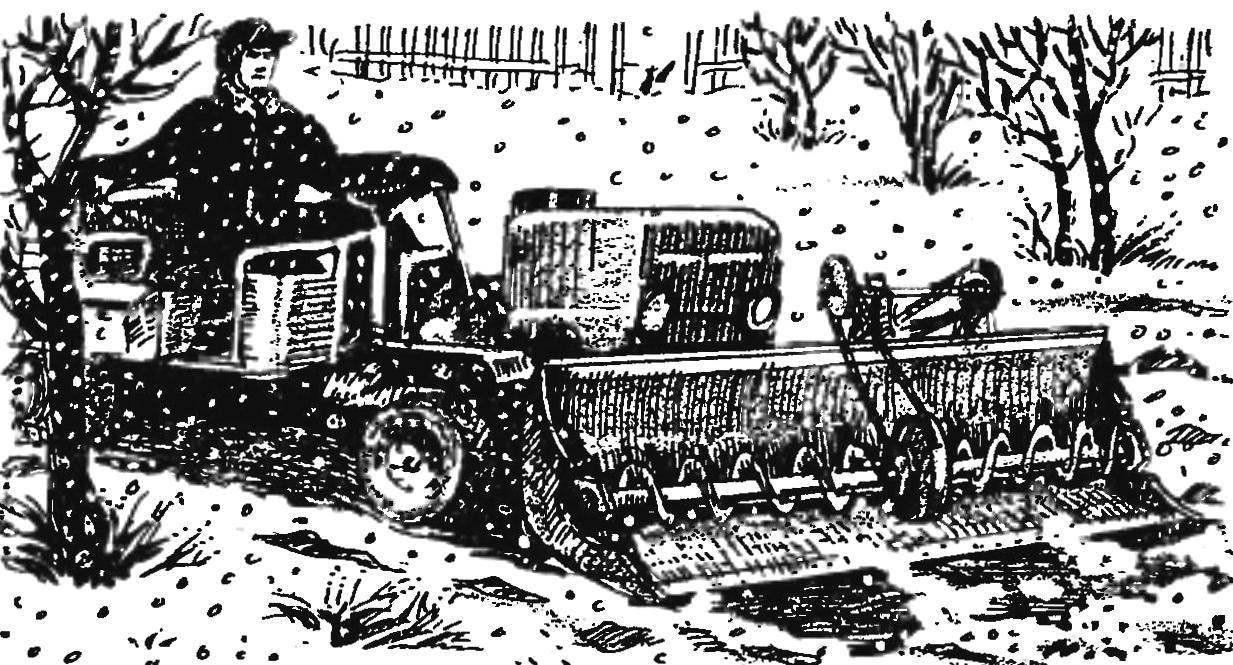
Here’s the problem: the site is located in the corner of the holiday village, half a kilometer from the highway. In winter this highway, the road is still clean, but in the streets and alleys of the village, they, of course, do not look — no obligation. And sometimes the snow piles so much that until you get to the gate, no strength remains.
But after in a suburban garage have Careful, there are powerful homemade all-terrain vehicle-amphibious designer issue winter road decided once and for all. When you select a sequence in the manufacture of attachments should be given priority in snow removal mechanism.
What is needed is not a simple dozer blade and auger snowthrower, Victor D. realized when I saw one in the town square neat foreign car, deftly straightened with drifts hinged mechanism with a screw of Archimedes. Just decided for themselves that need two screws below the snow they threw not one, but both sides.
Povorotu your stash in a corner of the garage and finding a suitable sprockets, chains, bearings, angles and sheet steel, the designer has estimated the future size of the Assembly and for a short time together a mechanical assistant.
