A friend of mine started making the car we are talking about in the late 1980s, when automotive abundance was just around the corner, but we didn’t know about it yet. However, as soon as he made the frame with suspensions, his enthusiasm dried up; I had to continue building the car. Having assessed my capabilities, I decided to take on this work, especially since I had experience in such a matter – a little earlier I had restored a Moskvich-401 practically from scrap metal.
In my plans I wanted to build a car that was roomy, simple and reliable: so that when traveling to the country or on a trip there would be enough space for all family members, and even the necessary cargo could be taken with them. The manufactured frame made it possible to make such a machine.
I decided to glue the body with fiberglass – it is more durable. I tried to avoid complex shapes of body panels (as they say, double-curvature surfaces) even in sketches: they are difficult to draw, much less make. At the same time, I wanted the car to look good. I tried to achieve this by carefully executing the body trim parts, especially the exterior ones.
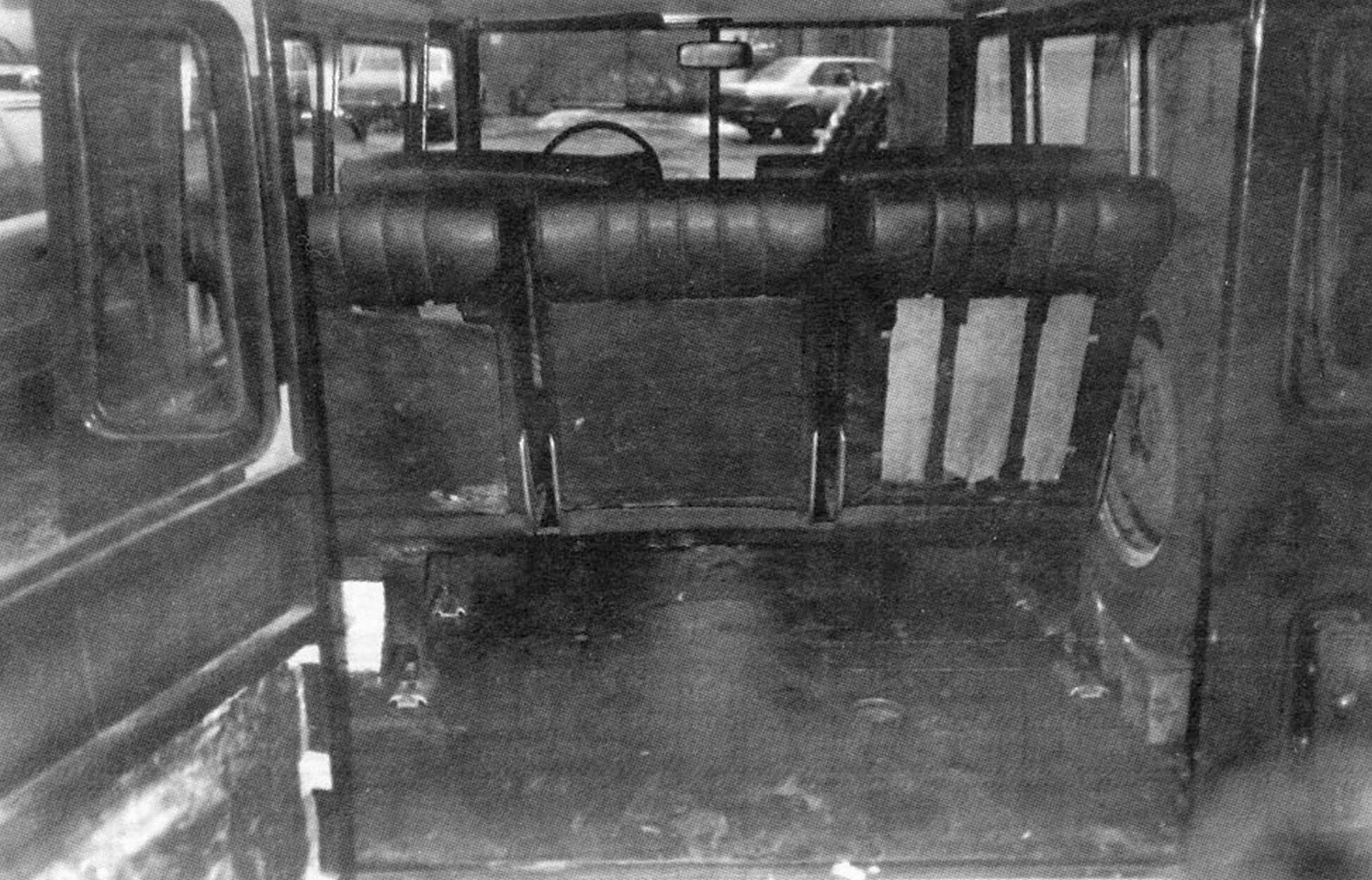
As a rule, the base – the chassis or the entire chassis – is taken by home-made workers from a specific car. I didn’t have that kind of “attachment.” The basis can be considered a whole family of gas vehicles. The engine is from the Volga GAZ-24-10, the gearbox, steering gear and rear axle are from the Gazelle GAZ-3302, the front axle is generally from the UAZ-451 (once such cars had only one rear drive axle were produced at the Ulyanovsk Automobile Plant). There were also components and mechanisms from other machines. So, the front suspension (springs and shock absorbers) is from Moskvich-412, the rear suspension is from Gazelle.
