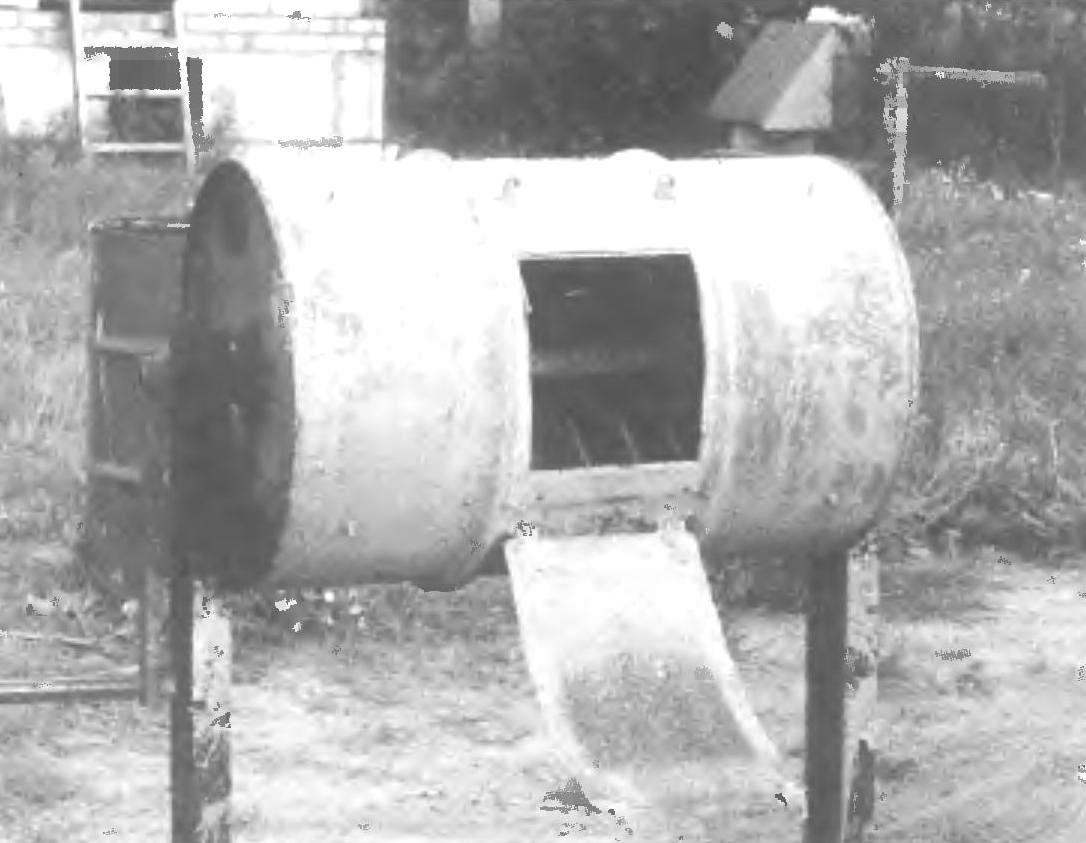
Mixer, the description of which is given below, is not only simple but also easy to operate.
Use it no tedious mixing of the components takes only 10 to 15 seconds, not counting loading concrete mixers. And mood improved quickly made this necessary work. And performed efficiently, as the mixture is thoroughly mixed and is homogeneous, which is very important for making concrete and reinforced concrete structures.
A significant advantage relative to many other variants of such devices is the fact that its production did not require sophisticated and expensive drive mechanisms (motor, gearbox, pulleys, belts), because drive — manual, lever rotation.
The mixer is made from 200-liter drums, horizontally mounted on the working shaft, mounted on two supports in antifriction bearings; loading and unloading through a rectangular opening in the shell. Describes many options of mixers based on standard barrels. Each of them has its own “osobinu”. Here “highlight” are located inside the drum of the comb, providing accelerated mixing and improving the quality of the concrete mix.
And now some practical advice on making concrete mixers for those who decided to repeat our experience.
First of all you should prepare the necessary materials: barrel of 200 liters, the channel number 10 (or weld along the edge corners 50×50), a circle with a diameter of 40 mm, the ball bearings 208 (2 PCs), etc., in accordance with the list of positions in the figure.
