In this issue we introduce young innovators, participants of operation “the Introduction” with an unusual method of drying developed in Nikolaev. At our request about it, say the authors of this new technology, which not only shortens the production cycle, but also provides high quality wood.
The most common method of drying wood by heat treatment, contributing to the removal of excess moisture. There are various options such dehydration: in a medium heated gas, air, superheated steam, infrared radiation in the field of high frequency currents.
Most commonly used drying medium of hot air (steam) or gas. It is carried out in chambers equipped with heating devices and air circulation system, supporting equipment temperaturnovlazhnostnogo environment settings.
Such cameras are usually referred to as convective, as they heat the wood and drying occur due to circulation (convection] of hot air.
But if you are creating a flow of heated gas or air then, of course, there is resistance to this flow, which renders the wood pile. So, you need to consider when laying the workpieces and the aerodynamics of the drying process. In short, innocuous at first glance, the concept of “drying” is associated with a wide variety of problems.
Now let’s discuss the question of the quality of the dried wood. Convective profes acts primarily on the outer layers of wood. Therefore, they perceive the greatest amount of heat, the temperature rises faster, which leads to the formation of shrinkage, tensile and compressive deformations and ultimately to marriage-dried wood.
Therefore, the achievement of uniformity of heating of workpieces and the entire pile as a whole — a serious technological challenge. Particularly acute problem of drying thick wood hardwood: oak, beech, hornbeam. It is widely used for making various machine designs, parts, special packaging, devices, special furniture; increasingly, it is used for interior decoration of modern buildings.
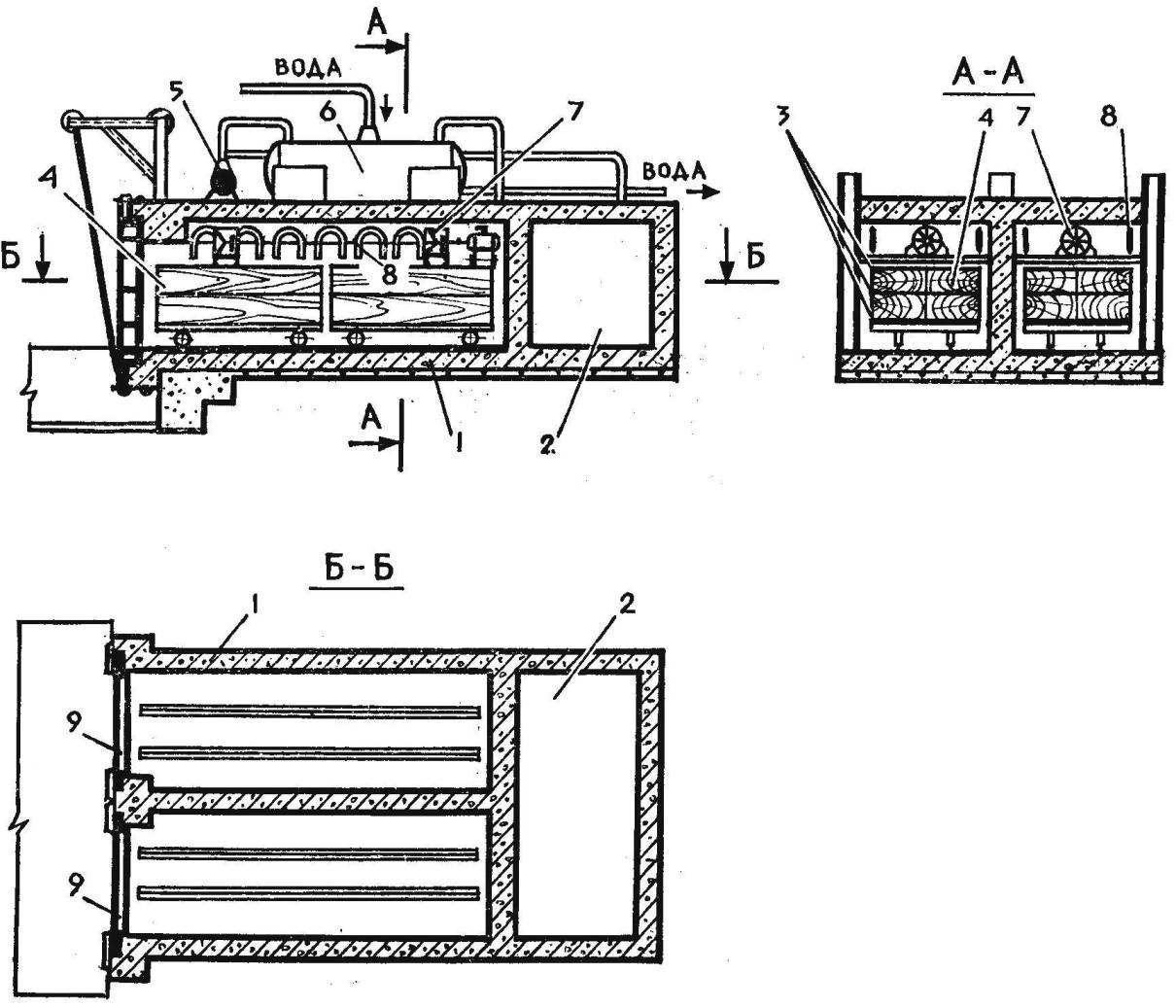
Fig. 1. Bath for drying (concrete, 2900Х1200Х Х2300 mm; an electrolyte of 3% NaCl or KCl):
1 — body, 2 — hot water tank, 3 — plate electrodes, 4 — wood, 5 — water pump 6 — heat exchanger for regulating the temperature of water in baths, 7 air fans included in the cooling-off period of wood, 8 — heaters to control the temperature of air, 9 is a cylindrical valve, sealing bath (cross-section b—B trucks with wood not shown).
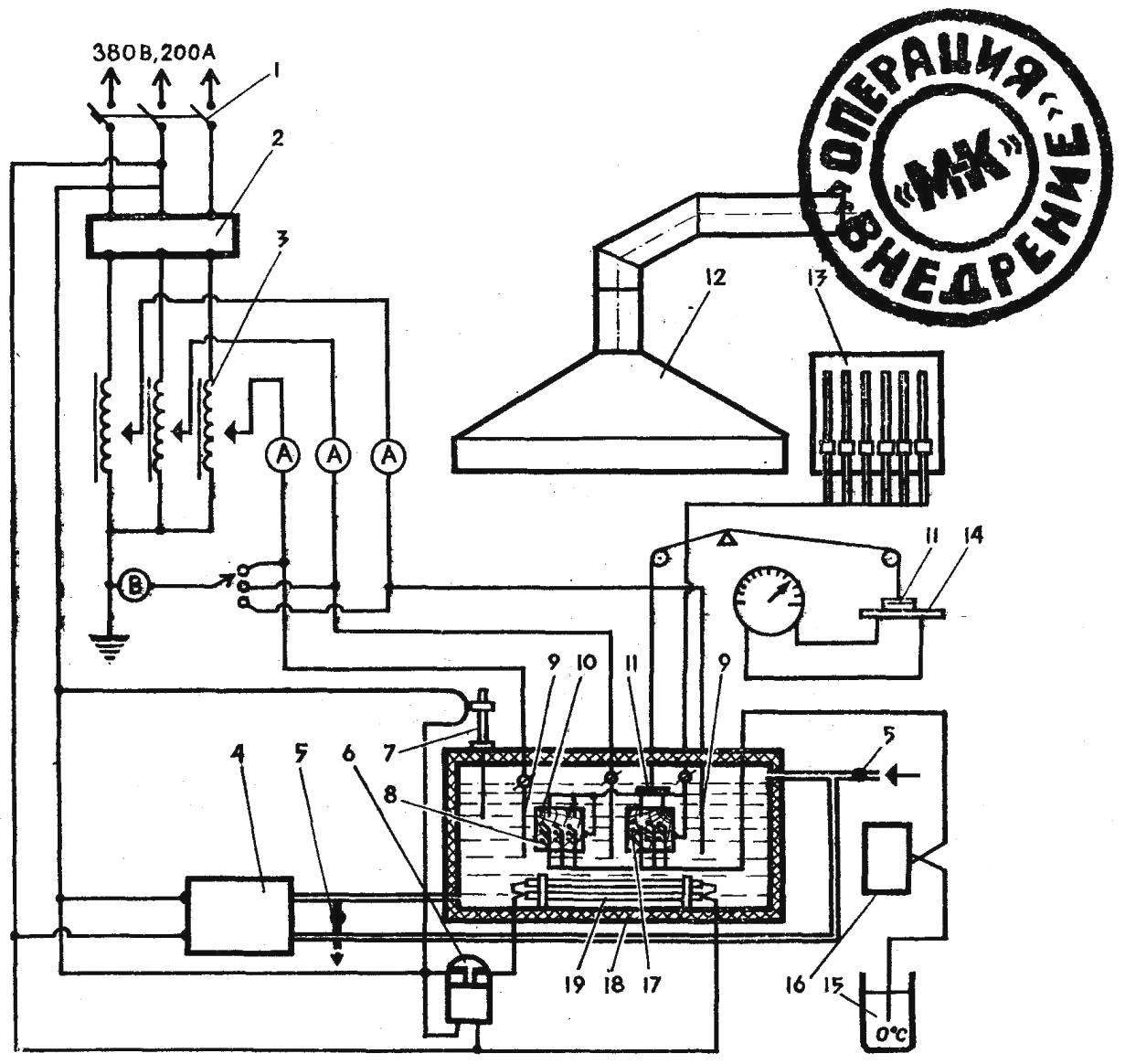
Fig. 2. Diagram of the electrokinetic setup:
1 — switch, 2 — voltage, 3 — autotransformer, 4 — thermostat, 5 — tap, 6 — relay 7 contact thermometer, 8 — thermocouple, 9 — electrode, 10 — pressure sensor, 11 — cargo, 12 — blower, 13 — manometer, 14 — weights, 15 — Dewar-flask, 16 — potentiometer with switch, 17 is a wooden beam, 18 — bath (dielectric), 19 — water heater.
From time immemorial these blanks were dried under canopies in the air — the process takes several years. Slightly faster and the storage in special premises, where constantly maintained at the necessary temperature and humidity controlled environment. In drying chambers is possible dehydration only thin workpieces or boards, but it lasts too long: one to two months.
Our search for high quality and intensive process led to thoughts about the possibility of heating and drying such wood… in water or conductive solutions.