Many do-it-yourselfers built their cars in cooperative garages. I didn’t have that. That’s why I asked permission from the management of the car dealership where I worked to make a car on its territory after a working day and on weekends. Permission was received, and we (me and my son) got down to business. Our colleagues watched to see if we had enough patience to make a car, and what kind of car it would turn out to be. Many offered help.

The frame of the car is quite simple (not even spatial), two-spar – wider at the rear and narrower at the front. The spars are made of steel (St3) closed profile of rectangular section with dimensions of 130×45 mm and a wall thickness of 4 mm. The profile size was calculated by specialists for maximum bending moment with a large margin of safety. The profile is adopted the same along the entire length to facilitate the manufacture of the frame in the field. The side members are connected to each other by several cross members welded to them, as well as by front and rear bumpers. Crossbars are made of steel strip 100×5 mm. The front bumper was borrowed from a decommissioned UAZ-469 and covered with a decorative plastic trim, and the rear bumper was made from channel No. 15, equipped with a tow bar and edge buffers. To enable the car to tow a trailer, the rear bumper was reinforced with an additional cross member with struts.
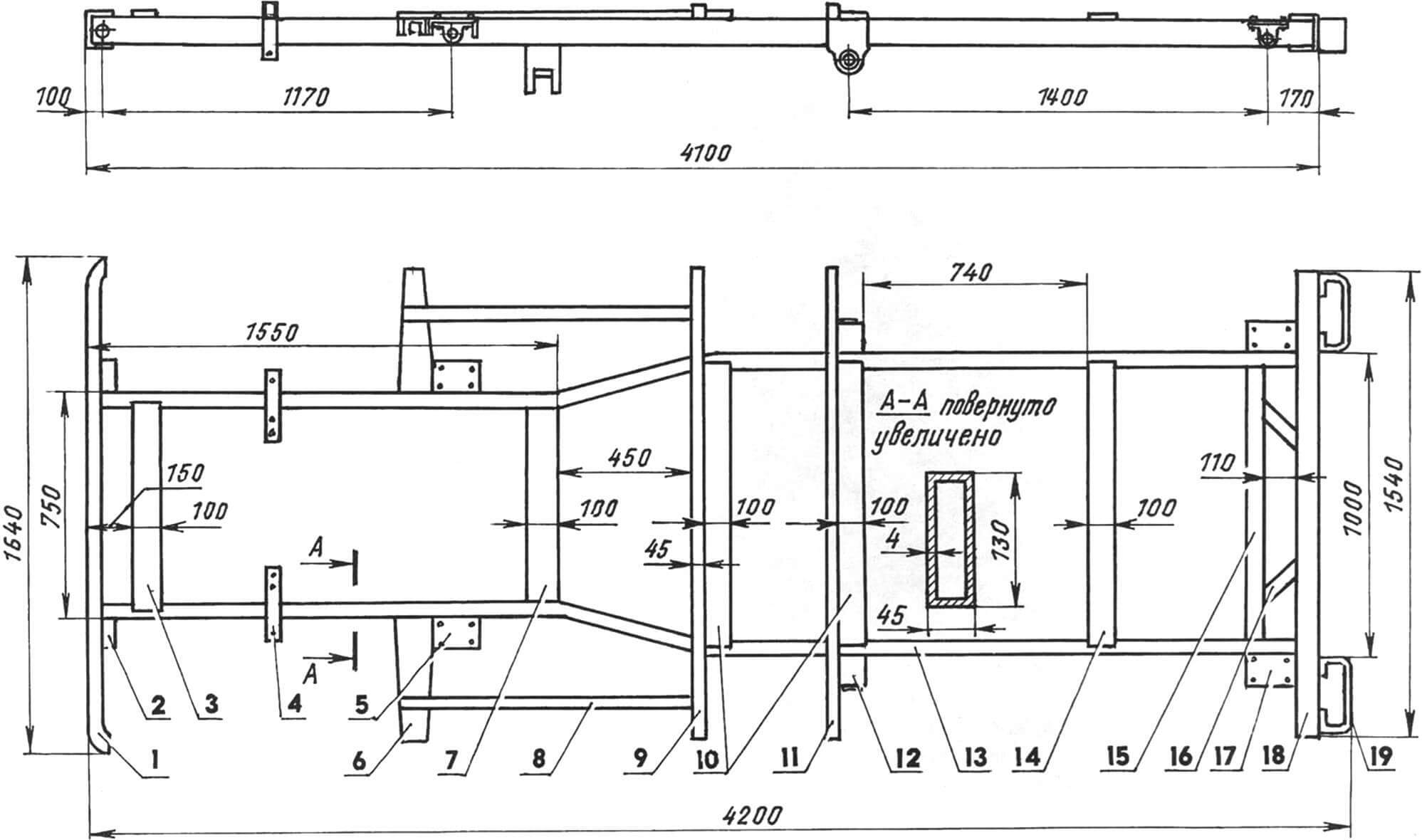