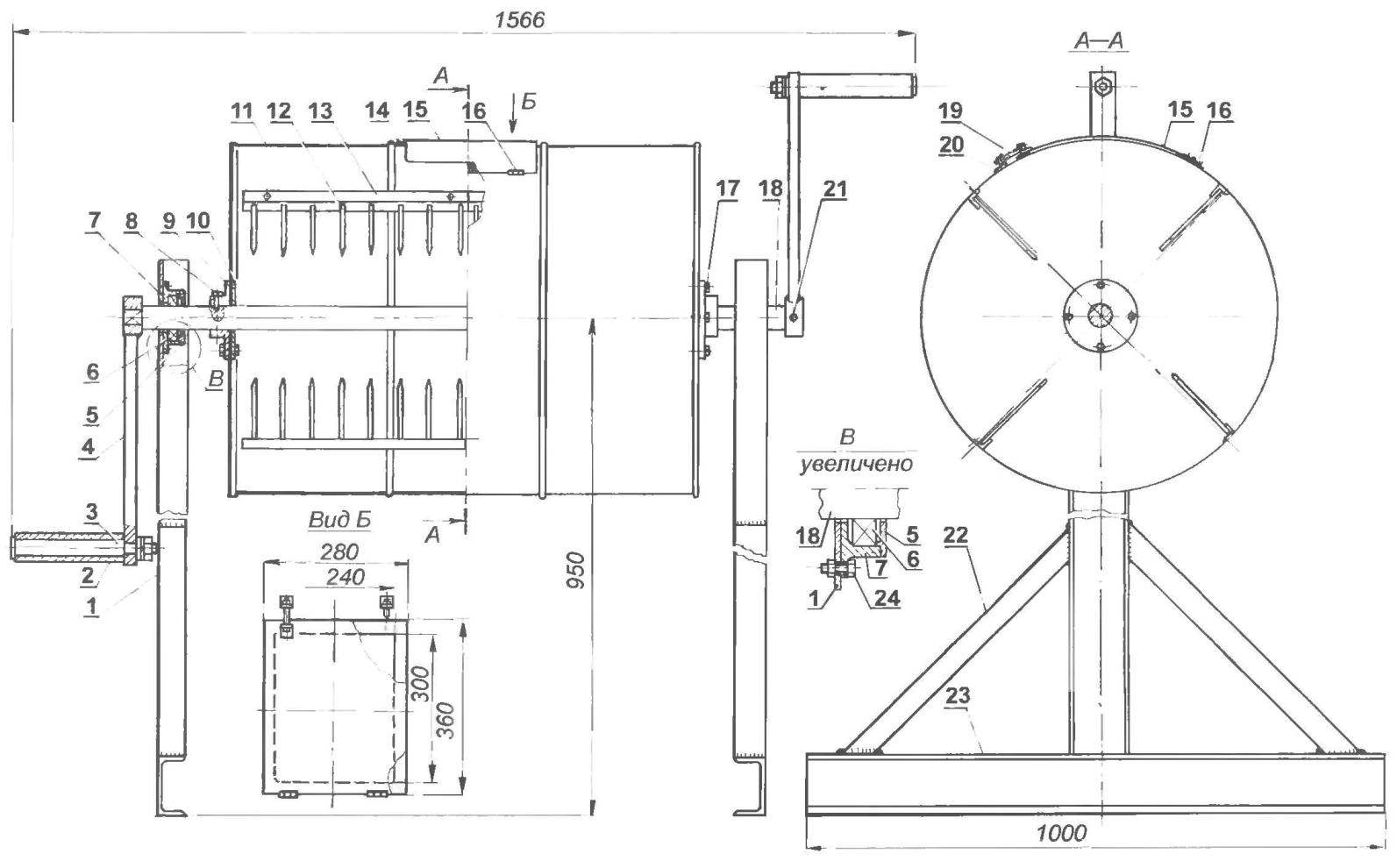
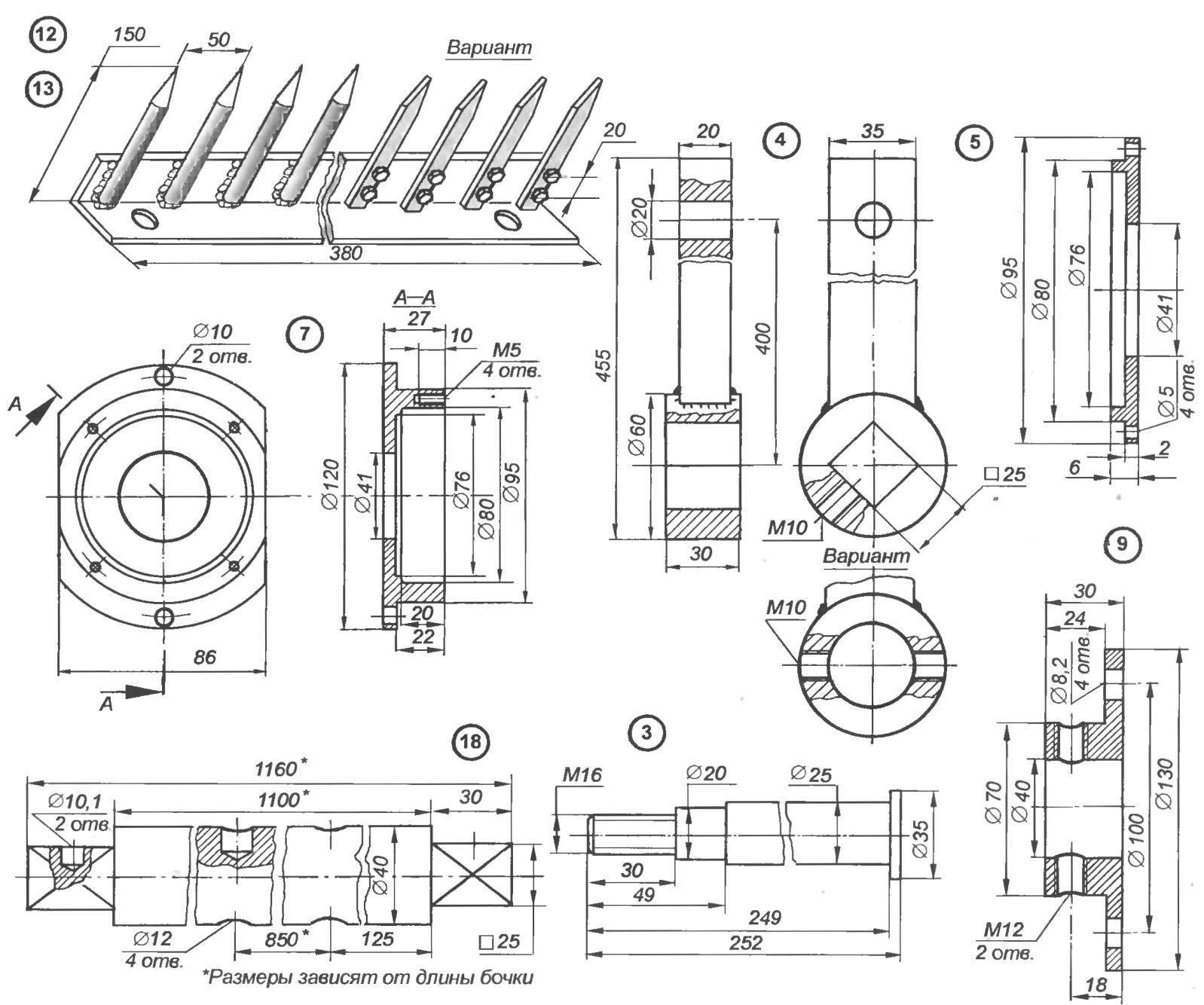
Mixer:
1 – (channel No. 8, No. 10 area No. 5); 2 – tip arm (pipe 40×5, 1.245, 2); 3 – axis arm (circle Ø35, 2 pieces); 4 lever (band 20×35, circle 060, 2 PCs.); 5 — cover of bearing housing (2); 6 — the bearing 208 (2); 7 — the bearing housing (2); 8 stopper flange (bolts M12, 4 PCs.); 9 flange of the working container (2 PCs); 10 reinforcing washer (2 PCs); 11 — working capacity (200 l barrel); 12 — pin comb (4×10 strip or rod Ø12 64 PCs) 13 — based combs (area 36×36, L380. 8 PCs): 14 — opening weatherstrip (rubber); 15 — cover (sheet sl — 1,5) 16 loop card (2 PCs); 17 – flange mount (bolt M8, 8 PCs.); 18 — shaft (Ø40 circle); 19 – coupling cap (bolt M8 2 PCs.). 20 bracket of the screed (area 40×40, 2); 21 – the stopper arm (M10, 2 PCs.); 22 spacer (channel No. 8, No. 10, area No. 5, zone); 23 brogue (channel No. 8, No. 10) 24 fastening the bearing housing (M10, 4 PCs)
The production start with the processing of the barrel. In the center of the bottom and cover the drill holes with a diameter of 40.5 — 41 mm under the shaft and the corresponding bolt holes of the mounting flanges by which the drum is rigidly connected with the shaft. To download the components of concrete in the middle of the barrel wall, cut rectangular opening size 240×300 mm and the contour of the outside of the paste with strips of soft rubber with a thickness of 5 — 8 mm for sealing.
Produce cover that encloses the drum during mixing, and attach it jointed with card hinges and to lock in closed position mounted on the barrel and the lid on two brackets (corners 40×40) with holes with a diameter of 8 — 9 mm coupling bolts (of course, it would be better to weld, but you can use the bolted connection). For fixing the cover is parts and tightening bolts are fine and the special clips, so-called “frogs”.