Dehydration in the water? Yes! This intriguing fact has a fairly reasonable sense. It appeared, that a uniform and simultaneous volumetric heating of the wood is quite feasible under the action of the current in the liquid as a conducting medium between the plate electrodes (Fig. 1). The current almost freely (with an extremely small transfer resistance) penetrates into the thickness of the wet wood, which electric resistance is small, and due to golevyh losses heats it.
Water, however, is also heated. However, handling this heat through a heat exchanger, it is easy to align the temperature of the material and liquid. And it means that there is a reliable guarantee uniform heating and thus minimize the danger of cracking of the workpieces.
But heating the wood to the necessary temperature state only half the battle; the other half of the problem — the removal from it of moisture.
There are various technological options for implementing this process. Among them are most attracted to two. The first is the creation of a positive temperature difference in the heated billet and the surrounding liquid. Then the inside towards the surface of the wood will act two forces, the diffusion of heat and moisture diffusion. It is enough to heat exchanger to maintain the temperature of water is slightly lower than the surface of the wood.
Second option: after heating in water up to 90°, the wood is cooled in air at a temperature of from 25 to 38°. Moreover, such cycles are repeated many times. Here heat and moisture will also be directed to peripheral layers. They will help another driving force — thermobarometry, due to an excess compared to the atmospheric pressure.