1 — front bumper (from UAZ-469 with plastic lining); 2 — front spring mounting bracket (from Moskvich-412, 2 pcs.); 3 — front cross member (steel strip 100×5); 4 — engine mounting bracket (2 pcs.); 5 — bracket and axis of the front spring shackle (from Moskvich-412, 2 pcs.); 6 — front console for fastening the body frame; 7 — suspension beam for gearbox and transmission (from GAZ-3302 “Gazelle”); 8 — riser (pipe 50×35, 2 pcs.); 9 — underbody beam (pipe 60×45); 10 — intermediate crossbars (steel strip 100×5); 11 — rear body mounting console (pipe 50×35, 2 pcs.); 12 — bracket and axis of the rear spring shackle (from GAZ-3302 “Gazelle”); 13 — spar (pipe 130x45x4, 2 pcs.); 14 — rear cross member (steel strip 100×5); 15 — rear bumper reinforcement (channel No. 10); 16 — strut (channel No. 8, 2 pcs.); 17 — rear spring mounting bracket (from GAZ-3302 “Gazelle”, 2 pcs.); 18 — rear bumper (channel No. 15); 19 — buffer (steel strip 150×3, 2 pcs.)
To install the body on the frame, paired (symmetrically located) consoles are welded to it on both sides, and in the middle of the frame there is an underbody beam. The frame is fastened to the frame using M10 bolts (through rubber gaskets).
In addition to the consoles, parts and components are welded or bolted to the frame for mounting the front and rear suspensions (springs, shock absorbers), as well as the power unit and transmission.
The seven-seat, two-volume body of a “Jeep” shape consists of a steel supporting frame and fiberglass lining.
The power spatial frame of the body is welded mainly from a square steel pipe with a cross-section of 45×45 mm and a wall thickness of 2 mm. And only its transverse beams are made of a steel rectangular pipe with a section of 100×60 and a wall thickness of 3 mm.
