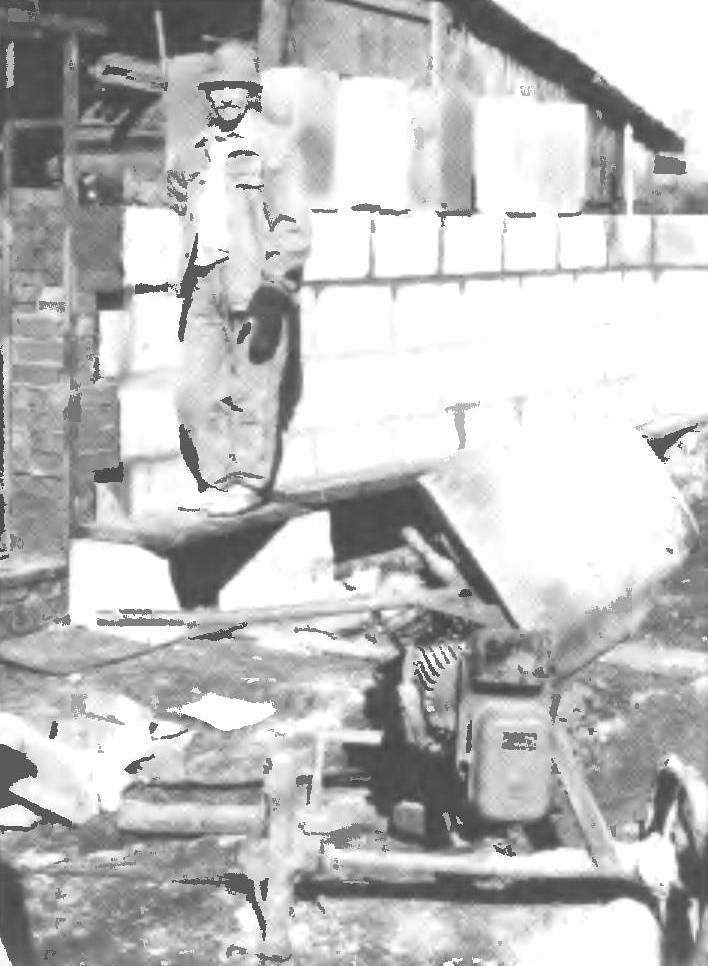
Of course, it would be easier to buy it (good choice on the market right now is great), but at that point, the money (which, as is known, superfluous) is much more useful to purchase materials.
Climb on sheds, garages and workshops at home and friends, to find a suitable components and materials. According to them, the mind has matured and the overall design scheme, but the dimensions of parts were determined in the course of work.
Manufacturer of concrete mixer started mixer — barrel-mixer. First, cut pieces: sheet steel 5 mm thick bottom plate 2-mm sheet — solid cylindrical shell belt and a few “petals”of the sectors of the conical part (although the shell is also quite possible to make a composite). Next, the workpiece with a hammer and vise gave the desired radiuses and bends. Then began assembling them. To the bottom and grabbed the belt, and the belt — petals (the latter also connected to each other). The resulting neckline was fringed with a rim of 10 mm rebar and edges savelevel around him. After that, all seams are carefully provari arc welding. Inside the mixer for forced stirring of the mixture welded three divider. They were made of the 16 mm reinforcing bars.