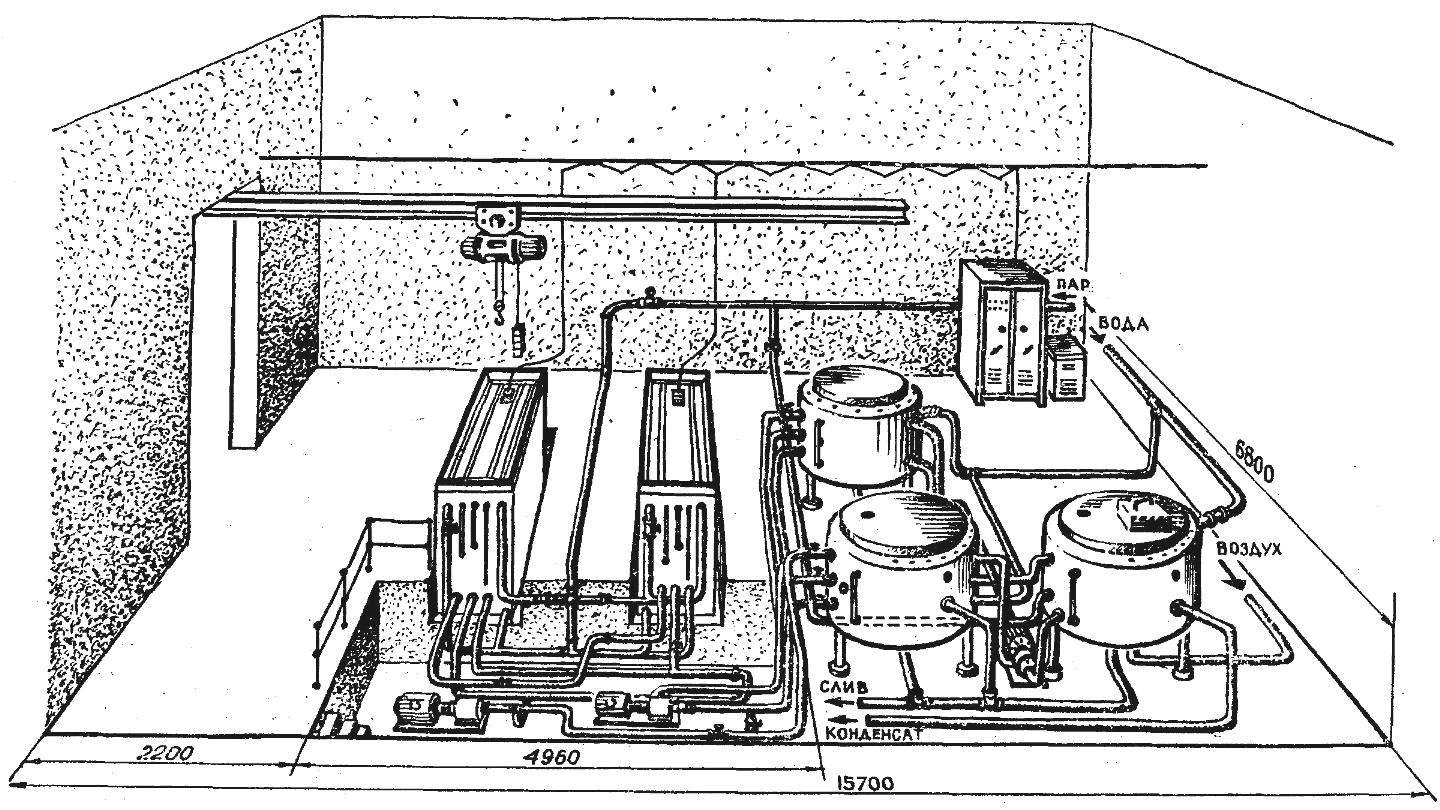
Fig. 3. Plot electrokinetic drying and impregnation of wood.