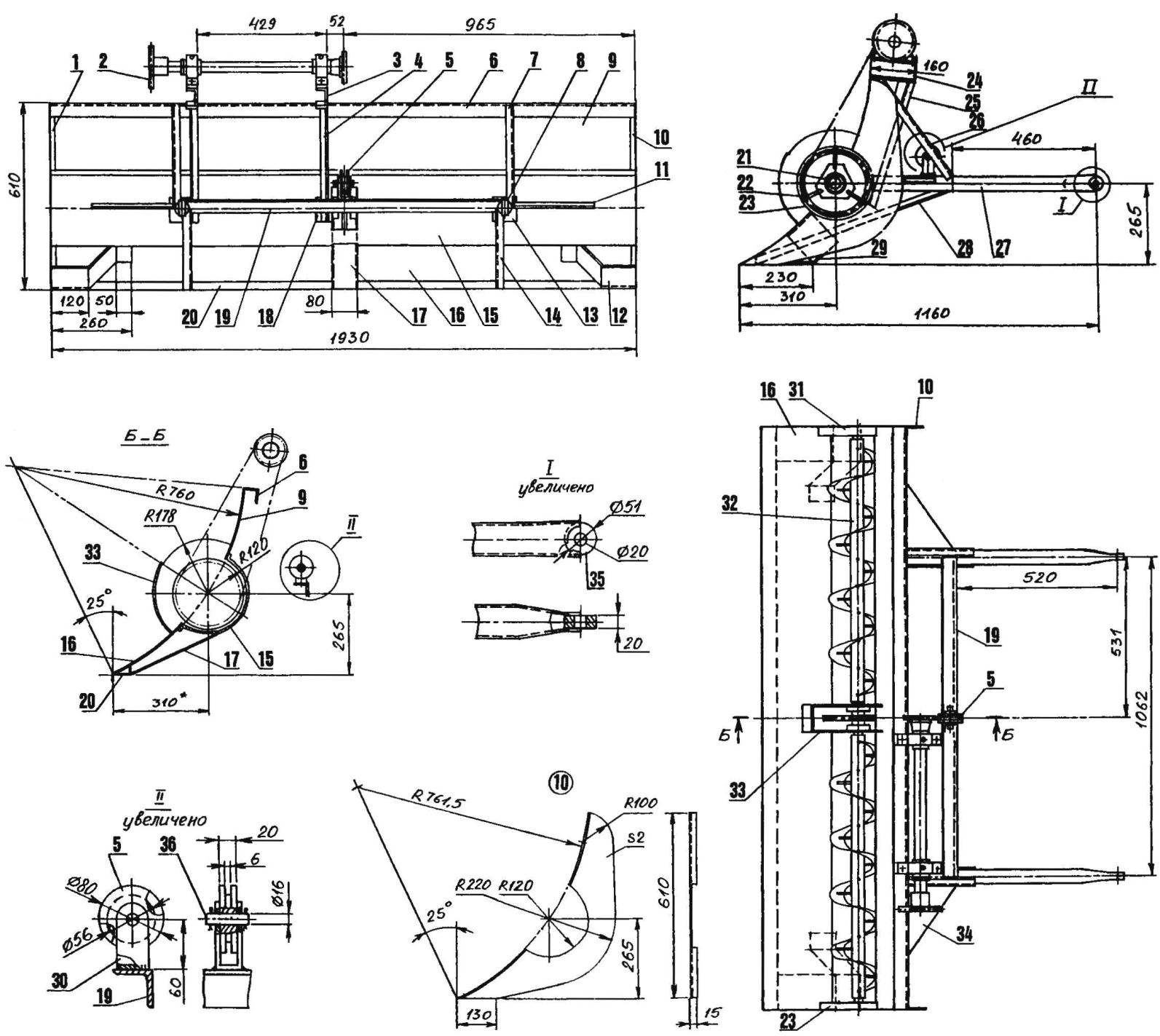
Auger snowthrower:
1,10 — Board (steel, sheet s2); 2 — an asterisk of a drive shaft; 3,24—mounting brackets drive shaft (steel, channel No. 6,5); 4,25 — struts (steel, angle 25x25x5); 5 — roller lift snow plow; 6 — upper bulkhead (steel, area 45x45x4); 7,26 — bracing (steel, angle 25x25x5); of 8.27—carrier (steel tube 50×1,5); 9,16 — upper and lower piles (steel, sheet s1,5); 11,34 — scarves (steel, sheet 270×190, s2); 12,29 — boots (steel, sheet s2); 13 — lateral lining (steel, sheet s4, 2 PCs.) of 14.28 — trays (steel, angle 25x25x5); 15—bed auger (steel, sheet s1,5); 17 — box (steel, sheet s2); 18 — the Central lining (steel, sheet s4); 19 — beam (steel, area 45x45x4); 20— lower bulkhead (steel, area 50x30x4); 21 — end bearing housing of the screw mechanism (2); 22— the needle (steel, Ø8 rod,6 PCs); from 23.31 — arc (steel, strip 25×5); 30 — roller bracket (steel, strip 40×5); 32 — the right auger shaft; 33 — cover sprocket screw mechanism (steel, sheet s2); 35 is a hinge carrier (2); 36 — the axis of roller (steel bar of Ø16, L50)
The snow thrower housing is made of three bent radius of the steel sheets with thickness 1.5 mm: auger bed, lower and upper dams. Body held it firmly in place, top and bottom welded to the side walls from the corners of various sections, and on the sides of the side of a steel sheet with a thickness of 2 mm.