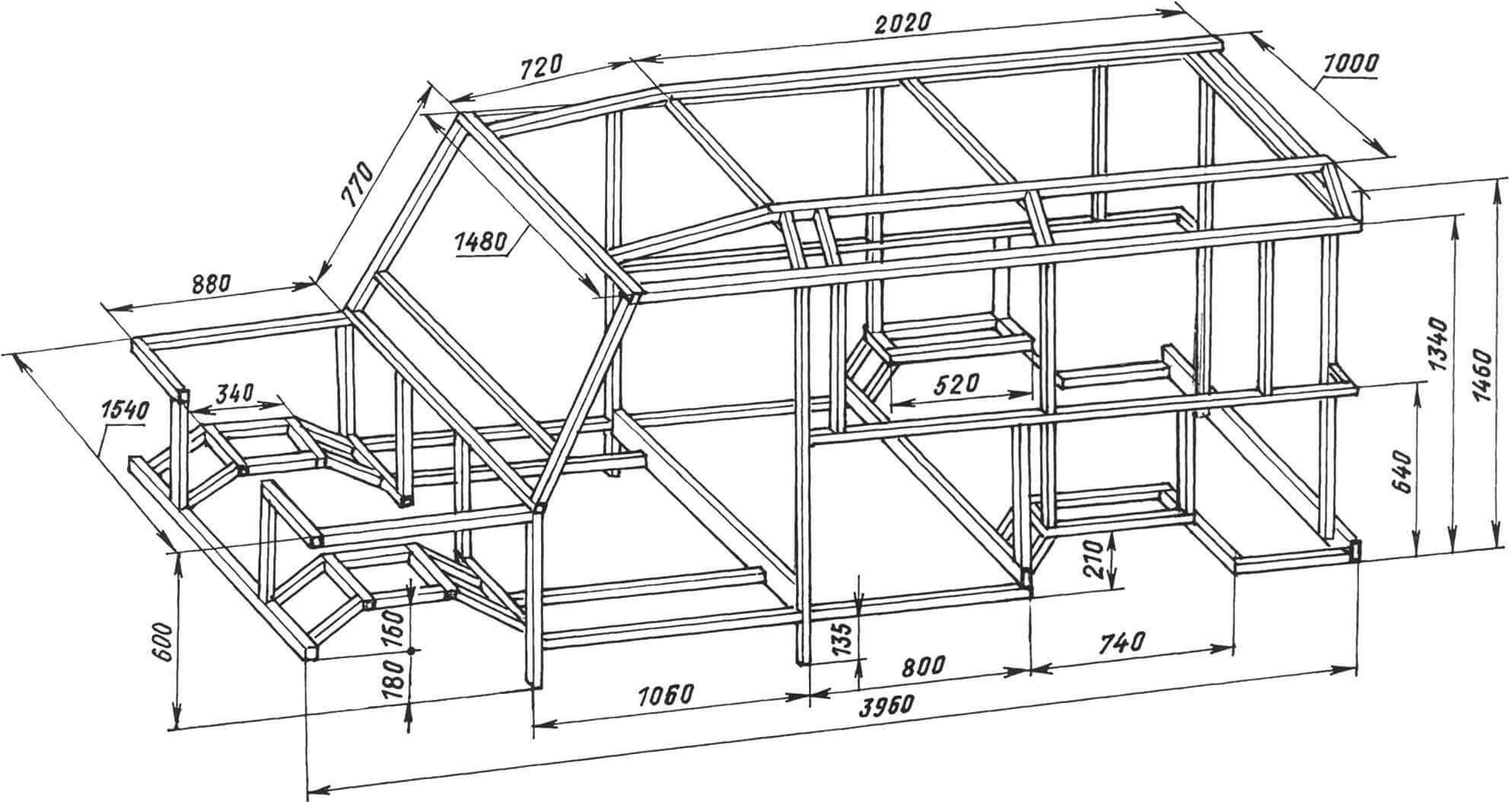
Although the frame was not calculated, however, as operating experience has shown, it is capable of withstanding significant torsional and bending moments when driving with a full load over rough terrain. Perhaps the main role in its design is played by the quality of the welds. I mastered the craft of a welder on my own a little earlier and even made a transformer with a toroidal core for a welding machine myself.
