No, it will, of course, is not about the equipment of the dental office on a production site. However… picture this: a dentist, firmly gripping with two hands the body of the machine with the motor inside, trying to get to the tooth of the patient a thin boron fixed in the Chuck mounted directly on the motor shaft. Inconceivable, right! Everyone knows that the engine and boron spaced and connected to a long flexible shaft: hand of the doctor easy and comfortable to hold thin tip of the working head.
Now look at the majority of manual mechanisms to facilitate work on certain operations in a variety of industries. Whether they are electric, pneumatic or even with a small internal combustion engine, as for the loggers, it is still most often workers have to hold not only the instrument itself, but built into it the heavy engine.
Obviously, affects the traditional thinking is another factor, in addition to purely structural issues, who is forced to overcome every innovator. And indeed, to mechanize any device, the easiest way is to impose it on the motor shaft. But you can also use the flexible shaft in protective sheath, as in the drill. It will allow you to separate and alienate the severity of the motor from the hand tool.
“M-K” reported about lightweight power trowel machine plasterer, has become such thanks to the flexible shaft: the engine is hung like a bandolier, belt, Builder, and carrying only the trowel head.
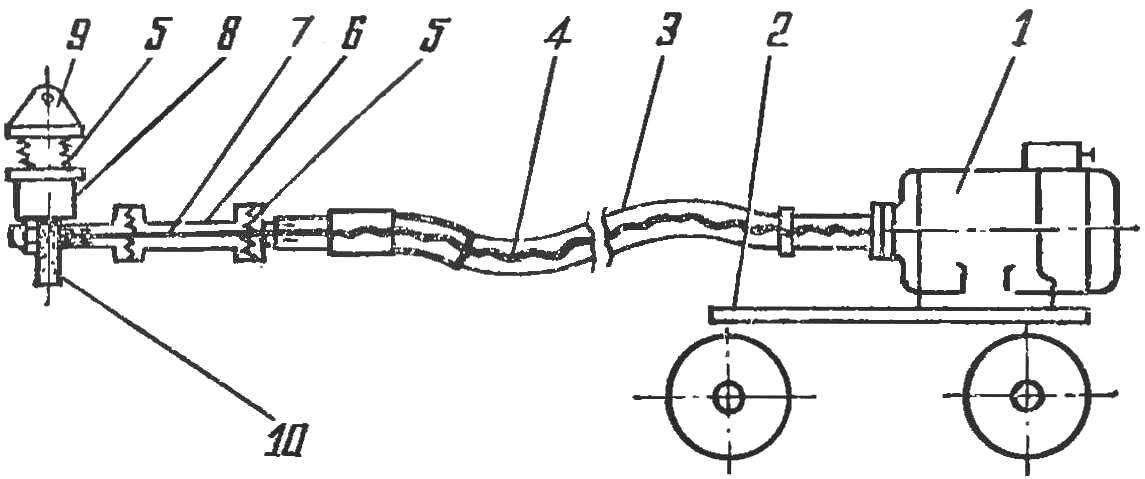
“Flexible” grinding machine and its diagram:
1 — motor (AOL, 2 kW, 36 V), 2 — truck, 3 — hose, 4 — Flexible shaft (b-123, Ø 15 mm, length — 1650 mm), 5 — vibration absorbing dampers (type DK-12 PCs), 6 — the main handle, 7 — spindle shaft, 8 — housing, grit, 9 — assist handle, 10 — grinding wheel.
The same principle was taken as a basis for Tbilisi and innovators, decided to ease the rough-grinding tool, used in steel mills and in the shops of machine-building enterprises for the cleaning of the surface of castings or welds. Using a powerful electric motor, they fixed it on the four-wheeled truck, and took his shaft flexible cable, rubber “armor” to the sanding head with an abrasive wheel (Fig. 1). The fixture turned out lightweight and easy to work with, thereby increasing the quality operations Head machine has one main handle on the shaft and supporting on the casing of the abrasive. They are both equipped with shock absorbers to reduce vibration exposure to the hands — up to 107 dB 117 is the norm and 130 dB from existing tools.
The necessary maneuverability of the machine is achieved thanks to the fact that both front wheels like a piano, legkobetonnye, and the engine itself, moreover, is mounted on platform rotating around its axis.
This design of the grinding machine increases productivity and efficiency in the use of the tool to perform many manufacturing operations.