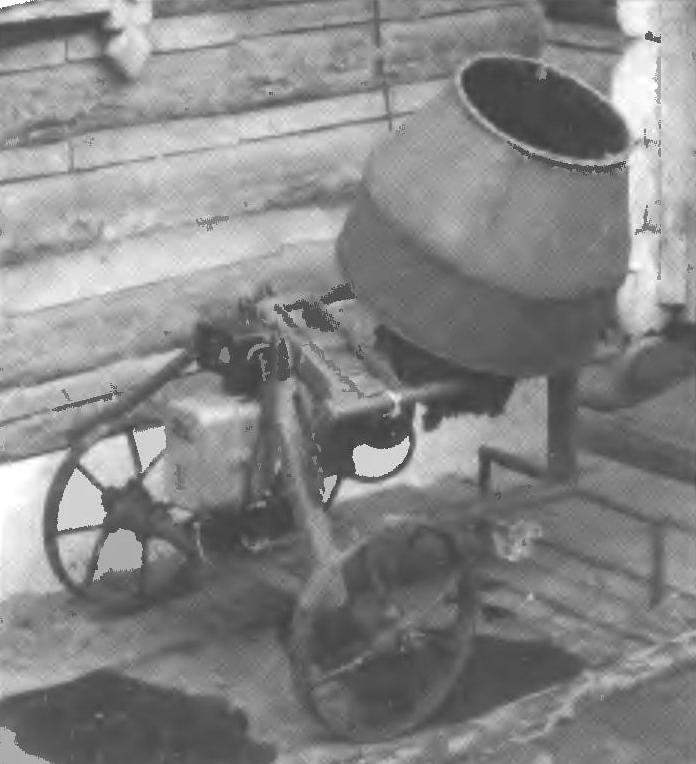
Mixer helper before commissioning
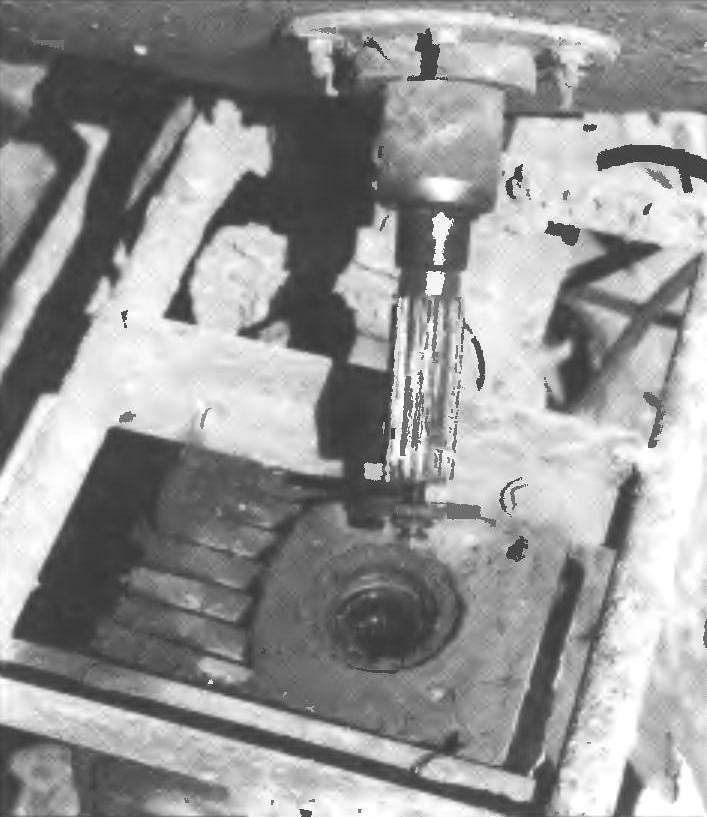
Docking port of the mixer and reducer
The rotational drive of the mixer consists of a three-phase motor (power supply 380 V) with a capacity of 1 kW with a speed of 950 rpm and the worm gear. Reducer although it is unknown what kind of technology, but approached its parameters is: having a reduction ratio equal to 17, it provides the optimal rotation of the mixer slightly less than 60 rpm.
Both mechanisms fixed rigidly and coaxially on a tubular subframe, and each other connected by rubber hose.
The subframe using 2 of the lug bolts М10х40 mm is mounted pivotally (rotatably) to the main frame. Spatial frame though, but very simple: its T-shaped base and stand (vertical and oblique) are made of welded rectangular tube section 60×20 mm. Inclined strut supported by an additional brace and it is welded to the panel, which is attached to the condenser box and the starter.
The frame has four legs: two wheels (thanks to which the mixer is moveable) and two legs. Wheels from agricultural equipment, without tires. Legs with the bridge between them is made of half-inch water pipe. From the bottom to the legs to increase the area of their supports welded flat glides.
Mixer through the bottom flange with the hub seated on the keyway on the output splined shaft of the gearbox and secured with M10 screw with washer, screwed into a corresponding threaded axial bore in the shaft end. For a thorough cleaning (when required even hitting the stuck mixture from the walls) the mixer is removed together with the shaft gear (see photo).