In the most critical places, in my opinion, I reinforced the joints with struts, overlays or gussets – where possible and appropriate. This frame allows you to transport up to 100 kg of cargo on the roof rack.
The skin of the car body was glued from fiberglass on epoxy binder in separate panels. I used sheets of Finnish plywood as matrices; To prevent them from warping, I laid them on a thick layer of sand.
Body parts panels are mostly of a simple flat shape. To strengthen them (and to some extent for decoration), I provided rectangular and triangular stiffening ribs; formed them during the manufacture of panels by attaching a planed wooden block, board or duralumin corner to the matrix.
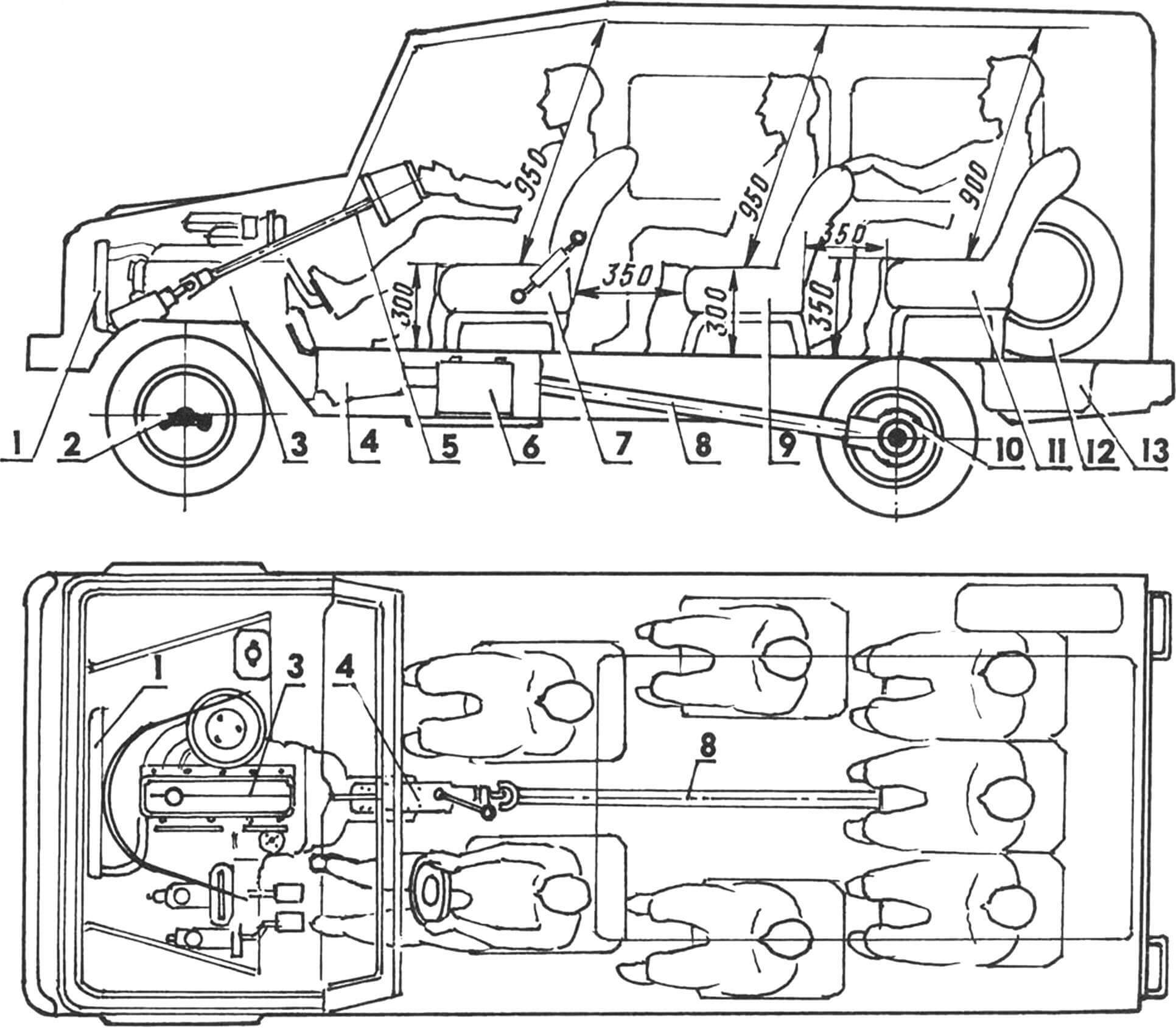
1 — radiator (from GAZ-3302); 2 — front axle (from UAZ-451); 3 — engine (from GAZ-24-10, 402nd model); 4 — clutch and gearbox (from GAZ-3302); 5 — steering (from GAZ-3302); 6 – battery; 7 — front seat (from RAF, 2 pcs.); 8 — driveshaft (from GAZ-24-10, shortened); 9 — middle passenger seat (from VAZ-2101.2 pcs.); 10 — rear axle (from GAZ-24-10); 11 — rear seat (from VAZ-2101.3 pcs.); 12 — wheel (from GAZ-21, 5 pcs.); 13 – gas tank
The body panels were connected to the frame and to each other using fiberglass with epoxy glue. External seams were sealed with epoxy putty and carefully sanded. This was followed by priming and painting with air-drying nitro enamel.
