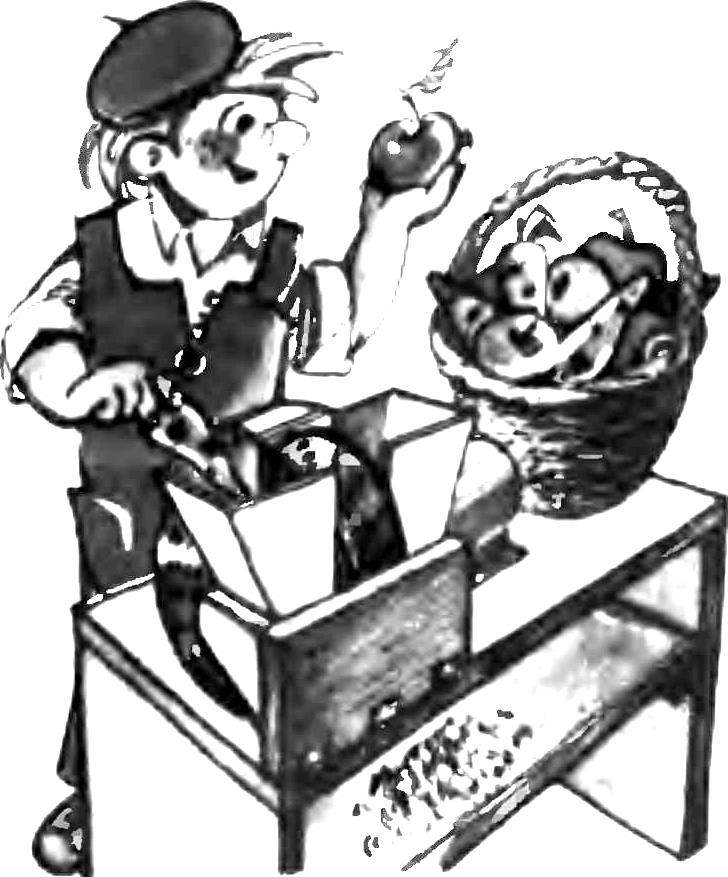
So I decided to share with readers my design chopper driven by a motor. Tried three options and settled on this as the most simple to manufacture and at the same time, a sufficiently high performance, easy to handle. It is possible to shred all kinds of fruits and vegetables, even squash and pumpkins, cut into pieces. Experience has shown that crushing of the same apples in this way the yield of juice during subsequent pressing much more than the crushing hand.
It is also important that the installation is justified from a hygienic point of view: after work it can be easily disassembled for cleaning, washing and drying.
All the main parts and components of the grinder are mounted on a wooden pole-base made of boards 30 mm thick and having two legs from the same Board, and a window for output of the crushed mass in the filled bottom container.