The design is reminiscent of horse-drawn rake, only their size is smaller and the device easier. Simplicity achieved by the fact that the nozzle rotating and even rotating parts (wheels) on their axles produced without bearings, as the latter would complicate the product. For easy transport of the rake from the windrow with the hay design provided for folding.
Make like a rake on these drawings handyman, owning welding, not much difficulty will be. But some features of their production all note.
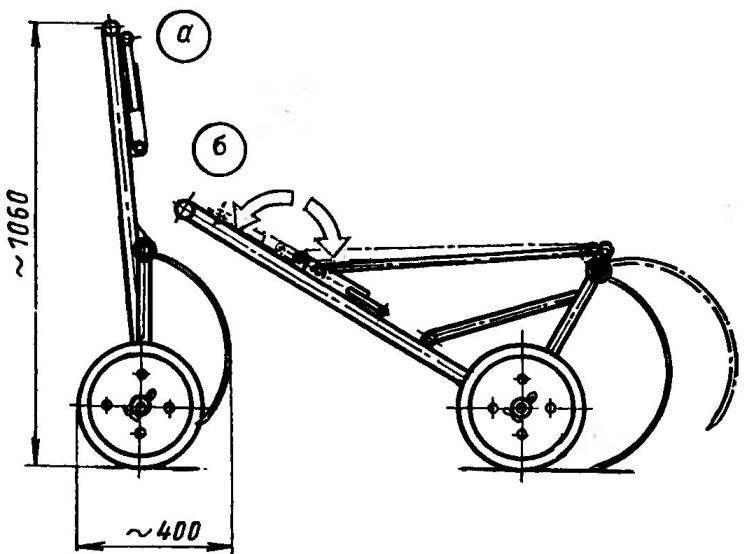
The layout of the rake:
and, in transport condition; b — in the working position
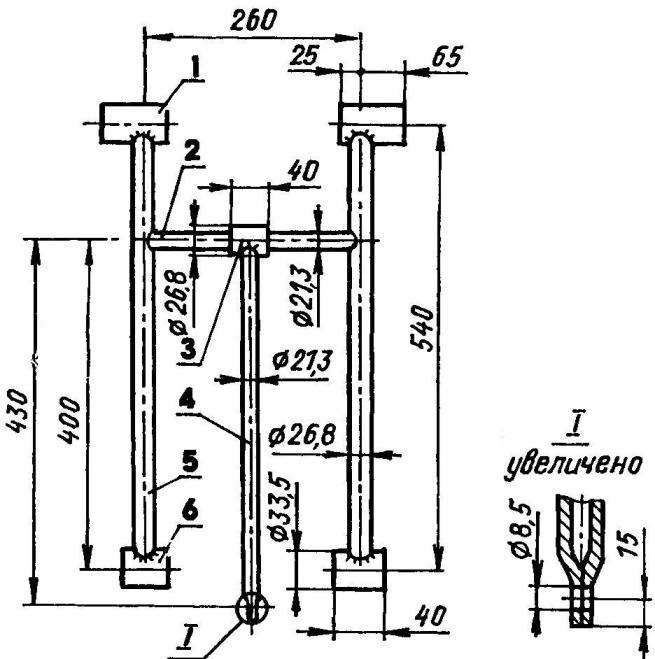
With the strut brace:
1 — sleeve (tube 33,5×3,2, 2); 2 — cross member (tube 21,3×2,8); 3 — bushing crossmember (pipe 26,8×2,8); 4 — brace (tube 21,3×2,8); 5 — leg (tube 26,8×2,8, 2); 6 — bushing (pipe 33,5×3,2, 2)
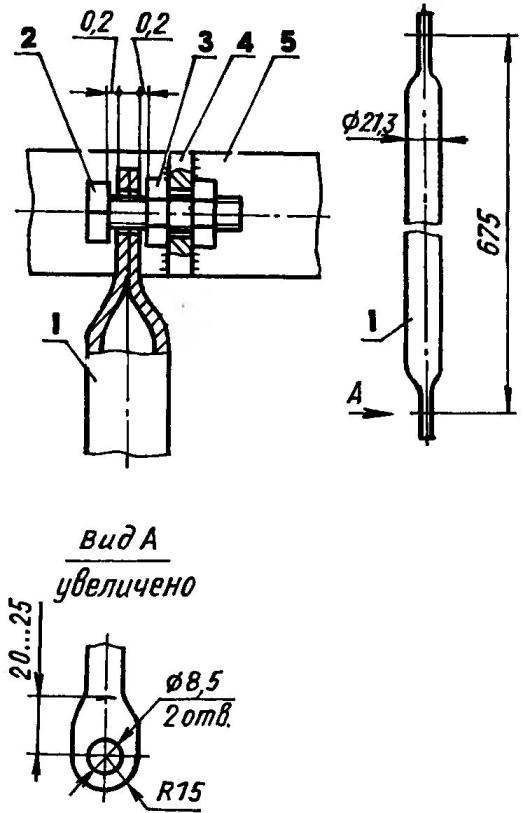
Craving and its hinged connection with brackets:
1 —pull (tube 21,3×2,8); 2 — M8 bolt; 3 — nut M8 (2 PCs); 4 — bracket; 5 — the console rake
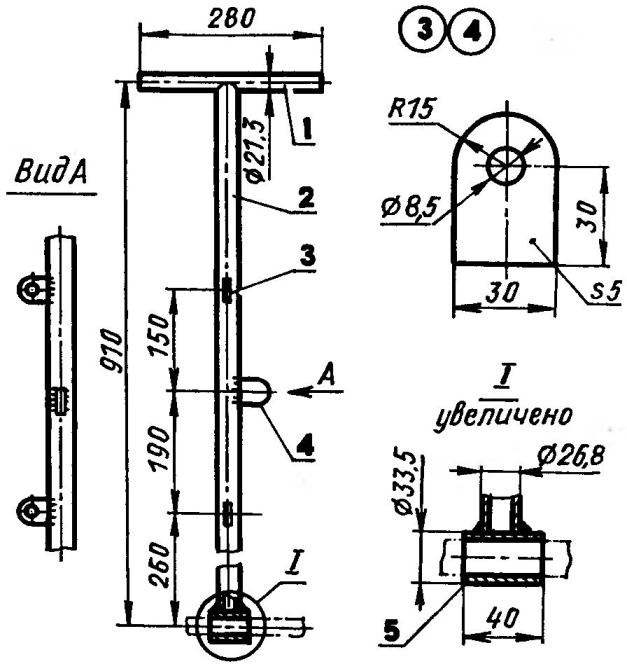
Pole:
1 —arm (tube 21,3×2,8); 2 — pole (pipe 26,8×2,8); 3 — bracket (St3, the sheet s5,2pcs); 4 — emphasis (St3, the sheet s5, is performed with the size of the POS.Z without hole); 5 — adapter sleeve (tube 33,5×3,2)
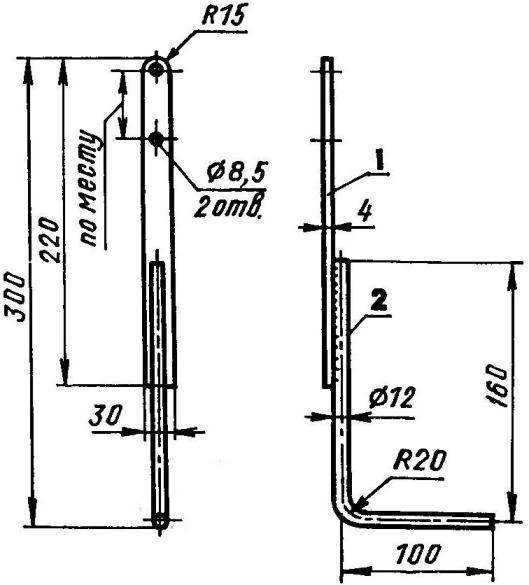
Arm lifting-lowering of the rake:
1 — lever (St3, strip 30×4) 2 — handle (St3, rod d12)
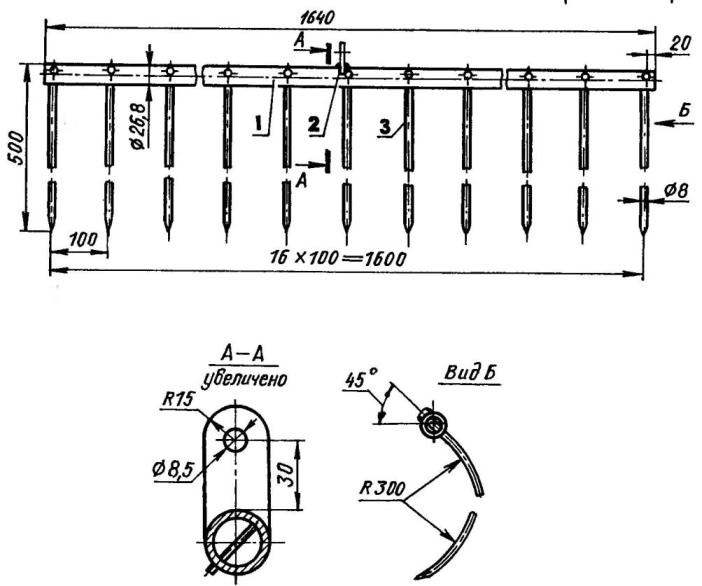
Rake:
1 — the console (the pipe 26,8×2,8;); 2 — bracket; 3 — tooth (45 steel, rod d8,17 PCs.)
Drilling in the tube console, rake holes for the teeth is better done on the machine. Then once you can drill holes with a diameter of 8 mm. the Axes of the holes in this case will guarantee parallel to each other and lie in one plane. I have the same machine, and this operation was produced in two passes — the first drill bit with a diameter of 4 mm, while being careful as possible to observe the parallelism of the axes of the holes.
Swivel with lever and console rake thrust both of its end tapered, drilled holes here and Stoch ends under radius. Did the same and at one end of the strut.
Before welding the parts with the bushings the ends are first processed through the arc of the outer diameter of the second. By the way, the drawbar to the axle can be welded without bushing.