In 1992, in a vacant lot outside the territory of the motor vehicle fleet, he conducted road tests of the car and eliminated the identified deficiencies. In particular, the fastening of the springs from under the beams of the front and rear axles was moved to the beams – at the same time, the vehicle’s maneuverability improved and it itself became taller and more impressive in appearance.
Front suspension: on longitudinal semi-elliptic springs (rear from Moskvich-412). Rear suspension: on longitudinal semi-elliptical springs (rear ones from Gazelle GAZ-3302). Brakes: service – drum, hydraulic drive, separate, with hazard warning light, vacuum booster; parking – on the rear wheels with mechanical drive
Legalizing the car, oddly enough (according to the stories of craftsmen, this is the most difficult stage in creating homemade cars), did not cause much difficulty. At least, no one created any bureaucratic obstacles: he quickly collected all the necessary documents, registered the car and received state license plates.
After registration, I operated the car in a rather harsh mode. It carried a large volume of cargo necessary for the construction of a summer house, sometimes overloading the car so that the springs bent in the opposite direction.
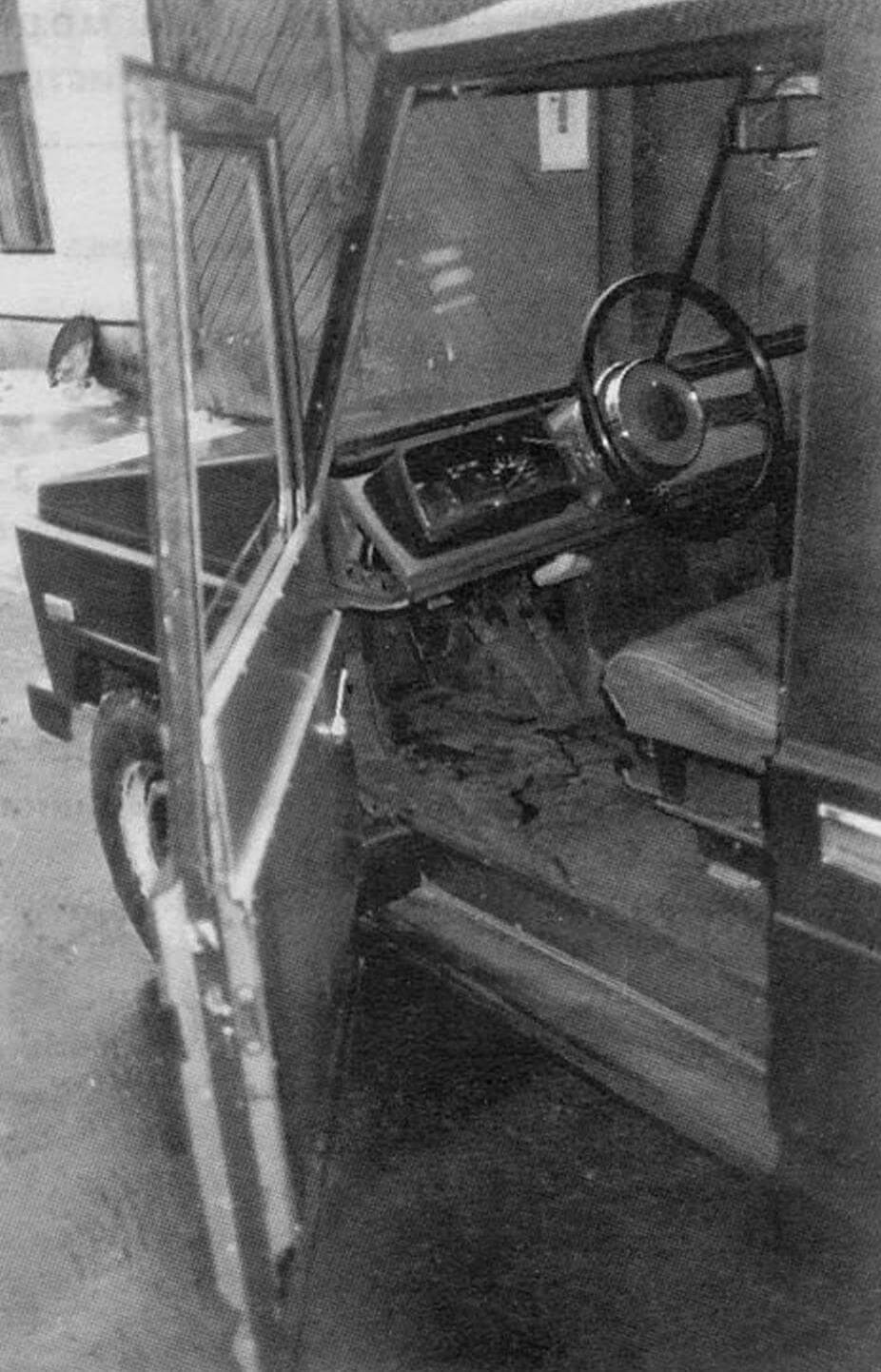
The car was shown to the general public in 1997 during a run of homemade cars. Then he participated in many “samavto” festivals, invariably receiving awards and prizes.