Unladen position of the mixer is balanced by the mass of the motor and reducer. But the mixer is set at different fixed angles. For this purpose, the inclined rack main frame is welded a lug with a hole diameter of 11 mm, and the subframe is a broad arched plate. In the hole of the eyelet is inserted a pointed pin and plate in place of drilled holes corresponding to the angles of inclination of the mixer to the vertical 40, 60 and 90 degrees. These inclination angles optimal answer produced by the mixing of the concrete mix, mortar preparation, clean-up of the mixer, respectively. Pin, not to lose, attached to the frame on the chain. The slope of the mixer is made by the handle lever, made of half-inch plumbing pipe and welded to the subframe. The connection is reinforced by the gusset, and the handle is slightly curved to ensure comfort and control at reasonable levels. For unloading the mixer is tilted up to the stop in the longitudinal beam of the frame. Sometimes loading components easier to produce, the maximum lifting mixer (at an angle of about 20°). The handle rests on the wheel.
Generally speaking, the mixer constructed under a right-handed medium height. If the owner-operator is left-handed, then the design should be done in a mirrored version, but with high growth should be increased 10 centimeters and the height of the standoff frame.
At maximum lift mixer handle rests on the wheel, and the maximum lowering of the casing rests on the longitudinal beam of the frame. In the last position if necessary, and “shock” cleaning mixer.
Electrical diagram model — are repeatedly cited in the publications, “Model construction”, so not going on it to focus the attention of the readers.
After a test run of the frame, the subframe and the mixer is coated with a primer, lubricated friction parts of gearbox, wheels, hinges.