Before welding the uprights to the tie bar should be worn, the bushing of the strut. In the manufacture of rakes before installing the teeth into the holes on console last need to wear the top cartridge racks. One sleeve must be placed between the 7th and 8th teeth and the other between 10-m and 11-m. the Lower bushing on the axle stands should be worn simultaneously with the sleeve hitch. Bushing drawbar is welded to the axle. The displacement of the bushing along the axis of the strut to limit welding to it next to the bushings wire rings (two half rings). The same rings offset is limited to inside of wheels with a diameter of 300 mm from the cultivator KRN (will fit others, but with a diameter of 500 mm, otherwise you’ll have to increase the sizes of other components and parts). The outside wheels on axis are mounted the thrust washers of inch pipe and zaspirtovannaya.
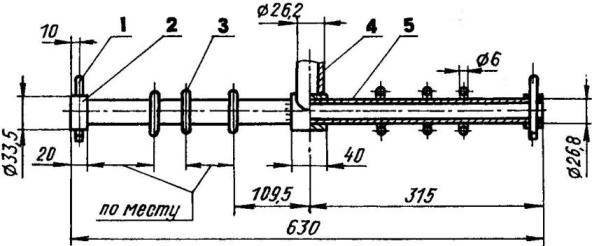
Axle:
1 — cotter pin 6,3×45 (2); 2 — thrust washer (tube 33,5×3,2, 2); 3 — restrictive ring (consists of two half-rings) (rod d6,6 PCs); 4 — pole transitional bushing; 5 — axis (pipe 26,8×2,8)
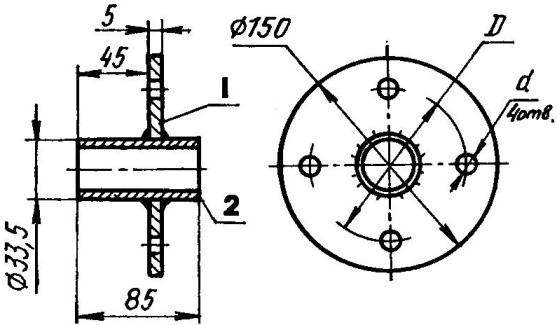
Hub:
1 disk (45 steel, sheet s5); 2 — bushing (pipe 33,5×3,2);
D and d are the holes in the wheel disc
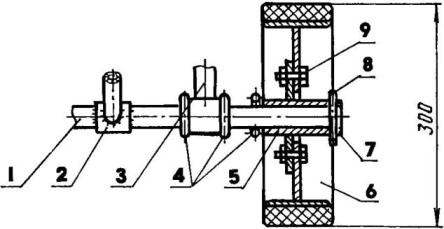
Installation of the wheel strut and the beam axis:
1 — axis; 2 — pole transitional bushing; 3 — hub; 4 — separation ring (each of two semi-rings); 5 — hub; 6 — wheel (rim and disc) with the bus; 7 — Circlip; 8 — pin; 9 — a bolt of fastening of a wheel
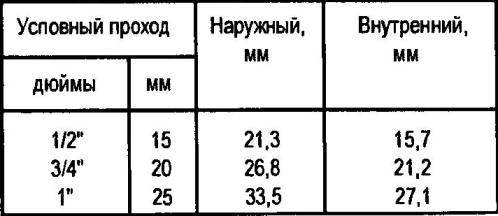
The diameters of the pipes
Some complexity may appear the choice of location of the second hole on the lever under the top end thrust. His place must match course rod bracket on the console from the raised position to the rake lowered to the ground level of the ends of the teeth.
Each swivel joint consists of a bracket, a bolt with two M8 nuts and the movable part (end of the pull rod or lever). The average nut is fixed by crushing the thread in position, providing a small gap between it and the movable part. Instead of the second hex nuts at each joint, you can use the wing— did not need open-end wrench. These swivel use with folding design for transport. To do this, Unscrew the outer nuts on both ends and thrust the lower end of the brace strut.
Dimensions rake in the folded (transport) position 1060х400х 1640 mm. nya Despite the fact that all parts steel rake turned out not-so-heavy — their weight is only 20 kg.
The most effective rake with a yield of dry weight of hay to 15 quintals per hectare for mowing a variety of manual by mechanized mowing or using power tillers. At higher yields the length (height) of the teeth of the rake should be increased to 700 — 800 mm. the Use of a rake allows you to rake the hay in swaths, with the area of 0.5 ha for 1 hour with a minimum of waste. Such a rake is easy to adjust under mechanical traction.
A. MASTERENKO, G. Kotelnikov, Volgograd region
Recommend to read
THE VAZ-2108/2109 SPUTNIK
The second-stage model of the Volga car was three-door front wheel drive hatchback VAZ-2108 "Sputnik". The design of the VAZ-2108 was started in may 1977, the launch of a series of...
IN THE AIR – “CORAL FISH”
PAINTING OF AIRCRAFT CARRIER-BASED AIRCRAFT Military aircraft painting aircraft have always played an important role. After all, well-chosen color camouflage reduce the visibility of...