To dock with the Rover uses two carrier of steel pipe 50 mm in diameter, a little flattened in the rear ends of which are welded steel washers as hinges. The front ends of the carrier are welded to the box and screw through the lining — pieces of steel sheet with a thickness of 4 mm.
The overall stiffness of the Assembly attach struts and bracing from the corner section of 25x25x5 mm, welded to the carrier and the side members, gusset plate sheet steel 2 mm thick, and cross beam from the corner 45x45x4 mm. On the latter is located in its bracket roller, over which is thrown the cable from the lift winch hidden under the hood of the Rover.
The lower corners of the snowthrower from random deformations are protected by shoes, figuratively bent from steel sheet 2 mm thick. They are welded to both sides of the spar and the blade.
The main working mechanism snowthrower —auger. It consists of two ribbons representing the Archimedes screws in the opposite direction and welded to the M6 studs sticking out of the screw shafts.
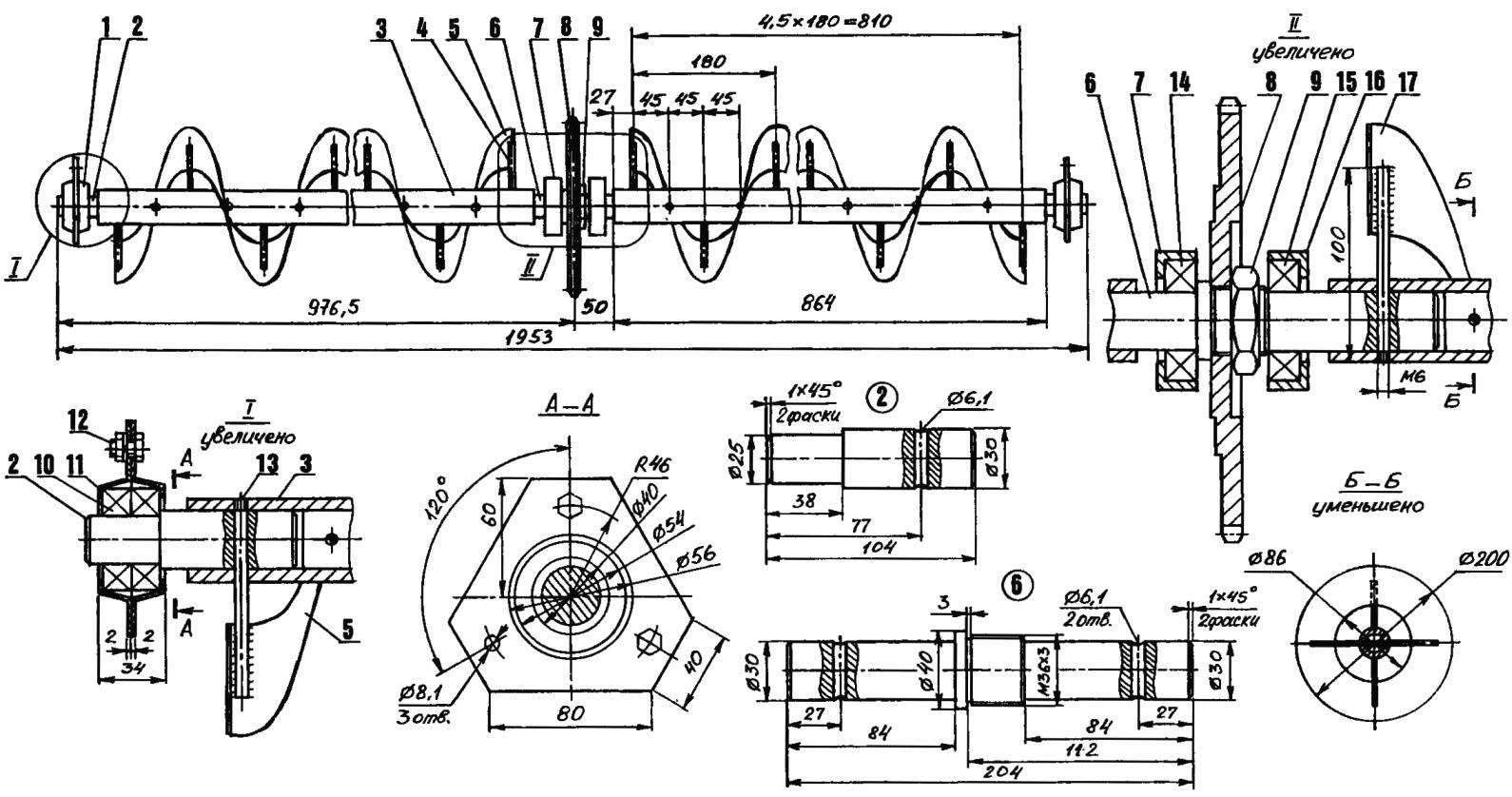
Screw mechanism:
1,11 — terminal halves of the bearing housing (steel, sheet s2, 4 pieces); 2 — trailing axle (steel bar Ø30, 2); 3— auger shaft (steel, pipe 42×6,5, 2); 4,13 — stud M6 (steel, rod Ø6, 36 PCs.); 5,17— screws (steel, sheet s2); 6 — the Central axis (steel, rod Ø40); 7,16 — Central bearing housing; 8 — sprocket (z = 36, t = 19,05); 9—nut М36х3; 10 — bearing 160205 (4 PCs); 12 — bolt M8 (6 PCs); 14,15 — bearings 236205
At the end of the axis of the screw shafts is mounted a pair of bearings series 160205, enclosed in a simple stamped case. Half-Cup of these housings bolted M8 with fixing spokes of rod with a diameter of 8 mm is attached by welding to the arcs on the snow thrower housing.
