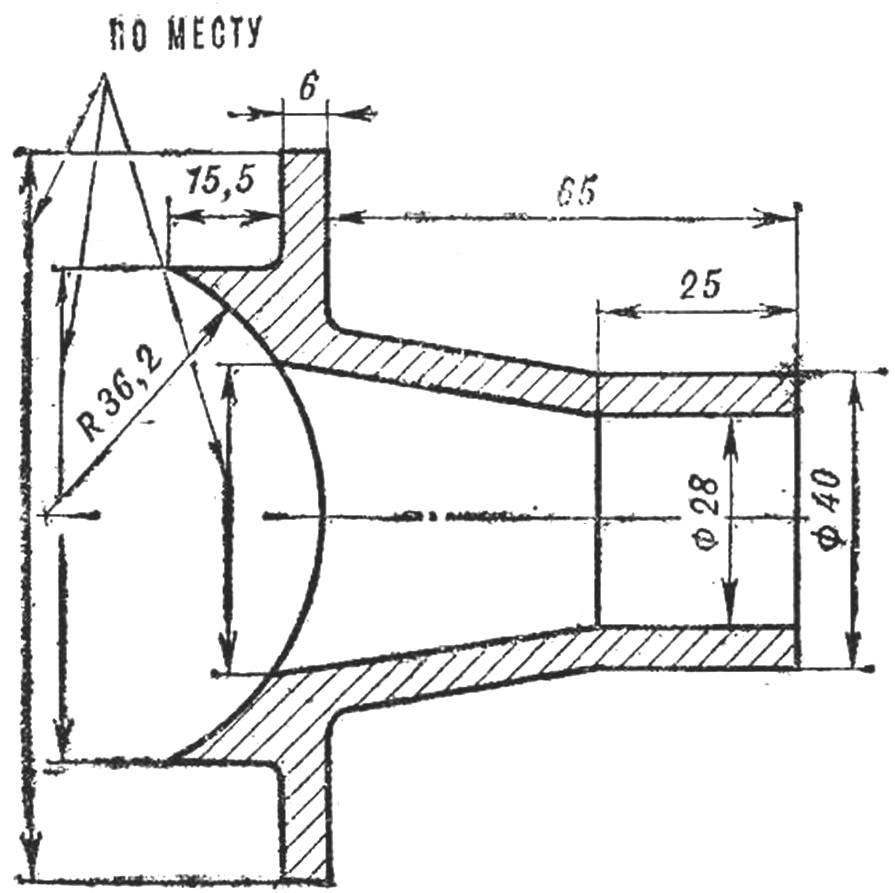
Fig. 10. The inlet fitting (the configuration of the openings corresponds to the inlet window).
Inlet tube should make a new configured (Fig. 10), they will increase the filling ratio by means of the optimal length. The duration of the phase of release should be increased to 144°, this exhaust window make above 1.5 mm.
These operations usually increase the power production engine of IZH-P-2 from 14.8 to 18.4 L. S. L. S. therefore, the capacity of a two-cylinder boxer motor as a result of his forcing will increase by approximately up to 36 HP with the same compression level (6,5).
Most suitable for this motor is the carburetor type K-28 or similar with a diameter of 27.5 mm.
The fuel must consist of gasoline with an octane rating of at least 80 (e.g., AI-93) and aviation oil MC-20 or MC-22, mixed in the usual proportions (1 : 25 by volume).
It should be remembered that the engine forced engine has been unavoidably reduced in comparison with the prototype, because he has to work in more severe thermal conditions with increased loads.
Boxer two-cylinder engine can be done on the basis of other motor motorcycle M-106, “Sunrise”, “Java-350”, respectively, by changing the dimensions of the crankcase, the crankshaft Ball bearings, etc.
Some recommendations wish to use a boxer engine to work in tandem with a propeller. Always remember that the maximum power can be removed only at the nominal rotational speed of the crankshaft (in our case 5000-5500 rpm). Therefore, if the screw is too “heavy” in aerodynamic terms, the engine will not work on maximum power.
Torque on the screw is recommended to pass through a reduction gear with a ratio of 1.2—1.5. This will reduce the propeller rpm to 2500— 3000 rpm, and linear speed of the ends of the blades of the screw 0 2000 mm will not exceed the critical 300 m/s. Under these conditions, the propeller is operating at maximum efficiency with minimum slip.
The use of a gearbox also eliminates unwanted thrust loads on the crankshaft of the engine. Note that when the engine is paired with a propeller without a gearbox on the root axle of the crankshaft, you need to install the angular contact ball bearing: standard radial bearing wears out quickly and fails.
F. KISELEV