Friends and acquaintances claim that my car is similar to the German Gelendvagen SUV, although I had no idea about this before. But nevertheless, they gave me a branded Mercedes radiator lining, which I installed instead of the previously homemade one.
For a long time the car existed without a name – it only had an alphanumeric designation. VK-2, which stood for Vladimir Komar 2 (the number “two” meant the second home-made vehicle; the first, as already mentioned, was the restored Moskvich-401). But somehow at the family council they decided to give it a name – their last name. After all, he became, as it were, a member of the family – you couldn’t do a single big thing without him.
Technical characteristics of the Komar car
Three-door body
Number of seats 7
Machine length, mm 4220
Width, mm 1680
Height, mm 1800
Front wheel track, mm 1442
rear wheels, mm 1420
Ground clearance, mm 220
Base, mm 2600
Overhang angles, degrees, front axle 47°
rear axle 25°
Smallest turning radius along the axis of the front wheel track, m 5.4
Vehicle’s own weight, kg 1082
Weight of passengers and cargo, kg 550
Gross weight, kg 1632
Front axle load, kgf 815
Rear axle load, kgf 817
Engine ZMZ-402
Front axle UAZ-451
Rear axle GAZ-3302
Gearbox GAZ-24-10
Steering mechanism, globoidal worm with three-ridge roller (gear ratio) 19.1
Wheel size 7.35-15
Drive axle wheel size for off-road 6.40-15
Maximum power, hp 75
V. KOMAR