In the middle of the screw mechanism is a sprocket with number of teeth 36 and pitch 19.05 mm, mounted on the Central axis of the nut М36хЗ. The right and left of the ball — bearings of series 236205, pressed into the chiseled body-cage, stuck welding to the cheeks of a casing of a sprocket. Previously with spokes exactly on the axis of the bed was exposed screw end bearings. And then finally welded all the joints, and the ends of the spokes sticking out of the holes in the arcs, cut and polished.
From pushing the front of the mass of snow is the star of a screw mechanism protects the casing, welded to the box blade and auger.
Since the strength of the body of the snowthrower has been weakened by an aperture cut in the middle of the bed of the screw (for the passage of the drive chain), had to strengthen the hull box — walleroobie part is welded below the opening to the spar and the blade.
As already noted, the snowthrower in action is a motorcycle chain with a pitch of 19.05 mm, stretched between the sprockets of the screw mechanism and the drive shaft located to the left on the top rail of the body of the snowthrower.
The drive shaft is a simple reducer that transmits to a screw mechanism torque from the PTO to the engine of the vehicle. Sprockets and bearings (cast housing and bushing) this gearbox is taken from the agricultural units. Sprocket on the shaft are fixed by means of dowels, a bearing sleeve of anti-friction cast iron— pins, the seat for which drill through the threaded holes in the housings when you unscrewed the butter dishes.