That showed that research in the industrial laboratory. With the hard mode, which corresponded to the temperature of the middle of oak timber 100° and ambient temperature of water 95— 97°, the dehydration process was intense, but was accompanied by strong internal cracking of the beam. The use of softer modes: the temperature of the timber is from 60 to 95° and water, respectively, 50-80° — showed that removal of moisture almost didn’t happen.
Then it was decided to conduct tests according to the second embodiment.
It turned out that if you heat the bar in water up to 75-95°, and then place it into the air with a temperature of 26-30°, the bar in the process of cooling gives the moisture, visibly obezvozhivani by repeating the cycle. This method, called the oscillating temperature drying, was approved by the Scientific-research Institute of heat and mass transfer of Byelorussian Academy of Sciences.
As a result of experiments determined the electrokinetic modes of drying are summarized in the table. The quality of materials after the process of dehydration in these modes satisfy all technical conditions y requirements: any external or internal cracks in the wood were not.
It should be noted that the period of dehydration of lumber from 80 to 15% moisture content can be drastically reduced if strictly maintain the air temperature of 28-30° and to provide periodic air circulation. These conditions can be obtained in an industrial setting.
A detailed study of the process associated with the use of oscillating modes, determined the scheme of the pilot plant shown in figure 2. It is managed from a single console and can be fully automated.
TABLE
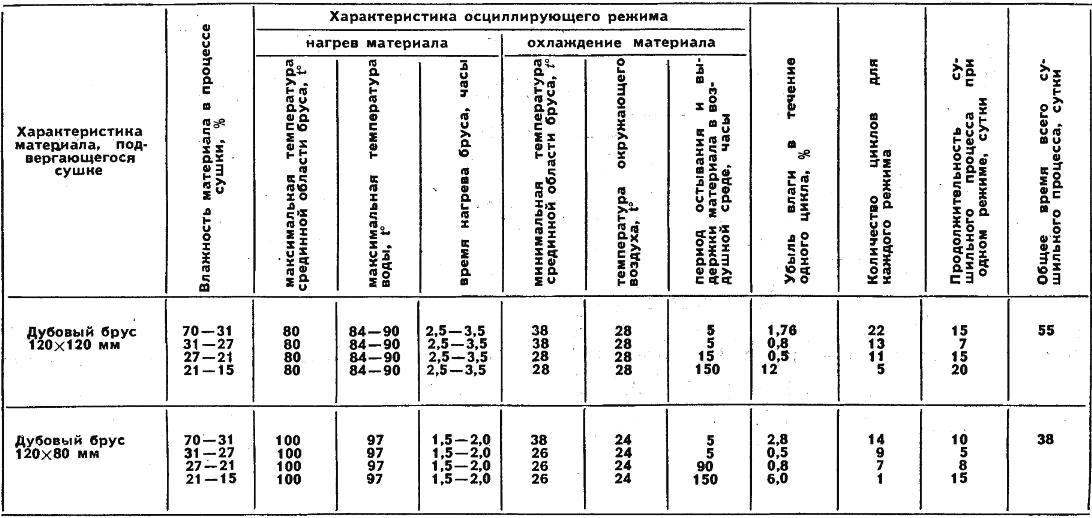
Speaking of the two options electro-kinetic drying, it should be noted that the first of them, with the use of temperature dehydration of the materials in a water environment can be successfully used for drying of thin wood bending and other capillary-porous materials, which by their structure is not prone to cracking, or if the latter circumstance is of no practical value.
Further production testing processes electrokinetic drying of wood hardwood, and other materials conducted by the Institute of heat and mass transfer, Belorussian Academy of Sciences, showed that the initial moisture content of 60-80% to the final 8-10% duration of drying may be reduced to 180— 200 hours. The power consumption is between 1400-2000 kcal/kg of evaporated moisture.
Interestingly, a similar process heating and drying can be combined with the impregnation process, not just wood hardwood, but also softwood. Such a scheme of an industrial site shown in figure 3.
Seems to be very efficient and economical combination in one machine of two independent, closely related and contributing to each other’s processes.
G. M. BALABAYEV, S. G. ROMANOVSKII