To allow movement of the concrete along the perimeter of the construction site made 15-metre extension cable made of flexible, but durable cable.
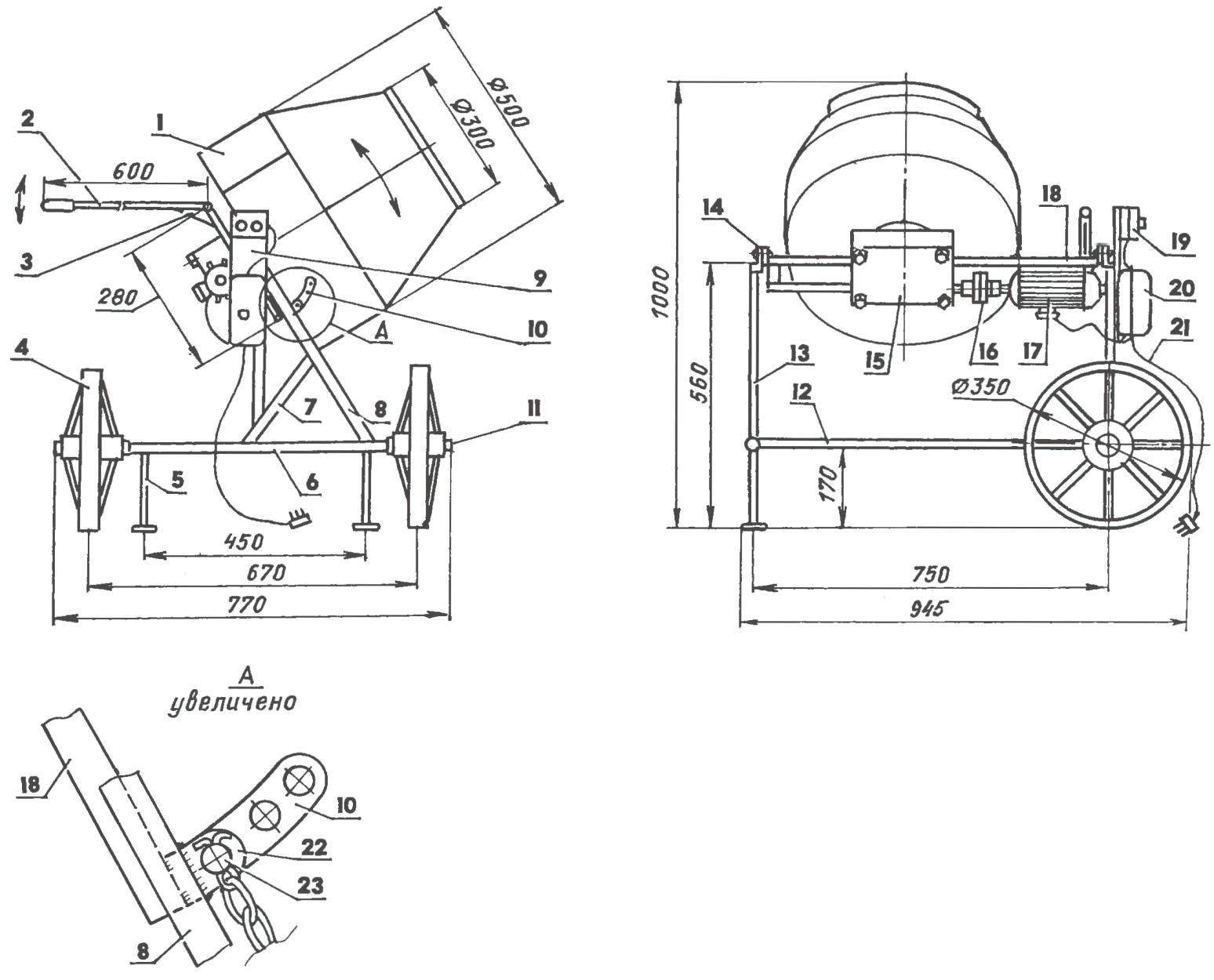
Fig. 1. Mixer helper:
1 — mixer; 2 — lever lever (pipe 1/2″); 3 — Klondike arm (St3 sheet s3); 4 — wheel (machinery); 5 —leg, with bearing (tube 1/2″ and the sheet s3. 2); 6 — transverse beam of the frame (tube 60×20); 7 — brace a tilted bar (pipe 1/2″); 8 — inclined strut (tube 60×20); 9 panel (St3 sheet s3); 10 — sector of the angle adjustment of the mixer with the pin on the chain (St3 sheet s3); 11 wheel axle (steel 45, range 16, 2); 12 — longitudinal beam of the frame (tube 60×20); 13 — vertical stand (tube 60×20); 14 — eyelet hinge pivoting subframe (St3, the sheet s5, 2); 15 — worm reducer (I = 17); 16 — rubber coupling shaft coupling motor and reducer; 17 — motor (N = 1 kW, n = 950 rpm, 3-phase 380V); 18 — subframe (spars — pipe 3/4″, cross – area 35×35, 4 valves); 19 — starter; 20 — condenser box; 21 — power supply cable; 22 — eyelet (St3 sheet s3) fixing the inclination of the mixer (the position of the angle of inclination of the mixer, compared with the main view in the callout, And, changed); 23 — pin with chain
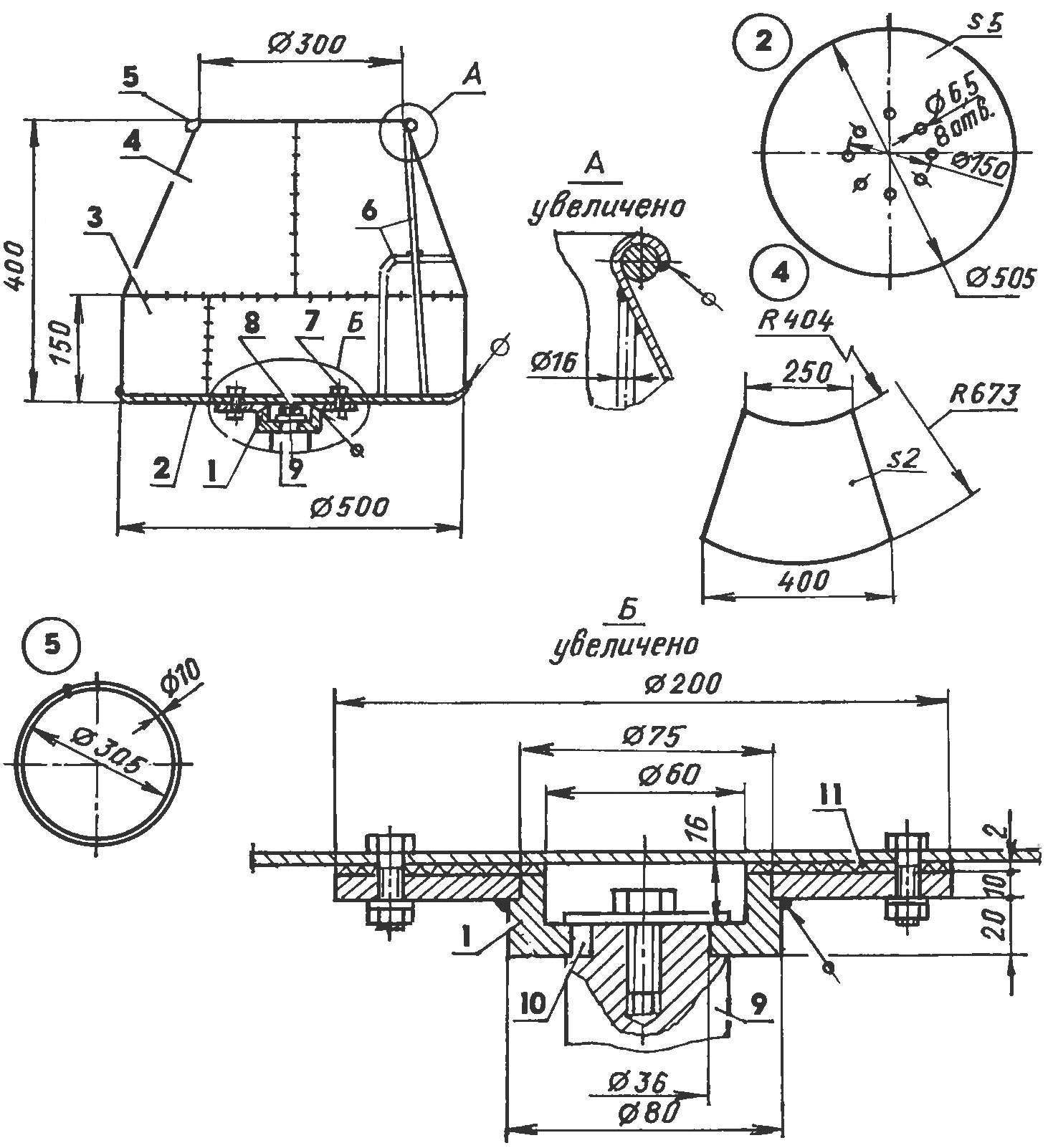
Fig. 2. Mixer:
1 — flange-hub (St3); 2 — the bottom (St3, sheet s5); 3 — shell cylindrical belt (St3, sheet s2, the band 150×2, L1580); 4 —sector of the conical part (St3, s2 sheet-4 pieces); 5-rim of the neck (St3, fittings Ø10); 6 — divider of the mixture (reinforcing bar Ø16, 3 pieces); 7 — bolt M6, 8 PCs; 8 — M6 screw; 9 — output shaft; 10 — key (St3) shaft; 11 — gasket (rubber, sheet s2)
Add to this that the small dimensions of the equipment often provide much greater opportunities: the ease of movement, maintenance, and improvement of the quality of mixing of the mixture, as well as ease of storage (space it takes a bit).