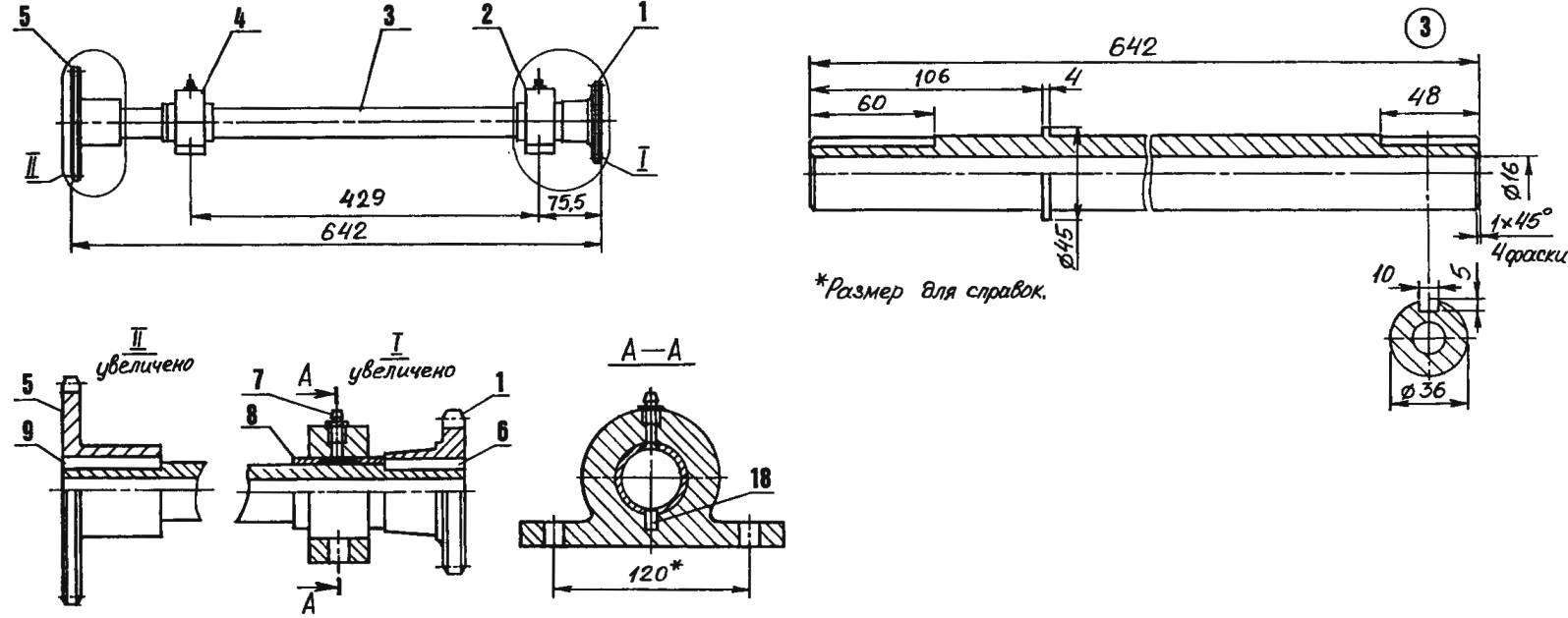
Drive shaft:
1 —sprocket (z = 15, t = 19,05); 2,4—bearing slides; 3 — shaft; 5 — a drive sprocket (z = 22, t = 19,05); 6,9 — prismatic pins; 7 — oiler 1М10х1 (2); 8 — the bearing bushing (antifriction cast iron Achs-1 or ABC-2,2 PCs); 10— pin (pin Ø8, L12, 2 PCs.)
Assembled drive shaft is mounted on two brackets from the channel number of 6.5, is welded to the upper spar. Because the length of the brackets is much greater than the width of the horizontal butt of the spar, it took backup. They were carved out of the corner of 25x25x5 mm and tack welded between the brackets and the padded bed of the auger.
In the end, the power circuit snowthrower lined up in such a way that all loads occurring in the structure during the “cutting” drifts, passed in the props, struts and braces on and drove next to the body of the vehicle, where and are closed.
After testing and final debugging unit was thoroughly cleaned from the attacks of the rust, treated with an anticorrosive composition, primed and painted in a light brown color. It turned out not worse the factory.
And now, when the streets of the holiday village is blocked up with snowdrifts, Victor D. put the snowthrower on the front of the vehicle and slowly rolled to the highway and back. It slowly to the neighbor’s fences inadvertently suffered under the pressure of his snow “bursts”. After this travel along the street leading to the gate Careful, you can walk on a city.
NIKOLAYEV