Inside the barrel by its forming with an interval of 90° mounted comb from the corner 36×36 mm (or slightly more) is welded with a pitch of 50 mm steel pins with a diameter of 10 — 12 mm length 150 mm (pins can also be manufactured from the strip by replacing the welding bolt-on). The length of each comb — 760 mm (for easy installation, inside the drum it is better to make two halves).
The next stage — the production of a manual drive mechanism which consists of a shaft rigidly connected to the drum, and rotation of levers mounted on the shaft ends.
Billet shaft — from a profile of circular cross section with a diameter of 40 — 45 mm, of ordinary carbon steel. It is well processed, so some wiring work, you can replace the plumbing, which will require a file with a large notch. With it on the ends of the shaft formed by the tetrahedron for the installation of the flanges of the levers of rotation. In one facet drill a shallow hole with a diameter of not less than 10 mm and, respectively, in the flanges of the lever of a cut through the threaded hole under the M10 retaining bolt. In addition, the shaft in two places drill two deaf diametrically located holes with a diameter of 12 — 12,2 mm; under the retaining bolts to the flanges of the drum.
In the manufacture of flanges can not do without turning the work, but you can try to find something suitable in a scrapyard. You will need only some fine tuning of your findings. If the internal hole is large, it is easy to reduce by means of the bushing are not necessary counterbore. All this will reduce the cost of production of concrete mixers.
After completion of the shaft and the flanges begin the Assembly: a shaft passed through the axial hole of the barrel with simultaneous mounting on him with external flanges and reinforcing washers from the inside of the drum. Washers are necessary to prevent tearing of the walls of the drum, as drums are made of very thin sheet steel. Four holes drilled in the flanges and the ends of the drum, skip the M8 bolts and tighten the nuts with spring washers.
After working on assembled, is to place it in the rack (better, of course, to make the frame, but this extra cost of materials and time). For stability and rigidity to the racks weld-in Shoe (channel No. 8 or No. 10 length 1000 mm) and spacers from the same channel or from corners, or from strip steel of thickness 8 — 10 mm If welding not, stand, shoes, and struts can be joined by using plates and screws. In the upper part of the uprights in alignment with the hole in shaft M10 screws fasten the bearing assemblies.
The figure shows the drawing of the housing for the ball bearing 208. You can put other important that the shaft diameter was not less than 30 mm. And one more requirement: the bearing housing should fit snugly to the inner wall of the stand, to ensure rigidity. Therefore, if the outer diameter of the body greater than the distance between the shelf channel, with a hacksaw, grinding or, if possible, on a milling machine should be removed from the side surfaces of the housing two flats to the correct size. To protect the bearing from moisture and dirt the case is closed by a lid.
The simplest (but less efficient) variant of the bearing Assembly — bronze bushing. To reduce friction in the pair “shaft — Bush”, it is desirable to drill a hole in the middle wall bronze bushings with access to the internal cavity, lay it in strips of felt and fill with engine oil. In the process, it is necessary to constantly add oil. To in the plug hole is not exposed to water during rain, it is necessary to screw the screw.
Left to make the leverage and arm rotation of the drum, again on the basis of the available material. These details are depicted in the figure. Another tip is not to fill the calluses on your hands, you must on the axis of the arms, previously missed any grease, install with a gap cut out of pipe bushings, ensuring their free rotation. Sleeve length should be such that you can grab it with two hands.
After manufacturing all parts and components manufactured final Assembly: drum shaft mounted in bearing assemblies in the racks, and the ends of the shaft to attach the levers of rotation of the drum.
Then dig in the ground two holes under the rack with the boots on the depth, which should provide a comfortable work with your growth. If the unloading of the final solution is expected to produce in the cart, the height of the mixer must be such that trolley freely was located under the hatch of the barrel.
Technology solution preparation is very simple: to be loaded into the mixer alternately sand with gravel, cement, fill with water (all in proportion), a rotatable drum (about 10 to 15 rpm) and the solution is ready.
When running large volumes of concrete have to use the mixer for a long time, with the inevitable buildup of solution in the gaps on the corners of the intersection of combs with the body of the drum and at its ends. Typically, for fighting off the build up using a crowbar. This process is labor intensive, and execute it extremely inconvenient because you need to reach the most secluded corners of the mixer, otherwise the cleaning will be ineffective. But all this can be avoided by using small boulders measuring 30 to 80 mm in an amount of 1.5 — 2 buckets. They fall asleep in a mixer, pour the bucket of water and produce rotation of the drum: 20 — 30 rpm in the same direction and the same in another. Then the contents of the mixer discharged into Chan or truck with sides (preferably not to stay with this process, particles of the solution is again deposited on the walls of the drum).
For the owner of this mixer work on the preparation of the solution does not require large expenditures of time and will cease to be heavy.
Patino V., Borisov, Belarus