In the preparation of the concrete mix (or mortar — with an extra dose of sand instead of gravel), I adhere to the following sequence and download of the mix ratio in litres (or dm3):
— inclusion of rotation of the mixer; pour in water (6 — 8); — filling cement (4 to 6); — load of sand (10 to 15); — loading of gravel (20 — 30).
The components are mixed for 3 to 5 minutes. At this time, fill the bucket for the next batch.
One day I filled a 10 m trench for the Foundation depth of 1 m and a width of 0.25 m, however put there still rubble. The mixer was placed directly over the trench obliquely, the wheels stayed on one side of the trench, and one leg on the other side (the second leg hung over the trench). The concrete fell out exactly in the trench, and the fills in this place, turning slightly to installation, rolled it on.
In five years of existence of the concrete mixer with it were built brick house with solid concrete Foundation dimensions 10×9 metres; a garage of foam blocks on a strip Foundation with dimensions of 12×5 meters; concrete cellar, septic tank, and underground Foundation for a bath. To do this, just mixed more than 10 dump trucks of gravel, sand, slag.
In conclusion, serious advice to homebrew: before you start building a house, but it is at least ten years of hard work, you should estimate in advance their strength and health. Because the mixer only opens his mouth and chews and feeds her with a shovel and bucket the owner-Builder.
Technical specifications of concrete mixer
Overall dimensions (length x width x height), mm……945x770x1000
Engine:
the voltage, V……………………….380
power, kW…………………………………….1
rpm/MIA…………………………….950
Gear ratio……17
The volume of the mixer, l………………………………50
The rotation speed of the mixer, rpm…..56
The output mixture from one batch, l
solution……………………………………………20
concrete………………………………………………30
Productivity, m3/h……………….0,5
Weight, kg …………………………………………..60
A. MATVEICHUK, Zavodoukovsk, Tyumen region.